La fábrica de VW en Braunschweig invierte en las máquinas
grandes de 32.000 kN de Battenfeld para el panel de
instrumentos del modelo Multivan
Nuevas dimensiones en la técnica de plásticos de VW
Redacción PU15/10/2002
Los transformadores de plásticos de la fábrica de VW en Braunschweig (Alemania) han dado un enorme salto con la adquisición de su más nueva máquina para el moldeo por inyección. Esta planta, equipada hasta ahora con unas 110 inyectoras entre 500 y 8.000 kN, ha adquirido una nueva máquina para el moldeo por inyección de la serie HM de Battenfeld con una fuerza de cierre de 32.000 kN. La máquina fabricará paneles de instrumentos.
Dentro de la planta de Braunschweig (Alemania), que produce componentes para automóviles, la transformación de plásticos representa una de las siete áreas de negocio. El pasado año, este campo — que emplea a 650 personas — alcanzó una facturación de unos 160 millones de marcos. "Aún considerando el elevado porcentaje de plásticos de un automóvil, nosotros sólo somos un pequeño segmento en la totalidad del grupo, pero producimos una gama de productos de gran especialización", explica Ralph Sundermeier, director del Área de Negocio de Plásticos desde principios de año. Algunos de los productos incluidos en su gama son piezas para asientos y revestimientos, y, en mayor medida, paneles de instrumentos, piezas para el motor, la tracción y el exterior del automóvil. La división produce componentes para los modelos propios de VW —Golf, Polo, Passat, Multivan y Caravelle—, y para otras marcas del grupo como Audi, Seat y Skoda.
Panel de instrumentos de lujo
La fábrica ha conseguido en los últimos meses numerosos pedidos y cuenta con un crecimiento continuado en el área de negocio Técnica de Plásticos. Así, el número de empleados pasará de los actuales 650 a 700 en 2004. Entre los pedidos destaca el panel de instrumentos para la configuración de lujo de la nueva generación de grandes limusinas ‘Multivan T5’, que saldrá al mercado en primavera de 2003 y que se fabricará en exclusiva en esta planta de Braunschweig. Aquí se produce el cuerpo central del panel de instrumentos, que se forma mediante la soldadura de tres componentes: la parte superior, la inferior y el canal de aire. Este panel de instrumentos se acaba de completar en la misma fábrica con partes individuales como la guantera, extractores, conductos de aire, tapas, etc. hasta formar un conjunto completo. Esto se lleva a la fábrica de Multivans en Hannover, donde se completan hasta estar listos para instalar en el automóvil, en función de las especificidades concretas de los salpicaderos de los clientes.
Robustos y fáciles de manejar
La fábrica de Braunschweig tuvo que hacerse con una nueva inyectora para la producción del gran cuerpo central de los paneles de instrumentos. Si hasta ahora contaba con un parque de maquinaria que incluía inyectoras de 500 a 8.000 kN de fuerza de cierre, en la actualidad se ha incorporado otra de gran tamaño, (32.000 kN). Entre los pocos suministradores de máquinas para el moldeo por inyección de estas dimensiones, Volkswagen se decidió por Battenfeld Spritzgiesstechnik, de Meinerzhagen. Para R. Sundermeier, la disponibilidad, la precisión y el servicio “son las cuestiones que los empleados más experimentados de nuestra empresa señalan como relevantes — y añade — Para nosotros también era importante la robustez y el fácil manejo, y creemos que lograremos todo ello con la adquisición del módulo de tres platos de Battenfeld".
Máquina de 32.000 kN con equipamiento universal
Los tres moldes de inyección para los tres componentes básicos de un panel de instrumentos realizado con PP y EPDM ya están en funcionamiento en la línea de Battenfeld, instalada en VW desde otoño de 2001. Battenfeld realizó el proyecto de toda la instalación, incluido el robot, pinzas o agarres de las piezas, el sistema de transporte de piezas con estación de enfriamiento, sistema de amarre electromagnético y otros equipos periféricos. La inyectora hidráulica, a excepción de la plastificación cuyo accionamiento es eléctrico, es un modelo HM 32000/19000 equipado con un robot lineal de la empresa Shuling, que extrae las piezas del molde y, en el caso de las piezas superiores del panel de instrumentos, las transporta mediante un sistema en el que van colgando, hasta la zona de enfriamiento. La complejidad de esta pieza destaca sobre todo por la delgadez de unas paredes que son también muy largas. Con el fin de poder superar unos canales de flujo de esta longitud, VW utiliza la técnica de inyección en cascada.
La máxima apertura para la instalación del molde se aumentó en 600 mm para poder instalar el molde para la pieza más grande: la parte superior del panel de instrumentos. La inyectora HM está equipada con un dispositivo de tracción de las columnas que facilita todo lo posible la instalación del molde de 40 toneladas. Otro elemento que facilita todo el proceso es el amarre electromagnético QMC de Stäubli. "Con este sistema somos más flexibles que con amarres de cambio rápido, porque también lo podemos utilizar para moldes más pequeños" explica R. Sundermeier
La máxima apertura para la instalación del molde se aumentó en 600 mm para poder instalar el molde para la pieza más grande: la parte superior del panel de instrumentos. La inyectora HM está equipada con un dispositivo de tracción de las columnas que facilita todo lo posible la instalación del molde de 40 toneladas. Otro elemento que facilita todo el proceso es el amarre electromagnético QMC de Stäubli. "Con este sistema somos más flexibles que con amarres de cambio rápido, porque también lo podemos utilizar para moldes más pequeños" explica R. Sundermeier
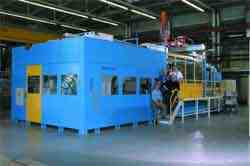
La instalación completa proyectada por Battenfeld
Empresas o entidades relacionadas
Stäubli Española, S.A.U.