La empresa continúa con el desarrollo de los sistemas ExAM 255 y ExAM 510
Relanzamiento de AIM3D tras la fase de consolidación
Tras una fase de consolidación y reorganización de la estructura accionarial, AIM3D, pionera en el campo de las impresoras 3D de granulado desde 2017, vuelve a la carga. AIM3D ha logrado optimizar el proceso patentado Voxelfill. Las pruebas de resistencia demuestran que este proceso puede superar las resistencias no homogéneas de los componentes 3D en los ejes X, Y y Z y, por lo tanto, se acerca a los procesos convencionales como el moldeo por inyección. AIM3D también ha iniciado una cooperación con el proveedor de servicios AM Replique de Mannheim con el objetivo de hacer que el material Ultem 9085 sea más adecuado para la impresión 3D.
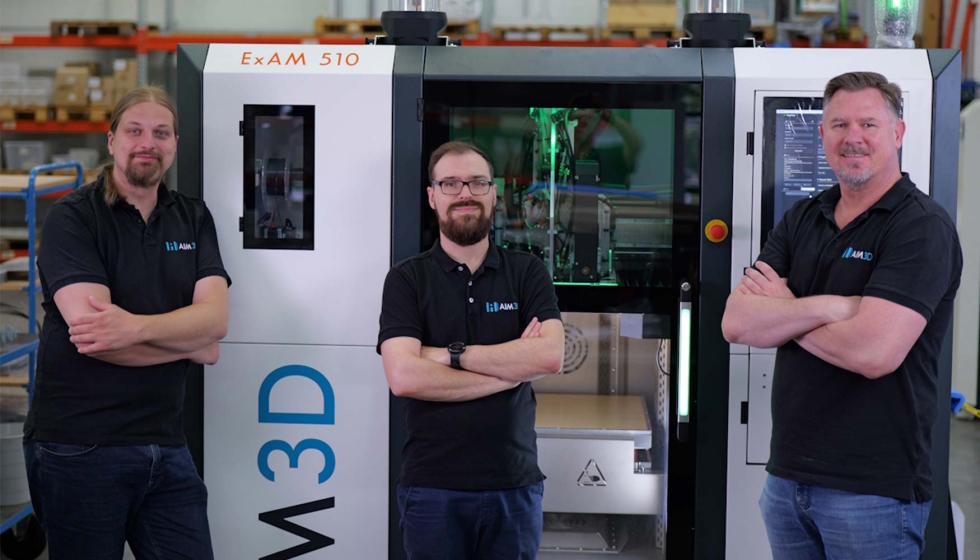
El mercado de los sistemas de fabricación aditiva se caracteriza por una serie de procesos y proveedores que compiten entre sí. La dinámica de las tecnologías modifica constantemente los aspectos de la eficiencia económica y el cálculo del precio de las piezas. Cada nuevo sistema y situación del proceso cambia fundamentalmente las condiciones del mercado. Desde 2017, AIM3D se ha centrado constantemente en las impresoras 3D de granulados en contraposición a las impresoras 3D FDM que procesan granulados con filamentos. Los costes de compra de material significativamente más bajos para los granulados y el uso de material recuperado directamente del molino forman la base de la alta rentabilidad de esta estrategia de producción AM con impresoras 3D de pellets.
Reajuste de las actividades empresariales de AIM3D
Diversos factores provocaron una difícil evolución del mercado durante el segundo semestre de 2023 y un retraso en las inversiones: Los altos costes de la energía, las incertidumbres en el desarrollo empresarial y los procesos de transformación inhibieron las decisiones de inversión en la industria. Un enorme desafío para los proveedores de sistemas de impresión 3D. Dr. Vincent Morrison (CEO): “En este difícil entorno de mercado, no nos fue posible ceñirnos a nuestros objetivos iniciales de desarrollo. Esto dio lugar a una reorganización de la estructura accionarial y a nuevas asociaciones estratégicas. Durante la fase de reestructuración, seguimos satisfaciendo las necesidades de nuestros clientes y continuamos desarrollando nuestra tecnología de impresión de granulados. Ahora creemos más que nunca en nuestra tecnología CEM y en el equipo establecido en AIM3D. Las impresoras 3D de granulado ofrecen la opción única de mapear las propiedades de las piezas fabricadas convencionalmente de una manera muy rentable con una estrategia de fabricación aditiva”. El relanzamiento de AIM3D fue el resultado de una combinación de una nueva estructura accionarial y una compra por parte de la dirección (MBO).
Mayor desarrollo de la impresión 3D de pellets en AIM3D
Parte de la reorientación de AIM3D se centró en asociaciones estratégicas con empresas que aportan conocimientos especiales. Por un lado, una cooperación con la empresa de desarrollo de software Create it Real de Dinamarca tiene como objetivo optimizar la estrategia Voxelfill para superar las fuerzas no homogéneas con respecto al control del proceso basado en la solución de software de rebanado establecida SlicEx. Por otro lado, Replique de Mannheim, un proveedor de servicios completos de AM, apoya la optimización de las aplicaciones Ultem con su experiencia y plataforma de impresión 3D. AIM3D también ha anunciado nuevas colaboraciones estratégicas y la validación de nuevos materiales para 2024.
Clemens Lieberwirth, director técnico, explica: “En el período previo al relanzamiento de AIM3D, continuamos persiguiendo nuestros objetivos de desarrollo para la impresión 3D de pellets: Mejora de la rentabilidad, refuerzo de la independencia del material, mayor calidad, capacidad de carga de componentes, reproducibilidad y estabilidad del proceso”. El sistema ExAM 510 de AIM3D está predestinado para su uso en la producción industrial. El sistema ExAM 510, que se lanzó en 2022, funciona actualmente a una velocidad de construcción máxima de 150 cm³/h. Según el fabricante, el objetivo es alcanzar con el tiempo tasas de construcción de 300 a 600 cm³/h. Con ello, podrían alcanzarse volúmenes de procesamiento de 1.000 a 4.000 kg al año (todos los datos se refieren a componentes con un grosor de capa máximo de 150 µm y el uso de una boquilla de 0,4 mm en la impresora 3D y, por tanto, son comparables a los componentes 3D de modelado por deposición fundida (FDM)).
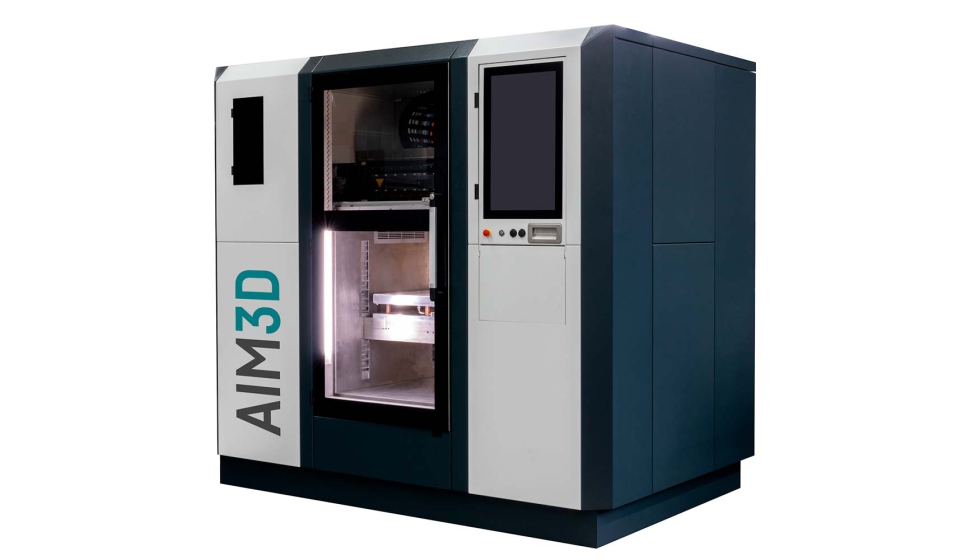
Mejora de la reproducibilidad de las aplicaciones Ultem con una impresora 3D de granulado
Pero, sobre todo, el factor decisivo para la construcción de un componente 3D es la reproducibilidad, es decir, la repetibilidad del proceso. Para un usuario, este es un punto clave para garantizar una calidad constante del componente, especialmente en la producción en serie de lotes pequeños y medianos. Los componentes de la tecnología de moldeo por inyección y los componentes impresos en 3D muestran homogeneidades de material comparables cuando se utiliza el granulado Ultem 9085. Así lo demuestran los últimos ensayos de tracción conforme a la norma DIN EN ISO 527-2 Tipo 1A, que confirman las bajas desviaciones estándar y, por tanto, una elevada estabilidad del proceso. Esto se consigue principalmente gracias a la tecnología patentada del extrusor de pellets, que garantiza un procesamiento cuidadoso del material y minimiza la degradación de los polímeros en el extrusor.
La impresión 3D de pellets abre nuevas áreas de aplicación para el material Ultem 9085
La impresión 3D de pellets con Ultem 9085 permite aumentar significativamente el potencial de tiempo de comercialización tanto para prototipos como para componentes de serie. Los extrusores y la tecnología de AIM3D también logran mejores calidades de superficie con el mismo tiempo de construcción. Esto es posible porque el uso de granulados permite mayores velocidades de construcción incluso con espesores de capa más bajos. El objetivo para el futuro es realizar soluciones para boquillas más finas por debajo de 0,4 mm, de modo que se pueda ampliar aún más el espectro para componentes fabricados con Ultem 9085.
Además de las ventajas en términos de coste y tiempo, el proceso CEM también abre nuevas áreas de aplicación para Ultem 9085 en general. Además de las aplicaciones aeroespaciales clásicas, Ultem 9085 también es adecuado para su uso en la tecnología automotriz y ferroviaria. Un ejemplo de ello es la sustitución de conjuntos complejos de chapa metálica en el área de ventilación, como se ha llevado a cabo en cooperación con Replique y Alstom. Es decir, allí donde se exigen las máximas prestaciones mecánicas y térmicas y un componente 3D debe garantizar unas propiedades mecánicas duraderas desde el punto de vista de la seguridad. Max Siebert, director general de Replique: “El uso de una impresora 3D de granulado no sólo hará que las aplicaciones existentes sean más rentables en el futuro. De hecho, veremos nuevas aplicaciones 3D de Ultem 9085, que no eran económicamente viables en el pasado. Se abren nuevos horizontes, especialmente en el sector aeroespacial”.
Innovador y disruptivo: el principio Voxelfill supera las propiedades de resistencia no homogéneas
En la fabricación aditiva de polímeros, los componentes tienen propiedades de resistencia no homogéneas debido al proceso de construcción basado en capas. Esto se manifiesta principalmente en forma de deficiencias de resistencia a la tracción y a la flexión, así como en un comportamiento muy frágil a lo largo del eje Z. Por el contrario, las resistencias alcanzadas a lo largo de los ejes X e Y con algunos procesos ya se aproximan a las resistencias posibles con el moldeo por inyección convencional. AIM3D ya lo ha demostrado con el procesamiento tanto de componentes rellenos de fibra basados en material PA6 GF30 como de termoplásticos puros como Ultem 9085. El fenómeno de las propiedades de resistencia no homogéneas debe resolverse para permitir una amplia aplicabilidad de los componentes impresos en 3D. Mediante el uso de la tecnología de extrusión 3D del proceso CEM, AIM3D ha desarrollado una estrategia Voxelfill que supera estas limitaciones y aumenta la rentabilidad del proceso CEM. Voxelfill también puede utilizarse para componentes multimaterial y, en general, es adecuado para construir componentes 3D utilizando plásticos, metales y cerámica. Clemens Lieberwirth, CTO de AIM3D: “Con el desarrollo de Voxelfill, el usuario tiene ahora la posibilidad de utilizar el nuevo proceso único de Voxelfill para mejorar la resistencia z y la velocidad de impresión. Por ello, seguimos desarrollando esta tecnología de forma constante”.
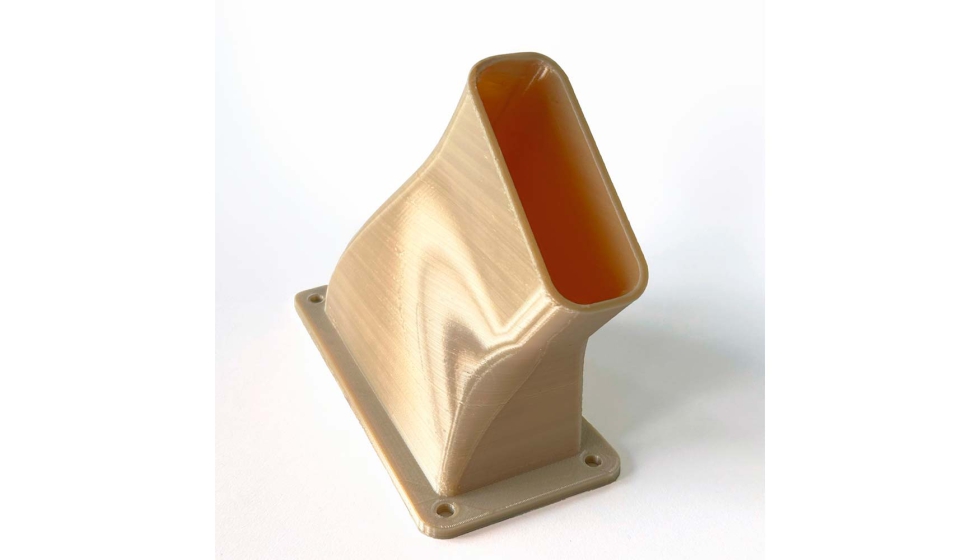
Un vistazo al potencial de Voxelfill
Las variaciones de la estrategia Voxelfill con el proceso CEM permiten el uso de diversos materiales: se hacen posibles soluciones híbridas multimaterial con diferentes materiales Voxelfill y diferentes materiales para el contorno o la estructura de las paredes interiores. De este modo, las propiedades de los materiales pueden “personalizarse”. El peso definido de los componentes, las propiedades de amortiguación, la elasticidad o los cambios en el centro de gravedad pueden adaptarse a la aplicación. Rellenando selectivamente sólo determinadas cámaras de volumen (densidades selectivas), las propiedades de los componentes podrían verse influidas de forma específica sobre la base de simulaciones FE. Con Voxelfill sólo es posible rellenar las zonas de un componente que son absolutamente necesarias para el flujo de fuerzas. Como resultado, desde el exterior, estos componentes parecen piezas convencionales y también pueden beneficiarse de la aplicación de procesos de acabado convencionales.
Al mismo tiempo, sin embargo, el proceso de impresión 3D se lleva a cabo con material y peso reducidos, hasta realizar componentes ligeros. Especialmente cuando se emplean materiales reforzados con fibras, el uso de Voxelfill ofrece una opción adicional para alinear específicamente las fibras en el componente con el fin de mejorar las propiedades mecánicas. En el plano plano, el proceso CEM ya ofrece muy buenas opciones para controlar la orientación de las fibras. Con la estrategia Voxelfill, esto afecta al contorno y a las paredes interiores del componente. Al inyectar el material en las cámaras de volumen (rellenando los voxels), el componente 3D también recibe fibras alineadas en el eje Z, lo que mejora aún más las propiedades mecánicas. Clemens Lieberwirth, CTO de AIM3D: “Por supuesto, el proceso Voxelfill es especialmente adecuado para la impresión 3D de plásticos y plásticos rellenos de fibra, pero también lo es para la impresión 3D de componentes metálicos y cerámicos mediante el proceso CEM. En general, se obtienen ventajas gracias a la mayor velocidad de construcción y al relleno de capas cruzadas”.