‘Window Wall’: análisis, diseño y ejecución
Este artículo es un resumen de un Trabajo de Fin de Máster del Máster de Fachadas Ligeras de la Universidad del País Vasco (UPV-EHU), cursado en 2021-2022. En este caso, su autora describe un nuevo sistema de fachada autoportante, especialmente indicado para obras de rehabilitación e industrialización.
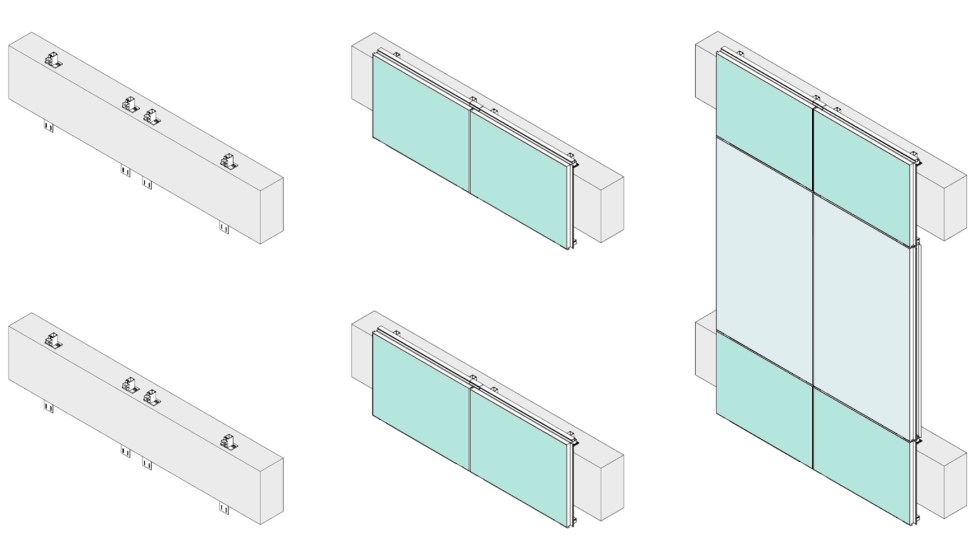
‘Window Wall’
El ‘window wall’ es una tipología de envolvente enmarcada dentro de la fachada ligera, lo que implica que no tiene una funcionalidad estructural, no recibe cargas derivadas del edificio. Es un sistema de fachada autoportante que confiere la estética exterior a la edificación, soportando y transmitiendo las cargas de viento y peso propio a la estructura portante.
La instalación en obra del ‘window wall’ se realiza entre forjados, lo que implica una discontinuidad del sistema entre plantas. Al contario del muro cortina, este sistema no pasa por delante del forjado, siendo interrumpido por la presencia de la losa.
El muro cortina se adhiere al exterior de las losas del edificio, donde su propio apelativo de ‘cortina’ le confiere su condición de elemento colgado. Al contario que el ‘‘window wall’’, cuyo funcionamientoestructural se basa en el apoyo del módulo en el forjado inferior.
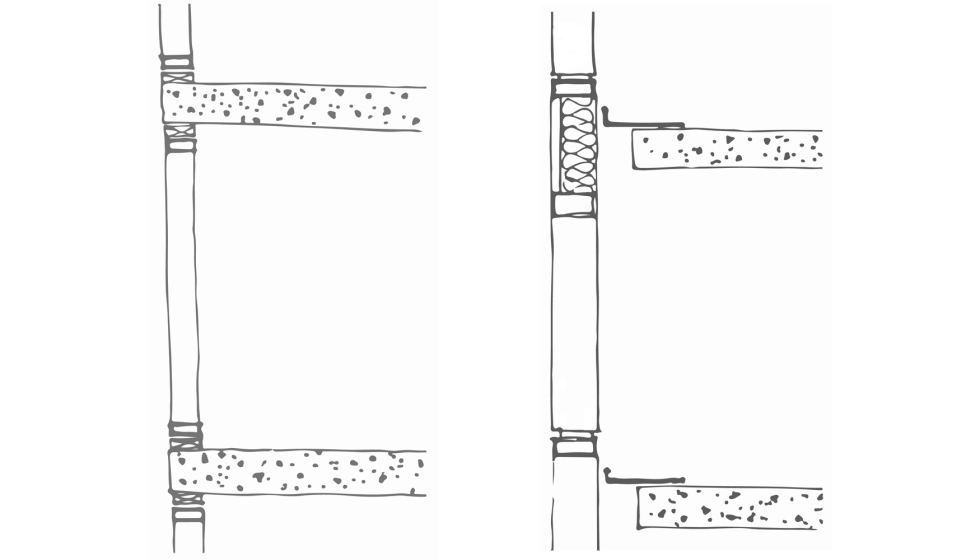
Esta diferencia en la disposición en fachada es un condicionante en el dimensionamiento de los perfiles de ambos sistemas. Mientras que el muro cortina necesita perfiles con mayor inercia y tamaño al abarcar luces de mayores dimensiones, el ‘window wall’ debido a su condición de elemento entre forjados, podrá diseñarse con una perfilería más reducida y compacta.
Tiene la característica de ser un sistema modular. Esto implica que la fabricación y ensamblaje, hasta la composición final del módulo, se realiza en taller, bajo unas condiciones ambientales y de ejecución controladas.
El hecho de que los módulos salgan de fábrica totalmente terminados nos permite una optimización de los tiempos de instalación en obra, al igual que con el muro cortina modular.
Un tema importante en el diseño de este sistema es el tratamiento del frente de forjado, ya que, como se ha explicado, su condición de fijación entre losas nos obliga a solucionar la continuidad de la envolvente en este punto.
Este frente suele tratarse con bandejas metálicas o elementos cerámicos o de vidrio, instalados independientemente a los módulos de fachada.
‘Window Wall’ vs Curtain Wall
Tras el análisis del sistema, surge la necesidad de realizar una comparativa con lo que podríamos denominar como el principal competidor del ‘window wall’, el muro cortina.
Dicha comparativa nos permitirá concretar las posibilidades (luces y sombras) del sistema.
1. Montaje
El primer punto en la comparativa del procedimiento de montaje de ambos sistemas, residirá en la localización (exterior o interior) de los operarios y medios auxiliares para llevar a cabo los trabajos de instalación.
En el muro cortina (según tipología) encontramos ambas opciones. El muro cortina stick se caracteriza por la presencia de medios auxiliares en el exterior, para la instalación del entramado de perfiles y los posteriores elementos de relleno. Por el contrario, en el muro cortina modular, todo el procedimiento de montaje de los módulos se realiza desde el interior del edificio.
En cuanto al ‘window wall’, la instalación se produce desde el interior, al igual que en el caso del modular.
Esta diferencia entre el sistema stick y los modulares reside en la propia concepción del sistema, al tratarse el primero, de una tipología cuyo ensamblaje entre perfiles e instalación de paneles se produce de forma íntegra en obra.
Este es un aspecto muy valorado actualmente en los sistemas modulares, debido a que el ensamblaje total del módulo se realiza en taller, bajo un entorno controlado, mientras que el resultado final del sistema stick se ve supeditado por las condiciones de la obra.
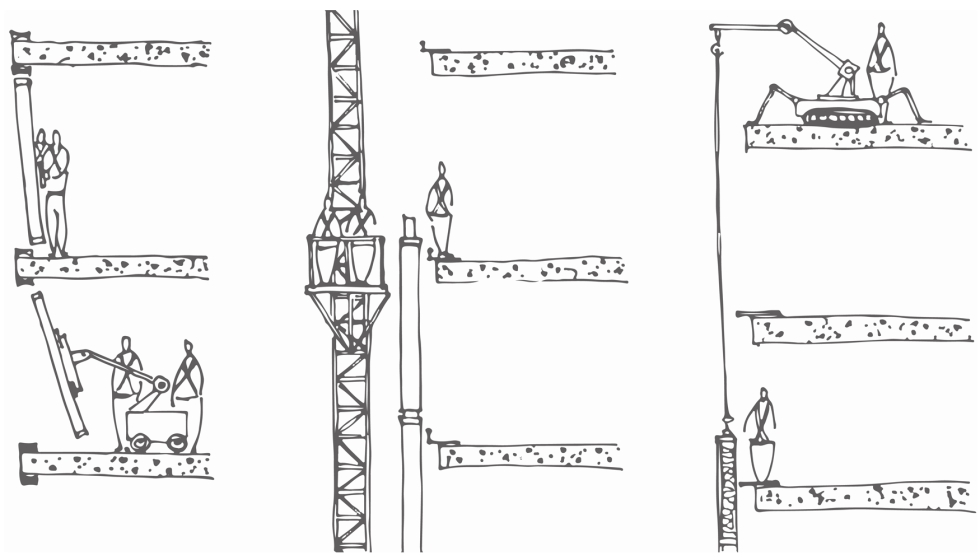
La instalación desde el exterior o el interior es un determinante que condiciona la elección de un sistema u otro, ya que debemos estudiar su viabilidad. En ocasiones, la localización de nuestro proyecto o las condiciones de entorno no nos permiten la instalación de medios auxiliares en el exterior, por lo que la opción de un sistema stick queda descartada.
El sistema de fachada no solo condiciona los medios auxiliares necesarios desde el punto de vista de su localización, sino también del tamaño de los mismos.
Tanto en el muro cortina modular como en el ‘window wall’ la instalación se realiza desde el interior, pero los medios auxiliares pueden no ser los mismos.
En el caso del muro cortina modular, debido a la dimensión de los módulos y a la envergadura de los perfiles que lo conforman, la instalación suele realizarse con la ayuda de una minigrúa o ‘spyder’, capaz de soportar el peso de los mismos.
Por su parte, en el ‘window wall’, al tratarse de módulos de menor dimensión y peso pueden instalarse en muchos casos mediante un robot de acristalamiento con ventosas o con el esfuerzo de los operarios.
Los medios auxiliares necesarios no solo repercuten en la planificación del procedimiento de montaje del sistema, también son un factor importante a tener en cuenta en la valoración económica
2. Tratamiento frente de forjado
La instalación entre forjados característica del ‘window wall’, y la continuidad por delante del mismo, del muro cortina nos permite analizar las consecuencias derivadas de esta disposición en fachada. El tratamiento del frente de forjado.
En el muro cortina, su posición adelantada respecto al frente de forjado y la separación que se produce con el mismo, nos obliga a realizar un tratamiento de este frente a nivel acústico y de propagación de incendios, evitando de esta forma la transmisión de ambos fenómenos de una planta a otra.
Por el contrario, en el ‘window wall’, debido a su disposición entre plantas, es el propio forjado el que actúa como barrera ante la transmisión del sonido y del fuego.

Desde el punto de vista contra incendios, aunque bien es cierto que el ‘window wall’ parte con una barrera ‘natural’ (el forjado), debemos tener muy en cuenta la normativa vigente de cada país.
En nuestro caso, la necesidad de disponer de una barrera al fuego de al menos un metro de altura entre plantas, nos obliga a adoptar diferentes estrategias para la implantación de este sistema. Una posible solución para la implantación del mismo, sería ejecutar un antepecho opaco de la altura necesaria a partir del cual, arranque nuestro ‘window wall’.
3. Comportamiento estructural
Atendiendo al comportamiento estructural, la condición de sistema colgado del muro cortina, y de apoyado en del ‘window wall’, es una de las características que más los diferencia.
El muro cortina se caracteriza, en la gran mayoría de los casos, por trabajar colgado. Esto significa que las cargas derivadas del peso propio del módulo son transmitidas a través de los montantes hasta el anclaje superior, un punto fijo que soporta la totalidad del peso. Por el contrario, las cargas de viento soportadas por la fachada, se transmitirán también a través de los montantes, pero en este caso se repartirá entre el anclaje superior e inferior, generando en este último el punto de dilatación.
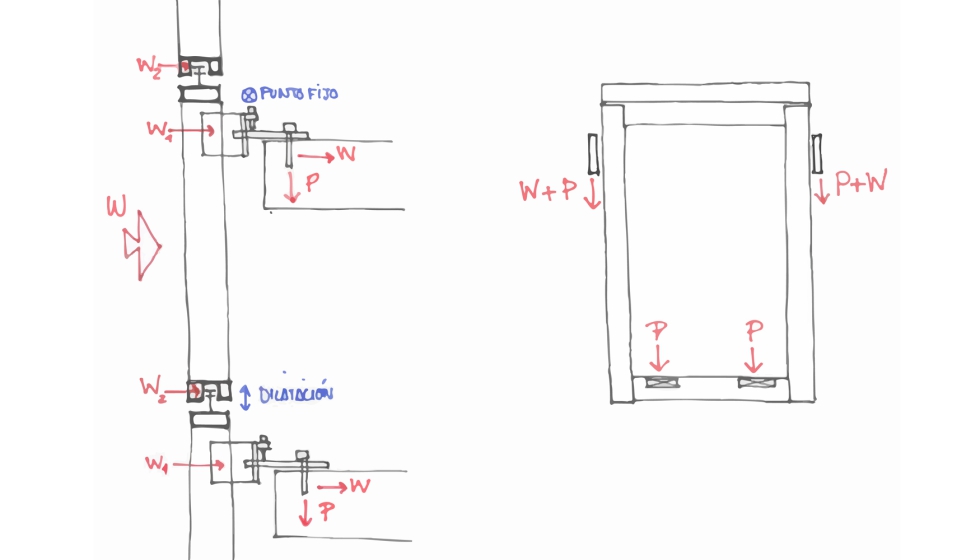
El concepto estructural del ‘window wall’ es precisamente el contrario, el módulo trabaja apoyado.
En este caso, la carga de peso propio se transmite directamente del travesaño inferior al forjado a través del perfil inferior corrido, por lo que los montantes solo trabajarán a viento, repartiendo esta carga entre el travesaño superior e inferior, encargados de transmitir las cargas al forjado.
En el ‘window wall’ el punto fijo se sitúa en el travesaño inferior, mientras que el superior se convierte en punto de dilatación al trabajar solo a viento.
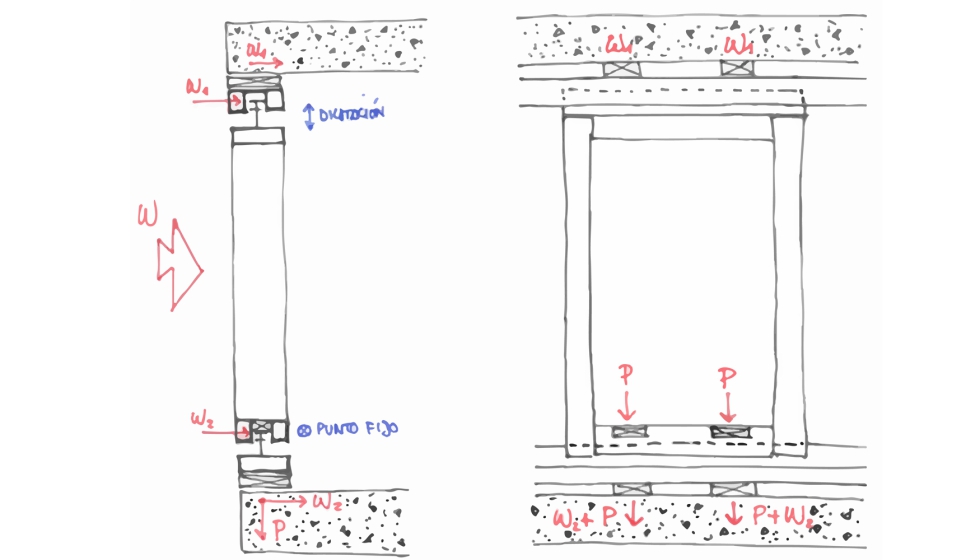
Oportunidad de implantación
El muro cortina se sitúa en una posición adelantada a la estructura portante del edificio, al pasar por delante de la misma, lo que implica un determinado saliente de la fachada respecto de la estructura.
Por el contrario, el ‘window wall’ queda prácticamente enrasado con el forjado, adelantando escasamente su posición para el tratamiento del frente del forjado.
Esta es la principal característica que convierte al ‘window wall’ en un sistema idóneo para las obras de rehabilitación. En este tipo de proyectos, en muchas ocasiones, estamos condicionados por la línea exterior preexistente de la envolvente, por lo que si queremos darle a nuestro edificio una apariencia exterior de todo vidrio, la implantación de un muro cortina aumenta su complejidad, debido a su condición de posición adelantada respecto de la estructura portante. Esto nos obligaría a mecanizar los montantes puntualmente en la zona de las losas o las vigas de borde, perdiendo en gran medida su capacidad portante, o a aplicar un muro cortina stick apoyado entre forjados, pero perdiendo de esta forma las ventajas de un sistema modular.
Otra tipología edificatoria dónde podríamos aplicar el ‘window wall’, es en aquellos proyectos donde aparece una segunda piel que debido a sus dimensiones y peso necesita ir anclada directamente a la estructura portante.
La fachada se ejecutaría de fuera a adentro, llevando a cabo en primer lugar la instalación de la piel exterior, anclándola a la estructura portante del edificio. Después, mediante la utilización de medios auxiliares desde el interior, realizaríamos el tratamiento del frente de forjado, salvando las penetraciones de las ménsulas. Para finalmente instalar los módulos de visión.
Sistema
Para el desarrollo del ‘window wall’ es necesario establecer una serie de premisas que nuestro sistema debe cumplir, las cuáles nos guiarán en la toma de decisiones ante las casuísticas que puedan surgir a lo largo del desarrollo del mismo.
1. Línea exterior de vidrio
Para poder respetar en la medida de lo posible la línea exterior preexistente de fachada, planteamos reducir los montantes en el módulo opaco para poder situarlo por delante del frente de forjado cumpliendo con la premisa fijada.
Esta decisión condiciona el funcionamiento estructural del módulo y debemos hacer un planteamiento del mismo para que el sistema funcione.
Al reducir a la mínima expresión los montantes, su inercia o capacidad portante frente a las cargas de viento será insuficiente. Por este motivo planteamos un vidrio monolítico que trabaje a dos lados, los travesaños serán los que trabajen a viento transmitiendo la carga a los forjados.
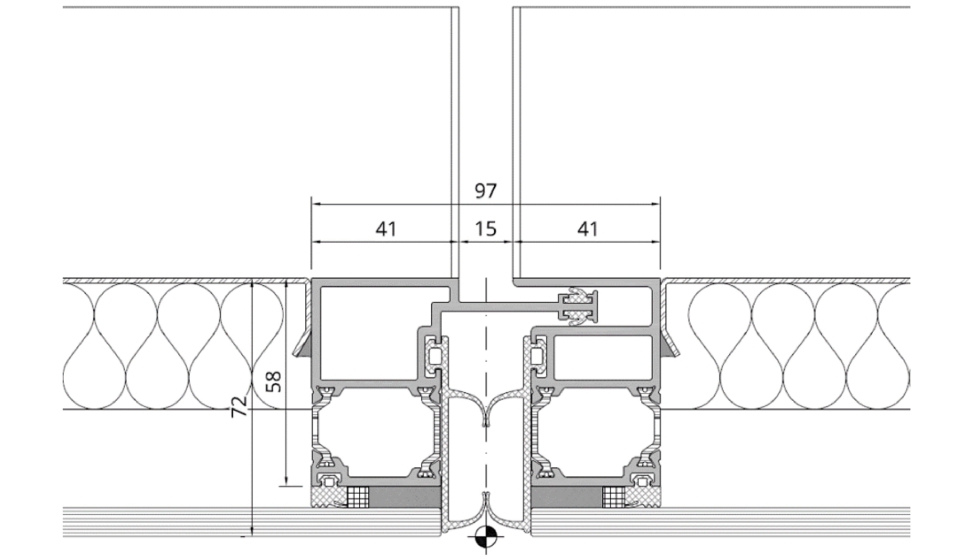
En el caso de la carga de peso, el módulo trabajará colgado. Dicha carga se transmitirá desde los apoya vidrios al travesaño inferior o hembra, los montantes actuarán como tirantes, transfiriendo la carga al travesaño superior o macho, y de ahí al forjado.
2. Instalación módulo de visión
En el ‘window wall’ tradicional, tal y como hemos analizado, el módulo de visión trabaja apoyado, lo que conlleva a instalar en primer lugar los perfiles continuos corridos donde se machihembra el mismo.
En nuestro caso, replicaremos esta secuencia de montaje debido a que es el módulo opaco el encargado de transferir a los anclajes sus propias cargas y las derivadas del módulo de visión.
Por lo tanto, al instalar en primer lugar los módulos de frente de forjado, debemos diseñar como machihembrar posteriormente el módulo de visión.
Para ello, el travesaño hembra del módulo opaco estará compuesto por dos perfiles de aluminio. El primero de ellos conformará el cuerpo principal del perfil, mientras que el segundo será una tapa posterior que atornillaremos al primero.
Los motivos de este diseño son, por un lado, permitir la instalación del módulo de visión desde el interior y, por el otro, poder tener acceso para el tratamiento de la junta entre módulos.
Al dejar abierta la parte posterior del perfil, tenemos el juego suficiente para aproximarnos con el módulo ligeramente inclinado hasta el punto de instalación, introducir el travesaño macho en esta cavidad y llevarlo al sitio apoyando el travesaño hembra en el macho del módulo opaco.
Terminada la secuencia de montaje y previo a la instalación de la tapa posterior, se llevará a cabo el saneamiento de junta entre módulos.

01.- Encaje de travesaño macho. 02.- Apoyo sobre módulo opaco. 03.- Tratamiento junta. 04.- Fijación tapa trasera.
3. Tratamiento de juntas
En los sistemas modulares, el punto más crítico a nivel de estanqueidad al agua y permeabilidad al aire se produce en el encuentro entre módulos.
En nuestro caso, este punto duplica su relevancia debido a que tenemos dos juntas en lugar de una, como ocurre en los sistemas modulares tradicionales.
La primera de ellas la definiremos como la junta opaco-visión, en la que se produce el machiembrado mediante el apoyo del travesaño hembra del módulo de visión sobre el travesaño macho del módulo opaco.
El tratamiento de esta primera junta horizontal se llevará a cabo de igual forma que en un sistema modular tipo, tratando este punto previamente a la instalación del módulo de visión.
Aplicaremos una cama de silicona sobre la junta horizontal entre módulos opacos, que servirá de asentamiento al perfil puntual en forma de ‘L’ que denominaremos camisa. Deslizaremos dicho perfil hasta su posición y lo sellaremos perimetralmente, prestando especial atención al encuentro entre las gomas de machiembrado de los travesaños, aplicando silicona para cerrar este punto.
La camisa tendrá una doble funcionalidad, por un lado, a nivel estructural, ya que de esta forma reforzamos la zona dónde el montante transmite las cargas de viento al travesaño inferior.
Y por otro, a nivel de estanqueidad, ya que la función de esta pieza es dar continuidad a los travesaños.
Por último, aplicaremos una banda puntual de flexiband sobre los machos de los travesaños. Para que cuando instalemos el módulo de visión, esta banda rellene la cavidad del travesaño hembra, bloqueando las filtraciones de aire que se producen en la parte inferior del machiembrado de los montantes.
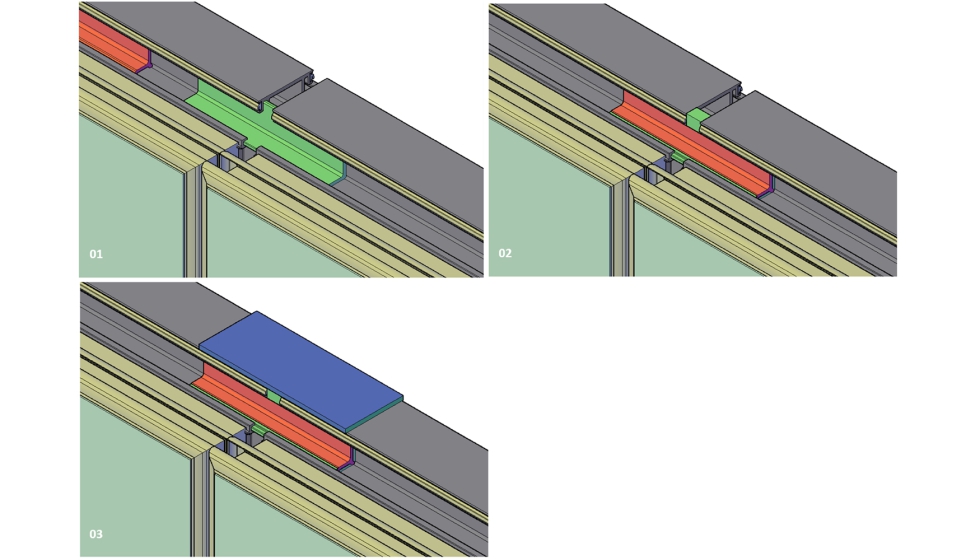
01.- Aplicar cama de silicona; 02.- Posicionar camisa y sellar; 03.- Instalar flexiband
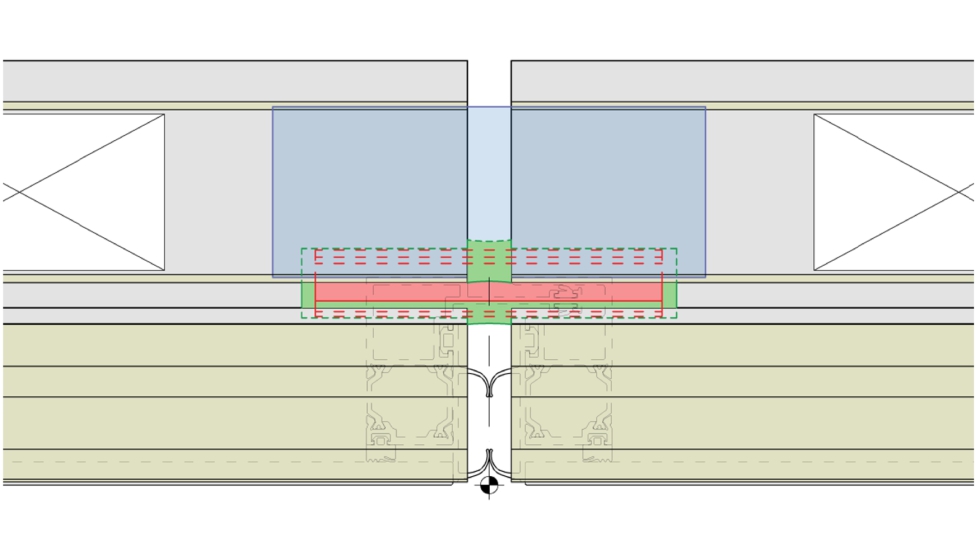
Vista en planta junta opaco – visión: Cama de silicona. Camisa. Flexiband.
La segunda junta horizontal de nuestro sistema la definiremos como junta visión-opaco, y es la que se produce precisamente en el encuentro entre el travesaño macho del módulo de visión y el travesaño hembra del módulo opaco.
El tratamiento de esta junta es más delicado que en el caso anterior, ya que el acceso a la misma es más complicado y está limitado por el módulo opaco superior.
Como hemos explicado, el diseño en dos piezas del travesaño hembra del módulo opaco nos permite tener acceso a la junta, pero para asegurar la estanqueidad del sistema en este punto hemos de jugar con la geometría de la camisa y la de la patilla de machiembrado del travesaño.
La solución consiste en prolongar la camisa hasta situarla por delante del machiembrado de los montantes de visión. Protegiendo este punto de la posible agua acumulada en la parte superior del travesaño, evitando su entrada y forzando el desagüe hacia el módulo inferior.
El procedimiento para el tratamiento de la junta será igual al anteriormente descrito. Aplicaremos la cama de silicona para posteriormente deslizar la camisa hasta su posición, asegurándonos de que el sellado sea perimetral. Instalaremos el flexiband puntual sobre las patillas de machiembrado de los travesaños y por último procederemos a la instalación de la tapa posterior, fijándola al travesaño hembra.
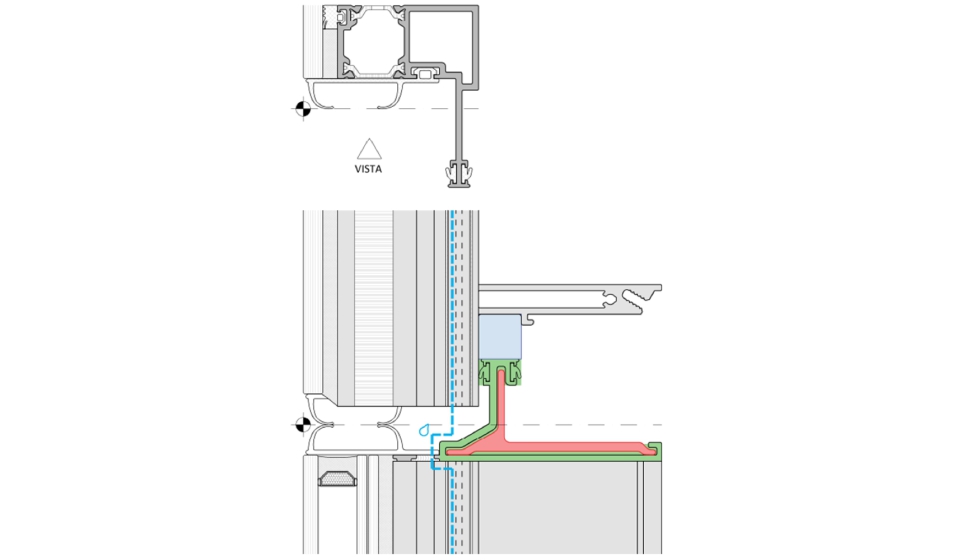
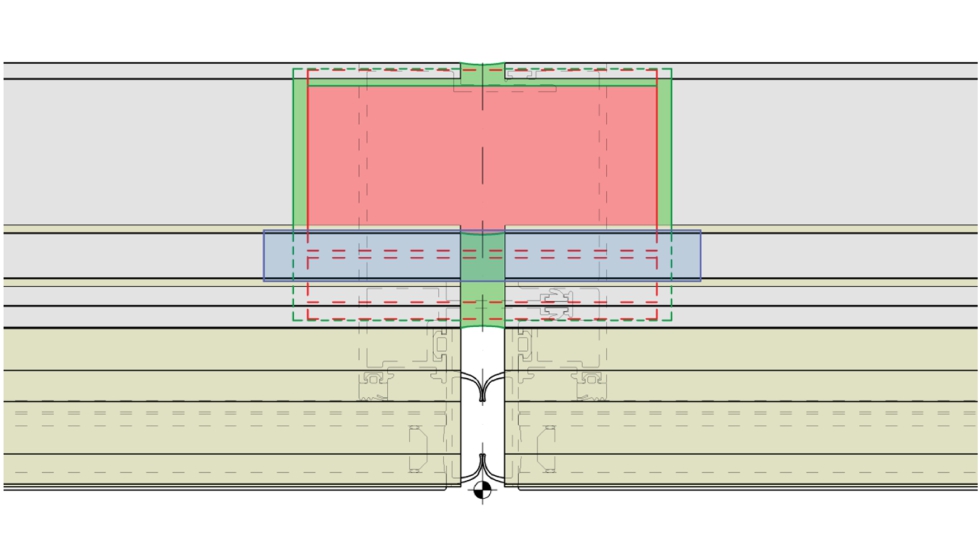
Vista en planta junta visión – opaco. Cama de silicona; Camisa; Flexiband.
4. Anclajes
En un modular tipo, la conexión entre el sistema y la placa de anclaje se produce generalmente en los montantes. En nuestro sistema, estos puntos de conexión se producirán en el módulo opaco y concretamente serán los travesaños los encargados de transmitir los esfuerzos a los anclajes.
Al instalar en obra estos módulos de forma exenta, debemos diseñar dos tipos de anclajes, los que irán en la parte superior del forjado o viga, que trabajarán a peso y viento, y los que irán en la parte inferior trabajando únicamente a viento.
4.1. Anclaje superior (viento peso)
Este anclaje se compone de tres piezas principales:
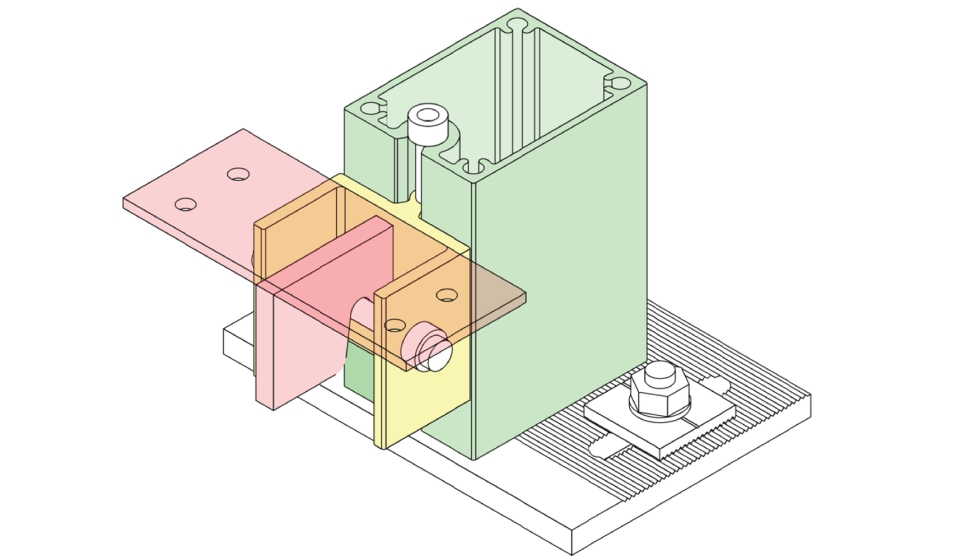
Placa de ancleje + tubo; pieza en 'U', cuelgue.
- Regulación en Y (Saliente):
La regulación en este eje la realizamos mediante los colisos situados en la placa de anclaje. Una vez regulada su posición, bloquearemos el movimiento mediante una contraplaca ranurada.
- Regulación en Z (Altura):
La regulación en este eje se realiza mediante un tornillo métrica 8, que soportará y transmitirá el peso del módulo a la placa de anclaje.
Este tornillo irá roscado a la pieza en forma de “U” que irá envainada en el tubo fijado a la placa de anclaje. Esto nos permite que, al roscar el tornillo en sentido horario o antihorario, la pieza en “U” se deslice hacia arriba o hacia abajo dentro de la cavidad del tubo, dándonos la regulación en altura.
- Regulación en X (Paralelo a fachada):
Esta regulación la realizaremos con la pieza de cuelgue que va fijada a la parte posterior del travesaño macho.
Colgaremos el módulo apoyando este cuelgue sobre una varilla de acero que forma parte de la pieza en “U”. De esta forma podremos deslizar el módulo de izquierda a derecha hasta llevarlo a su posición final.
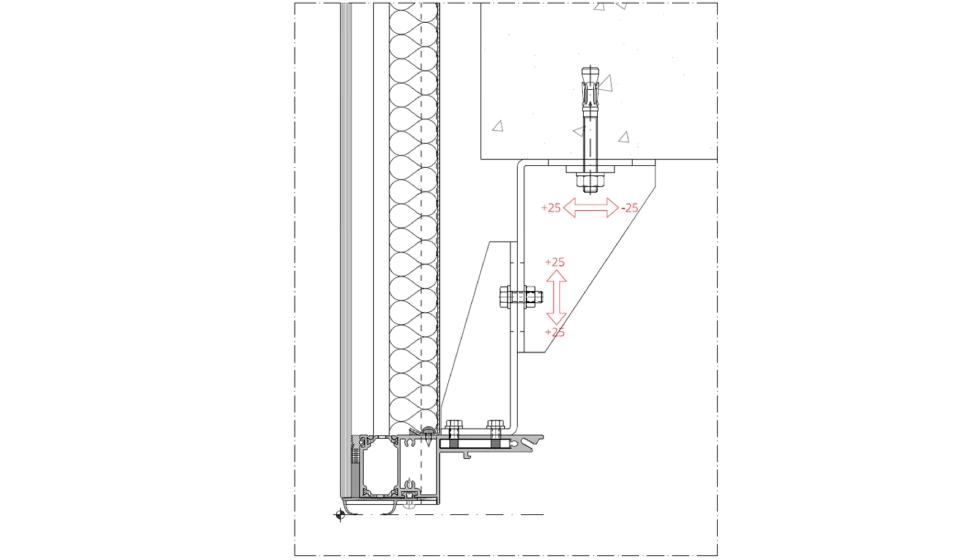
4.2. Anclaje inferior (viento)
El anclaje situado en la parte inferior del forjado lo resolveremos de una forma más sencilla debido a su condición de solo trabajar a viento.
Este anclaje estará formado por dos piezas. La primera de ellas en forma de ‘L’ acartelada que se fijará al forjado mediante tacos de expansión. En este punto tendremos la regulación en el eje X (paralelo a fachada) y en el eje Y (saliente), que bloquearemos mediante contraplaca soldada o fijada con pin.
El segundo elemento, también formado por una ‘L’ acartelada, irá fijado a la parte superior del travesaño hembra. Al instalar el módulo opaco fijaremos esta “L” a la del forjado mediante tornillos métrica. Ambas piezas tendrán colisos longitudinales en el punto de unión para permitir la regulación en el eje Z (altura). Este punto no se bloqueará para permitir la dilatación.
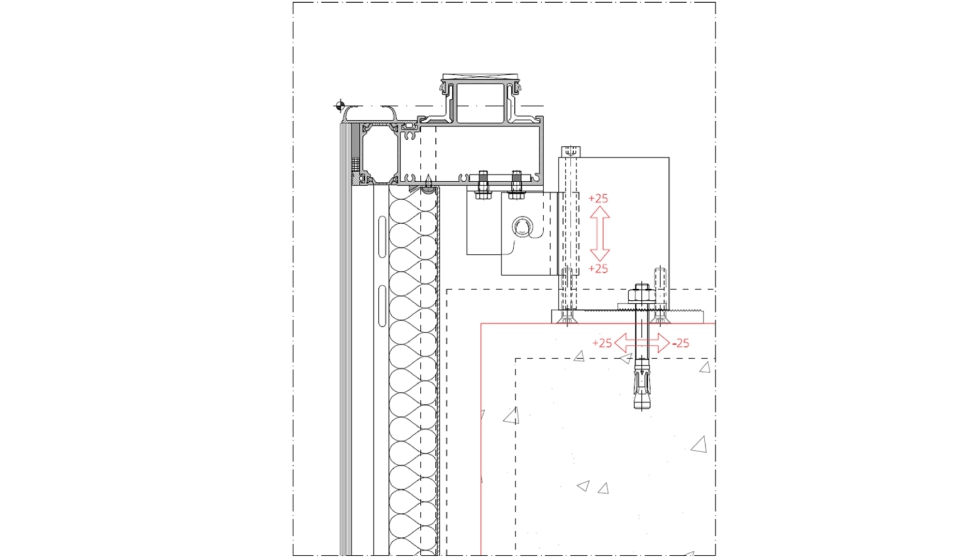