El proceso de fabricación de las palas de rotor para aerogeneradores
Gamesa, Neg Micon, Made, Bazán-Bonus, Ecotècnia, Desa, Enercon, Nordex, Jacobs, M. Torres, Repower, GE Wind Energy o Vestas son algunas de las empresas que se ponen a disposición de la energía eólica en Galicia, España y el resto del mundo.
Las factorías están ubicadas en puntos estratégicos de la geografía gallega para facilitar de la misma manera su traslado hasta el terreno donde se desarrollará el proyecto. Tanto el fuste como las palas tienen una longitud media de treinta metros, por lo que deben moverse con extrema precaución y en vehículos especiales. A veces un equipo especializado debe trasladarse hasta la superficie del complejo para soldar allí las piezas de la máquina.
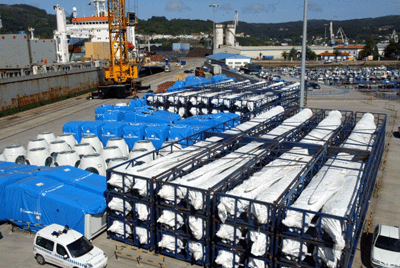
El poliéster es endurecido después de que haya impregnado la fibra de vidrio. El epoxi puede ser utilizado en lugar de poliéster. De esta forma la matriz base puede estar fabricada, total o parcialmente, de fibra de carbono, que es un material con alta resistencia y ligereza, aunque más caro. En grandes palas de rotor también están siendo utilizados materiales laminares madera-epoxi.
Estas palas, antes de salir de fábrica, se somen a las denominadas pruebas de fatiga: son flexionadas utilizando un ciclo próximo a la frecuencia natural de la pala.
La frecuencia natural es aquella con la que la pala oscilará de una parte a otra, si la empuja una vez en una determinada dirección y luego la suelta. Las frecuencias naturales son diferentes en la dirección de flap y en la dirección periférica: la pala tiende a ser mucho más rígida en esta última, por lo que tiene una frecuencia natural más alta para la flexión periférica.
Cada pala se pone en movimiento por un motor eléctrico montado sobre ella que balancea un peso hacia arriba y hacia abajo. Las cimentaciones que soportan el casquillo de la pala deben ser muy sólidas, pueden llegar a componerse de 2.000 toneladas de hormigón.
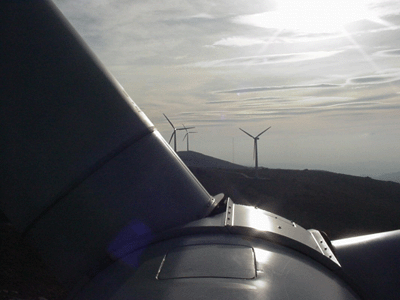
Las factorías dedicadas a la fabricación de palas en Galicia son LM Composites, en As Pontes, y Gamesa- As Somozas, de Gamesa, en As Somozas.
La mayoría de las torres en los aerogeneradores modernos son tubulares tronco-cónicas de acero. Es complicado conseguir esa forma cónica, pues la tensión (presión) de los cilindros de acero tiene que ser diferente en ambos extremos, con el fin de que la plancha se curve adecuadamente.
Las torres son ensambladas a partir de estas subsecciones cónicas más pequeñas, que son cortadas y laminadas con la forma correcta, y posteriormente unidas por soldadura. Suelen fabricarse en módulos de veinte a treinta metros, siendo el transporte por tren o por carretera el factor limitante. Los pesos típicos de las torres modernas son cuarenta toneladas para una torre de 50 metros, a la que le corresponde una turbina con un diámetro de rotor de 44 metros (600 kW), y de 80 toneladas para una torre de 60 metros, para un diámetro de rotor de 72 metros (2.000 kW).
Cada sección de la torre está soldada con un cordón longitudinal y otro circular que la une a las siguientes secciones de la torre. Esto se hace colocando las secciones sobre un banco de rodillos que gira lentamente. Mientras un operador con una máquina de soldadura por arco sumergido suelda las secciones desde el exterior, otro hace lo correspondiente con un grupo de cordones en el interior.
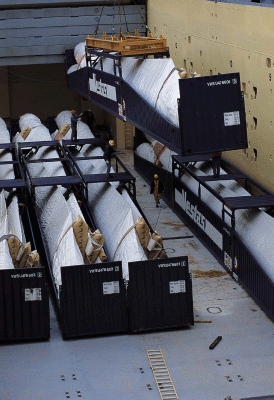
Este sistema requiere que la torre esté provista de guías y abrazaderas especiales para mantener las dos secciones de la torre en su sitio mientras se está realizando la soldadura. También requiere una pequeña fábrica de torres móvil, incluyendo un generador, un equipo de soldeo y un equipo de inspección de rayos-x para inspeccionar los cordones de soldadura.
En Galicia, las empresas dedicadas a la fabricación de torres son Montajes del Atlántico, en Mugardos (Ferrol); Danigal SA, en As Pontes, Gamesa- As Somozas, en As Somozas, y Emesa, en Coirós (A Coruña).
Otras compañías ubicadas en Galicia se dedican al ensamblaje de todas las piezas que conforman el aerogenerador, como Ecotecnia Galicia, en As Somozas; Gamesa Eólica, en Sigüeiro; o la fábrica de Vestas en Viveiro.
El control y mantenimiento de los parques, una vez instalados, corre a cargo de Siemsa Galicia, en A Coruña; Gamesa Eólica, en Bahamonde (Lugo); y Energea, en sus instalaciones de Mazaricos (A Coruña), A Cañiza (Pontevedra) y Ferreira de Valadouro (Lugo).