“e-Manufacturing” mediante sinterizado por láser para la producción de series
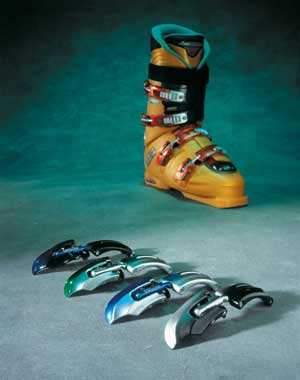
- Producción directa de prototipos funcionales en varios materiales plásticos.
- Producción directa de útiles en metal para moldes de inyección de plástico y otras aplicaciones.
- Producción directa de patrones y moldes para varias técnicas de fusión.
- Producción directa de piezas de uso final en cantidades cuyo número varía de una sola pieza (piezas únicas) hasta decenas de miles.
Para cubrir este amplio rango de aplicaciones, se ha elegido el término e-Manufacturing, que se refiere a la producción rápida, flexible, y rentable de piezas directamente desde un fichero electrónico. Puede incluir los términos “rapid prototyping”, prototipado rápido, “rapid tooling”, “(spare) parts on demand”, fabricación de piezas o recambios bajo pedido, etc. Las recientes innovaciones relativas a las máquinas de sinterizado por láser, materiales, accesorios y métodos de postproceso han aumentado el rango de aplicaciones, gracias a la mejora en las propiedades de las piezas. Al mismo tiempo los aspectos económicos de la tecnología han sido mejorados considerablemente
Este artículo presenta e ilustra casos reales recientes mostrando proyectos de éxito con “e-Manufacturing”. Los ejemplos incluyen la producción de lotes de pequeñas series, y la producción de series personalizadas, para varios sectores industriales.
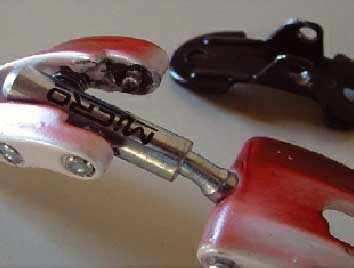
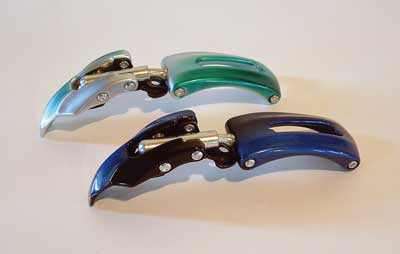
Un proyecto llevado a cabo por Tecnología & Design ilustra bien como el “e-Manufacturing” a través de sinterizado por láser, puede ser aplicado de forma beneficiosa para la producción de pequeñas series de dichos productos, en este caso del cierre de una bota de esquí (Fig.1). El cierre lo componen dos piezas principales de plástico unidas por una barra metálica y montadas sobre un soporte metálico, en forma de hoja (Fig. 2). Tanto el aspecto como la funcionalidad del cierre vienen determinados fundamentalmente por las piezas de plástico, las cuales poseen acabados y formas libres complejas. Las reducidas dimensiones, la escasa cantidad a producir y la complejidad de la geometría constituyen una coincidencia ideal para aprovechar las ventajas que ofrece el “e-Manufacturing. Pero en este producto otros dos importantes requerimientos han de ser cubiertos. Primero, el producto ha de soportar peso e impactos de forma repetida. Segundo, al ser una parte visible debe de alcanzar los más elevados estándares estéticos.
Las piezas en plástico fueron producidas directamente por sinterizado por láser con poliamida 2200 (nylon 12) como material de serie. Las piezas fueron luego pulidas y revestidas. El artículo acabado (Fig. 3) es imposible de distinguir respecto de los cierres producidos a través de métodos convencionales. Tanto el test de fatiga, como el test de impacto fueron efectuados con resultado satisfactorio.
En Tecnologia & Design también analizaron la rentabilidad de producir las dos piezas de plástico y compararon los resultados con el modelo tradicional, vía molde de inyección. El análisis económico mostró que para un tamaño de lote de hasta 600 piezas, la vía del sinterizado por láser es más barata que la opción de molde de inyección. Un análisis de tiempos mostró que, utilizando un sistema EOSINT P380, un lote completo de 600 cierres podía ser producido en 27 días, mientras que mediante molde de inyección eran necesarios 65 días.
Evidentemente la vía del “e-Manufacturing” ofrece más beneficios adicionales tales como flexibilidad en la producción, posibilidad de modificar el diseño sin costes adicionales, etc.
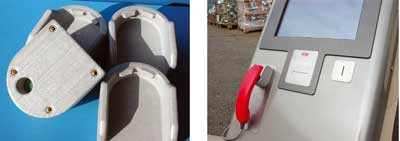
Soportes de auriculares telefónicos para las cabinas públicas
Los soportes fueron realizados a través de sinterizado por láser en una EOSINT P 380 utilizando como material Alumide, una poliamida 12 mezclada con aluminio. Después del proceso de construcción, la superficie fue suavizada completamente con el método AutoFinish. La plataforma de trabajo de la EOSINT P 380 fue suficientemente grande para producir 120 soportes en un solo proceso de construcción (Fig.5). Cada uno de los soportes alcanzó las exigencias de producto final en especial atendiendo al aspecto metálico, calidad de superficie, rigidez, resistencia y precisión en cuanto a sus dimensiones.
De esta forma, los soportes fueron instalados en las cabinas de teléfono públicas con muy buenos resultados. Debido al enorme éxito que obtuvo el proyecto, Telekom Austria decidió producir más soportes de auricular telefónico mediante sinterizado láser. En este momento está planificado construir una cantidad de 300 a 500 piezas año. Esto significa realizar solamente 4 procesos de construcción en la EOSINT P 380. Las modificaciones sobre el diseño son posibles en cualquier momento, sin costes.
Este ejemplo muestra cómo es posible realizar una producción de pequeñas series a través de sinterizado por láser de forma exitosa, sin inversiones iniciales en utillaje o molde. Las propiedades del producto alcanzan los requerimientos en todos los aspectos. Más aún, las superan incluso.
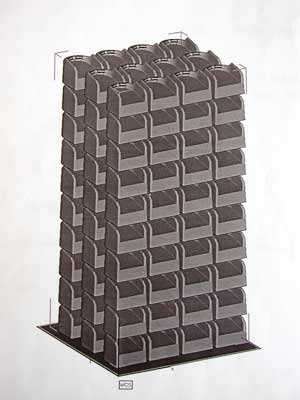
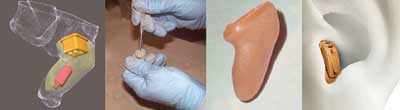
Producción masiva de productos a medida
- Alta precisión y enfoque en el detalle para asentarse bien en el oído.
- Paredes finas que dejen espacio para la electrónica.
- Biocompatibilidad, es decir, permitir el contacto con la piel sin alteraciones alérgicas.
- Tiene que superar el entorno vital del cuerpo (grasa, sudor, etc.) durante años sin degradarse.
Tradicionalmente estas carcasas han sido fabricadas tomando una impresión de cera de la cavidad del oído del paciente, formando un molde flexible alrededor de él y colando dentro de él una resina acrílica curable por UV. Esto consume mucho tiempo en trabajo manual y si la carcasa no encaja perfectamente en el oído todo el proceso ha de empezar de nuevo.
Por ello existía, una necesidad, y un alto potencial de mejora. Phonak identificó la posibilidad de optimizar éste proceso mediante el sinterizado por láser directo de las carcasas, y desarrolló la cadena de procesos correspondiente. Hoy en día las impresiones en cera se someten al scanner, los datos digitalizados son convertidos en carcasas virtuales que se adaptan tanto al oído del paciente como a la electrónica, y luego son sinterizadas por láser (Fig.6).
Phonak ahora construye hasta tres niveles de carcasas por trabajo, cada nivel conteniendo 60-120 carcasas, con medidas que van desde 10 x 10 x 15 mm a 30 x 30 x 25 mm.
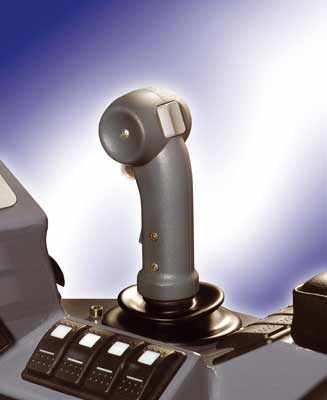
Producción de series rentables mediante la fabricación de moldes o útiles
Para la producción de una de las piezas plásticas FIT utilizó el sinterizado por láser directo sobre plástico, de forma similar a los proyectos descritos antes. Para los otros 14 componentes se requería inyección en molde de PA 6.6 GF 30 (poliamida con fibra de vidrio). FIT construyó el utillaje utilizando el sinterizado por láser directo sobre metal. Para poder producir el utillaje completo para los 14 componentes en el plazo de pocas semanas fue necesario optimizar tanto el concepto del molde como el del proceso. El concepto utilizado se ilustra mediante la inyección de molde mostrada en la Fig. 8. Esta muestra un molde de cuatro cavidades conteniendo los lados derecho e izquierdo de las cavidades para dos de las partes. Cada cavidad ha sido diseñada de tal forma que tenga que ser sinterizado por láser el mínimo volumen de material. El utillaje entero pudo ser producido en una única máquina EOSINT M 250 Xtended en solo 290 horas.
De hecho el cliente hizo varias modificaciones en las piezas después de que el proyecto hubiese ya iniciado, lo que provocó 3 semanas de retraso en el proyecto. Pero con la ayuda de sus tecnologías de sinterizado por láser, FIT mantuvo su disponibilidad en la entrega, a Hamm, de todas las piezas necesarias para el lanzamiento del producto en la feria. El lote completo de producción siguió sirviéndose en tiempo record y con la máxima calidad.
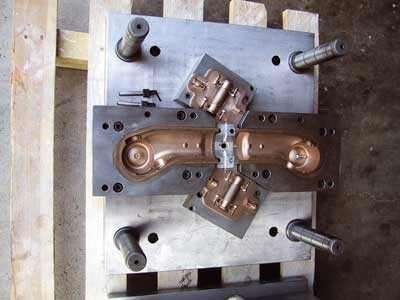
Resumen y comentario
Una fuerza importante que empuja esta tendencia es el factor “coste por pieza”. Hay una tendencia general en el mercado, hacia el incremento de las variantes de producto y también hacia ciclos de vida de los productos más cortos. Estas tendencias dan como resultado un menor número de piezas requeridas por variante, es decir, menores cantidades de producción. El ”e-Manufacturing” posee una ventaja natural en esta situación. También las mejoras que van incorporándose, en cuanto a la productividad de los sistemas de sinterizado láser y a la cadena de procesos, significan que los puntos de equilibrio mejoran de forma continuada. Es decir, las cantidades para las que el empleo del “e-Manufacturing”, de una geometría dada, es más económico que la producción convencional, están aumentando.
Y en último lugar, pero no por ello menos importante: El sinterizado por láser es y será la tecnología clave para el “e-Manufacturing” gracias, de forma particular, a las propiedades de los materiales disponibles. También existirán más métodos de postproceso, y más automatizados, por ejemplo para el pulido o revestimiento de piezas sinterizadas por láser, de tal forma que se podrán llegar a alcanzar texturas y patrones específicos.