Mayor precisión gracias a un modelo de freno mejorado
Durante aproximadamente un año AutoForm, como responsable del desarrollo del algoritmo, y sus clientes y colaboradores, Matrici S. Coop., asumiendo la dirección de la parte experimental del proyecto, y la Universidad de Mondragón, como experto en el desarrollo de metodologías para la optimización de los procesos de conformado, han trabajado juntas con el fin de aumentar la precisión del cálculo de la fuerza de apertura de los frenos hecho en AutoForm.
¿Qué es un freno y cuál es su función en un proceso de estampación de chapa metálica?
Para asegurar un proceso óptimo de estampación de chapa metálica, consiguiendo una pieza bien estirada, sin roturas ni arrugas, es fundamental controlar el flujo del material. Para ello, se suele actuar principalmente sobre la presión de pisado, sobre la definición de los frenos o sobre la combinación de ambos.
Si se decide actuar sobre los frenos, durante la fase de ingeniería se analiza y ajusta la posición, longitud, forma y retención de los mismos con el fin de conseguir un diseño apropiado. En general, cuando se usan frenos, se deben tener en cuenta varios aspectos para conseguir las condiciones de conformado óptimas:
- La fuerza de pisado necesaria para formar los frenos durante el cierre del pisador
- La influencia de los frenos en la forma de la chapa tras el cierre del pisador
- La fuerza de pisado necesaria para mantener las herramientas cerradas durante el proceso de embutición
- La variación de las propiedades del material en aquellas zonas que han pasado a través del freno
- La entrada del material
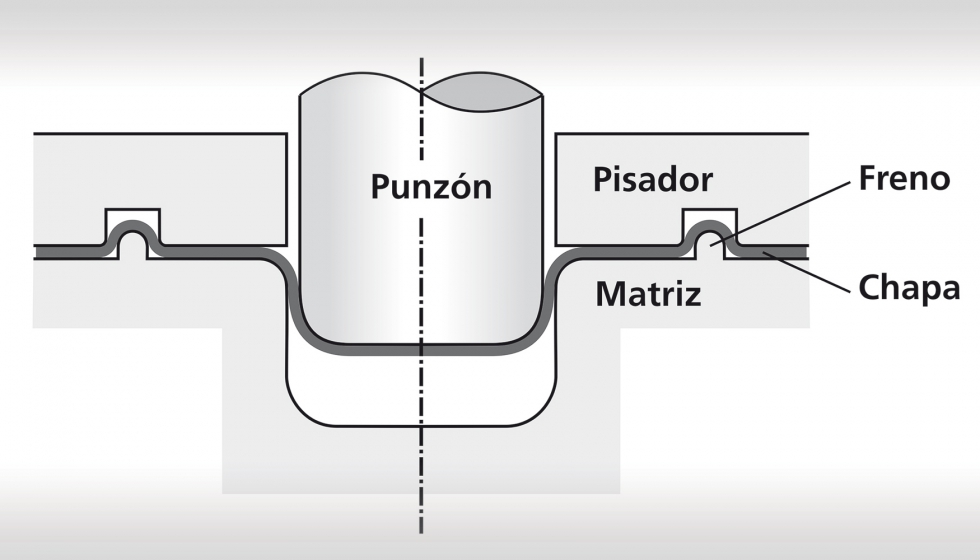
El uso intensivo de este elemento en la estampación y la necesidad de optimizarlo durante la fase de ingeniería requiere un modelo de simulación de freno efectivo. A su vez, este modelo debe ser fácil y rápido de modificar sin que influya en un aumento del tiempo de cálculo.
Este modelo de freno debe calcular con precisión tanto la fuerza de restricción como la fuerza de apertura que ejerce el freno contra las herramientas. Esta última es importante para definir la fuerza real necesaria de la matriz para poder conformar los frenos del proceso y mantener el troquel cerrado durante todo el proceso de estampado.
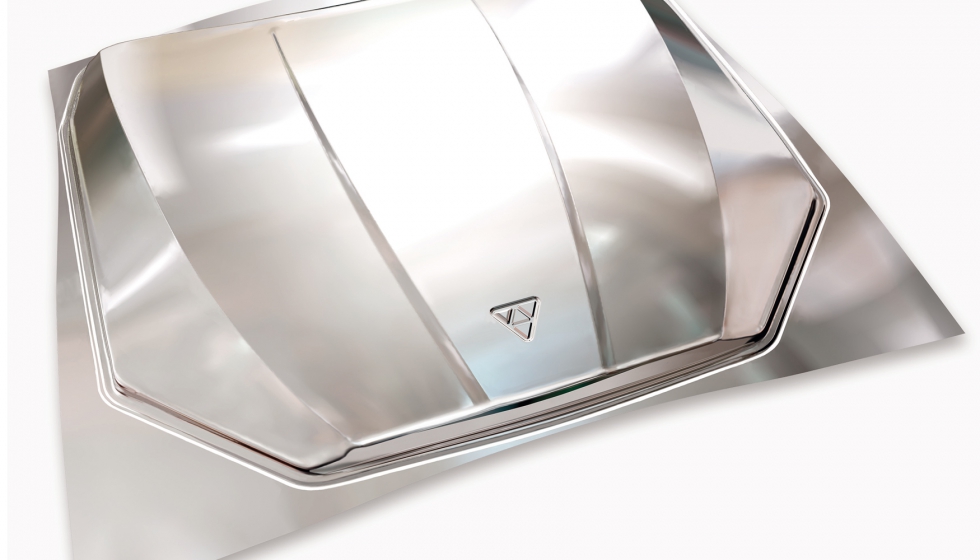
¿En qué consistió el proyecto?
Se realizaron varios ensayos experimentales en las instalaciones de la Universidad de Mondragón, donde se construyó un pequeño útil de embutición, con una geometría de freno redondo de altura variable. Se testearon tres materiales distintos: acero convencional, acero de alto límite elástico y aluminio. El concepto del útil, la geometría del freno y los materiales fueron proporcionados por Matrici S.Coop.
El equipo de desarrollo de AutoForm utilizó los resultados experimentales obtenidos para mejorar el modelo de cálculo y así acercarse más a los datos reales medidos.
Tras un tiempo de estudio y desarrollo por parte de AutoForm, se introdujeron en el software algunas modificaciones en el modelo de freno lineal y se compararon los resultados del modelo mejorado con los datos reales. El resultado fue un éxito. El modelo mejorado de freno se acercaba mucho más a los datos medidos experimentalmente.
No sólo los resultados de las fuerzas de apertura fueron más precisos sino también los valores de adelgazamiento, entrada de chapa y recuperación elástica se acercaban más a la realidad.
El modelo de freno mejorado ha sido implementado en la última versión del software, AutoFormplus R7, presentada en enero de 2017.
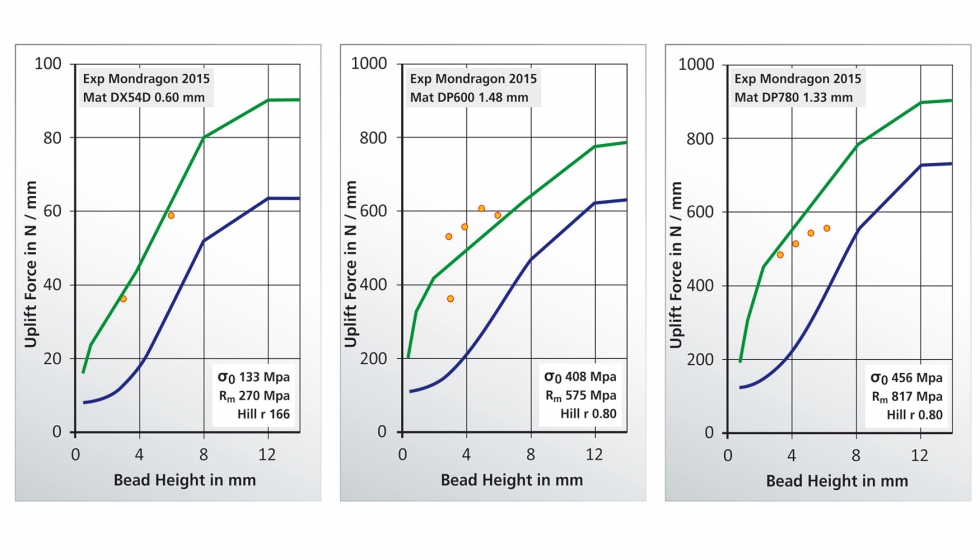
El grupo de investigación de la Universidad de Mondragón se ha mostrado satisfecho con el trabajo realizado y la implementación y añade: “hemos dado un nuevo paso hacia la correcta caracterización de los esfuerzos que entran en juego en el enclavamiento de los frenos en embutición”.
El equipo de ingenieros de desarrollo de AutoForm comenta “los inicios del modelo mejorado de cálculo de fuerzas de frenos se basaron únicamente en conceptos teóricos. En esa primera fase no fue posible una verificación”.
En la Universidad de Mondragón, se desarrolló una herramienta experimental que permitió medir con gran precisión y reproducibilidad los datos de las fuerzas de retención y apertura de los frenos. Estos datos fueron extremadamente útiles para la verificación del nuevo modelo, el cual está disponible en la nueva versión de AutoForm, AutoFormplus R7. Fue un gran placer colaborar con la Universidad de Mondragón y Matrici S. Coop, y estamos muy orgullosos de haber presentado nuestra colaboración en la conferencia Numisheet 2016”.
Matrici S.Coop. es un referente world class en el desarrollo producto-proceso de todo tipo de piezas BiW (Body in white) en el sector del automóvil, con especial mención al ámbito de las piezas de piel (piezas exteriores). Dentro de estas, Matrici S.Coop. es requerido por los principales constructores automovilísticos para el desarrollo tanto del producto, como del proceso de obtención de la pieza que entraña más dificultad dentro de la carrocería, el lateral, siendo actualmente un referente mundial de calidad.
La Universidad de Mondragón es una entidad de iniciativa y vocación sociales. Forma personas en siete áreas de conocimiento distintas y cuenta con cuatro facultades y nueve ubicaciones distintas. Su grupo de investigación de Procesos Avanzados de Conformado de Materiales tiene más de 10 años de experiencia en la modelización de procesos de transformación de chapa. Durante este tiempo el grupo ha focalizado sus actividades en la optimización de la simulación numérica de estos procesos mediante la mejora de los modelos de material y del contacto con las herramientas de conformado.
AutoForm Engineering ofrece soluciones para matricerías y troquelerías durante toda la cadena de proceso. Con 300 empleados dedicados a este campo, AutoForm es un conocido proveedor de software para la factibilidad del producto, cálculo de costes de herramienta y material, diseño de matriz y mejora del proceso virtual. Con sede en Suiza, cuenta con oficinas en Alemania, Holanda, Francia, España, Italia, Estados Unidos, México, Brasil, India, China, Japón y Corea.