Avances en el sector de la fabricación aeronáutica: máquinas para una industria muy exigente
A. Del Olmo 1, 2; G. Martínez de Pissón 1,2; N. Villarrazo 1,2; S. Caneda 1,2; I. Ayesta 1,2; A. Artabe 1,2; I. Zamakona 3; O. Pereira 1,2; S. Sedino 1,2
1) Dpto. de Ingeniería Mecánica, Universidad del País Vasco (UPV/EHU),
2) Centro de Fabricación Avanzada en Aeronáutica (CFAA), Universidad del País Vasco (UPV/EHU)
3) ITP Aero, S.A.
07/07/2023En los últimos años, el sector de la fabricación aeronáutica ha experimentado importantes avances tecnológicos en la producción de componentes de aeronaves. Estos avances han sido impulsados por la cuarta revolución industrial y han dado lugar a un nuevo concepto de fabricación de máquinas más robustas y altamente fiables en comparación con las anteriores.
En este contexto, estas máquinas destacan por su capacidad para supervisar y controlar los complejos pasos que implica la fabricación de piezas de alto valor añadido. Emplean una combinación de datos procedentes de sus controles, sensores integrados y sistemas de procesamiento de datos para detectar y corregir incertidumbres en tiempo real, lo que permite una supervisión continua y precisa de los procesos de producción. Tanto el diseño como la construcción de estos dispositivos se basan en la premisa específica de garantizar la producción de componentes que cumplan las normas de calidad y precisión exigidas por la industria aeronáutica. Esto implica trabajar con materiales exigentes que presenten una increíble resistencia mecánica, resistencia a la corrosión y resistencia a la fatiga, incluso a altas temperaturas. Esto se convierte en un proceso extremadamente complejo debido a las importantes fuerzas de corte y tensiones que intervienen.
Para hacer frente a estos retos, se necesitan técnicas adecuadas y máquinas capaces de soportar las fuerzas generadas durante el proceso, así como herramientas específicamente diseñadas para el mecanizado de estas superaleaciones. La integración de tecnología avanzada en la fabricación aeronáutica ha dado lugar a mejoras significativas en la seguridad, fiabilidad y eficiencia de las aeronaves. Estas máquinas de fabricación han reducido los costes de producción y aumentado la capacidad de producción de piezas, lo que ha sido crucial para satisfacer la creciente demanda en un sector tan competitivo. Además, su implantación ha contribuido a la optimización de los procesos de producción, mejorando la calidad, la precisión y la productividad en la industria aeronáutica y en muchas otras.
En esta línea, el Centro de Fabricación Avanzada Aeronáutica (CFAA) ubicado en Zamudio desarrolla diversas actividades de investigación centradas en los procesos de fabricación de componentes aeronáuticos, incluyendo máquinas, procesos y herramientas de corte.
Proceso de fabricación de CFAA
Un avión es un sistema de transporte de gran complejidad, compuesto por múltiples piezas que requieren la intervención de diversos procesos de fabricación en su conformación. Para garantizar unos resultados óptimos, es necesario utilizar distintas máquinas, cada una de ellas con características específicas adaptadas a su función. Es crucial distinguir entre estas máquinas en función de los procesos en los que intervienen, ya que cada proceso presenta exigencias y requisitos diferentes.
1. Proceso de fabricación sustractivo
La fabricación sustractiva es un método muy utilizado en la industria manufacturera. Consiste en retirar material de un bloque más grande o material de reserva para crear los objetos o piezas deseados. El proceso se conoce como mecanizado o corte. Las máquinas-herramienta, como taladros, tornos, fresadoras y rectificadoras, se utilizan para eliminar material y conseguir diseños o instrucciones específicos. El mecanizado permite producir formas precisas e intrincadas con tolerancias estrechas, lo que lo hace adecuado para diversas industrias, incluida la aeroespacial. Sin embargo, puede llevar mucho tiempo y generar una gran cantidad de residuos de material debido a su naturaleza sustractiva. No obstante, la fabricación sustractiva sigue siendo popular para crear componentes funcionales y prototipos. Hasta la fecha, es la técnica básica para alcanzar simultáneamente precisión y productividad.
La máquina CFAA es un buen ejemplo del estado actual de la industria aeronáutica.
1.1. GMTK Multiproceso VR 2.4
Existe una demanda urgente para mejorar la eficiencia y minimizar las posibilidades de desechos en el proceso de fabricación de componentes de motores aeroespaciales. Debido al elevado coste de las superaleaciones y a los importantes retos geométricos y técnicos que plantean, el control continuo del mecanizado es de vital importancia para anticiparse a los problemas [G1]. La investigación presenta varios retos tecnológicos, y la colaboración entre los fabricantes de máquinas herramienta y los fabricantes de componentes aeroespaciales es indispensable en un entorno de investigación.
En este contexto, el centro de mecanizado GMTK VR2.4 destaca como una solución altamente flexible que satisface los requisitos específicos de la producción de componentes aeroespaciales, al tiempo que presenta una configuración rígida y una elevada dinámica. Esta avanzada máquina destaca tanto en operaciones de torneado como de fresado, equipada con dos ejes lineales hidrostáticos y un eje C rotativo hidrostático. Con un novedoso sistema integrado de cambio de herramientas, portaherramientas y cabezales, ofrece flexibilidad, precisión y productividad. Con un rango de trabajo máximo de 2.400 mm de diámetro y una potencia de accionamiento de 56 kW, es ideal para la fabricación de componentes de revolución como discos y carcasas aeronáuticas. El centro de mecanizado GMTK VR 2.4 ofrece una eficacia y fiabilidad excepcionales para la manipulación de geometrías complejas en la industria aeroespacial.
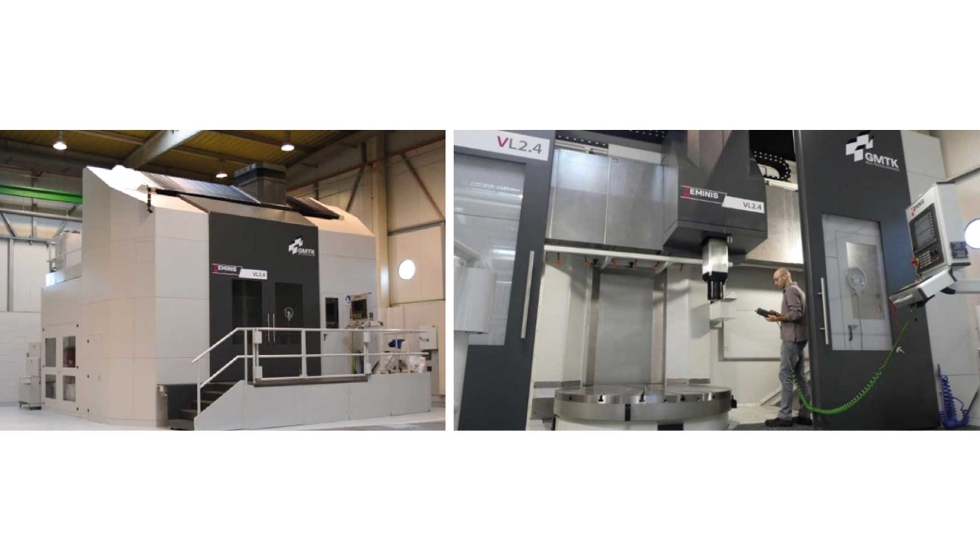
- Líneas de investigación: Proyecto FIDATU
En el CFAA, una de las principales líneas de investigación en el campo de la fabricación de componentes aeronáuticos es el proyecto FIDATU (ZE-2022/00009) financiado por el Gobierno Vasco dentro del programa HAZITEK 2022. Este proyecto aborda el reto de evitar el desguace de piezas debido a una mala calidad superficial o a requisitos de tolerancia. El objetivo del proyecto es monitorizar los procesos de fabricación mediante la sensorización del cabezal de mecanizado.
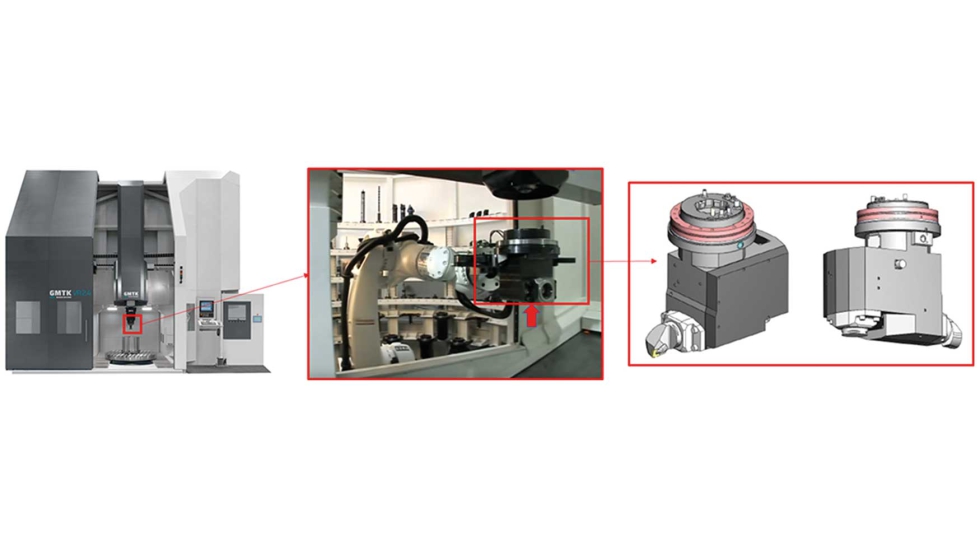
Como se muestra en las fotografías anteriores, el cabezal puede colocarse y retirarse en la RAM de la máquina, asemejándose a un proceso de cambio de herramientas. Además, el cabezal cuenta con dos posiciones de sujeción de la herramienta que son controladas por un sistema hidráulico de sujeción del portaherramientas. Por lo tanto, el sistema de detección instalado en la máquina debe ser capaz de soportar cortes de energía. Además, los dispositivos de supervisión deben ser independientes de la herramienta de corte utilizada y asequibles para la empresa.
Para el propósito definido en el proyecto FIDATU, se están analizando diferentes alternativas entre las soluciones que pueden ofrecer los principales proveedores de tecnología. En este sentido se están considerando tecnologías basadas en sensores piezoeléctricos, galgas extensométricas, capacitivos, etc. Los seleccionados serán puestos a prueba, para evaluar cualitativa y cuantitativamente, la capacidad de cada tipo de sensor para representar las fuerzas reales de torneado, en comparación con el estado del arte actual en equipos de laboratorio para ensayos de mecanizado [G2]. Para el informe final del estudio de viabilidad se evaluarán distintos aspectos, como la conectividad inalámbrica, la deriva de la señal, la sensibilidad, la miniaturización, la integración en la máquina, la capacidad de mantenimiento, la escalabilidad y la industrialización.
1.2. Torno vertical de carro transversal TV-1500 de Danobat
El ahorro de material es una preocupación importante en los procesos de fabricación, sobre todo cuando se trata de materiales caros como las superaleaciones utilizadas en el sector aeronáutico. La fabricación con forma ultra neta (UNNS) es un método para abordar este problema, en el que la geometría de mecanizado inicial o pieza en bruto se ajusta, lo más posible, a su forma final, minimizando la necesidad de un mecanizado extenso o la eliminación de material. Sin embargo, el acabado de estos componentes plantea retos debido a su variabilidad, a las tensiones residuales desconocidas y al limitado conocimiento científico de su comportamiento, por lo que se están realizando esfuerzos para comprender la evolución de las tensiones residuales durante el mecanizado y optimizar las estrategias de mecanizado [D2]. Las nuevas líneas de investigación se centran en la construcción de modelos para predecir las deformaciones que puede sufrir la máquina en función de datos preliminares procedentes de ensayos END o ensayos DT [D1].
En este sentido, la Danobat TV-1500 es una construcción robusta que combina precisión y versatilidad para permitir un rendimiento de mecanizado eficiente en el torneado de piezas grandes gracias a su configuración de carro transversal que permite el mecanizado de geometrías complejas con la máxima precisión. Cuenta con un potente husillo y un cambiador automático de herramientas que permite realizar transiciones de herramientas sin problemas durante las operaciones más exigentes. En particular, incorpora un mecanismo de doble RAM para mejorar la eficacia de arranque de viruta y la estabilidad durante el proceso de torneado en duro. Además, se ha integrado en la máquina un sistema de computación de bordes para facilitar el análisis, la organización y la clasificación basada en la nube de estos datos.
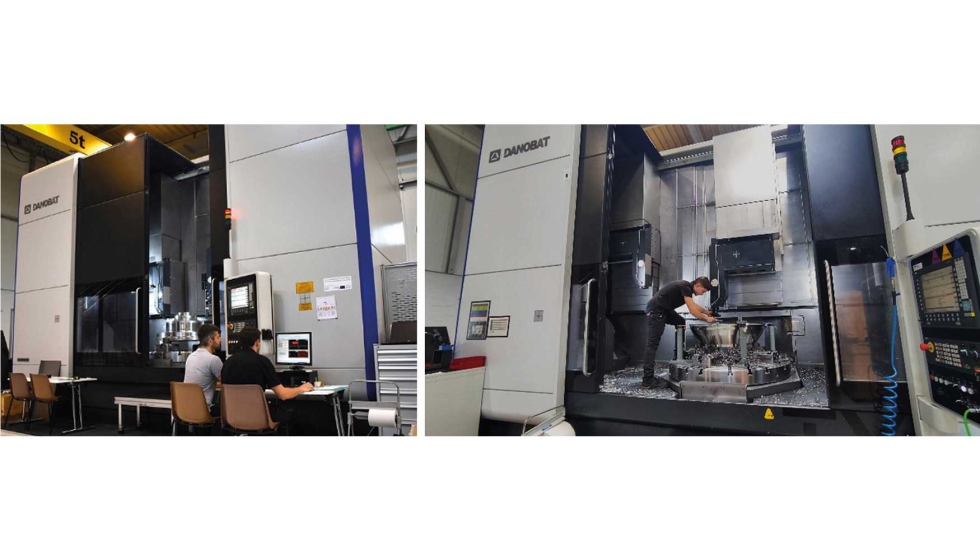
- Líneas de investigación: proyecto CORTEX
En el CFAA estamos llevando a cabo un proyecto denominado CORTEX (ZE-2022/0029) financiado por el Gobierno Vasco ‘HAZITEK 2022’, que aborda el problema de los campos de tensiones residuales desconocidas en componentes fabricados a partir de preformas UNNS. El objetivo principal de este proyecto es establecer una metodología fiable para medir las tensiones residuales en geometrías de pieza iniciales resultantes de procesos primarios como la forja o la fundición. Estos datos se utilizarán después para predecir cómo se deformará la pieza durante las operaciones de mecanizado posteriores.
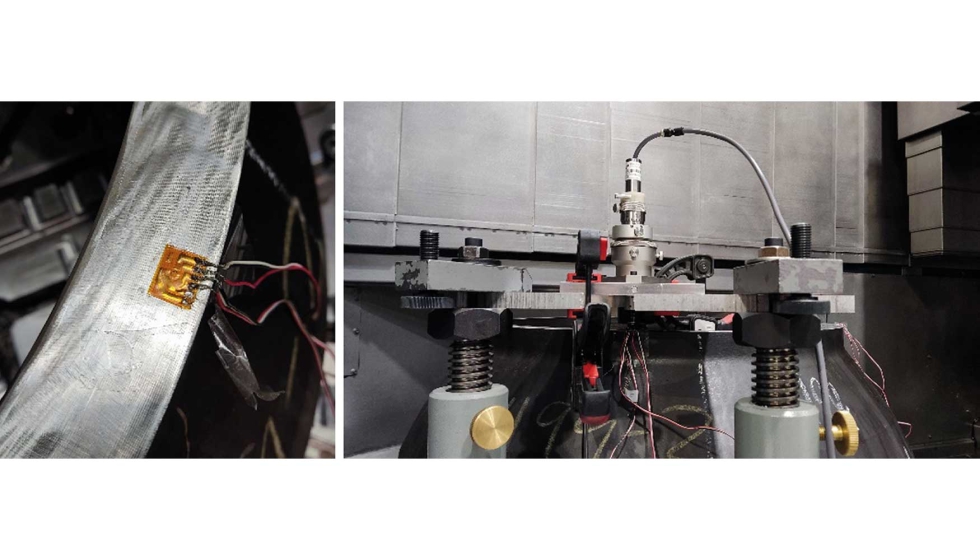
Aunque los programas informáticos numéricos pueden ofrecer información sobre las posibles deformaciones en función de la rigidez de la pieza y la fijación, la creación de un modelo predictivo de deformación requiere ensayos de calibración para predecir con exactitud la distribución de tensiones en toda la geometría. En este caso, se aplican operaciones de taladrado para obtener algunos datos iniciales del estado tensional residual de la preforma, realizadas antes y después de la operación de mecanizado, para mostrar cómo influye el proceso de mecanizado en el estado tensional.
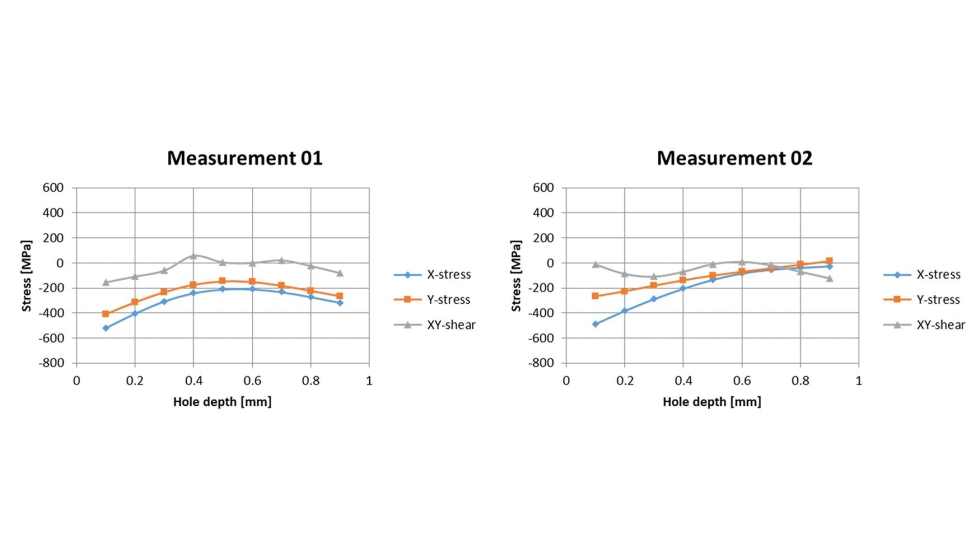
Además, para validar los datos obtenidos, se propone una prueba experimental reducida del proceso de torneado de la carcasa. Mediante el mecanizado y la extracción de un anillo, se mide su deformación a lo largo del proceso utilizando una sonda. Esto se hace para observar cómo, a medida que se extrae el material, la pieza se deforma en la dirección medida, confirmando así la tendencia.
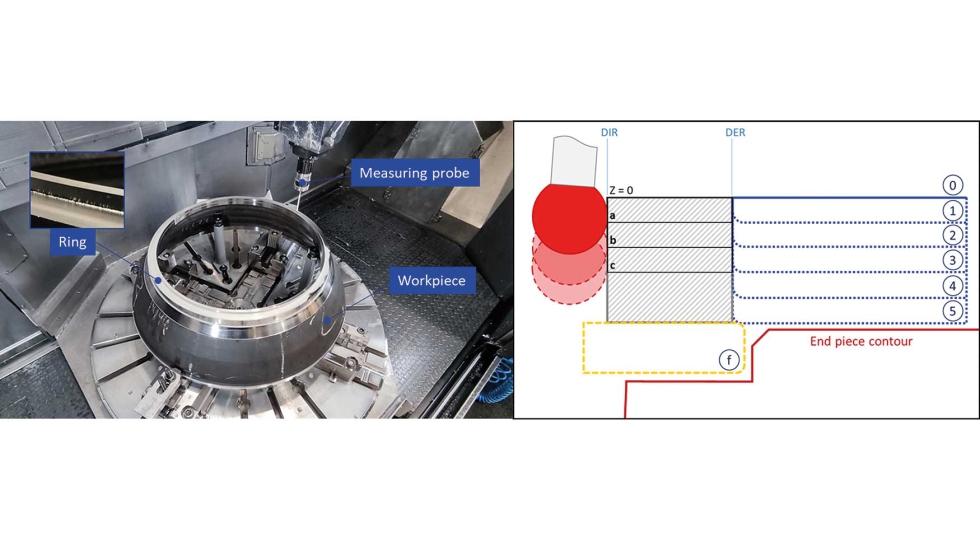
Se trata de múltiples métodos que podrían aplicarse para garantizar la medición óptima de las tensiones residuales iniciales en una pieza y comprender su influencia en la deformación cuando la pieza se suelda al útil. Detectar las tensiones residuales y cuantificar con precisión las inducidas por el mecanizado es crucial para evitar errores causados por deformaciones. Es importante reconocer que estas tensiones pueden mitigarse a menudo mediante un diseño adecuado de la fijación y estrategias de mecanizado.
1.3. Centro de mecanizado multitarea THR 16 Multiproceso de Ibarmia
La creciente competitividad en la fabricación de herramientas de corte para mecanizado ha experimentado un crecimiento exponencial. La combinación del material (sustrato), el recubrimiento, la macrogeometría y el filo de corte son parámetros fundamentales para conseguir un buen rendimiento de las herramientas de corte. Esto adquiere especial relevancia en las herramientas de metal duro para el mecanizado de materiales difíciles de mecanizar, como los aceros inoxidables y los aceros de alto rendimiento. Los primeros presentan una elevada ductilidad con una dureza que dificulta el mecanizado, mientras que los segundos son generalmente aceros aleados y/o templados con una elevada dureza y resistencia a la abrasión, lo que se traduce en una vida útil de la herramienta especialmente corta. Concretamente, estos aceros se utilizan principalmente en la industria de la valvulería, especializada en Petróleo y Gas a través de dos vías. Por un lado, el acero inoxidable se utiliza
principalmente para la fabricación de válvulas propiamente dichas (racores, manguitos, cruces, válvulas, etc.), y los aceros de alto rendimiento, que generalmente son aceros al carbono aleados y templados, se utilizan para fabricar moldes y utillajes para la obtención de válvulas. En este contexto, las herramientas de metal duro necesitan demostrar un rendimiento óptimo, que se consigue mediante la combinación adecuada de sustrato y recubrimiento, para lograr aumentos de productividad en los procesos de mecanizado que justifiquen su uso [I2].
En este sentido, Ibarmia THR 16 Multiprocess es un centro de mecanizado de 5 ejes muy versátil y avanzado que combina operaciones de fresado y torneado. Su husillo principal cuenta con una potencia de 74 kW, mientras que el motor de par de la mesa (eje C) alcanza los 70 kW, lo que permite una alta velocidad de rotación para las operaciones de torneado. Con su cambiador de herramientas automatizado integrado, facilitado por un robot antropomórfico, el cambio de herramientas se realiza de forma fluida y eficaz. Además, un cabezal angular permite realizar operaciones de mecanizado incluso en ángulos y orientaciones difíciles. Esta máquina repleta de funciones ofrece un posicionamiento preciso, repetibilidad y un control fácil de usar, lo que permite a los fabricantes lograr una precisión y productividad excepcionales en sus procesos de mecanizado.
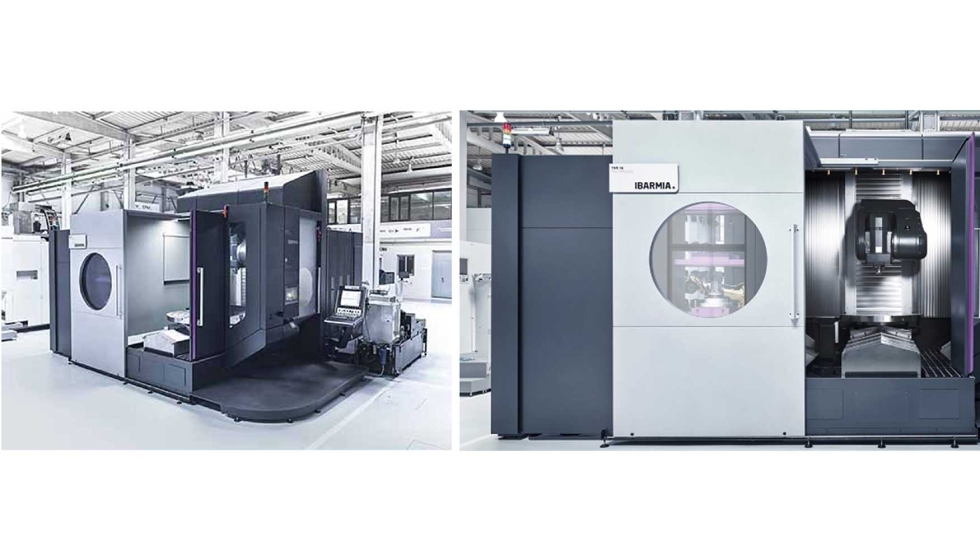
- Líneas de investigación: proyecto GENESIS
En el CFAA, junto con Izar Tool y Oerlikon, empresa de recubrimientos, estamos llevando a cabo un proyecto denominado GENESIS (ZL-2023/00229) financiado por el Gobierno Vasco, que tiene como objetivo generar 5 nuevos productos totalmente optimizados y orientados a mejorar la productividad del mecanizado de aceros inoxidables y de altas prestaciones en el sector Oil & Gas. No sólo desde un punto de vista tecnológico sino también medioambiental. Para conseguirlo, se están evaluando diferentes combinaciones de sustratos y recubrimientos avanzados para satisfacer las demandas de estos aceros. Además, se está evaluando el uso de CO2 como fluido de corte con el objetivo de controlar el impacto medioambiental del uso de la herramienta. Se están realizando pruebas exhaustivas de fresado en condiciones de corte extremas para determinar la combinación ideal de parámetros de la herramienta para un mecanizado competitivo de aceros difíciles de mecanizar. Además, para obtener productos más competitivos desde el punto de vista técnico, se está analizando la posibilidad de aplicar refrigeración criogénica para reducir la huella medioambiental durante la vida útil de la herramienta. Los resultados están demostrando cómo productividad y sostenibilidad son conceptos interconectados, donde el incremento de uno no compromete la optimización del otro [I1].
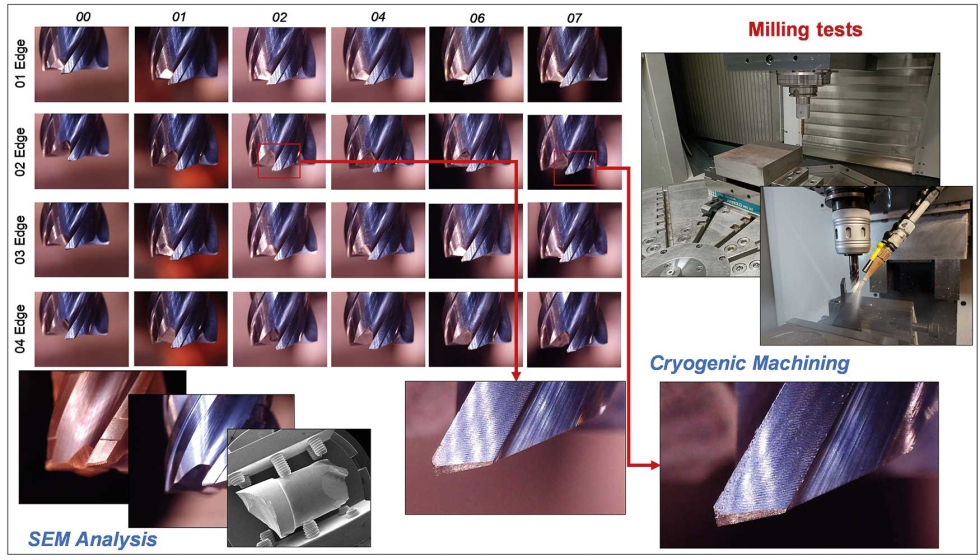
Evolución del desgaste de la herramienta con refrigeración criogénica de CO2.
1.4. Mazak Integrex i-200 Centro de torneado multitarea
Aumentar el rendimiento de los motores de las aeronaves y reducir su impacto medioambiental es un objetivo importante dentro del sector aeronáutico. Un aspecto clave para mejorar la eficiencia de los motores es mejorar la relación de compresión del aire y reducir el peso de los componentes. Esto requiere un rediseño exhaustivo de los componentes, en particular del compresor, y conlleva varias etapas críticas, como la creación de prototipos, la fabricación, la realización de pruebas rigurosas y las fases posteriores de validación, integración y producción [M1]. Además, se hace especial hincapié en la fabricación y medición de componentes aerodinámicos ligeros del compresor diseñados específicamente para bancos de pruebas. Estos esfuerzos pretenden optimizar el rendimiento de los motores, reducir el consumo de combustible y minimizar las emisiones, contribuyendo así a una industria aeronáutica más sostenible y eficiente.
En esta línea, el centro de torneado multitarea Mazak Integrex i-200 es una máquina avanzada y versátil que combina a la perfección las capacidades de las operaciones de torneado y fresado. Con cabezal giratorio y eje B, permite un mecanizado preciso en varios ángulos y orientaciones, ampliando las posibilidades de mecanizado de geometrías. Con su funcionalidad multieje y el acoplamiento del contrapunto (0,1 - 0,7 kN), este centro de mecanizado ofrece una mayor eficacia en la producción de piezas complejas y precisas. Equipado con un avanzado sistema de control CNC (Mazatrol), cambiadores automáticos de herramientas y husillos de alta velocidad (cabezal de fresado de 12.000 rpm), garantiza un posicionamiento preciso, cambios de herramientas sin interrupciones y velocidades de mecanizado aceleradas. En particular, la capacidad de mecanizado simultáneo en 5 ejes reduce la necesidad de múltiples configuraciones, lo que aumenta significativamente la productividad.
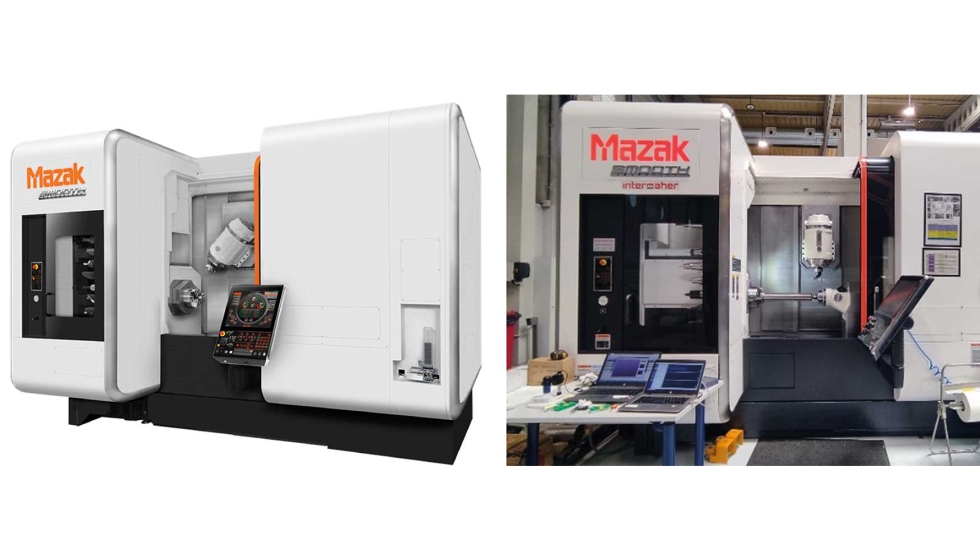
- Líneas de investigación: proyecto TASTE
El CFAA participa actualmente en un proyecto de I+D denominado TASTE: Techniques for new geared turbofan (RTC2019-007194-4), financiado por el Ministerio de Ciencia e Innovación y la Agencia Estatal de Investigación de España ((MCIN/ AEI/10.13039/501100011033/)). Este proyecto se enmarca dentro de la convocatoria ‘Retos Colaboración 2019’. El objetivo de TASTE es mejorar la eficiencia del motor reduciendo el peso de los componentes del compresor y optimizando sus prestaciones aerodinámicas. Por lo tanto, es necesario realizar varias pruebas a la hora de ensayar diferentes prototipos. Desde el punto de vista de la fabricación, el reto de los prototipos suele ser la reducción de las tolerancias debido al escalado de la geometría para un número reducido de elementos.
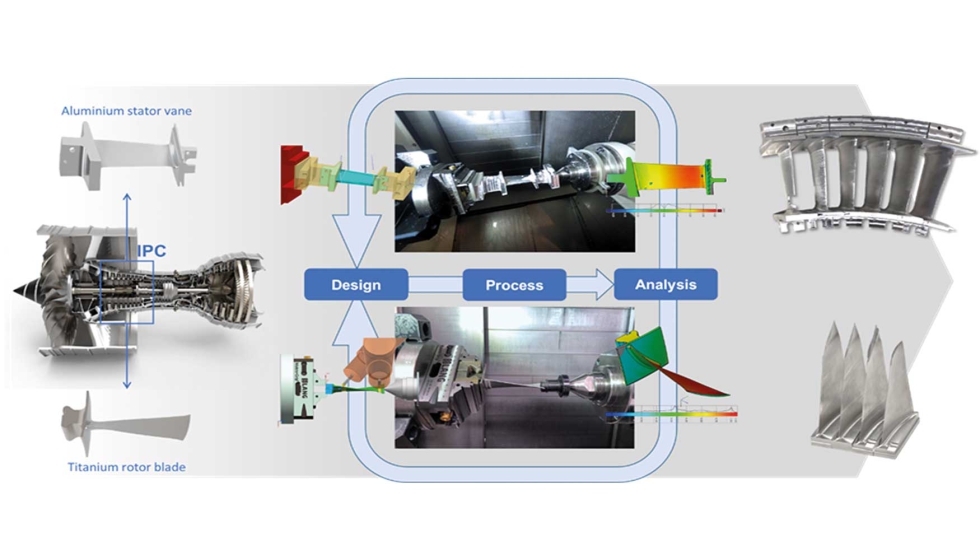
En el centro de mecanizado Mazak se está desarrollando el proceso de mecanizado de dos tipos de componentes de compresores: álabes giratorios de titanio y paletas de estator de aluminio. La atención se centra principalmente en el perfil aerodinámico, ya que representa la característica principal de estos componentes, lo que exige requisitos estrictos en este ámbito. La intrincada geometría de la superficie y las delicadas paredes delgadas plantean retos que exigen un control preciso de las vibraciones y la generación de trayectorias durante el proceso de mecanizado [M2]. El CFAA participa activamente no sólo en el perfeccionamiento del proceso de fabricación de estos componentes específicos, sino también en el desarrollo de una metodología robusta que pueda aplicarse a componentes similares en el futuro.
1.5. Banco de pruebas de brochado electromecánico EKIN A218/Rashem
Una de las operaciones críticas en la fabricación de motores aeronáuticos es el mecanizado de los discos de turbina. El proceso de brochado se emplea para crear ranuras ‘abeto’, que aseguran la fijación de las palas a la periferia del disco. Estas ranuras deben cumplir requisitos exigentes en cuanto a precisión e integridad de la superficie para garantizar el buen funcionamiento de la turbina. Las superaleaciones de níquel y cobalto son materiales de uso común debido a sus excelentes propiedades mecánicas, que dificultan el proceso de fabricación y requieren medidas especiales para mejorarlo [B1]. Para garantizar la funcionalidad y la calidad de los componentes, las empresas recurren a una supervisión intensiva para detectar cualquier perturbación en el proceso a través de los datos obtenidos.
En el CFAA hay un banco de pruebas especializado para el proceso de brochado externo, que utiliza un disco de Ø400-500 mm. Este banco de pruebas tiene una capacidad de carga máxima de 70 kN y puede alcanzar velocidades de hasta 40 m/min. El soporte para brochas permite instalar un juego completo de brochas, con una longitud total de la herramienta de 2,5 m. La máquina está totalmente equipada con sistemas de supervisión, que incluyen sensores integrados e incluso un analizador de datos del codificador del motor. Estos sistemas permiten obtener distintas fuentes de datos precisos en tiempo real sobre el proceso. Además, el banco de pruebas cuenta con un microscopio USB integrado, situado en la propia máquina, que nos permite supervisar el desgaste de la herramienta durante el proceso de corte del metal. Toda esta información recopilada se organiza y clasifica antes de ser enviada a un sistema basado en la nube a través de una compleja arquitectura de datos, cuya cúspide es el dispositivo Edge Computing.
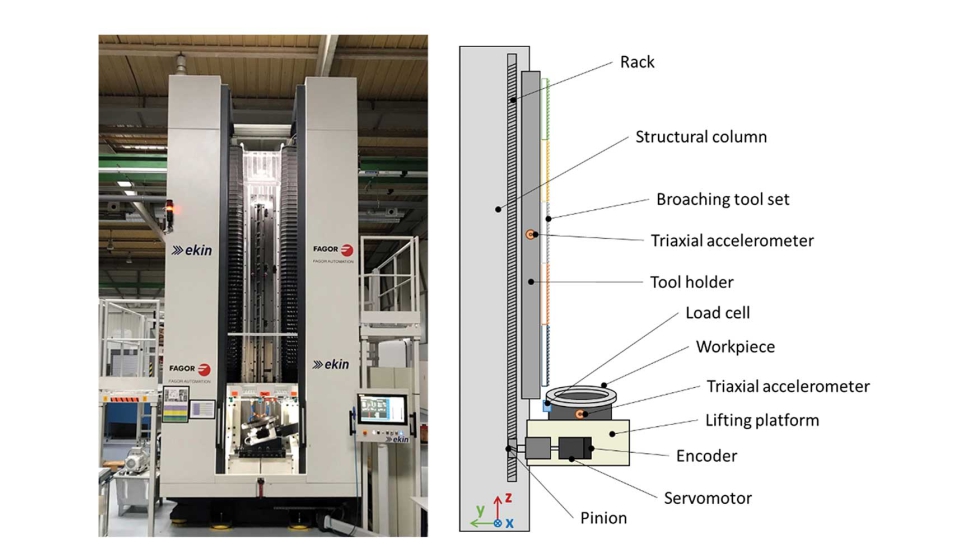
- Líneas de investigación: INTERQ
El CFAA participa activamente en el campo del brochado, en particular a través de su implicación en el proyecto europeo INTERQ, financiado por el programa Horizonte 2020 (subvención n. 958357). Este proyecto forma parte de la iniciativa Factories-of-the-Future (FoF) y tiene como objetivo dotar a las máquinas de capacidades avanzadas de ‘inteligencia’. En consonancia con este objetivo, el CFAA está desarrollando un sofisticado sistema que predice el desgaste de las brochas. Este sistema tiene el potencial de evitar el descarte de componentes valiosos que pueden producirse de forma adecuada. Se basará en la correlación de datos obtenidos de la estación de brochado, junto con la integración de dispositivos de visión artificial [B2].
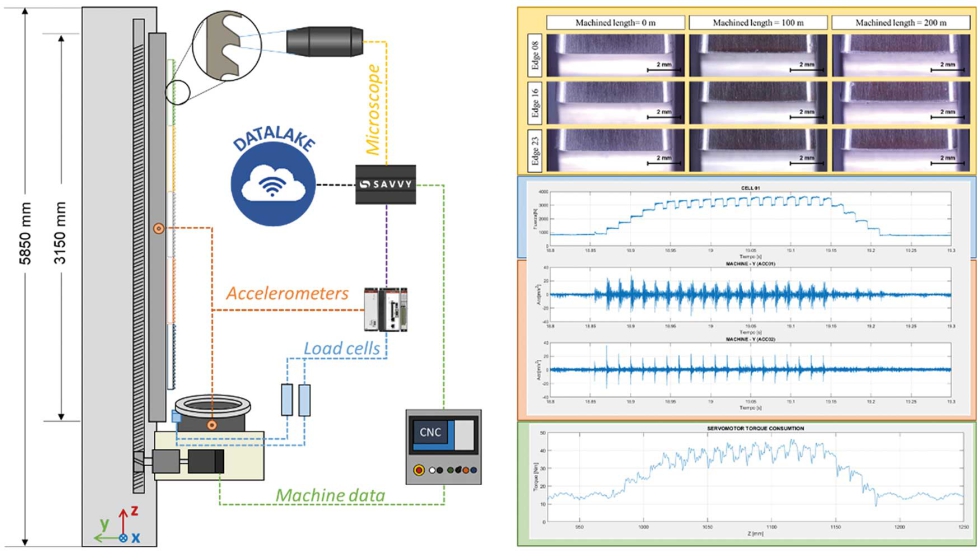
Se recogen diferentes tipos de datos a distintas frecuencias para representar el proceso de brochado. Posteriormente, se buscan relaciones significativas entre las señales adquiridas para representar con precisión el desgaste de la herramienta y de cada uno de sus dientes. A este respecto, se puede realizar una evaluación de la vida útil restante de la herramienta y se puede entrenar un modelo para predecir el estado de la herramienta al mecanizar una pieza similar del mismo material en condiciones equivalentes, lo que ayudará a reducir las piezas de desguace.
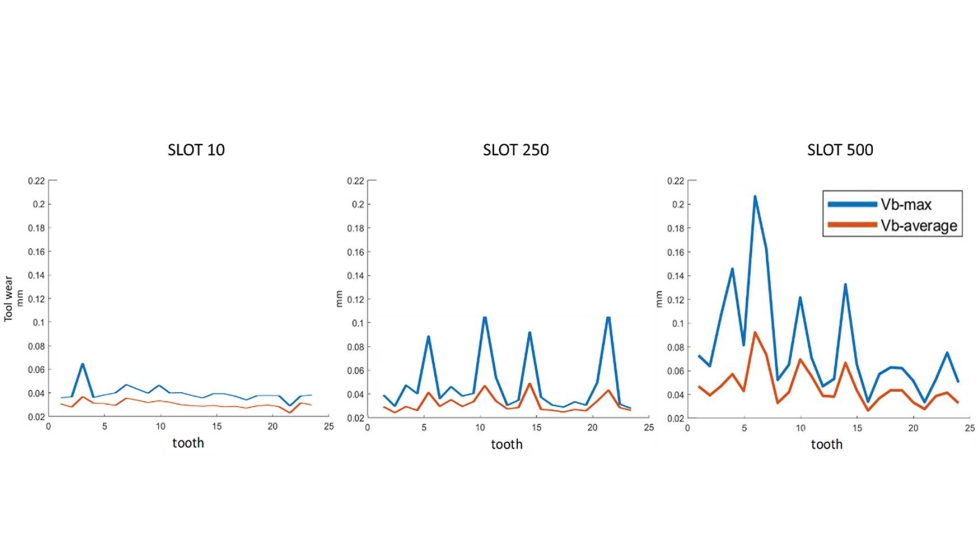
2. Procesos de mecanizado por descarga eléctrica
2.1. Máquina de electroerosión por hilo ONA AV35
Las máquinas de electroerosión por hilo son famosas por su capacidad para alcanzar altos niveles de exactitud y precisión en la producción de piezas intrincadas y complejas manteniendo tolerancias muy ajustadas. Sin embargo, se enfrentan a ciertos
retos durante el proceso de mecanizado. Uno de estos retos es la rotura del hilo, que puede mitigarse encontrando los parámetros óptimos para evitarla [W1]. Además, la obtención de los acabados superficiales deseados en las piezas mecanizadas puede ser un reto debido a factores como las fluctuaciones de la descarga eléctrica y la vibración del hilo, lo que hace necesario optimizar los parámetros de corte y las técnicas de acabado superficial [W2]. Para hacer frente a estos retos se requiere una investigación continua, avances en el diseño de máquinas, optimización de procesos y la integración de tecnologías emergentes.
ONA AV35 es una fresadora de vanguardia diseñada para aplicaciones de mecanizado de precisión. Con su estructura estable, generosa área de trabajo y eficaz sistema de enhebrado de hilo, permite el corte preciso de formas y contornos complejos en diversos materiales conductores. La interfaz fácil de usar de la máquina, los parámetros de mecanizado personalizables y las funciones de automatización avanzadas garantizan un manejo sencillo, cortes de alta calidad y un funcionamiento seguro (Ra 0,1 μm). El sistema automático de tensión del hilo mantiene una tensión óptima del hilo durante todo el proceso de corte, lo que da como resultado cortes uniformes y precisos (450 mm2/min).
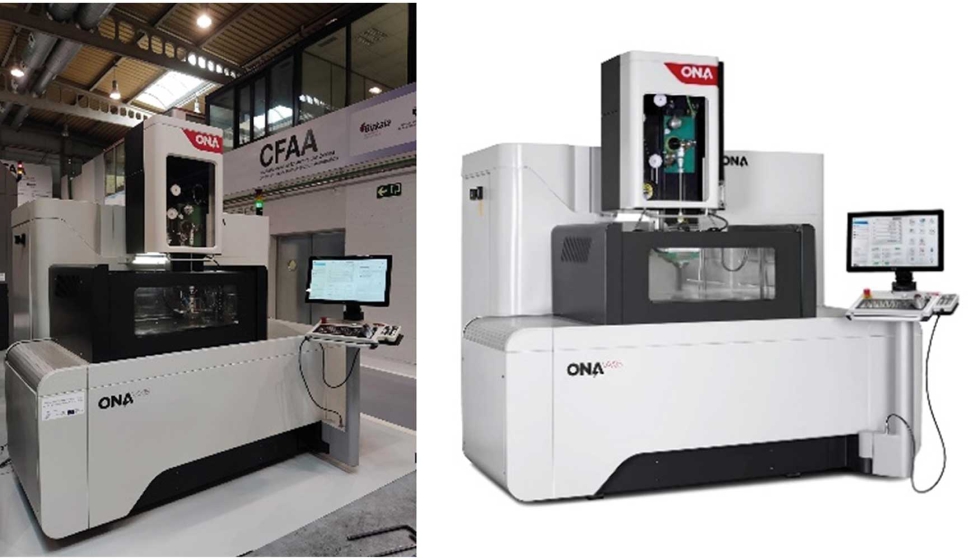
- Líneas de investigación
Uno de los principales proyectos del CFAA en el campo de WEDM forma parte del Proyecto MHAYA (MIG-20221059) de la convocatoria ‘Misiones 2022’ del CDTI. El objetivo de este proyecto es dotar a las máquinas de funcionalidades de ‘inteligencia’, para que tomen sus propias decisiones durante el proceso. En WEDM, uno de los retos es localizar el punto exacto en el que se produce la descarga a lo largo del cable. Se sabe desde hace muchos años que la localización de la descarga puede obtenerse con la relación de la corriente que pasa por el cabezal superior e inferior de la máquina, pero el mayor problema es la frecuencia ultraelevada de las descargas eléctricas.
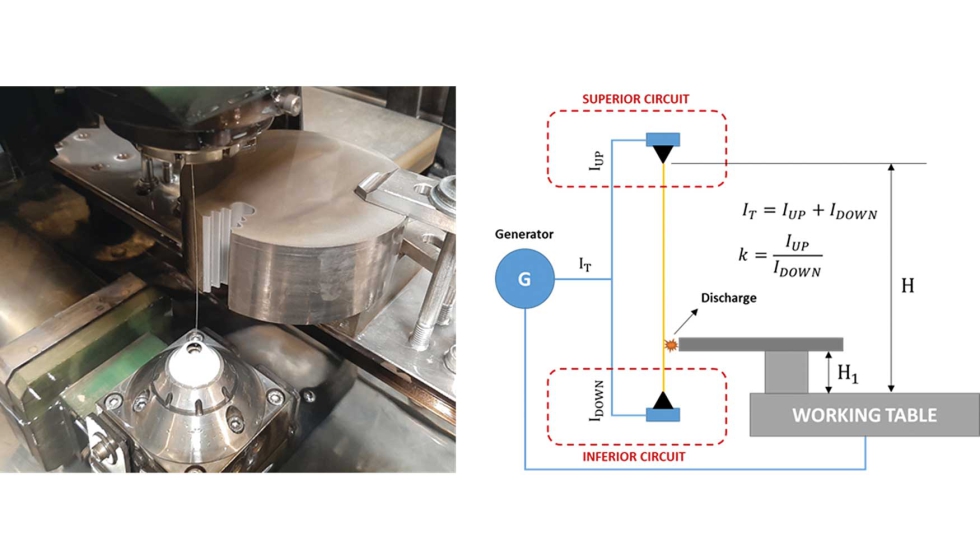
El tratamiento de estas señales en tiempo real requiere sensores y equipos específicos, así como la programación de algoritmos eficaces. Conocer la ubicación exacta del vertido mejorará el proceso en varios aspectos.
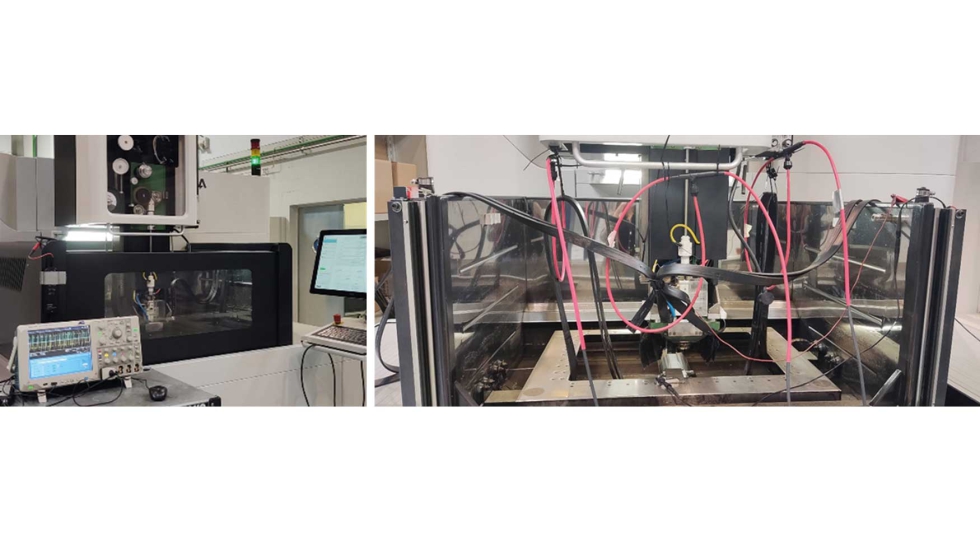
La primera es conocer la altura de corte en cada momento. En piezas de sección variable, esto es muy importante porque los parámetros de corte pueden adaptarse a cada altura automáticamente durante el corte, aumentando considerablemente la velocidad de corte. Otra mejora es aumentar la precisión de las piezas altas, ya que la acumulación de descargas a determinadas alturas puede provocar una pérdida de precisión. Si se conocen las zonas de acumulación de descargas, esto puede evitarse. Lo mismo ocurre con la prevención de la rotura del hilo, ya que también es consecuencia de una acumulación de descargas, que debilita la sección del hilo [W3]. Estas son sólo algunas de las ideas, pero el abanico de soluciones es mucho más amplio. En conclusión, trabajar en la localización de la descarga en el proceso WEDM puede repercutir en el desarrollo de máquinas con una mayor eficiencia del proceso.
3. Fabricación aditiva
La fabricación aditiva es un proceso que construye objetos capa a capa utilizando datos de diseño digital. Ofrece la posibilidad de crear geometrías complejas, reducir el desperdicio de material y permite fabricar piezas personalizadas y complejas con gran precisión. Al añadir material en lugar de restarlo, la fabricación aditiva proporciona flexibilidad y versatilidad en la fabricación de diversos componentes en todos los sectores.
3.1. Sistema de fabricación aditiva RenAM 500 de Renishaw
Las tecnologías aditivas, en concreto la fusión de lecho de polvo por láser (L-PBF), han ganado un considerable terreno en diversos sectores, entre ellos el aeronáutico, debido a su facilidad para dar forma a geometrías complejas, pero se enfrentan a varios retos para su plena implantación en la línea del proceso de fabricación: La tecnología encuentra limitaciones a la hora de fabricar componentes con propiedades mecánicas significativas debido a la presencia de porosidad estocástica durante el proceso de fundición del metal, que socava la confianza en el producto final. Detectar esta porosidad es todo un reto, incluso con métodos de inspección posterior [S1]. Por ello, los esfuerzos en curso se centran en el desarrollo de sistemas de monitorización avanzados que puedan captar señales y datos durante el proceso de fabricación para su detección. A pesar de adquirir una cantidad sustancial de datos, sigue existiendo la necesidad de interpretar e integrar eficazmente esta información en herramientas útiles, como modelos, capaces de correlacionar con precisión el proceso con las características finales de la pieza fabricada [S2].
Hay dos sistemas de fabricación aditiva de Renishaw en CFAA: El RenAM500 y el AM400.
RenAM 500 es un avanzado sistema de impresión 3D de metal que utiliza tecnología de fusión de lecho de polvo basada en láser. Con un gran volumen de construcción, láseres de alta potencia y gestión de polvo integrada, permite la producción de componentes metálicos intrincados con excelentes propiedades mecánicas. El sistema cuenta con un sistema de gas en cascada para lograr unas condiciones de procesamiento uniformes y una eliminación eficaz de las emisiones del proceso. Su sistema óptico de enfoque dinámico minimiza los tiempos de fabricación optimizando la distribución de la energía láser. El sistema incorpora sistemas integrados de gestión del polvo, supervisión avanzada y control, basados en sensores fotodiodos y software de fácil manejo para un funcionamiento eficaz y una calidad óptima de las piezas.
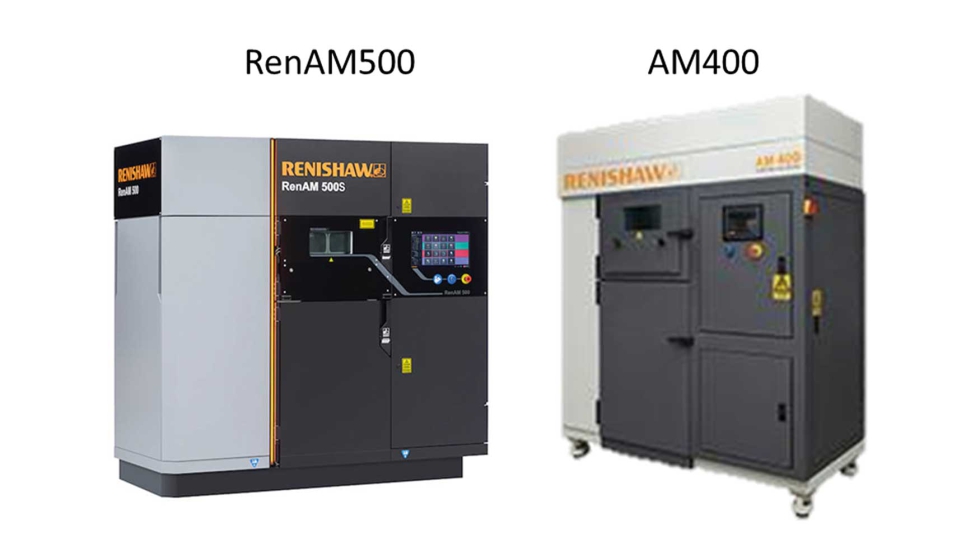
Además del sistema de supervisión, la otra diferencia significativa entre ambos sistemas es que el AM400 no dispone de un sistema de tamizado automático integrado, lo que facilita el seguimiento del lote de polvo utilizado con fines de sostenibilidad.
- Líneas de investigación
En este contexto, uno de los principales proyectos llevados a cabo en el CFAA relacionados con esta problemática en el campo de la fabricación aditiva es el proyecto denominado EDISON (KK-2022/00070) de la convocatoria ‘ELKARTEK 2022’ del Gobierno Vasco. El objetivo de este proyecto es establecer una correlación entre las señales detectadas por sensores fotodiodos y la presencia de porosidad en la pieza final fabricada. Para ello se explorarán diferentes técnicas de programación que permitan generar una porosidad controlada en la pieza que permita un correcto etiquetado de los datos.
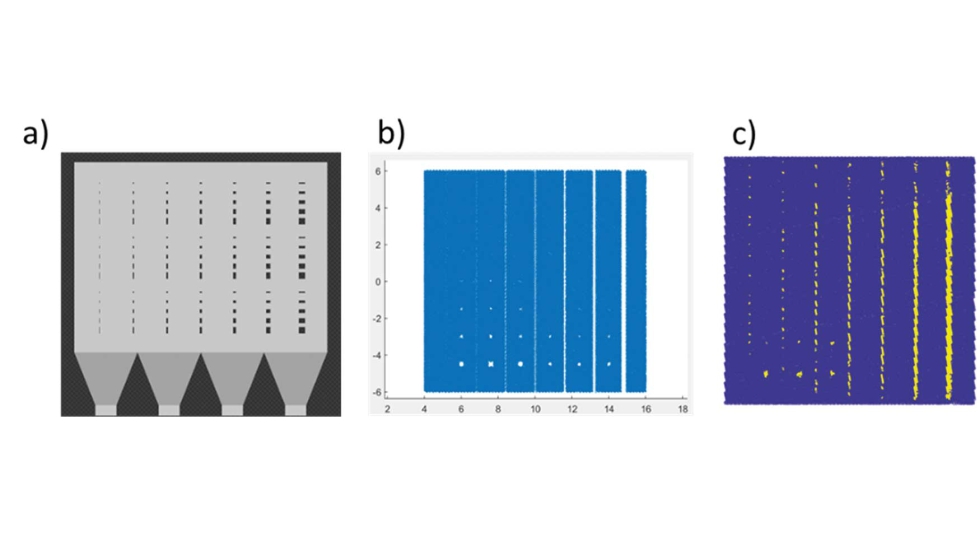
Las pruebas se realizaron con la RenAM500, que está equipada con un sistema de monitorización formado por tres fotodiodos. El primer fotodiodo capta la potencia del láser en tiempo real durante el proceso de fabricación aditiva, mientras que el segundo se encarga de detectar las señales visibles, concretamente las chispas que puedan producirse durante el proceso. Por último, el tercer sensor está diseñado para detectar la señal infrarroja, estrechamente relacionada con la temperatura del baño de fusión. Estos fotodiodos captan continuamente señales a una frecuencia de 50.000 Hz, lo que permite registrar una gran cantidad de datos del proceso. La información extraída de estos experimentos permite entrenar diversos modelos de aprendizaje automático para detectar automáticamente defectos mediante algoritmos de clasificación supervisados. Analizando las señales de los sensores junto con los defectos introducidos deliberadamente, los modelos pueden aprender a identificar patrones y características asociados a las piezas defectuosas. Este proceso de entrenamiento facilita el desarrollo de algoritmos robustos de detección de defectos que pueden aplicarse en entornos de fabricación en tiempo real.
Otras tecnologías
Un aspecto muy importante en la fabricación mecánica es la verificación final de las piezas fabricadas. Tan importante como producir es asegurar que está bien producido. En el nuevo centro no tendría sentido no contar con las más modernas máquinas de metrología, que permitirían la medición de aquellas dimensiones funcionales, como longitudes, ángulos, tolerancias geométricas y acabados superficiales, que permiten validar un proceso de fabricación de piezas, aún más importante cuando se trata de niveles de LMR tan elevados, muy cerca de la pieza final.
El sector impulsor de la CFAA es el aeronáutico. En este sector, estas limitaciones de fabricación son aún más evidentes, exigiendo unos requisitos de calidad superiores a los de cualquier otro mercado industrial como la automoción o el sector energético.
Por ello, el nuevo centro contará con dos máquinas de medición de coordenadas de cinemática cartesiana de la empresa Mitutoyo, una de ellas para mediciones con contacto y la otra para mediciones sin contacto:
- Mitutoyo Crysta Apex C162012: es el más grande, y montará una sonda de contacto rápido Revo de Renishaw para medición de 5 ejes con contacto. Esta sonda permite trazar una trayectoria continua alrededor de componentes geométricamente complejos.
- Mitutoyo Crysta Apex S 9106: Una máquina más pequeña que incluirá un cabezal de exploración y un raster láser. Ambas máquinas fueron suministradas por Metrología Sariki.
Por otro lado, las amplias exigencias de control sobre los procesos de fabricación y los requisitos de calidad a cumplir por los componentes aeronáuticos requieren la aplicación de rigurosos controles de sus procesos con el fin de obtener un control total sobre los mismos. En este escenario, es vital el uso de sistemas de inspección para controlar la integridad de la pieza. La figura 18 muestra una verificación de un engranaje espiral producido en CFAA en fresado de cinco ejes. Se aplicaron tres estrategias de inspección a lo largo de la trayectoria de inspección en tres superficies de un engranaje cónico en espiral. La estrategia variable y la optimizada 3+2 tuvieron un rendimiento bastante similar. La estrategia de 3 ejes obtuvo resultados considerablemente peores. Tomando como referencia la estrategia de 5 ejes, se calcularon los errores de desviación dimensional cometidos por la estrategia propuesta y la de 3 ejes.
En cuanto a la tomografía, GE X-Cube Compact 225 (Trimek) dispone en el CFAA de una estación de radiografía digital en la que es posible realizar escaneos 3D en componentes que hayan sido sometidos a alguna operación como soldadura, microfresado o fabricación aditiva entre otras, así como la detección de posibles defectos asociados a cada proceso de fabricación. Esta estación tiene un volumen de inspección de 600 x 900 mm y un peso máximo de pieza de 100 kg con una potencia de 195 kV.
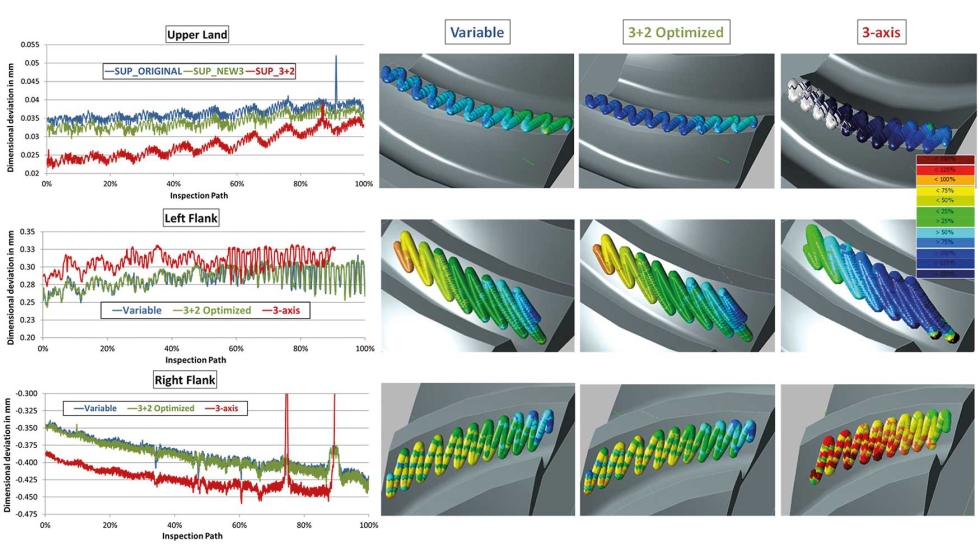
Figura 19: Verificación rápida de engranajes tras el fresado en cinco ejes con doble contacto.
Conclusiones
La evolución de los centros de mecanizado ha sido un viaje extraordinario, impulsado por la necesidad constante de mejorar la precisión, la productividad, la flexibilidad y la automatización de los procesos de fabricación. Desde la temprana integración de la tecnología CNC hasta los avances en las capacidades multieje y el mecanizado de alta velocidad, los centros de mecanizado han ampliado continuamente los límites de lo que es posible en el mecanizado de metales. La demanda de geometrías complejas, velocidades de arranque de material más rápidas y tiempos de preparación reducidos ha impulsado el desarrollo de centros de mecanizado de 5 (o más) ejes y la integración de automatización y tecnologías inteligentes.
A medida que la Industria 4.0 sigue configurando el panorama de la fabricación, la necesidad de centros de mecanizado se ha ampliado aún más. Además de conectividad, análisis de datos y capacidades de supervisión en tiempo real, existe una creciente demanda de robustez en las máquinas. Se espera que los centros de mecanizado minimicen las vibraciones y mantengan la estabilidad durante el funcionamiento, garantizando unos resultados de mecanizado uniformes y precisos. Además, la capacidad de intervenir en el funcionamiento y autoajustarse en función de los datos recogidos mediante sensores integrados es cada vez más importante. Esta capacidad permite a los centros de mecanizado adaptarse a las condiciones cambiantes, optimizar el rendimiento y maximizar la productividad. Mediante la combinación de conectividad, análisis de datos, supervisión en tiempo real y robustez, los centros de mecanizado están equipados para afrontar los retos de la fabricación moderna, proporcionando soluciones de mecanizado de alto rendimiento fiables y eficientes.
Centro de Fabricación Avanzada Aeronáutica, CFAA, en Bilbao, donde colaboran Máquina-Herramienta y Aeronáutica
Una visita a las nuevas instalaciones del CFAA (Centro de Fabricación Avanzada Aeronáutica), en el parque tecnológico de Bizkaia, cerca de Bilbao (País Vasco), pone de manifiesto la colaboración entre los fabricantes de máquina-herramienta y las empresas Tier 1 y 2 del sector de los motores aeronáuticos. Los primeros se encargan de investigar nuevos procesos y desarrollar máquinas-herramienta especialmente adaptadas para mejorar la productividad, la calidad y la precisión, mientras que las segundas trabajan en el desarrollo de nuevos motores.
El CFAA se inauguró en 2017 con el objetivo de desarrollar tecnologías de fabricación avanzada y trabajar en torno a los niveles de preparación para la fabricación (MRLs 5-7). La apuesta conjunta entre la agrupación de empresas aeronáuticas y el sector de máquina-herramienta del País Vasco, con la iniciativa del Departamento de Desarrollo Económico e Infraestructuras del Gobierno Vasco y la Diputación Foral de Bizkaia, más
la Universidad del País Vasco, ya está cosechando sus frutos. El CFAA es un nuevo modelo diseñado para fomentar las relaciones entre empresas de dos sectores y en el eje universidad-empresa. La asociación española AFM también contribuye a promover el centro y sus funciones, ya que las máquinas, las herramientas, los servicios y el talento son elementos básicos del CFAA. Además, varios miembros de AFM son socios activos del CFAA.
Actualmente hay 109 empresas asociadas. Entre ellas se encuentran ITP Aero (desarrollador y fabricante de turbinas) y Danobat Group como socios principales, que trabajan en colaboración con Ibarmia, ONA Electroerosión, GMTK, Intermaher-Mazak, Trimek, Sariki, Fagor Automation, Renishaw, Ekin, EIPC, Metalúrgica Marina, Mesima, Fresmak, Wolco, Nippon Gases, Ceratizt, Metal Estalki e Izar, entre las principales. El compromiso de los socios incluye la realización de proyectos en el centro y la colaboración con otros, con sus correspondientes gastos.
Con esta idea como marco del centro, la misión del CFAA puede resumirse así:
- Fomento de la investigación y el desarrollo en colaboración en el campo de las tecnologías de fabricación aeronáutica.
- Realización de actividades que permitan una rápida transferencia de resultados al entorno productivo asociado a la cadena de valor. Su actividad se clasifica entre TRL 5 y 7 en la escala de la NASA (pilar 2) con respecto a la proximidad a la aplicación final.
- Atraer iniciativas innovadoras en el campo de la fabricación aeronáutica avanzada que puedan desarrollar y generar una nueva red industrial regional o reforzar la estructura existente.
- Desarrollar proyectos de fabricación avanzada que integren y focalicen los recursos de los socios y aprovechen los recursos y el know-how generado por los socios de la Red Vasca de Ciencia, Tecnología e Innovación.
- Ser un centro de referencia para proveedores de equipos y fabricantes del sector aeronáutico con el objetivo de lanzar su participación como socios en proyectos de desarrollo de procesos de fabricación avanzada y aportar sus equipos y know-how. El sector de la máquina-herramienta es clave en las soluciones y muchas empresas españolas y extranjeras son miembros.
- Aprovechar la sinergia de la universidad, las empresas y las instituciones, centrando los esfuerzos en el desarrollo de la I+D+i, las actividades formativas orientadas a tecnologías de interés para las industrias vascas y las competencias científico-tecnológicas en el ámbito de la fabricación avanzada.
Ya se han realizado más de 600 proyectos, con una tasa de transferencia muy elevada, a fabricantes tanto de componentes de turbinas como de máquinas herramienta. En general, pueden clasificarse en los siguientes grupos:
- Procesos de mecanizado de alto rendimiento, que incorporan conceptos de mecanizado multieje, multiárea, de precisión y de alta velocidad. La mitad del centro y la mitad del negocio de las turbinas es el mecanizado. Además, es, por supuesto, clave para los fabricantes de máquinas-herramienta de gran tamaño.
- Procesos no convencionales, como la electroerosión y el láser. Los motores son de metal, con aleaciones de níquel y titanio, lo que significa que la electroerosión es una tecnología clave.
- Fabricación aditiva de metales, tanto con técnicas LMD (deposición láser de metales) como SLM (fusión selectiva por láser). La fabricación aditiva mediante SLM es clave para reducir el peso gracias a los cambios de diseño que permite este tipo de tecnología. La agenda de la CFAA en esta línea está creciendo considerablemente; con las predicciones más optimistas, previendo que entre el 20 y el 30% de los motores se fabricarán con esta tecnología en los próximos 15 años.
- Procesos especiales de soldadura robotizada, mediante robots industriales y colaborativos.
- La inspección, la medición y los ensayos no destructivos (END) son elementos clave.
- Software CAM y fabricación virtual, el concepto de gemelo digital manual.
- Procesos de rectificado y acabado, desbarbado, cepillado, etc.
- Integración avanzada de modelos, simulación, seguimiento y predicción de resultados de procesos. En esta línea, la universidad trabaja intensamente para cumplir la tarea de mejorar la productividad y la repetibilidad de los procesos.
- Integración de la información y la digitalización, en línea con la iniciativa Industria 4.0. De hecho, el CFAA es una planta piloto para desarrollar y probar conceptos de fábrica inteligente.
También se desarrollan proyectos digitales en la Unidad especial AIMS (fabricación inteligente artificial para la sostenibilidad) en cooperación con Ideko-BRTA, BCAM a IMH campus.

El CFAA se inauguró en 2017 con el objetivo de desarrollar tecnologías de fabricación avanzada y trabajar en torno a los niveles de preparación para la fabricación.
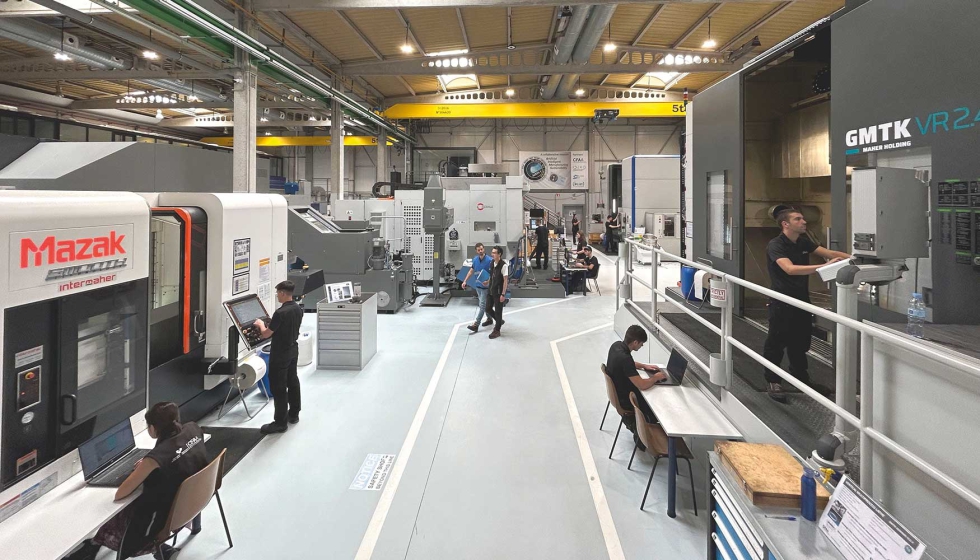
Referencias
[G1] C.H. Lauro, L.C. Brandão, D. Baldo, R.A. Reis, J.P. Davim. Monitoreo y procesamiento de señal aplicado en procesos de mecanizado - Una revisión. Medición, 58, 2014, pp 73-86
[G2] A. Siddhpura y R. Paurobally. A review of flank wear prediction methods for tool condition monitoring in a turning process. The International Journal of Advanced Manufacturing Technology 65(1-4), 2013, pp 371-393.
[D1] D. Ulutan, B. Erdem Alaca, I. Lazoglu. Analytical modelling of residual stresses in machining. Journal of Materials Processing Technology, 183 (1), 2007, pp 77-87.
[D2] Soroush Masoudi, Saeid Amini, Ehsan Saeidi & Hamdollah Eslami-Chalander. Effect of machining-induced residual stress on the distortion of thin-walled parts. The International Journal of Advanced Manufacturing Technology, 76, 2015, pp 597-608.
[I1] O. Pereira, A. Rodríguez, A.I. Fernández-Abia, J. Barreiro, L.N. López de Lacalle. Lubricación criogénica y de cantidad mínima para un torneado ecoeficiente de AISI 304. Journal of Cleaner Production, 139, 2016, pp 440-449.
[I2] Ç. V. Yildirim, T. Kivak, M. Sarikaya, S. Sirin. Evaluation of tool wear, surface roughness/topography and chip morphology when machining of Ni-based alloy 625
under MQL, cryogenic cooling and CryoMQL. Journal of Materials Research and Technology, 9(2), 2020, pp 2079-2092.
[M1] B. Li & S.N. Melkote. Fixture Clamping Force Optimisation and its Impact on Workpiece Location Accuracy. The International Journal of Advanced Manufacturing Technology, 17, 2001, pp 104-113.
[M2] Mehrdad Givi, J.R.R. Mayer. Validation of volumetric error compensation for a five-axis machine using surface mismatch producing tests and on-machine touch probing. International Journal of Machine Tools and Manufacture, 87, 2014, pp 89-95.
[M3] Jun Zha, Nagore Villarrazo, Gonzalo Martínez de Pisson, Yipeng Li, Huijie Zhang & Luis Norberto López de Lacalle. Un método de evolución de la precisión aplicado al mecanizado en cinco ejes de superficies curvas. The International Journal of Advanced Manufacturing Technology, 125, 2023, pp 3475-3487.
[B1] P. J. Arrazola, J. Rech, R. M'Saoubi, D. Axinte. Brochado: Herramientas de corte y máquinas-herramienta para la fabricación de características de alta calidad en componentes. Anales del CIRP, 69 (2), 2020, pp 554-577.
[B2] A. del Olmo, L.N. López de Lacalle, G. Martínez de Pissón, C. Pérez-Salinas, J.A. Ealo, L. Sastoque, M.H. Fernandes. Monitorización del desgaste de herramientas en procesos de brochado de alta velocidad con herramientas de metal duro para reducir errores de producción. Mechanical Systems and Signal Processing, 172, 2022, 109003.
[W1] M. Boccadoro, R. D'Amario, M. Baumeler. Towards A Better Controlled Edm: Industrial Applications of a Discharge Location Sensor in an Industrial Wire Electrical Discharge Machine. Procedia CIRP, 95 (2020), pp. 600-604.
[W2] U. Küpper, E. Tchoupe, A. Klink, T. Bergs. Prediction of Geometrical Accuracy In Wire EDM By Analyzing Process Data. Procedia CIRP, 113 (2022), pp. 23-28
[W3] S. Caneda, I. Ayesta, J. Wang, O. Flaño, E. Perez, J.M. Ramos. Estudio de la influencia de los condicionantes industriales reales durante el WEDMroughing de abetos sobre discos de Inconel® 718. Procedia CIRP, 113 (2022), pp. 131-136.
[S1] M. Bayat, A. Thanki, S. Mohanty, A. Witvrouw, S. Yang, J. Thorborg, N. S. Tiedje, J. H. Hattel. Porosidades inducidas por ojo de cerradura en la fusión de lecho de polvo basada en láser (L-PBF) de Ti6Al4V: modelado de alta fidelidad y validación experimental. Fabricación aditiva, 30, 2019, 100835.
[S2] S. L. Sing, C. N. Kuo, C. T. Shih, C. C. Ho & C. K. Chua (2021) Perspectives of using machine learning in laser powder bed fusion for metal additive manufacturing, Virtual and Physical Prototyping, 16:3, 372-386.