Freeformer produce componentes de avión con materiales originales certificados
Arburg Plastic Freeforming (APF) y Freeformer, de Arburg, permiten la fabricación aditiva de componentes funcionales a partir del material Lexan 940 (PC), aprobado para la industria aeroespacial.
“Las piezas de repuesto funcionales, los implantes médicos y las piezas de repuesto funcionales son sólo tres de las muchas áreas para las cuales nuestros Freeformer y Arburg Plastic Freeforming son la elección ideal”, explica Eberhard Lutz, director de ventas de Freeformer de Arburg. Por ello Arburg abrió recientemente su nuevo Centro de Prototipos en la sede de Lossburg. Eequipado con seis Freeformers, está disponible para la fabricación de piezas de muestra de materiales originales calificados y certificados, lo que significa que sus expertos de APF pueden responder aún más rápidamente a las preguntas de los clientes y producir piezas de muestra prácticamente durante todo el día.
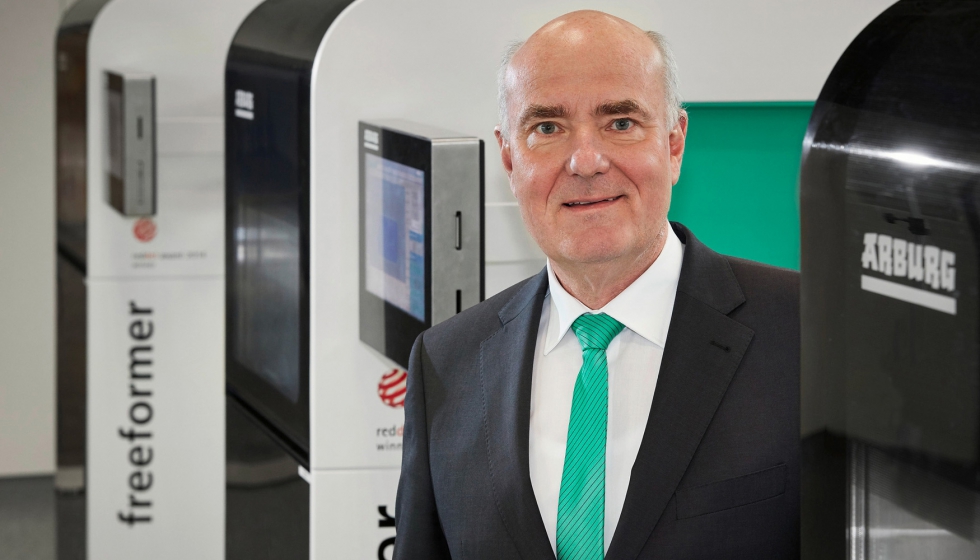
Piezas funcionales hechas de materiales originales calificados
Una de las principales ventajas de Arburg Plastics Freeforming (APF) es la opción para procesar los mismos granulados estándar calificados que se usan para el moldeo por inyección. El Freeformer está equipado con dos unidades de descarga de serie. Esto le permite procesar un componente adicional para fabricar una pieza en diferentes colores, con cualidades táctiles especiales o como combinación dura/suave, por ejemplo. Con el fin de implementar geometrías complejas, las estructuras de soporte se pueden utilizar como el segundo componente. En la Rapid.Tech 2017, que se celebra del 20-22 de junio en Erfurt, Arburg mostrará la producción de los conductos de aire fabricados con el material original PC Lexan 940, autorizado para la industria aeroespacial. Se producirán pequeños lotes de nueve componentes funcionales cada uno en un tiempo de construcción de alrededor de 24 horas.
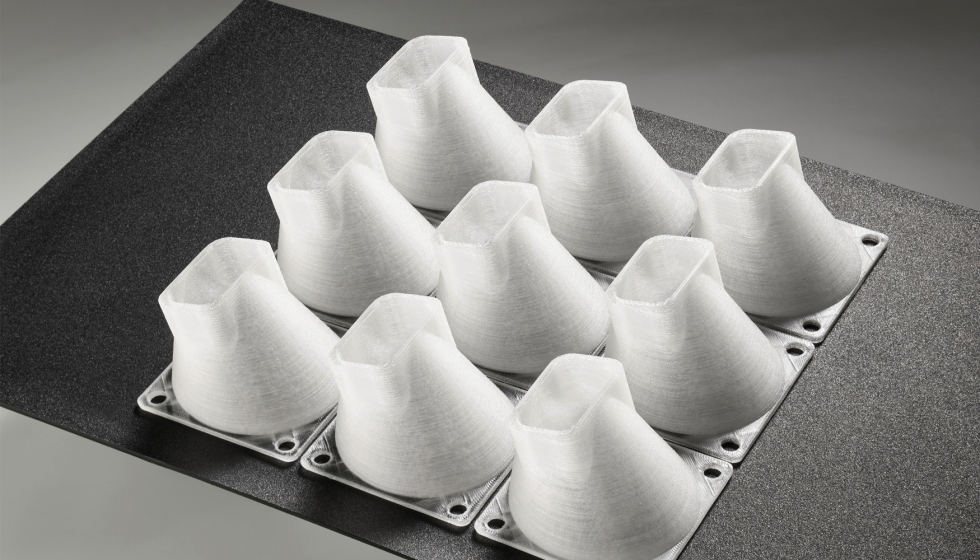
Ejemplo de una aplicación aeroespacial: un Freeformer produce conductos de aire fabricados con PC especialmente aprobados para la industria de la aviación.
Las ventajas del sistema abierto
Freeformer y APF son sistemas abiertos, por lo que los parámetros del proceso pueden optimizarse específicamente para la aplicación correspondiente. Arburg ya ha utilizado muchas piezas de muestra para mostrar cuántas áreas de aplicación pueden ser servidas con el Freeformer, incluyendo:
- Implantes adaptados individualmente hechos de PLA de grado médico que pueden ser absorbidos por el cuerpo después de un período de tiempo definido,
- Conectores PC / ABS a prueba de llama para la industria electrónica,
- Herramientas de montaje, pinzas para automatización y otros equipos, por ejemplo PA en combinación con TPE suave,
- Una polea de cuerda articulada, cuya carcasa y gancho de fijación están fabricados con un robusto Bio-PA (Grilamid).
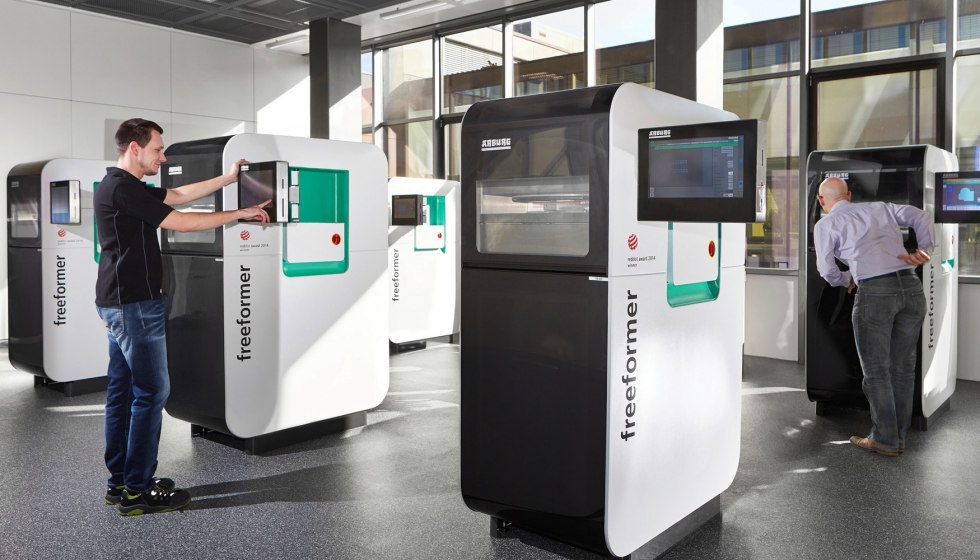
Las piezas de la muestra se producen en seis Freeformers en el nuevo Arburg Prototyping Center en respuesta a las preguntas de los clientes.
Nuevo material de apoyo de Arburg
Además del material de soporte soluble en agua Armat 11, ya está también disponible Armat 21, un material soluble en hidróxido de sodio. Se trata de un material de soporte que se puede procesar con facilidad y es térmicamente estable. Tiene muy buenas propiedades de formación de gotas y adhesión, así como una excelente definición de los bordes en relación con el material de construcción.
Individualización de piezas de gran volumen
Más allá de la fabricación aditiva de piezas únicas y pequeños lotes, las piezas de gran volumen también se pueden mejorar bajo demanda del cliente, incorporándose directamente en la cadena de valor, combinando la fabricación aditiva con el moldeo por inyección y las tecnologías Industry 4.0.