Nueva embaladora Schubert para 'Pick Up!' la barra de galletas de Bahlsen
Cajas plegables de cartón garantizan mayor sostenibilidad
Ya sea para un refrigerio, un breve descanso o la sobremesa del domingo, con su amplia gama de barquillos, galletas y pasteles, el fabricante de galletas Bahlsen, con sede en Hannover, lleva más de 130 años proporcionando un placer de alta calidad. Para que los dulces lleguen intactos al consumidor, la empresa colabora desde hace años con el fabricante de máquinas embaladoras Schubert. La primavera pasada, Bahlsen renovó el embalaje de su barra de galletas 'Pick Up!' y amplió su maquinaria existente con dos empaquetadoras de barras de la empresa de Crailsheim. La gran ventaja: las etiquetas adhesivas aplicadas que envolvían varias barritas, formando así un paquete, fueron sustituidas por cajas de cartón con pliegues.
Disfrutar y apostar por la protección ambiental no son conceptos opuestos para Bahlsen. Por ello, además de su propio compromiso con la calidad y la innovación continua, el fabricante de galletas también ha priorizado el tema de la sostenibilidad en todas sus actividades. Por ejemplo, la empresa trabaja con socios cuidadosamente seleccionados en todo el mundo que ya actúan de forma responsable en el cultivo de materias primas como el cacao o el azúcar. Pero además de los ingredientes, el embalaje de los productos también desempeña un papel decisivo en la acción sostenible. Por eso, para 'Pick Up!', la popular galleta de chocolate, Bahlsen quería una nueva máquina embaladora que permitiera el cambio a embalajes más respetuosos con el medio ambiente.
Menos plástico y más cartón para el deleite con las galletas de chocolate
Hasta ahora, las barras 'Pick Up!' se embalaban en bolsas tubulares, se agrupaban y etiquetaban. Para producir de forma más sostenible, se pretendía sustituir este embalaje secundario en el futuro por cajas de cartón plegables. A tal efecto, Bahlsen buscaba una nueva solución de automatización que, sobre todo, protegiera las delicadas barras de galleta de daños y roturas durante el proceso de embalaje. Además, la empresa de confitería optó por películas más finas para las bolsas tubulares con el fin de lograr un ahorro de material al reducir la cantidad de película. Algo que también debía hacer posible la maquinaria actualizada. Aparte de ello, independientemente de las exigencias que debía satisfacer la embaladora propiamente dicha, era menester tener en cuenta las condiciones especiales de la planta de Bahlsen en cuanto a la ubicación de la máquina: el espacio para la producción era muy limitado debido a las numerosas columnas y los techos bajos, por lo que se requería un diseño compacto y estrecho de la línea.
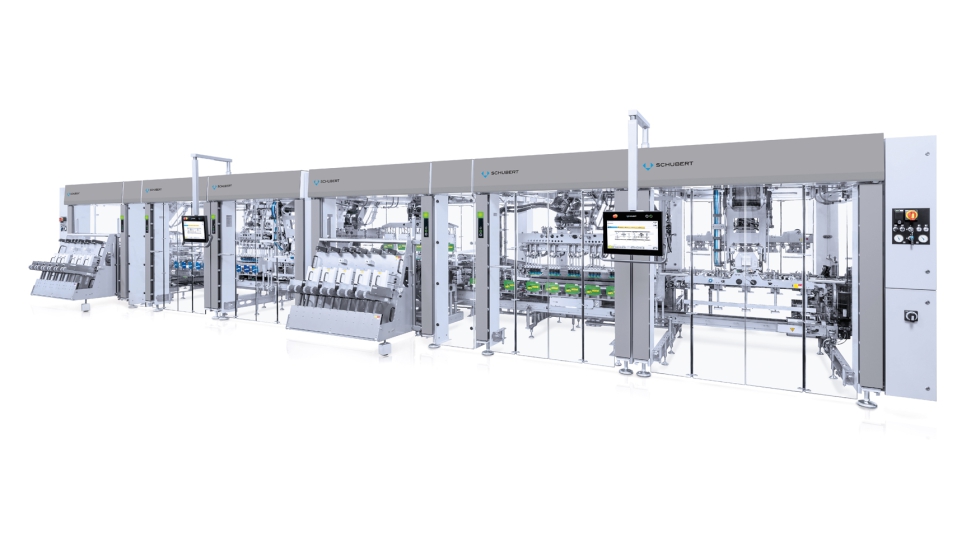
La nueva línea Schubert de Bahlsen impresiona especialmente por su gran flexibilidad y alto rendimiento.
Solución con dos empaquetadoras de barras flexibles totalmente automatizadas
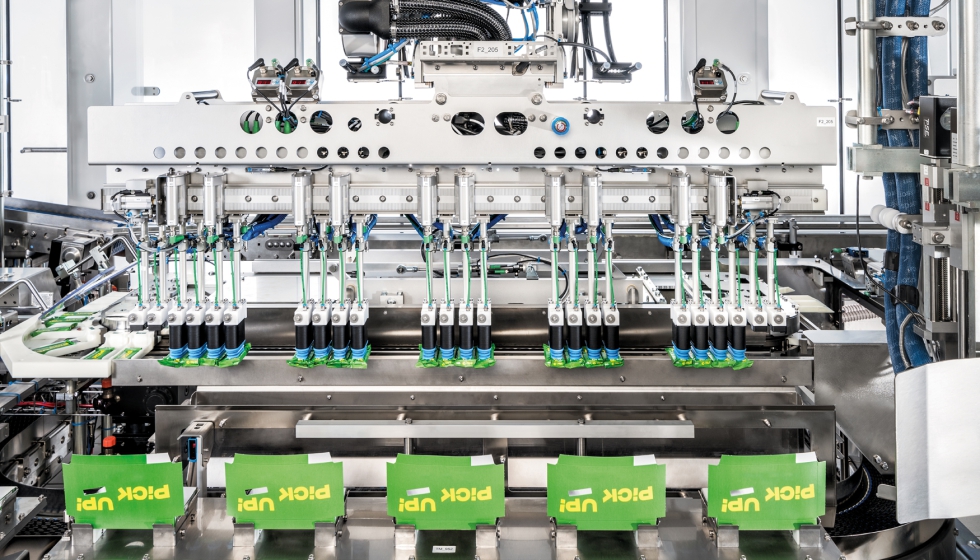
Bahlsen ahorra 112 toneladas de plástico al año con el nuevo embalaje para sus barras de galleta.
Procesos eficientes en la máquina: los robots trabajan codo con codo
Con la nueva solución de embalaje, las barras de galleta ya embaladas en bolsas tubulares se colocan en el embalaje secundario en las empaquetadoras de barras, que constan cada una de tres bastidores de máquina. En primer lugar, los pliegos planos se introducen en la línea a través de un depósito. Dependiendo del formato, un robot extrae hasta seis pliegos del depósito y los transfiere a otro robot que forma las cajas de cartón. Acto seguido, las cajas formadas se colocan en el robot de transporte Transmodul y se transportan a la estación de llenado. En paralelo, las barras 'Pick Up!' se introducen en el proceso a través de una cadena agrupadora y se preagrupan. A continuación, un robot recoge varias barras al mismo tiempo mediante una pinza de ventosas y las transfiere en un número de unidades predefinido en función del formato, al interior de las cajas, que en este punto tienen la tapa abierta. A continuación, el Transmodul traslada las cajas al último paso, el sellado. Allí, los paquetes se cierran con una prensadora de solapas en un proceso especialmente diseñado para cajas bajas.
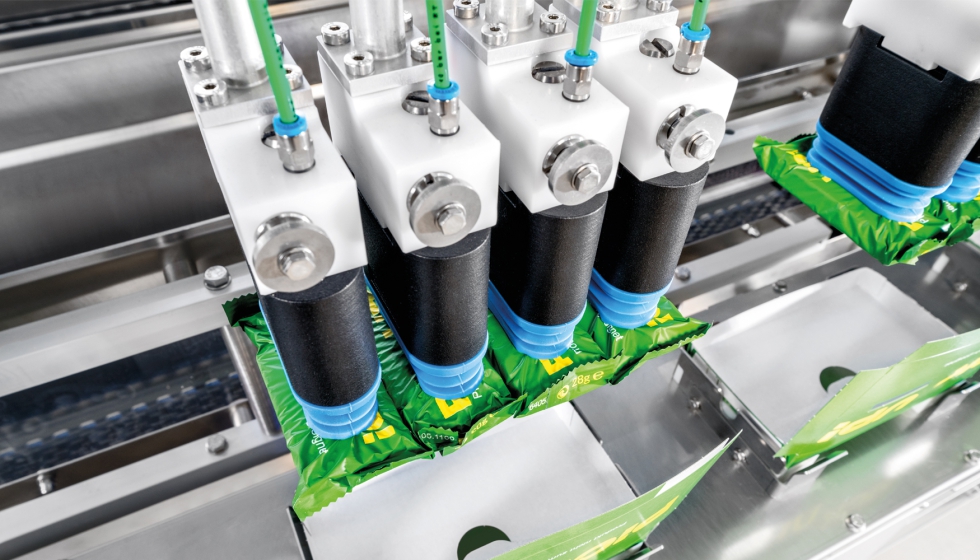
Doble efecto: el nuevo proceso es al mismo tiempo sostenible y económico
El cambio a cartón, películas más finas y una nueva línea no sólo mejora la sostenibilidad, sino que también resulta muy económico para Bahlsen. La solución de alto rendimiento puede procesar hasta 850 barritas por minuto. Gracias a la gran precisión de trabajo de los robots, que colocan el producto con total exactitud dentro de los embalajes, fue posible diseñar las nuevas cajas de embalaje con un tamaño y una altura mínimos y, por tanto, sin mucho espacio vacío. Además, el fabricante de galletas puede utilizar diversos formatos para sus especialidades: son posibles embalajes envolventes con ocho disposiciones de producto diferentes. Un cambio de formato mayor será únicamente necesario cuando se utilicen embalajes con bases de otro tamaño y se puede llevar a cabo en tan sólo 20 minutos.
Bahlsen está más que satisfecho con la nueva línea. La amplia gama de formatos y alturas de cajas y la capacidad de las máquinas robotizadas para procesar un exceso de capacidad proveniente del proceso previo de hasta el diez por ciento hacen que la solución no sólo impresione por su sostenibilidad, sino también por su flexibilidad y eficiencia. La empresa valora igualmente el hecho de que Schubert haya diseñado una máquina de tan alto rendimiento para un lugar de emplazamiento tan limitado. Lo que ratifica también Ulrike Arnold, directora de proyectos de Schubert: “El diseño de la línea ha sido complicado, había muchas columnas y techos bajos que restringían el espacio, y sin embargo el resultado es una línea que satisface las altas exigencias".
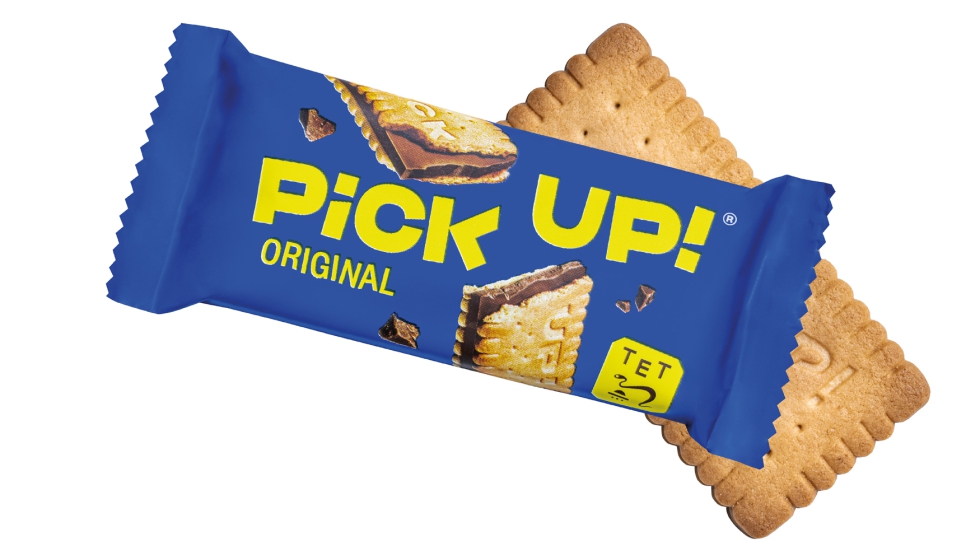
La barra de galleta 'Pick Up!' queda protegida de todo daño, gracias a la cuidadosa manipulación de los robots durante el proceso de embalaje.
Hechos y cifras
- 2 embaladoras de barras con una capacidad de hasta 850 productos por minuto
- 8 formatos diferentes
- Cambio mayor de formato en sólo 20 minutos
- Eficiencia del 98 por ciento
- Ahorro de 112 toneladas de plástico al año
- Aplicación de Transmodul