Aplica los conceptos del modelo de gestión 'Lean Industry'
ADR renueva las líneas de producción
El grupo ADR AXLES renueva las líneas de producción dentro de su estrategia de optimización de los flujos y procesos productivos, así como su integración de la logística.
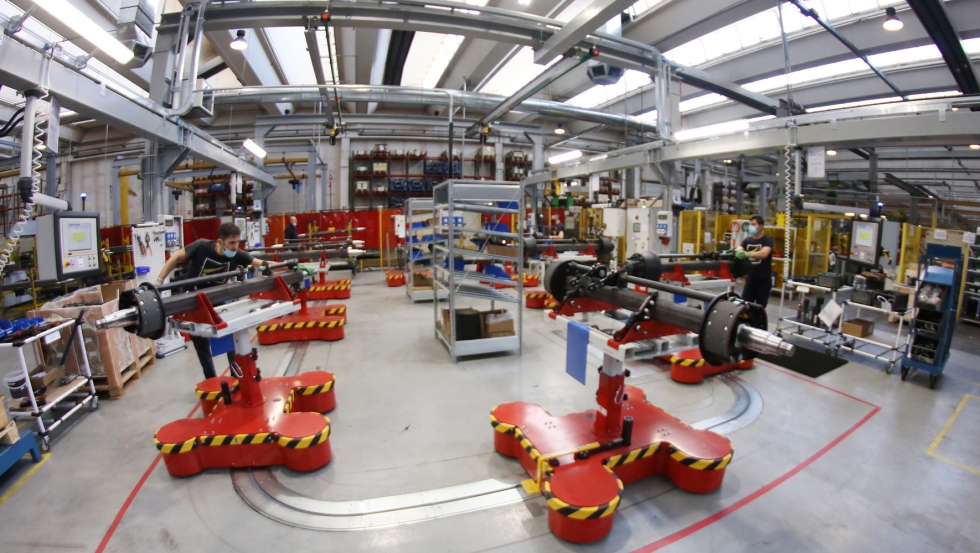
En 2020 renovó los almacenes y ahora llega el momento de las líneas de producción. El grupo ADR AXLES, especialista en la fabricación de ejes, suspensiones y sistemas de frenado para vehículos agrícolas e industriales, continúa a un ritmo vertiginoso su estrategia de optimización de los flujos y procesos productivos, así como su integración de la logística, con miras a una mayor eficacia productiva y de calidad.
'Lean Industry', que de forma no literal se puede traducir como 'producción ágil', es un término acuñado en 1988 por el ingeniero estadounidense John Krafcik para connotar aquellos estándares de fabricación introducidos por Toyota en sus fábricas entre 1950 y 1975, destinados a conseguir grandes volúmenes de producción sin penalizar la calidad del producto y garantizando la máxima eficacia posible en la fabricación y la logística.
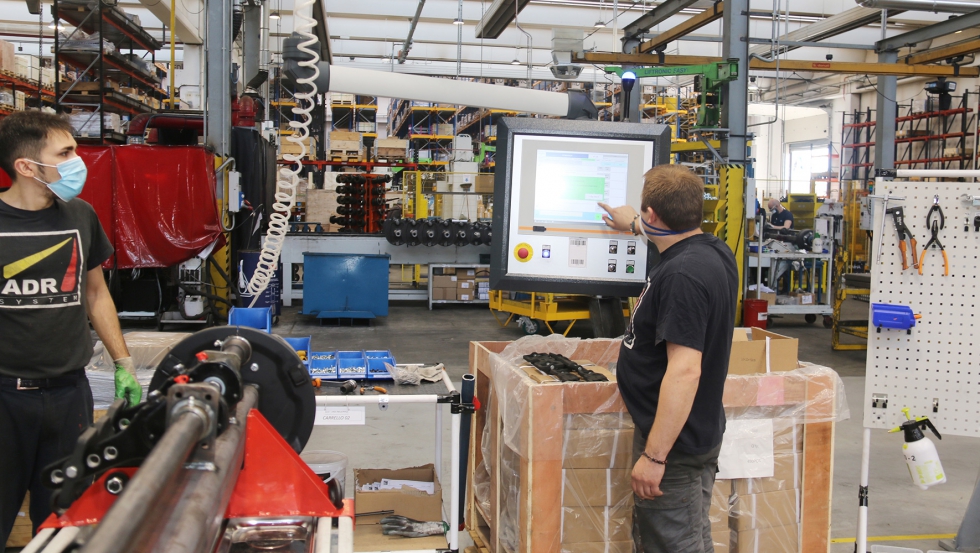
Una mayor integración de los procesos productivos agiliza la entrega de pedidos.
Calidad y eficiencia
Hoy en día los conceptos inspiradores de 'Lean Industry' se han extendido a todos los sectores industriales que operan en términos de grandes volúmenes y en los últimos tiempos también han sido adoptados por el grupo ADR AXLES, uno de los fabricantes de ejes agrícolas más importantes del mundo.
Precisamente, con vistas a agilizar la producción, el año pasado intervino sobre sus almacenes de Uboldo, en las afueras de Milán (Italia), para integrarlos de manera directa en el ciclo de la producción. Reestructuró por completo la circulación interna de materiales y racionalizó cada área de trabajo. Este último ha sido reorganizado centrándose en cuatro elementos básicos: la integración de los procesos productivos con un software de gestión ampliado, la mejora de la logística interna para reducir el tiempo de tránsito del material, la automatización de los controles de calidad en línea y sobre todo, la reevaluación del personal colocando la figura del operador en el centro de los procesos de la planta con el fin de enfatizar su valor y profesionalidad. Por tanto, ya no es un mero ejecutor de órdenes sino un protagonista activo del ciclo productivo.
Integración informática
En la base del nuevo sistema de producción ADR AXLES existe una integración informática profunda entre las distintas divisiones de la compañía, un software de gestión que en la práctica envuelve y conecta personas, máquinas, proveedores, clientes y a cada individuo enlazándolo con el grupo ADR, asegurándose de que cada pedido se traduzca de inmediato y sin la necesidad de pasos en papel o instrucciones de trabajo a las que cada departamento debe responder.
En el momento en el que todos los detalles necesarios para hacer un simple producto están disponibles, comienza el ensamblaje final, que a su vez está impulsado por listas de verificación intuitivas y precisas que aseguran el cumplimiento de los estándares de calidad establecidos por ADR para cada uno de sus productos.
Puntos clave de la renovación
- Cadencia piezas/hora. La reorganización de las operaciones de montaje permite aumentar la capacidad de producción en un 30/40% en comparación con la producción actual.
-
Ergonomía de montaje. Ya no existe el inconveniente de una línea de montaje fija frente al operador, por lo que puede realizar más fácilmente las operaciones de montaje y control de la pieza final.
-
Calidad. Al tener una interfaz hombre/máquina muy avanzada, cada operador es guiado paso a paso en la secuencia de ensamblaje. De esta manera, se acortan los tiempos de aprendizaje de los nuevos operadores, aumenta la productividad y, sobre todo, limita cualquier riesgo de errores durante el montaje, gracias al software que, mostrando listas de control muy intuitivas, simplifica enormemente el trabajo de cada operario.
-
Lean Industry. Desde hace varios años, ADR ha presionado al sector de producción para que evolucione desde una perspectiva de industria ajustada para mejorar todos los ámbitos. Esta nueva línea de montaje es prueba de ello porque nació precisamente sobre los conceptos básicos del pensamiento Lean, situándolos en la realidad ADR. Esta nueva línea será el embrión de una profunda renovación que afectará a los principales polos de producción de todo el grupo, dando también a cada operador la oportunidad de permanecer en un entorno de trabajo mucho más cómodo y humano.
-
Factory 4.0. La nueva instalación ha sido diseñada para integrarse completamente con el software de gestión ERP utilizado en la empresa. Esta conexión hombre / máquina / software trae consigo muchas ventajas. Al interconectar completamente la línea con el sistema de gestión, se crea una extensión directa y natural entre los diferentes departamentos de la empresa. De hecho, la línea recibe todas las órdenes de trabajo directamente dentro de su sistema de gestión y realiza de forma autónoma las demandas del material necesario para la autoalimentación, garantizando la continuidad y eliminando la gestión del papel. También es posible monitorear en tiempo real su eficiencia y cada orden en el punto de ejecución.
-
Integración logística. La nueva línea no es un proyecto autónomo, sino que ha sido integrada como hardware y software a los sistemas de gestión y logística, en este caso en contacto directo con dos operarios del 'tren logístico', que es la columna vertebral para distribuir el material y alimentar los puestos de trabajo. De esta forma, se cumple también con uno de los principales retos internos, que es la seguridad, ya que al ser la línea totalmente autoalimentada por dicho tren se eliminan los desplazamientos diarios en carretilla elevadora.
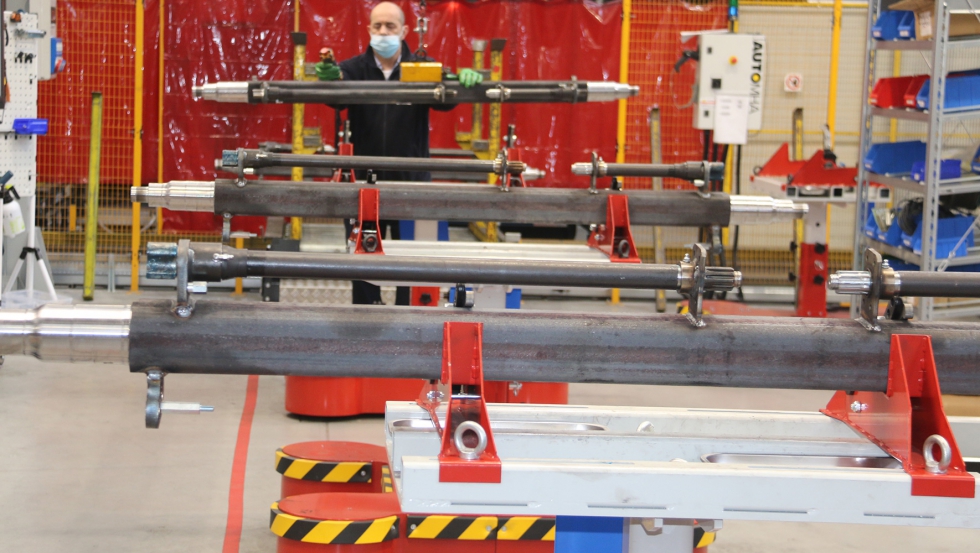
Cada trabajador gana protagonismo con la nueva filosofía de trabajo aplicada.
Aumento de la capacidad de producción
El nuevo escenario, antecedente de una renovación productiva que afectará a todas las plantas del Grupo en el futuro, además de permitir mayor flexibilidad en la producción sin necesidad de reorganizar la línea cada vez, asegura una mayor calidad del producto ya que utiliza sistemas de control automatizados que ayudan a los operarios evitando que cometan errores y juegan a favor de la eficiencia al aumentar la capacidad de producción entre un 30% y un 40% en comparación con un sistema de producción tradicional. Los operarios trabajan más fácilmente y ven crecer sus habilidades profesionales.