Tres casos reales: amortizaciones desde dos meses y ahorros hasta 60 mil €/ año
Mejorando la eficiencia de nuestras instalaciones industriales
El Comité Técnico de la Asociación de Fabricantes Españoles de Lanas Minerales Aislantes (Afelma) examina a través de tres casos prácticos las acciones que podemos llevar a cabo para que nuestras instalaciones industriales sean más eficientes. La potencialidad de estas actuaciones va a estar siempre condicionada al tipo de instalación con la que nos encontremos; pero hay un factor común a todas ellas: el consumo energético.
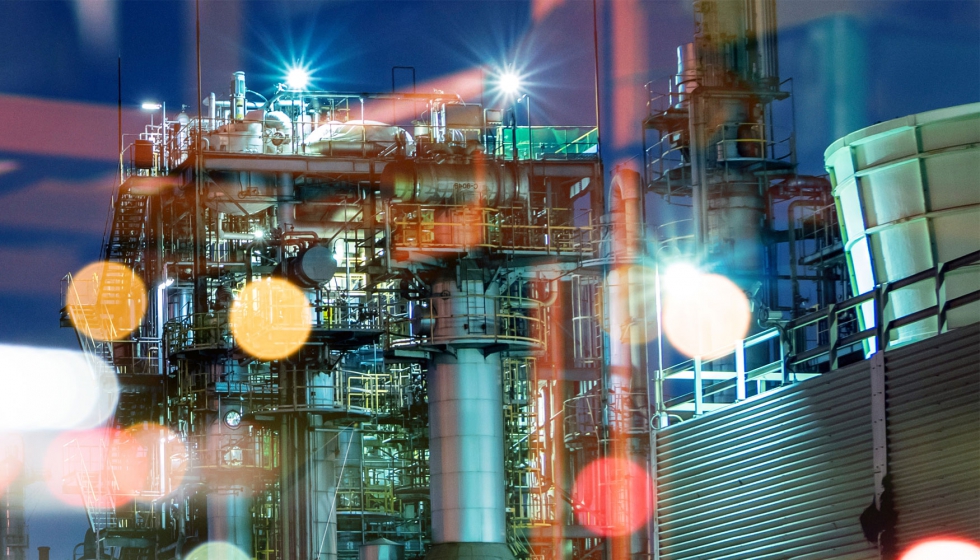
Hoy en día, al margen de los precios de la energía, es indispensable cuestionarnos si toda la energía que consume un proceso es necesaria, o, por el contrario, se puede reducir. Una reducción del consumo energético que permitirá, además del consiguiente ahorro económico, la disminución de emisiones de CO2 al entorno, con lo que estaremos contribuyendo, a tener un mundo más sostenible.
Existen multitud de medidas o buenas prácticas para disminuir el consumo energético y hacer realidad los consiguientes ahorros, pero, en cualquier caso, no debemos perder de vista el impacto en inversión que esas medidas suponen y, por tanto, su plazo de amortización. Por lo que tendremos que estudiar las diferentes acciones y evaluar todas sus implicaciones.
Aislar una instalación que previamente carecía de aislamiento, como una tubería, un tanque o un equipo, es una tarea relativamente fácil y económica de llevar a cabo, si la comparamos con otras medidas de ahorro energético como pueden ser la automatización de equipos o un cambio de variadores por arrancadores en los motores. Por ello, el aislamiento constituye una de las medidas más eficaces y rentables, consiguiendo importantes ahorros energéticos, sin requerir grandes inversiones.
En 2014, EIIF (la Fundación Europea del Aislamiento Industrial) coordinó un estudio con ECOFYS en el que se detectó que al menos un 10% de las instalaciones no están aisladas o lo están con un aislamiento insuficiente o en malas condiciones. En los casos en los que existía aislamiento la inversión realizada fue mínima, ya que solo se tuvo en cuenta la temperatura superficial para evitar daños personales, así como las puras necesidades del proceso industrial.
De este estudio se dedujo que el potencial de ahorro en la industria europea supone el equivalente al consumo energético de 15 plantas de energía alimentadas por carbón (500MW) o el consumo energético de 10 millones de viviendas. Sin perder de vista la reducción de emisiones de CO2 que acompaña a este ahorro energético, esta sería equivalente a la reducción de emisiones de CO2 de 18 millones de coches. En definitiva, la inversión que supondría aislar estas superficies no aisladas o con un aislamiento deficitario se estima en 900 millones de euros que permitirían un ahorro en energía para la industria de unos 3.5 billones de euros cada año.
Si nos centramos en las zonas o partes de la instalación que no estén aisladas o que tengan el aislamiento muy deteriorado, el retorno de la inversión será normalmente menor a 1 año (amortización < 1 año).
¿Cuáles serían los pasos a seguir para identificar el potencial de ahorro energético a través del aislamiento?
1. Aislar las partes no aisladas o dañadas (serán las que tengan el mayor potencial, con plazos de amortización menores a un año).
2. Calcular el aislamiento Coste-Efectivo y tener en cuenta el Coste Energéticamente Eficiente.
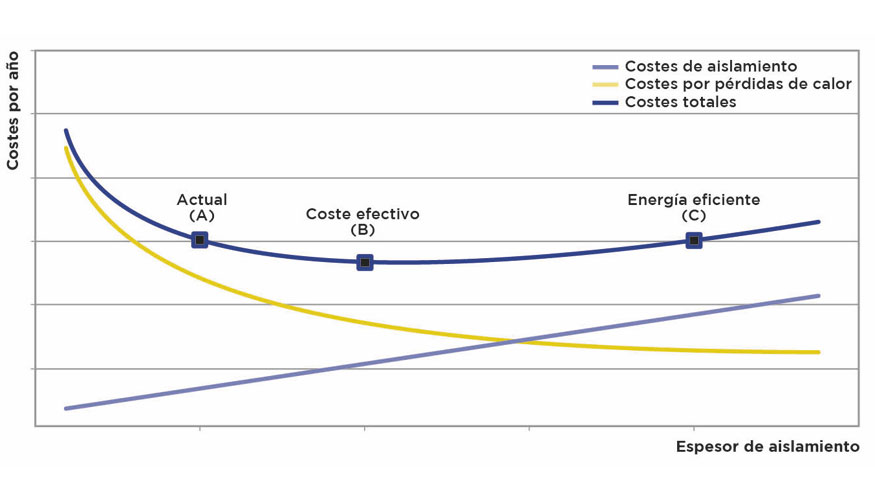
3. Involucrar a expertos en aislamiento.
Con el propósito de conocer el estado actual del aislamiento de una instalación y poder analizar el potencial de ahorro económico a través del aislamiento, EIIF forma a ingenieros expertos en la materia para poder llevar a cabo auditorías energéticas del aislamiento denominadas Tipcheck.
La herramienta Tipcheck permite identificar las zonas de la instalación de mayor potencial de ahorro energético donde se cuantifica la cantidad de energía y, por tanto, de dinero, que se está perdiendo en la instalación actual, para finalmente proponer unas soluciones específicas de aislamiento para cada parte de la instalación. También se analiza el coste de la inversión que supone la implementación de la solución indicada, para poder obtener el payback de cada caso.
A continuación, se muestran varios Tipchecks realizados recientemente donde se pone de manifiesto el potencial de ahorro que existe en nuestras plantas industriales a través del aislamiento:
1. Tipcheck realizado en un secadero de placa de yeso laminado.
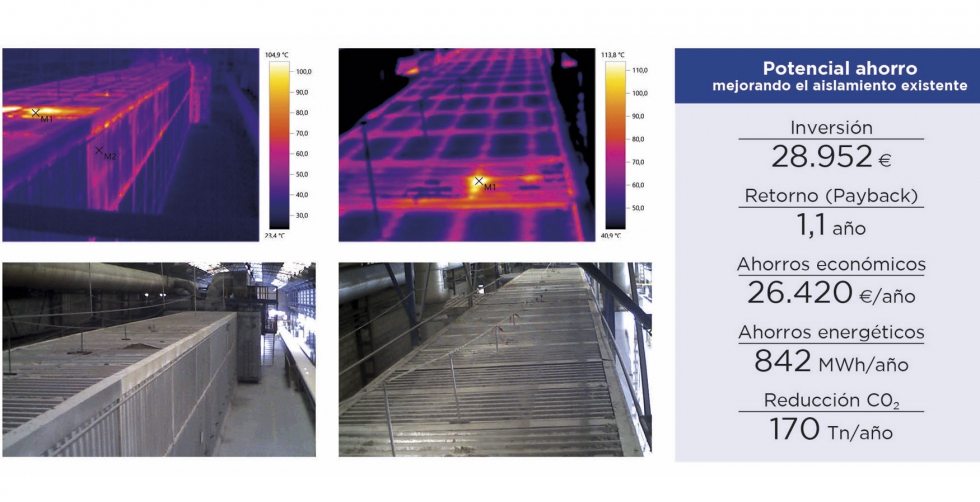
2. Tipcheck realizado en un horno de tratamiento térmico de piezas metálicas para la automoción.
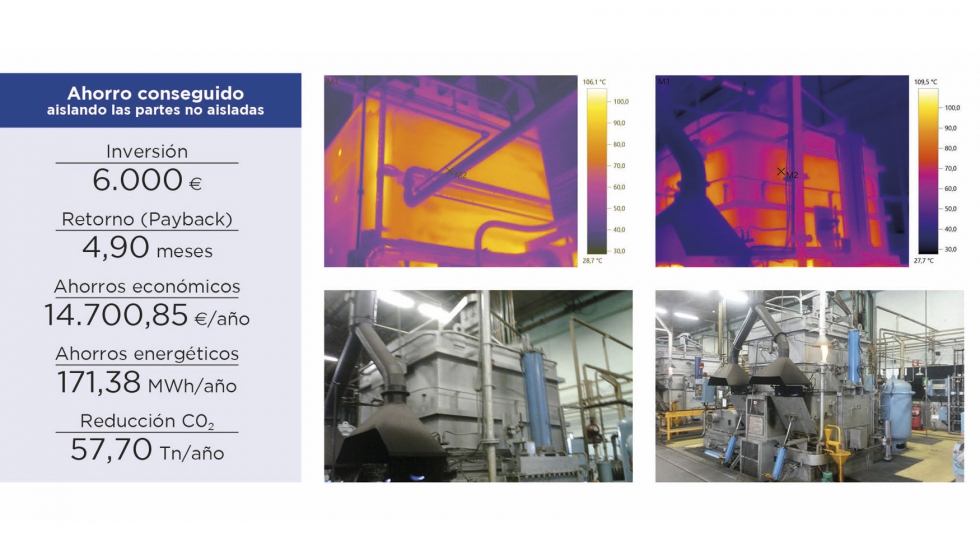
3. Tipcheck realizado en un horno cerámico para la construcción modular prefabricada.
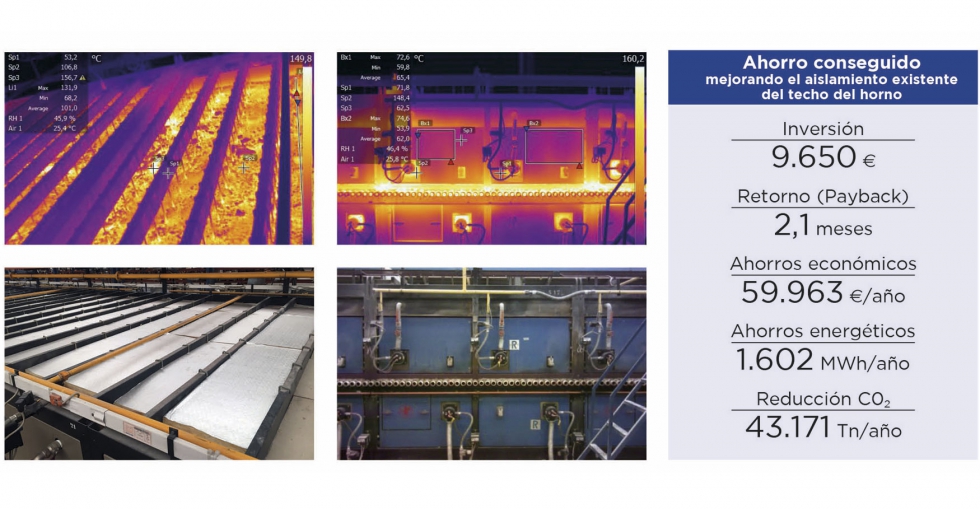
Las empresas asociadas a Afelma cuentan con especialistas acreditados como Tipcheck Engineer, que ya han realizado auditorías a compañías y empresas, con las soluciones de aislamiento térmico que han permitido reducir las pérdidas energéticas, optimizando su consumo, con el consiguiente ahorro.