El desarrollo de nuevas tecnologías que permitan el superacabado de estas superficies, mediante procesos automatizados, es una constante en las empresas del sector
Pulido de superficies funcionales. Donde el acabado importa
Jokin Pérez, Ander Arroyo, Mikel González, Adrián Rodríguez, del Centro de Fabricación Avanzada Aeronáutica. Universidad del País Vasco (UPV/EHU)
31/05/2024Actualmente, muchos de estos procesos de acabado se realizan a mano por operarios cualificados. El impulso en el desarrollo de nuevas tecnologías de acabado que permitan el superacabado de estas superficies funcionales mediante procesos automatizados es una constante en todas las empresas del sector. El reto de trabajar geometrías complejas y materiales de difícil maquinabilidad únicamente puede ser afrontado utilizando las más novedosas tecnologías de acabado. En esta línea se trabaja en el CFAA de la UPV/EHU.
Células de acabado, la clave para el pulido de piezas obtenidas mediante fabricación aditiva
En la búsqueda continua de eficiencia y mejora en los procesos industriales, la automatización se muestra como una solución clave en diversos sectores. Un ejemplo destacado es la creciente utilización de células robotizadas para tareas de mecanizado y acabado, destacando su flexibilidad y costos horarios reducidos en comparación con las máquinas-herramienta convencionales. Esta tendencia se ha establecido hace ya muchos años en la industria automotriz, donde la agilización de procesos y la obtención de acabados uniformes son imperativos.
El sector aeronáutico, en constante expansión, se encuentra en una fase de gran crecimiento. Según un informe de Airbus [1], se prevé un aumento considerable en el tráfico aéreo y la demanda de aviones comerciales en los próximos 20 años. Ante estos desafíos, se estima la necesidad de incorporar 39,000 nuevas aeronaves para hacer frente al crecimiento del Producto Interno Bruto (PIB), la clase media y la demanda a nivel global. La urgencia de retirar aeronaves más antiguas para reducir las emisiones de CO2 prioriza la eficiencia, los avances tecnológicos y la adopción de combustibles sostenibles.
En el ámbito de la industria aeroespacial, el uso de la fabricación aditiva ha experimentado un crecimiento significativo, alcanzando un valor estimado entre 1,76 y 2,66 mil millones de dólares en 2021, con un pronóstico de crecimiento anual entre el 19,4% y el 20,23% en los próximos años [2]. Este crecimiento refleja los avances en el diseño y fabricación de nuevas familias de motores y sus componentes, con el propósito de reducir las emisiones de gases de efecto invernadero a medio plazo [3].
En la última década, la fabricación aditiva emerge como una tecnología clave en diversas industrias, incluyendo la aeronáutica. La capacidad de construir componentes capa por capa a partir de diseños digitales complejos ha impulsado la producción de elementos geométricamente eficientes, reduciendo el desperdicio de material y ofreciendo flexibilidad en la creación de diseños innovadores. Esta evolución ha permitido la producción de geometrías complejas que antes eran inalcanzables mediante métodos sustractivos tradicionales. Entre las técnicas de fabricación aditiva de metales, la fusión láser en lecho de polvo (L-PBF) ha recibido atención significativa por sus destacables capacidades en comparación con otros procesos de fabricación aditiva [4,5]. Aunque aún presenta desafíos en casos como la selección de materiales o el control de procesos, esta técnica es relevante por su habilidad para producir piezas metálicas con una excelente integridad estructural, una alta precisión dimensional y una calidad superficial superior.
Esta precisión mejorada se atribuye en parte a la utilización de partículas de polvo más finas y un grosor de capa más delgado. En consecuencia, la L-PBF ha despertado el interés de la industria aeroespacial, especialmente para la fabricación de geometrías complejas como las que se encuentran en las terminaciones de componentes de turbomaquinaria, y se espera que mantenga un crecimiento constante en los próximos años [6].
La combinación de tecnologías de fabricación aditiva, como el L-PBF, junto con el uso de materiales avanzados como el Inconel 718, abre nuevas perspectivas en la fabricación eficiente y de alta calidad de componentes para turbinas aeroespaciales [7]. Estas turbinas operan en entornos extremos, soportando temperaturas que superan los 1000°C y demandando un alto rendimiento mecánico. El Inconel 718, conocido por su excepcional resistencia a altas temperaturas y corrosión, es una opción frecuente en esta aplicación [8]. Esta coordinación entre tecnología y material permite obtener componentes optimizados geométricamente y con características mecánicas excepcionales a altas temperaturas. Sin embargo, la implementación de piezas fabricadas con tecnologías aditivas en el sector aeronáutico es un proceso complejo debido a las estrictas normativas y estándares de seguridad. La fabricación aditiva presenta una serie de limitaciones desde el punto de vista de características mecánicas, tolerancias dimensionales y acabado superficial, comprometiendo el rendimiento de las piezas fabricadas por esta tecnología. Por este motivo, por un lado, se aplican tratamientos térmicos como el HIP (Hot Isostatic Pressing) o ciclos de precipitación, para incrementar la dureza y resistencia del material hasta valores óptimos [9,10]. Por otro lado, las tolerancias dimensionales requeridas se logran mediante procesos posteriores de mecanizado, aprovechando los avances científicos recientes en este campo. Sin embargo, el acabado superficial sigue siendo un desafío, tanto a la hora de caracterizar defectos como a la hora de eliminarlos con tecnologías abrasivas. Un ejemplo típico es el de la figura 1, donde se aprecian las marcas superficiales en la misma dirección que la capa de polvo fundido.
![Figura 1. Marcas superficiales originadas a partir del proceso de fabricación aditiva. Prototipo de carcasa de turbina tipo fabricada en el CFAA [11]... Figura 1. Marcas superficiales originadas a partir del proceso de fabricación aditiva. Prototipo de carcasa de turbina tipo fabricada en el CFAA [11]...](https://img.interempresas.net/fotos/4698925.jpeg)
Este tipo de defecto es común en el proceso de fabricación L-PBF y está directamente vinculado a la deformación térmica. Específicamente, en las áreas que experimentan sobrecalentamiento, pueden producirse curvaturas de hasta 100 μm. Si esta deformación excede el grosor de la capa de polvo, pueden surgir crestas en las capas posteriores, como se ilustra en la figura 1. Por consiguiente, las piezas fabricadas mediante fabricación aditiva requieren un proceso de acabado para alcanzar la rugosidad superficial deseada.
Las nuevas tecnologías en pulido abrasivo con cepillo flexible se consolida como una técnica prometedora para mejorar el acabado superficial de componentes aeroespaciales fabricados mediante fabricación aditiva. Este enfoque ofrece eficiencia y versatilidad en la mejora de las superficies, con el potencial de abordar las marcas superficiales y la rugosidad inherentes a la fabricación aditiva. La selección cuidadosa de parámetros de proceso y materiales es fundamental para garantizar resultados óptimos y cumplir con los rigurosos estándares de calidad de la industria aeroespacial. Además, el cepillado abrasivo se destaca como una de las operaciones de acabado más comúnmente utilizadas en varios procesos de fabricación. Estas herramientas de cepillado flexibles se integran sin problemas en fresadoras, tornos o rectificadoras, ofreciendo una solución rentable sin la necesidad de invertir en maquinaria nueva [12].
Tecnologías de cepillado. Un extenso mar de posibilidades
En el mundo de las tecnologías de cepillado, se abre un abanico de posibilidades para diversas aplicaciones industriales y comerciales. Desde la precisión del acabado hasta la eliminación eficiente de materiales no deseados, los cepillos abrasivos son fundamentales en muchos sectores. Desde el Centro de Fabricación Avanzada Aeronáutica (CFAA), se han llevado a cabo una serie de estudios exhaustivos utilizando diferentes cepillos abrasivos bajo diversas condiciones. Estos estudios han permitido identificar las mejores características de cada cepillo, así como sus condiciones óptimas de uso. Además, se han analizado aspectos clave como la durabilidad de los cepillos, la eficiencia en la eliminación de material, la capacidad de mantener la calidad de la superficie tratada, y la influencia de variables como la velocidad de giro, la velocidad de avance y las temperaturas máximas que alcanzan los cepillos durante las operaciones. También se ha evaluado el impacto de estos factores en la productividad y los costos operativos, proporcionando una visión integral sobre cómo maximizar la eficiencia y eficacia de las operaciones de cepillado en distintos contextos industriales.
El cepillo radial Scotch-Brite de 3M, es un ejemplo que destaca dentro del campo del cepillado por su innovación. Con un diseño de filamentos rectos dispuestos radialmente alrededor de un núcleo central, este cepillo ofrece un acabado preciso en diversas de superficies. Tiene una combinación de nylon flexible y óxido de aluminio abrasivo que garantiza efectividad en la eliminación de material, convirtiéndolo en una herramienta esencial para aplicaciones industriales.
Generalmente, se utiliza para diferentes tareas de acabado, desde el pulido hasta la eliminación de rebabas y la limpieza de superficies. Su diseño por componentes y su capacidad para adaptarse a diferentes formas y tamaños de piezas lo hacen ideal para aplicaciones en industrias como la automotriz, aeroespacial, metalúrgica y más.
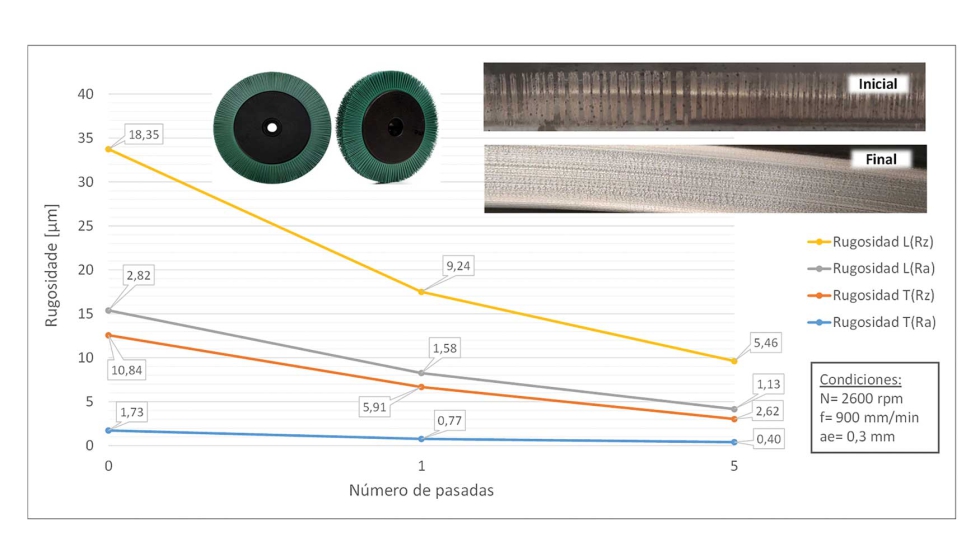
Una de las ventajas clave de este cepillo es su larga vida útil y su resistencia al desgaste, convirtiéndolo en una opción muy beneficiosa para cualquier operación de acabado. Además, su diseño está pensado de tal forma que ofrece seguridad en entornos sensibles donde se requiere un control preciso de la contaminación. Con una única pasada donde la profundidad de corte no llega a 1mm, los resultados presentados en la figura 2, demuestran una gran capacidad de eliminación de marcas.
Siguiendo la línea, el cepillo de abanico de núcleo, de Pferd, ofrece otra solución eficiente y versátil para una variedad de aplicaciones de acabado y pulido. Con su diseño de abanico y materiales abrasivos de alta calidad como el corindón o el grano cerámico CO-COOL, este cepillo es ideal para tareas de desbaste, pulido y acabado, proporcionando un acabado uniforme y preciso en una amplia gama de materiales.
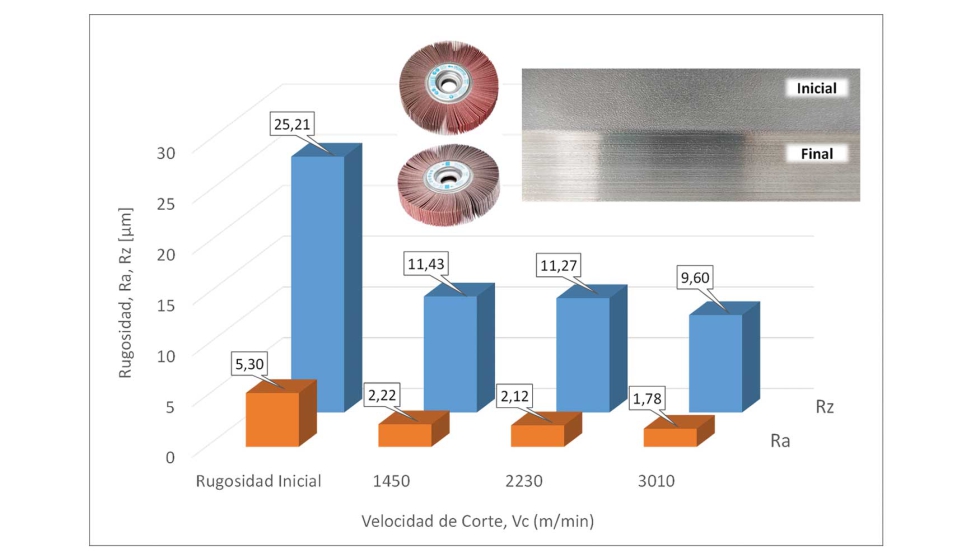
El diseño de abanico del cepillo permite una mayor flexibilidad y adaptabilidad a diferentes formas y contornos de piezas de trabajo, convirtiéndolo en una herramienta muy práctica para superficies curvas o irregulares. Además, el núcleo central proporciona estabilidad y resistencia estructural al cepillo, garantizando un rendimiento consistente y duradero. Con todo esto, su uso en industrias como la metalúrgica, automotriz y aeroespacial está más que justificada.
En las pruebas realizadas en el CFAA, con esta clase de cepillos en abanico se ha visto que para aplicaciones de desbaste la profundidad de corte es un parámetro esencial, ya que a medida que se incrementa este valor su diseño curvo permite ampliar el contacto con la superficie abrasiva, aumentando notablemente su capacidad de arranque de material. Sin embargo, esta acción también genera un incremento significativo en la temperatura durante el proceso de desbaste. Este incremento es un factor a considerar especialmente en piezas de chapa de poco espesor, dónde el calor residual puede acumularse en la zona de corte, aumentando el riesgo de producir quemados en la pieza a la vez que se reduce la vida útil del cepillo. Además, los desbastes con granos abrasivos de mayor tamaño generan marcas superficiales que requieren de pasadas adicionales de acabado con menor tamaño de grano.
Para tareas de trabajo en superficies diversas dentro del ámbito de la aeronáutica, el cepillo nylon circular, de JAZ, ofrece una solución práctica y efectiva. Gracias a su composición de nylon flexible, este cepillo proporciona propiedades abrasivas suaves pero efectivas, ideales para eliminar residuos, óxido y pintura sin dañar la superficie posterior. Gracias a su diseño circular y su tamaño compacto, se muestra adecuado para trabajos de mantenimiento y reparación de componentes aeronáuticos, garantizando la integridad superficial y funcional de las piezas.
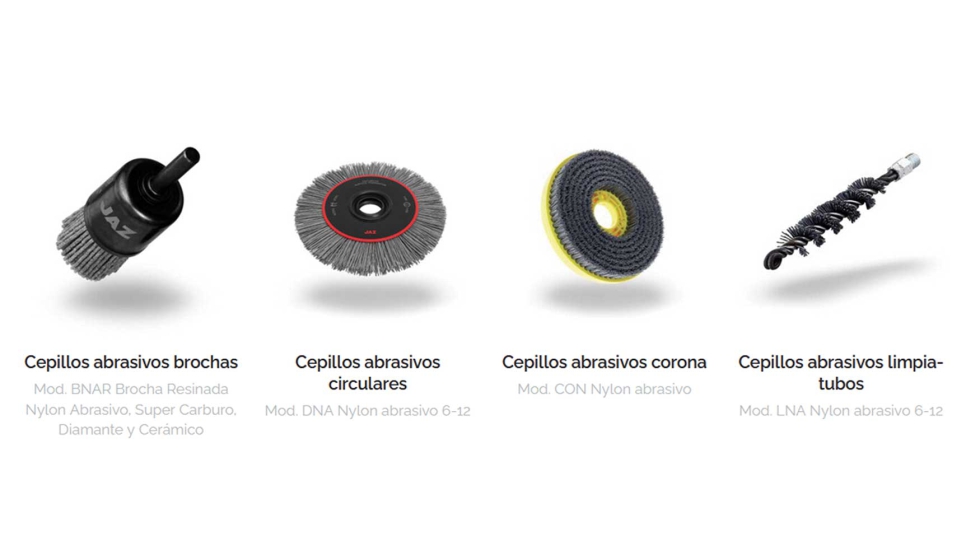
La forma del cepillo permite un fácil montaje en herramientas rotativas estándar, como taladros o amoladoras, facilitando su uso y manipulación durante el trabajo. Además, ofrece un equilibrio entre tamaños ajustados y alto rendimiento que lo hace ideal para zonas difíciles de alcanzar o espacios estrechos.
Los cepillos de lija SATINEX – Beartex, de Norton, son herramientas abrasivas innovadoras que ofrecen un acabado suave y uniforme en una variedad de materiales y superficies. Su diseño único, con láminas de lija entre las cerdas del cepillo, permite un lijado simultáneo al cepillado de la superficie, eliminando imperfecciones, rebabas y óxido en una sola pasada. Se usan materiales abrasivos de óxido de aluminio o carburo de silicio, ya que su durabilidad y capacidad de corte garantizan un rendimiento estable y eficiente en aplicaciones duraderas. Son herramientas ideales para una amplia variedad de sectores industriales, desde metalurgia hasta automoción y construcción, con un diseño funcional de fácil manipulación.
El cepillo de disco de decapar, de 3M, es una herramienta versátil y altamente efectiva para procesos de pulido y cepillado de una variedad de superficies y materiales. Este disco Clean & Strip Scotch-Brite está diseñado específicamente para limpiar soldaduras, retirar óxido y eliminar las primeras capas de la superficie, dejando una rugosidad mejorada y una preparación óptima para trabajos posteriores de acabado.
El mineral de carburo de silicio utilizado en la fabricación de este disco proporciona una abrasión eficiente y duradera, lo que garantiza resultados de pulido y cepillado de alta calidad en una amplia gama de superficies. Su grano ofrece un desbaste rápido y eficiente en una variedad de materiales y superficies, lo que lo hace ideal para aplicaciones que requieren un alto nivel de precisión y acabado.
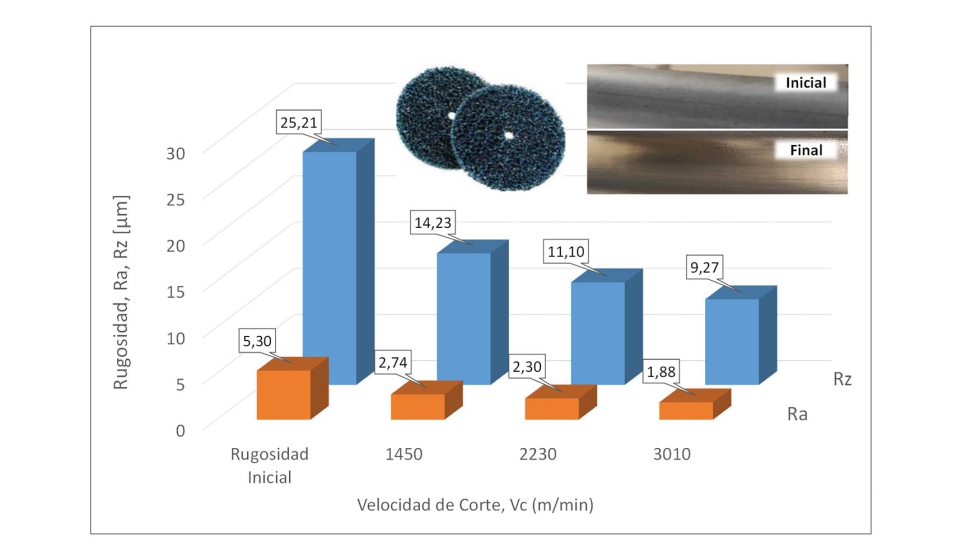
La acción agresiva de este cepillo, permite eliminar imperfecciones de la superficie de manera eficiente, dejándolas limpias y listas para su posterior tratamiento, como se puede apreciar en la figura 4. Su diseño resistente a dobleces y a las manchas asegura un rendimiento constante y prolongado, incluso en condiciones exigentes.
Por otro lado, otra de las ventajas destacadas de este disco es su prolongada vida útil, lo que implica que puede soportar un uso duradero sin perder su eficacia. Dado que su desgaste se compensa mediante la reducción del diámetro, el disco sigue siendo completamente funcional, manteniendo su capacidad de trabajo de manera consistente a lo largo del tiempo. Esta característica no solo contribuye a reducir los costos de reemplazo, sino que también aumenta la productividad al minimizar los tiempos de inactividad asociados con el cambio frecuente de herramientas.
Finalmente, dejando de lado los cepillos de disco, los cepillos de ataque frontal Xebec permiten un acabado general suavizado de toda la pieza. Su capacidad de arranque de material puede regularse a partir de las velocidades de giro y de avance, y son capaces incluso de eliminar pequeñas rebabas residuales, realizando una segunda pasada alternando el sentido de giro para asegurar una adecuada orientación de las fibras.
![Figura 6: Resultados del uso del cepillo de ataque frontal Xebec en probetas de Inconel 718 proveniente de fabricación aditiva[11]... Figura 6: Resultados del uso del cepillo de ataque frontal Xebec en probetas de Inconel 718 proveniente de fabricación aditiva[11]...](https://img.interempresas.net/fotos/4698914.jpeg)
Este cepillo ofrece una eficiencia abrasiva excepcional gracias a su material cerámico de alta calidad. Su alta resistencia al desgaste garantiza una larga vida útil, reduciendo los costos operativos. En caso de desgaste, los filamentos internos pueden extraerse para recuperar la longitud deseada. Además, proporciona resultados consistentemente de alta calidad en una variedad de aplicaciones y superficies, siendo una solución versátil y eficaz para el desbarbado y acabado.
En resumen, los diversos cepillos abrasivos analizados, demuestran una notable eficiencia y versatilidad en aplicaciones industriales. Estos cepillos, fabricados con materiales abrasivos de alta calidad, garantizan una larga vida útil y con ello reducen los costos operativos. Su capacidad para adaptarse a diferentes formas y tamaños de piezas, así como su eficacia en tareas de desbaste, pulido y acabado, los convierten en herramientas esenciales en el sector aeronáutico, entre otros sectores. Además, ofrecen resultados de alta calidad y seguridad en entornos sensibles, asegurando un rendimiento constante y duradero incluso en condiciones exigentes.
Bandas de lijado/pulido. Una solución de nota
Los procesos de lijado son esenciales para eliminar imperfecciones, suavizar irregularidades y preparar las superficies para etapas posteriores como el pintado, el recubrimiento o el pulido. Además, se utilizan para ajustar dimensiones y mejorar tanto la apariencia estética como la calidad superficial de las piezas. En un sector tan importante como la industria aeroespacial, el lijado es crucial para garantizar que los productos cumplan con los estándares de calidad y rendimiento requeridos. Sin embargo, conseguir la precisión necesaria para lograr esos objetivos resulta todo un reto.
En la actualidad, muchas empresas realizan estas tareas de forma manual, lo que expone a los operarios a grandes cantidades de polvo industrial, elevado ruido y continuas vibraciones mecánicas, factores que pueden tener un impacto nocivo en su salud. Adicionalmente, la falta de precisión y repetitividad en las operaciones manuales a menudo resulta en un rechazo frecuente de las piezas, principalmente debido a desviaciones en la forma geométrica. Por este motivo, se busca la automatización de estos procesos mediante células robotizadas, lo que aporta una mayor flexibilidad, consistencia y velocidad en la producción. Para que esta automatización sea adecuada, es necesario tener un control exhaustivo de los parámetros de operación. Si la estrategia de control es lo suficientemente buena, se puede llegar al nivel de conseguir superficies perfectamente pulidas. El desarrollo y la implementación de este tipo de tecnologías de control es un tema de investigación actual en el CFAA.
A la hora de seleccionar una herramienta idónea para realizar el trabajo, existe un amplio abanico de posibilidades. Estas van desde lijadoras orbitales y lijadoras de tambor, hasta lijadoras de banda, e incluso lijas manuales como la solución más rudimentaria. El uso de lijas de banda representa una excelente solución no rotativa además de común para este propósito. En particular, son ampliamente utilizadas debido a su capacidad para trabajar grandes superficies y su eficiencia en la eliminación rápida de material. Los modelos actuales de lijas de banda son capaces de asegurar un acabado uniforme a largo de la vida del producto y evitar el quemado de las superficies, empleando granos cerámicos de orientación electrostática para formar picos afilados, en comparación con los abrasivos convencionales que se desgastan, se pelan, se vitrifican y, por lo tanto, se desechan considerablemente más rápido.
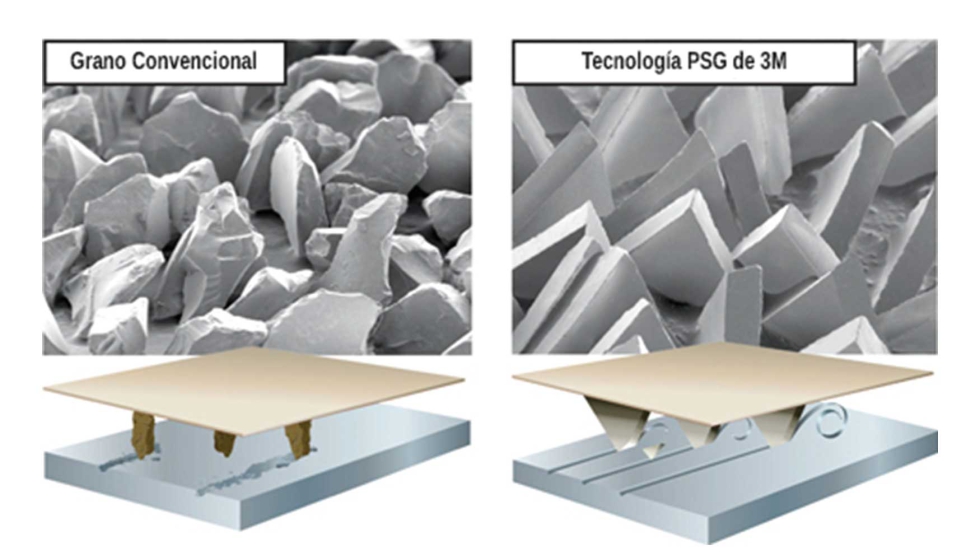
Una solución innovadora y muy utilizada consiste en combinar uno o varios brazos robóticos junto con lijas o cintas de banda. De esta manera, cabe la posibilidad de que el brazo robótico lleve la herramienta y trabaje sobre la pieza fijada en una mesa, o que el robot acerque la pieza a una lija de banda dispuesta en una estación fija. Para que estos movimientos sean posibles, es necesario programar previamente las trayectorias que debe realizar el brazo robótico. En este contexto, SprutCAM es un software capaz de generar y simular las trayectorias que necesite seguir el brazo robótico para garantizar el contacto adecuado entre la herramienta y la pieza. Además, permite personalizar de forma sencilla una gran cantidad de parámetros, como la orientación en el contacto o los enlaces entre operaciones, mediante una interfaz clara e intuitiva.
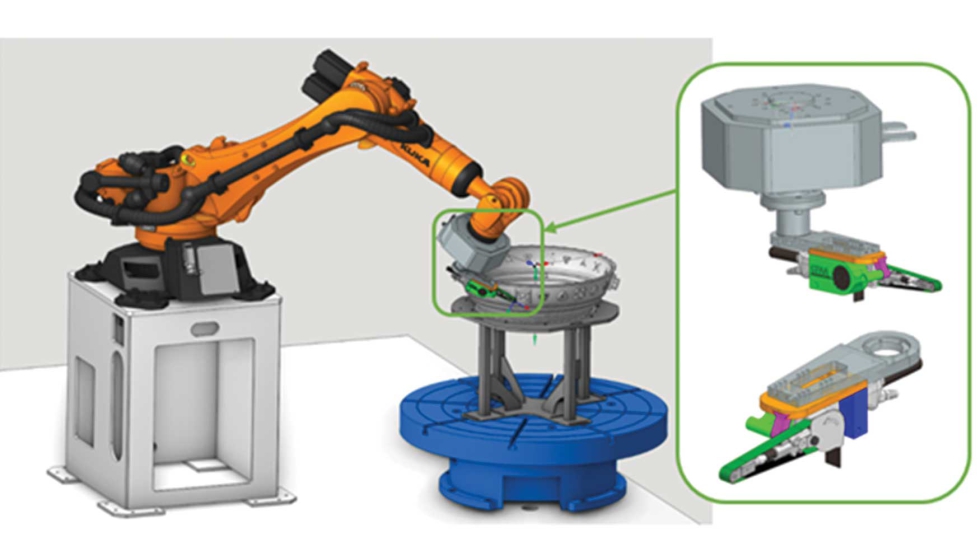
El modelo mostrado en la imagen es parte de un proyecto de investigación enfocado en la automatización de las operaciones de lijado, que se encuentra en curso en el Centro de Fabricación Aeronáutica Avanzada (CFAA). Esta solución consiste en la fijación de una lijadora de banda neumática en la muñeca de un brazo robótico Kuka KR 240 R2500 prime. Utilizando las trayectorias generadas en CAM, el brazo puede acercarse a la pieza situada en la mesa rotativa y realizar el proceso de acabado en su superficie. Este proyecto, al igual que muchos otros desarrollados en el CFAA, subraya la relevancia del trabajo del centro y lo posiciona como un líder en innovaciones tecnológicas.
Métodos alternativos de acabado. Cruzando los límites de lo convencional
Además de los procesos de acabado superficial convencionales que se suelen encontrar en la industria del entorno, existe una constante investigación en la búsqueda de procesos que sean capaces de mejorar la rugosidad de las superficies de las piezas mejorando además sus propiedades mecánicas, como por ejemplo comportamiento frente a fatiga. Algunos de esos procesos alternativos pueden son los siguientes:
Cavitation Water Jet Peening Technology (Granallado mediante tecnología de chorro de agua en cavitación). Este proceso se realiza utilizando un chorro de agua a gran velocidad. El chorro de agua que sale de la boquilla se encuentra a unos 20-30 MPa de presión, esto genera que adquiera una alta velocidad suficiente para que el agua entre en cavitación. Las burbujas generadas en la cavitación son las que realizan el proceso. Estas burbujas al chocar con la superficie generan zonas localizadas de alta presión que pueden obtener hasta 1000 MPa de presión en la superficie.
Este proceso presenta numerosas ventajas además del acabado superficial de la pieza. Por ejemplo, induce mayores tensiones de compresión y más profundas que el granallado convencional, además sin producir zonas afectadas térmicamente. Por otra parte, también se trata de un proceso que no contamina ya que al utilizar únicamente agua no se producen residuos en el proceso y resulta un proceso más eficiente económicamente que otras técnicas de granallado.
Chemically Assisted Surface Enhancement (C.A.S.E. acabado isotrópico). Esta técnica se ha desarrollado para aquellas superficies que requieren un excelente comportamiento ante fatiga de flexión y contacto, así como a altas cargas de trabajo. El primer paso consiste en aplicar al componente un proceso de granallado. Este proceso genera una capa de tensiones de compresión que eliminan cualquier tensión de tracción residual haciendo las superficies más resistentes al inicio y propagación de las grietas. Posteriormente se realiza un segundo granallado a menor intensidad y reduciendo el tamaño del abrasivo, este segundo proceso reduce la rugosidad e incrementa las tensiones compresivas en la superficie. Por último, se lleva a cabo un proceso de pulido, utilizando pellets cerámicos no abrasivos. Se termina obteniendo superficies tipo espejo. Las ventajas que este proceso ocasiona son la reducción de rugosidad y tensiones en la superficie de las piezas, se obtiene un acabado espejo.
En conclusión, se puede decir que existe un gran interés en el desarrollo de nuevas tecnologías para la mejora superficial de las piezas. Se está intentando desarrollar nuevas tecnologías o realizar combinaciones de estas que mejoren los procesos existentes. Siendo el principal objetivo eliminar rugosidades excesivas e inducir tensiones residuales compresivas que mejoren las propiedades mecánicas y la resistencia fatiga.
Aliados tecnológicos. Imposible sin ellos
Como ya se ha presentado en anteriores ocasiones, entre los socios tecnológicos que colaboran en la línea de acabado y pulido del CFAA, destacan 5 grandes grupos: desarrolladores e integradores de robots; proveedores y fabricantes de herramientas y soluciones; proveedores de husillos y accesorios; otros accesorios y soluciones tecnológicas y tecnologías software.
Uno de los casos de éxito en lo referente a colaboración tecnológica en los últimos meses ha sido MECDATA. Se trata de una empresa en constante desarrollo de aplicaciones enfocadas a dar solución a necesidades de generación de trayectorias complejas para gestionar el movimiento de robots o de centros de mecanizado. Ofrecen software y soporte técnico al CFAA, en concreto con SprutCAM en lo referente a programación y postprocesado de trayectorias.
La integración del software SprutCAM en la célula de rebabado del CFAA ha permitido el diseño de trayectorias complejas para facilitar el acceso a zonas complicadas de las carcasas empleadas en la fabricación de turbinas para motores aeronáuticos. Además, gracias a su flexibilidad para customizar los programas de post-procesado, se ha adaptado el código generado para habilitar el posicionamiento automático de las piezas, así como el ajuste automático del TCP de la herramienta. En definitiva, se cuenta con un software muy versátil y potente, adaptado las necesidades intrínsecas de la planificación de trayectorias sobre geometrías complejas.
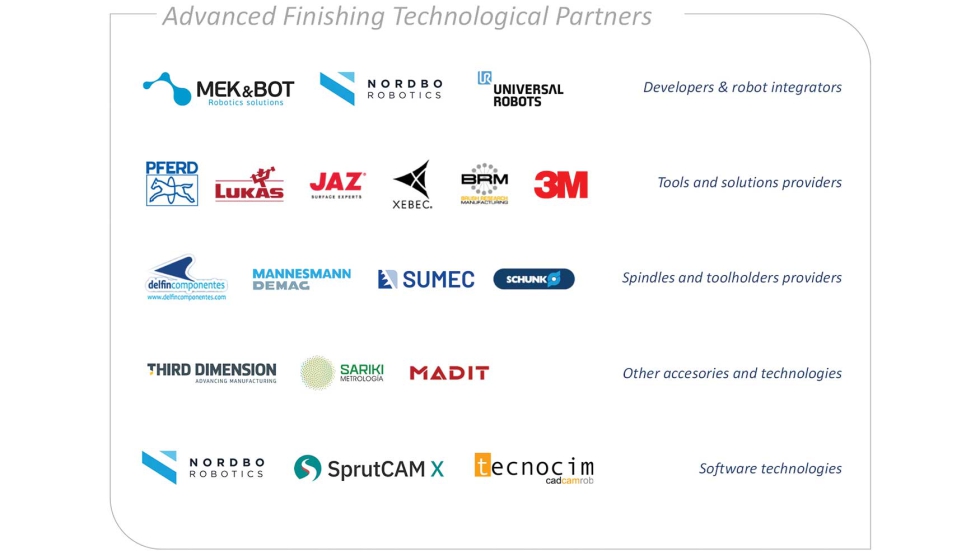
Agradecimientos
Las actividades presentadas en este trabajo se enmarcan dentro de la unidad AIMS (Artificial Intelligent Manufacturing for Sustainability) de la Universidad del País Vasco (UPV/EHU), y también como parte del proyecto de acrónimo CRESCENDO referencia CPP2021-008932 financiado por MCIN/AEI/10.13039/501100011033 y por la Unión Europea ‘NextGenerationEU’/PRTR y el proyecto QUOLINK TED2021-130044B-I00. Los autores agradecen también al grupo IT 573-22 del Gobierno Vasco.
Referencias
[1] Aerospace & Defense Manufacturing, (n.d.). https://www.statista.com/markets/407/topic/939/aerospace-defense-manufacturing/#overview (accessed May 20, 2024).
[2] A. Boretti, A techno-economic perspective on 3D printing for aerospace propulsion, J Manuf Process 109 (2024) 607–614. https://doi.org/10.1016/j.jmapro.2023.12.044.
[3] M.F. Shahriar, A. Khanal, The current techno-economic, environmental, policy status and perspectives of sustainable aviation fuel (SAF), Fuel 325 (2022). https://doi.org/10.1016/j.fuel.2022.124905.
[4] Y. Tian, K. Chadha, C. Aranas, Laser powder bed fusion of ultra-high-strength 420 stainless steel: Microstructure characterization, texture evolution and mechanical properties, Materials Science and Engineering: A 805 (2021). https://doi.org/10.1016/j.msea.2021.140790.
[5] N. Babacan, S. Pauly, T. Gustmann, Laser powder bed fusion of a superelastic Cu-Al-Mn shape memory alloy, Mater Des 203 (2021). https://doi.org/10.1016/j.matdes.2021.109625.
[6] Martínez S, Jimeno A, Sendino S, Murua O, Ruiz J E, Ostolaza M, Arrizubieta I, Fabricación aditiva por L-PBF en el CFAA: procesos híbridos, (2021). https://www.interempresas.net/Fabricacion-aditiva/Articulos/349309-Fabricacion-aditiva-por-L-PBF-en-el-CFAA-procesos-hibridos.html (accessed May 20, 2024).
[7] J. Jiang, H. Gu, B. Li, J. Zhang, Y. Gu, Effect of Solution Treatment on Mechanical Properties of Inconel 718 Alloy Formed by SLM, in: J Phys Conf Ser, Institute of Physics, 2024. https://doi.org/10.1088/1742-6596/2679/1/012008.
[8] B. Anush Raj, J.T. Winowlin Jappes, M. Adam Khan, V. Dillibabu, N.C. Brintha, Direct metal laser sintered (DMLS) process to develop Inconel 718 alloy for turbine engine components, Optik (Stuttg) 202 (2020). https://doi.org/10.1016/j.ijleo.2019.163735.
[9] J. Cao, Z. Guo, T. Sun, Y. Guo, Y. Liang, J. Lin, Microstructure evolution and mechanical properties of a high Nb–TiAl alloy via HIP and heat treatment, Materials Science and Engineering: A 884 (2023). https://doi.org/10.1016/j.msea.2023.145517.
[10] S. An, D.R. Eo, I. Sohn, K. Choi, Homogenization on solution treatment and its effects on the precipitation-hardening of selective laser melted 17-4PH stainless steel, J Mater Sci Technol 166 (2023) 47–57. https://doi.org/10.1016/j.jmst.2023.04.055.
[11] M. González, A. Rodríguez, O. Pereira, L.N.L. de Lacalle, Surface roughness evaluation when brushing heat-resistant alloy components, International Journal of Advanced Manufacturing Technology (2024). https://doi.org/10.1007/s00170-024-13695-5.
[12] R.W. Overholser, R.J. Stango, R.A. Fournelle, Morphology of metal surface generated by nylon/abrasive filament brush, 2003.