Consecuencias para el acabado de superficies de zinc-níquel
Las influencias de la protección del clima en el acabado de superficies de zinc-níquel no son evidentes, pero son significativas. Hablar sobre la protección del clima y la fabricación de automóviles significa que la característica más buscada en un coche es su economía en el consumo de combustible, directamente correlacionado con las emisiones de dióxido de carbono. Los parámetros más relevantes que influyen en el consumo de combustible de un vehículo, entre otros, son la eficiencia del motor, el peso total del automóvil y el aire arrastrado por el vehículo. La resistencia aerodinámica está influenciada por el tamaño y la forma del vehículo sin ninguna influencia directa en el acabado de superficies.
¿Cuál es el impacto en la eficiencia del motor en los recubrimientos protectores?
La reducción del tamaño de los motores de combustión se lleva a cabo comúnmente para lograr una mayor eficiencia mediante la reducción del volumen de desplazamiento, pero manteniendo el mismo rendimiento en términos de par y de potencia de salida [1].
Tal reducción de tamaño hace que los motores más eficientes funcionen a temperatura media significativamente más alta en el motor y el colector de escape y los tubos de salida de un motor sean más grandes todo y siendo de la misma potencia. En consecuencia, temperaturas elevadas en el compartimento debajo del capó son de esperar con espacios más reducidos y motores más eficientes.
¿Cómo afecta a la construcción de un automóvil más ligero en el acabado superficial?
Se espera que la proporción de elementos más ligeros en la construcción de automóviles aumente del 30 al 70% en el 2030 con aleaciones de aluminio y aceros de alta resistencia que son los componentes que tienen la proporción más significativa [2].
Las condiciones de uso han cambiado y los nuevos materiales compuestos hacen que deban considerarse seriamente el tipo de acabado para asegurar una alta protección contra la corrosión del componente individual y el conjunto completo.
Además de las capacidades de protección contra la corrosión de un recubrimiento, debe cumplir con los tres factores principales que se necesitan, como son, la resistencia a temperaturas altas, la fragilización por hidrógeno y la corrosión galvánica en los contactos con diferentes metales.
Materiales de acero de alta resistencia son principalmente más susceptibles a la fragilización por hidrógeno que los aceros dulces. El montaje de materiales de aluminio con cualquier componente de acero recubierto tiene, básicamente, la desventaja de causar la corrosión galvánica o denominada de contacto.
La evitación de la fragilización por hidrógeno y de la corrosión galvánica, manteniendo las propiedades bajo las altas temperaturas de forma repetida, son importantes retos para la selección del material de recubrimiento.
El cambio constante en los materiales utilizados en el montaje del automóvil y una tendencia general hacia la producción de automóviles de mayor calidad, contribuye a un aumento de la demanda de acabados de zinc-níquel. Tal aumento de la demanda puede ser introducido en líneas de cincado tradicionales o alternativamente con procesos con una mayor productividad. Las siguientes investigaciones se han llevado a cabo utilizando un nuevo desarrollo de procesos Enthone de zinc-níquel, Zincrolyte Sprint y Zincrolyte Falcon optimizados para una mayor productividad, rendimiento y uniforme deposición de la aleación de zinc-níquel, dando una mayor calidad de acabado.
El zinc-níquel y la fragilización por hidrógeno
La deposición electrolítica de recubrimientos metálicos potencialmente puede introducir hidrógeno en materiales de acero. Tal hidrógeno, bajo ciertas condiciones de los materiales y de carga, puede causar que el componente de acero se fragilice y por lo tanto degradar su resistencia mecánica. La deposición de zinc-níquel ha demostrado ser muy adecuada como capa de protección, prácticamente sin generar hidrógeno durante su deposición electrolítica y así minimizar la fragilización del material [3]. Esta ventaja se atribuye al hecho de que el zinc-níquel es altamente permeable al hidrógeno y adicionalmente se forma una fina capa de níquel puro a la interfaz con el sustrato de acero en el proceso de recubrimiento. Esta capa intermedia de níquel se asume para facilitar catalíticamente la recombinación de átomos de hidrógeno que forman el hidrógeno molecular, por lo tanto, reduciendo la concentración de hidrógeno atómico sobre el metal base a la interfaz del recubrimiento de zinc-níquel. Las investigaciones, teniendo en cuenta la susceptibilidad para la refragilización en la vida de servicio del recubrimiento de zinc-níquel, han demostrado que es superior a otros recubrimientos [4].
El zinc-níquel y materiales de aluminio
La causa raíz de la menor corrosión por contacto con el zinc-níquel en diferentes proporciones de aleación de níquel ha sido investigada con una aleación de aluminio-magnesio. Paneles de AlMg3 se han conectado a los paneles recubiertos con aleaciones de zinc-níquel con diferentes porcentajes de níquel. Ambos paneles habían sido sumergidos en una solución al 3% de cloruro sódico, ajustado el pH a 7 y la corriente de corrosión o acoplamiento resultante, fue grabada por un analizador electroquímico, según se muestra en la figura 1. La investigación fue llevada a cabo con un panel con 12 micras de zinc puro depositado sobre acero dulce con un electrolito alcalino (Enthobrite NCZ Dimensión, Enthone) y revestimientos de aleación de zinc-níquel 7 micras sobre acero dulce con un 12 a un 15% en peso de níquel (Zincrolyte Falcon, Enthone). No hay pasivados u otros tratamientos posteriores sobre dichos recubrimientos.
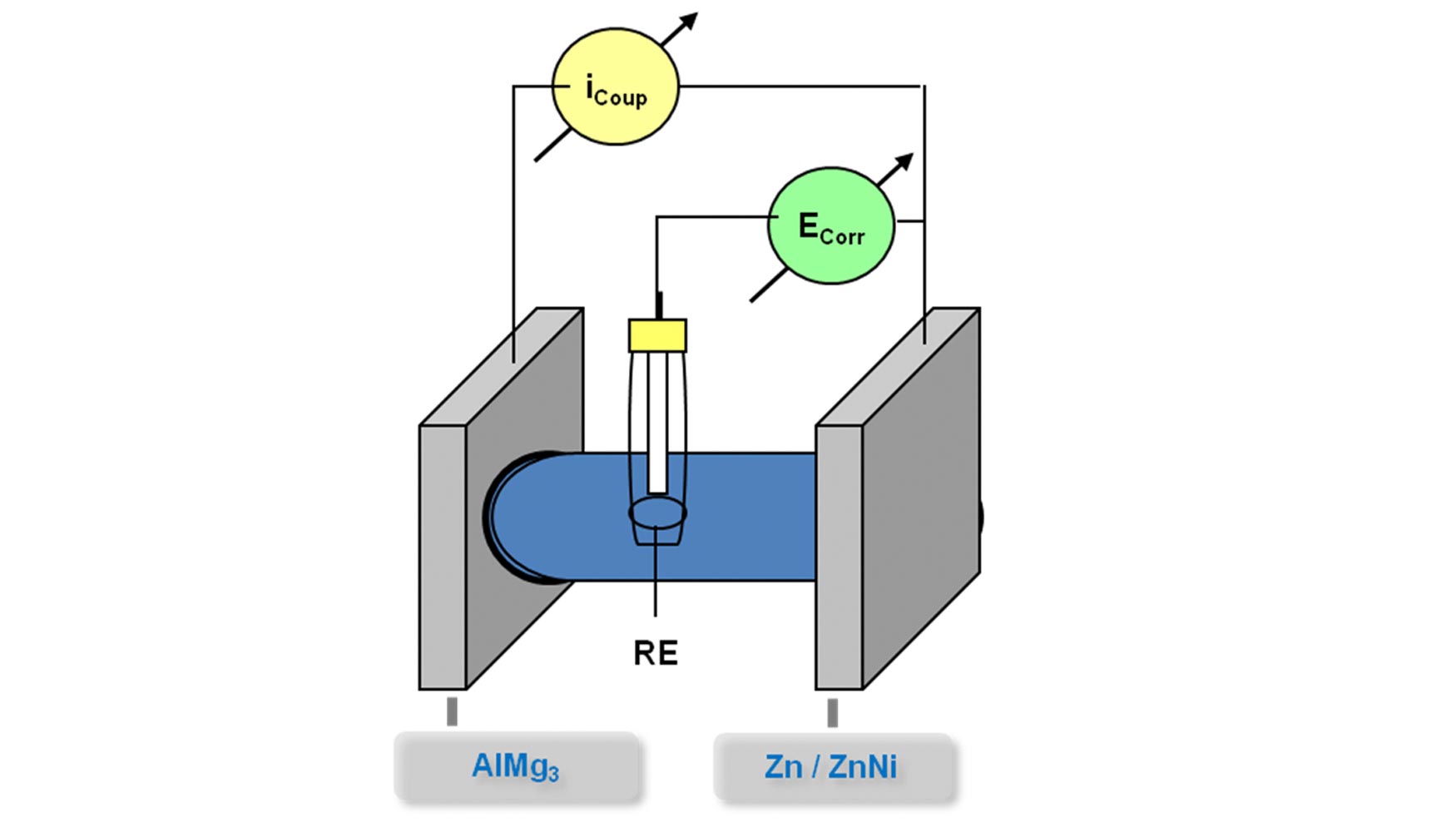
Las corrientes de corrosión registradas para las diferentes aleaciones de zinc-níquel son significativamente inferiores a las de un recubrimiento de zinc puro (figura 2). Este diagrama muestra las densidades de corriente de corrosión grabadas durante un tiempo de inmersión de 6 h. Las densidades de corriente fluctuantes en el comienzo del experimento se estabilizan después de unas 4 h con una alta densidad de corriente anódica en la superficie de zinc. Todas las aleaciones de zinc-níquel probadas sobre la aleación de AlMg3 muestran un contacto significativamente más bajo de densidades de corriente, que van aproximadamente a una quinta parte de la densidad de corriente de corrosión observada en el experimento utilizando una superficie de zinc.
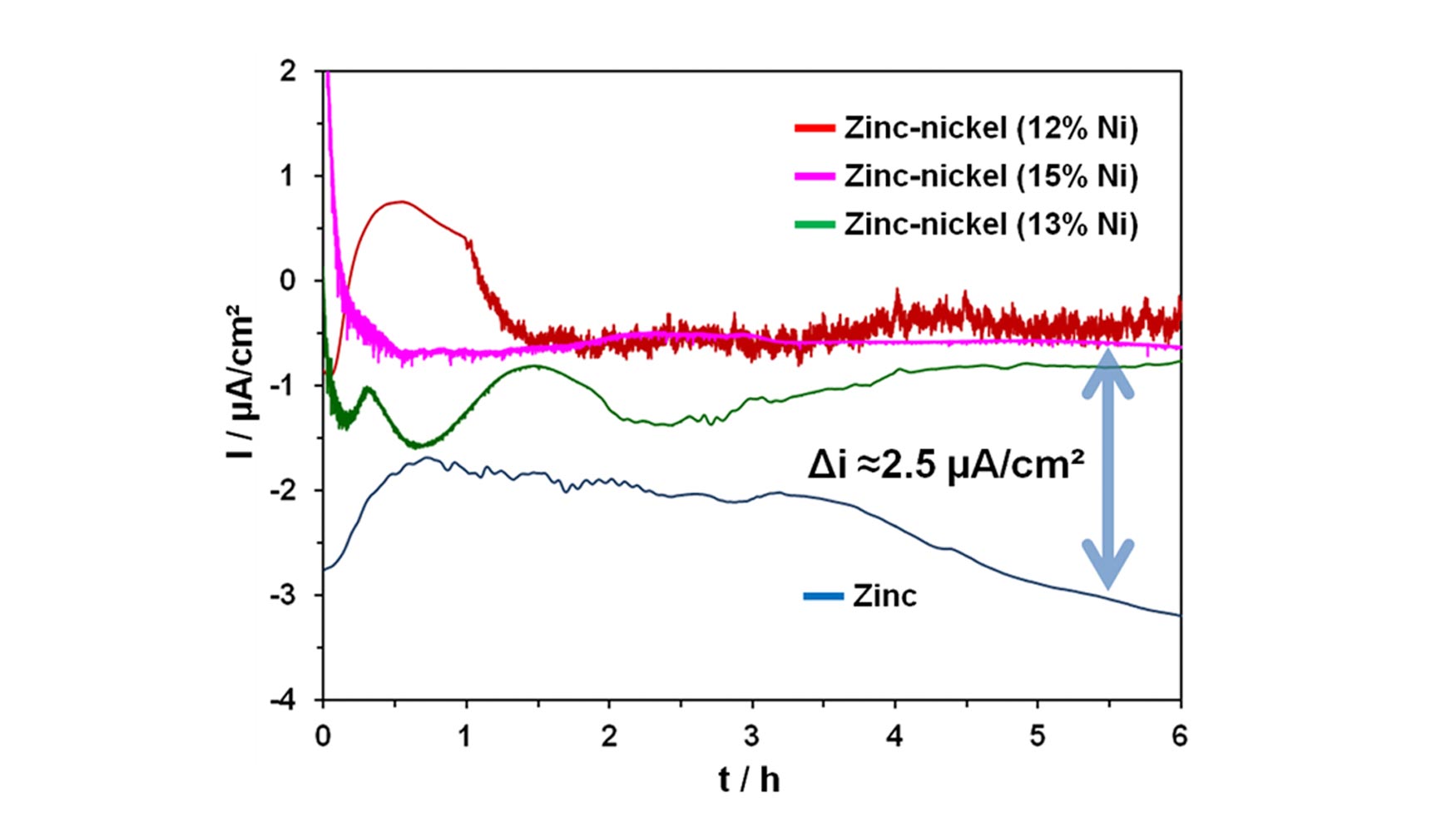
Figura 2. Curvas de corriente de corrosión del AlMg3 en contacto con recubrimiento de zinc (curva azul) y con aleación de zinc-níquel con diferentes porcentajes de Ni en el depósito.
Curiosamente, las diferencias en la densidad de corriente de corrosión encontradas con las tres aleaciones de níquel diferentes no son muy distintas y en la escala de la señal así se observa. Dentro de la gama investigada del contenido de níquel del 12 al 15% en peso no se encuentran diferencias significativas para estas aleaciones en el comportamiento a la corrosión de contacto hacia AlMg3. Altamente significativo es que la superficie recubierta de zinc con corrosión es aproximadamente unas 5 veces mayor que la de zinc-níquel con el mismo material base.
El resultado de estas diferentes corrientes de corrosión se puede ver en las imágenes tomadas de muestras de ensayo después de 17 horas en contacto con AlMg3 sumergidas en solución de NaCl al 3% (y ajustado el pH a 7). La superficie de zinc aparece fuertemente corroída, mientras que el zinc-níquel (con un 15% en peso de Ni) muestra solamente cierta decoloración superficial (figura 3).
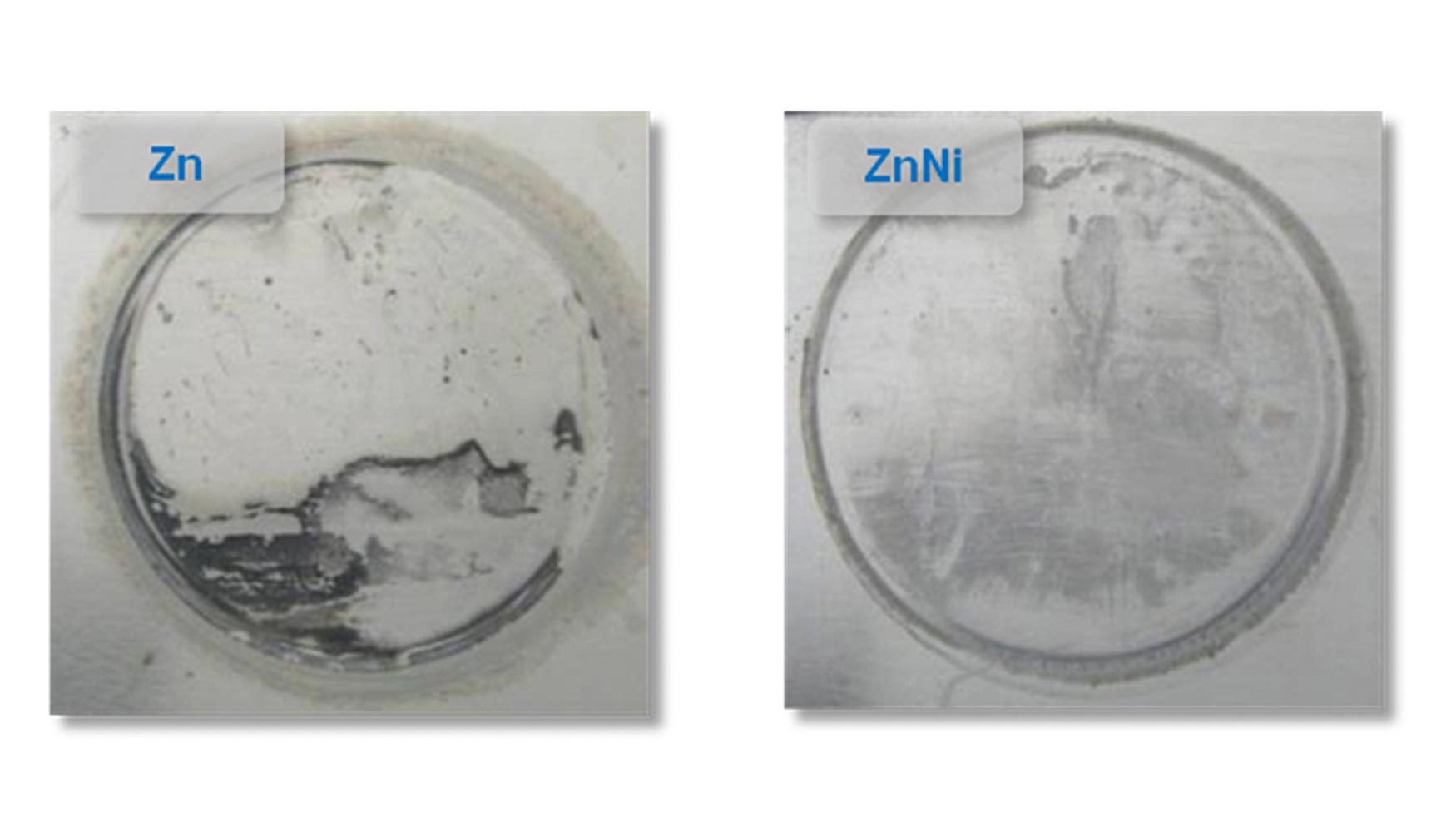
Figura 3. Paneles de acero recubiertos de Zn (izquierda) y Zn-Ni (derecha), después de 17 h en contacto con AlMg3, con una solución al 3% de NaCl a pH 7.
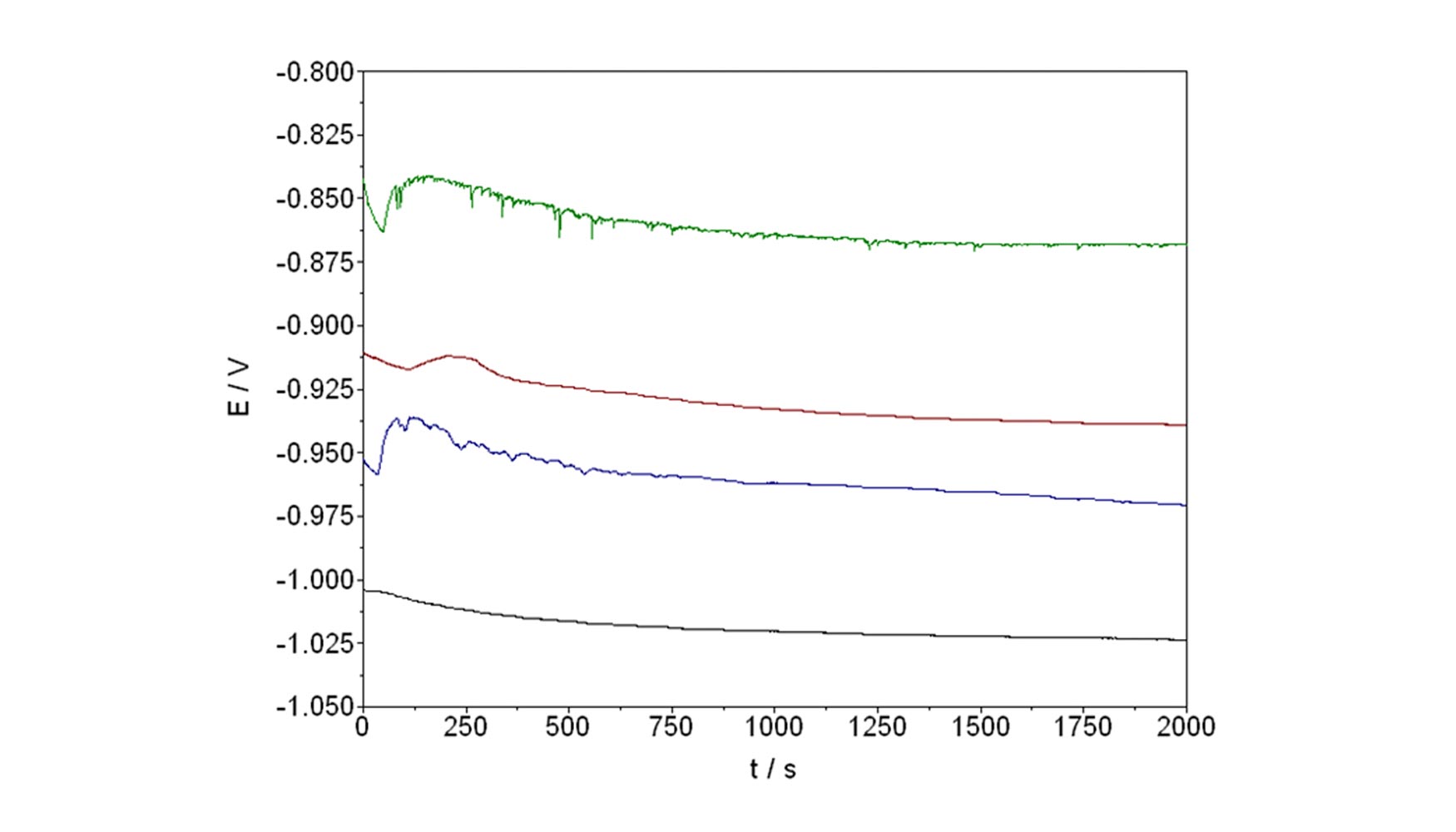
Figura 4. OCP de zinc (negro) y zinc-níquel (en azul con un 12% de Ni, en rojo con un 13% de Ni y en verde con un 15% de Ni). OCP del AlMg3 medido en la misma solución es – 0,68 V.
Se utilizaron tres electrodos con los espectros de impedancia que se registran en el potencial de circuito abierto. A plata / electrodo de referencia de cloruro de plata se acopló capacitivamente a un alambre de Pt para reducir el desplazamiento de fase a altas frecuencias. Espectros de impedancia registraron el potencial de circuito abierto en el intervalo de frecuencia de 10 kHz a 10 MHz usando un analizador de respuesta en frecuencia (Autolab PGSTAT 30, Eco-Chemie). La amplitud de la señal de tensión sinusoidal fue de 20 mV (rms).
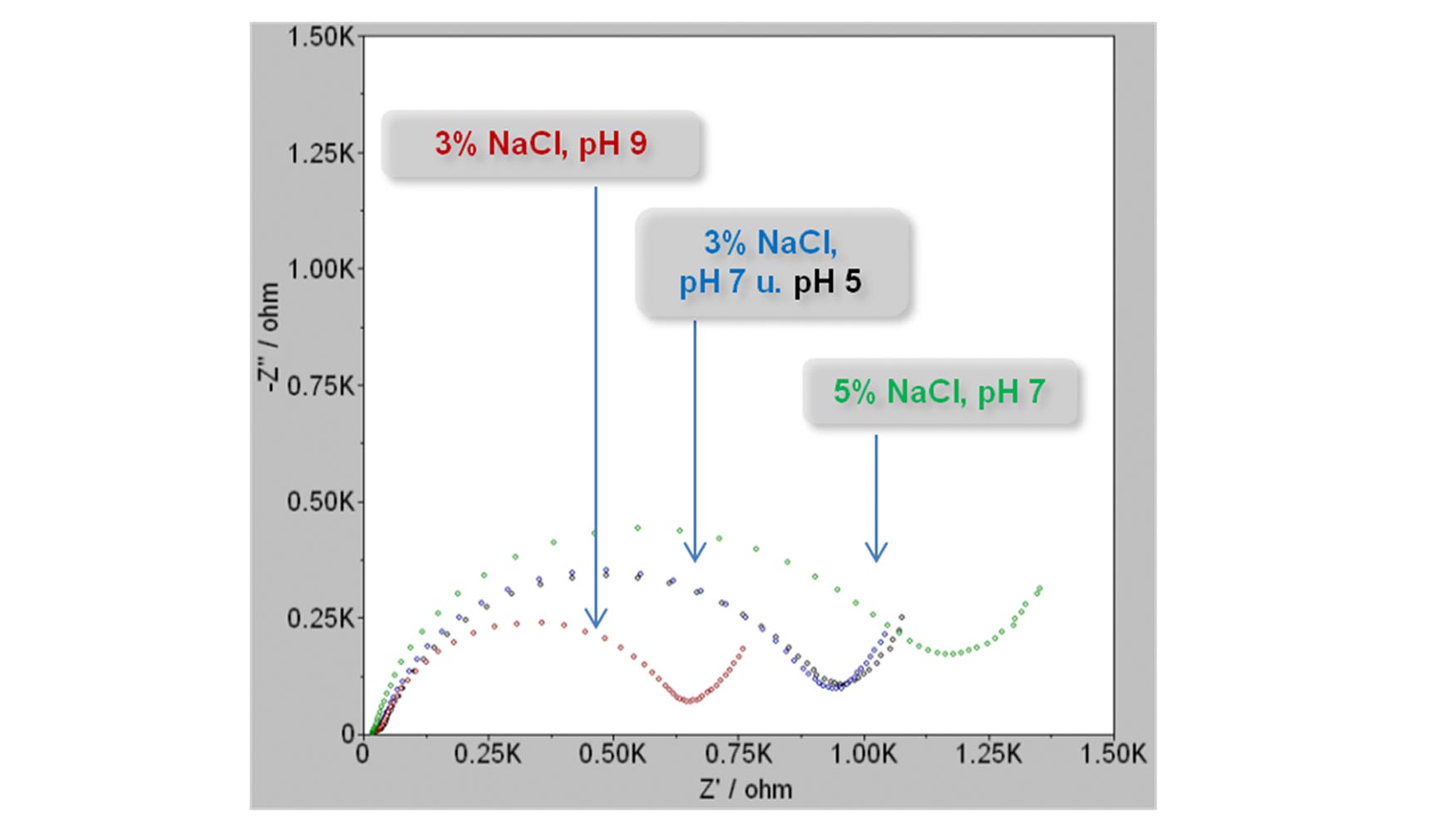
La figura 6 muestra los correspondientes diagramas de Nyquist para zinc puro en estos ambientes.

Figura 6. Diagramas de Nyquist de recubrimiento de zinc alcalino sobre acero dulce, en los mismos ambientes que en la figura 5.
Estos resultados son una fuerte indicación de que no sólo son las diferencias de potenciales de corrosión entre el zinc y el zinc-níquel las que favorecen unas corrientes de corrosión más bajas en la capa de zinc-níquel, sino a una significativa capacidad del zinc-níquel para formar una capa pasiva sobre su superficie.
Zinc-níquel y altas temperaturas en su entorno
Después de 7 días a 250°C, muestras con 8-10 micras Zn-Ni (14% en peso de Ni) tratadas con un pasivado libre de cobalto (Zincrolyte Sprint, Perma Pass, Ultra IV Plus, Enthone) y selladas con un recubrimiento de polímero (Enseal 21, con un coeficiente de fricción μtot = 0,09-0,14), no muestran corrosión significativa incluso después de 768 horas en ensayo de niebla salina neutra (NSS) según la norma ISO 9227.
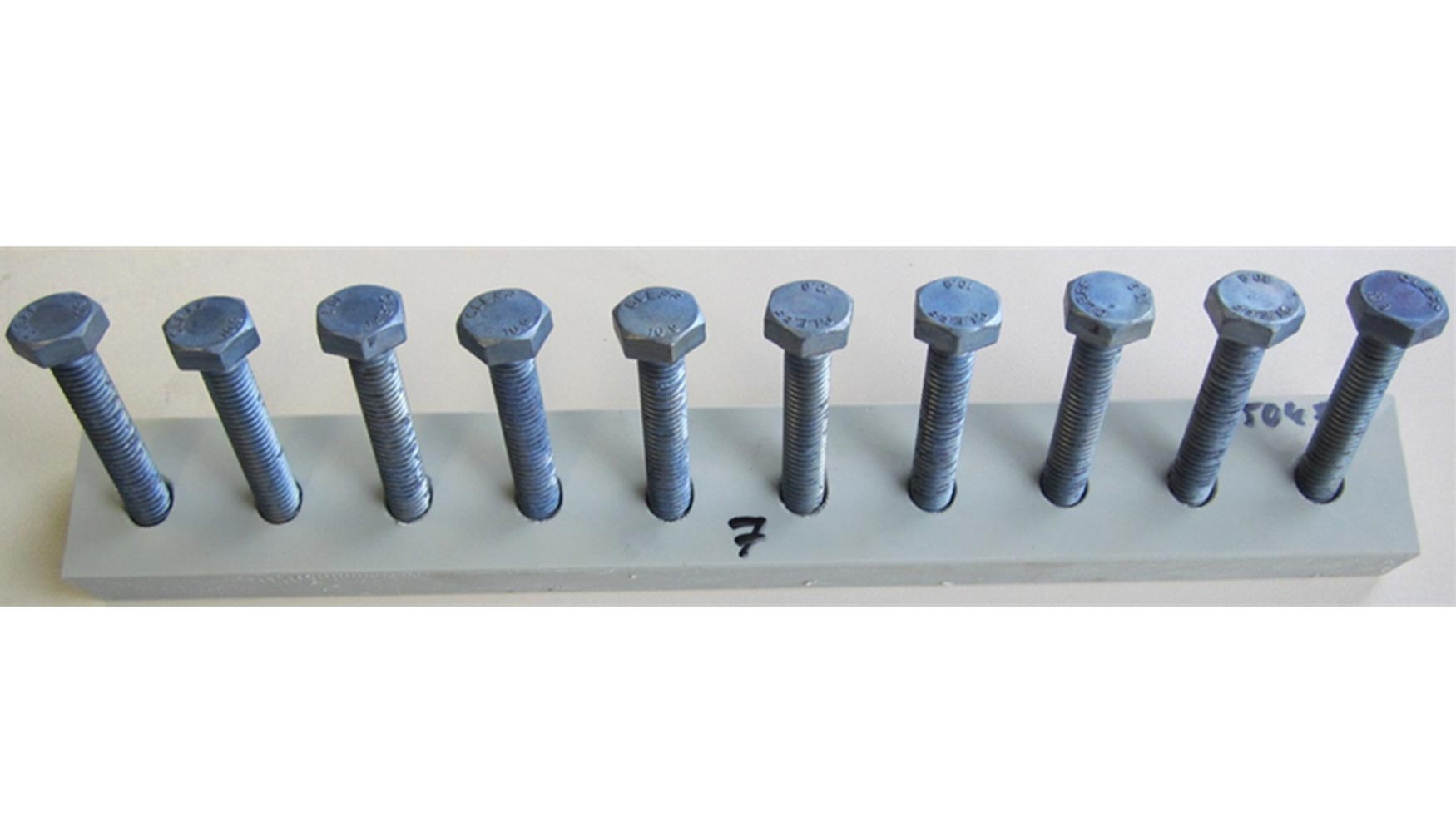
Conclusiones
- El zinc-níquel es un excelente material para proporcionar protección contra la corrosión catódica a los componentes de acero. Dentro de las muchas propiedades beneficiosas de este recubrimiento está la baja fragilización por hidrógeno y refragilización, así como las propiedades de resistencia a la corrosión galvánica en contacto con aleaciones de aluminio y su resistencia a altas temperaturas.
- Se puede concluir que el zinc-níquel es un recubrimiento excelente para los cambios en curso con la industria del automóvil en movimiento hacia la menor emisión, vehículos de mayor economía de combustible y el cambio resultante en los materiales y condiciones de uso.
- Junto con un aumento constante en la demanda de calidad y los períodos de garantía prolongados, estos cambios representan un aumento de la demanda en los recubrimientos de zinc-níquel.
- Nuevos desarrollos recientes de electrolitos Zincrolyte Sprint para aplicaciones a tambor y Zincrolyte Falcon para aplicación a bastidor, en los procesos de recubrimiento de zinc-níquel proporcionan una alta calidad más consistente y una mayor productividad. Aprovechando estas características de las aleaciones de zinc-níquel, crea aún más valor al utilizar soluciones de acabado que tienen una mayor calidad y productividad, siendo un nuevo nivel superior de acabado.
Referencias
- P. Leduc, B. Dubar, A. Ranini, G. Monnier, ‘Downsizing of Gasoline Engines: An Efficient Way to Reduce CO2 Emissions’ Oil & Gas Science and technology, Rev. IFP, Vol. 58 (2003), No. 1, pp. 115-127
- R. Heuss, N. Müller, W. van Sintern, A. Starke, A. Tschiesner, ‘Lightweight, heavy impact’, McKinsey report, Feb 2012
- W. Paatsch, R. Landgrebe, M.M. Lohrengel, ‘ZnNi – Beschichtung hochfester Bauteile aus Stahl’, Mat.-Wiss.u. Werkstofftech, 2008, 39, No. 1
- C. Krauß, O. Golenishcheva, G. Andersohn, M. Oechsner, ‘Mechanisms of hydogen-induced cracking in high-strength screws’, Mat.-Wiss.u. Werkstofftech, 2015, 46, No. 2