Ejemplos de aplicación del Mecanizado de Alta Velocidad (2ª parte)
Juan Martín - Técnico Comercial - Juan Martín, S.L.15/03/2002
MECANIZADO DE MOLDES Y MATRICES
Los moldes y las matrices son, sin duda, la aplicación más amplia de la nueva filosofía del mecanizado de alta velocidad. En este sector la introducción de esta nueva tecnología significa más que comprar una nueva máquina herramienta.
En general se necesita sobredimensionar las oficinas técnicas porque como ya se ha explicado en el capitulo 6, el tiempo necesario para el CAM es claramente superior al necesario para estrategias de corte más convencionales.
En cambio la sección de electroerosión se verá reducida con toda seguridad, porque como también se ha dicho, ahora se puede mecanizar para arrancar de viruta materiales que antes eran impensables gracias a los nuevos recubrimientos de las herramientas, y también se pueden reproducir formas más complejas y con radios más pequeños gracias a la estabilidad de los nuevos cabezales y la precisión y dinámica del sistema de accionamiento.
Por este mismo motivo se minimizan los tiempos siempre inciertos de pulido manual y se pueden casi eliminar los procesos de ajuste final (gracias a la precisión de la máquina y a la no- imprecisión de la mano humana).
Todo junto permite reducir los plazos de entrega y mejorar la calidad, que es el verdadero objetivo del mecanizado de alta velocidad en este sector.
España, y en particular Cataluña. Es una de las regiones europeas con una densidad más alta de moldesy matrices y esta industria es sin duda el primer campo de aplicación del mecanizado por arranque de viruta.
Cada uno de los sectores de los muelle y matrices se enfrenta, pero, a problemas diversos y El mecanizado de alta velocidad puede responder también de diversas formas a estas necesidades. A continuación se hace un estudio particularizado con alguno de estos sectores.
Moldes de inyección de plásticos
Este es el sector más amplio de los moldes. Componente de todo tipo de plásticos son múltiples y están presentes en todos los niveles de nuestras vidas. Si en cualquier ambiente nos fijamos en la cantidad de objetos hechos con plásticos, y se piensa que cada uno de esos objetos puede intervenir uno o diversos moldes de inyección de plásticos, se puede tener una idea de la potencia del sector.
En Cataluña se fabrican moldes de inyección de plásticos para muy diversas actividades pero podríamos destacar al sector automovilístico, en el que gran parte de la producción se exporta a las grandes áreas europeas de fabricación de automóviles / entre ellas España).
Las características del molde de inyección de plásticos son tan diversas como los mismos componentes, cosa que hace difícil argumentar soluciones globales para todas las empresas del sector. Las precisiones, los acabados superficiales, etc. son muy diferentes entre un molde destinado a la fabricación de conectores telefónicos o equipamiento médico y otro destinado a parachoques de coche.
Ahora bien, el sector siente la presión constante de unos plazos de entrega cada vez más cortos y exigencias de calidad que hace 5 años eran impensables.
La globalización, además, está abriendo todos los mercados del mundo, y por lo tanto la competencia de las industrias del molde se sitúan a menudo en países menos desarrollados donde los coste fijos y laborales son más bajos. Las industrias transformadoras todavía se sitúan cerca, por ejemplo, de los fabricantes de automóviles porque el sobrecoste del transporte es demasiado caro por pieza. Pero para un molde que inyecta millones de piezas, y con los medios actuales que aseguran la calidad, las distancias no son ningún impedimento y los factores de elección de proveedores ya no son geográficos sino de, y en este orden, plazos de entrega, calidad y precios.
Nada más que con innovación tecnológica se puede, por tanto, mantener las cuotas del mercado para esta industria en nuestro país. El mecanizado de alta velocidad, es uno de los medios para resolver estos conflictos, con las siguientes estrategias:
- Especialización de la industria. A la tecnología de mecanizado de alta velocidad las dimensiones, precisiones y características de los materiales son muy importantes, y dominar esta tecnología para cualquier tipo de molde se hace, casi siempre inviable. Se requiere, por tanto, especialización en un tipo y dimensión de molde que obliga a menudo a sobrepasar fronteras si se quiere aumentar la producción (globalización). Esta realización implica también la subcontratación de faenas auxiliares, que a la vez serán especializaciones de otras empresas del sector (por ejemplo, la fabricación de porta-moldes y otros normalizados).
- Adopción de métodos de fabricación automáticos sin presencia de operadores. Los costos laborales serán siempre más bajos en otras partes del mundo y se ha de intentar reducirlos. Las máquinas de alta velocidad son más caras pero, en general, mucho más pensadas para la operación automática. A demás las estrategias de mecanizado de alta velocidad intentan ya hacer constantes las condiciones de corte, evitando así rotura de herramientas.
- Redefinición de las etapas de la fabricación simplificándolas y haciendo más fácil su planificación y control. La reducción de los procesos de electroerosión, siempre que sean posibles, son fundamentales para el ahorro de tiempo en el mismo tiempo de electroerosión y en el de fabricación de electrodos de cobre o grafito, que no aportan beneficio al molde. Los únicos elementos que todavía continuaran siendo propiedad de la electroerosión son las esquinas con radios muy parecidos a 0 y las ranuras muy profundas (pensemos que con mecanizado de alta velocidad se llegan a hacer ranuras con esbeltez profundidad / anchura = 15.
- También en muchos casos, reducción de los tiempos de fabricación por la posibilidad de mecanizar directamente los bloques de acero templado desde el desbaste hasta el acabado y ahorrarse así los tratamientos térmicos intermedios. Estos procesos están siempre sujetos a condicionamientos económicos, pero si se consideran todos los factores involucrados es a menudo muy ventajoso.
- La rapidez de los procesos de alta velocidad permiten hacer pasadas de mecanizado mucho más pequeñas mejorando en 4 o 5 veces los acabados superficiales con un tiempo de mecanizado parecido o ligeramente mayor, Así permite reducir los procesos manuales de pulido, ahorrando mano de obra muy cara. El mecanizado de alta velocidad puede llegar a producir acabamientos superficiales de Ra = 0,1 mm y mejores, superando los limites de las erosiones en tiempos considerablemente mejores y sin necesidad de producción de electrodos.
- La precisión estática y dinámica de las nuevas máquinas de alta velocidad, y la presencia mínima de operaciones manuales permiten muchas veces eliminar los procesos de ajuste de moldes, que a menudo duran semanas y suponen costes altísimos en dinero y tiempo.
Pero estos avances no se quedan aquí. La presencia cada vez más importante de los moldistas en la fase de diseño de los componentes automovilísticos, puede permitir la adopción de nuevas formas de producto que hagan más fácil la aplicación del mecanizado de alta velocidad y reduzcan por lo tanto costes globales al sector.
A continuación se presentan algunos ejemplos de mecanizados utilizando la tecnología de alta velocidad (figuras 14, 15, 16).
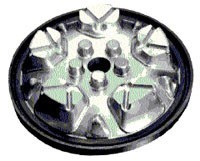
Fig. 14.- Macho de un molde de inyección de plástico para
tapacubos. Pieza de Ø470 en acero pretratado a 46 HRc.
Tiempo total de mecanizado desde el desbaste al acabado: 17 h.
tapacubos. Pieza de Ø470 en acero pretratado a 46 HRc.
Tiempo total de mecanizado desde el desbaste al acabado: 17 h.
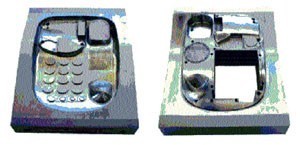
Fig. 15.- Molde entero (macho y hembra) de la carcasa
exterior de un teléfono de mesa. Hasta las ranuras del macho
están mecanizadas en el centro de mecanizado.
Todas las superficies están acabadas de máquina, sin pulir.
Material DIN 1.2344 a 54 HRc.
Tiempo total de mecanizado 28 horas para la hembra y 52 para el macho.
exterior de un teléfono de mesa. Hasta las ranuras del macho
están mecanizadas en el centro de mecanizado.
Todas las superficies están acabadas de máquina, sin pulir.
Material DIN 1.2344 a 54 HRc.
Tiempo total de mecanizado 28 horas para la hembra y 52 para el macho.
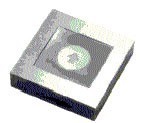
Fig. 16.- Hembra de un molde minúsculo para la
fabricación de una tapa de baterías.
Acero templado a 54 HRc. La herramienta más grande utilizada es de Ø0,5 mm y la más pequeña Ø0,2 mm.
Tiempo de mecanizado 1,5 horas.
fabricación de una tapa de baterías.
Acero templado a 54 HRc. La herramienta más grande utilizada es de Ø0,5 mm y la más pequeña Ø0,2 mm.
Tiempo de mecanizado 1,5 horas.
Moldes de inyección de aluminio
Las exigencias del producto en este sector son muy parecidas al de los moldes de inyección de plásticos y también, por lo tanto los beneficios de del mecanizado de alta velocidad.
Pero se han de destacar algunas características propias:
- Los componentes de aluminio se utiliza a menudo en aplicaciones donde se necesita una refrigeración eficiente e incluyen por lo tanto aletas de refrigeración. Estas, en los moldes, Suponen ranuras muy esbeltas que tradicionalmente han supuesto grandes producciones de electrodos de grafito y dedicación en tiempo a los procesos de electroerosión. Este elemento ha de ser por tanto uno de los objetivos del mecanizado de alta velocidad en esta industria (figura 17).
- Los acabados superficiales no son tan críticos como en el caso de los molde de inyección de plásticos al ser, en general, los componentes de aluminio piezas funcionales no vistas. A demás la misma inyección de aluminio no consigue cualidades superficiales a las piezas muy buenas. Si se necesitan componentes vistos de aluminio a menudo se acaban en procesos de pulido automático.
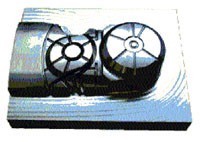
Fig. 17.- Cárter del motor una motocicleta. Las ranuras
que conforman las aletas de refrigeración son muy profundas.
Material DIN 1.2344, 54 HRc. Tiempo: 9,5 horas
que conforman las aletas de refrigeración son muy profundas.
Material DIN 1.2344, 54 HRc. Tiempo: 9,5 horas
Moldes de soplado
Los moldes de soplado son un caso diferente dentro de los moldes de componentes plásticos. Estos moldes se utilizan para la fabricación de botellas de plástico. El sector más alto de consumo es el de las bebidas refrescantes y sobre todo el agua mineral.
El funcionamiento del molde no es de inyección. Se utiliza una preforma de plástico inyectado (este componente sí que es inyectado y requiere precisiones muy elevadas), que incluye la rosca recipiente alargado con un grosor de paredes determinado. Esta preforma se sitúa dentro del molde y se sopla aire caliente por el interior de la preforma que calienta el plástico y lo hace expandirse contra las paredes del molde. Esto da al molde características particulares:
- El molde se fabrica en aluminio porque al no existir mucho rozamiento del plástico se pueden conseguir producciones bastante elevadas. Las máquinas dedicadas a estos moldes han de tener características adecuadas para estos materiales. El mecanizado del molde supone un tiempo muy limitado.
- Los acabados superficiales son muy exigentes. Nada más hay que comprobar las superficies de las botellas de plástico. El mecanizado de alta velocidad puede ahorrar tiempo de pulido que es porcentualmente, muy elevado en estos tipos de moldes. En este sector se comenzó, hace años, a utilizar interpolaciones NURBS para rebajar tiempos y mejorar la calidad superficial.
- La producción de un determinado componente (por ejemplo la botella de 1,5l de Font Vella) es muy intensa (algunos cientos de miles o millones cada día) y por lo tanto se han de fabricar muchos moldes iguales. Esto permite reducir los costes de programación por molde, y optimizar las trayectorias para intentar mejorar tiempos y acabados superficiales. Muy a menudo se pueden utilizar máquinas de mecanizado horizontales más comunes en los campos de producción de pieza final, aprovechándola mejor evacuación de las virutas que presentan estas configuraciones, y los elementos auxiliares para reducir el tiempo de no corte como cambiadores automáticos de palets. En un palet se puede montar un cubo y en cada uno de sus costados un molde mejorando la autonomía de la máquina y haciendo el proceso más económico.
- Tradicionalmente estos moldes no se han utilizado nunca en electroerosión, y por lo tanto, no se da esta substitución de tecnologías.
En la figura 18 se presenta uno de estos moldes.
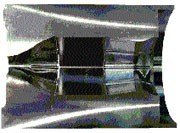
Fig. 18.- Molde de soplado en material de aluminio.
Tiempo de mecanizado 56min. Rugosidad superficial: 0,6 µm.
Tiempo de mecanizado 56min. Rugosidad superficial: 0,6 µm.
Matrices de forja en caliente y frío
Este sector también requiere piezas repetitivas, reduciendo por tanto el coste de CAM por pieza fabricada.
Los materiales utilizados en la forja en caliente son aceros templados (generalmente DIN 1.2344 de 44 a 54 HRc). En el capitulo 10 se ha hecho el estudio económico de viabilidad de una empresa fabricante de este tipo de matrices. En el estudio de viabilidad se explican otras características del sector.
En la figura 19 se muestra una de las matrices más estudiadas de la forja en caliente.
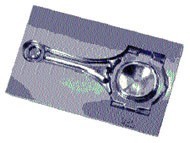
Fig. 19.- Matriz de forja caliente para la producción de
bielas para el sector del automóvil. El material es soldadura de
muy baja maquinabilidad. Tiempo total: 2 horas
bielas para el sector del automóvil. El material es soldadura de
muy baja maquinabilidad. Tiempo total: 2 horas
La forja en frío utiliza materiales todavía más duros y difíciles de mecanizar (como por ejemplo un material de la empresa Uddeholm, ASP-23, que después del tratamiento térmico llega a 62 HRc).
Este sector se debate todavía entre la conveniencia o no de adoptar máquinas de alta velocidad, o continuar con las máquinas de electroerosión. Como se ha explicado ya en el capitulo 5, dedicado a la herramientas, el rendimiento de estas baja mucho en durezas de 62 HRc y por lo tanto los costos pueden se inviables.
Así y todo el futuro es claro, nada más que un pequeño paso de las herramientas puede desbancar las electroerosiones totalmente. Ya, que de todas las maneras, hay empresas que utilizan El mecanizado de alta velocidad para producir sus matrices de forja en frío.
En la figura 20 se muestra el punzón de una matriz de forja fría para la fabricación de colzas homocinéticas para la dirección de los automóviles.
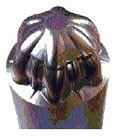
Fig. 20.- Punzón para la fabricación de colzas homocinéticas.
Material: ASP-23. Dureza: 62 HRc. Tiempo: 3 horas
Matrices de extrusión de aluminio
Las matrices de extrusión de aluminio se utilizan en prensas de extrusión que conforman el aluminio en perfiles. Estos se utilizan básicamente en la construcción (puertas, ventanas, etc.).
Este sector también requiere grandes producciones de matrices pero en este caso no repetitivas. De todas maneras las matrices de extrusión tienen elementos morfológicamente muy semejantes y el elemento más cambiante es el perfil de calibración que se hace únicamente con electroerosión de hilo.
Los materiales utilizados son también DIN 1.2344 con tratamientos técnicos para inducirlos a 52-54 HRc (figura 21).
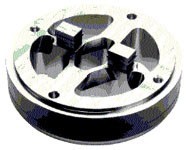
Fig. 21.- Pieza puente de una matriz de extrusión de aluminio.
Material Din 1.2344 a 54 HRc. Tiempo total de mecanizado: 2,5 horas.
Material Din 1.2344 a 54 HRc. Tiempo total de mecanizado: 2,5 horas.
Las ventajas de producción y mecanizado de alta velocidad son claras para este sector.
El problema más importante de estas matrices es el plazo de entrega. Estos se están intentando reducir por debajo de ¡ una semana ¡. Tradicionalmente el desbaste se produce con el material todavía blando, se templa, y después se acaba en el centro de mecanizado o electroerosión. Así muchas de estas empresas productoras incorporan el tratamiento térmico en sus instalaciones para reducir tiempo.
Aún y esto el tiempo para endurecer una de estas matrices no es nunca menor de 24 horas, que supone el 20% del tiempo total de producción de la matriz.
El mecanizado de alta velocidad está comenzando a revolucionar este sector. Las empresas líderes han adoptado ya esta nueva tecnología simplificando el proceso de mecanizado integrado al centro de mecanizado desde el bloque ya templado, ahorrando cambios de máquina, operadores, tiempo y costes.
En muy poco tiempo la substitución de electroerosión de penetración será casi del 100% en este sector.
El proceso total entonces se simplifica en mecanizado al centro de mecanizado de alta velocidad y electroerosión de hilo para formar el calibración del perfil.
CENTRO DE MECANIZADO PARA MOLDES Y MATRICES DE PRECISIÓN
Para esta aplicación hemos escogido el centro de mecanizado Makino V33 de fabricación japonesa. A continuación se presenta la imagen y características fundamentales de la máquina (figura 22 y tabla 23, respectivamente).
Se trata de un centro de mecanizado de alta velocidad diseñado para fabricar piezas de ultra precisión con unos acabados superficiales excelentes. Es por lo tanto adecuado para moldistas de inyección de plásticos de piezas pequeñas (moldes multicavidad).
Veremos a continuación las soluciones técnicas que se han desarrollado para este modelo y cómo se han conseguido estas características.
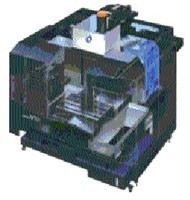
Fig. 22.- Aspecto del centro de Makino modelo V23
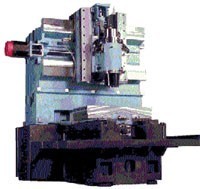
Fig. 23.- Estructura de la máquina Makino V23
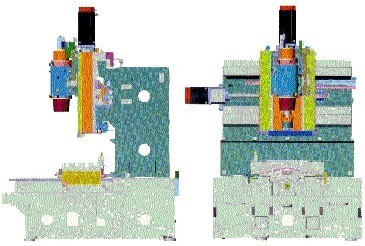
Fig. 24.- Esquema de la estructura de la máquina Makino V23
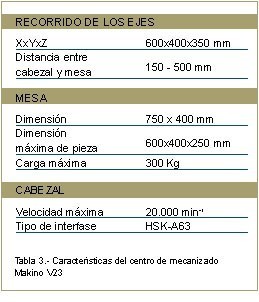
Estructura
La estructura de la máquina se ha diseñado para mejorar la precisión estática y dinámica de los centros convencionales. Se utilizan guías hidrodinámicas muy amplias para aumentar el amortiguamiento de las vibraciones y mejorar así los acabados superficiales (figuras 23 y 24).
Se aumentan las rigideces de los carros de los ejes X y Z con distancias entre guías muy amplias y alargando las guías del eje Z evitando voladizos, Así se mantiene la rigidez del sistema en cualquier posición de los ejes.
Los husillos de bolas son también extra- rígidos. El diámetro de 45 mm y el paso de 8 mm le conforman una respuesta muy elevada a las necesidades de aceleración para la realización de trayectorias complejas de 3D.
CNC y sistemas de accionamiento
Los sistemas de medida de los accionamientos incorporan encoders y reglas.
Los encoders realizan el cierre del lazo de velocidad. Estos tienen resolución de 1 millón de pulsos por vuelta.
El CNC de esta máquina utiliza la tecnología básica del FANUC 16iM pero el control de los ejes está programado por el fabricante de la máquina adaptándolo así a los algoritmos las ecuaciones de respuesta de la mecánica de la máquina.
La cadena cinemática de los ejes, los nuevos sistemas de medida de alta resolución y los algoritmos de control numérico adaptado a la mecánica de los ejes nos permiten obtener precisiones y acabados superficiales excepcionales.
La precisión se comprueba mecanizando un circulo de Ø40 mm en aluminio a 8000 mm/min de avance. Los resultados se presentan en la figura 26.
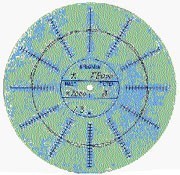
Fig. 26.- La prueba es mostrar un error de circularidad
máxima de 1.3 µm, en un avance de 8.000 mm/min.
máxima de 1.3 µm, en un avance de 8.000 mm/min.
Con este nuevo sistema de lectura de la posición se pueden controlar las 0,1 µm.
Esto mejora mucho el acabado superficial de las piezas.
En las figuras 27 y 28 se muestran, al microscopio, las diferencias entre un acabado con el lazo de posición estándar de 1 µm y otro con el lazo de posición de 0,1 µm. En la 27 se muestra el acabado con feedback de 0,001 mm y en la 28 el de feedback de 0,0001 mm.
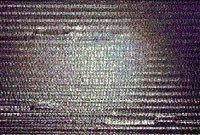
Fig. 27.- Acabado con feedback de 0,001 mm
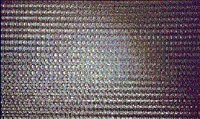
Fig. 28.- Acabado con feedback de 0,0001 mm
Cabezal
El cabezal de la máquina es uno de los elementos más especiales en esta máquina.
Para conseguir hacer piezas de ultra precisión se necesita que también el cabezal mantenga precisiones por debajo de 0.002 mm. El control térmico de este ha de ser, por tanto muy apurado. Su sistema de refrigeración se muestra en la figura 29.
Se trata de un cabezal integrado con un motor de doble bobinado para conseguir parejas respetables a bajas revoluciones. Las revoluciones máximas son 20.000 rpm.
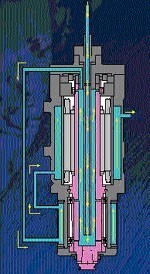
Fig. 29.- Sistema de refrigeración del cabezal
Como se ha explicado en el capitulo 8, la dicotomía entre potencia y velocidad de cabezal se produce fundamentalmente por la imposibilidad con sistemas normales de refrigeración, de montar rodamientos rígidos (tamaño grande) en un cabezal de altas revoluciones y con una vida estimada muy aceptable.
El cabezal de este centro de mecanizado presenta dos características que permiten sobrepasar los valores establecidos en el capitulo 8.
- Refrigeración directa del rotor. El cabezal (como se ve en la figura 28) se refrigera primero dentro del rotor, después enfría el exterior de los rodamientos frontales y por último los devaneos del estator del motor. Esta refrigeración es muy eficiente porque evacua el calor directamente del lugar donde se concentra el mayor número de focos: el estator. A demás esta refrigeración se controla para actuar con más intensidad cuando aumenta la velocidad del cabezal, Así, a más velocidad, el rotor del cabezal es más frío que la parte fija y por lo tanto se aligera la precarga de los rodamientos. Esto nos permite precargar los rodamientos a bajas revoluciones, obteniendo así un cabezal capaz de una rigidez axial y radial muy alta en las revoluciones donde se hacen los desbastes. Y en cambio a otras revoluciones cuando los esfuerzos de corte son mínimos liberar las precargas.
- Lubricación directa de la jaula interna de los rodamientos. El mismo aceite que se utiliza para la refrigeración del interior del rotor, lubrica directamente la jaula interior de los rodamientos frontales, mediante unos agujeros que se practican antes del montaje. Esta lubricación nos permite cifras DN 5 veces superior a los obtenidos con refrigeración aire- aceite. Tenemos por tanto más juego con el tamaño del rodamiento (en la máquina se montan rodamientos de Ø interior = 65 mm), y la vida efectiva de los mismos se alarga (20.000 horas mínimo).
Este cabezal supera en todos los aspectos a los cabezales de máquinas similares. Los acabados superficiales que se obtienen con la máquina son también muy superiores (hasta Ra = 0.03 mm, o sea el espejo).
La figura 30 muestra los gráficos de potencia y par respecto a la velocidad del cabezal.
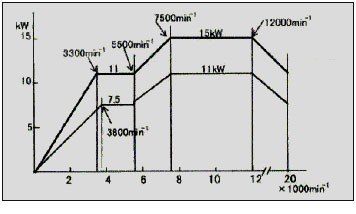
Fig. 30.- Gráficos de potencia y par respecto a la velocidad del cabezal.
Sistemas auxiliares
Esta máquina esta especialmente diseñada para El mecanizado de piezas de ultra precisión y acabados superficiales excelentes para moldes.
Estas piezas son normalmente pequeñas y por tanto la cantidad de material a mecanizar es insignificante. Por eso la máquina no incorpora, al menos de serie, ningún extractor de virutas.
Estas se pueden extraer con la mano mientras la máquina esta en funcionamiento con el inteligente sistema descrito en la figura 31.
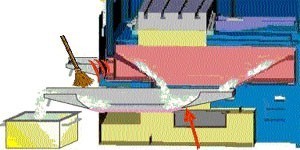
Fig. 31.- Extracción de virutas mediante un cajón que se puede vaciar mientras la máquina se encuentra en funcionamiento.
Control térmico y evacuación del calor
Para obtener precisiones inferiores a los 0,002 mm son necesarios controes térmicos estrictos que impidan la aportación de calor a la estructura.
Los motores de los ejes tienen ventilación forzada para extraer el calor generado en sus devanados y rodamientos.
Las uniones motor-estructura y el cabezal de la máquina se refrigeran y mantienen a +-0,5oC de la temperatura de la estructura. Esta temperatura es controlada por sensores térmicos que hacen de input al sistema de realimentación del refrigerador.
La emulsión refrigerante también refrigera a +-0,5oC de la temperatura de la estructura.
Las fuentes de calor, tales como el armario eléctrico, se mantienen siempre con una barrera térmica para no aportar calor a la estructura (figura 32).
Los motores de los ejes tienen ventilación forzada para extraer el calor generado en sus devanados y rodamientos.
Las uniones motor-estructura y el cabezal de la máquina se refrigeran y mantienen a +-0,5oC de la temperatura de la estructura. Esta temperatura es controlada por sensores térmicos que hacen de input al sistema de realimentación del refrigerador.
La emulsión refrigerante también refrigera a +-0,5oC de la temperatura de la estructura.
Las fuentes de calor, tales como el armario eléctrico, se mantienen siempre con una barrera térmica para no aportar calor a la estructura (figura 32).
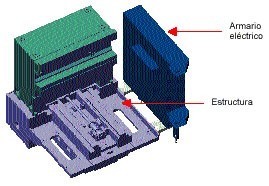
Fig. 32.- Barrera térmica entre armario eléctrico y estructura
5) METALUNIVERS Marzo 2002
Empresas o entidades relacionadas
FANUC Iberia, S.L.U.
Juan Martín, S.L.