Electrodos de electroerosión fabricados mediante Impresión 3D
Josefa Galvañ Gisbert, Asunción Martínez García y Rubén Beneito (proyectos@aiju.info), de AIJU; Angel Mira (tallerestibi@tallerestibi.com), de Talleres Tibi; y Rubén Paz y Mario Monzón (ruben.paz@ulpgc.es), de la Universidad de las Palmas de Gran Canaria
04/05/2021Utilizando tecnologías de fabricación aditiva o impresión 3D con material plástico, tal como se propone en este proyecto, se pueden fabricar uno o varios electrodos al mismo tiempo en unas 24 a 48 horas, ahorrando mucho tiempo, materia prima, recursos y costes. El método alternativo para la fabricación de estos electrodos con AM mediante Sinterizado Láser de Metal (SLM), no obstante, es bastante caro e inaccesible para muchas pequeñas y medianas empresas, pudiendo costar una pieza hasta 60 veces más que una fabricada mediante tecnologías de fabricación aditiva basadas en extrusión de material, también conocidas como Modelado mediante Deposición Fundida (FDM) o Fabricación de Filamentos Fundidos (FFF).
Dadas los antecedentes indicados, la empresa Talleres Tibi, S.L., en colaboración con ADD:North y +90 3B Dijital Fabrika y el soporte de AIJU y la ULPGC, ejecutan el proyecto EDM-Additive para la obtención de materiales conductores de base polimérica para tecnologías de impresión 3D, específicamente Sinterizado Láser (LS) y FDM. Con estos materiales en fase de optimización, se fabricarán electrodos para EDM que, con el fin de alcanzar las especificaciones del proceso, deben tener alta precisión dimensional, una rugosidad superficial adecuada y alta conductividad eléctrica.
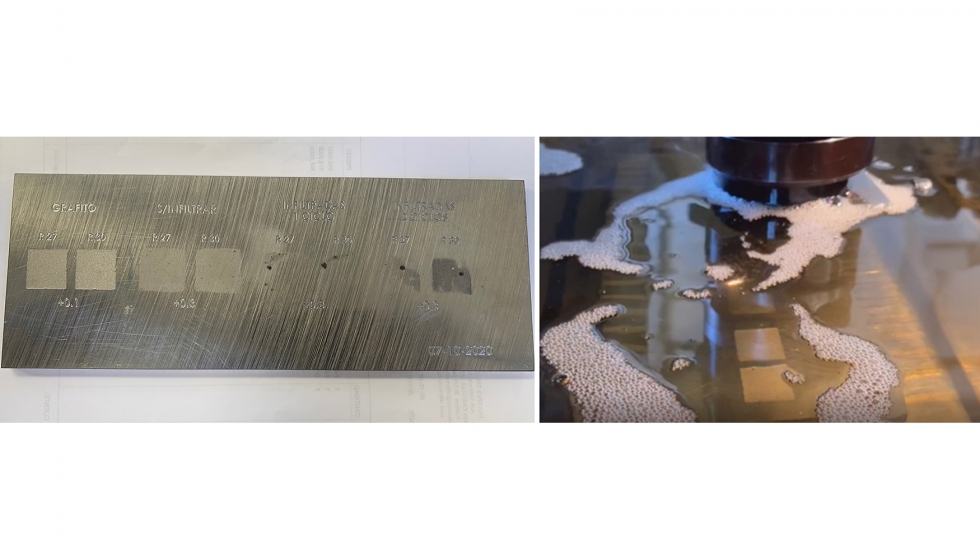
1. Introducción
El proyecto ‘EDM Additive’ tiene como objetivo el desarrollo de electrodos de electroerosión (EDM) fabricados con materiales conductores mediante fabricación aditiva (AM). Para ello, ha acometido el desarrollo de materiales plásticos eléctricamente conductores para las tecnologías de LS y filamentos de FDM. Los materiales desarrollados se basan en resinas fenólicas y grafito, en el caso de las tecnologías de LS (basadas en una patente de AIJU [1]). En cuanto a las tecnologías FDM, los materiales obtenidos tienen como matriz plástica ABS, PLA y PVDF a los que se integran cargas carbonosas, tales como nanofibras de carbono, grafeno, etc.
El proyecto EDM-Additive ofrece la oportunidad a las empresas fabricantes de moldes de abaratar sus tiempos de entrega y costes de producción, en tanto que se pueden realizar electrodos con formas más intrincadas que ofrezca una determinada libertad de diseño.
La propuesta está liderada por Talleres Tibi, S.L. y se desarrolla con el soporte de AIJU y de la Universidad de las Palmas de Gran Canaria (ULPGC). En el marco internacional participan +90, factoría digital líder en el mercado turco, y AN3D, empresa sueca experta en la producción de filamentos de última generación para FDM.
[1] WO2013144399 – Method for the Production of Monolithic Carbonaceous or Ceramic Systems [online: https://patentscope.wipo.int/search/en/detail.jsf?docId=WO2013144399]
2. Tipos de materiales conductores desarrollados y su rendimiento
En el marco de ejecución del proyecto, se han obtenido materiales para sinterizado láser y FDM, alcanzando conductividad eléctrica sobre matriz plástica.
2.1 Materiales eléctricamente conductores para sinterizado láser
Se han desarrollado de forma iterativa hasta cinco formulaciones de materiales para sinterizado láser a escala laboratorio y se ha validado una formulación a escala industrial.
Siguiendo el procedimiento establecido en la patente, una vez preparada la mezcla homogénea de partida se obtuvieron electrodos simples mediante sinterizado. Esto permitió la evaluación del comportamiento de la formulación durante el proceso de LS y la optimización de sus parámetros experimentales. Estas formulaciones, basadas en resinas fenólicas con aditivos conductores, requieren de una velocidad de escaneo láser más lenta con el fin de transferir más energía por unidad de tiempo para lograr buenas piezas. En su producción, ninguna de las formulaciones presentaba huecos en el lecho de sinterización.
Seguidamente, estas piezas pasaron por un posprocesado que incluye una etapa de curado, para mejorar la resistencia mecánica y estabilidad de las piezas, otra de pirólisis para mejorar su estabilidad térmica y conductividad, y finalmente una de infiltración, para aumentar su densidad y conductividad eléctrica. Siguiendo una estrategia marcada previamente, algunas de estas piezas no se infiltraron.
Una vez obtenidas las piezas, se procedió a su caracterización para determinar parámetros como la contracción de las piezas, propiedades mecánicas y eléctricas de los distintos electrodos obtenidos para cada formulación.
Características funcionales de los materiales conductores para LS
Las formulaciones están basadas en distintos porcentajes de resinas. En consecuencia, en los procesos de curado y pirolisis (y no así el de infiltración), estas piezas se contraen a medida que aumenta el contenido de resina en la formulación de los materiales. Asimismo, reducen significativamente su peso debido a la descomposición térmica de la resina. Esto determinó el factor de corrección a aplicar a los diseños 3D iniciales.
En el proceso de infiltración, no obstante, la densidad aparente (y peso) aumenta exponencialmente con cada ciclo de infiltración. Después de dos ciclos de infiltración, la densidad aparente sigue siendo inferior a la correspondiente al grafito puro.
Los ciclos de infiltración mejoran claramente las propiedades eléctricas de los materiales, especialmente en el primer ciclo de infiltración. En los siguientes ciclos, en cambio, permanece supuestamente constante. No obstante, esta conductividad es todavía inferior a la de los electrodos de grafito comerciales actuales.
Con los electrodos obtenidos, se realizaron pruebas de EDM que han dado unos resultados muy interesantes desde la perspectiva de la investigación, ya que se pudo llevar a cabo una electroerosión relativa en una placa de acero estándar (Figura 1). Específicamente para este proceso, las piezas no infiltradas tienen un rendimiento superior al de las piezas infiltradas. Sin embargo, el ratio de desgaste es elevado. La teoría establece que tanto la densidad como la conductividad están separadas de la tasa de desgaste. Por ello, se va a aplicar una estrategia distinta basada en la compactación de las partes, en lugar del incremento de conductividad de las piezas, y a determinar estrategias de electroerosión más suaves.
2.2 Materiales eléctricamente conductores para FDM
En el desarrollo de esta acción se han obtenido 5 formulaciones distintas sobre base polimérica ABS, PLA, PETG y PVDF con distintas tipologías de aditivos conductores. A todas ellas se les aplicaron ensayos de conductividad volumétrica y de superficie, aplicando una metodología unificada previamente determinada.
La formulación de PVDF fue la que demostró mejor desempeño, alcanzando niveles de conductividad de apantallamiento electromagnético tanto en los filamentos como en las piezas fabricadas con estos. Una vez demostrada la conductividad de esta formulación, se ha mejorado su facilidad de impresión, precisión dimensional y estabilidad de los filamentos a nivel industrial.
A partir de ahora, se pretende aplicar diversos procesos de recubrimientos para verificar su efecto en la conductividad de los filamentos y las piezas, con el fin de alcanzar la conductividad requerida para los procesos de electroerosión o EDM.
El mercado de los filamentos conductores es un mercado inmaduro, pero con un alto potencial. Hasta la fecha, los filamentos eléctricamente conductores se encuentran limitados por factores como la conductividad eléctrica, costes elevados, fragilidad, bajo punto de fusión, etc. Un estudio de la competencia ha determinado que la formulación de PVDF es la formulación con mejor desempeño en el mercado.
El miembro del consorcio que ha desarrollado los filamentos basados en PVDF es la empresa Add North 3D. Esta organización tiene como objetivo implementar esta nueva formulación de PVDF entre su gama de productos una vez los materiales obtengan el mejor rendimiento. Esta empresa es la única fabricante de filamentos en los países nórdicos y la primera en obtener filamentos eléctricamente conductores aptos para su implementación en el mercado en cuanto los resultados así lo establezcan.
Nils Åsheim, co-fundador de Add North 3D explica que “Un análisis de los competidores ha demostrado que el nuestro es el único filamento conductor polimérico de grado técnico”. Ellos se adscribieron al proyecto considerando que “el mercado de los filamentos conductores está bastante inmaduro, pero tiene un gran potencial. Esta formulación ya ha alcanzado el mercado del apantallamiento electromagnético. Este es un mercado muy prometedor”.
3. Validación del proceso de EDM: determinación de la estrategia VDI de los materiales
Los ensayos de EDM llevados a término por Tibi han demostrado que el mejor marcado se produce con la estrategia más baja. Por ello, el objetivo es encontrar un conjunto de valores VDI específicos para los materiales de LS ensayados.
Para ello, la Universidad de las Palmas de Gran Canaria (ULPGC) ha testado una metodología para optimizar los parámetros de procesado de EDM. Esta metodología se aplica sobre electrodos y cobres de la misma tipología y en base a estrategias de VDI estándar bajas. A partir de este análisis se seleccionaron las variables a estudiar y sus límites y se aplicó un diseño factorial de experimentos completo.
Después de las pruebas de electroerosión de cada muestra, se calcula la rugosidad (y el VDI resultante), el desgaste del electrodo y la eliminación de material (tasa de arranque de material). Así, con la consecución de todos los datos experimentales, se puede aplicar una metodología de optimización basada en métodos de interpolación y algoritmos genéticos para seleccionar la mejor combinación de parámetros de acuerdo con el objetivo y las limitaciones deseadas. Esta metodología se aplicará en los nuevos materiales y electrodos desarrollados en el proyecto.
En su aplicación a electrodos estándar sobre pletina estándar, se llevó a cabo la optimización con diferentes variables discretas y manteniendo un VDI bajo previamente establecido. Los resultados determinaron las mejores estrategias del diseño de experimentos en función de los objetivos y establecidos, como minimizar el desgaste o maximizar el arranque de material, sujeto a mantener el VDI por debajo del valor establecido.
Por último, también se optimizó la mayor relación de arranque de material frente a desgaste del electrodo, normalizando ambos términos para obtener valores cercanos a uno y darles así un peso equivalente. La estrategia óptima resultante coincidió con la de mínimo desgaste anterior, por lo que dicha estrategia es la que consigue mayor eficiencia de arranque de material frente al desgaste del electrodo.
Estos datos experimentales a escala laboratorio se están aplicando en el momento actual a escala industrial para su transferencia a este ámbito.
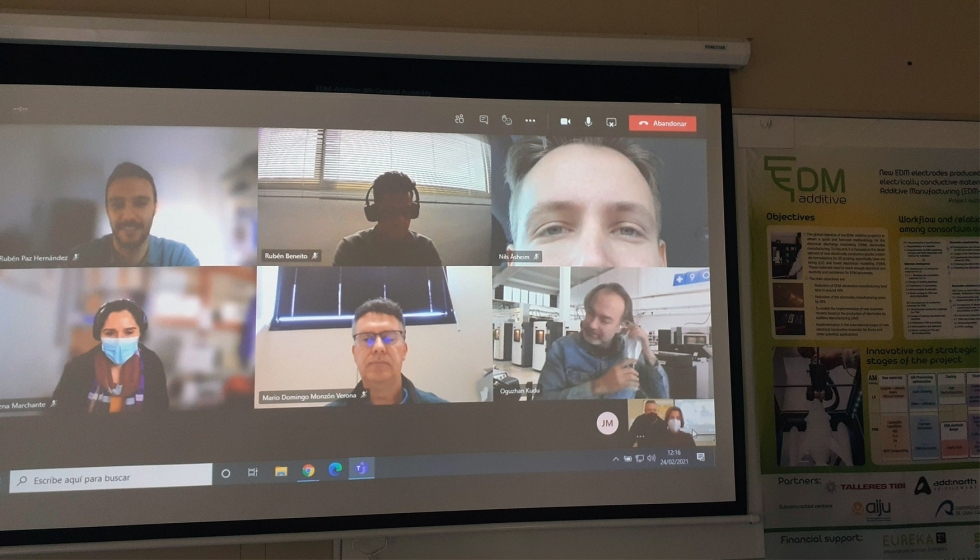
4. Siguientes pasos: recubrimiento de PVD y electrodeposición, ponderación de la tasa de desgaste del electrodo
Para alcanzar la conductividad eléctrica requerida se aplica una estrategia de recubrimiento. En el desarrollo del proyecto, se ha establecido la aplicación de recubrimientos de PVD y electroforming tanto a piezas como a filamentos, para determinar el incremento de conductividad en la aplicación prevista, así como su rendimiento.
Estos recubrimientos se realizan con cobre (Cu) y se prevé que los recubrimientos van a mejorar notablemente el rendimiento de la formulación en las aplicaciones previstas.
Además, también se analizará la tasa de desgaste de estos recubrimientos. De hecho, la ULPGC ha aplicado un electroconformado fino de materiales de Cu estándar para analizar el desgaste de este recubrimiento durante la electroerosión, especialmente en lo relativo a electrodos obtenidos mediante FDM. El objetivo es observar si existe delaminación y desgaste excesivo durante la electroerosión. En las pruebas realizadas se completó el proceso de electroerosión correctamente sin observarse delaminación del recubrimiento. Asimismo, se determinó el papel fundamental que el espesor del recubrimiento tiene para garantizar una mínima vida útil del electrodo obtenido por FDM.
5. Resultados
De las cinco formulaciones desarrolladas hasta la fecha para cada tecnología de fabricación aditiva objetivo, SL y FDM, se han conseguido dos, una para cada tecnología, que ofrecen unos resultados muy prometedores. Estas han mejorado de forma iterativa parámetros como conductividad, facilidad de impresión, precisión dimensional, etc. Se están investigando otros aspectos como el análisis de recubrimientos para alcanzar su aplicación en electrodos de EDM.
Se ha obtenido un hito técnico importante en la ejecución del proyecto, que consiste en la obtención de unos materiales que han alcanzado niveles de conductividad de apantallamiento electromagnético.
Las estrategias establecidas por el consorcio permiten la aplicación de diversas vías paralelas para la obtención de mayor conductividad eléctrica en los materiales objetivo. Estas estrategias parten de las pruebas de EDM realizadas con electrodos simples obtenidos. La re-formulación de los materiales, la densificación de los electrodos y la determinación de una estrategia VDI específica para cada material son factores considerados clave en la obtención de electrodos conductores realizados mediante tecnologías de AM para EDM. Algunas de estas estrategias ya se han aplicado y otras están en proceso de aplicación. Entre estas últimas destacan la aplicación y análisis del rendimiento de los recubrimientos, tasa de desgaste de los electrodos y la tasa de absorción de líquidos.
El consorcio tiene una gran complementariedad y deseos de alcanzar los objetivos del proyecto, motivo por el cual trabaja arduamente en su consecución. TTIBI, como coordinador y líder del mismo, está muy satisfecho con los resultados alcanzados y tiene grandes expectativas en obtener electrodos funcionales para EDM con estos materiales a través de las tecnologías de fabricación aditiva objetivo.
Queda un alentador camino para lograr una mejora en la electroerosión para su aplicación industrial como electrodos, no obstante, el consorcio se siente optimista con este camino a seguir y la superación de los retos que van a tener que afrontarse.
Agradecimientos
Las actividades desarrolladas en el presente artículo han sido llevadas a cabo en el marco del proyecto ‘EDM-Additive: Nuevos electrodos fabricados con materiales eléctricamente conductores mediante fabricación aditiva’, apoyado por el programa Eureka – Smart (expediente S0110) y financiado por el programa del CDTI Innoglobal.
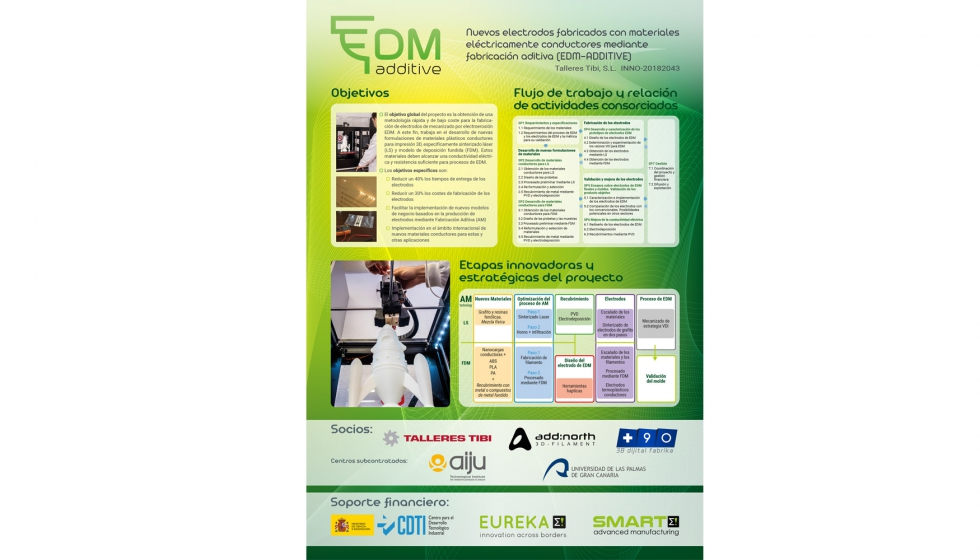