Acabado eficiente y completamente automático de los canales internos impresos en 3D
La fabricación aditiva permite la integración de canales de refrigeración internos colocados con precisión en los componentes. Con el enfoque en el posprocesamiento automatizado —eliminación de polvo residual y alisado de la superficie de estos canales— los departamentos de Ingeniería Mecánica y Química del Politécnico de Milán (Italia) junto con Rösler Italiana S.r.l. llevaron a cabo un estudio con los métodos de tratamiento de superficie acabado en masa, granallado y acabado en masa con soporte químico. Los resultados demostraron claramente que con los tres métodos se podía lograr una mejora significativa de la calidad general de la superficie.
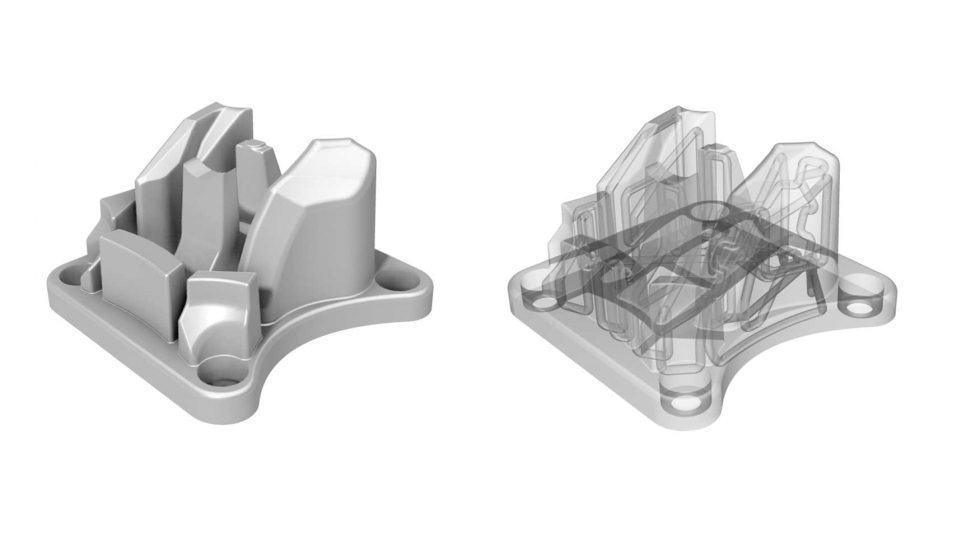
Fusión láser selectiva: forma perfecta pero alta rugosidad de la superficie
Por consiguiente, la elección del sistema de acabado de superficies más adecuado es fundamental para la vida útil de un componente y la eficiencia general de un sistema. Una opción para suavizar las superficies externas e internas de los componentes fabricados aditivamente es el acabado en masa. Durante el proceso de acabado, las piezas de trabajo se sumergen en un recipiente de trabajo circular lleno de medios de procesamiento especiales. Además, durante el proceso se añaden compuestos especiales. La vibración de la cubeta de trabajo hace que los medios y las piezas de trabajo se muevan alrededor de la cubeta en un movimiento espiral. El constante ‘frotamiento’ de los medios contra las piezas de trabajo produce un efecto de molienda/alisado que resulta en la calidad de la superficie deseada.
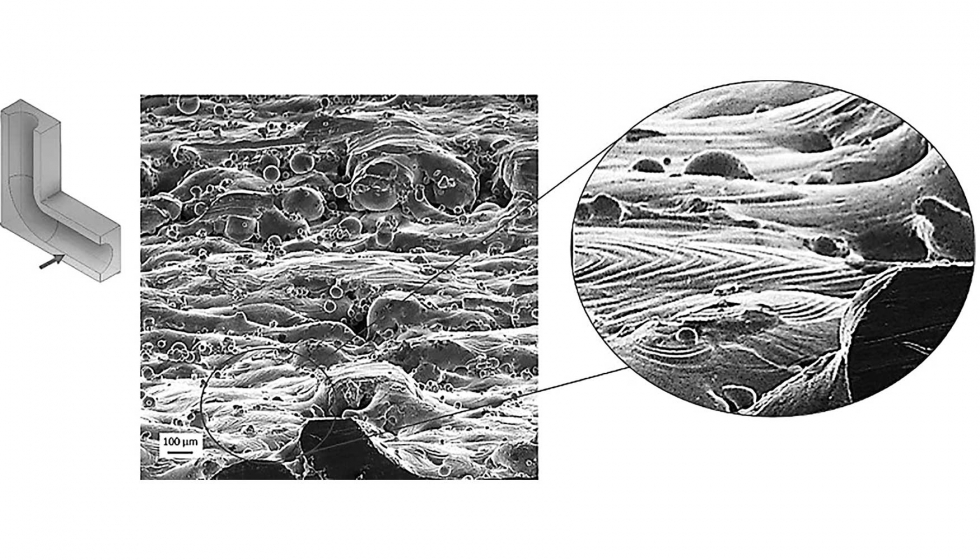
El método de impresión en 3D de SLM es ideal para la fabricación de componentes de herramientas. Sin embargo, su superficie, incluyendo los pasajes internos, contiene polvo residual del proceso aditivo y muestra una alta rugosidad inicial. Por eso, los componentes fabricados aditivamente deben pasar por una etapa de posprocesamiento adecuada. Foto: Rösler Italiana S.r.l.
El acabado en masa permite el alisado eficiente de las áreas de superficie de los canales internos
Para evaluar los diferentes métodos de tratamiento, entre ellos el acabado en masa, para el alisado de las superficies externas e internas de los componentes impresos en 3D, los departamentos de Ingeniería Mecánica y Química del Politécnico de Milán (Italia), junto con Rösler Italiana S.r.l., realizaron un estudio exhaustivo. Esto supuso el tratamiento de piezas de diferentes formas y pasajes internos de diferentes diámetros (3, 5, 7,5 y 10 mm) con acabado en masa, granallado y acabado en masa con soporte químico. Los tres sistemas de tratamiento de superficies produjeron resultados sorprendentemente similares. El acabado en masa convencional y la granalladura eliminaron sistemáticamente los picos de rugosidad y produjeron perfiles de rugosidad superficial similares. Sin embargo, los mejores resultados se lograron con el acabado en masa apoyado químicamente: las piezas de trabajo tenían la superficie más lisa, como se muestra en las lecturas de rugosidad superficial comparativamente más bajas, y mostraban el típico acabado acelerado químicamente. Con valores de Ra de 0,7 µm, el método de acabado en masa apoyado químicamente produjo no sólo los valores más bajos de rugosidad superficial, sino que también requirió el tiempo de ciclo más corto. Los resultados también mostraron que los valores finales de rugosidad eran más o menos idénticos en los pasajes internos verticales y horizontales.
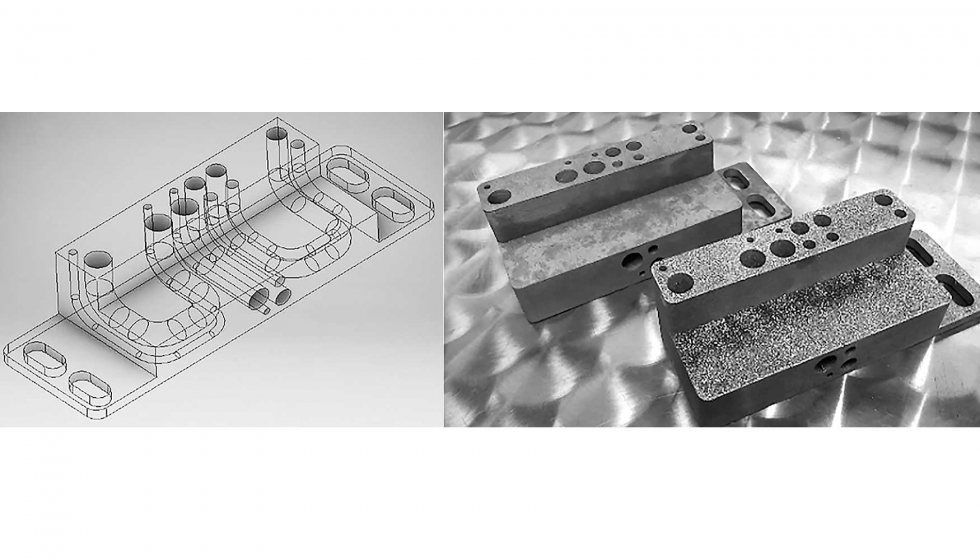
Los ensayos se realizaron con diferentes geometrías que contenían pasajes interiores con diámetros de 3, 5, 7,5 y 10 mm. Foto: Rösler Italiana S.r.l.

Considerando la estructura de la superficie de los pasajes internos y la alta rugosidad inicial de la superficie de los componentes tridimensionales, los ensayos mostraron claramente que el método de acabado en masa apoyado químicamente produjo los mejores resultados de acabado. Foto: Rösler Italiana S.r.l.
Proceso completamente automático en una sola máquina
El desarrollo ulterior del actual sistema M3 no sólo permitirá el tratamiento eficaz y específico de los pasajes internos en el futuro, sino que también será un sistema totalmente automatizado para el acabado coherente de los componentes impresos en 3D sin necesidad de trabajo manual. Por supuesto, la carga y descarga de las piezas de trabajo también puede automatizarse con un robot. La dosificación precisa de los medios de molienda y del compuesto con una reposición especial, respectivamente, el sistema de dosificación y la función ‘Start’ del equipo también están totalmente automatizados. Dependiendo de los requisitos de acabado de la superficie, se pueden ejecutar varios procesos de esmerilado y pulido en secuencia. Después de la descarga automática de los medios de trabajo del recipiente de trabajo, las piezas de trabajo tratadas se retiran del dispositivo de sujeción. Si es necesario, se puede añadir una etapa de limpieza y secado separada, por supuesto, también totalmente automatizada. Lo mismo ocurre con la manipulación de las piezas de trabajo, incluida la transferencia a las etapas de fabricación posteriores. Los controles del sistema permiten el almacenamiento y la llamada de múltiples programas de procesamiento específicos para las piezas de trabajo. Los parámetros de proceso para las distintas piezas de trabajo pueden seleccionarse simplemente pulsando un botón o con un sistema de reconocimiento de piezas de trabajo.
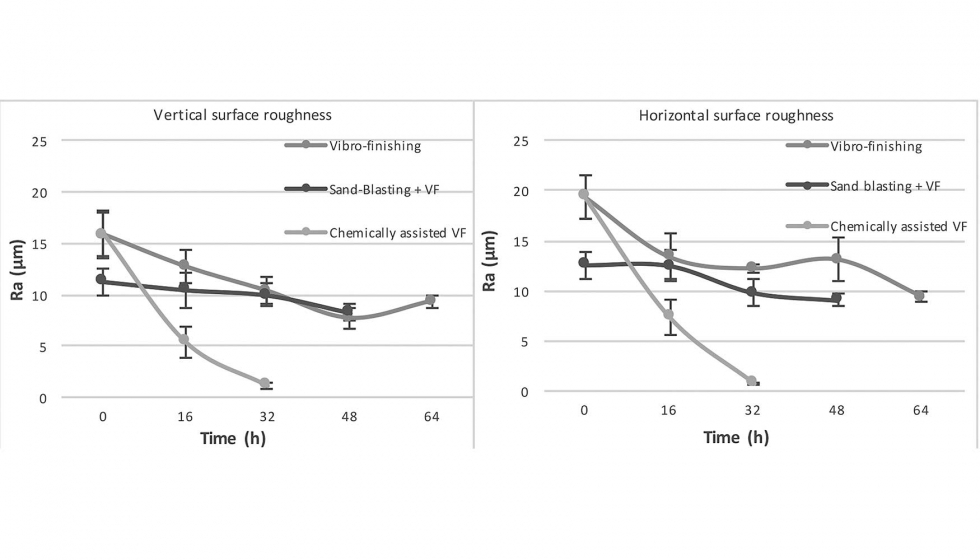
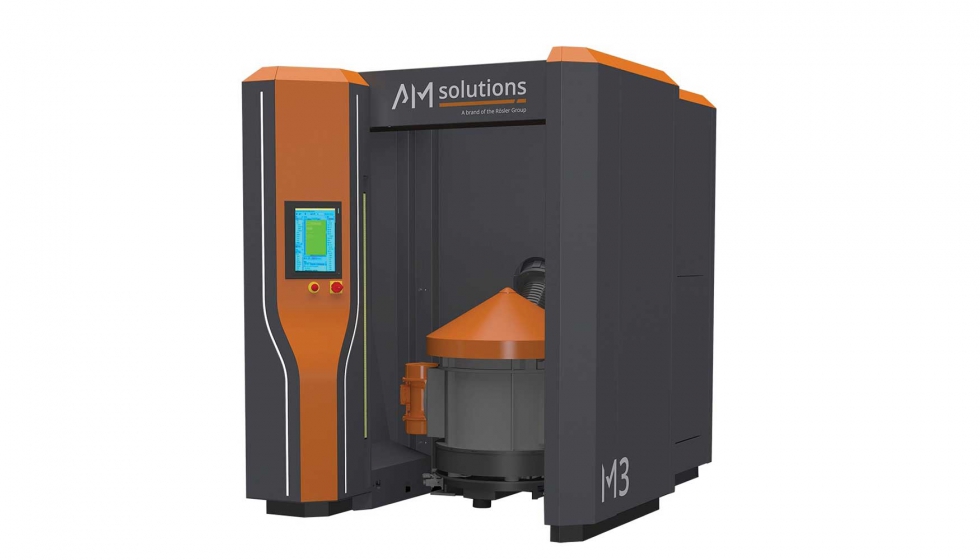