Estabilidad dimensional de componentes soldados mediante vibración
El alivio de tensiones por vibración es un proceso igualmente probado desde hace décadas, pero mucho menos conocido y utilizado, ya que es considerablemente más rápido, barato y respetuoso con el medio ambiente. En vista de las crecientes demandas de protección medioambiental, conservación de recursos y estructuras de costes, el alivio vibratorio de tensiones para la estabilización dimensional de componentes soldados antes, durante o después del procesamiento mecánico es, por tanto, cada vez más importante desde la perspectiva de la sostenibilidad y la rentabilidad. Jebens GmbH, con sede en Korntal-Münchingen (Alemania), es una empresa experta en piezas oxicortadas grandes y pesadas, así como en ensamblajes complejos, que cree firmemente en este proceso y aboga por su reconocimiento generalizado.
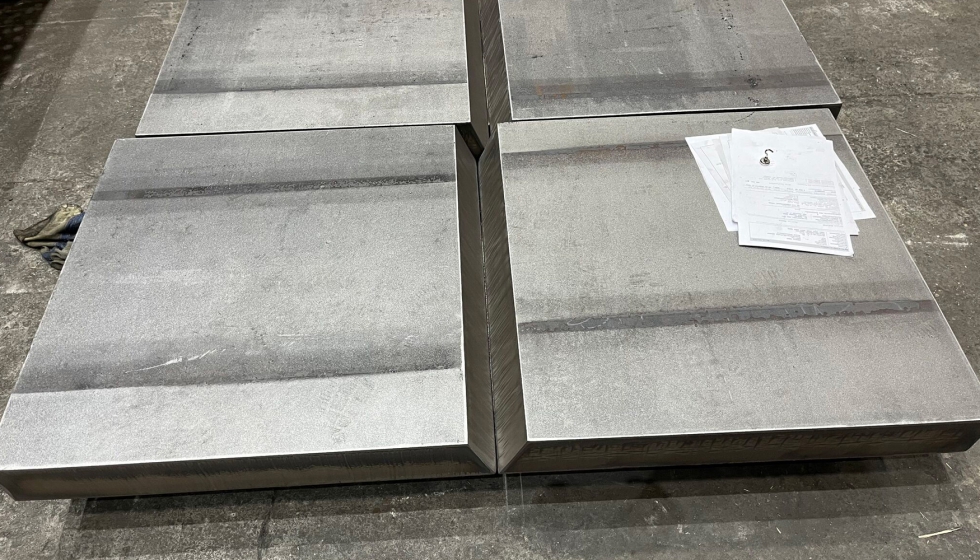
El alivio de tensiones por vibración, introducido en EE. UU. hace unos 100 años y comercializado y mejorado significativamente por VSR Industrietechnik GmbH en Alemania en los últimos 50 años, funciona aplicando vibraciones dirigidas a las zonas de los componentes con tensiones residuales existentes. Debido al efecto de carga específico del motor de masas excéntricas en las zonas con tensiones residuales elevadas, el límite elástico del material se supera en puntos localizados. El resultado es un alivio localizado y la reducción de las tensiones residuales.
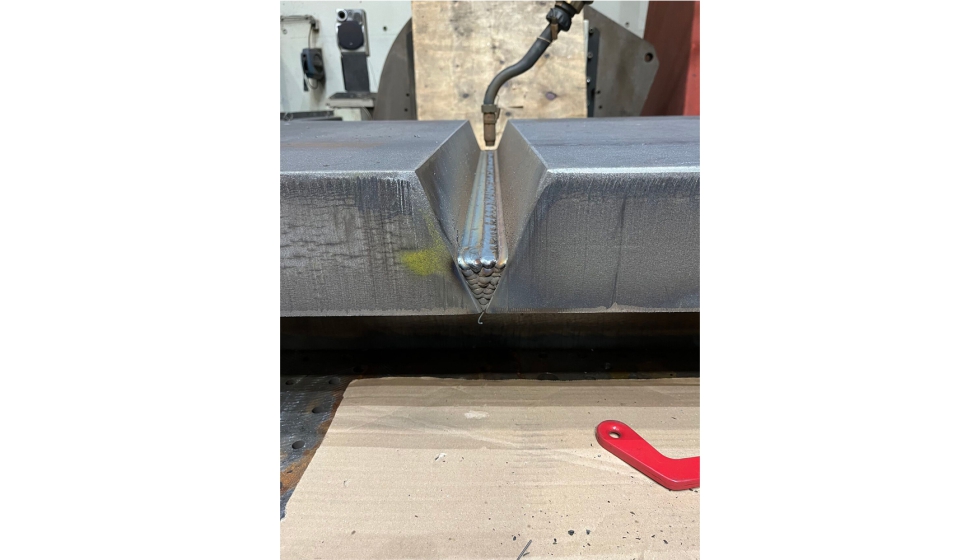
El proceso de alivio de tensiones
Al principio del proceso, es importante tener en cuenta el posicionamiento correcto de la pieza de trabajo, además del material y el peso del componente. A continuación, se determinan la aceleración mínima requerida en el componente de diez metros por segundo al cuadrado y la velocidad máxima de hasta 6.000 revoluciones por minuto y se ajustan al nivel de las frecuencias naturales. El martillo modal genera múltiples impulsos de fuerza golpeando el componente brevemente y con fuerza. Durante la descarga vibratoria, dos transductores de vibración miden y controlan la aceleración desencadenada en el componente por el impulso aplicado. Un acelerómetro triaxial mide la aceleración de la pieza en los ejes X, Y y Z. Un sensor monoaxial mide la aceleración aplicada en el punto de la placa más alejado del motor.
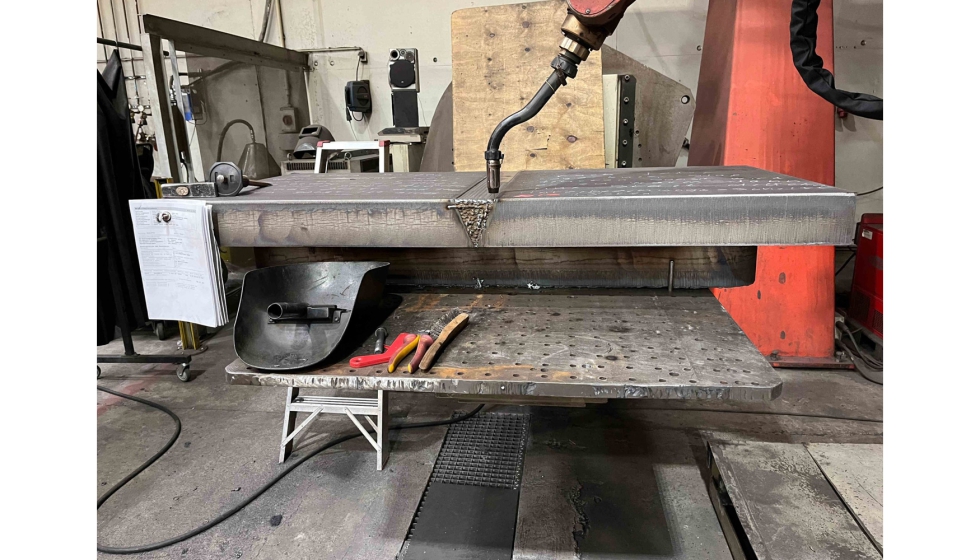
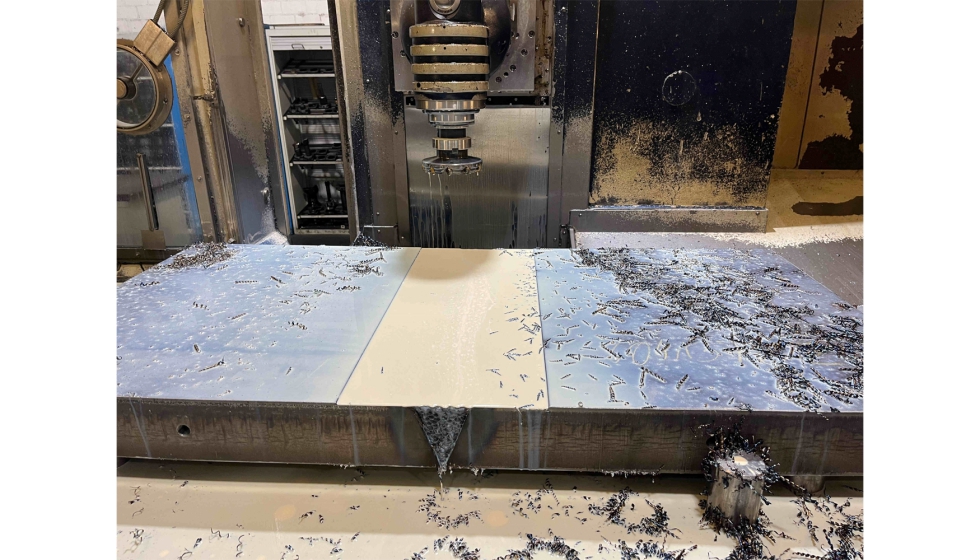
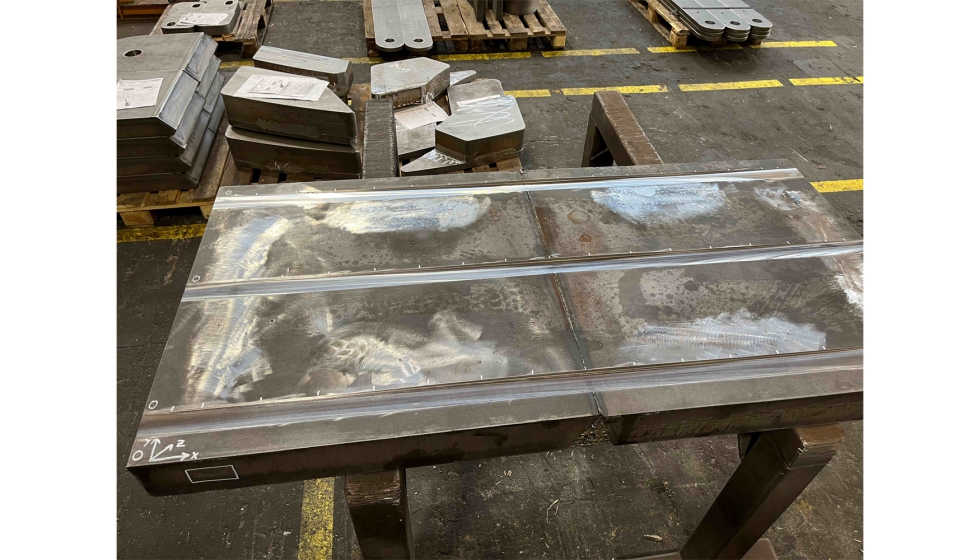
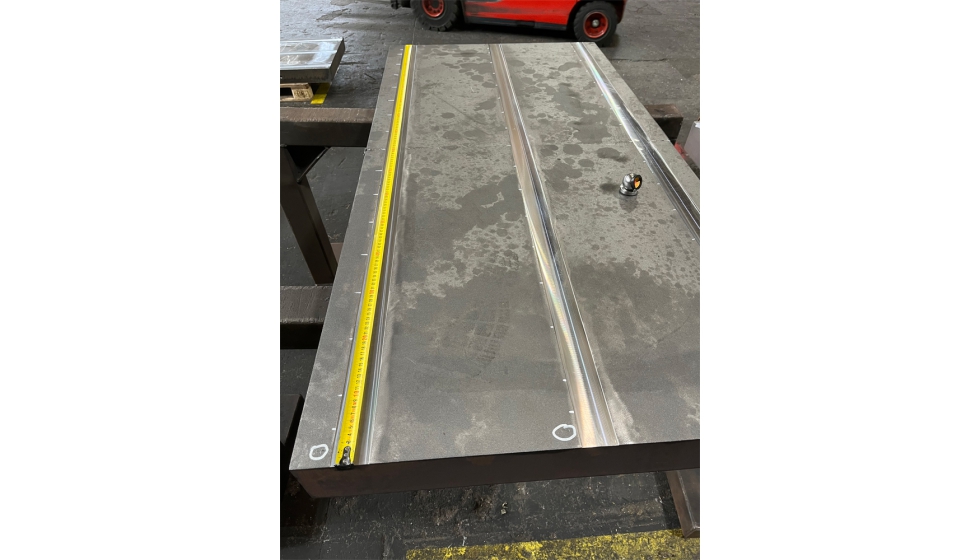
Según VSR Industrietechnik, el análisis modal ha proporcionado pruebas científicamente válidas de que las tensiones residuales en el componente se han reducido hasta tal punto que puede descartarse la distorsión en el componente. La baja amplitud de vibración también elimina la formación de grietas en los componentes. La empresa de Duisburgo ha vendido hasta la fecha unos 150 sistemas vibratorios de alivio de tensiones. Empresas industriales de renombre como ThyssenKrupp, Audi, Ford, Caterpillar, Liebherr y Sennebogen utilizan este proceso en su propia producción desde hace décadas o han prescrito su uso a sus proveedores. También en Jebens, muchos clientes industriales exigentes confían ya en la descarga vibratoria de tensiones para componentes de prensas plegadoras con pesos de pieza de hasta 100 toneladas, para manipuladores de forja con pesos de pieza de hasta 40 toneladas o para prensas con pesos de pieza de hasta 80 toneladas.
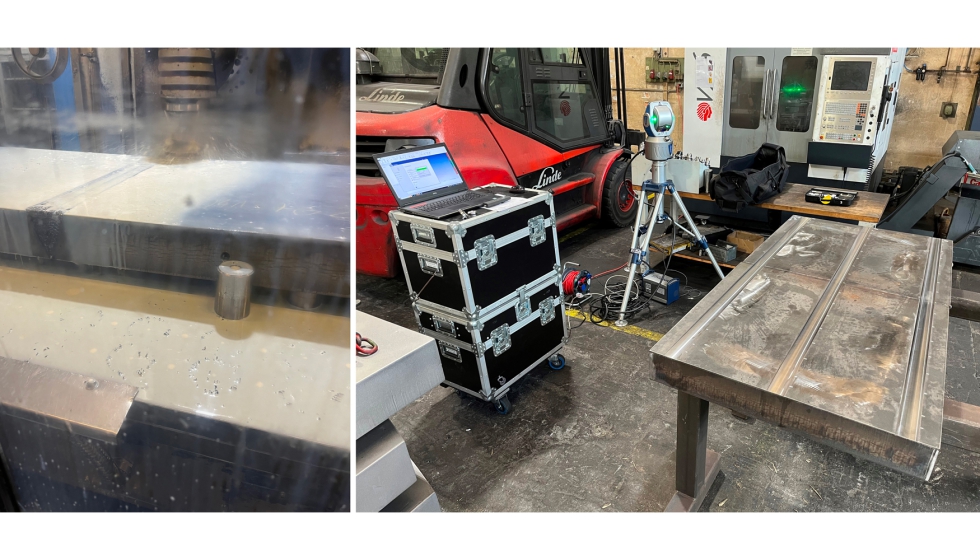
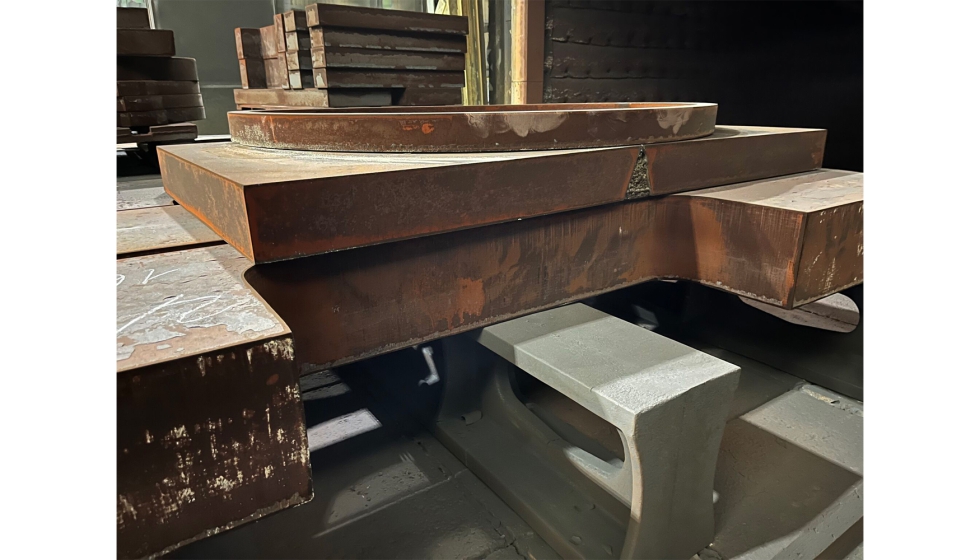
Las ventajas
Este método presenta numerosas ventajas: mientras que un proceso medio de recocido de alivio de tensiones emite unas 6,6 toneladas de CO2, las emisiones de CO2 del alivio de tensiones por vibración son de sólo 0,03 toneladas. El consumo de energía de 32.400 kWh para el recocido de alivio de tensiones contrasta con los sólo 8 kWh del alivio de tensiones por vibración. El tiempo necesario también es significativamente menor: un proceso de horno suele requerir 72 horas, mientras que el alivio de tensiones por vibración para componentes grandes sólo tarda unas ocho horas. Además, el alivio de tensiones por vibración no produce una capa de cascarilla en el componente, que tendría que eliminarse mediante chorro de arena. Esto no sólo elimina la necesidad de un costoso tratamiento posterior, sino que también es más respetuoso con el material. Por lo general, tampoco es necesario el enderezado posterior, ya que no se produce ninguna distorsión durante el alivio de tensiones por vibración. Dado que cualquier tamaño de componente de entre 100 kilogramos y 200 toneladas, e incluso las geometrías extremas de los componentes, pueden tratarse in situ, no es necesario transportarlos a un horno de recocido adecuado. A pesar de los mayores costes de mano de obra durante el tratamiento, el enorme ahorro de energía, posprocesado, transporte y tiempo hacen del alivio de tensiones por vibración una solución considerablemente más rentable para reducir las tensiones residuales. Desde el punto de vista de Jebens, otro argumento a favor de este proceso era que las dimensiones de los componentes que producimos aquí son a menudo tan grandes que el recocido completo no es posible o sólo se puede conseguir un horno adecuado con un esfuerzo considerable. Por último, pero no por ello menos importante, el recocido no es viable para los componentes templados, ya que no se produciría un alivio significativo de la tensión a la temperatura de recocido permitida.
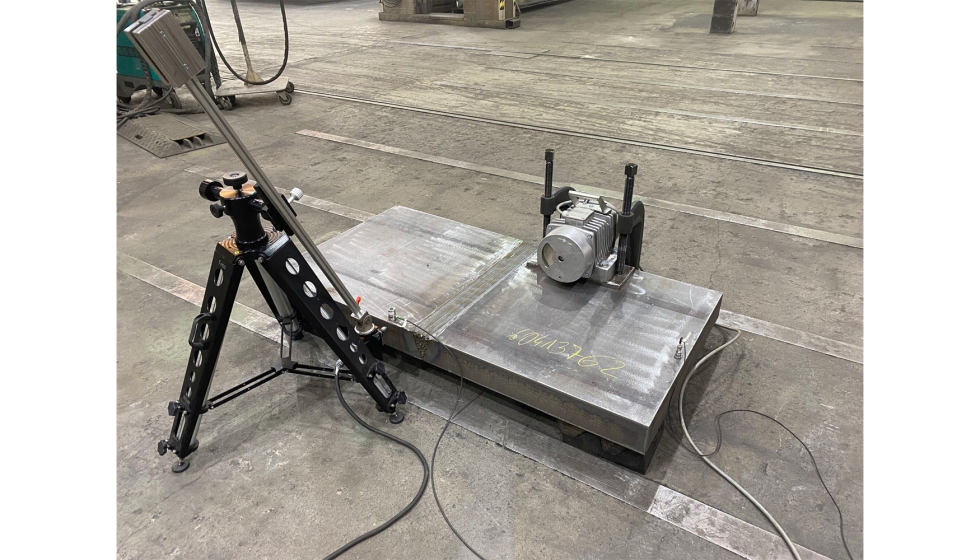
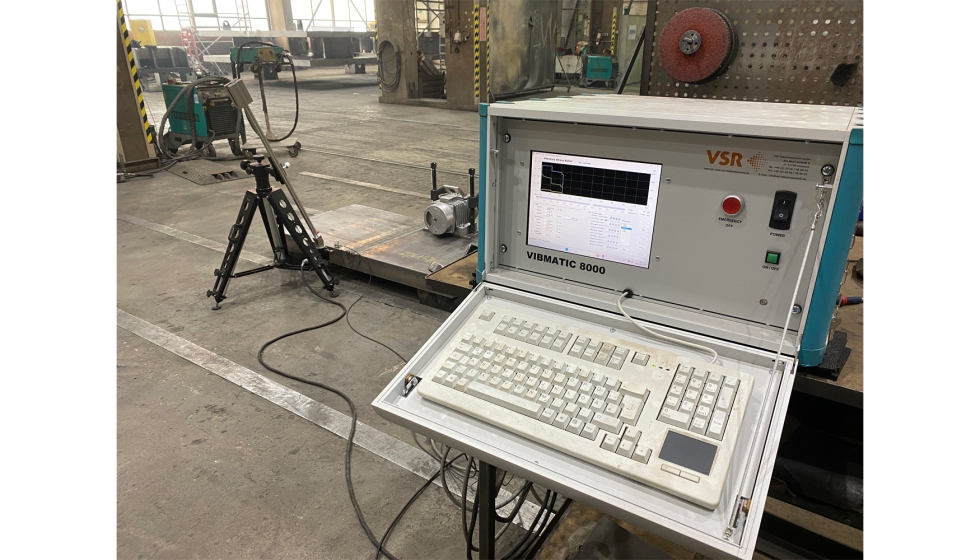
La prueba comparativa
No obstante, Jebens también tiene clientes que aún no han autorizado el proceso. A diferencia del recocido de alivio de tensiones, en la directriz FKM no hay ningún factor establecido para calcular la resistencia de los componentes de las máquinas como directriz de diseño para probar la resistencia a la fatiga. Por este motivo, Jebens llevó a cabo un ensayo comparativo ampliamente observado sobre la deformación durante el fresado de componentes recocidos por alivio de tensión y componentes sometidos a alivio de tensión por vibración. El objetivo de esta prueba era extraer conclusiones sobre el estado de tensión en el componente. Para ello, Jebens cortó dos placas de 110 milímetros de espesor a 800 x 800 milímetros. A continuación, aplicaron una preparación de soldadura para una costura en V 110 en uno de los lados y clavaron los componentes a mano. A continuación, se soldaron con un robot soldador. Ambas soldaduras se realizaron con los mismos parámetros. Los parámetros también se seleccionaron para maximizar las tensiones residuales en la zona del cordón de soldadura. A continuación, un conjunto de placas se sometió a un recocido de alivio de tensiones y el otro a un alivio de tensiones por vibración. El fresado en la zona del cordón de soldadura debería provocar entonces un cambio en las tensiones residuales de los componentes y dar lugar a la deformación de las piezas. A diferencia de la deformación, la tensión residual no puede medirse en un componente, por lo que se fresaron tres ranuras de medición en la parte posterior de cada juego de placas. Las respectivas desviaciones de planitud en estas ranuras debían medirse con láser después de cada fresado. En este estado se realizó una medición inicial como medición cero. En la parte superior del cordón de soldadura se fresó una amplia trayectoria de fresado para fresar completamente el material de soldadura y la zona afectada por el calor. Se introdujeron tres milímetros por cada pasada de fresado. En total se realizaron tres procesos de fresado con un espesor de viruta de tres milímetros. Los dos primeros procesos se fresaron con lubricante refrigerante, el tercero sin lubricante refrigerante. Además, los distintos procesos de fresado se realizaron siempre con los mismos parámetros. Después de cada pasada, se midió la planitud de las ranuras de medición y se introdujo en un gráfico, en el que cada pista se muestra por separado. La escala normalizada de los diagramas permitió comparar directamente los resultados: en el componente sometido a alivio de tensiones por vibración, el pandeo era sólo un tercio del del componente recocido sometido a alivio de tensiones. De esto, Jebens puede deducir que las tensiones residuales en el componente sometido a alivio de tensión por vibración son menores que en el componente recocido por alivio de tensión. Un estudio teórico realizado hace unos años por VSR con la Universidad RWTH de Aquisgrán confirma este resultado en la práctica. Los investigadores de Aquisgrán utilizaron cálculos de elementos finitos para demostrar que el alivio de tensiones por vibración es más eficaz que el recocido de alivio de tensiones.

Estos resultados también fueron confirmados por usuarios como Audi, Ford y ThyssenKrupp en sus propias pruebas prácticas, y desde entonces utilizan el proceso. Desde la perspectiva de Jebens y VSR Industrietechnik, el alivio vibratorio de tensiones es un método tan seguro como el recocido de alivio de tensiones convencional, pero lo supera en la mayoría de los casos debido a sus numerosas ventajas.
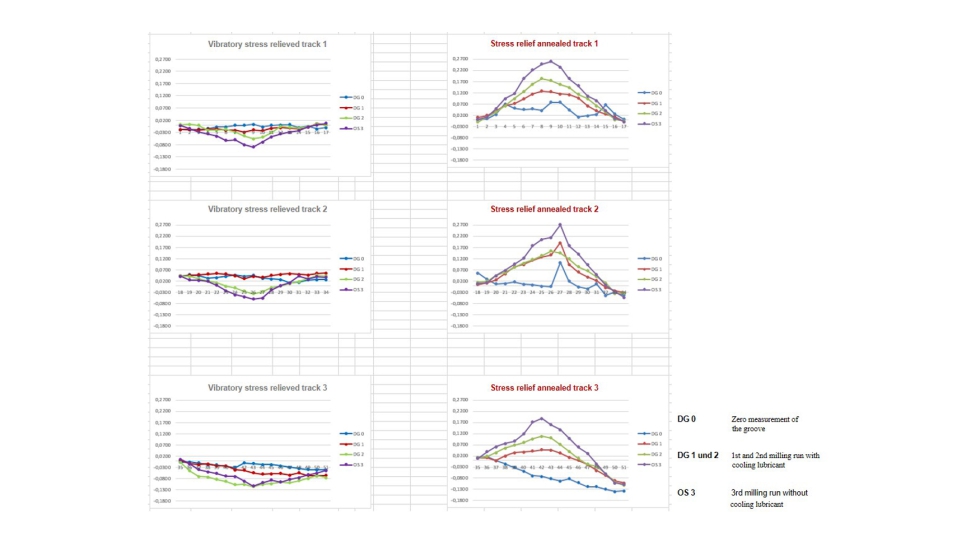