Formación en inyección asistida por ordenador (Fiapo)
Este artículo describe el programa Fiapo, de formación práctica de las características de los procesos de transformación por inyección. Describe el funcionamiento del paquete desarrollado por los autores, y del cual se adjunta una versión demostrativa de las pantallas en una parte de los ejemplares de Plásticos Universales que se distribuyen a transformadores por inyección. No es pues un disquette operativo.
1. Antecedentes
Hace dos años, la Unión Europea, a través de la convocatoria de programas FORCE, apoyó el desarrollo de un proyecto cuyo objetivo era preparar una herramienta de autoformación que permitiera a los trabajadores de las empresas transformadoras de plásticos por inyección comprender los aspectos básicos de esta tecnología de transformación. De esta forma se constituyó una sociedad temporal de interés que ha llevado a cabo estos desarrollos. Esta sociedad estaba formada por los socios ejecutantes Taller de Inyección de la Industria de Plásticos (TIIP) de la Universidad de Zaragoza, School of Polymers de la Universidad del Norte de Londres y por los socios del consejo empresarial y de difusión de la Confederación Española de Empresarios de Plásticos (Anaip), la Chambre de Commerce de Pau, las firmas Pascor, S.A., Dynamit Nobel, S.A. y Eurotech-Manducher.
La herramienta se definió de forma que tuviera unas características parecidas a los juegos de ordenador en que, de forma sencilla, el operador maneja al protagonista decidiendo qué opción debe seguir y, en función de ello, se suceden diversos acontecimientos.
Con este marco se ha llevado a cabo la puesta a punto de dos paquetes o juegos: uno, denominado FIAPO, contempla la globalidad del proceso, en el sentido de que se juzga y se experimenta la bondad de unas condiciones de inyección en función del peso y dimensión de la pieza; otro, denominado Injection Game, muestra los aspectos de las condiciones de inyección en el llenado del molde.
Se describe en este artículo al primero de ellos. Es preciso indicar que, debido a la complejidad de interacciones que existen en el proceso de inyección, se han elegido sólo cuatro parámetros, a fin de no complicar en exceso una herramienta que debe ser accesible y fácil de utilizar con objeto de que sea lo más pedagógica posible.
2. Introducción
La inyección es una tecnología que abarca muchos campos industriales. La producción de una pieza por inyección significa en muchas ocasiones resolver la puesta a punto de un sistema complejo, ya que se interrelacionan parámetros de máquina con materia prima utilizada y diseño de pieza y moldes. Tener una visión de conjunto en la que saber discernir cómo afectan unos cambios de materia prima o de parámetros de inyección a la calidad de la pieza, entendida en primera instancia como peso y dimensión de la misma, es un tema difícil y no siempre bien comprendido. Este juego de ordenador pretende hacer más asequible este problema a cualquier usuario, trabajador, técnico o persona relacionada con la inyección.
Injection Game es una herramienta que, sin necesidad de ningún conocimiento, y a base de equivocaciones que se suceden en distintos escenarios y las rectificaciones que el usuario puede hacer, le hará sentirse protagonista de un proceso de inyección figurado, pero absolutamente real en cuanto a situaciones y datos, y le hará comprender la influencia de los distintos parámetros de inyección en la calidad final de la pieza. Probando y observando las tendencias de peso y dimensión con estos cambios, podrá comprender la interrelación entre los parámetros y la pieza de una forma sencilla.
Como todo juego, tiene sus limitaciones. Por este motivo, no hay que pedirle más que aquéllo para lo que ha sido diseñado. No es pues un manual de soluciones, ni una guía de inyección. Ahora bien: ofrecerá al usuario esta visión de conjunto máquina-material-pieza. Léase el breve manual que sigue antes de empezar a utilizar el juego, con lo que resultará más asequible.
3. Escenarios
Un programa didáctico con unos escenarios deficientes no llenará tanto como ese mismo programa con unos escenarios claros que permitan al usuario centrarse solamente en la labor didáctica pretendida. Se describen a continuación los diferentes escenarios.
3.1. Taller de trabajo (figura 1)
El objetivo de este escenario es el aprovisionamiento del material, los útiles y la documentación a fin de realizar un buen proceso de inyección. Este punto del programa se puede tratar como el punto de unión de los diferentes escenarios que permiten un aprovisionamiento para el proceso de inyección. Figura 1Taller de trabajo. Al fondo, puertas de los recintos.
Al fondo pueden observarse distintas puertas que permiten el acceso a otras dependencias y, en primer plano, una mesa con útiles. Sobre ella se depositarán los distintos utensilios necesarios para realizar el proceso de inyección.
Cada una de las puertas que se encuentran en el fondo de la pantalla tiene un rótulo que indica cuál es su misión. Así, se puede leer "ALMACÉN", "TALLER MECÁNICO", "ARCHIVO" y "LABORATORIO". A través de esas puertas, realizando un doble-click, se accederá a los distintos escenarios.
3.2. Almacén de material (figura 2)
Como se puede observar en la imagen, la misión de esta habitación es almacenar los distintos sacos de material que se ha previsto poder utilizar: ABS, PP y PC. Figura 2 Almacén de materiales. Sacos de ABS, PP y PC.
Para elegir el material deseado se debe hacer un click. Aparecerá una pantalla en la que se ofrecen unas características de material seleccionado. A esta pantalla de características se podrá acceder desde el ARCHIVO.
3.3 Taller mecánico (figura 3)
Consta de los siguientes elementos destacables:
- Molde: componente de la máquina. Ya instalado. Se encuentra en la estantería verde.
- Presurizador: sirve para presionar el plástico fundido. Elemento grande situado en el centro de la pantalla sobre la mesa.
- Contenedor: componente de la máquina. Ya instalado. Se encuentra en la estantería marrón.
- Calentador: sirve para presionar el plástico fundido. Se encuentra sobre la estantería marrón.
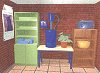
El taller mecánico es un almacén de útiles donde se encuentran todos los aparatos necesarios para realizar el proceso de inyección. El objeto de esos aparatos no es propiamente la construcción de una máquina de inyección, sino la de unir unos elementos cuyas acciones sobre el termoplástico representen lo más exactamente posible las transformaciones sufridas por el material durante el proceso de inyección. Para seleccionar cualquiera de los útiles presentados basta con realizar un proceso de doble-click sobre cualquiera de ellos. Al seleccionarlos aparecerá una pantalla de información sobre cada elemento en particular, indicando cuál es su función principal.
3.4. Archivo (figura 4)
Consta de los siguientes elementos destacables:
- Carpeta PP: presenta las características del PP. Se encuentra en el tercer estante de la librería de la derecha.
- Carpeta PC: presenta las características del PC. Se encuentra en el segundo estante de la librería de la izquierda.
- Carpeta ABS: presenta las características del ABS. Se encuentra en el tercer estante de la librería de la izquierda.
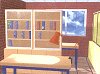
El archivo es el lugar de aprovisionamiento de la información que va a permitir la obtención de las pautas que han de guiar un buen proceso de inyección. El escenario presenta una librería con carpetas, en cuyos lomos están escritos los nombres de los materiales (si bien en la impresión no pueden observarse adecuadamente). Realizando un proceso de doble-click se muestran algunas características del material seleccionado: temperatura de inyección y temperatura máxima que soporta el material, temperatura recomendada del molde, máximo shear stress soportado sin degradarse y máximo shear rate soportado sin degradarse. Además, en la barra de menú superior se puede pedir información sobre las dimensiones de las cavidades del molde con los que se va a realizar el proceso.
3.5. Laboratorio (figura 5)
Consta de los siguientes elementos destacables:
- Calibre: determina la longitud de la pieza. Se encuentra en el tablero de la esquina superior derecha, junto a la sierra.
- Báscula: pesa la pieza inyectada.
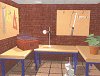
El laboratorio es un escenario al cual se puede acceder desde el taller de trabajo, aunque en este momento no esté permitido operar con él. Su puesta en funcionamiento se realiza cuando, una vez realizado el proceso de inyección, se debe comprobar la calidad dimensional de la pieza. En este escenario se pueden ver diferentes útiles relacionados con procesos de comprobación de dimensiones: una balanza, un calibre, un comparador, unas reglas, etc. A la hora del funcionamiento, se deberá elegir el método de comprobación de la pieza entre la báscula y el calibre, por medio de otro doble-click. A continuación aparecerá otra pantalla en la que se verá cómo se mide o pesa un cilindro o una placa, dependiendo del método que se haya escogido y de la pieza que se esté inyectando.
3.6. Panel de control (figura 6)
Consta de los siguientes elementos destacables:
- Botón pieza: su misión es recordar la pieza que se inyecta.
- Botón material: recuerda el material de inyección.
- Botón analizar: analiza los parámetros introducido.
- Botón inyectar: comienza el proceso de inyección.
- Botón calidad: nos dirige hacia el laboratorio.
- Manómetro: representa la presión ejercida por la máquina durante el ciclo.
Es el escenario principal del programa. En él se han de indicar los diferentes parámetros de inyección con lo que, tras la realización de los correspondientes pasos que se pueden dar dentro de este escenario, se obtendrá la pieza inyectada que, posteriormente, será llevada al laboratorio para realizar el proceso de control de calidad. Al panel de control se puede acceder desde el taller en cualquier momento de la ejecución del programa, independientemente de los elementos que hayan sido seleccionados.
En este escenario se dispone de tres botones que realizan las siguientes funciones:
- Analizar. Con este botón se lleva a cabo un análisis de los distintos parámetros de inyección que se hayan definido en el panel, a fin de que el usuario no introduzca valores inadecuados tales como una temperatura de inyección del material superior a la temperatura máxima soportada por el mismo, etc.
- Inyectar. Con este botón se pone en marcha el proceso de inyección, con las siguientes fases:
- Llenar: proceso por el cual se vierte la granza en la tolva.
- Fundir: la granza se funde a la temperatura de colada indicada por el usuario dentro de los parámetros que rigen el proceso.
- Llenar presurizador: el material plástico fluye, una vez fundido, hasta el presurizador, elemento que controlará la velocidad de inyección.
- Llenado volumétrico: se procede a llenar el molde con la geometría determinada anteriormente mediante el proceso de selección de pieza.
- Compactación: segunda fase del proceso de inyección.
- Calidad. Una vez completado el proceso de inyección es preciso realizar el control de calidad de la pieza. Para ello el programa dirige al usuario al laboratorio en el que deberá elegir el proceso mediante el cual comprobará si la pieza se ciñe a lo requerido.
En función de los resultados obtenidos se efectuará una variación de los parámetros de inyección hasta encontrar aquéllos con los que la pieza haya resultado correctamente inyectada.
Además, realizando un proceso de doble-click sobre el manómetro que marca la presión realizada por el presurizador, se puede ver un gráfico en el que se representa la variación de la presión con el tiempo de ciclo, presentándose en color rojo durante el tiempo de inyección y en color azul durante el tiempo de segunda fase. Obsérvese que el valor reflejado en el reloj es el 50% del valor medido en el presurizador.
4. Modo de operación
Una vez elegido el problema a resolver (de entre los dieciséis posibles cambiando material, tipo de pieza, dimensión y peso de la misma, que es el objetivo a alcanzar) y habiendo resuelto los pasos previos que conducen al montaje de la máquina, se procede a seleccionar los parámetros de inyección (también figura 6). Éstos son:
- Temperatura de material: 260C
- Tiempo de inyección: 3 s
- Presión mantenimiento: 100 bar
- Tiempo de enfriamiento: 5 s
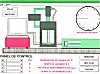
El sistema procede a analizar los parámetros introducidos. Si son correctos, el texto del botón de inyectar adquirirá color negro y estará en condiciones de operar. En este instante se estará ya en condiciones de realizar la primera inyección. Se podrá ver cómo el material se vierte en el contenedor, cómo se funde, cómo pasa el presurizador y a partir de ese momento cómo llena el molde. En ese instante, si se observa el manómetro, se verá cómo va marcando la presión de inyección. El material dentro del molde adquiere color rojo. Pasados unos instantes el presurizador volverá a empujar al material, y entonces el polímero que se encuentra dentro del molde cambiará de color a un rojo más oscuro (figura 7). Ese cambio de color se debe a la compactación del material. Realizando un doble-click sobre el manómetro se podrá ver la variación de presiones a lo largo del ciclo. El tiempo de representación es la duración de la primera fase del proceso de inyección más los 10 segundos que dura la fase de compactación.
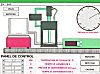
Una vez realizada la inyección de la pieza, el botón que indica calidad habrá cambiado de color claro a oscuro, de forma análoga al botón de inyectar. Entonces, al pulsar ese botón, el sistema dirigirá al usuario al laboratorio, pero previamente dará un aviso de qué es lo que hay que hacer en él. Este aviso dice que hay que elegir entre la báscula y el calibre para ver calidad de la pieza. Una vez dentro del laboratorio se elige en este caso la báscula. Para ello realizamos un doble-click sobre ella.
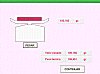
A continuación, el sistema mostrará una pantalla en la que se puede observar una báscula con botones y valores numéricos (figura 8). Al pulsar el botón de pesar, se pondrá en marcha la báscula e indicará el peso de la pieza obtenida y el peso teórico que debería tener. En este caso el peso de la pieza es de 105,155 g mientras el peso teórico es de 106,451 g. Si se pulsa el botón de continuar aparecerá una pantalla en la que se indica que la pieza es pequeña (figura 9). Y al pulsar de nuevo el botón de continuar el programa mostrará una tabla de resultados, que será similar a la siguiente:
Una vez se han visto los resultados escritos en la tabla debe pulsarse el botón continuar. El sistema devolverá al usuario al panel de control. Figura 9Pantalla que indica que los parámetros introducidos en el panel de control no son correctos, y que ello ha dado lugar a una pieza más pequeña de lo previsto.
Ahora es el momento de pensar. Se han dado unas condiciones de inyección que hacen que la pieza sea pequeña. Es decir, su contracción ha resultado ser excesiva. Es pues preciso modificar los parámetros de inyección originales de manera que pueda obtenerse una pieza más grande. Qué parámetros de inyección hay que modificar? A partir de ahí empieza una dinámica de prueba y error hasta ajustar unos parámetros que permiten obtener la pieza deseada, lo que permite ensayar la sensibilidad del proceso a los cambios sugeridos. Al final, una tabla resumen muestra cómo se ha ido convergiendo al resultado apetecido.
5. Conclusión
El programa ha sido probado con más de doscientos trabajadores del sector mostrando su eficacia y su potencialidad como elemento autoformativo.
EXP | T.MAT | T.INY | P.MAN | T.ENF | P.INY | PESO | LONG |
1 | 260 | 3 | 100 | 5 | 109,5 | 105,15 | 489,14 |
1 | 260 | 3 | 100 | 5 | 109,5 | 105,155 | 489,14 |
2 | 240 | 3 | 100 | 5 | 118,2 | 105,185 | 489,29 |
3 | 240 | 1 | 100 | 5 | 133,7 | 105,264 | 489,652 |
4 | 240 | 1 | 175 | 5 | 133,7 | 106,692 | 496,282 |
5 | 240 | 1 | 165 | 5 | 133,7 | 106,501 | 495,398 |
6 | 260 | 1 | 165 | 5 | 123,8 | 106,484 | 495,319 |
7 | 260 | 2 | 165 | 5 | 116,6 | 106,443 | 495,129 |
8 | 250 | 2 | 165 | 5 | 121,3 | 106,45 | 495,161 |
9 | 250 | 2 | 165 | 1 | 121,3 | 106,45 | 495,139 |