Procesos de fabricación de piezas complejas composites más eficientes
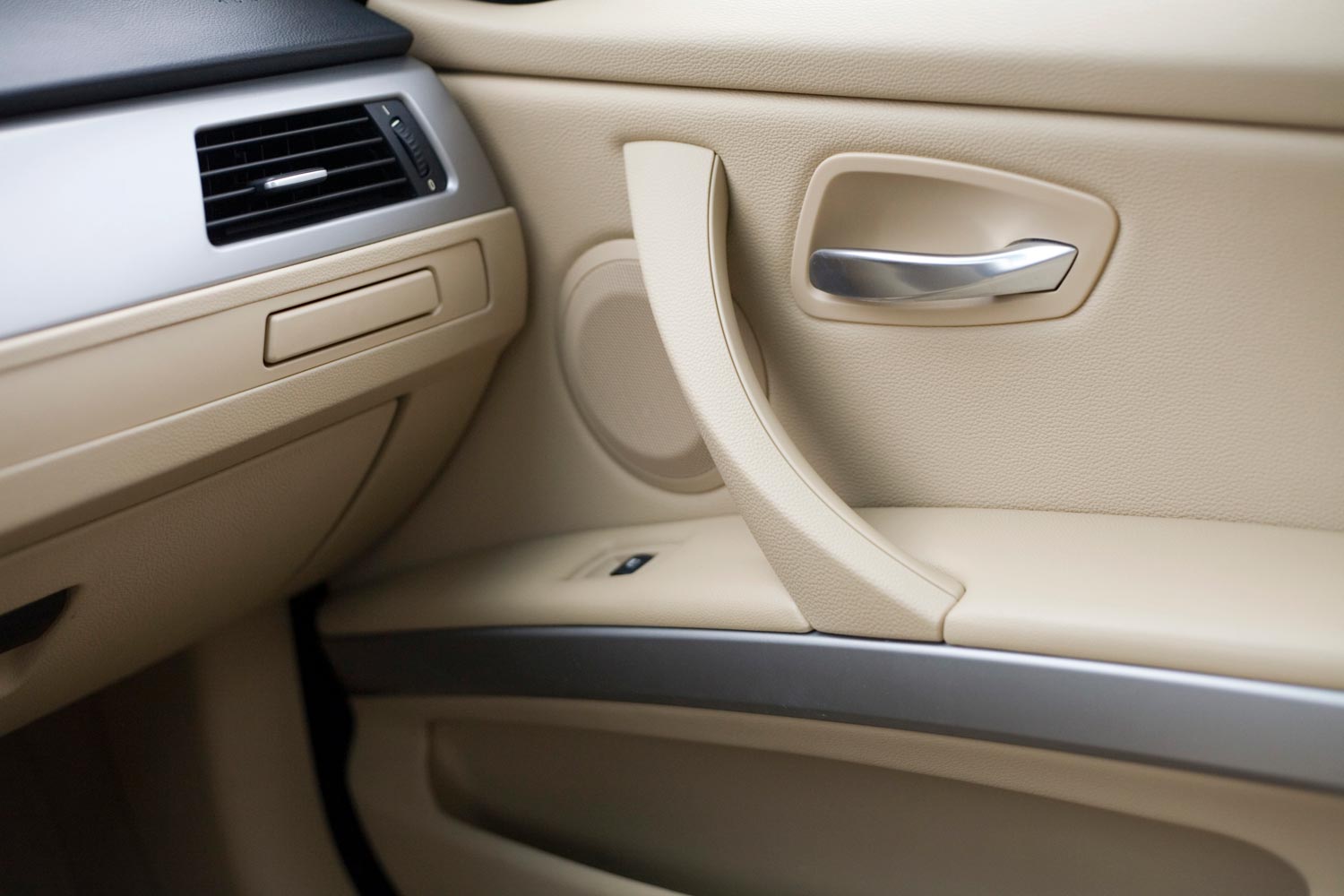
El proyecto Fortape tiene como objetivo estratégico ofrecer soluciones a estos inconvenientes a través del desarrollo de un sistema eficiente e integrado de fabricación de piezas complejas basadas en el uso de tapes unidireccionales para su aplicación en la industria del automóvil y aeronáutica, optimizando el uso de material y energía.
Para conseguir este objetivo global, se han identificado diferentes retos y en consecuencia se plantean las siguientes líneas de trabajo:
1. Desarrollo de un proceso de fabricación eficiente de los tapes unidireccionales de fibra de vidrio y carbono reduciendo el uso de material y generación de scrap y mejorando las prestaciones mecánicas. Este objetivo se alcanzará gracias a la mejora del proceso de impregnación. Durante la ejecución del proyecto se desarrollarán diversas tecnologías innovadoras que permitirán solventar las dificultades causadas por la alta viscosidad de las resinas termoplásticas, especialmente significativo en el caso de las resinas que contienen elementos ignífugos.
2. Desarrollo de una tecnología innovadora de sobreinyección para fabricar piezas con geometrías complejas localmente reforzadas con una o dos láminas de tapes, mediante la combinación de técnicas de inyección-compresión, un posicionamiento automatizado de las láminas termoplásticas en el molde adaptado a los tiempos ciclo exigidos en automoción y un control de proceso online, que permita reducir las deformaciones de las piezas causadas por la naturaleza anisotrópica de los UD tapes, además de reducir de forma significativa las piezas defectuosas, los costes de producción y el impacto medioambiental. Se espera poder integrar este innovador proceso en la industria del automóvil gracias a la drástica reducción de piezas defectuosas, una mejora en la eficiencia, así como reducción de costes y de impacto ambiental.
3. Desarrollo de una tecnología innovadora de consolidación in situ para fabricar piezas composite de geometría compleja sin necesidad de autoclave para estructuras secundarias de avión y de interior de cabina que cumplan con las regulaciones de resistencia al fuego. Para ello se desarrollarán nuevas poliamidas de alta resistencia térmica y con propiedades ignifugas, así como una adaptación de la configuración del láser que permita trabajar con dichos materiales (actualmente la tecnología está desarrollada para PEEK). Se espera integrar rápidamente este proceso en la industria aeronáutica ya que permitirá reducir drásticamente la generación de desechos (actualmente, se desperdicia un 90% de material en componentes de aluminio obtenidos por mecanizado), así como una mejora considerable en la eficiencia de recursos y el impacto ambiental.
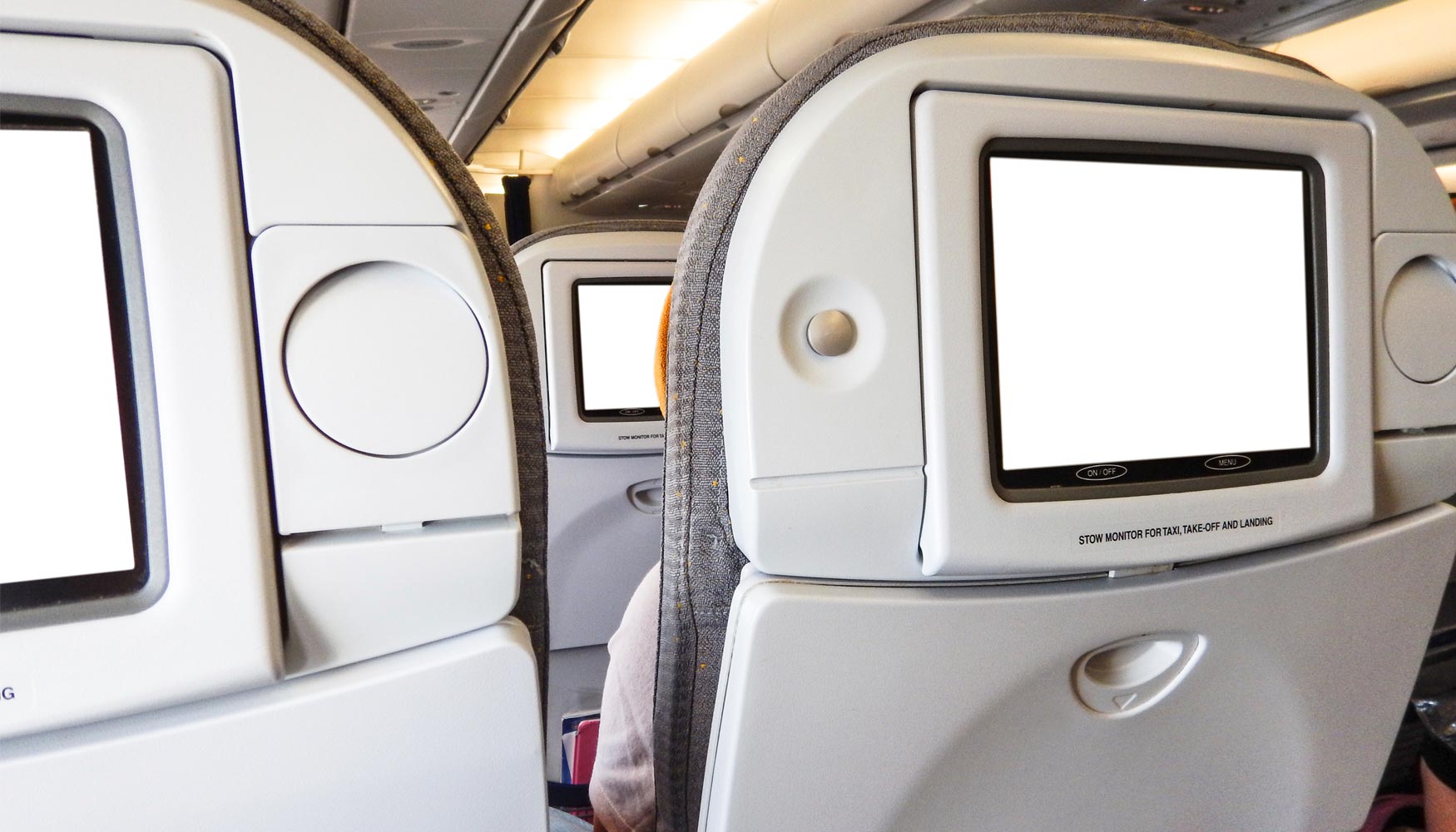
4. Desarrollo de nuevos conceptos de modelización para optimizar la geometría de piezas complejas y determinar el mejor proceso de fabricación. Este objetivo será desarrollado a través de dos líneas de investigación:
- Creación de un nuevo modelo matemático que sirva de herramienta para el diseño estructural y prediga la respuesta de las piezas fabricadas con tapes ante un impacto. El modelo estará basado en la combinación de metodologías ‘Equivalente Static Loads (ESL)’ y ‘Linear Static (LS)’. En función de la geometría de partida y las exigencias de la pieza, se espera poder llegar a optimizaciones hasta el 20% de reducción en peso.
- Desarrollo de nuevo modelo predictivo para simulación del proceso de sobreinyección con UD tapes (1 o 2 capas), de modo que se puedan prevenir las deformaciones en la pieza final.
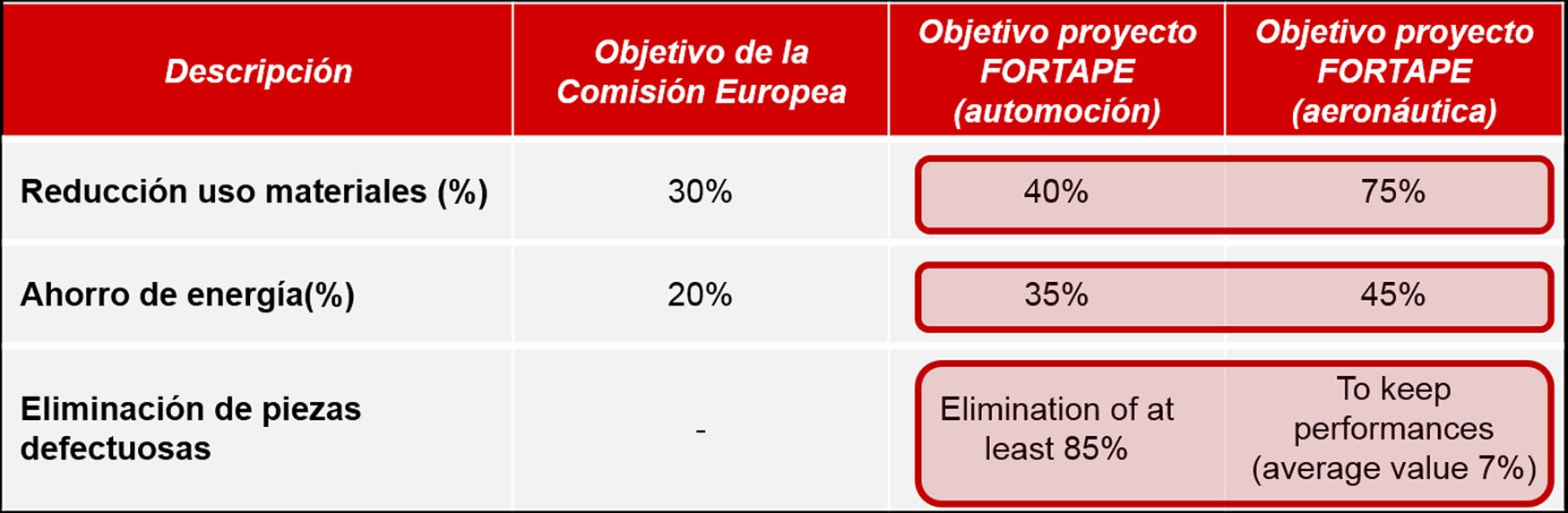
Los objetivos de impacto para lograr el objetivo estratégico del proyecto y ligados directamente con los objetivos técnicos son:
- Eficiencia de recursos (consumo de materiales y energía) en la fabricación de piezas de geometría compleja, aplicado en toda la cadena de valor. Los factores que permitirán alcanzar esta meta son varios: eliminación y optimización de ciertas fases de proceso, el uso de sistemas de calentamiento más eficaces basados en ultrasonidos, la mejora en las metodologías de impregnación de las fibras, reducción del número de capas de tape necesarios en cada pieza, optimización estructural del diseño geométrico optimizando las áreas de colocación de tapes.
- Eliminación de al menos un 85% de las piezas defectuosas en el proceso de sobreinyección gracias a los desarrollos explicados anteriormente. En cuanto al proceso para componentes aeronáuticos se estima una mejora de un 7% en cuanto a piezas defectuosas.
- Producción eficiente, en términos económicos: las mejoras desarrolladas en el proceso de fabricación de UD tapes (una mejor impregnación de las fibras, mayor porcentaje de fibras, eliminación de fases del proceso) permitirá obtener un producto con mayores prestaciones técnicas a menor coste. Si a esto unimos la automatización de los procesos de inyección y consolidación insitu, así como el uso de herramientas de simulación, el resultado se traduce en piezas de alta calidad con el mínimo consumo de material y energía, y por tanto de coste inferior a las presentes actualmente en el mercado.
- Producción sostenible: cada una de los desarrollos contemplados en el proyecto Fortape tendrán un impacto positivo en la huella ecológica ligada al proceso, desde la reducción de materias primas hasta un menor consumo de energía en comparación con los procesos actuales. Asimismo, la eliminación de un porcentaje importante de piezas defectuosas supondrá una mejora. Además, algunas de las líneas de investigación, tales como la optimización estructural de la geometría o el uso de refuerzos localizados de una sola capa contribuirán a una reducción del peso de la pieza final, lo que redunda en una disminución de las emisiones de CO2 durante toda la vida útil del vehículo o avión.
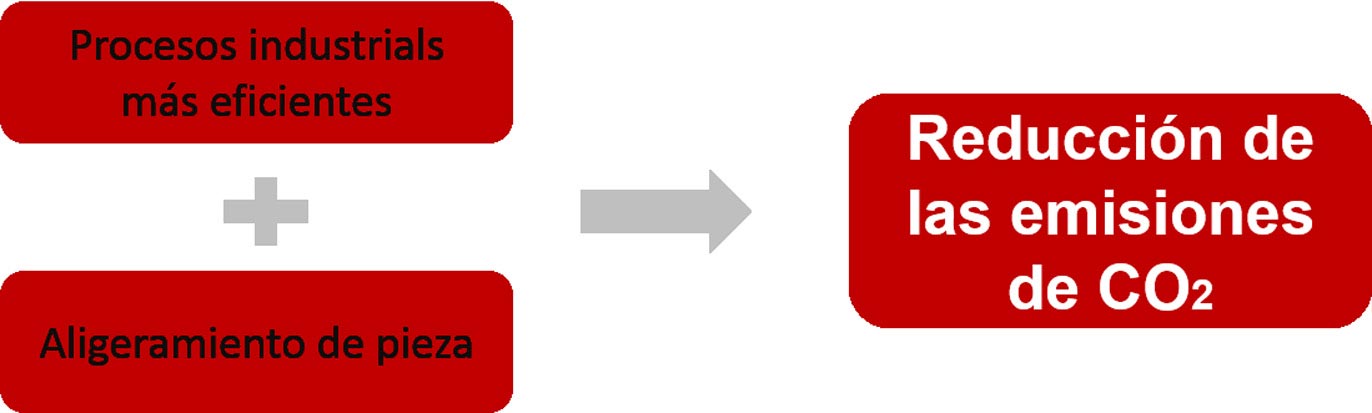
¿Cuál es el impacto en el mercado que se espera conseguir con estas innovaciones?
Impacto en los proveedores de material
Los tapes existentes actualmente en el mercado son vendidos como productos semiacabados por las grandes multinacionales del sector del plástico (Ticona, BASF). Estos productos tienen un margen de beneficio muy superior al de los productos plásticos convencionales, lo que los convierte en una línea de negocio muy interesante. Sin embargo, su alto precio está limitando las aplicaciones finales y dificulta su introducción masiva en el mercado.
Por el contrario, los nuevos tapes desarrollados en Fortape reducirán en gran medida el consumo de energía, así como la tasa de defectivo, lo que resultará en reducciones en el precio de fabricación en torno al 30%.
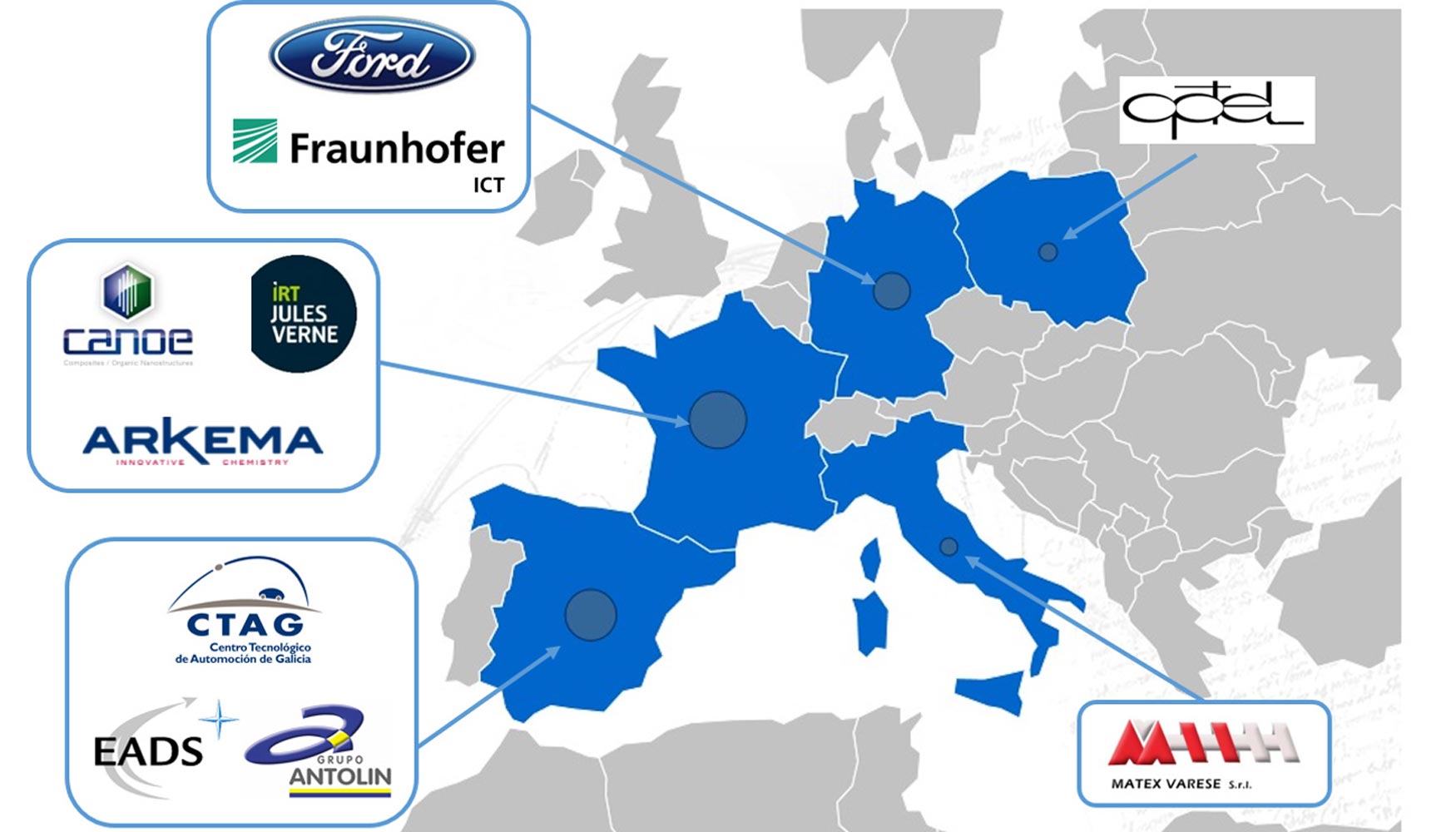
Impacto en la industria de automoción
A pesar de la recesión económica actual, el sector de automoción europeo representa una gran oportunidad para el mercado de los composites, para el que se prevé alcanzar un crecimiento hasta 2.270 millones de dólares en 2018. Este crecimiento se basa principalmente en el potencial de estos materiales para conseguir reducciones de peso hasta un 35%, gracias a las cuales los constructores podrán cumplir las nuevas regulaciones europeas referentes a las emisiones, además de conseguir vehículos con mayor autonomía (en el caso de los vehículos eléctricos). Los materiales composites son ya una realidad en los automóviles de gamas altas, pero no han conseguido introducirse en las gamas de gran cadencia (gamas medias-bajas); los principales motivos de esto y para los que Fortape ofrece soluciones son:
- Precio de las materias primas: todos los materiales basados en semiacabados termoplásticos (prepregs, insertos, tapes unidireccionales) tienen un precio excesivo para el mercado de los vehículos de segmento medio. Fortape reducirá el precio de los UD tapes en un 30% con respecto al valor de mercado actual.
- Carencia de herramientas de validación virtual: en los últimos años, se han reducido constantemente los tiempos de desarrollo de los nuevos modelos, estando actualmente en torno a los dos años y medio. Trabajando con estos periodos tan reducidos, se hace imprescindible el apoyo de herramientas virtuales que permitan predecir y validar los componentes. Este proyecto desarrollará los modelos numéricos necesarios para minimizar los tiempos de desarrollo de los componentes, así como modelos predictivos del proceso de fabricación.
- Cadencias de fabricación elevadas: para los segmentos de gran cadencia (más de 60.000 vehículos/año), los tiempos ciclos deseados para la fabricación de pieza están en torno a los 60 segundos, valores imposibles de alcanzar actualmente para componentes que incluyan UD tapes (estructura de asiento, panel interior de puerta, etc.). La automatización de todas las fases del proceso, así como la monitorización online prevista en Fortape permitirán reducir los tiempos de fabricación y cumplir las exigencias del sector.
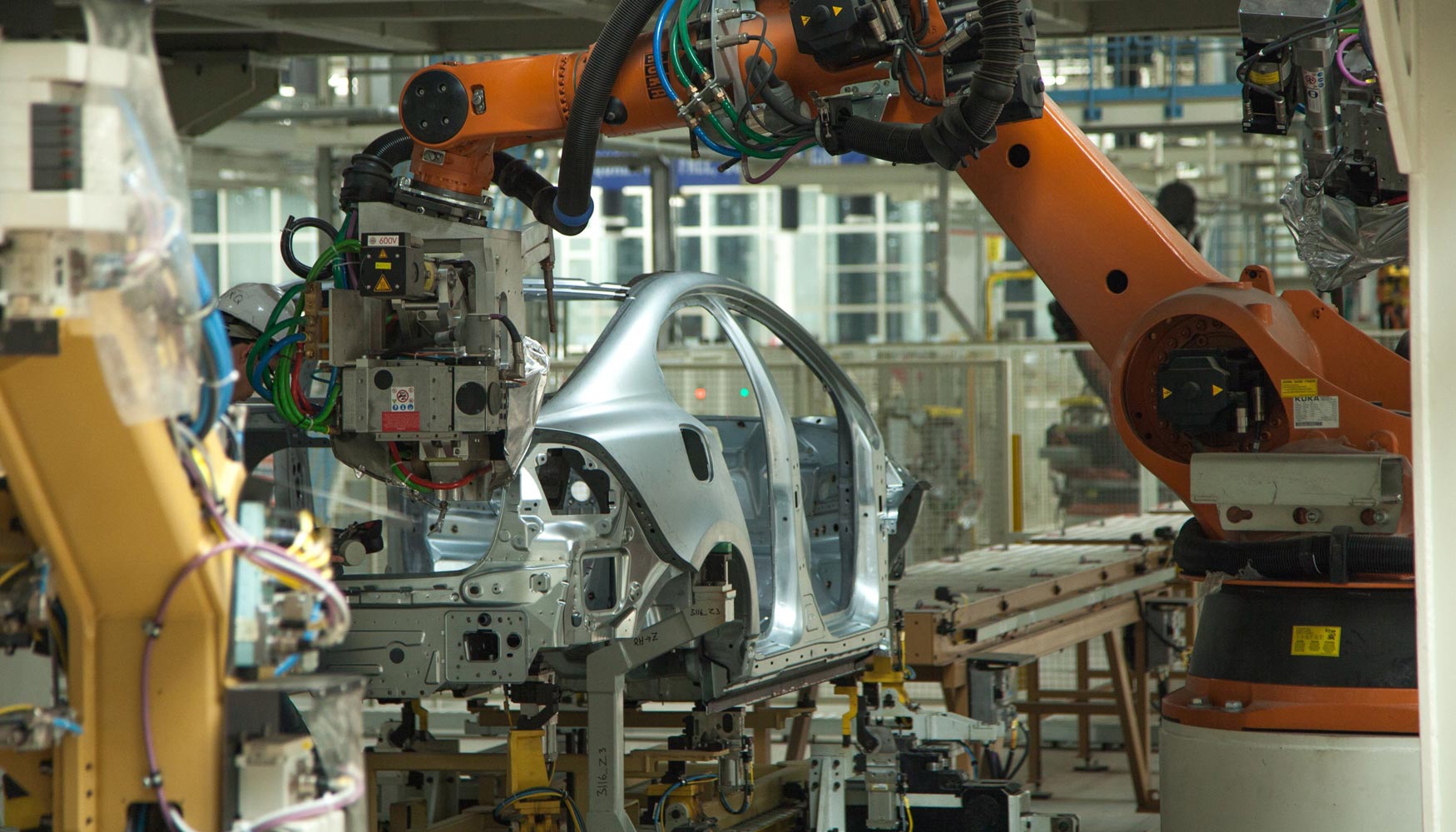
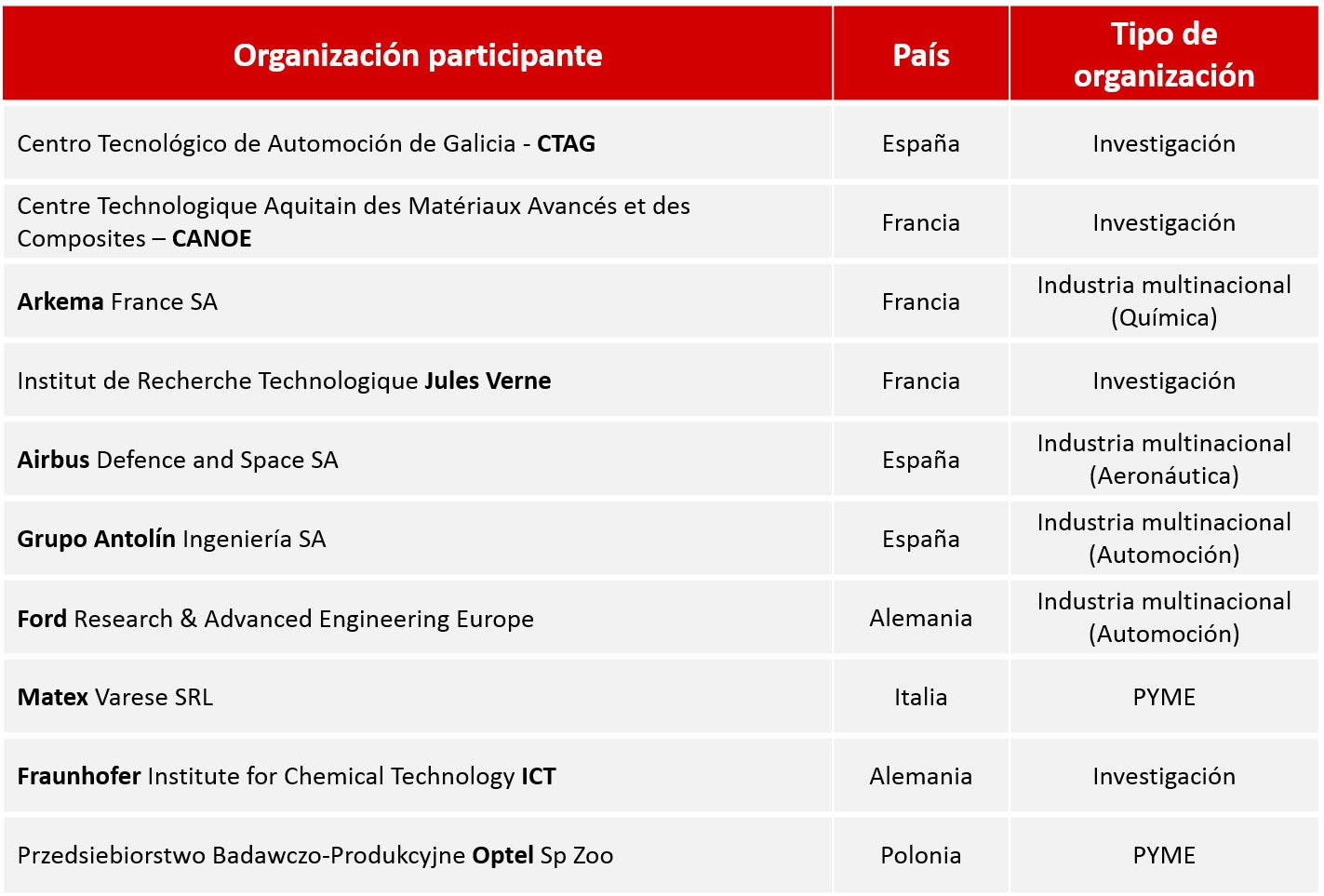
Impacto en la industria aeronáutica
Actualmente, más del 80% de los materiales utilizados en los componentes aeronáuticos pertenecen al grupo de los denominados materiales ligeros: metales ligeros, aluminio, plásticos y composites, muy por encima de otros sectores industriales. Diversos componentes de la estructura secundaria del avión, o las estructuras de los asientos de pasajeros son algunos ejemplos de componentes repetitivos dentro de una aeronave, lo que significa que las cadencias de producción exigidas son mayores. La mayor parte de estos componentes son fabricados en aluminio mediante procesos tradicionales como el mecanizado, siendo procesos caros y con unos ratios de scrap elevadísimos (se puede alcanzar el 90% de desperdicio de material). A mayores, a pesar de ser un metal ligero, la densidad del aluminio sigue siendo elevada si la comparamos con un tape de poliamida con fibra de carbono. Con esta situación, la propuesta de Fortape de implementar un proceso de consolidación insitu de tapes de poliamida con fibra de carbono implica una reducción más que significativa en el uso de materia primas y por tanto, directamente en el coste de producción.
El consorcio que se ha formado en torno a este proyecto aúna experiencia y conocimiento en todas las áreas productivas, desde la fabricación de la materia prima hasta la puesta en mercado de los nuevos componentes. El proyecto tiene una duración prevista de 3 años y cuenta con un presupuesto de 5 millones de euros (La Unión Europea aporta la financiación a través del programa de innovación Horizon 2020).
Este proyecto ha recibido financiación del programa de la Unión Europea de investigación e innovación H2020 bajo el contrato nº 636860.
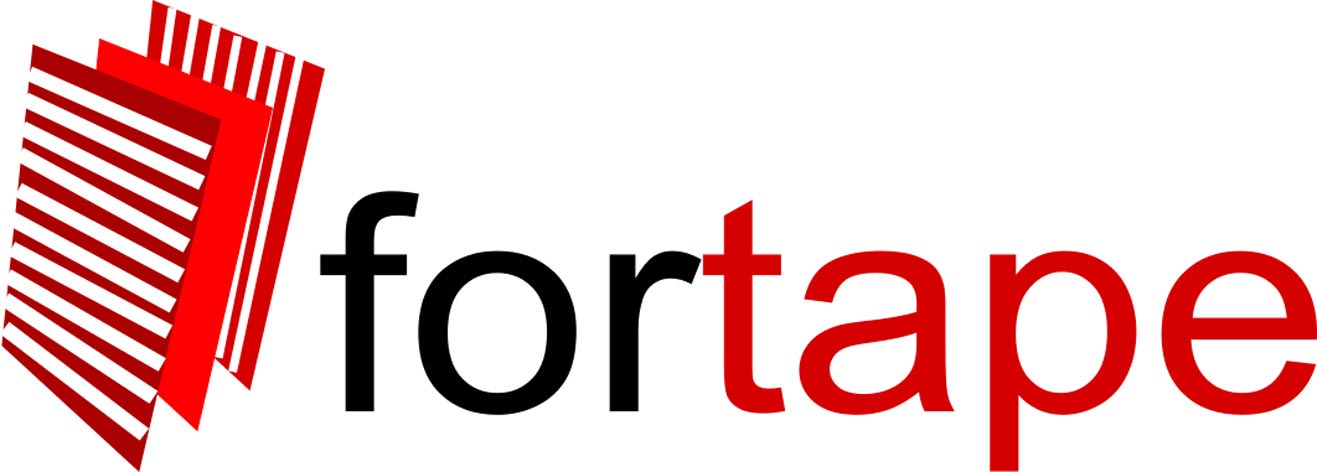