AITEX desarrolla una nueva generación de honeycombs
Por ello, en el proyecto HONEYTEX 2021 se ha desarrollado una tecnología de fabricación de una nueva generación de honeycombs con una relación calidad/precio muy optimizado. Dicho proyecto ha sido subvencionado por el IVACE (Instituto Valenciano de Competitividad Empresarial).
Actualmente los honeycombs que se pueden encontrar de altas prestaciones mecánicas presentan un coste bastante elevado y los de menor precio se quedan cortos de dichas prestaciones mecánicas. Además, la mayoría de los honeycombs que se pueden encontrar a día de hoy presentan una gran dificultad de reciclado.
Por otra parte, los materiales base que forman los honeycombs son bastante limitados. Debido a esto a las empresas les es difícil la obtención de núcleos de unas prestaciones más elevadas a unos precios razonables, por lo que descartan este tipo de soluciones y adoptan materiales de núcleos más baratos como espumas, maderas, corchos, etc., que se quedan cortos de prestaciones, en según aplicaciones, o incrementan el peso del producto final.
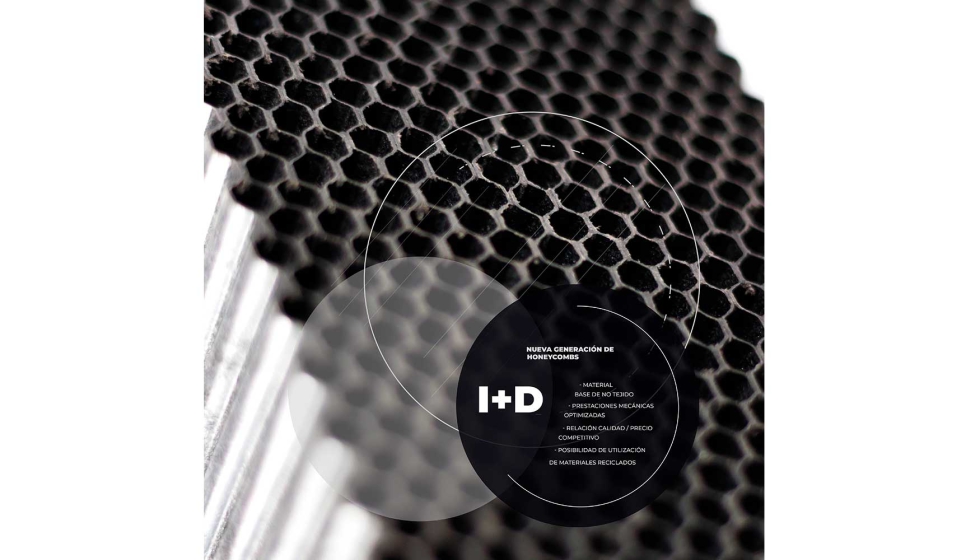
Los honeycombs que AITEX ha desarrollado en el marco del proyecto HONEYTEX 2021 presentan un rendimiento de propiedades medias altas, comparado con los honeycombs que se pueden encontrar comercialmente. Por tanto, se encuentran a término medio entre los núcleos poliméricos y de núcleos de altas prestaciones utilizados en el sector aeronáutico y aeroespacial.
En el proyecto HONEYTEX 2021 se ha realizado el desarrollo de una nueva tecnología de fabricación de honeycombs en continuo a partir de la utilización de no tejidos como base para la formación del núcleo. Esto es lo que los distingue de los honeycombs que se pueden encontrar comercialmente, representando un concepto nuevo en este sector, ya que ninguna de las tecnologías actuales de fabricación de honeycombs admite este tipo de formato no tejido. Además, la utilización de los no tejidos como base posibilita la reducción del coste del producto final, así como también proporciona la posibilidad de utilización de muy distintos materiales de refuerzo. Esto da lugar a la posibilidad de una optimización de coste/rendimiento superior a los honeycombs comerciales habituales.
Estos no tejidos base pueden presentar una composición muy variada de fibras termoplásticas (PLA, PP, PE, PET, etc.) combinadas con fibras de refuerzo (carbono, aramida, residuo textil, cáñamo, lino, etc.).
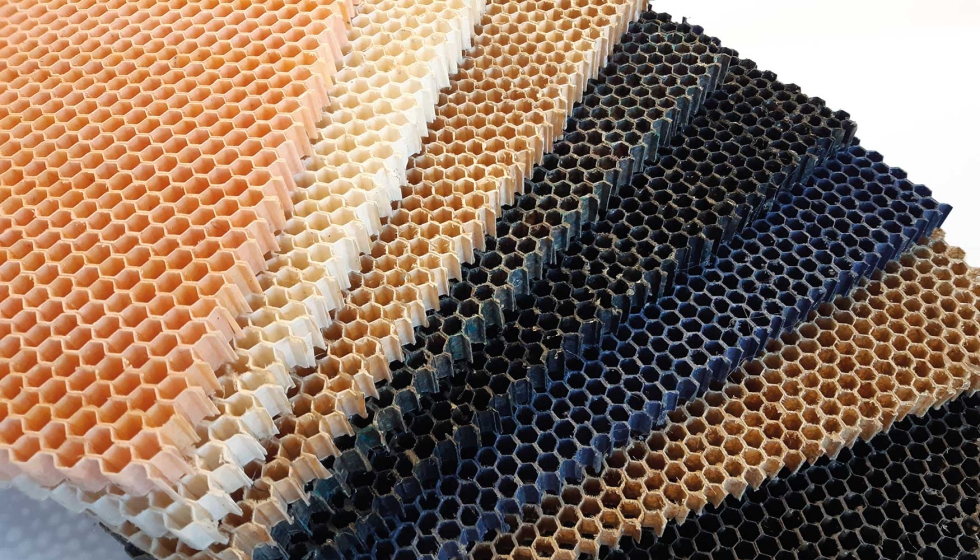
Mediante esta nueva tecnología de fabricación de honeycombs se han logrado obtener núcleos compuestos de fibras de carbono, aramida, acrílica, lino, algodón, residuo textil y bambú, combinadas con fibras de polipropileno (PP) y ácido poliláctico (PLA). Este abanico de materiales es ampliable a cualquier tipo de materia prima que se pueda utilizar (en formato fibra) para la formación de los no tejidos base. Por lo que posibilita la formación de honeycombs de muy diversos tipos de material, pudiendo optimizar la composición del núcleo a la aplicación determinada en servicio, optimizando al máximo el coste y prestaciones del honeycomb y, por tanto, del producto final.
De entre esta nueva generación de honeycombs hay que destacar el formado por fibras de carbono combinadas con fibras de PP.
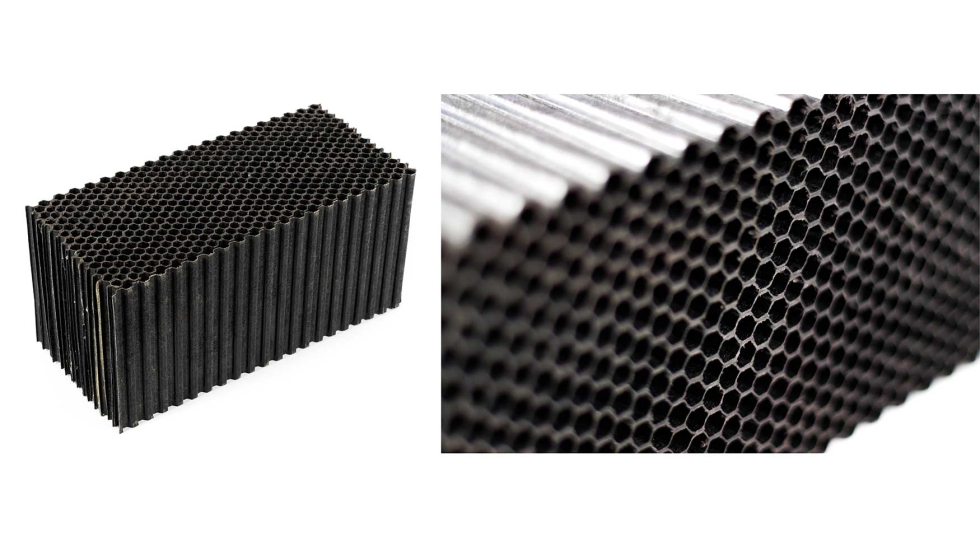
Este honeycomb de fibra de carbono y PP, comparado con los honeycombs de PP 100% de marcas comerciales, presenta las siguientes mejoras de resistencia mecánica:
- Incremento de la resistencia a la compresión del 43%.
- Incremento de la resistencia al corte: Dirección L = 52% y Dirección W = 40%.
- Incremento del módulo de corte: Dirección L = 449% y Dirección = 217%.
Esto demuestra que la utilización de no tejidos con fibras de refuerzo, como base de formación de los honeycomb, presenta una mejora sustancial de las propiedades mecánicas finales del núcleo, comparado con los comerciales de 100% polímero.
La tecnología de formación de esta nueva generación de honeycombs ha sido completamente desarrollada por AITEX. Esta tecnología consiste en procesos de termocompresión en contínuo adaptados para la formación de honeycombs de diferentes tamaños y geometrías. Pudiéndose desarrollar núcleos con diferentes espesores y tamaños de celda, por lo que la versatilidad de formación es bastante amplia. Este equipo se ha desarrollado a escala semi-industrial teniendo un ancho de formación de un máximo de 50 cm a una velocidad máxima de 10 m/min. Se ha desarrollado básicamente para la utilización de no tejidos en la formación de los honeycombs, no obstante, se pueden utilizar films de varios tipos de polímeros además de tejidos híbridos refuerzo/polímero, por lo que presenta una gran adaptabilidad de utilización de diversos materiales y formatos en una misma tecnología de formación.
Esta posibilidad amplia de utilización de materiales posibilita que se puedan utilizar tanto materiales técnicos (fibra de carbono, aramida, etc.), como materiales reciclados (residuo textil, residuo fibra carbono, etc.) y materiales naturales (fibras de cáñamo, lino, etc.). Esta amplia variedad de materiales actualmente no se puede utilizar en las tecnologías tradicionales de fabricación de honeycombs.
El coste por metro cuadrado de esta nueva generación de honeycomb puede llegar a situarse en torno al 30-70% más bajo (según composición del núcleo) que los núcleos comerciales de PP 100%, debido básicamente a la utilización de no tejidos como base de formación y a la nueva tecnología desarrollada para la formación de esta nueva generación de honeycombs.
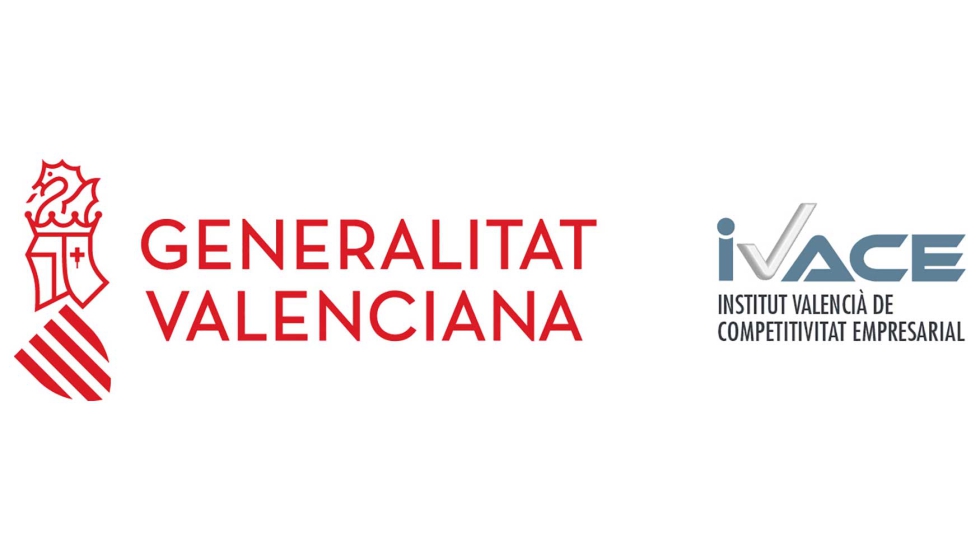