Bost ha desarrollado un nuevo concepto de máquinas para el mecanizado de este tipo de piezas. El nuevo concepto aúna rigidez, precisión y un nivel de automatización tal que hace posible su trabajo sin intervención continua de un operario
Mecanizado de un tren de aterrizaje
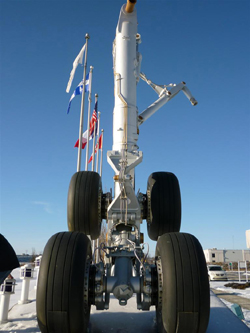
El conjunto del tren de aterrizaje de un avión se compone normalmente de 3 partes: una parte delantera y otras 2 partes bajo las alas. Las partes de las alas son las más robustas por ser las que soportan más peso y las primeras en recibir el impacto a la hora del aterrizaje. Bost ha desarrollado para este tipo de aplicaciones un nuevo concepto de máquina que permite al cliente su uso continuado de forma totalmente automática. La máquina cuenta con un sistema de monitorización de forma que en todo momento se vigila el nivel de vibraciones, temperaturas y consumos de ejes y se contrasta con los niveles máximos que para cada uno de esos parámetros que el fabricante ha fijado. De esta manera, el cliente final puede contar con un sistema de producción que además de ser totalmente automático, es fiable y no depende del buen hacer del operario para detectar anomalías en el proceso de producción. Bost mediante la incorporación de este nivel de automatización y monitorización ha perseguido los siguientes objetivos:
- Reducción de tiempos muertos inherentes a los procesos de verificación manuales.
- Drástica reducción de los fallos generados en el proceso productivo.
- Reducción de los tiempos de mecanizado mediante el incremento de las prestaciones de la máquina con condiciones de corte muy superiores que se pueden aplicar en un proceso de producción o mecanizado menos robusto.
- Reducción de mano de obra directa en el proceso de producción.
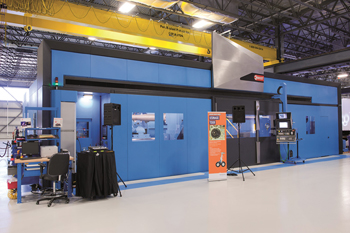
Como parte de este nuevo programa Bost ha entregado al grupo Safran un centro de torneado especial diseñado a las necesidades del cliente dentro de un programa de colaboración. El centro de torneado está diseñado para el mecanizado de los trenes de aterrizaje de los últimos proyectos de las compañías Boeing y Airbus. El torno Bost modelo T4H15 realiza el torneado de la pieza más importante del conjunto del tren de aterrizaje; una pieza donde dependiendo del modelo de avión, se parte de un peso bruto de 6 toneladas. Para terminar, una vez acabado el mecanizado, con un peso de unos 850 kilos. El material de las piezas es un acero aleado especial.
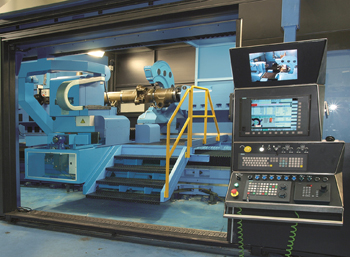
El proceso del mecanizado
La única operación manual que se realiza en la máquina entregada al cliente Safran es la carga y descarga de la pieza en el centro Bost T4H15. Este proceso de carga y descarga se tiene que realizar en el desbaste, antes del tratamiento térmico necesario para la pieza y después de este último para proceder al acabado de la misma.
La tecnología instalada en el centro está enfocada a la supervisión del mecanizado y a la anticipación a posibles incidencias que puedan dañar la pieza. El mecanizado exterior e interior se realiza sin interrupciones salvo que aparezca alguna incidencia detectada por la propia máquina que desemboque en una alarma que obligue a la intervención manual para proceder a su corrección. Por exigencias de proceso específicas del cliente final, es necesario realizar un protocolo de mediciones automáticas que se contrastan con las mediciones fuera de máquina realizadas por el cliente que sirven para realizar ajustes en el proceso automático.
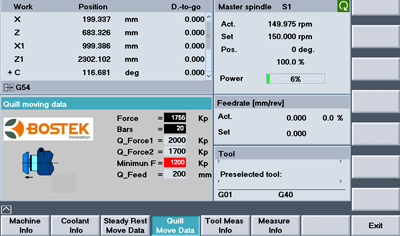
Para el montaje de la pieza, el operario la sitúa entre el utillaje del cabezal y el contrapunto en el otro extremo. El contrapunto está controlado, el operario lo posiciona inicialmente desde un panel que se encuentra en el propio contrapunto. La salida de la caña del contrapunto se realiza por una subrutina. Una vez comprobado el equilibrado del conjunto, el operario cierra el carenado para iniciar el mecanizado. Se inicia el mecanizado en el que los dos carros de la máquina van sucediendo diferentes operaciones para las que requieren diferentes herramientas que son suministradas por parte de un robot que es capaz de:
- Administrar un almacén con capacidad hasta 300 herramientas.
- Gestionar el cambio automático de herramienta a los dos carros de la máquina de forma independiente.
- Gestionar la instalación automática de los dos carros de sondas de medición de pieza de máxima precisión.
- Gestionar el desgaste de herramienta de forma que cuando una plaquita de herramienta llega a su vida útil el robot procede a instalar una herramienta gemela, la máquina incluye los nuevos decalajes necesarios y la herramienta con plaquita desgastada es entregada por parte del robot para que el operario proceda a reponerla.
- Permite el chequeo continuo de la herramienta mediante el sistema de lectura de chip de Balluff. Este sistema de lectura de chip se ejecuta en todos los cambios de herramienta para evitar errores y garantizar que la herramienta real coincide con la teórica.
- Adicionalmente después de cada cambio de herramienta la máquina cuenta con un sistema de presetting “in-process” mediante el que se mide la herramienta y se incorporan al programa de mecanizado las compensaciones necesarias de forma totalmente automática.
Otras tecnologías instaladas en el centro de torneado
- Deslizamiento hidrostático en los 4 ejes de mecanizado. Carros independientes para torneado exterior e interior. Este tipo de guiado aúna la máxima rigidez proporcionado por el colchón de aceite hidrostático con una capacidad de absorción de vibraciones que confiere a la máquina de un excepcional nivel de precisión en las operaciones de acabado con ausencia de las marcas generadas por la vibración. Estas guías, además, permiten a la máquina realizar trabajos de desbaste fuerte sin comprometer su nivel de precisión en las operaciones de acabado debido a la ausencia de contacto superficial entre guía y contraguía hidrostática.
- Medición automática de pieza y herramientas. Software específico desarrollado por Bostek Innovation. Salvaguarda de protocolos de medida automática.
- Software y hardware de control de colisión y rotura de herramientas. Retiradas e interrupciones automáticas del mecanizado. Retiradas automáticas por decisión del operador.
- Barra antivibratoria para el mecanizado interior. Proyecto desarrollado conjuntamente entre Safran, Bostek innovation y Sandvik Coromant. Paso de señal de las sondas de medición de pieza por la barra. Instalación en el interior de hardware para la detección de colisión y rotura de herramienta. Paso de caudal para limpieza y arrastre de virutas del interior de la pieza. Refrigerante de alta y baja presión. Amarre automático de herramienta. Soplado automático de limpieza.
- Refrigerante de corte. Central de refrigerante de corte con varias bombas para mecanizado con alta, baja presión y limpieza. Separador magnético de partículas, separador de aceite, filtrado del retorno del refrigerante por papel continúo. Interrupciones y retiradas automáticas del mecanizado por alarmas de falta de caudal o presión del refrigerante de corte.
- Luneta autocentrante diseñada íntegramente por Bostek Innovation, para conseguir que una pieza tan desequilibrada como el tren de aterrizaje del Boeing 787 Dreamliner no pierda el centro de giro cuando gira a más de 200 rpm. Esto requiere una rigidez del conjunto muy superior a los estándares del mercado para lunetas autocentrantes.
- Posicionamiento del conjunto longitudinalmente por programa. Avance y retroceso transversal automático. Cierre autocentrante programable, diseño exclusivo que garantiza una irreversibilidad total del cierre. Lubricación automática interna a los rodillos. Hardware de detección de vibraciones para el análisis durante el mecanizado de desequilibrio excesivo de pieza y del estado de los rodamientos de la luneta.
- Bancada. Diseño con guías hidrostáticas independientes para los ejes de mecanizado. Doble protección por fuelle y chapas telescópicas de toda la zona.
- Carro exterior e interior de mecanizado. Transmisión longitudinal por doble motor-cremallera. Transmisión transversal por husillos a bolas. Carro de mecanizado exterior con guillotina retráctil, la guillotina en posición de trabajo permite sin colisiones el torneado de las bandas de rodadura de la luneta. Otro carro exclusivo para la barra anti-vibratoria realiza todo el mecanizado interior de la pieza.
- Paneles de mando y cámaras. Permiten la supervisión del proceso de mecanizado. El panel principal se encuentra en el exterior con un desplazamiento longitudinal completo. El operario puede desplazar el control desde la zona del robot hasta el otro extremo. El panel principal tiene desplazamiento en altura, el operario lo ajusta a su conveniencia. Un panel móvil permite el desplazamiento de los ejes y otras funciones durante las operaciones de reglaje dentro de la zona de mecanizado. Paneles fijos a ambos lados del cabezal permiten al operario realizar todas las operaciones en el cabezal durante el montaje de la pieza. Funciones como el bloqueo y giro sensitivo del cabezal y la selección de un punto muerto que permite la operación de equilibrado del conjunto pieza-utillaje.
Como en todas las máquinas de Bost, la máquina T4H15 cuenta con una gran cantidad de ciclos de fabricante tanto para el mecanizado como para la medición automática de la pieza. Este nivel de personalización es una constante en las máquinas de Bost que siempre ofrece a sus clientes un nivel de detalle en los ciclos de trabajo que permite reducir la complejidad de la programación por parte del propio cliente. Este alto nivel de personalización forma parte de las características del proyecto llave en mano que Bost entrega junto con sus máquinas.
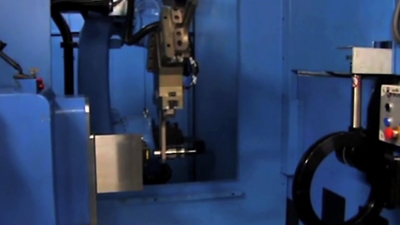
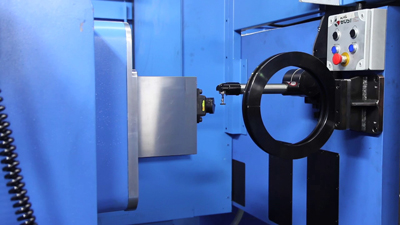
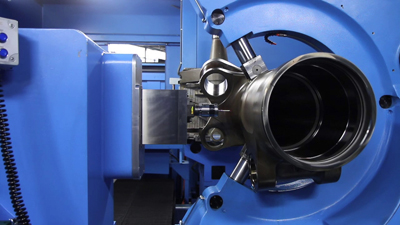
La máquina T4H15 cuenta también con un complejo sistema de monitorización continua que mide, entre otros parámetros, las fuerzas de corte generadas por cada herramienta. La señal de dos acelerómetros instalados en la barra comparan las señales actuales con las señales de aprendizaje registradas anteriormente.
Cuando la señal sobrepasa un umbral por rotura de plaquita u otro motivo… una subrutina controla la interrupción segura del mecanizado.
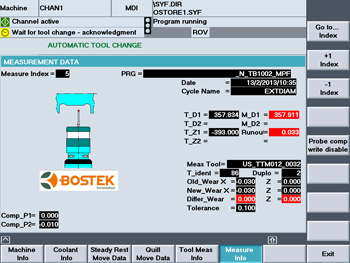
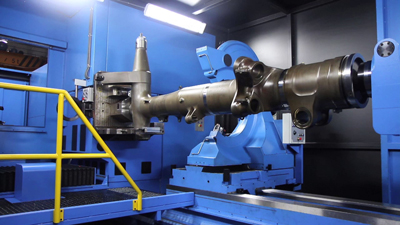
El refrigerante de corte es también monitorizado durante el proceso. Desde una pantalla interactiva o desde el programa de mecanizado, se ajustan los valores para la visualización de mensajes o alarmas por falta del caudal o presión requerido en cada momento. La aparición de una alarma, activa la subrutina de interrupción del mecanizado. También se utilizan en el proceso herramientas de corte específicas para alta presión.
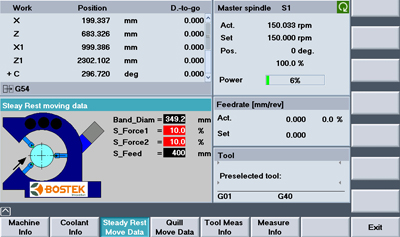
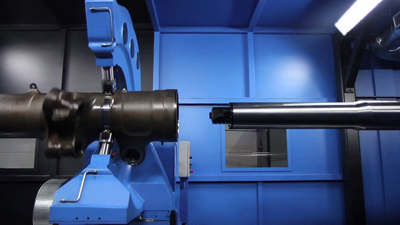
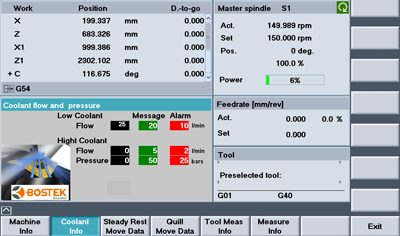
El mecanizado interno requiere el uso de herramientas gemelas. El software de gestión de herramientas junto con el programa de mecanizado, controlan la vida útil de las herramientas y su remplazo por una de sus gemelas. Estas herramientas con vida agotada quedan registradas en el almacén de herramientas y el operario en cualquier momento puede pedir su descarga automática para su reparación. El ciclo de mecanizado termina posicionando todos los ejes de mecanizado en su lugar de ‘parking’. El contrapunto y su caña vuelven automáticamente a su posición inicial sujetando la pieza. En este momento la luneta se abre automáticamente, se retira transversalmente y vuelve a su posición de ‘parking’. La máquina queda lista para el desmontaje de la pieza actual y el montaje de la siguiente.
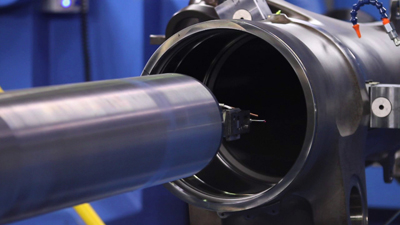
Los protocolos de medida de herramienta y de medida de la pieza han quedado registrados en 2 ficheros en la memoria del control. El operario puede enviar estos ficheros por DNC a un ordenador central para su archivo y en las pantallas interactivas del control quedan también registrados los últimos 50 ciclos de medida de herramienta y los 50 últimos ciclos de medida de pieza.
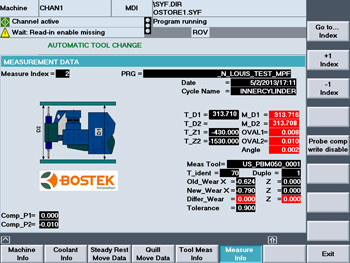
En definitiva, el T4H15 de Bost es una máquina moderna para procesos modernos a la vanguardia de la tecnología dentro del sector de la máquina herramienta. Una máquina con un alto nivel de prestaciones y productividad y un nivel de precisión y fiabilidad, por encima del estado del arte en la actualidad.
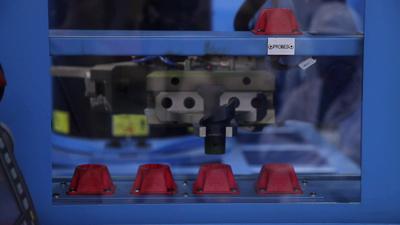