Lo frío, lo limpio, llave para lo difícil
Convencionalmente, en los procesos de mecanizado con el fin de alargar la vida útil de las herramientas y conservar la integridad superficial de los componentes es habitual utilizar emulsiones de refrigerantes/lubricantes, conocidos como fluidos de corte. La cantidad de refrigerante/lubricante que contienen dichas emulsiones varía en función de su composición. En el caso de utilizar emulsiones de aceite mineral su concentración está por encima del 40%. En cambio, si se utilizan emulsiones semi-sintéticas esta cifra puede reducirse hasta suponer un 5% del total, aunque económicamente supone duplicar la inversión en fluidos de corte.
La problemática del uso de estas emulsiones, coloquialmente conocidas como taladrinas, radica en su insalubridad e impacto que tienen tanto económico como medioambiental en los procesos de mecanizado. Económicamente, su uso en la industria automovilística alemana llega a suponer entre un 7 y 17% del coste total de fabricación de la pieza [1]. Sin embargo, en el sector aeronáutico esta cifra puede ascender hasta suponer entre el 20-30% en piezas de alto valor añadido [2]. Además, su tratamiento una vez terminada su vida útil ronda 0,6 €/kg de taladrina en función de la región donde deba ser manipulada. Desde un punto de vista medioambiental su tratamiento no resulta totalmente eficiente ya que durante su vida útil de las 320.000 Tm/año que se utilizan en Europa, el 30% se pierden por fugas, suciedad, procesos de limpieza de las piezas, etc. [3, 4]. Finalmente, en cuanto a salubridad humana, según el NIOSH (National Institute of Occupational, Safety and Health de EE UU) hay alrededor de 1,2 millones de trabajadores a nivel mundial expuestos a sus efectos nocivos entre los que se encuentran la irritación cutánea o acné y en los casos más extremos pérdida de función pulmonar o neumonía hipersensible [5, 6].
En este contexto, una de las apuestas de la Unión Europea es la fabricación limpia o ‘green manufacturing’ en cuanto a sus objetivos ‘20-20-20’, es decir, reducir los gases de efecto invernadero en un 20%, conseguir que el consumo de energía proveniente de fuentes renovables sea del 20% y aumentar un 20% la eficiencia energética en el año 2020 [7]. Con este fin, en la industria del mecanizado se han desarrollado diferentes alternativas que van desde utilizar recubrimientos de herramientas formados por lubricantes sólidos hasta el mecanizado de taladrina con alta presión. Estas técnicas tienen el hándicap de que o no son económicamente sostenibles, o por el contrario lo son, pero medioambientalmente son ineficientes. Sin embargo, dos técnicas que están cogiendo peso industrialmente en los últimos años —y que son tanto económicamente como medioambientalmente sostenibles— son la lubricación por pulverización de micropartículas de aceite biodegradable (MQL) o la refrigeración criogénica. Además, actualmente el uso de las tecnologías limpias en Sudamérica presenta un creciente interés y puede suponer un gran nicho de mercado debido a la tendencia de las compañías del sector ubicadas allí en obtener procesos de mecanizado más eficientes y sostenibles.
En los siguientes puntos se exponen dichas tecnologías y cómo su combinación puede dar respuesta al sector de turbomaquinaria aeronáutica y su creciente demandada de mecanizado de materiales de difícil maquinabilidad.
Sistemas MQL
Las primeras patentes de sistemas de lubricación por micropulverización de aceite propiamente dichas parten de 1964 donde se patenta un sistema MQL de un canal el cual incorpora una cámara de mezcla y dos llaves de paso para el control del caudal de aire y aceite, respectivamente [8]. Sin embargo, no es hasta inicio del siglo XXI que debido a la toma de conciencia medioambiental y de salubridad laboral donde los sistemas MQL empiezan a ser tenidos en cuenta para los procesos de mecanizado.
Actualmente los sistemas MQL, han supuesto una alternativa medioambientalmente respetuosa a la vez que económicamente factible. Ventajas como la disminución del uso de fluidos de cote, el aumento de la higiene industrial, la utilización de aceites biodegradables, su estabilidad térmica durante el mecanizado o la obtención de virutas prácticamente limpias han logrado que estos sistemas tengan una buena aceptación en los entornos industriales.
El funcionamiento de todos los sistemas MQL están basados en la micropluverización del aceite mediante efecto Venturi con una corriente de aire. Sin embargo, actualmente existen variantes en cuanto a cómo y dónde se produce dicha pulverización. En función de ello existen sistemas MQL de un canal o de dos canales como se puede observar en la figura 1. Con los primeros sistemas el aerosol es formado en el propio depósito de aceite y transportado por un solo conducto hasta la zona de corte. Sin embargo, con los sistemas MQL de dos canales el aire y aceite son conducidos por canales independientes hasta el extremo de la tobera de inyección donde el aerosol es formado.
![Figura 1. Sistemas MQL. (a) Dos canales. (b) Un canal. [9] Figura 1. Sistemas MQL. (a) Dos canales. (b) Un canal. [9]](https://img.interempresas.net/fotos/1293460.jpeg)
Aunque tribológicamente ambas técnicas son análogas, tecnológicamente están diseñadas para dar respuesta a diferentes situaciones en función de si se desea aplicar el aerosol de forma externa o interna a la herramienta. Por un lado el sistema de un canal puede ser aplicado en ambas situaciones. Por otro, el sistema MQL de dos canales está diseñado primordialmente para lubricación externa. Aunque este planteamiento inicial hace pensar como primera opción el instalar únicamente sistemas MQL de un canal, hay que tener en cuenta que es sensible a la condensación de las micropartículas de aceite en el interior de los conductos de los canales de inyección. Dicha condensación provoca un ‘babeo’ en la salida que se traduce en una lubricación ineficiente de la herramienta que acortará su vida útil. Por ello la elección de un sistema u otro debe estudiarse con detenimiento.
La aplicación de la lubricación mediante MQL en materiales como el aluminio o aceros al carbono por lo general resulta satisfactoria. Concretamente, para el mecanizado de aluminio, en el taller del Dpto. de Ingeniería Mecánica de la ETSI de Bilbao se realizó en 2006 una investigación con una aleación 5083-H112 donde se fresó a una velocidad de corte de casi 1.000 m/min y 5.000 mm/min de avance. La herramienta utilizada fue una fresa de acero rápido (HSS) con un 8% de cobalto de 12 mm de diámetro y dos labios. Al comparar la lubricación mediante MQL durante el mecanizado a alta velocidad frente al uso de taladrina se observó como con la lubricación MQL se conseguía una mayor productividad gracias al aumento de la velocidad de corte en combinación con un menor de desgaste de la herramienta debido a la mejor penetración de las micropartículas de aceite en el filo de corte frente a la taladrina.
En cuanto a aceros al carbono, en una investigación publicada en Journal of Materials Technology en 2009 al tornear con un inserto de metal duro sin recubrir un acero AISI 9310 se concluyó que al utilizar la lubricación mediante MQL se obtenía una temperatura de corte inferior en un 10% a la vez que se reducía el desgaste en un 60% después de 45 minutos de mecanizado frente al uso de taladrina [10].
Refrigeración criogénica
La refrigeración criogénica tiene su principal aplicación, al contrario que ocurre con la lubricación MQL, en el mecanizado de aquellos materiales que provocan sobre la herramienta desgastes debido a efectos térmicos como la difusión o adhesión. El primer sistema de refrigeración criogénica aplicado al mecanizado data de 1919. Sin embargo, debido al alto coste que suponía licuar los gases no es hasta nuestros días en el que se vuelve una alternativa factible.
Los gases que normalmente se utilizan como fluidos de corte son el nitrógeno líquido (LN2) y el dióxido de carbono licuado (CO2). La razón por la que estos gases son utilizados como fluidos de corte se debe a un equilibrio entre razones económicas y físicas. El LN2 es utilizado debido a que el aire atmosférico está compuesto de nitrógeno en un 70% aproximadamente y tiene una alta capacidad refrigerante (-196 °C). Sin embargo, como contrapartida es de difícil almacenamiento ya que el LN2 es mantenido en estado líquido por temperatura, es decir, se encuentra en un recipiente en dicho estado a -196 °C y presión atmosférica. Por ello, el LN2 está continuamente evaporándose generando sobrepresiones en el recipiente que deben ser expulsadas a la atmósfera para evitar explosiones. Este inconveniente hace que desde un punto de vista industrial sea más atractivo el dióxido de carbono –a pesar de tener una capacidad refrigerante menor (-78 °C)–. El CO2 se encuentra en estado líquido en recipientes presurizados a 55-60 bares a temperatura ambiente lo que hace que no existan pérdidas debido a su evaporación. Además, desde un punto de vista ambiental el CO2 utilizado es reciclado, es decir, se captura de un proceso primario en el cual sería expulsado como desecho y se licua para un posterior uso. De este modo al utilizar el CO2 se mantiene la inocuidad medioambiental asociada a la refrigeración criogénica. Por contrapartida, el CO2 tiene la propiedad de convertirse en hielo seco antes de evaporarse una vez es despresurizado, como se puede observar en el diagrama de fases de la figura 2. Esto hace que sea necesario un sistema de regulación para impedir que los conductos se taponen con hielo seco. Habitualmente, dichos sistemas se basan en la presurización de los conductos por los que va a circular el CO2 con un valor por encima del punto triple y así conseguir llevarlo hasta la zona de corte en estado líquido donde se expande convirtiéndose en gas y micropartículas de hielo seco.
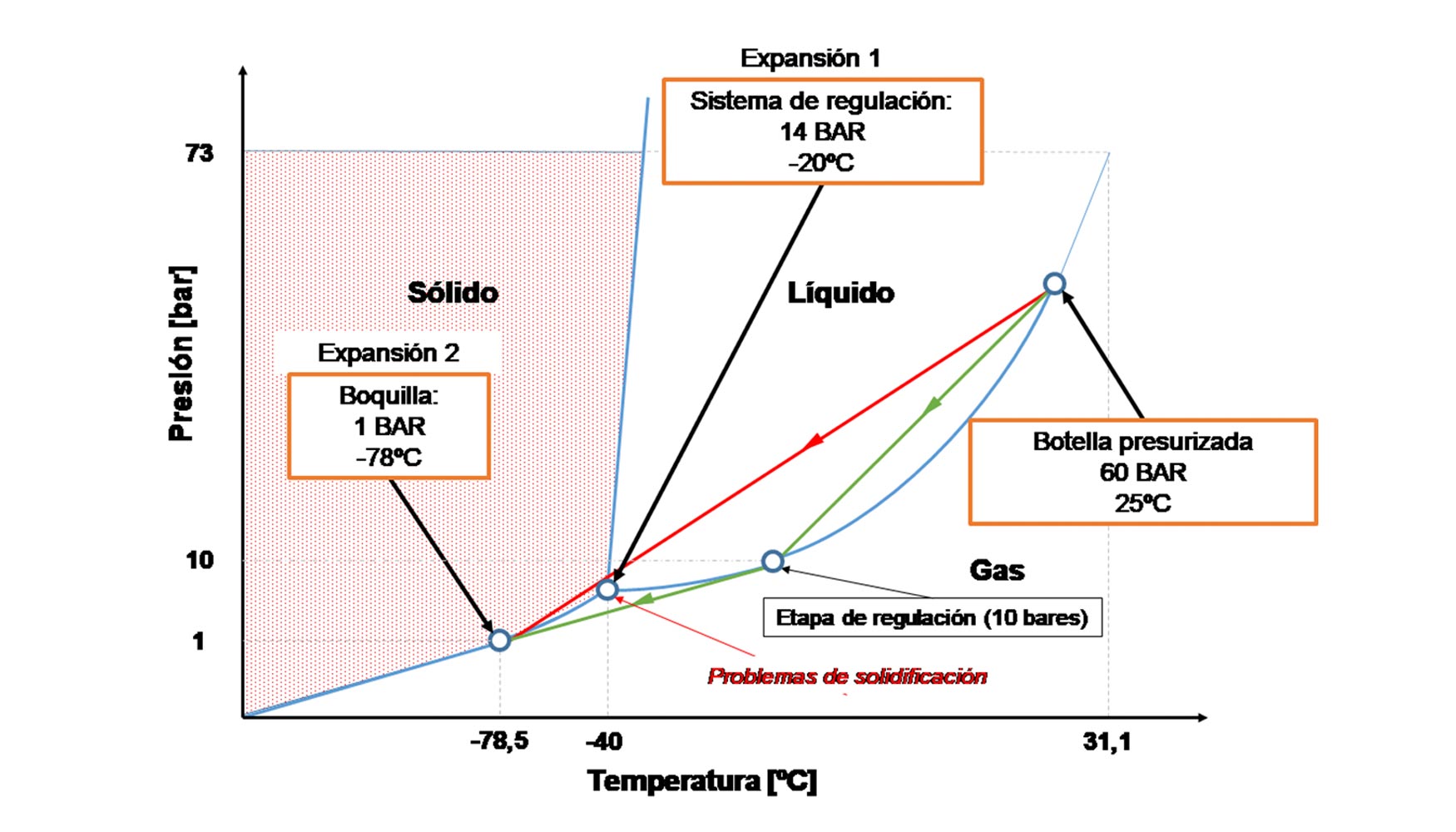
La refrigeración criogénica, como se indicó anteriormente, es una alternativa viable cuando el desgaste predominante de la herramienta es provocado por efectos térmicos. En esta línea son varios los trabajos llevado a cabo por el Grupo de Fabricación de Alto Rendimiento del Dpto. de Ingeniería Mecánica de la UPV-EHU junto con Tecnalia. Uno que cabe destacar es la aplicación de la refrigeración criogénica con CO2 en el taladrado de stacks de fibra de carbono y titanio (CFRP-Ti6Al4V), material compuesto demandado tanto en el sector aeronáutico como aeroespacial con el fin de reducir el peso de las aeronaves. Debido a la diferencia de propiedades entre los diferentes materiales que componen el composite, por un lado la herramienta se ve sometida a abrasión por parte del CFRP y por otro a la adhesión por parte del Ti-6Al-4V. Además, los taladrados deben ser realizados en seco con el fin de que la taladrina no contamine el CFRP, con lo que las condiciones de trabajo para la herramienta son muy severas. En el caso de combinar brocas con conductos internos y la refrigeración criogénica después de 160 taladrados, como se puede observar en la figura 3, los agujeros no muestran ningún daño térmico ni la herramienta contiene Ti-6Al-4V adherido al filo de corte de la broca. Además, el diámetro de los agujeros a lo largo del ensayo se mantiene más constante y cercano a la medida nominal de la broca de lo que ocurre cuando se mecaniza en seco.
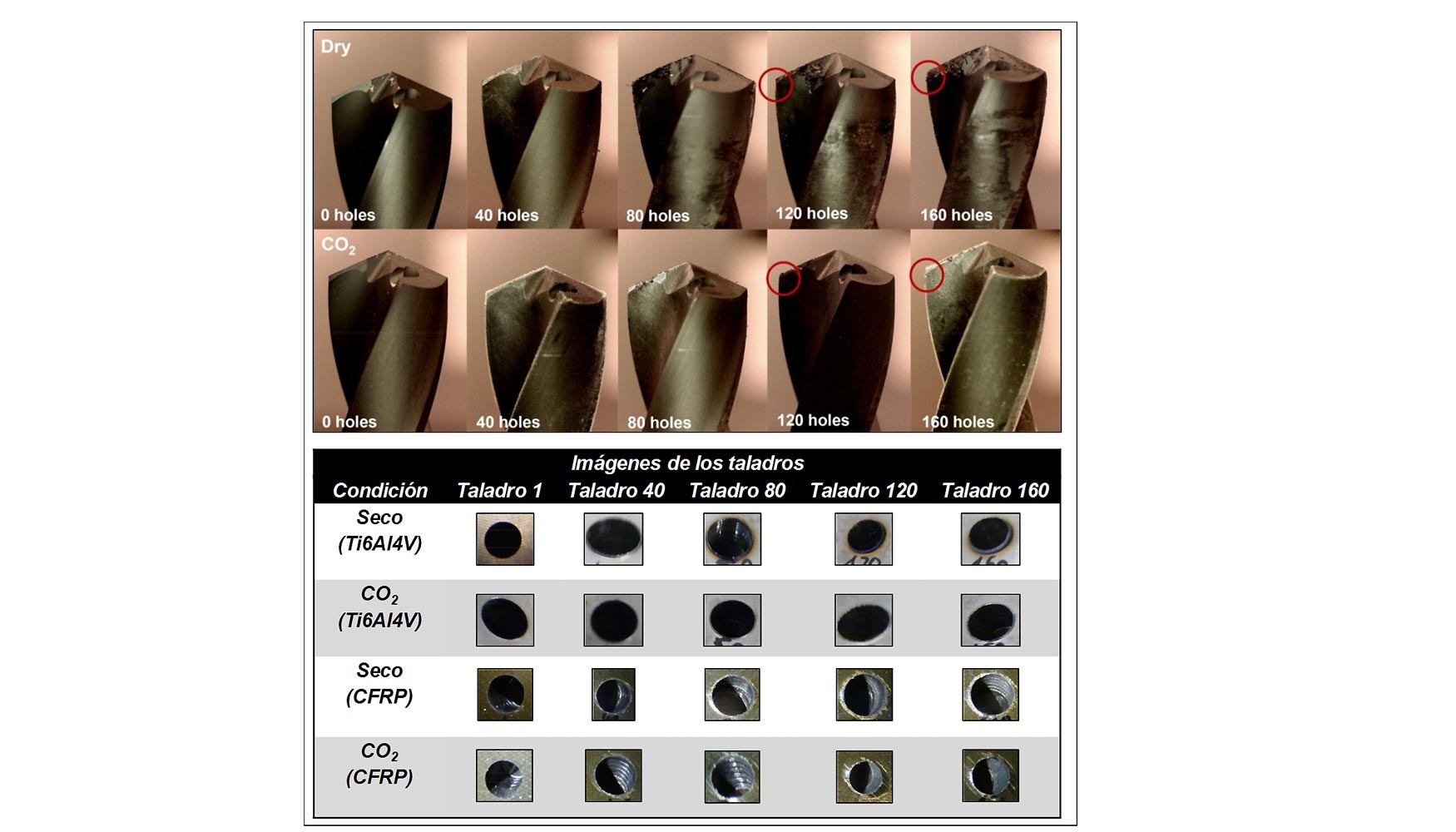
CryoMQL
Esta tecnología surge de la unión de las dos anteriores, es decir, se combina el poder refrigerante de la criogenia con la capacidad de lubricación de los sistemas MQL. Gracias a ella el abanico de materiales a los que se puede aplicar con un resultado exitoso aumenta hasta incluso ser factible de ser aplicado en materiales de difícil maquinabilidad como las aleaciones de base níquel.
Comercialmente, esta técnica se lleva ofreciendo en EE UU desde 2008. En ese año, la empresa americana CoolClean, dedicada a la limpieza de superficies con chorros de micropartículas de hielo seco, patenta una boquilla que es capaz de combinar el CO2 con las micropartículas de aceite por efecto Coanda con el fin de adaptar sus sistemas de limpieza al mecanizado [11]. Dado el éxito que tuvo, en 2011 patenta y empieza a comercializar su propia línea de CryoMQL denominada ‘Chill-Aire’ en la cual se ofrecen 3 gamas diferentes, como se puede observar en la figura 4.
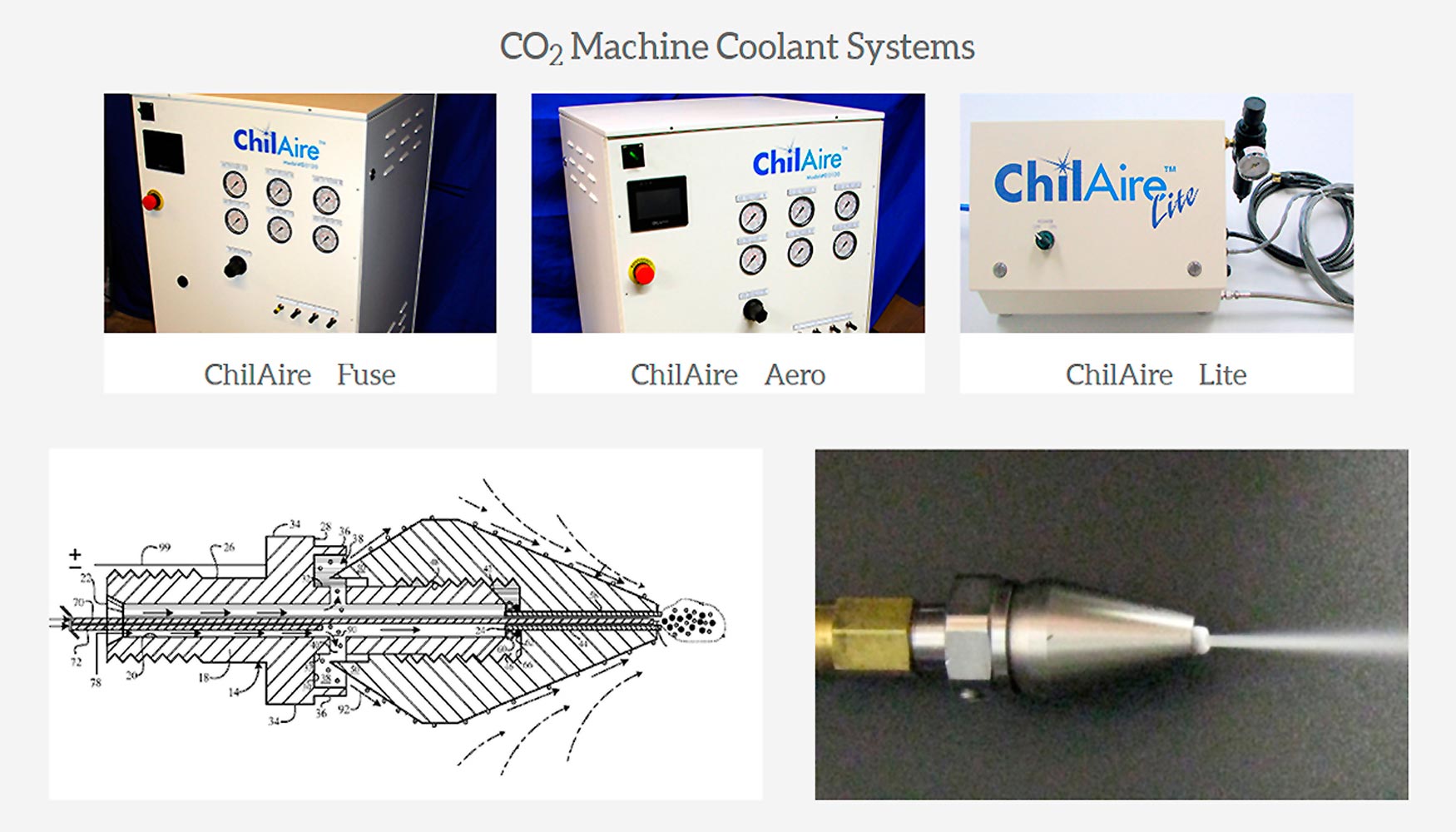
En cuanto al continente europeo se refiere, la empresa alemana Rother, también desde 2011 tiene su propia línea de inyección de ‘CryoMQL’, como se muestra en la figura 5. En este caso sus sistemas reciben el nombre comercial de ‘Aerosol Master’ y tienen la característica de poder alimentar varias tomas de ‘CryoMQL’ de forma totalmente independiente con un mismo sistema, es decir, en una misma máquina se pueden instalar varias boquillas para poder inyectar el aerosol criogenizado desde diferentes puntos a la zona de corte.
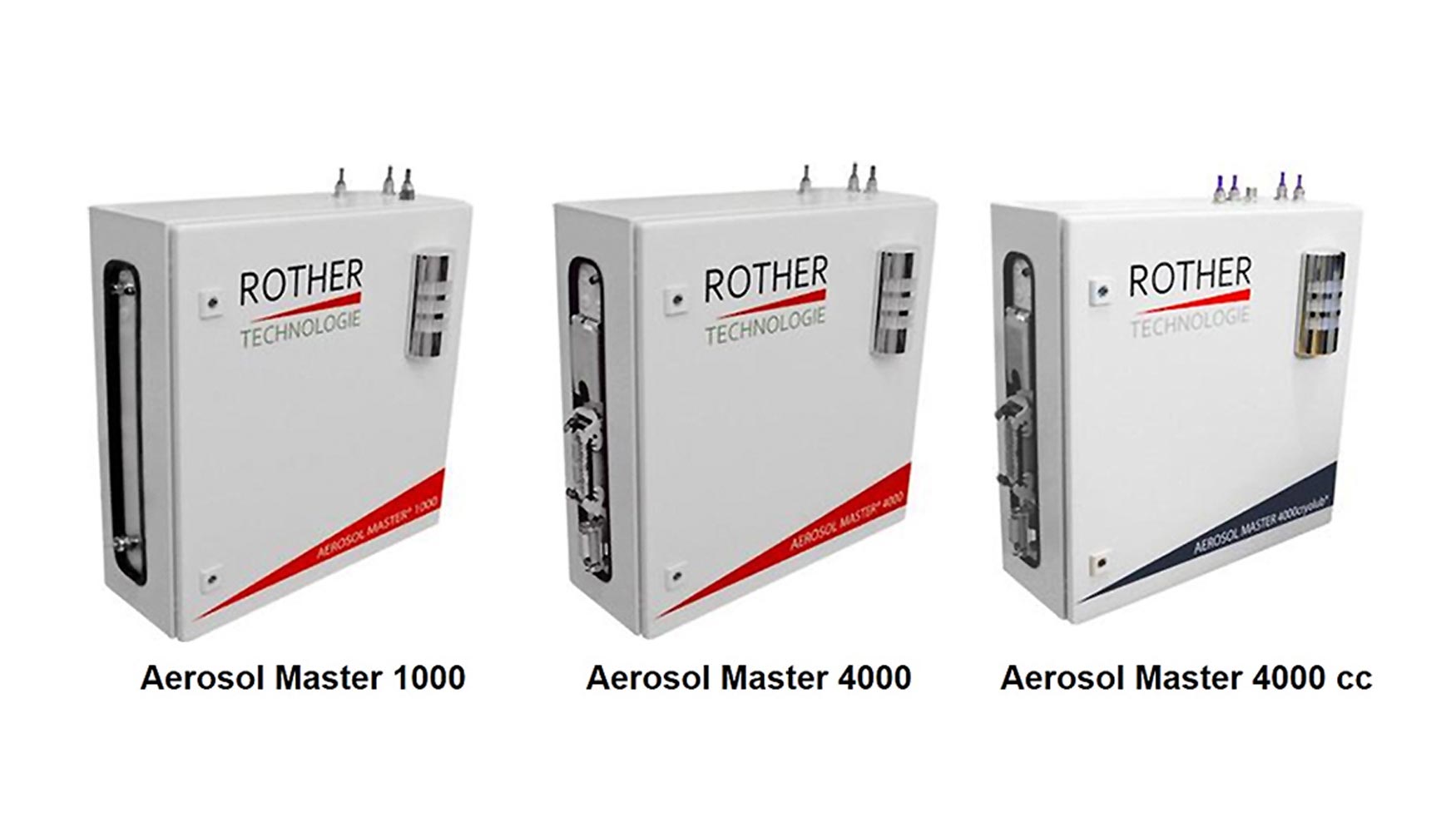
Finalmente, con el fin de poner al alcance de las empresas del entorno esta tecnología desde la UPV-EHU junto con Tecnalia se ha desarrollado un sistema ‘CryoMQL’, mostrado en la figura 6, en el que también se combina la tecnología criogénica con la pulverización de micropartículas de aceite de los sistemas MQL. El sistema desarrollado tiene la característica de ser totalmente ‘plug&play’, es decir, está diseñado de tal modo que puede ser instalado en cualquier máquina-herramienta ya existente de forma totalmente independiente o ser conectado al PLC de la máquina si así fuera necesario. Además, no sólo tiene la capacidad de utilizar ambas tecnologías de forma combinada sino también en modo ‘stand alone’ de forma independiente en función de los requerimientos del material a mecanizar.
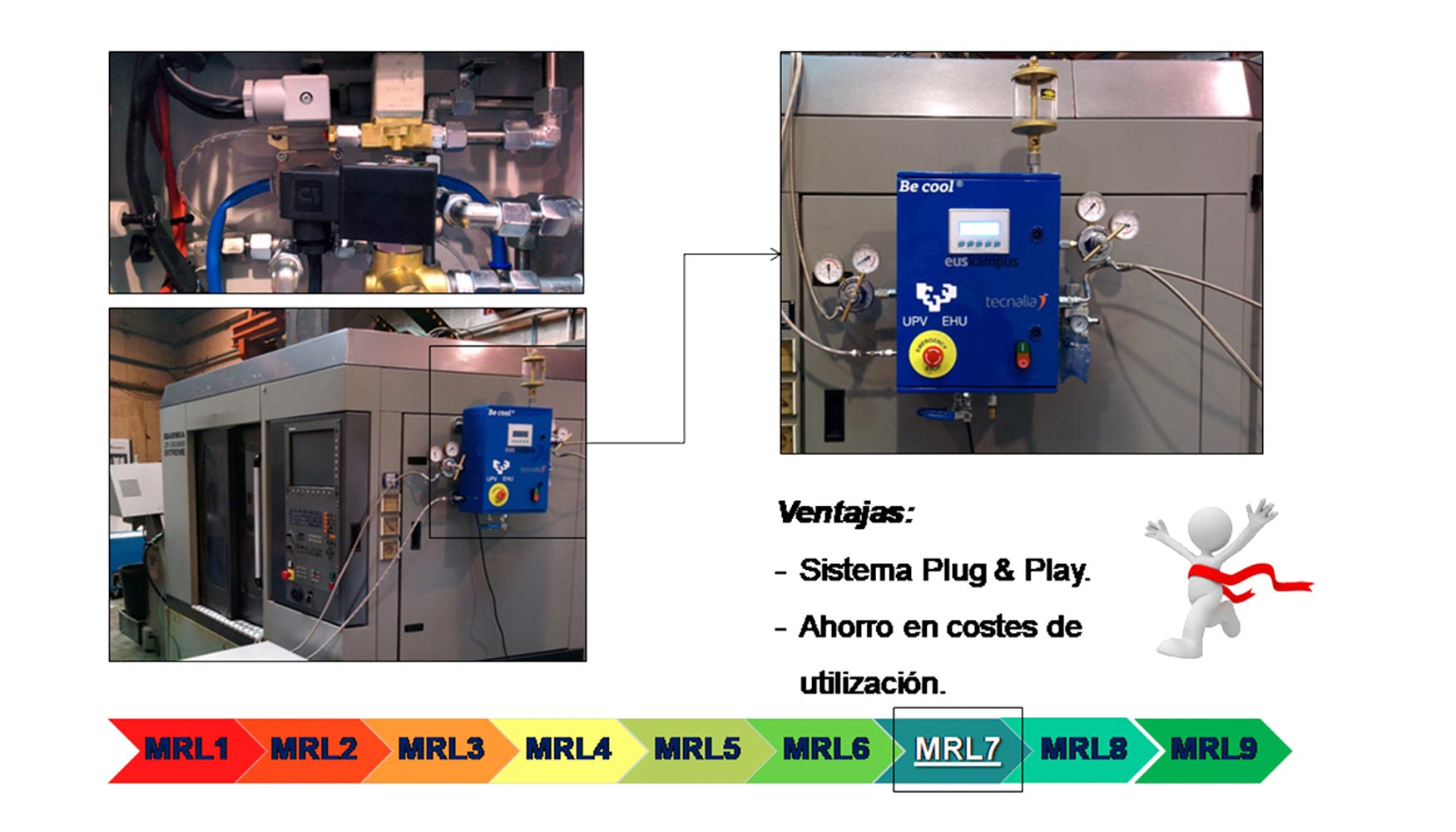
Por otra parte, el uso de esta tecnología durante el mecanizado de materiales de difícil maquinabilidad es una de las líneas de investigación que se está siguiendo por parte de la UPV-EHU desde hace más de 3 años. Generalmente los resultados obtenidos son bastante prometedores y apuntan a que esta tecnología, que aporta tanto refrigeración como lubricación, a medio plazo pueda llegar a ser una alternativa real al uso de taladrina. Sin embargo, a corto plazo antes de aplicarla se debe tener en cuenta el coste económico antes de aplicarlo a todo tipo de procesos y materiales. Actualmente esta tecnología está indicada principalmente para materiales difíciles de mecanizar en piezas de alto valor añadido.
Como ejemplo de su aplicación a este tipo de materiales cabe destacar el fresado de Inconel 718. Esta aleación de base níquel presenta unas excelentes propiedades mecánicas entre las que cabe destacar su alta resistencia a la fluencia en caliente y estabilidad química a altas temperaturas, por lo que forma parte de muchos componentes críticos de la turbomaquinaria aeronáutica, como por ejemplo los álabes de la turbina de alta presión, entre otros. En caso de ser mecanizado con ‘CryoMQL’ se obtienen rendimientos muy cercanos al uso de taladrina, como se muestra en la figura 7. Gracias a ello el mecanizado de estas aleaciones se puede realizar de una forma totalmente limpia a la vez que se sigue siendo económicamente viable.
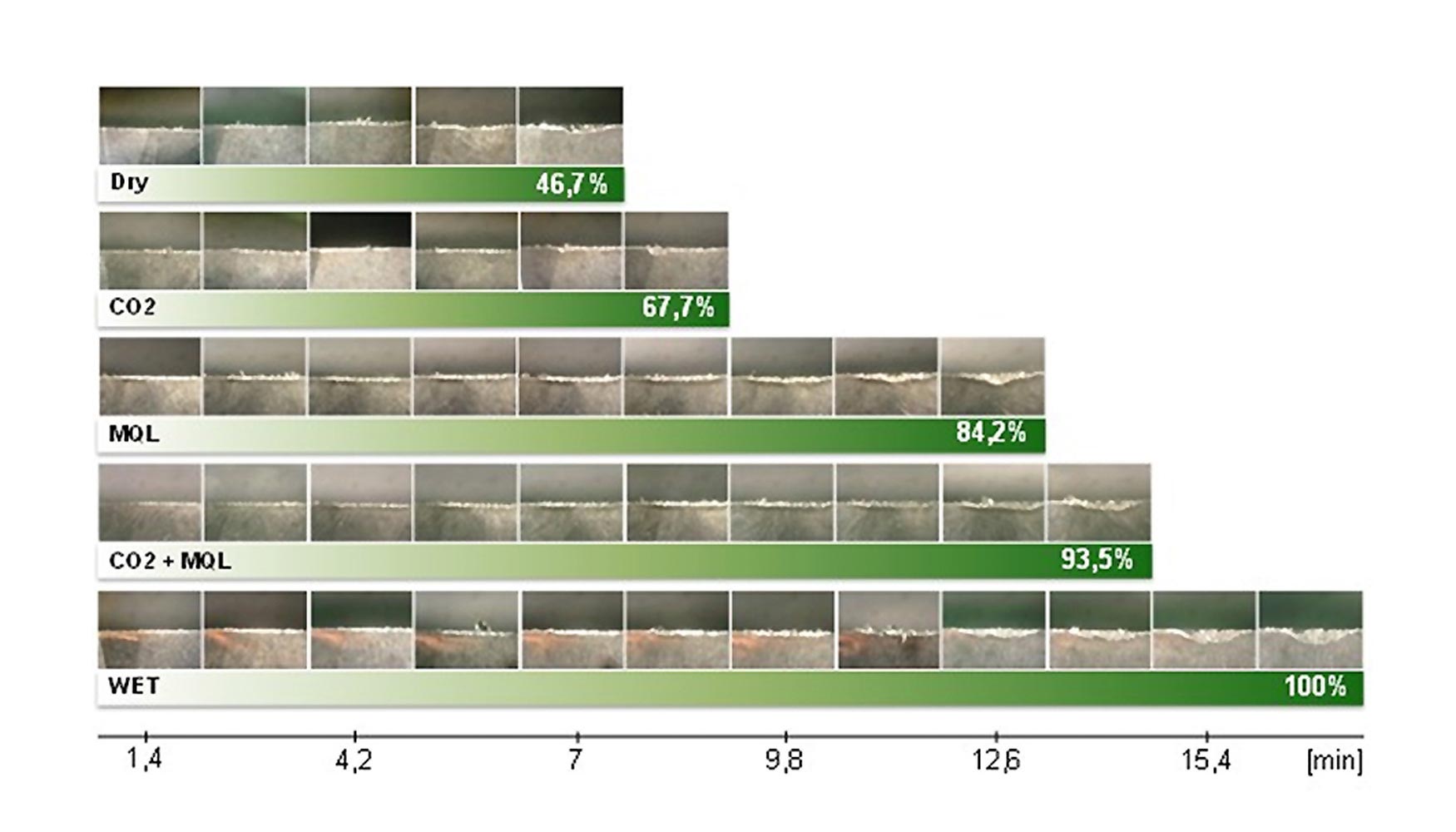
Conclusiones
En este artículo se han desglosado cada una de las alternativas ecológicamente más factibles para sustituir el habitual uso de taladrinas a corto-medio plazo durante el mecanizado de diferentes materiales. El avanzar hacia talleres más limpios y salubres a la vez que se es ecológica y económicamente más eficiente es el reto que hay que superar con el fin de llegar a un mecanizado de rendimiento ECO2.
Los sistemas MQL a día de hoy están teniendo una gran aceptación por parte del sector industrial con el fin de aplicarlo a un gran abanico de materiales utilizados en el día a día por las empresas del entorno. Sin embargo, con el fin de dar respuesta a materiales de difícil maquinabilidad, como las aleaciones de base níquel, la tecnología ‘CryoMQL’ es la más prometedora. Con esta técnica se consigue refrigerar a la vez que se lubrica simultáneamente la zona de corte pudiendo ser aplicada tanto de forma externa a la herramienta como interna a ésta.
No obstante, no todos los resultados han sido exitosos durante el desarrollo de la tecnología ‘CryoMQL’. Hay situaciones donde el gasto de los fluidos criogénicos no justifica las mejoras técnicas obtenidas. Por ello es de suma importancia identificar aquellas aplicaciones donde esta tecnología pueda llegar a tener su nicho de mercado.
Desde España a Argentina, la colaboración leal
A raíz del acuerdo de financiación firmado por el Instituto Nacional de Tecnología Industrial de Argentina (INTI) y la Unión Europea para la ejecución del proyecto ‘Mejora de las economías regionales y desarrollo local’, la Escuela Técnica Superior de Ingeniería de Bilbao ha acordado con dicha institución una alianza estratégica de colaboración para la transferencia e investigación en el campo de la fabricación mecánica, entre otros.
El convenio, firmado a finales de 2015, busca fortalecer las capacidades institucionales en función de la generación conjunta de información, tecnología y conocimiento técnico-científico así como la formación de recursos humanos con el fin de mejorar la calidad y la competitividad de las pymes de las zonas desfavorecidas del norte grande argentino.
A partir de este convenio se facilitará el intercambio de contenidos entre estudiantes, investigadores, profesores y técnicos en ámbitos de la ingeniería. Se colaborará en las áreas de asesoría, cooperación técnica y transferencia de tecnología a la vez que se cooperará en programas de formación de personal técnico e investigador.
El convenio significa una declaración de intenciones que tienen como fin promover relaciones de beneficio mutuo en materia de colaboración industrial y tecnológica, entre el INTI y la Escuela Técnica Superior de Ingeniería de Bilbao.
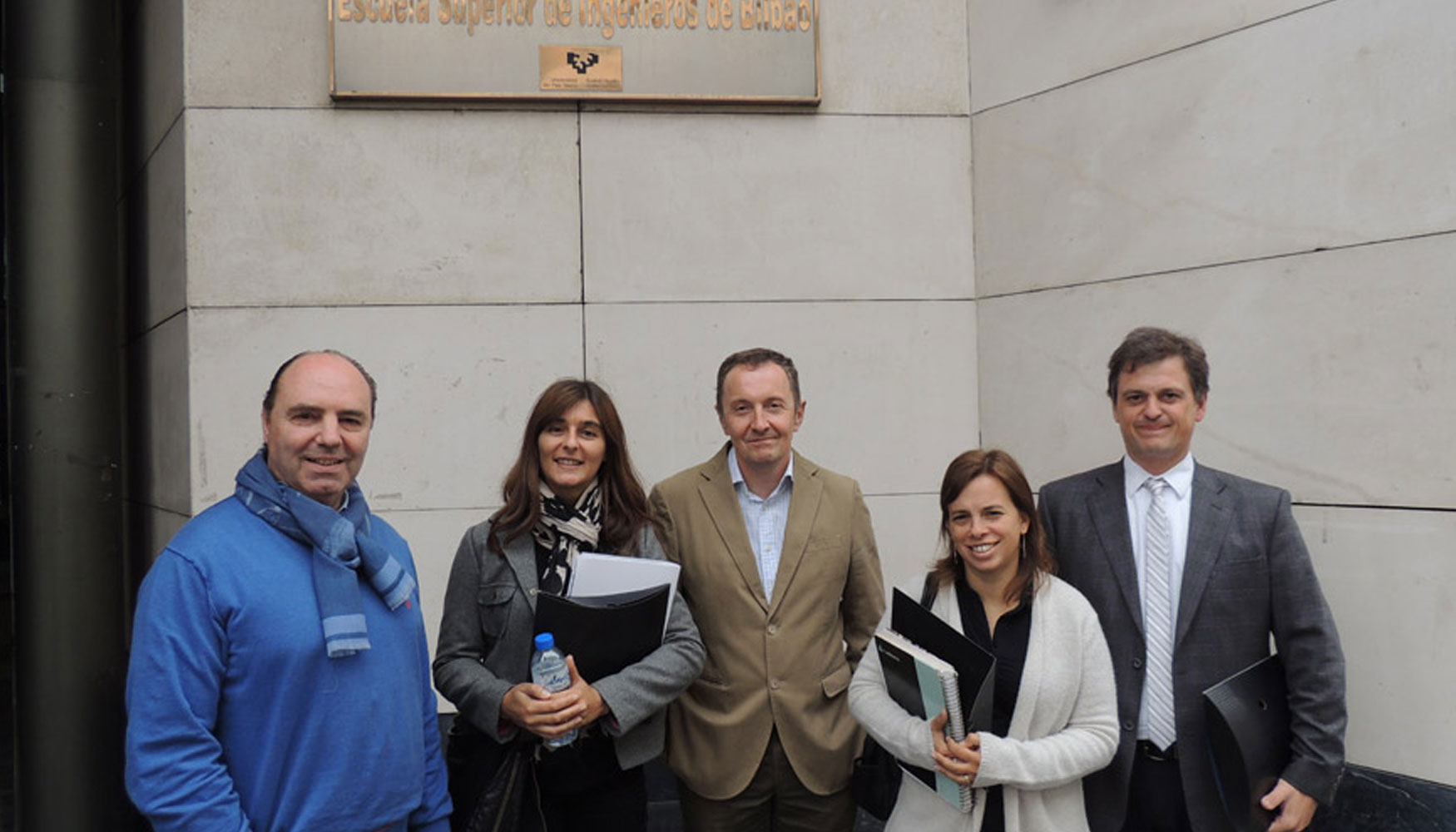
Referencias
[1] Klocke, F. & Eisenblatter, G. Dry Cutting CIRP Annals - Manufacturing Technology, 1997, 46, 519 – 526.
[2] Shokrani, A.; Dhokia, V. & Newman, S. Environmentally conscious machining of difficult-to-machine materials with regard to cutting fluids International Journal of Machine Tools and Manufacture, 2012, 57, 83-101.
[3] Lawal, S.; Choudhury, I. & Nukman, Y. Application of vegetable oil-based metalworking fluids in machining ferrous metals. A review International Journal of Machine Tools and Manufacture, 2012, 52, 1 – 12.
[4] Byrne, G.; Dornfeld, D. & Denkena, B. Advancing Cutting Technology CIRP Annals - Manufacturing Technology, 2003, 52, 483 – 507.
[5] Park, K.-H.; Olortegui-Yume, J.; Yoon, M.-C. & Kwon, P. A study on droplets and their distribution for minimum quantity lubrication (MQL) International Journal of Machine Tools and Manufacture, 2010, 50, 824 – 833.
[6] Cetin, M. H.; Ozcelik, B.; Kuram, E. & Demirbas, E. Evaluation of vegetable based cutting fluids with extreme pressure and cutting parameters in turning of AISI 304L by Taguchi method Journal of Cleaner Production, 2011, 19, 2049 – 2056.
[7] Pusavec, F.; Deshpande, A.; Yang, S.; M'Saoubi, R.; Kopac, J.; Jr., O. W. D. & Jawahir, I. Sustainable machining of high temperature Nickel alloy – Inconel 718: part 1 – predictive performance models Journal of Cleaner Production, 2014, 81, 255 – 269.
[8] Vega, S. & Walker, S. US 3,131,869. Coolant device for mahcine tools, 1964.
[9] Attanasio, A.; Gelfi, M.; Giardini, C. & Remino, C. Minimal quantity lubrication in turning: Effect on tool wear Wear, 2006, 260, 333 – 338.
[10] Khan, M.; Mithu, M. & Dhar, N. Effects of minimum quantity lubrication on turning AISI 9310 alloy steel using vegetable oil-based cutting fluid Journal of Materials Processing Technology, 2009, 209, 5573 – 5583.
[11] Jackson, D. P. US 7,389,941 B2. Fluid device and method for forming Cryogenic composite fluid spray, 2008.