Esmaltado de aleaciones de alumino con alto contenido en magnesio
El esmaltado se puede definir como un proceso de tratamiento superficial. En el caso particular del aluminio hay dos procesos básicos de tratamiento o acabado superficial, de gran aplicación hoy en día, que son el anodizado y el lacado. El esmaltado sería un tercer proceso, con posibilidades comerciales, pero apenas desarrollado en los tiempos actuales.
Para seleccionar una aleación de aluminio que sea ‘esmaltable’ es necesario tener en cuenta la composición química de la misma, la cual determinará unas propiedades físicas. Así mismo, es fundamental conocer la aplicación o uso final del producto esmaltado así como el proceso partir del cual se va a obtener el producto de aluminio (por laminación, extrusión, inyección, etc.).
1. Introducción
El esmalte es un vidrio obtenido por fusión a alta temperatura, entre 1.000 y 1.300 °C. Su constituyente principal es el SiO2, que es asimismo el constituyente más abundante de la corteza terrestre. El SiO2 libre existe sobre todo en estado cristalizado, formando el cuarzo, cuya pureza es superior al 99%. Se encuentra asimismo en forma combinada con feldespatos, arcillas y micas. El vidrio de sílice, por sí solo, no permite conferir a la pieza esmaltada sus propiedades de inalterabilidad, dado que su temperatura de fusión es excesivamente elevada, su coeficiente de dilatación es demasiado reducido en comparación con el del aluminio y su adherencia sobre el metal es nula. Por lo tanto, es preciso agregar a la sílice diversos elementos constituyentes para poder obtener, tras diversas operaciones, el esmalte propiamente dicho. Estos elementos pueden clasificarse en cuatro grandes familias, en función de las propiedades que aportan al esmalte (1):
-1ª familia: los refractarios, que aportan la estructura amorfa del esmalte y sus propiedades de resistencia mecánica. Entre estos constituyentes se encuentra, por ejemplo, la alúmina Al2O3, cuya función es reducir el coeficiente de dilatación, aumentar la resistencia a la temperatura a los agentes químicos y a la abrasión y facilitar la acción de los agentes opacificantes, que intervienen asimismo en la composición del esmalte.
-2º familia: los fundentes, que reducen las temperaturas de fusión y de cocción, y aumentan el coeficiente de dilatación. Se componen principalmente de borax, tetraborato de sodio en forma anhidra (Na2B4O7) o hidratada (Na2B4O7, 10H2O) y óxidos alcalinos (Na2O, K2O, Li2O, CaO, MgO y SrO). Con estos compuestos se obtienen borosilicatos de sodio, de potasio, de litio, de calcio, de magnesio o de estroncio, cuyo punto de fusión es inferior al del SiO2 (aproximadamente 1.400 °C en lugar de 1.720 °C). El punto de fusión puede reducirse, asimismo, mediante la adición de F2, B2O3 y nitratos. Los fundentes, a través de los óxidos alcalinos, aumentan el coeficiente de dilatación al colmar las ‘oquedades’ de la estructura del SiO2.
-3ª familia: los agentes potenciadores de la adherencia, son óxidos metálicos que intervienen en las reacciones químicas de oxidación-reducción, permitiendo la adherencia del esmalte sobre el metal. Estos óxidos metálicos están contenidos en el esmalte de capa base. Se trata principalmente de óxidos (NiO, MoO, CoO, CuO, MnO2 y Cr2O3).
-4ª familia: los opacificantes y los colorantes, aportan las propiedades visuales y táctiles a las piezas esmaltadas. Los opacificantes potencian la opacidad del esmalte. Estos compuestos están contenidos en el esmalte de cobertura. Los más frecuentemente utilizados son los siguientes óxidos: TiO2, Sb2O5, ZrO2 y SnO. Los colorantes se obtienen mediante la combinación de óxidos minerales. El color de un esmalte depende de la naturaleza del colorante, de su concentración en el esmalte, de la composición química del esmalte y de las condiciones de cocción en el horno de esmaltación. Habitualmente, la sustancia colorante, en forma de partículas finas, se mezcla por medios mecánicos con el esmalte durante el proceso de triturado, antes de la aplicación sobre el sustrato.
Los esmaltes de cocción a baja temperatura han sido desarrollados para la esmaltación de cuerpos de aluminio o de sustratos aluminizados. Se han desarrollado a partir de los esmaltes utilizados para el acero, adaptando su coeficiente de dilatación. Su temperatura de cocción (560 °C) es inferior a la de los esmaltes utilizados sobre sustratos de acero no recubierto. Los esmaltes vítreos que se usan en la actualidad para el acabado superficial de algunos productos de aluminio se obtienen a partir de fritas. Se define ‘frita’ como una mezcla de sustancias químicas inorgánicas obtenida por enfriamiento rápido de un fundido, que es una combinación compleja de materiales, convirtiendo las sustancias químicas así elaboradas en compuestos vítreos insolubles que se presentan en forma de escamas o gránulos. Para el esmaltado del aluminio las fritas suelen estar compuestas por silicatos de Na, K, óxidos de Ti, Ca y Al2O3.
Las principales propiedades físicas y químicas que vienen determinadas por la aleación de aluminio son:
- Resistencia al choque térmico. Temperatura de reblandecimiento o de comienzo de fusión
- Resistencia mecánica, definida por tres parámetros: límite elástico, resistencia a rotura y elongación
- Resistencia a la fatiga
- Resistencia a la corrosión
- ‘Esmaltabilidad’ o capacidad para el esmaltado de la aleación
2. Parámetros fundamentales en el esmaltado del aluminio
Los principales parámetros que se deben tener en cuenta a la hora de esmaltar un producto de aluminio y que se van a desarrollar en el presente artículo son los siguientes (2):
- Temperatura de esmaltado de la aleación de aluminio
- Influencia de la composición química de la aleación de aluminio
- Estructura cristalina de la aleación de aluminio
- Acabado superficial del aluminio previo al esmaltado. Pre-tratamiento
- Adherencia del esmalte
- Aplicación del esmalte
- Aspectos teóricos de la intercara aluminio - esmalte
- Esmaltado de aleaciones de aluminio de alto contenido en magnesio
2.1. Temperatura de esmaltado de la aleación de aluminio
Considerando una temperatura de esmaltado entre 540 – 560 °C, el aluminio tiene que resistir sin llegar a fundirse, para poder ser esmaltado. Algunas aleaciones de aluminio presentan puntos eutécticos en los que se produce la fusión en dicho intervalo de temperaturas. Las aleaciones de aluminio cuyo punto de fusión es superior, como por ejemplo la aleación 1050 (cuyo contenido en aluminio alcanza el 99,5%) tiene un rango de fusión entre 645 – 658 °C; la aleación 3003 tiene un rango de fusión entre 643 – 654 °C; y la aleación 4006 tiene un punto de fusión por encima de los 608 °C. La principal consecuencia del proceso de esmaltado del aluminio es la disminución de las propiedades mecánicas, debido a la re-cristalización que se produce cuando se alcanzan temperaturas de 320 – 360 °C (3).
2.2. Influencia de Composición química de la aleación de aluminio
Una aleación de aluminio se considera apta para el esmaltado, cuando se produce adherencia entre en la superficie del aluminio y el esmalte, debido a la formación de una ‘intercara’ en la zona de contacto de ambos materiales, sin que se aprecien defectos en la superficie que se obtiene finalmente.
La aleación de aluminio 4006 cuyo contenido en Si es del 1% y que prácticamente no contiene Mg (máximo 100 ppm) se utiliza para fabricar útiles de cocina, tales como sartenes, ollas y cazuelas. En un ciclo corto de calentamiento durante el proceso de esmaltado con una aleación 4006, se produce una ‘solubilización’ y un efecto de templado siempre que el enfriamiento sea rápido, lo cual condiciona las propiedades mecánicas finales. Se ha constatado experimentalmente que a pesar del bajo contenido en magnesio en las aleaciones 4006, 3003 e incluso en la 8006, se producen defectos de adherencia entre la superficie del aluminio y el esmalte (4). Cuando el contenido en Mg llega a una cierta concentración, que incluso en algunas aleaciones de aluminio se considera como impureza, dificulta la adherencia. Desde un punto de vista más científico que industrial es interesante conocer que es lo que sucede exactamente en la intercara entre los dos materiales, si el Mg se presenta en forma óxido, que tipo de óxido se forma, y si eventualmente se descompone a temperaturas de 540 – 560 °C. Estas cuestiones y sus respuestas son importantes para una mejor comprensión de la dinámica de los fenómenos de adherencia – no adherencia. Sin embargo es importante señalar que en el caso de la aleación 6082 que contiene entre un 0,6 y un 1,2% de Mg y entre un 0,7 y un 1,3% de Si, la presencia del primero no afecta a la adherencia del esmalte. Esto se debe a la formación del compuesto SiMg, por lo que la conclusión que se extrae es que aunque el contenido en Mg sea elevado, si éste elemento se puede combinar químicamente con otros (caso de Si), de forma que el compuesto formado sea inactivo (SiMg) no afecta a la adherencia del esmalte (5). La buena capacidad de esmaltado de la aleación 6082 es interesante desde un punto de vista práctico, ya que gracias a la elevada resistencia mecánica que tiene esta aleación, permite la fabricación de perfiles estructurales esmaltados.
Las aleaciones de alto contenido en Mg son las de las series 3XXX, 5XXX y 6XXX (6). Hay que señalar que las dos primeras son aleaciones no templables mientras que la tercera es templable. Las dos primeras suelen ser aleaciones de laminación, mientras que la tercera es una aleación que se usa en la extrusión del aluminio, para la obtención de perfiles. Dentro de la serie 3XXX, las más comunes son: 3103, 3005 y 3105 (figura1).
Aleación |
Si % |
Fe % |
Cu % |
Mn % |
Mg % |
Zn % |
Ti % |
Cr % |
3005 |
0,6 |
0,7 |
0,3 |
1,0 - 1,5 |
0,2 - 0,6 |
0,25 |
0,1 |
0,1 |
3103 |
0,5 |
0,7 |
0,1 |
0,9 - 1,5 |
0,3 |
0,2 |
- |
0,1 |
3105 |
0,6 |
0,7 |
0,3 |
0,3 - 0,8 |
0,2 - 0,8 |
0,4 |
0,1 |
0,2 |
Dentro de la serie 5XXX las más comunes son: 5005, 5052, 5083 y 5754.
Aleación |
Si % |
Fe % |
Cu % |
Mn % |
Mg % |
Zn % |
Ti % |
Cr % |
5005 |
0,3 |
0,7 |
0,2 |
0,2 |
0,5 - 1,1 |
0,25 |
- |
0,1 |
5052 |
0,25 |
0,4 |
0,1 |
0,1 |
2,2 - 2,8 |
0,1 |
- |
0,15 - 0,35 |
5083 |
0,4 |
0,4 |
0,1 |
0,4 - 1,0 |
4,0 - 4,9 |
0,25 |
0,15 |
0,05 - 0,25 |
5754 |
0,4 |
0,4 |
0,1 |
0,5 |
2,6 - 3,6 |
0,2 |
0,15 |
0,3 |
Dentro de la serie 6XXX las más comunes son: 6060, 6005 y 6082
Aleación |
Si % |
Fe % |
Cu % |
Mn % |
Mg % |
Zn % |
Ti % |
Cr % |
6060 |
0,3 - 0,6 |
0,1- 0,3 |
0,1 |
0,1 |
0,35 - 0,6 |
0,15 |
0,2 |
0,05 |
6005A |
0,5 - 0,9 |
0,35 |
0,3 |
0,5 |
0,4 - 0,7 |
0,2 |
0,1 |
0,3 |
6082 |
0,7 - 1,3 |
0,5 |
0,1 |
0,4 - 1,0 |
0,6 - 1,2 |
0,2 |
0,1 |
0,25 |
El Mg es un elemento aleante muy importante, en las aleaciones de aluminio, que se adiciona con el fin de aumentar la resistencia mecánica, así como la resistencia a la oxidación en atmosfera salina y a la oxidación anódica. Muchas de las aleaciones de laminación y de extrusión de uso extendido, contienen Mg en mayor o menor medida, por lo que la presencia de Mg va a ser un factor a tener en cuenta a la hora de esmaltar productos laminados o perfiles extruidos, ya que va a afectar a la adherencia (7). Para productos esmaltados habrá que intentar trabajar con aleaciones de bajo contenido en Mg u otras en las que a pesar de que el contenido en Mg sea elevado se formen compuestos inertes como el SiMg. La presencia de Pb de Bi y de todos los elementos químicos que contribuyen a bajar el punto de fusión, tienen un claro efecto negativo ya que dificultan la adherencia del esmalte. Particularmente se ha constatado que el contenido en Pb y Bi, incluso en cantidades muy pequeñas, en presencia de Cr y Cu en cantidades superiores reducen significativamente la adherencia (8). En la siguiente tabla (figura 2) se observan de forma diferenciada los elementos químicos que influyen de modo favorable, neutro o negativo la en la adherencia aluminio – esmalte.
Elementos aleantes que influyen positivamente en la adherencia del esmalte
|
1ª |
2ª |
3a |
4a |
5a |
6a |
7a |
|
8 |
|
1b |
2b |
3b |
4b |
5b |
6b |
7b |
0 |
1 |
H |
|
|
|
|
|
|
|
|
|
|
|
|
|
|
|
|
He |
2 |
Li |
Be |
|
|
|
|
|
|
|
|
|
|
B |
C |
N |
O |
F |
Ne |
3 |
Na |
Mg |
|
|
|
|
|
|
|
|
|
|
Al |
Si |
P |
S |
Cl |
Ar |
4 |
K |
Ca |
Sc |
Ti |
V |
Cr |
Mn |
Fe |
Co |
Ni |
Cu |
Zn |
Ga |
Ge |
As |
Se |
Br |
Kr |
5 |
Rb |
Sr |
Y |
Zr |
Ni |
Mo |
Tc |
Ru |
Rh |
Pd |
Ag |
Cd |
In |
Sn |
Sb |
Te |
I |
Xe |
6 |
Cs |
Ba |
La |
Hf |
Ta |
W |
Re |
Os |
Ir |
Pt |
Au |
Hg |
Ta |
Pb |
Bi |
Po |
As |
Rn |
7 |
Fr |
Rd |
AC |
Th |
Pa |
U |
|
|
|
|
|
|
|
|
|
|
|
|
Elementos aleantes que no influyen la adherencia del esmalte
|
1ª |
2ª |
3a |
4a |
5a |
6a |
7a |
|
8 |
|
1b |
2b |
3b |
4b |
5b |
6b |
7b |
0 |
1 |
H |
|
|
|
|
|
|
|
|
|
|
|
|
|
|
|
|
He |
2 |
Li |
Be |
|
|
|
|
|
|
|
|
|
|
B |
C |
N |
O |
F |
Ne |
3 |
Na |
Mg |
|
|
|
|
|
|
|
|
|
|
Al |
Si |
P |
S |
Cl |
Ar |
4 |
K |
Ca |
Sc |
Ti |
V |
Cr |
Mn |
Fe |
Co |
Ni |
Cu |
Zn |
Ga |
Ge |
As |
Se |
Br |
Kr |
5 |
Rb |
Sr |
Y |
Zr |
Ni |
Mo |
Tc |
Ru |
Rh |
Pd |
Ag |
Cd |
In |
Sn |
Sb |
Te |
I |
Xe |
6 |
Cs |
Ba |
La |
Hf |
Ta |
W |
Re |
Os |
Ir |
Pt |
Au |
Hg |
Ta |
Pb |
Bi |
Po |
As |
Rn |
7 |
Fr |
Rd |
AC |
Th |
Pa |
U |
|
|
|
|
|
|
|
|
|
|
|
|
Elementos aleantes que influyen negativamente en la adherencia del esmalte
|
1ª |
2a |
3a |
4a |
5a |
6a |
7a |
|
8 |
|
1b |
2b |
3b |
4b |
5b |
6b |
7b |
0 |
1 |
H |
|
|
|
|
|
|
|
|
|
|
|
|
|
|
|
|
He |
2 |
Li |
Be |
|
|
|
|
|
|
|
|
|
|
B |
C |
N |
O |
F |
Ne |
3 |
Na |
Mg |
|
|
|
|
|
|
|
|
|
|
Al |
Si |
P |
S |
Cl |
Ar |
4 |
K |
Ca |
Sc |
Ti |
V |
Cr |
Mn |
Fe |
Co |
Ni |
Cu |
Zn |
Ga |
Ge |
As |
Se |
Br |
Kr |
5 |
Rb |
Sr |
Y |
Zr |
Ni |
Mo |
Tc |
Ru |
Rh |
Pd |
Ag |
Cd |
In |
Sn |
Sb |
Te |
I |
Xe |
6 |
Cs |
Ba |
La |
Hf |
Ta |
W |
Re |
Os |
Ir |
Pt |
Au |
Hg |
Ta |
Pb |
Bi |
Po |
As |
Rn |
7 |
Fr |
Rd |
AC |
Th |
Pa |
U |
|
|
|
|
|
|
|
|
|
|
|
|
2.3. Influencia de la estructura cristalina
El contenido en elementos químicos Cr, Mn y Mg en una aleación de aluminio implica un importante aumento de las propiedades mecánicas, pero dichos elementos también actúan modificando el tamaño de los granos cristalinos, haciendo que sus dimensiones sean más pequeñas. El tamaño del grano cristalino tiene una gran influencia en la adherencia del esmalte sobre la superficie del aluminio. Tomando como ejemplo práctico el de las sartenes fabricadas en aluminio esmaltado, se observa en la siguiente foto (figura 3), zonas en las que la adherencia es defectuosa, mientras que en otras zonas de la misma muestra la adherencia es óptima. Analizando más en detalle este efecto, se constata de forma generalizada que en las zonas que presentan granos cristalinos grandes, que son zonas de deformación por templado y segunda re-cristalización, la adherencia es positiva, mientras que en las zonas en las que los granos son pequeños la adherencia es negativa.
La adherencia defectuosa es debida en un primer término a un contenido excesivo en Pb y Bi en la aleación de aluminio, como se ha indicado anteriormente. Sin embargo una estructura cristalina de granos de gran tamaño permite superar el efecto de la ‘no adherencia’ provocada por los elementos descritos. Por lo tanto, un producto de aluminio puede presentar un correcto esmaltado siempre que la cristalización haya producido granos grandes, que permitan compensar el efecto negativo de algunos elementos químicos (8).
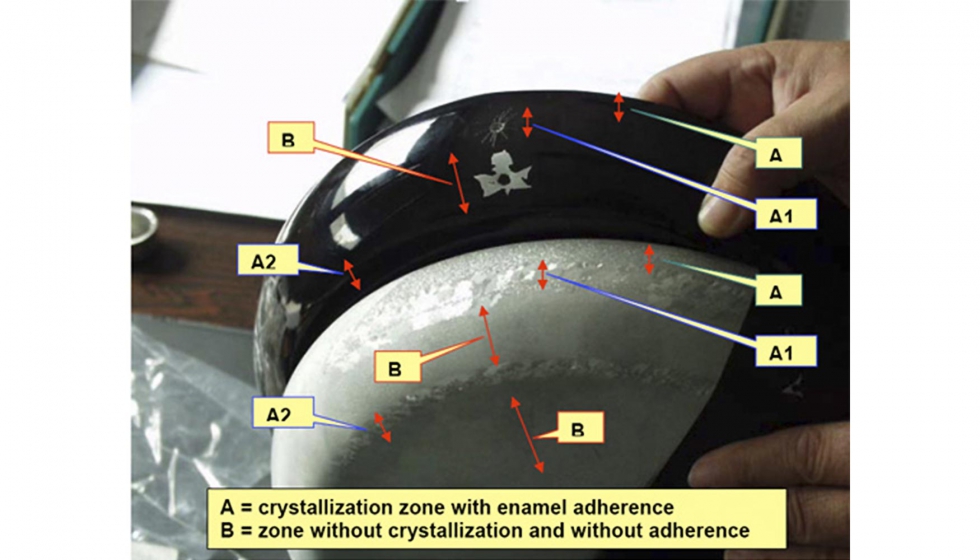
2.4. Pre-tratamiento. Influencia de los residuos superficiales
El pre-tratamiento químico tiene una influencia muy notable en la dinámica de adhesión entre la superficie de aluminio y el esmalte. Una buena limpieza del producto de aluminio previamente al tratamiento superficial bien sea lacado, anodizado o esmaltado, es una operación fundamental. Es muy importante seleccionar debidamente los productos de limpieza ya que hay ciertos productos orgánicos que pueden tener un efecto negativo. Se recomienda el uso disolventes y desengrasantes que no sean muy agresivos. En el caso particular del esmaltado, es recomendable que el pre-tratamiento posterior al lavado, pero previo al esmaltado se lleve cabo mediante un ligero ataque químico, de forma que se aumente la micro-rugosidad superficial, con el objetivo de favorecer la adhesión. Gracias a un adecuando pre-tratamiento se puede conseguir mejorar la adherencia del esmalte sobre determinadas aleaciones de aluminio, difíciles de esmaltar.
El siguiente diagrama muestra (figura 4) el caso de un laminado de aluminio, que sería el soporte, y los diferentes sustratos que se pueden formar. La primera película o sustrato (color amarillo) es la que debe de limpiarse, mediante lavado, ya que contiene restos de grasas y lubricantes de la laminación. Esta operación a veces de denomina ‘desengrasado’ (en proceso como la laminación o la mecanización de piezas y perfiles. Suponiendo que se haya llevado a cabo la limpieza o desengrasado, la siguiente película que se observa contiene restos de agua, sosa, etc. La tercera película que se puede encontrar se debe a reacciones químicas (segregación y migración superficial) produciendo óxidos (9).
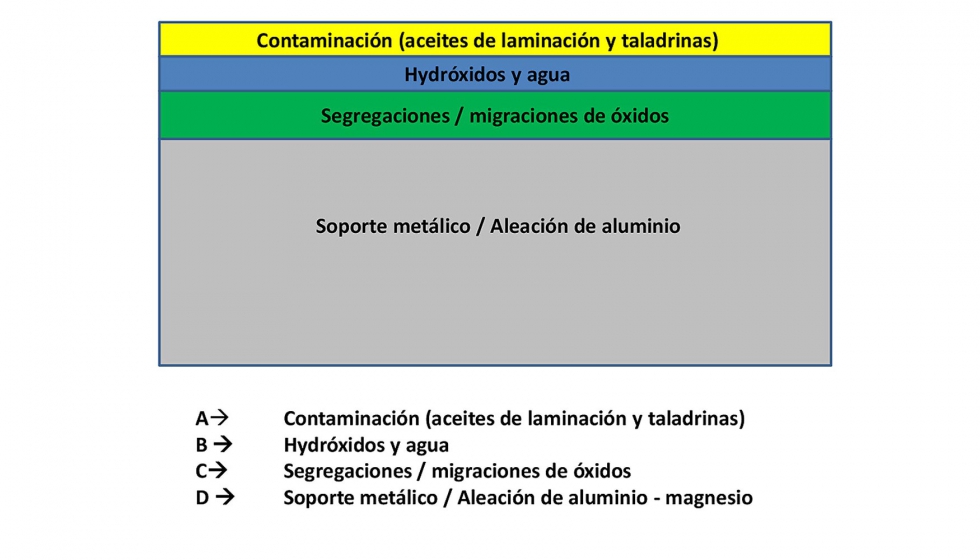
La preparación superficial idónea para el esmaltado constaría de las siguientes fases:
a) Desengrasado. Eliminación de grasas y aceites sin afectar químicamente a la superficie
b) Pickling o Decapado (mecánico o químico). Separación de una capa finísima superficial obteniendo una micro-rugosidad que aumenta y refuerza el contacto superficial
c) Tratamiento químico. Mediante cromatizado o fosfatado-cromatizado, para modificar la naturaleza de los óxidos residuales
d) Anodización. Formación de una capa muy fina de Al2O3 mediante electrolisis con ácido fosfórico. La capa anódica continua es una base óptima para el esmaltado.
Según D. A. Estrada e I. Jiménez Calvo (10) para obtener un buen esmaltado sobre aluminio es necesario elegir adecuadamente el proceso de tratamiento, que depende del material empleado. Si se emplea aluminio puro o aleaciones sin magnesio el pre- tratamiento puede hacerse en una sola operación consistente en un desengrasado térmico a 540 °C durante 10 minutos, pero en los demás casos es necesario completar la preparación con otros tratamientos. Si bien las aleaciones que no contienen Mg, son susceptibles de ser esmaltadas tras un simple desengrasado, es conveniente someterlas a un decapado para obtener mejores resultados. El desengrasado se puede realizar mediante un tratamiento térmico, o bien químicamente, con una solución acuosa de 50 gramos de P04Na3 y 50 gramos de CO3Na2 por litro a 60-70 °C, durante 5 minutos. La secuencia de fases de tratamiento superficial posterior al desengrasado son las siguientes:
a) Decapado alcalino.
b) Lavado.
c) Decapado ácido oxidante.
d) Lavado.
e) Cromatizado (o fosfatado).
f) Lavado.
g) Fijación térmica del cromatizado.
Las aleaciones sin Mg estrictamente no necesitan el decapado, pero es conveniente llevarlo a cabo. Las aleaciones con Mg necesitan, además del decapado, un cromatizado, fosfatado o anodizado como base para el esmaltado.
2.5. Adherencia del esmalte
Si bien es importante controlar las condiciones físicas y químicas de los esmaltes, también lo es conocer las interacciones de éste con el propio soporte metálico, fenómeno de ‘adherencia’. Los procesos de fabricación de estos esmaltes determinan su estructura interna y las características de su superficie, parámetros ambos de los que dependen sus propiedades y que influyen directamente en la adherencia (11).
Según el Grupo de trabajo italiano WG3 del C.I.S.P (12), el test de adherencia realizado del esmalte sobre el sustrato de aluminio se lleva a cabo en una primera fase mediante un ataque químico con SbCl3, durante 60 segundos. En una segunda fase se somete a la probeta de aluminio a un test de impacto. Como consecuencia del test de impacto, la superficie del esmalte se deforma y se producen fisuras lineales (figura 5).
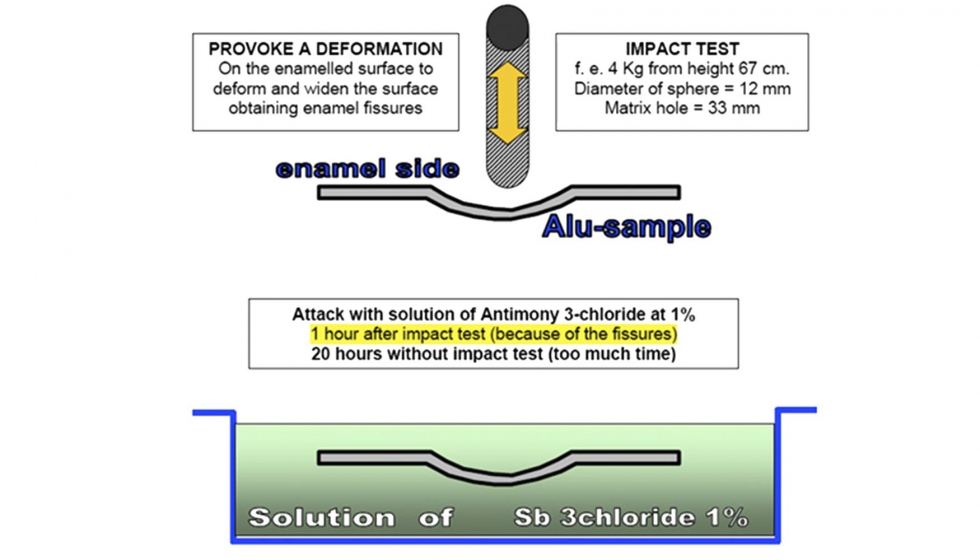
3. Resultados y conclusiones
Los test realizados con diferentes grados de fluidez de frita sobre el sustrato de aleación de aluminio 3105 cuyo contenido en Mg alcanza hasta un 0,8%, considerada una aleación ‘no adecuada para el esmaltado’ han arrojado los siguientes resultados:
- A mayor fusibilidad del esmalte, se mejora la humectación, obteniéndose mayor adherencia
- La perdida de transparencia del esmalte puede llegar a anular totalmente la adherencia
- La adición de óxidos micronizados (CaO, TiO2, Al2O3, etc.) en el esmalte en cantidades entre 1 - 10% aumenta considerablemente la adherencia.
- La mezcla de diferentes fritas, con adiciones de óxidos puede mejorar el esmaltado de la aleación de aluminio 3105.
Para permitir que el esmalte funda a temperaturas cercanas a los 600 °C, se añade V2O5, ya que se forma un eutéctico que permite la fusión de la mezcla que constituye el esmalte a esa temperatura, y se incrementa la resistencia química. Generalmente cada fabricante de fritas cerámicas dispone de sus propios aditivos y elementos químicos los cuales añade en matriz vítrea del esmalte para favorecer la adherencia aluminio-esmalte, la resistencia al ataque de ácidos y agresivos químicos, así como para bajar el punto de fusión y colorear la frita.
Los componentes de la frita reaccionan durante el proceso de fusión, provocando un aumento de volumen de hasta 2, 3 y 4 veces según las temperaturas de trabajo. Por este motivo la fusión en horno rotatorio es recomendable para alcanzar una mejor maduración y refinado del vidrio obtenido. La frita a alta temperatura puede ser soluble en agua por lo que el enfriamiento se debe realizar de forma rápida, pero por vía neumática evitando así el contacto con el agua.
3.1. Formación de la intercara aluminio – esmalte
Si se comprende bien el mecanismo que permite la adherencia entre los dos materiales, se podrán desarrollar y mejorar ambos productos. El aluminio es un material con una estructura cristalina cubica centrada en caras y cuya estructura atómica esta unida mediante un enlace metálico. El esmalte es una masa vítrea solidificada, que presenta una estructura amorfa (no cristalizada), en la cual prevalece el enlace iónico. Durante el proceso de esmaltado la unión físico-química de estos materiales totalmente diferentes se lleva a cabo mediante un mecanismo en diferentes fases (13):
- Primera fase, en la cual el metal es fuertemente oxidado gracias al aumento de temperatura dentro del horno de esmaltado (atmosfera oxidante). La capa de óxido de aluminio en teoría deberá crecer hasta los 150 – 250 Angstrom, para poder obtener las mejores condiciones de de unión con la capa de esmalte, según un mecanismo químico de tipo Redox.
- Segunda fase, en la que el esmalte líquido ‘moja’ y humecta la superficie metálica disolviendo los óxidos presente y reaccionando con los óxidos contenidos en el esmalte fundido.
- En la tercera fase la capa superficial de óxido de aluminio se disuelve completamente en el esmalte fundido. El sustrato metálico es atacado y corroído por el fundido, el cual penetra en la micro-rugosidad metálica, proporcionando así la adherencia mecánica.
- En la cuarta fase se produce el mecanismo de intercambio iónico entre los elementos químicos contenidos en la aleación de aluminio con los óxidos y silicatos del esmalte fundido. La presencia de determinado óxidos disueltos en el esmalte favorece el intercambio iónico, formándose una interfase de material compuesto, la cual une el aluminio y el esmalte haciéndolos teóricamente ‘inseparables’.
Se puede afirmar que “una buena adherencia es el mejor índice de un buen esmaltado” (14). A continuación se resumen los principales parámetros y fenómenos que determinan la adherencia:
- Composición química y reactividad de la superficie de aluminio
- Pre-tratamiento de la superficie de aluminio que va a ser esmaltada
- Calidad y cantidad de la superficie de óxido formado sobre la superficie
- Tipo de atmosfera en el interior del horno
- Calidad y cantidad de los óxidos que determinan la adherencia del esmalte
- Cantidad y calidad de los óxidos que se adicionan para la molienda de las materias primas del esmalte
- Capacidad de humectación, fluidez, viscosidad y tensión superficial del esmalte líquido
- Presencia de elementos que determinan el crecimiento de la capa de óxido
- Expansión térmica del esmalte
- En cuanto a la aleación de aluminio, formación de un tamaño de grano cristalino ‘ideal’
3.2. Esmaltado de aleaciones de aluminio de alto contenido en Mg
Las principales aleaciones de aluminio con alto contenido en magnesio son las que pertenecen a la serie 3000 y 5000. Por ejemplo la 3105 y la 5010, ambas poseen un rango completo de características físicas positivas para ser esmaltadas. Incluso si se obtienen a partir de aluminio secundario (mezcla de aluminio de primera fusión y chatarra) e incluso en el caso de laminados fabricados mediante colada continua. La gran resistencia mecánica de estas aleaciones permite reducir los espesores, para la fabricación de las piezas y productos finales.
En las siguientes fotos se muestran probetas de aluminio laminado de unos 0,5 mm de espesor, y esmaltadas. Las probetas son de aleación de aluminio de alto contenido en Mg (aleación 3105). El esmaltado es perfecto, pudiendo obtenerse acabados brillo y mate y diferentes colores.
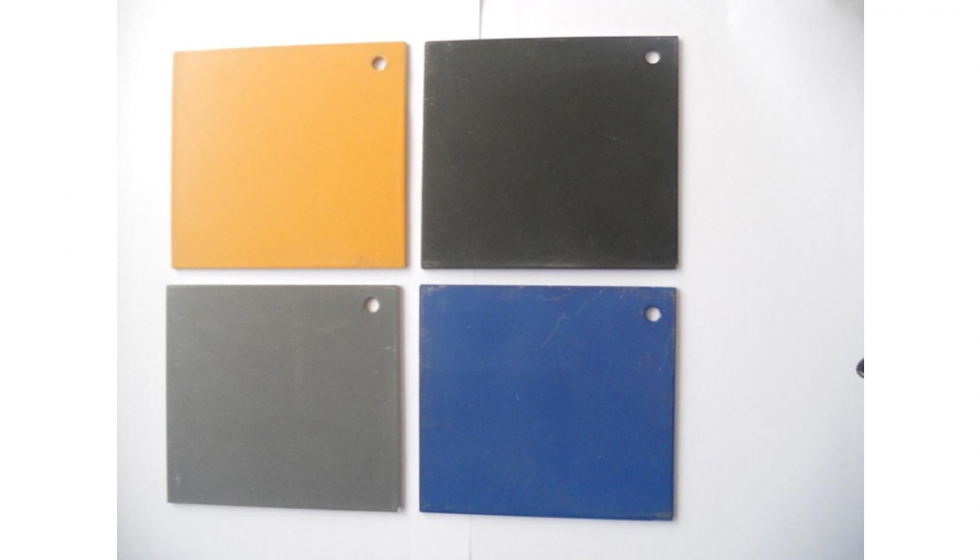
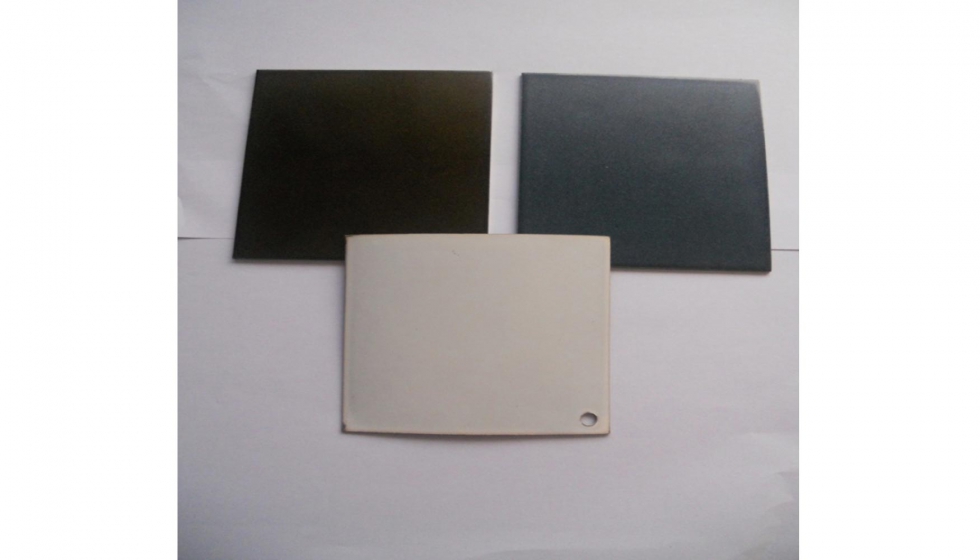
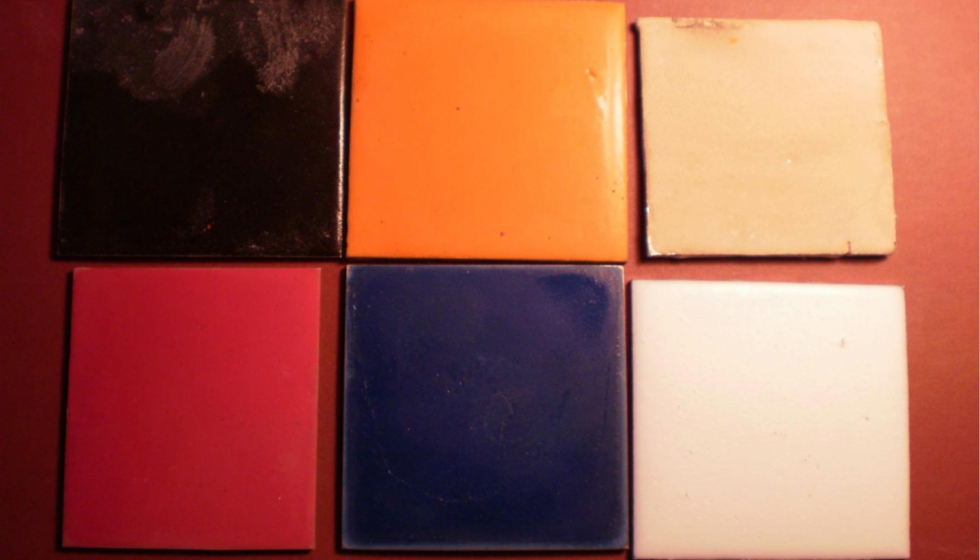
Previamente al esmaltado se formulan y desarrollan fritas diferentes de la estándar mediante la adición de óxidos capaces de reaccionar positivamente con el Mg de la aleación de aluminio. Estas diferentes fritas permiten la realización de un ‘test de esmaltado’ que permita la obtención de la frita adecuada a la aleación. Mediante estos experimentos se ha descubierto que los esmaltes de gran transparencia, es decir, los que no tienen pigmentos, carecen de adherencia. Esta condición permite clasificar los aditivos de la frita que pueden o no favorecer la adherencia según la mayor o menor opacidad que confieran al esmalte. En otras palabras se desarrolla una frita a medida para la tipología de pieza a esmaltar, considerando que dicha pieza está fabricada con una aleación de aluminio de alto contenido en Mg.
Posteriormente a las verificaciones a nivel de laboratorio y los test con pequeñas cantidades de esmalte y en piezas pequeñas, si el resultado es positivo se continúa con pruebas industriales a mayor escala con varios cientos de piezas. Esta forma de trabajar se ha llevado a cabo en Italia con fabricantes de ‘holloware’ (por holloware se entienden objetos y utensilios metálicos de mesa como cafeteras, soperas, teteras, jarras, etc.). El resultado en cuanto a la esmaltabilidad en este tipo de piezas ha sido excelente ya que con solo un pre-tratamiento y una única cocción en el horno de esmaltado se han obtenido una óptima adherencia y calidad superficial en el acabado de las piezas. En resumen, el esmaltado de piezas tipo holloware fabricadas con aleaciones de aluminio de alto contenido en Mg, siguiendo las pautas anteriormente indicadas arroja los siguientes resultados (15):
- Superficie brillante
- Buen desarrollo del color
- Muy buena adherencia
- Resistencia química del esmalte desarrollado ad-hoc análoga a la de un esmalte estándar.
3.3. Conclusiones finales
En general, las aleaciones de aluminio con alto contenido en Mg no son las más adecuadas para el esmaltado, pues la capa superficial de alúmina que se genera por oxidación natural no es homogénea y no se disuelve totalmente en el esmalte, impidiendo que adhieran esmalte y metal. Algunas aleaciones de magnesio, como las que lo contienen en forma de SiMg, se pueden esmaltar si se han sometido a un pre-tratamiento de cromatizado, aprovechándose así las buenas propiedades mecánicas que proporciona este elemento al aluminio.
Es sobradamente conocido que el Mg es un elemento muy importante en ciertas aleaciones de aluminio. Sin embargo a la hora de esmaltar este tipo de aleaciones la adherencia aluminio – esmalte puede ser deficiente sobre todo si el contenido en Mg supera las 100 ppm. En caso de que el Mg se una a otro elemento químico formando un compuesto, se queda inactivo, no afectando negativamente a la adherencia. Por otra parte se ha constatado que las aleaciones de aluminio con alto contenido en Mg tienden a aumentar la rugosidad, debido al aumento de la capa de óxido superficial.
En los últimos años se han esmaltado diferentes objetos de aluminio fabricados a partir de aleaciones de alto contenido en Mg como la 3105 y la 5010, producidas en algunos casos a partir de colada continua, sin problemas de adherencia, obteniendo buenos resultados sin necesidad de inversiones o de procesos de mayores costes productivos. No obstante, hay problemas que no han sido resueltos todavía, como la deformación producida durante el esmaltado en productos laminados de gran formato, debido a la temperatura y la expansión térmica. Los equipos de esmaltado que se utilizan en la actualidad están concebidos para trabajar con productos de acero y no con aluminio. Esto limita mucho las posibilidades de esmaltado de productos de aluminio, especialmente los laminados de gran formato.
Agradecimientos
En primer término agradecer a Angelo Ferraro su ayuda y total disposición para la publicación de artículo. Así mismo agradecer a Ignacio Ruiz-Bustinza del CENIM, su ayuda y apoyo en la preparación del artículo, así su tiempo y su interés dedicados al desarrollo del aluminio esmaltado.
Referencias
- Arcelor Mittal, Los aceros para esmaltación y el acero esmaltado, Guía de utilización, 8-9.
- A.M. Compagnoni, A. Ferraro, Enamelling of aluminium alloys with high content of magnesium, 20th International Enamellers Congress, Turkey (2005).
- A.M. Compagnoni, A. Ferraro, Enamelling of aluminium alloys with high content of magnesium, 20th International Enamellers Congress, Turkey (2005).
- A.M. Compagnoni, A. Ferraro, Enamelling of aluminium alloys with high content of magnesium, 20th International Enamellers Congress, Turkey (2005).
- A.M. Compagnoni, A. Ferraro, Enamelling of aluminium alloys with high content of magnesium, 20th International Enamellers Congress, Turkey (2005).
- J. L. Guillén, El aluminio en el mundo actual: Tecnología, Aplicaciones y Reciclado, Industria y Minería, V., 366, 26-38 (2006).
- L.J. Gazo, C.A. Baldwin, W.D. Faust, Ferro Corporation USA, Appliance Division, Enamelled grates in aluminum alloy, a new application, 19° international Congress, Venice (2001).
- A.M. Compagnoni, A. Ferraro, Enamelling of aluminium alloys with high content of magnesium, 20th International Enamellers Congress, Turkey (2005).
- A.M. Compagnoni, A. Ferraro, Enamelling of aluminium alloys with high content of magnesium, 20th International Enamellers Congress, Turkey (2005).
- D.A. Estrada, I. Jiménez Calvo, Esmaltes sobre aluminio, Bol. Soc. Esp. Ceram., Vol. 12, 2, 124 (1974).
- J.M. Gómez de Salazar, M.I. Barrena, A. Soria, M. Menéndez y A. González, Estudio de capas vitro-cerámicas depositadas sobre acero, Bol. Soc. Esp. Ceram., Vol. 41, 6, (2002).
- M. Leveaux, N. Crevits, K. Lips, B. Schepers, A. Aerts, E. Verboom, Bonding, of vitreous enamels onto aluminium alloys: The horizon extends, 19th International Enamellers Congress, Venice (2001).
- W. Kùhne, La smaltatura dei metalli leggeri, Tratto da Smalto Porcelanato - Tecnolgia e Mercati, Centro Italiano Smalti Porcellanati, N. 1 (2002).
- A.M. Compagnoni, A. Ferraro, Enamelling of aluminium alloys with high content of magnesium, 20th International Enamellers Congress, Turkey (2005).
- W. Kùhne, La smaltatura dei metalli leggeri, Tratto da Smalto Porcelanato – Tecnologia e Mercati, Centro Italiano Smalti Porcellanati, N. 1, 7-9, (2002).