Kodak demuestra en una jornada por qué Flexcel NX ha revolucionado la impresión flexo
Miguel Angel Beltrán, Account Manager Iberia Flexographic Printing Solutions, abrió la jornada explicando las problemáticas que ha tenido que superar la flexografía para evolucionar y adaptarse a las necesidades de los clientes y del mercado. Según Beltrán, “la tradicional inconsistencia del proceso flexográfico ha limitado hasta ahora el avance de la flexografía y dificultado su acceso a determinados niveles de exigencia. A ello se le añaden nuevos y exigentes requerimientos a afrontar por parte del impresor flexográfico; como la integridad de la marca, la complejidad de los gráficos, las presiones en los precios, los aumentos de costes, la competencia global y las presiones medioambientales. Con el objetivo de superar todas estas problemáticas Kodak ha desarrollado la tecnología Flexcel NX que da una respuesta eficiente a las necesidades del mercado flexográfico”.
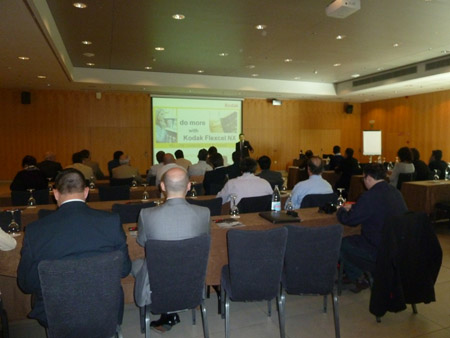
El principal problema a superar en la flexografía es sin duda la inconsistencia de la impresión, para lo que se debería contar con una plancha que cumpliera con cuatro requisitos básicos: reproducción, consistencia, densidad y predecibilidad. Beltrán precisa: “Una tecnología de elaboración de planchas flexográficas capaz de cumplir con esos requisitos debería ser capaz de reproducir el 100% de la imagen digital sobre la plancha sin perdidas de información gráfica y obtener puntos de trama mínimos de hasta 10 micrones de diámetro con estructura resistente y cabeza plana. Por otra parte, sus características estructurales deben permitir que la presión en máquina sea uniforme en todo el rango tonal reproducido y garantizar una transferencia de tinta eficiente que permita densidades de color más altas y estables durante la tirada. Además, el sistema debe tener la precisión suficiente como para repetir con exactitud cualquier trabajo”.
Puntos de trama
El cumplimiento de estos requisitos es fundamental para que el proceso sea predecible, y con ello poder adaptarse así a las condicionantes de la impresión y obtener el rendimiento en impresión necesario para cumplir con los requerimientos de calidad y producción requeridos. Beltrán explica que aunque los procesos digitales tradicionales basados en la ablación de máscara (LAM) han conseguido importantes mejoras en los últimos años, presentan serias dificultades para afrontar los nuevos desafíos que se presentan en la impresión flexográfica debido a limitaciones del proceso de reproducción.
Por lo que a los puntos de trama se refiere, hay que destacar la importancia de la forma plana en la cabeza, ya que ésta permite delimitar con mayor exactitud el área de impresión, la cual se ha calculado previamente al generar el archivo digital y corresponde a un determinado valor tonal predefinido. Este factor es muy importante para poder obtener valores más precisos y predecibles en el proceso, dado que los tradicionales puntos de cabeza curva característicos de las planchas digitales LAM hacen que la superficie impresa pueda variar respecto del valor que se intenta obtener en función de la fluidez de la tinta o a la presión.
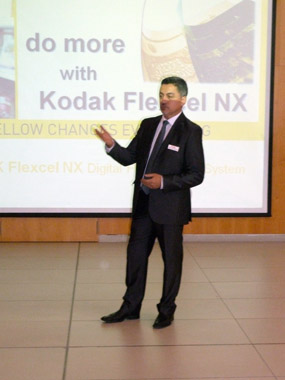
Por el propio concepto de reproducción, la tecnología LAM presenta dificultades a la hora de predecir los puntos de trama que se reproducirán en las planchas debido principalmente al efecto inhibidor del oxígeno durante el proceso de formación. Beltrán explica que “el sistema LAM se basa en la formación de un punto afilado para conseguir detalles finos. Este proceso no puede garantizar un control estructural de los elementos más pequeños y es necesario aplicar ciertas curvas de calibrado en el CTP. No se trabaja con valores del todo reales, ya que para obtener un 2% en plancha hay que reproducir un punto mayor en la máscara a través de una curva en el CTP (Bump Curve) con objeto de compensar la retracción de su estructura que se produce durante la formación. Obviamente esto tiene sus efectos en las transiciones tonales y también hace que la prueba contractual deba adaptase para reflejar esos efectos”.
Por otra parte, “la retracción también puede afectar al calibre de la plancha en función del área tonal, haciendo que éste pueda presentar alguna irregularidad y obligue a efectuar ajustes de presión en máquina, lo cual tiene su repercusión en la impresión, preferentemente en las transiciones tonales, perjudicando también a la durabilidad de la plancha e incrementando la necesidad de paradas de limpieza por saturación de tinta”, dice Beltrán.
Finalmente, Flexcel NX utiliza durante su proceso un sistema de microtexturización incorporado en el sistema y llamado DigiCap NX que permite mejorar las capacidades de transmisión de tinta de la plancha hasta el punto de incrementar las densidades de impresión de forma considerable pero utilizando la misma cantidad de tinta. Esto es posible gracias a una cobertura eficiente del sustrato, lo que permite una absorción y reflejo de luz más uniforme y una mayor percepción del color más impactante.
Según Beltrán, “con más color y con la excepcional capacidad de reproducción del sistema, que permite una baja ganancia de estampación, se consigue ampliar la gama de color imprimible y la posibilidad de reducir el número de colores necesarios en los trabajos. Gracias a esta ventaja y ajustando las densidades a valores estándar reduciendo el exceso de aportación, ahora innecesario del anilox, se consigue un menor consumo de tinta a la vez que una mayor estabilidad durante la tirada, incrementar velocidades, reducir paradas, mermas de ajuste y con todo ello, un ahorro importante en los costes de producción y una reducción considerable en el impacto medioambiental gracias al menor uso de planchas, al ahorro energético y a la optimización de todo el proceso”.
Flexcel Direct Engraving
Otra de las tecnologías desarrolladas por Kodak para flexo es la denominada Flexcel Direct Engraving, la tecnología de grabación directa 3D que trabaja sobre elastómero. La grabación directa de camisas de elastómero no es nueva, pero es ahora cuando la impresión de camisas en continuo está creciendo ya que aportan una serie de ventajas importantes para el sector, como impresiones más rápidas y largas, reducción de tiempos en cambios, registros de color más precisos, mayor estabilidad de la impresión, y reducción de las mermas.
Beltrán explica que “el motivo de tener que trabajar con elastómero con la tecnología de grabación directa es principalmente debido a que se trata de un material que responde muy bien, tanto en definición como en productividad, al láser de alta potencia utilizado para la construcción en relieve de la imagen, y además es un material con unas excelentes capacidades para la transmisión de la tinta. El control absoluto de la escultura del grabado permite obtener elementos con estructura resistente y definida con una resistencia a tintas y sustratos agresivos mucho más eficiente que el polímero”.
Pero para llegar a este punto la tecnología de grabación directa ha tenido que superar varios retos como la existencia de desequilibrios entre definición, consistencia y potencia del láser, el estar orientada a impresión sobre soportes especiales o de poca exigencia en calidad de impresión, la elevada inversión y mantenimiento y baja rentabilidad.
Kodak ha superado todos estos retos con la tecnología Flexcel Direct Engraving basada en un sistema de cabezal de diodo multicanal de alta potencia y eficiencia energética. El equipamiento incorpora un sistema en voladizo de carga lateral que lo hace fácil y rápido de utilizar y puede trabajar con planchas y camisas ITR de elastómero.
Flexcel Direct es una tecnología abierta que puede utilizar cualquier elastómero que haya en el mercado aunque Kodak presenta una solución completa compuesta por el ctp, el software de grabación 3D y un consumible desarrollado específicamente por Kodak para ofrecer el máximo rendimiento con el equipo. Esta tecnología es válida para un rango muy extenso de aplicaciones como embalaje flexible, etiquetado, folding, etc.
Según Miguel Angel Beltrán, “este sistema permite grabar camisas con un ancho máximo de 1.600 mm y un desarrollo máximo de 1.067 mm. Cuenta con un sistema eficiente de evacuación y recogida del residuo generado durante la grabación. El cabezal láser es una consolidada tecnología de diodo multicanal con 915 nm y 1.280 W de potencia. Es rápido y preciso, ofrece una grabación de 1,5 m2/hora a 175 lpi, y un reducido consumo de energía. Es de 4 a 6 veces más eficiente que los láseres tradicionales de gas. Requiere 1/3 de los requerimientos de refrigeración, con bajo coste de mantenimiento y menor coste de los diodos láser. Esto garantiza eficiencia con la ventaja que el fallo de un diodo no causa la parada de la producción del equipo”.

El sistema Flexcel Direct Engraving lleva incorporado un sistema automático de calibración del láser, cuenta con la conversión automática de archivo Tiff1bit a 3D Tiff, un sistema automatizado de escaneado y detección de defectos en el elastómero, y un mecanismo de autofoco que mantiene la precisión y consistencia del láser controlados. En cuanto al software cuenta con un sistema que permite establecer un control del layout y de la calidad para la integridad de la repetición ITR, así como integración con aplicaciones Step & Repeat. La conversión automática de 2D a 3D tiff para grabación. Parámetros standard de grabación desde las aplicaciones más populares, y parámetros de grabación personalizables.
Por lo que a la Grabación 3D de la imagen se refiere, el mayor ángulo de inclinación inicial permite crear bordes afilados y más definición, la impresión de imagen precisa y con menor riesgo de suciedad, control de la formación de la estructura hasta la base para añadir resistencia y estabilidad. Sin olvidar que la presión y el desgaste uniformes reducen la ganancia de punto.
En resumen, Flexcel Direct ofrece una reproducción de imagen con lineaturas de 175 lpi, amplio rango tonal en plancha, textos y líneas finos, y una estructura robusta. La capacidad del elastómero formulado por Kodak permite una excelente transferencia de tinta, alta densidad y estabilidad, y la obtención de colores impactantes a la vez de una reproducción extremadamente definida de los elementos de la imagen. La consistencia en impresión garantiza una baja ganancia de estampación, impresión limpia, textos y líneas muy finas, y sólidos densos e intensos. Y también ofrece beneficios para la sostenibilidad: Reducción del consumo energético en la producción de camisas, diodos láser de bajo consumo, eliminación de la exposición UV, el procesado solvente y el secado, eliminación de la recuperación de solventes, no utilización de químicos agresivos, y puesta en producción más rápida y reducción de merma en impresión.
Tecnología Stream en packaging
Luis Virgos, responsable de Negocio de Impresión Digital en Kodak, habló de la impresión híbrida y de cómo es posible añadir dato variable en equipos offset o líneas de acabado. Según Virgos, “la impresión híbrida nos permite añadir información variable directamente en su rotativa offset, o bien en la línea de acabado en un solo paso y sin pérdida de productividad”.
Teniendo claro este concepto hay que recordar que el dato variable no tiene por qué ser solo 1:1, también puede ser 1:5.000 ó 1:10.000. Se puede ir variando la información en línea ya no solo en cada impresión si no en cada cierto número de impresiones. Virgos explica que “en el ámbito comercial esto ya es muy habitual pero en el entorno de packaging aún no es tan frecuente”. Por eso, para demostrar sus usos Virgos puso algunos ejemplos de envases en los que se había llevado a cabo la introducción de dato variable, como envases de alimentación con diferentes recetas impresas, o cupones personalizados. Además, precisó que “en sectores como el de farmacia y cosmética esta impresión es de gran ayuda para la trazabilidad del producto y es habitual encontrar los cabezales de impresión variable en la plegadora”.
Para poder hacer posible esta impresión variable Kodak ha desarrollado la tecnología de inyección de tinta Stream que tras una evolución ahora ya está disponible con el tamaño de gota adecuado para la resolución que requiere la impresión variable en el sector del packaging. Según Virgos, “esta tecnología es la más adecuada para añadir información variable ya que se añade sólo donde se necesita. Se integra en entorno offset con periodos largos de amortización respecto a la impresión digital habitual, sin costes fijos, está orientada a sectores convencionales y es capaz de igualar velocidades de capacidad de producción elevadas”.
Los modelos disponibles son Prosper S5, S10, S20, y S30. Los puntos en común de todos ellos es que el cabezal tiene el mismo ancho de 105 milímetros, utilizan tintas base agua que pueden ser colorantes o pigmentadas y permiten trabajar en diferentes gramajes incluido el cartoncillo. Las diferencias se centran básicamente en la velocidad y resolución de cada modelo. A tener en cuenta también que la integración de este tipo de impresión variable Prosper S-Series se realiza a medida, analizando en cada instalación cuál es el lugar más adecuado en el proceso de impresión, bien en la rotativa, en el acabado, o incluso utilizando una mesa auxiliar.
Virgos resume las ventajas de esta tecnología en los siguientes puntos: permite integrar información variable calidad offset, bajo coste de producción, utiliza tintas base agua pigmentadas o con colorantes, permite imprimir en negro, colores planos o cuatricromía, se pueden incluir tintas personalizadas, y se pueden unir digitalmente varios cabezales para cubrir una mayor superficie de impresión.