Fabricación aditiva de componentes bimateriales para la mejora de prestaciones de los motores aeroespaciales
En el año 2022 el mercado global de la fabricación aditiva para aplicaciones aeroespaciales se estima en casi 1.000 M$ y para el año 2030 se estima que alcance el valor de 3.500 M$, con un crecimiento anual del 18,1% [1]. Este crecimiento se debe principalmente en dos factores: por un lado, en el desarrollo de materiales y procesos específicos y que han permitido expandirse a la fabricación aditiva y, por otro lado, las ventajas que ofrece en comparación con otras tecnologías de fabricación como el mecanizado, la forja o el conformado.
La FA permite una personalización de componentes, haciendo rentable la fabricación de lotes pequeños e incluso unitarios. De esta manera, posibilita la reparación de componentes (operaciones de MRO) y facilita el mantenimiento de productos obsoletos (legacy parts) cuyo repuesto no sería económicamente viable de otra manera.
Además, gracias a que la FA permite la fabricación de componentes con una geometría cercana a la final, elevado buy-to-fligh ratio, se reduce la cantidad de desperdicio que se genera. Esta ventaja al mismo tiempo se traduce en otros dos beneficios, ya que un consumo más eficiente de la materia prima permite un uso más responsable de los recursos naturales y abarata el coste del tratamiento de los residuos generados, como sería el material en forma de viruta que se produce en la operación de mecanizado.
Por último, habría que subrayar que la FA permite un diseño de componentes prácticamente libre de restricciones geométricas y con un peso reducido, siendo ambos factores críticos para el sector aeroespacial, donde una reducción de peso resulta en un ahorro de combustible y por lo tanto de costes de operación e impacto ambiental de la aeronave durante su vida útil. Gracias al empleo de la FA los ingenieros encargados del diseño de los componentes pueden plantearse geometrías complejas y topológicamente optimizadas para la función exacta que deben cumplir. Además, la FA permite fabricar conjuntos de componentes en una única pieza, lo que supone una simplificación considerable de las posteriores operaciones de montaje. Pero las ventajas no se limitan únicamente a mejoras en el diseño, sino que la FA permite combinar diferentes materiales e incluso variar la composición de estos de manera progresiva, lo que resulta en una optimización de las propiedades de los componentes.
Aplicaciones de la fabricación aditiva multimaterial
A día de hoy se puede afirmar que las piezas fabricadas mediante FA ya están en otro planeta: el rover Perseverance incluía hasta 11 componentes fabricados por aditiva. Por ejemplo, contenía un elemento estructural fabricado por la empresa Carpenter Additive mediante la tecnología de Electron Beam Melting (EBM) que permitió reducir la masa aproximadamente en un 25% en comparación a la que tendría si se hubiera fabricado mediante otras tecnologías convencionales [2].
Pero centrándonos en ejemplos más terrenales, la FA se está empleando para la mejora de las prestaciones de los dispositivos de propulsión y componentes estructurales, como es el caso de los motores de propulsión. Entre las ventajas de la FA figuran la reducción del número total de piezas del motor, la simplificación de los diseños, la impresión de canales de refrigeración con ángulos salientes únicos y la mejora del empuje.
Una de las aplicaciones más novedosas de la FA en el sector aeroespacial es la fabricación de componentes bimateriales. Gracias a la capacidad única de cambiar de material durante el proceso de impresión, es posible variar la composición en cada zona del componente en función de las condiciones de trabajo a las que estará sometida. Así, se pueden diferenciar dos estrategias diferenciadas: 1) generación de recubrimientos de conductividad mejorada para una distribución de calor más homogénea, evitar puntos calientes y mejorar la refrigeración de ciertas superficies cercanas a focos calientes. 2) Generación de barreras térmicas que aíslen la superficie recubierta. En los siguientes apartados se resumen algunos de los avances realizados en estos dos ámbitos.
Componentes bimateriales para la mejora de la conductividad térmica
Las toberas de propulsión de los motores de los vehículos aeroespaciales son elementos que necesitan una alta capacidad de disipación del calor y buen comportamiento a altas temperaturas. Consecuentemente, los materiales empleados en su fabricación son de gran importancia. Hoy en día, con el aumento del conocimiento de la ciencia de materiales se han desarrollado nuevos materiales e incluso combinaciones de materiales que permiten aumentar las prestaciones de estos componentes. En este sentido, la fabricación aditiva (FA) permite la fabricación de componentes bimateriales, abriendo un nuevo campo de aplicaciones.
Un componente bimaterial, tal y como se deduce del propio término, es una pieza compuesta por dos materiales diferentes que están unidos metalúrgicamente. No obstante, a diferencia de las aleaciones que se han venido empleando tradicionalmente en la industria, como es el caso de aleaciones base níquel (Inconel 625, Inconel 718, Hastelloy X, MAR M247, etc.) o aleaciones base titanio como el TiAl4V, en la estructura de los bimateriales sus constituyentes están perfectamente diferenciados.
Otro ejemplo de componentes bi- o multi-materiales serían los materiales compuestos. Estos se definen como la combinación de dos o más materiales que forman una estructura discreta a fin de obtener ciertas propiedades que no disponen los materiales originales, y en ellas se diferencian la matriz y el agente discreto a modo de refuerzo. Entre los materiales compuestos se encuentran los materiales compuestos de matriz metálica (MMC) los cuales están constituidos principalmente por un metal y otros componentes metálicos, cerámicos u orgánicos. Por lo tanto, un componente bimaterial podría ser un material compuesto como se muestra en la figura 1.
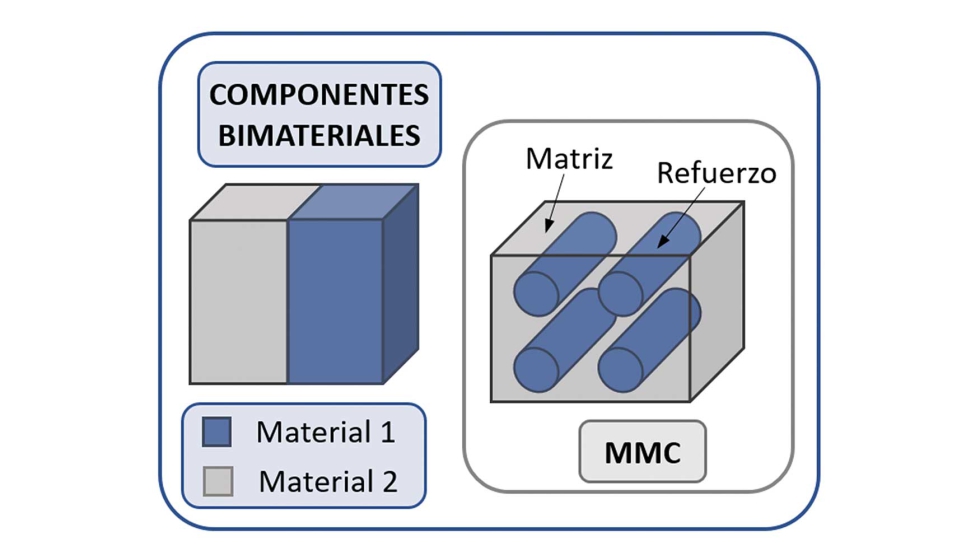
Los componentes bimateriales fabricados por FA han ganado fiabilidad expandiéndose a la industria aeroespacial a medida que dicha tecnología ha ido madurando. Así, son numerosas las investigaciones llevadas a cabo con la intención de obtener componentes con propiedades termomecánicas mejoradas con respecto a los de los materiales de origen. El intercalar capas de cobre (Cu) en una estructura de Inconel 625 puede ser una solución para mejorar el comportamiento térmico del motor de un cohete. Ejemplo de ello es que, hoy en día, ya se han fabricado las primeras piezas demostradoras mediante la tecnología de fusión del lecho de polvo, PBF-LB (Figura 2(a)) y se encuentran pendientes de validación en un futuro próximo.
Por otro lado, existen toberas de combustión fabricadas híbridamente, combinando las tecnologías de fusión del lecho de polvo (PBF-LB) para obtener la parte interior de cobre y el aporte directo de energía (DED-LB) para el recubrimiento de Inconel 625. Ejemplo de ello es la pieza que se muestra en la figura 2(b), la cual está validada por la NASA [4].
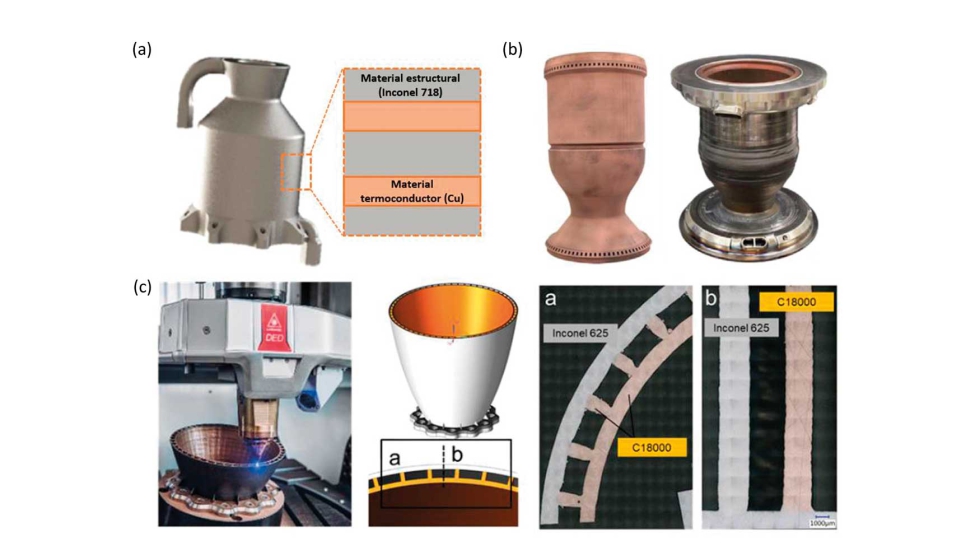
Una alternativa a la hibridación de dos procesos, uno por material, es la solución propuesta por DMG MORI, véase la figura 2(c), donde es posible cambiar el material durante el proceso de aporte. Empleado exclusivamente la tecnología de aporte directo de energía (DED-LB) y una única máquina, la Lasertec 125 DED, se fabrica una tobera de combustión bimaterial en una única atada.El interés hacia el aporte de aleaciones del cobre ha sido traccionado en gran medida por el programa RAMPT (Rapid and Analysis Manufacturing Propulsion Technology) de la NASA [6] cuyo objetivo principal es desarrollar nuevos métodos para la fabricación de cohetes mediante el aporte directo de energía (DED) e inyección directa del material en forma de polvo. Asimismo, otra línea de desarrollo en la que se trabaja en el proyecto RAMPT está relacionada con la reducción del peso y coste del conjunto de la cámara de propulsión de los cohetes y la tobera de salida de gases. Por ejemplo, se ha detectado que, gracias al empleo de uniones bimetálicas, es posible fundir la cámara de combustión de cobre directamente en la tobera sin juntas ni pernos metálicos adicionales, lo que reduce el peso del componente y minimiza aquellas zonas de concentración de tensiones, alargando así la vida útil y seguridad del componente. En paralelo al proyecto RAMPT, otras empresas de lanzamiento privadas, como Launcher y Virgin Orbit, también han fabricado grandes componentes de aleación de cobre mediante el PBF-LB y DED-LB.
El efecto que produce la combinación de varios materiales de diferente conductividad térmica sobre el comportamiento térmico del componente es fácilmente visible mediante una simulación térmica de dichos componentes. A modo de ejemplo, en el proyecto ReIMAGIN financiado por el Gobierno Vaso (KK-2023/00096) se ha simulado mediante el software Ansys Workbench 2024-R1 el comportamiento estático de dos paralelepípedos de 100 x 100 x 20 mm3. Uno de ellos fabricado íntegramente en Inconel 625 y otro bimaterial Inconel 625 + Cobre, véase la figura 3. En ambos casos las caras de 100 x 100 mm2 están sometidas a una convección forzada, una cara en una corriente de aire caliente a 400 °C, y la otra a una corriente de refrigeración a 20 °C, suponiendo en ambos casos un coeficiente convectivo de 100 W/m2K. En las 4 caras restantes se ha supuesto que no hay transferencia de calor, que es la condición análoga a indicar que la pieza el continua en dichas direcciones X e Y.
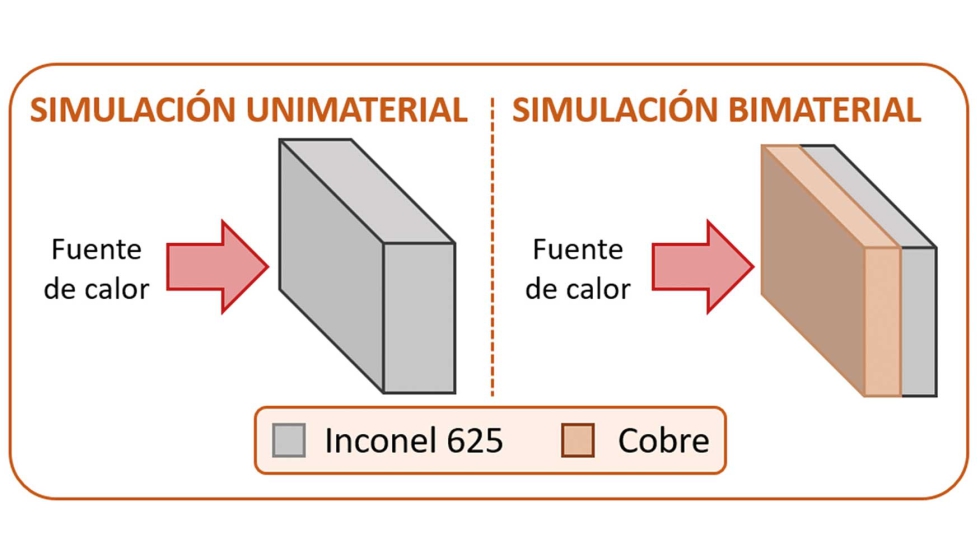
Como puede observarse en los resultados de las simulaciones mostradas en la figura 4 en el componente monomaterial las temperaturas que se alcanzan son superiores al componente bimaterial, donde se observa que en el cobre las temperaturas alcanzadas son prácticamente constantes (ausencia de puntos calientes).
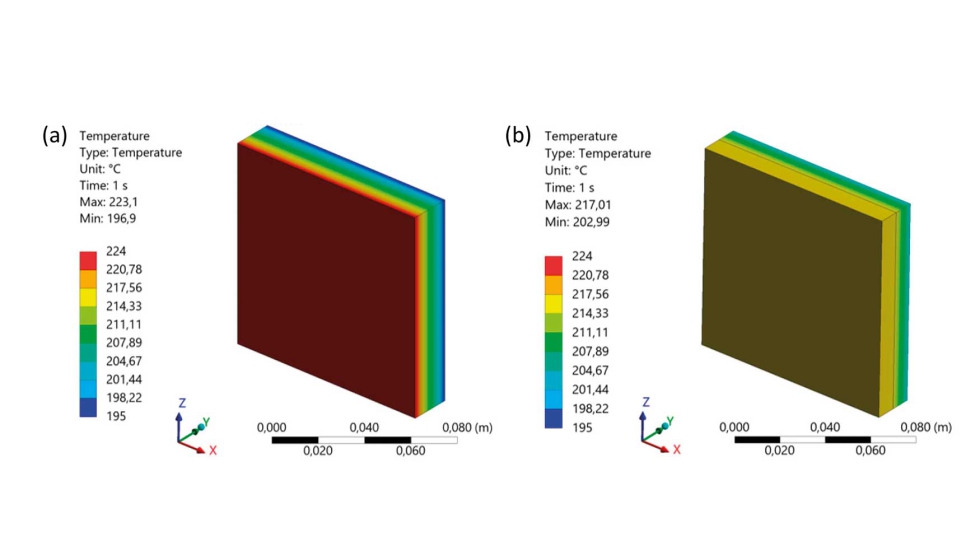
Recubrimientos superficiales para el aislamiento térmico
Los recubrimientos de barrera térmica o Thermal Barrier Coatings (TBC) del inglés, son estructuras multimaterial empleadas para mejorar las propiedades de componentes expuestos a altas temperaturas. La estructura básica de un TCB consiste en un sustrato, una capa de adherencia, un óxido formado térmicamente (thermally grown oxide) y una capa exterior, y en conjunto pueden medir entre 100 µm y 2 mm (figura 5). El material exterior del recubrimiento cuenta con una baja conductividad térmica, por lo que funciona como aislante térmico reduciendo la temperatura que se alcanza en el material base. La capa de adherencia se escoge en función del material base, para que al aumentar la temperatura los elementos que los componen reaccionen entre ellos formando una capa protectora de óxido.
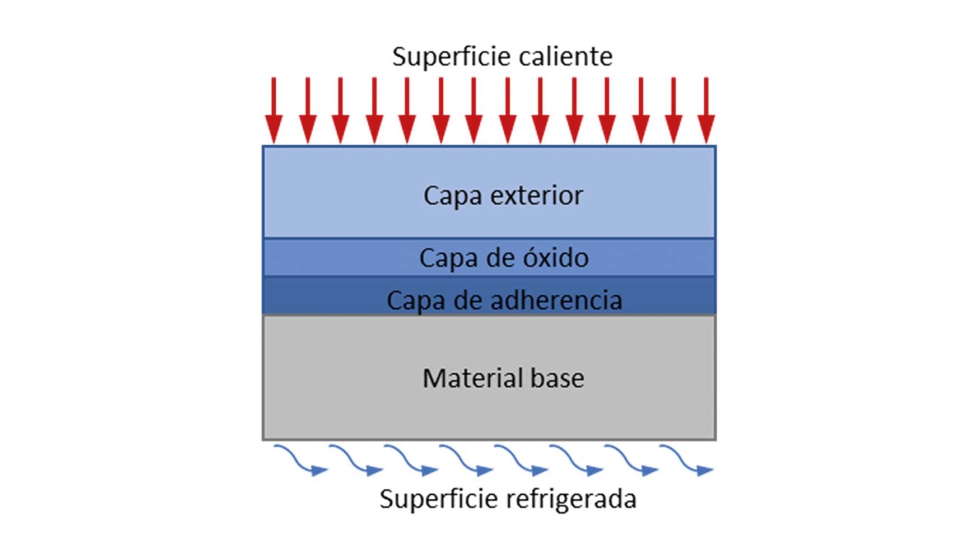
Los TBC no sólo permiten aumentar las temperaturas de funcionamiento mediante el aumento de la resistencia térmica de un componente, sino que también restringen la pérdida de calor hacia el entorno, ofreciendo así un mejor aislamiento y una mayor eficiencia térmica. Debido a esto, las principales aplicaciones de estos recubrimientos son los componentes de las zonas calientes de las turbinas de gas, los motores de combustión interna y componentes nucleares avanzados [7].
Los principales requerimientos de materiales que forman los TBC son la baja conductividad térmica y la resistencia a la oxidación y la corrosión. Aunque, en función de los distintos materiales base y condiciones de trabajo de cada aplicación, características adicionales también pueden ser requeridas. Por ejemplo, en el caso de las turbinas de gas, los cambios repentinos de temperatura requieren de una alta resistencia al shock térmico. Por otro lado, la compatibilidad de los coeficientes de dilatación del material base y recubrimiento también es crítico para la vida útil de este.
Como ya se ha mencionado previamente, las superaleaciones de base níquel, como el Inconel 625 o Inconel 718 se emplean habitualmente en componentes de turbinas y en dichos casos los recubrimientos más empleados se basan en el circonio estabilizado con itria (YSZ) como capa exterior [8]. En la mayoría de los casos, la capa de adherencia es una aleación de NiCrAlY, donde el aluminio forma la capa de óxido para proteger el material base y el resto de elementos proporcionan ductilidad a la matriz de unión [9].
Este tipo de TBC es ampliamente empleado en alabes de motores comerciales como los V2500, CF6-50 y CF6-80, y tradicionalmente se fabrica mediante rociado de plasma atmosférico (Atmospheric Plasma Spraying, APS) mostrado en la figura 6. El recubrimiento resultante contiene una alta porosidad (entorno al 25%), con el objetivo de reducir la conductividad térmica del material completamente denso entorno al 50%.
![Figura 6. Configuración del rociado de plasma atmosférico de Sultzer [10] Figura 6. Configuración del rociado de plasma atmosférico de Sultzer [10]](https://img.interempresas.net/fotos/4502202.jpeg)
Por otro lado, la formación de porosidad cumple con la función de reducir las tensiones internas a las que está sometida el recubrimiento. De esta manera, se minimiza el riesgo de agrietamiento y se mejora la unión entre el material base y la capa externa, que constituye el principal punto débil de un TBC.
La posible integración de tecnologías de Fabricación Aditiva en la fabricación de TBC ha sido estudiada en los últimos años, en concreto en el caso del DED-LB de polvo metálico. Por un lado, el ajuste de los parámetros de aporte permite generar recubrimientos de porosidad controlada de manera simple (figura 7).
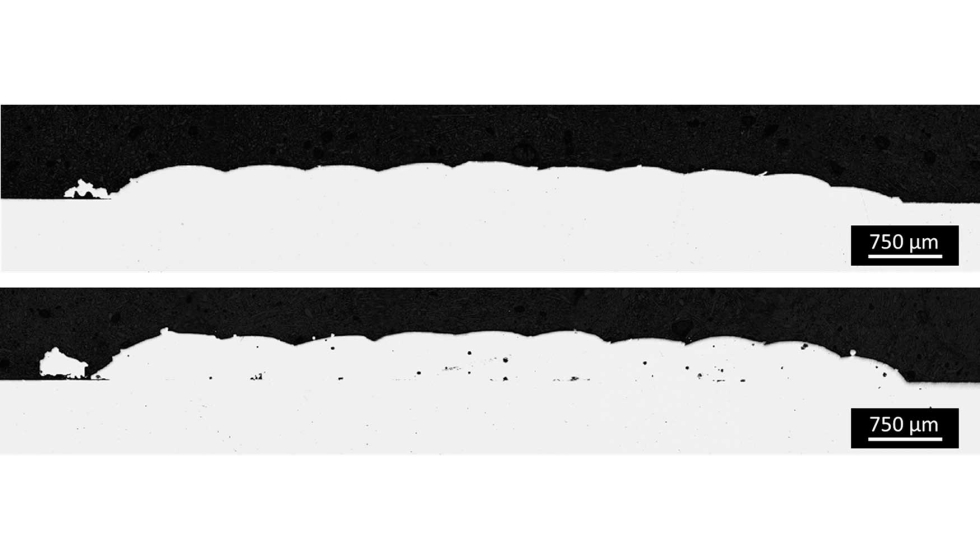
Por otro lado, el DED-LB posibilita la generación de estructuras de gradiente funcional o FGM mediante el empleo de más de una tolva de alimentación. De esta manera, se pueden depositar capas de composición intermedia entre la capa de adherencia y la capa exterior del TBC, como se muestra en la figura 8.La incorporación de dicha estructura reduce la tensión entre capas y mejora el comportamiento del recubrimiento durante su ciclo de vida [11].
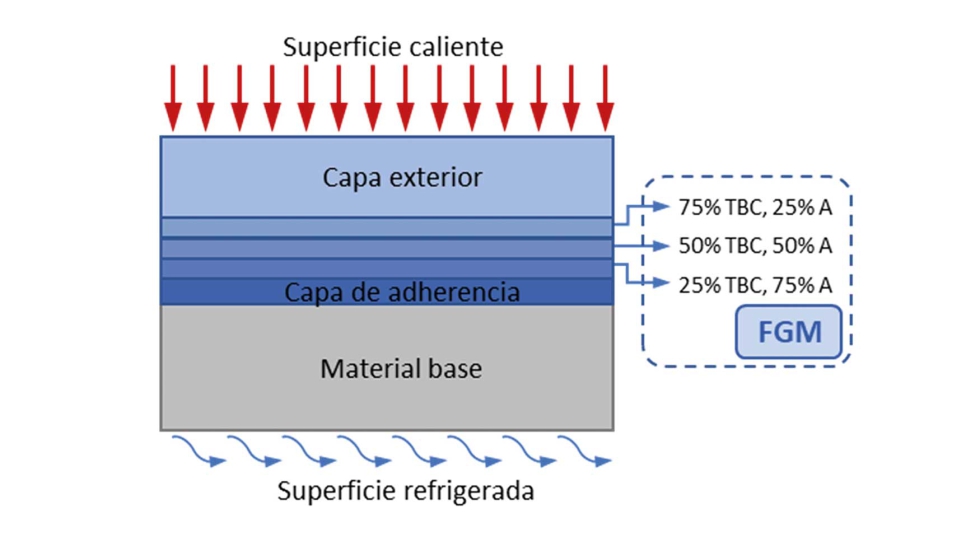
Nuevos desarrollos para maximizar la productividad
El aporte de materiales de alta reflectividad como el cobre mencionado en el apartado previo, requiere de elevadas potencias del láser, lo que resulta en reflexiones que pueden dañar tanto el cabezal del aporte, como las ópticas o incluso la propia máquina. Una alternativa para solucionar este problema ha sido la de emplear aleaciones de cobre como el CuAl10 o el CuSn8, para los cuales la absortividad se incrementa ligeramente. No obstante, esta sigue siendo muy baja para láseres de estado sólido y potencias superiores a los 3 kW suelen ser habituales para este tipo de aplicaciones.
Ante esta problemática, recientemente se han desarrollado nuevos láseres que permiten trabajar en diferentes longitudes de onda, y así aprovechar mejor la energía del láser gracias a una mayor absortividad del material. En la figura 9 se muestra a modo de ejemplo la absortividad del titanio (Ti), cobre (Cu), acero inoxidable (SS304) y aluminio (Al) para diferentes longitudes de onda, donde se resalta tres franjas. La línea roja situado en la longitud de onda de 1.060 nm se corresponde con la luz que emiten los láseres de fibra y disco. La verde y azul se corresponden con las longitudes de onda que emiten los láseres que se identifican con los mismos nombres y cuyas longitudes de onda se encuentran entorno a los 520 y 450 nm, respectivamente. Como puede apreciarse, el empleo de los láseres azul y verde conlleva un incremento considerable de la absortividad, que es especialmente notable para materiales como el cobre.
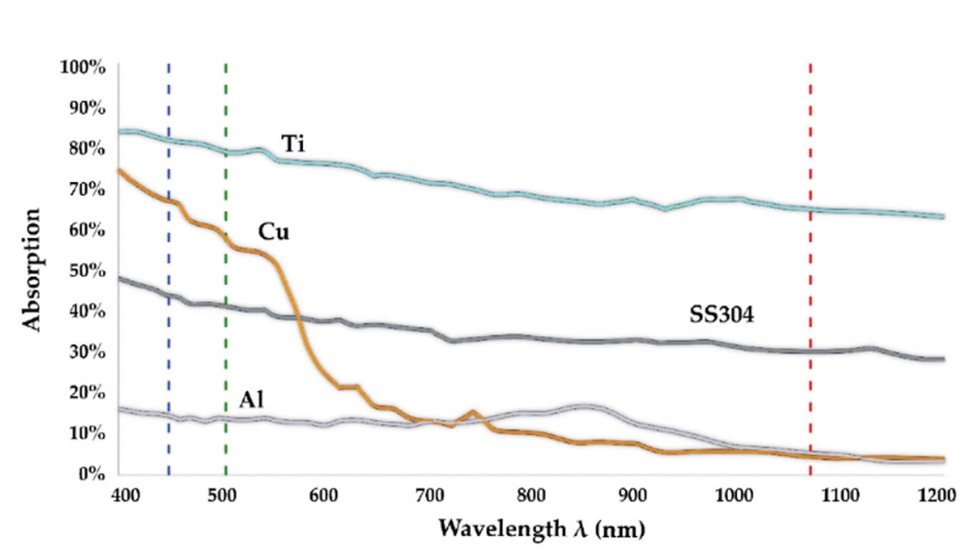
Láser verde
El láser verde tiene una longitud de onda de entorno a los 520 nm y coincide exactamente con la mitad de la longitud de onda que los de estado sólido (fibra y disco), de ahí que a estos láseres se les denomine como láseres de segunda generación harmónica. Para conseguir esta longitud de onda, es necesario alterar la luz emitida por un láser YAG o YVO4 pasándolo a través de un monocristal de óxido (LBO: borato de litio).
La razón de la denominación de ‘láser verde’ se debe a que esta longitud de onda de 520 nm se corresponde con la del color verde dentro del espectro de luz visible y presenta la ventaja de que muchos materiales tienen una mayor tasa de absorción a esta longitud de onda que a 1.060 nm. Por ejemplo, para materiales como el cobre o el oro que, a la longitud de onda de los láseres IR (1064 nm) tienen una absortividad por debajo del 10%, se consiguen absortividades por encima del 50%. Además, esta menor longitud de onda permite concentrar el haz láser en un spot más pequeño, por lo que se obtienen resultados de mayor precisión.
Gracias al empleo de láseres verdes se evitan los problemas que se producen al acoplar el haz láser con el material, donde además de generar elevadas pérdidas por reflexiones, el baño fundido suele ser inestable, se producen salpicaduras en la superficie aportada y los aportes tienden a presentar una elevada porosidad. Consecuentemente, los láseres verdes permiten eliminan estos problemas y Prima Additive afirma que las piezas fabricadas en cobre pueden alcanzar densidades superiores al 99,8% [13] y se puede aportar cobre a velocidades 10 veces superiores a los que se pueden alcanzar con un láser IR.
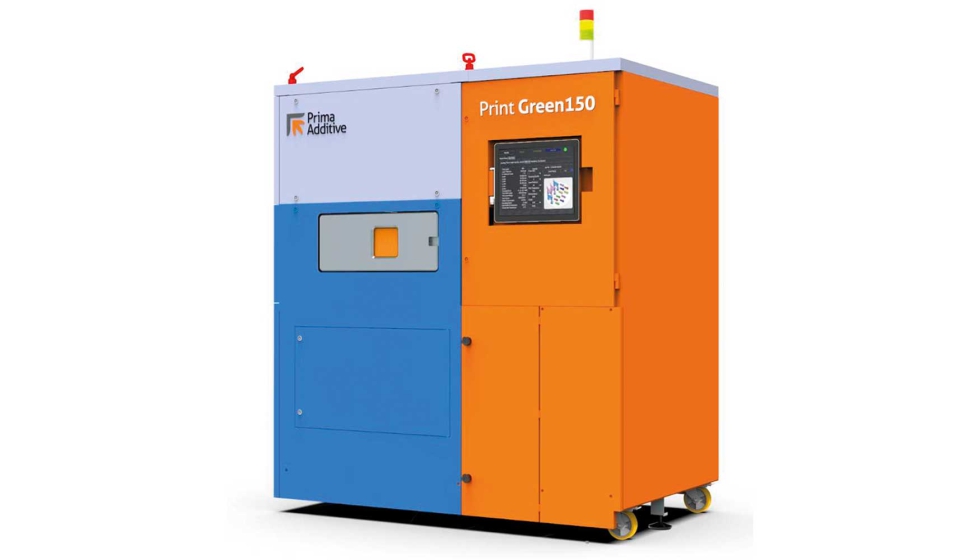
Otros sistemas como los desarrollados por Trumpf también ofrecen láseres verdes en su catálogo de quipos, enfocando su utilización principalmente a la soldadura de cobre y a la impresión 3D de cobre puro mediante la tecnología de PBF-LB. En figura 11 se muestran dos ejemplos de componentes fabricados mediante láseres verdes.
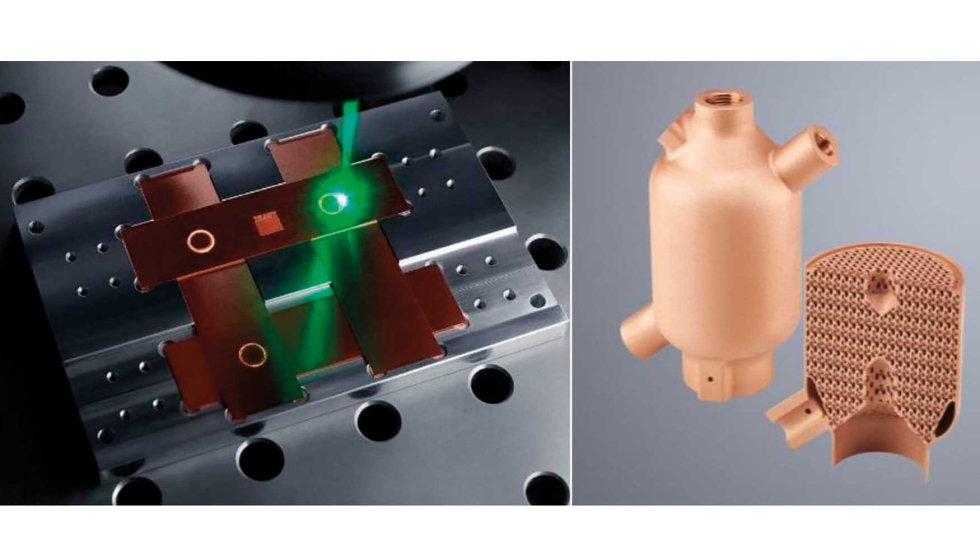
Láser azul
El desarrollo de los láseres azules es más reciente que el de los verdes y su integración en máquinas y disponibilidad en el mercado es muy limitado. Los primeros láseres azules se desarrollaron aproximadamente hace 5 años y la empresa Nuburu ha sido una de las primeras en integrar un láser azul en una máquina de PBF-LB. No obstante, a la vista de las mejoras en eficiencia que estos láseres prometen frente a los láseres IR, figura 12, empresas punteras del sector de la máquina herramienta de FA están apostando por esta tecnología.
![Figura 12. Comparativa entre la eficiencia de impresión del láser azul y el láser IR para diferentes metales [15] Figura 12. Comparativa entre la eficiencia de impresión del láser azul y el láser IR para diferentes metales [15]](https://img.interempresas.net/fotos/4502213.jpeg)
Por ejemplo, empresas como Prima Additive están desarrollando equipos de fabricación aditiva, DED-LB, con generadores láser fabricados por la propia empresa que emiten en la longitud de onda de la luz azul. Otro ejemplo es el acuerdo que han firmado las empresas Nuburu y GE Additive, donde se quieren explorar las capacidades del láser azul desarrollado por la primera y GE Additive pretende sacar al mercado una máquina de PBF-LB basada en ella.
Conclusiones y perspectivas de futuro
En términos generales, el futuro de la FA gira en torno a aplicaciones de alto valor añadido. Así, el sector aeroespacial resulta ser uno de los principales mercados de la tecnología cara a futuro, sin embargo, todavía se requieren nuevas soluciones para la mejora de la eficiencia y reducir los costes de producción. Además de las ventajas de complejidad geométrica y flexibilidad de diseño que ofrece la FA, cada vez cobra mayor interés el desarrollo de nuevos materiales y combinaciones de materiales que hasta la fecha no se contemplaban.
El aumento de la eficiencia en los propulsores pasa principalmente por dos aspectos, la optimización geométrica que facilite una reducción de peso y mejore el flujo de gases y la correcta gestión térmica. Con el incremento local de la temperatura de funcionamiento en ciertas zonas es posible aumentar la eficiencia, de modo que, combinando mayores temperaturas de funcionamiento y mayores relaciones de compresión se incrementa el rendimiento de los motores. La introducción de la FA permite combinar materiales y geometrías más complejas, por lo que se abre la puerta a la introducción de estas mejoras. Además, es posible incluir elementos para la recuperación energética y gestión térmica mediante el uso de intercambiadores y zonas con recubrimientos de baja conductividad térmica, por lo que se podría incrementar el rendimiento en mayor medida.
Los desarrollos dentro de la tecnología de DED-LB para la combinación de materiales, está posibilitando el desarrollo de nuevas estructuras bimateriales y de materiales compuestos haciendo posible aumentar la resistencia y/o modificar las propiedades térmicas de modo localizado en función de las necesidades para la mejora de la eficiencia global.
En algunos casos debido a la complejidad geométrica y los requisitos de acabado superficial de ciertos componentes, no es viable el uso de la tecnología DED-LB. En estos casos, la resolución proporcionada por procesos como el PBF-LB resulta más adecuado, sin embargo, la combinación de materiales y el tamaño de piezas que se pueden procesar resultan más limitados. El desarrollo de nuevas fuentes láser, con longitudes de onda más corta, capaces de procesar materiales de alta reflectividad como el cobre abre un nuevo escenario para la generación de estructuras de alta conductividad térmica y elevada complejidad. En este contexto, los desarrollos de procesos multimaterial en LPF-LB y la fabricación híbrida de piezas combinando tecnologías DED-LB y PBF-LB proporciona unas nuevas capacidades que nos acercan a una mayor eficiencia energética.
Siguiendo la tendencia de los últimos años, los desarrollos en tecnología PBF-LB irán orientados a la fabricación de componentes de mayor tamaño con una mayor productividad y la combinación de materiales. Actualmente, existen desarrollos que combinan aleaciones de acero con aleaciones de cobre, sin embargo, la combinación de materiales está limitada por la necesidad de separar los materiales, por lo que uno de los materiales empleados debe ser necesariamente ferromagnético.
En relación a los procesos DED-LB, tanto con material de aporte en polvo o hilo, se espera que exista un aumento de las capacidades de generación de aportes de alta resolución en combinación con una tasa global de producción adecuada. Actualmente existen sistemas capaces de combinar boquillas diferentes, permitiendo combinar cabezales con un control preciso en zonas de detalle con boquillas que consiguen una mayor tasa de aporte para piezas de mayor tamaño. Asimismo, la combinación de materiales cerámicos y metálicos con estrategias de variación gradual de la composición se plantea como un campo de notable interés de cara a la obtención de recubrimientos y componentes con nuevas funcionalidades.
Agradecimientos
Los autores quieren agradecer al proyecto PID2022-141946OB-C21 financiado por MCIN/AEI/10.13039/501100011033/ y por FEDER Una manera de hacer Europa y al Gobierno Vasco por su financiación al proyecto ReIMAGIN (KK-2023/00096).
Referencias
[1] ‘Global Aerospace Additive Manufacturing Market to Reach $3.5 Billion by 2030’ maitworld.com. [Online] https://www.maintworld.com/News/Global-Aerospace-Additive-Manufacturing-Market-to-Reach-3.5-Billion-by-2030
[2] M. Aysha. ‘NASA’s Perseverance rover carries 11 3D printed parts to Mars’. 3dnatives.com (26 Oct 2020). [Online] https://www.3dnatives.com/en/perseverance-rover-3d-printed-parts-261020205/#
[3] A. Marques, Â. Cunha, M. Gasik, O. Carvalho, F. S. Silva, y F. Bartolomeu. ‘Inconel 718–copper parts fabricated by 3D multi-material laser powder bed fusion: a novel technological and designing approach for rocket engine’. International Journal of Advanced Manufacturing Technology. (2022). https://doi.org/10.1007/s00170-022-10011-x
[4] F. Kerstens, A. Cervone, y P. Gradl. ‘End to end process evaluation for additively manufactured liquid rocket engine thrust chambers’. Acta Astronautica, 182, 454–465. (2021). https://doi.org/10.1016/j.actaastro.2021.02.034
[5] N. Niemeyer. ‘Advances in Bimetallic-DED Enables Copper Alloy Processing’. sme.org. [Online] https://www.sme.org/technologies/articles/2023/june/advances-in-bimetallic-ded-enables-copper-alloy-processing/
[6] ‘Rapid Analysis and Manufacturing Propulsion Technology’ nasa.gov. [Online] https://www.nasa.gov/rapid-analysis-and-manufacturing-propulsion-technology/
[7] K. Mondal, L. Nuñez, C. M. Downey, I. J. van Rooyen. ‘Thermal Barrier Coatings Overview: Design, Manufacturing, and Applications in High-Temperature Industries’. Industrial & Engineering Chemistry Research. (2021). https://doi.org/10.1021/acs.iecr.1c00788.
[8] B. Gleeson. ‘Thermal Barrier Coatings for Aeroengine Applications’. Journal of Propulsion and Power 22. (2006). https://doi.org/10.2514/1.20734
[9] M. Bai, B. Song, L. Reddy, T. Hussain. ‘Preparation of MCrAlY–Al2O3 Composite Coatings with Enhanced Oxidation Resistance through a Novel Powder Manufacturing Process’. Journal of Thermal Spray Technology 28. (2019). https://doi.org/10.1007/s11666-019-00830-y.
[10] ‘Rociado de plasma atmosférico (Atmospheric Plasma Spraying, APS)’. sultzer.com. [Online] https://www.sulzer.com/es-es/spain/shared/services/atmospheric-plasma-spraying-aps
[11] M. M. Gasik, A. Kawasaki, y Y. S. Kang. ‘Optimisation of FGM TBC and Their Thermal Cycling Stability’. In Materials Science Forum. Trans Tech Publications, Ltd. (2005). https://doi.org/10.4028/www.scientific.net/msf.492-493.9
[12] R. Bidulsky, F. S. Gobber, J. Bidulska, M. Ceroni, T. Kvackaj y M. A. Grande. ‘Coated Metal Powders for Laser Powder Bed Fusion (L-PBF) Processing: A Review’. Metals 11, no. 11: 1831. (2021) https://doi.org/10.3390/met11111831
[13] ‘Green Laser for Powder Bed Fusion Technology’ primadditive.com. [Online] https://www.primaadditive.com/en/technologies/powder-bed-fusion/green-laser-pbf
[14] Trumpf.com. [Online] https://www.trumpf.com/es_ES/
[15] ‘Demonstrating the capabilities of blue lasers in additive manufacturing’ lasersystemseurope.com. [Online] https://www.lasersystemseurope.com/analysis-opinion/demonstrating-capabilities-blue-lasers-additive-manufacturing