La colaboración entre GE Aviation y GE Additive está demostrando que la fabricación aditiva de metales puede competir en precio con las piezas de fundición convencionales
Ingenieros de GE Aviation y GE Additive cambian cuatro piezas existentes de fundición a impresión metálica en 3D
A la mayoría de los fabricantes nunca se les ocurriría cambiar una pieza de fundición por otra realizada mediante fabricación aditiva, especialmente si ya han pagado el molde de fundición. Sin embargo, eso es exactamente lo que está haciendo GE Aviation con cuatro piezas de aire de purga de una turbina terrestre/marina. Tomaron la decisión basándose en el coste y el tiempo de comercialización.
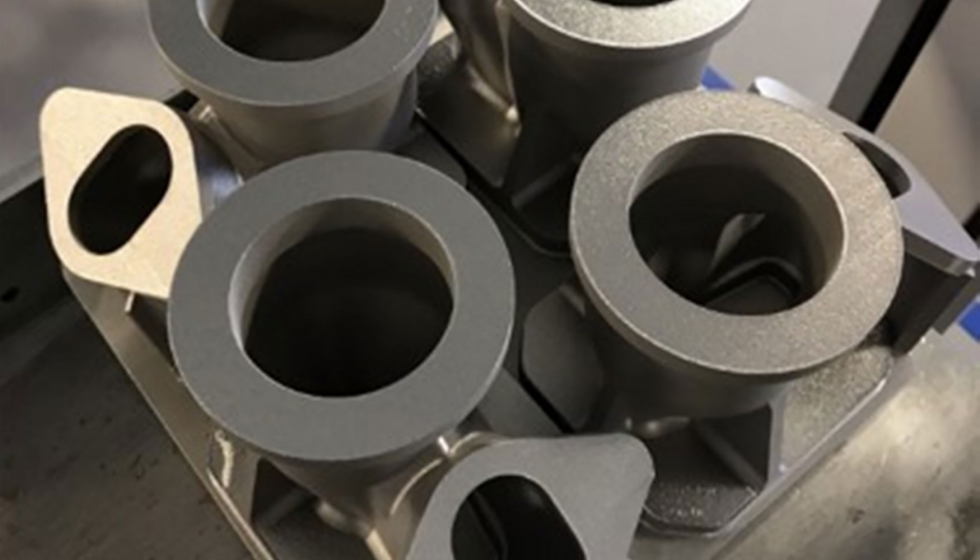
La colaboración entre GE Aviation y GE Additive está demostrando que la fabricación aditiva de metales puede competir en precio con las piezas de fundición convencionales. De hecho, el equipo de ingenieros espera que sus cuatro piezas impresas en 3D reduzcan hasta un 35% su coste. Esto es suficiente para justificar la retirada de los viejos moldes de fundición para siempre.
Y lo que es más importante, el proceso de conversión sólo llevó 10 meses desde la identificación de las piezas objetivo hasta la impresión en 3D de los prototipos finales. Normalmente, la producción de piezas de turbinas aeroespaciales y terrestres/marinas mediante un proceso de fundición lleva de 12 a 18 meses o más.
“Se trata de un cambio de juego”, dijo Eric Gatlin, jefe de Fabricación Aditiva de GE Aviation. “Es la primera vez que hacemos una sustitución pieza por pieza y resulta más barato hacerlo con aditivos que con fundición. Para asegurarnos de que demostrábamos la competitividad de los costes, pedimos a cuatro proveedores externos que cotizaran las piezas, y aun así nos salió más barato con la fabricación aditiva”.
Esto es sólo el principio. El proyecto ha identificado decenas de otras piezas en una variedad de motores que podrían convertirse con la fabricación aditiva y ahorrar costes.
Impulsar el cambio
A medida que aumentaba el número de aplicaciones exigentes, los fabricantes de equipos se esforzaban por mejorar la productividad de sus impresoras láser de metal, que construyen piezas a partir de polvos metálicos, una fina capa cada vez.

La mejora de la productividad reduce los costes, así como el tiempo de desarrollo. “Dijimos desde el principio que íbamos a elegir un material que ya habíamos calificado”, dijo Gatlin. “En producción, optamos por el M2 porque lo conocemos bien. Y no íbamos a hacer ningún cambio de diseño al por mayor, sólo algunos retoques para poder imprimir las piezas con éxito. Simplificamos todos los pasos que pudimos para que el equipo pudiera correr rápido”.
Esto permitió al equipo del proyecto desarrollar los prototipos finales entre abril y septiembre de 2020. Aunque las cuatro piezas se destinaron al LM9000, una turbina terrestre/marina derivada del turborreactor GE90, que GE Aviation está construyendo para Baker Hughes, el grupo consideró también docenas de piezas para motores y productos más antiguos.
Las empresas de aviación suministran piezas de recambio durante toda la vida útil de sus productos, explicó Joseph Moore, director del proyecto y jefe de Proyecto de GE Aviation. ¿Qué ocurre —preguntó— cuando sólo quedan unos pocos repuestos y un proveedor planea dejar de fabricar el material con el que están hechos?
“Tenemos que pensar en cómo conseguir repuestos antes de que nos quedemos sin ellos”, dijo Moore. “Tenemos que avanzar rápidamente en el ciclo de desarrollo y crear una pieza que podamos enviar. Para demostrar que podíamos hacerlo, nos pusieron un plazo y nos dijeron que hiciéramos la pieza lo más rápido y rentable posible”.
“Nuestro objetivo fue siempre buscar formas de no interrumpir la producción”, dijo Moore. “Sólo hay unos pocos proveedores que hacen piezas de fundición a presión para el sector de la aviación, por lo que necesitamos tener opciones para asegurarnos de no sufrir el impacto de la obsolescencia y depender de los modelos de costes de proveedores específicos. Si podemos hacer una pieza aditiva por menos, podemos ahorrar dinero ahora y evitar cualquier aumento en el futuro”.
Auditoría anual
El proceso de selección tuvo en cuenta tanto los productos nuevos como los más antiguos. Se tuvieron en cuenta diversos factores, como las capacidades de las impresoras 3D de GE Aviation y el tamaño, la forma y las características de las piezas. Los ingenieros se preguntaron si las piezas utilizaban materiales bien caracterizados con los que habían trabajado antes en esas máquinas. También tuvieron en cuenta la facilidad de los pasos de posprocesamiento, como el mecanizado para eliminar las imperfecciones de la superficie y la soldadura para añadir accesorios a una pieza.
La auditoría examinó tanto las piezas de repuesto de bajo volumen como las piezas de producción para nuevos programas, como el motor LM9000.
En febrero de 2020, el equipo de GE Aviation ya había identificado 180 piezas de fundición para las que pensaban que la impresión 3D podría ahorrar dinero. Para asegurarse, un equipo de ingenieros de GE Aviation y GE Additive, cada uno de los cuales utilizó los modelos financieros y de producción de su propia organización, se dividió en pequeños grupos para calcular el retorno de la inversión en la impresión de cada pieza.
A continuación, COVID-19 recorrió el mundo.
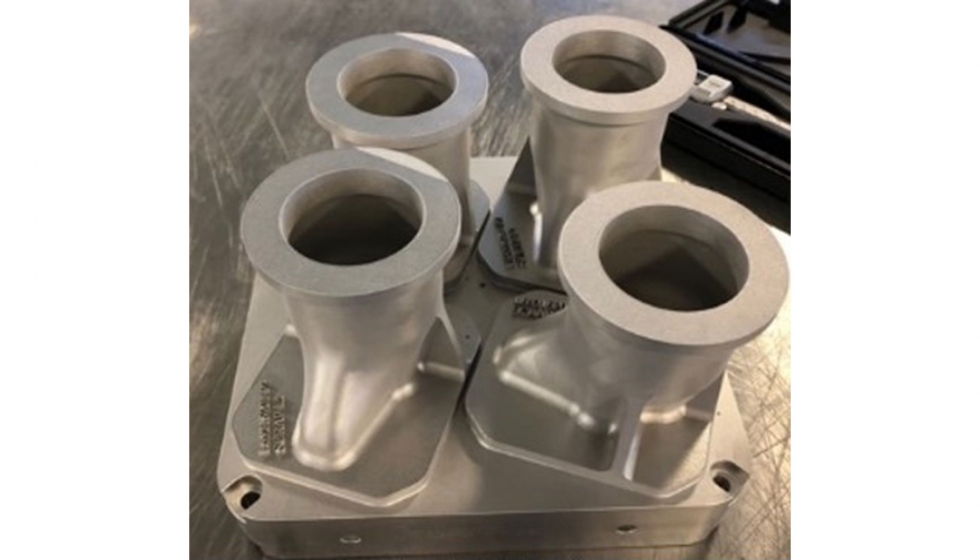
La producción en la pandemia
“Somos un taller de producción y no veríamos un proyecto como éste hasta después de que el Centro de Tecnología Aditiva de GE Aviation hubiera desarrollado el proceso para la producción a baja velocidad”, dijo Jeff Eschenbach, un director de Proyecto senior y líder del proyecto en las instalaciones de Auburn. “La diferencia de este proyecto es que lo asumimos desde el principio. Se creó una oportunidad para que los ingenieros de aquí se involucraran”.
La formación del equipo puso todo en marcha. Decenas de piezas habían pasado la criba inicial. Un análisis adicional permitió seleccionar nueve piezas entre ellas. Entre ellas había piezas de otros motores de turbina de gas de la industria naval, turbofanes de reactores regionales y algunos programas militares. Todas las piezas estaban hechas de CoCr, una aleación de cobalto y cromo muy utilizada para las piezas de turbinas calientes, o de Ti-64, una aleación de titanio-aluminio-vanadio rígida y ligera que se utiliza para piezas estructurales. Sólo buscaron piezas que pudieran caber en una máquina Concept Laser M2.
Las cuatro tenían un diámetro de unas 3,5 pulgadas y una altura de unas seis pulgadas. Estarían hechas de CoCr para manejar el aire comprimido caliente de la sección del compresor de la turbina.
Desde el punto de vista de la fabricación, compartían una geometría base y características similares. El equipo asumió que la M2 podía imprimir tres piezas a la vez, pero los ingenieros pronto rediseñaron la disposición para aumentar a cuatro. Esto aumentó inmediatamente la productividad, ya que se tarda aproximadamente el mismo tiempo en imprimir cuatro que tres piezas.
Mediante simulaciones y análisis, el equipo demostró que las piezas tenían el mismo rendimiento que las piezas de fundición a las que sustituían, dijo Steve Slusher, ingeniero de fabricación aditiva de GE que participó en el proyecto. El equipo también construyó barras de prueba con cada impresión, algunas en la cavidad abierta de la tapa que bajaba hasta la placa de construcción, para que los técnicos pudieran medir la integridad de cada tirada de producción.
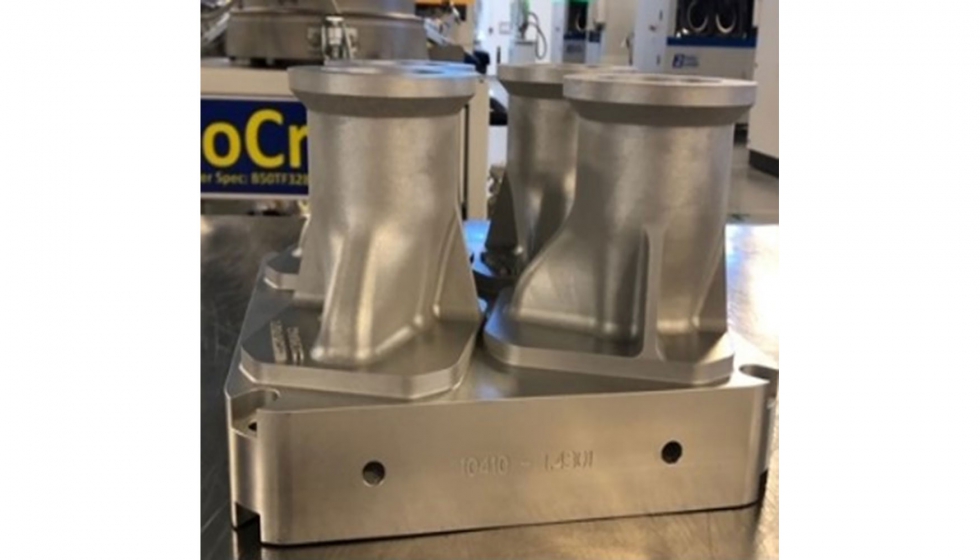
Conclusiones
Lo que más me llamó la atención", dijo Eschenbach, “fue que pudimos tomar un diseño de fundición existente, replicarlo rápidamente en nuestras impresoras y, a las pocas semanas de comenzar el proyecto, las piezas finales tenían la misma calidad que sus homólogas de fundición”. Este proyecto sirve de plantilla para futuros trabajos".
Kelly Brown, jefe técnico senior de GE Additive, coincidió: “Desde el punto de vista empresarial, Auburn mostró un músculo que no teníamos en el pasado, y ahora tenemos un banco de piezas al que podemos acudir después. Lo que el equipo ha hecho es notable y realmente muestra sus capacidades”.
Cambiar las piezas de fundición por inversión a la impresión 3D en metal es algo que la mayoría de los fabricantes nunca soñaría con hacer. Pero los ingenieros de GE Aviation y GE Additive lo hicieron, y su nueva realidad promete ahorrarles tiempo y dinero en docenas y, eventualmente, cientos y miles de piezas en todas sus líneas de productos.
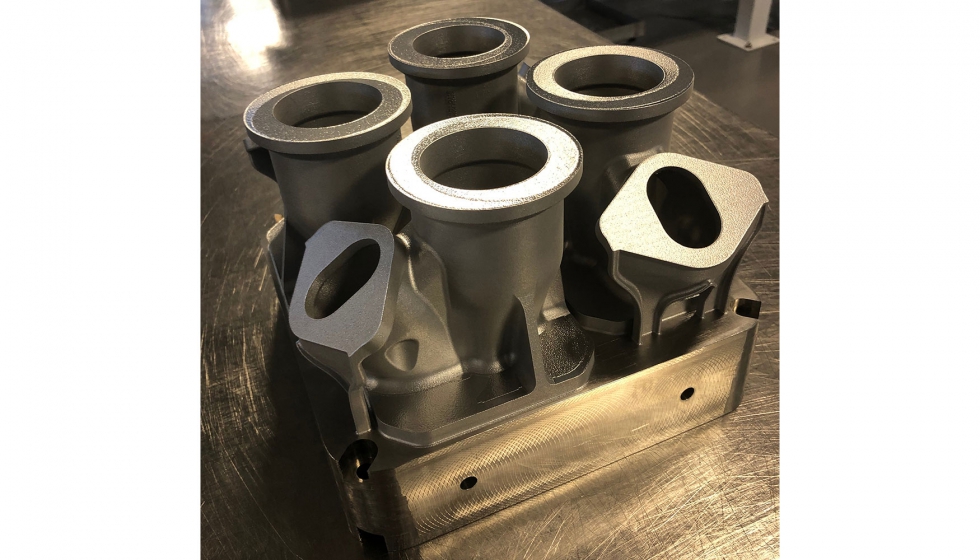