Renishaw muestra sus soluciones aditivas en la instalaciones de Optimus 3D
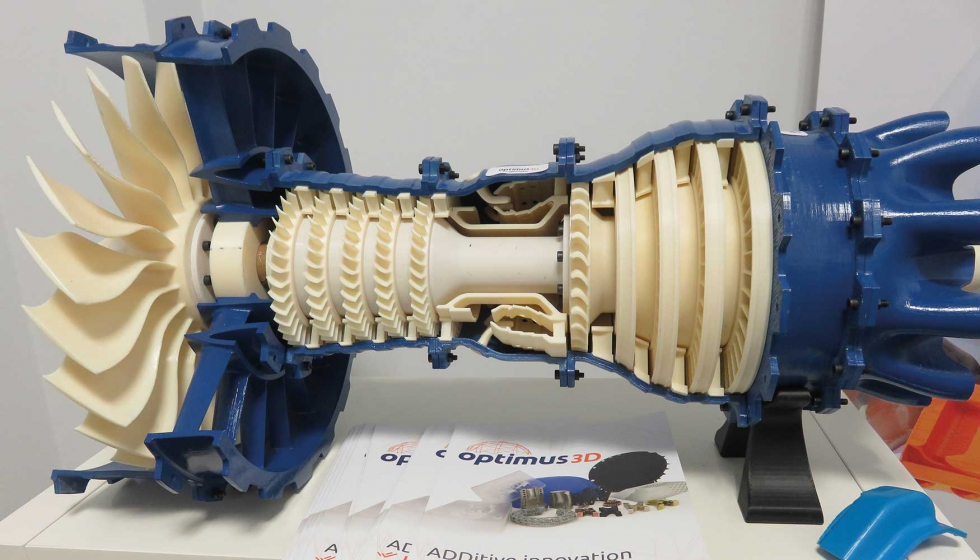
El pasado 8 de marzo Renishaw y Optimus 3D organizaron una jornada bajo el título ‘Reflexión sobre las verdaderas posibilidades de la fabricación aditiva industrial’ en las instalaciones de Optimus, situadas en el Parque Tecnológico de Álava.
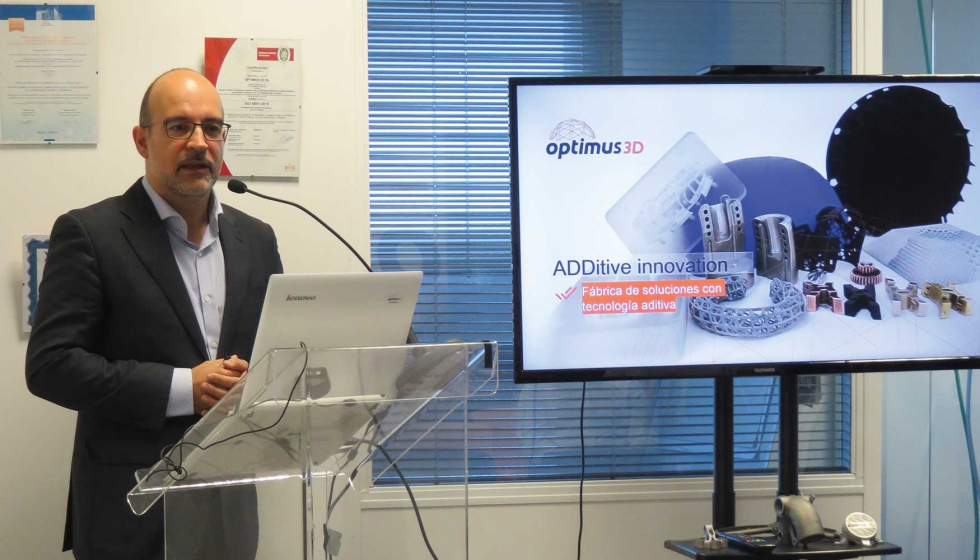
Fernando Oharriz, CEO de Optimus 3D, explicó la actividad de esta empresa, “una fábrica de soluciones en el mundo de la aditiva”. Habló de la cantidad de materiales que utilizan con estas técnicas e informó sobre las diversas máquinas y soluciones que existen para la impresión 3D destinada a todo tipo de sector. “Nuestro know how —afirmó— nos permite condensar toda esta información para acercarla con más facilidad a los usuarios. Optimus 3D es un partner tecnológico que acelera e implementa la fabricación aditiva para la industria. Llevamos cinco años aquí, tras una larga experiencia en grandes empresas en las que descubrimos el potencial de la fabricación aditiva. En 2017, RPK entró a formar parte de la empresa y esto nos permitió realizar más inversiones, tener presencia internacional y utilizar su centro tecnológico”.
Según explicó Oharriz, Optimus 3D se sustenta sobre pilares como la cercanía con el cliente, la rapidez, el trabajo integral con soluciones llave en mano y las máquinas de primer nivel, como Renishaw. Todo ello con las piezas de serie como objetivo. Cuentan con equipos para FDM (Stratasys), Polijet (Stratasys), estereolitografía, SLM Metal Laser (Renishaw) y Multijet Fusion (HP). “También estamos trabajando con una nueva tecnología FFF que parte de granza y no de filamento, que adquiriremos próximamente. Otra tecnología a la que nos estamos acercando es la tecnología Clip (tecnología de proyección digital para carbonos). Tras la explicación de los servicios que presta Optimus 3D, como la fabricación, la ingeniería (optimizan la topología de la pieza y reducen la cantidad de materia prima) y la consultoría/formación, el CEO de la empresa hizo un repaso de sus trabajos más representativos.
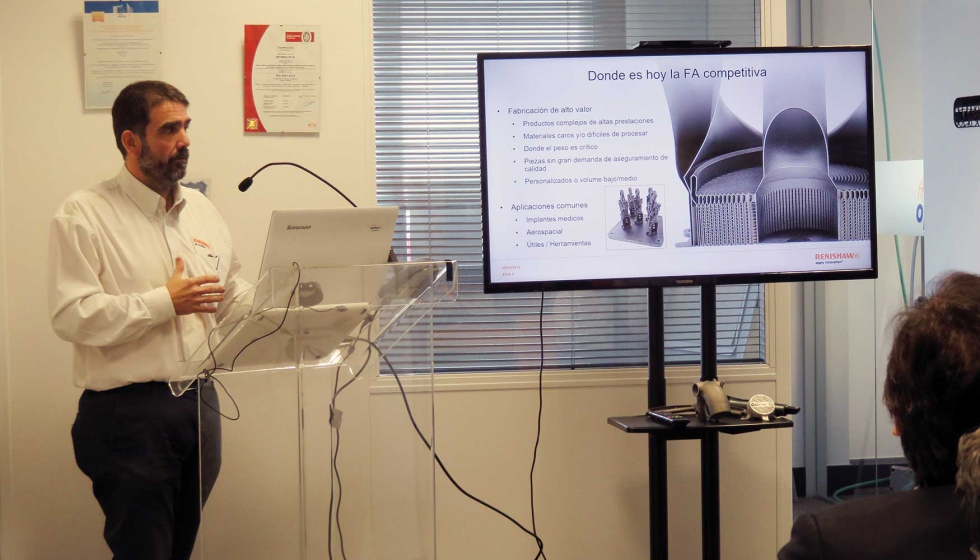
Iñigo Bereterbide (Renishaw). “En 2020 se estima que el 0,1% del mercado total abarcable de la fabricación se realizará mediante técnicas aditivas”.
El turno de Renishaw
A continuación tomó la palabra Iñigo Bereterbide, product manager Additive Manufacturing de Renishaw, quien habló sobre los nuevos retos de la fabricación aditiva y destacó como fundamentales el aumento de la productividad y la reducción del coste por pieza. Según dijo, en 2020 se estima que el 0,1% del mercado total abarcable de la fabricación se realizará mediante técnicas aditivas. “Su crecimiento -explicó- vendrá traccionado por la demanda (clientes que usen de forma cada vez más inteligente la fabricación aditiva y creando productos de más valor) y por la oferta, que tendrá que crear innovaciones en tecnología y proceso para que estas técnicas sean competitivas y puedan fabricar, en calidad y precio, lo que demanda el mercado”.
Los asistentes a la jornada pudieron escuchar que los implantes médicos, el sector aeroespacial y los utillajes son los tres campos importantes actuales para la fabricación aditiva.
Como destacó Bereterbide, la técnica aditiva tiene también sus limitaciones o barreras para un crecimiento más acelerado. Señaló entre ellas el estrés residual, la validación de la calidad y el coste por pieza. “Renishaw se encuentra ahora trabajando en ellas y hoy nos centramos en cómo aliviar el coste por pieza. Si en la fabricación convencional cuando sube el volumen de producción el coste unitario baja, eso no es tan claro en la aditiva. Si conseguimos reducir el coste por pieza se abrirá mucho el nicho”.
La muestra de piezas fue uno de los momentos clave de su presentación. Uno de los ejemplos mostrados fue el de una pieza para bicicleta de monte, con la que explicó cómo reducen el coste de la fabricación recurriendo a multi láser, la reducción de los postprocesos y la mayor automatización para reducir tiempos de mano de obra, por ejemplo en carga y descarga de material. Relacionó todo ello con la máquina de Renishaw Quad laser, cuyo precio es más elevado, pero que consigue un aumento de la productividad de más del 200 o 300%, en función de la pieza. Según dijo, “en algunos casos el coste de la fabricación se puede reducir a la mitad”.
En opinión de este experto de Renishaw, la fabricación aditiva va a dejar de tener la barrera del coste por pieza y pasar a fabricaciones más masivas. Para que esto sea posible, la industria debe poner sobre la mesa productos que estén pensados para ser fabricados con esta tecnología y que rompan con las inercias y reticencias que hay en la industria. “La fabricación aditiva va a cambiar el mercado, se va a generalizar y las tres barreras citadas antes se van a ir derribando”.
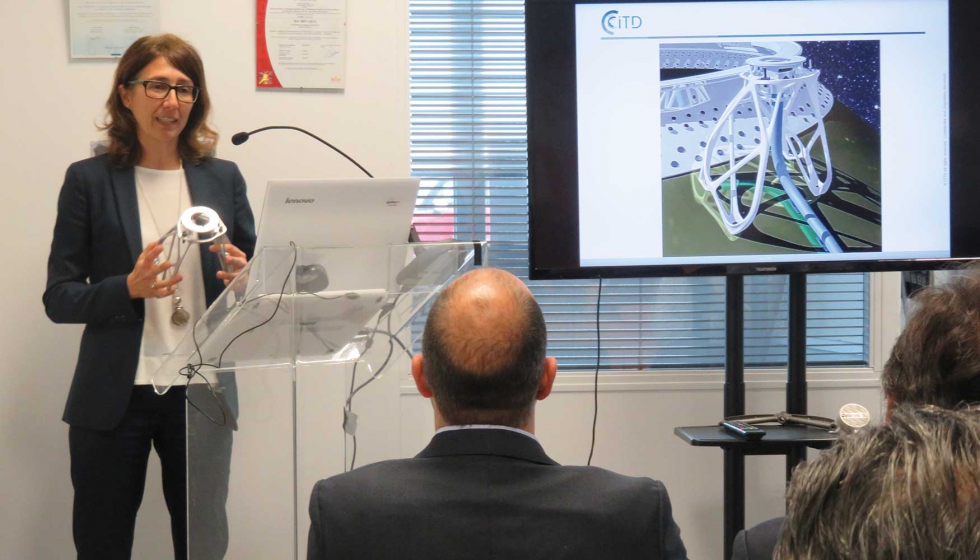
CITD: la fabricación aditiva como solución
Marta García-Cosido, de la ingeniería de diseño y cálculo de sistemas y estructuras CITD HO Engineering& Additive Manufacturing, fue la encargada de cerrar la jornada. Basó su presentación en el camino tomado por la fabricación aditiva en el sector aeroespacial. Según García-Cosido, “la fabricación aditiva tiene muchas bondades, pero hay que vencer muchas resistencias y hay que ser conscientes de las limitaciones de esta tecnología”.
En el sector aeroespacial, especialmente en el espacial, la reducción del peso de una pieza, es un éxito. “¡Un kilo es carísimo en el espacio!”.
Centrada en las aplicaciones metálicas, CITD cuenta con máquinas Renishaw en sus instalaciones. Tal y como explicó, “para nosotros diseñar para la fabricación aditiva significa identificar la oportunidad y acompañar a la pieza hasta su calificación final. El control del proceso es muy importante, desde el material hasta la calificación de la pieza. El postprocesado también debe tenerse en cuenta desde el primer diseño de la pieza”.
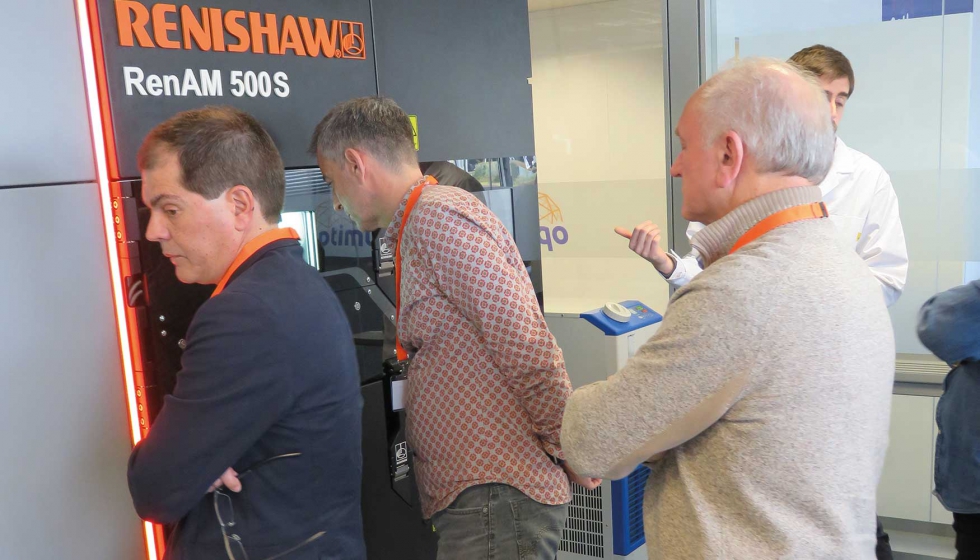