Unilever utiliza cobots para aliviar la carga de los empleados en el proceso de paletizado
Las medidas de reestructuración a corto plazo llevadas a cabo en la planta de Unilever, en Heilbronn, Alemania, implicaron el mantenimiento de una gran estación de paletizado. En lugar de personal adicional, por primera vez desde la compañía optaron por utilizar cobots durante un periodo de una semana, utilizando un práctico modelo de alquiler. La flexibilidad fue solo una de las muchas ventajas de las que se benefició la planta.
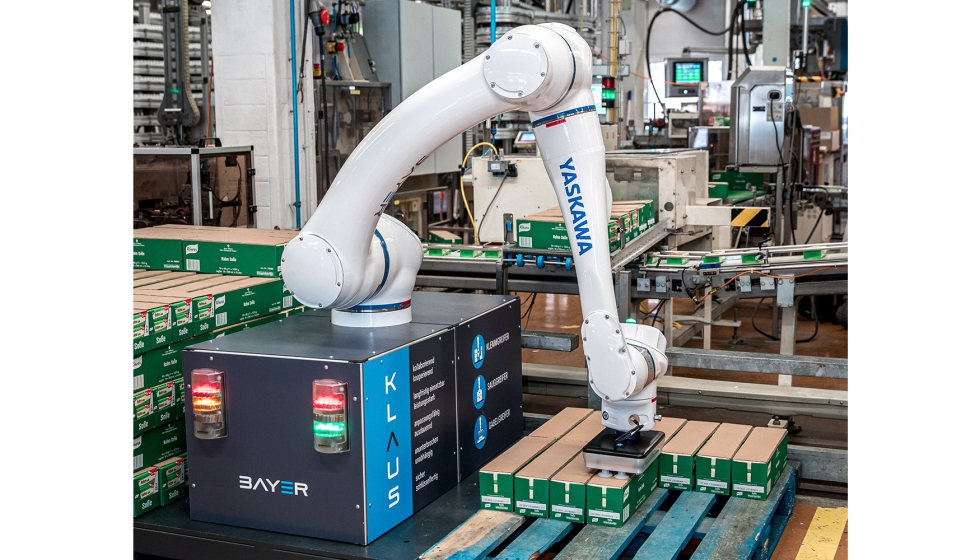
“Concedemos gran importancia a la gestión activa de la salud de nuestros empleados”, afirma Michael Schenk, técnico superior en electrónica industrial en la planta de Unilever Knorr en Heilbronn y responsable de los asuntos técnicos dentro de la empresa, explicando esta primera integración de cobots en la compañía. Y añade: “Por eso nos preocupa fundamentalmente el tema de la ergonomía, sobre todo en el ámbito del paletizado. Vimos en los cobots una oportunidad para aliviar eficazmente la carga de nuestros empleados”.
El proyecto se inició cuando la variación de la maquinaria obligó a parar durante una semana una de las grandes estaciones de paletizado automatizado de la planta. Ante esta circunstancia, se aprovechó para realizar tareas de mantenimiento, pero supuso que la labor de paletizado de los paquetes terminados se tuviera que hacer de manera manual. Si bien en el pasado se habría resuelto recurriendo a personal adicional, el ingeniero de proyectos Thomas Bittner, especializado en proyectos de automatización en Unilever, decidió utilizar cobots por primera vez en la primavera de 2023.
“En ese momento, ya habíamos valorado en muchas ocasiones si el uso de cobots nos compensaría”, afirma. “Sin embargo, como el gasto monetario para ello es bastante significativo, dudamos durante mucho tiempo. Pero cuando conocimos el modelo de alquiler de cobots de Bayer en relación con nuestros planes de introducir la nueva variación, aprovechamos la oportunidad de probarla en funcionamiento y prácticamente sin riesgos”.
La gran importancia de la ergonomía y la seguridad operativa
En la zona de la estación de paletizado afectada hay máquinas llenadoras y estuchadoras. Aquí, los envases producidos se envían mediante una cinta transportadora al sistema central de paletización y, a continuación, como palets acabados, al almacén de estanterías altas. Si el proceso automatizado cambia, por ejemplo, por mantenimiento o la instalación de una nueva máquina, algunos procesos deben realizarse a mano durante este periodo. En este caso, algunas líneas los paquetes deben depositarse manualmente: siendo los empleados responsables de recoger los paquetes manualmente, colocarlos en el palet y que otro empleado los transporte con una carretilla elevadora eléctrica hasta el sistema de acoplamiento, desde donde pasan al almacén de estanterías altas.
“Si tienes que depositar los paquetes así durante ocho horas, por la tarde tu cuerpo te hace saber lo que has estado haciendo durante todo el día”, dice Bittner. “Por eso era importante para nosotros aliviar la carga de nuestros empleados mediante la automatización. Y gracias a los cobots, lo hemos conseguido”.
Para llevar a cabo el proyecto, Bittner contó con los especialistas en automatización de Bayer GmbH & Co KG de Wörnitz, en Franconia. Además de la oferta única de poder alquilar los cobots durante un periodo de tiempo limitado, las décadas de experiencia de los ingenieros de Bayer en el campo de la automatización, así como su proximidad, fueron factores importantes a la hora de tomar una decisión.
“Sobre todo porque era la primera vez que utilizábamos cobots, que trabajan codo con codo con nuestro equipo y sin valla de seguridad, era importante que el proveedor de servicios pudiera llegar hasta nosotros en muy poco tiempo”, afirma Bittner. Además de la ergonomía, el tema de la seguridad operativa también es muy importante en la planta de Unilever en Heilbronn.
Máxima seguridad gracias a un proveedor de servicios experimentado
Dado que Unilever no tenía experiencia trabajando con cobots en aquel momento, los ingenieros llevaron a cabo una introducción basada en vídeo, explicando también los criterios y normas de seguridad que rigen el uso de cobots. Centrando la atención principalmente en la directriz ISO 15066 sobre requisitos de seguridad para sistemas de robots industriales colaborativos y el entorno de trabajo.
Con toda esta información en sus manos, Unilever decidió hacer el pedido y, en solo cuatro semanas, los cobots estaban listos para funcionar. En general, la cuestión de la seguridad es una de las principales razones por las que muchas empresas dudan en utilizar cobots, sobre todo por la falta de experiencia práctica con esta tecnología relativamente joven. Por eso, muchos proveedores experimentados suelen ofrecer una evaluación de riesgos en una fase muy temprana del proyecto, basada en ejemplos, si es necesario incluso como parte de una inspección in situ. Además, en casos concretos también se consulta sobre el proyecto a un experto externo en seguridad de cobots, un especialista experimentado que, como Bayer GmbH, es miembro de la Asociación Alemana de Robótica.
Sin embargo, antes de que se entregaran los cobots, el departamento de seguridad de la planta participó en el proyecto y fue informado desde el principio sobre cómo funcionarían una vez instalados. Algo que también hicieron los directores de planta, división y producción, los coordinadores de turno y los empleados de las estaciones de paletizado afectadas, la mayoría de los cuales siguieron el proyecto con gran interés e, incluso, entusiasmo. Schenk, el ejecutor del proyecto, comentó: “A nadie le preocupaba que el cobot pudiera quitar puestos de trabajo. Y es que no hay motivo para preocuparse, porque en realidad el cobot solo hace el trabajo desagradable y, más allá de colocar los palets, hay muchas otras tareas que realizar. Al final, todos estaban contentos de que ‘Klaus’ hubiera hecho tan bien todo el trabajo pesado”.
Una evaluación interna positiva de los riesgos por parte de la dirección de la planta y de producción, así como la medición de la fuerza y una prueba de funcionamiento antes de poner en marcha los cobots, acabaron por disipar las últimas preocupaciones que aún tenían los responsables de seguridad y de área.
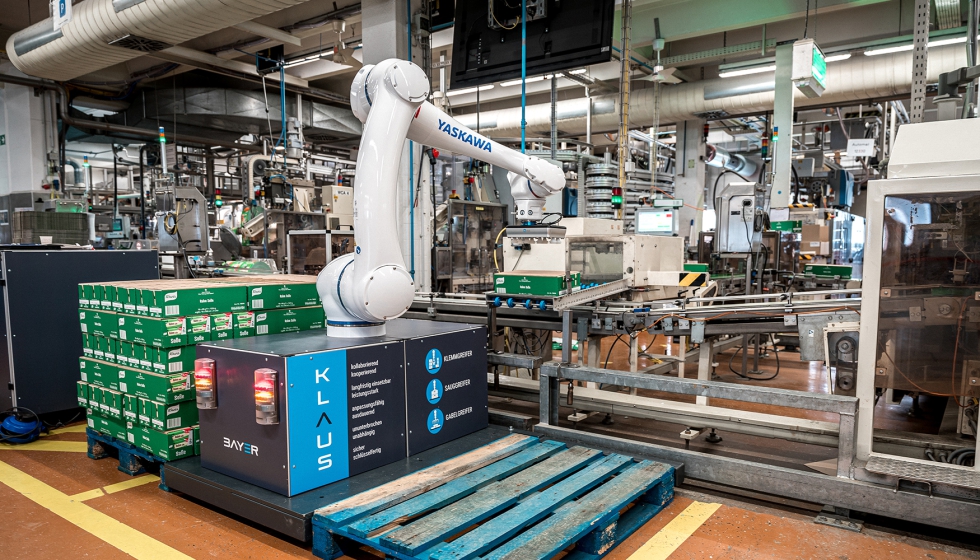
El cobot ‘Klaus’ no necesita aire comprimido
En total, se instalaron dos cobots de Bayer del tipo ‘Klaus’ (montados sobre un modelo básico de Yaskawa) en Unilever, cuyos bastidores también fueron proporcionados por Bayer en régimen de alquiler. Aunque la principal ventaja competitiva del cobot, los conductos de aire integrados, que hacen superfluo el aire comprimido, no jugaron ningún rol en el proyecto de Unilever, en muchas otras aplicaciones, la situación es diferente, ya que los envases suelen recogerse por vacío con ayuda de una ventosa. En el caso de Unilever, sin embargo, los envases se recogieron de forma puramente eléctrica mediante una pinza robótica de terceros. La pinza fue seleccionada por un experimentado ingeniero de forma que no fuera necesario utilizar el costoso aire comprimido. Y como se trata de un producto estándar, también pudo entregarse de inmediato; lo que suponía otra ventaja teniendo en cuenta el ajustado plazo.
Por su parte, la instalación se llevó a cabo en cuatro estaciones de llenado y dos encajadoras del sistema central de paletizado. Mientras en una estación se montaban tres paquetes, en la otra se montaban dos. El trabajo se realiza normalmente en tres turnos, por lo que los cobots asumieron el trabajo de seis empleados potenciales durante la semana que estuvo parado el paletizador.
Dado que el empujador que normalmente se encargaba del transporte de los envases acabados había dejado de funcionar junto con el sistema central de paletización, y que el proveedor externo no pudo proporcionar una cinta transportadora en el ajustado plazo previsto, un distribuidor de servicios externo instaló dos transportadores de rodillos flexibles en los que los envases se introducían centrados en los cobots. El centrado es fundamental para ahorrar tiempo. Si es preciso, el cobot sólo tiene que coger los paquetes y no moverlos de un lado a otro para alcanzarlos. De esta manera se consiguió ahorrar aún más tiempo haciendo que cada uno de los dos cobots trabajara en dos posiciones de palet. Así, cuando un palet estaba terminado, sólo tenían que cambiar al otro lado para seguir trabajando sin interrupción. Mientras tanto, un empleado se llevaba el palet terminado.
Reto y evaluación del proyecto
Antes de poner en marcha los dos cobots, Unilever había proporcionado a los ingenieros diagramas de paletizado, dimensiones de los productos e información sobre la planta técnica y los cobots ya estaban programados de antemano en base a esta información. Un desafío fue el tiempo de ciclo deseado dentro del cual el cobot tenía que recoger los paquetes: una pieza cada diez segundos. Fue posible alcanzar aproximadamente la velocidad deseada, por un lado, gracias a los conocimientos de programación, pero también reduciendo ligeramente la producción por el otro. El hecho de que no se pudiera alcanzar la velocidad deseada también se debió a que originalmente se planeó un cabezal doble, en el que se podrían acomodar dos paquetes a la vez. Sin embargo, debido al apretado calendario, esto no pudo implementarse.
En conclusión, el uso de cobots para el paletizado en la planta de Unilever en Heilbronn ha tenido tanto éxito que la empresa ya está planteándose equipar con sus propios cobots de forma permanente las dos plantas que, en la actualidad, aún funcionan sin paletizado centralizado y en la que, por lo tanto, los paquetes se siguen colocando de manera manual.
Sobre todo, porque se espera que esto reduzca también las bajas por enfermedad en la empresa. Una situación en la que todos salen ganando, ya que la empresa se beneficia de la reducción de las tasas de absentismo y los empleados de la protección de su salud.
No obstante, también es posible que el modelo de alquiler vuelva a utilizarse cuando haya que realizar el próximo lote de trabajos de mantenimiento. “Una cosa está clara, los cobots también nos han aportado un gran avance a nivel interno. Porque todos los directivos han podido comprobar por sí mismos lo bien que podemos integrar un cobot en nuestras operaciones. Ahora tenemos una perspectiva completamente nueva sobre el tema. Es algo sobre lo que podemos seguir trabajando. ‘Klaus’ ha dejado una impresión duradera”, concluye Bittner.