La metrología ayuda a incrementar la calidad en el proceso de producción
Asegurar la fiabilidad de los sistemas de medición por coordenadas
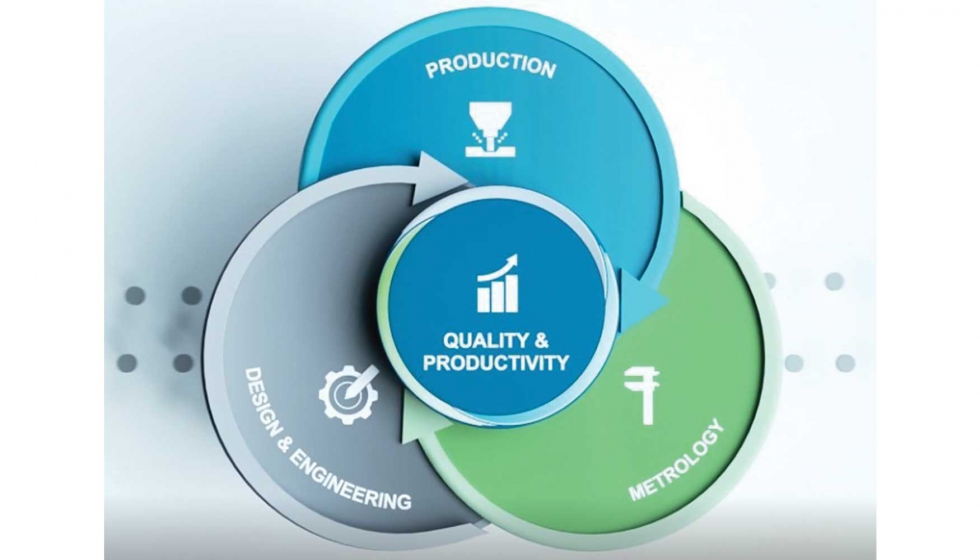
Diagrama de la importancia de la integración de la metrología en los ciclos de producción industriales.
La metrología es la ciencia de las medidas y constituye, junto con otras especialidades, como la normalización, los cimientos de la calidad productiva. La medición es la acción de determinar la longitud, extensión, volumen o capacidad de algo.
Ya hace años que la industria ha estado siempre muy interesada en saber cómo se produce. Prueba de ello es que la mayoría de empresas están realizado un gran esfuerzo, para invertir en la adquisición de soluciones digitales que siempre van ligadas a instrumentos y aparatos de medida y control.
Con las implantaciones de las nuevas tendencias de la industria 4.0, los fabricantes buscan formas más inteligentes para mejorar la calidad y la productividad, para ello es preciso el aseguramiento de las mediciones y de los elementos con que son realizadas.
Para controlar la calidad en la producción es necesario medir parámetros, y lo que es más importante, hay que cuantificar la calidad de la medida.
Por tanto, resulta que metrología, calibración y verificación van de la mano en el aseguramiento de la medida, puesto que todas las mediciones están en dependencia directa del equipo o máquina de control.
Según la norma UNE EN ISO 14253-1. Especificación geométrica de productos GPS. Inspección mediante medición de piezas y equipos de medida. Parte 1: “Cuando se verifica cualquier especificación geométrica de cualquier pieza, se debería tener en cuenta la incertidumbre de medición”.
Incertidumbre de Medición
Se trata de un parámetro, asociado al resultado de una medición, que caracteriza la dispersión de valores que podrían ser razonablemente atribuidos al mensurando (mensurando = magnitud particular, objeto de la medición).
La incertidumbre de medida permite la mejora de la calidad en la ejecución de una medición, ya que refiere a un entorno del valor proporcionado por la medida, donde es probable que se encuentre el valor real.
Existen muchos y varios factores que pueden contribuir a la incertidumbre de medida.
Algunas de las causas más frecuentes de incertidumbres en la medida pueden ser las siguientes:
- Condiciones de la medición (temperatura, humedad, vibraciones...).
- El equipo de medida (incertidumbre de la calibración, coeficientes de dilatación, resolución...).
- La realización.
- El procedimiento de la medida.
- Las características GPS.
- La persona que realiza la medición.
Uno de los factores que contribuyen a la incertidumbre de medida mencionada anteriormente es el propio equipo de medida.
Aseguramiento de la fiabilidad de los sistemas de medición por coordenadas
Ajuste/Calibración – Aceptación - Verificación periódica – Control periódico
Para asegurar un correcto funcionamiento de los sistemas de medición por coordenadas y una buena fiabilidad de las mediciones realizadas, se deberían seguir unas determinadas pautas de control dichos sistemas.
Un buen ejemplo de ello sería:
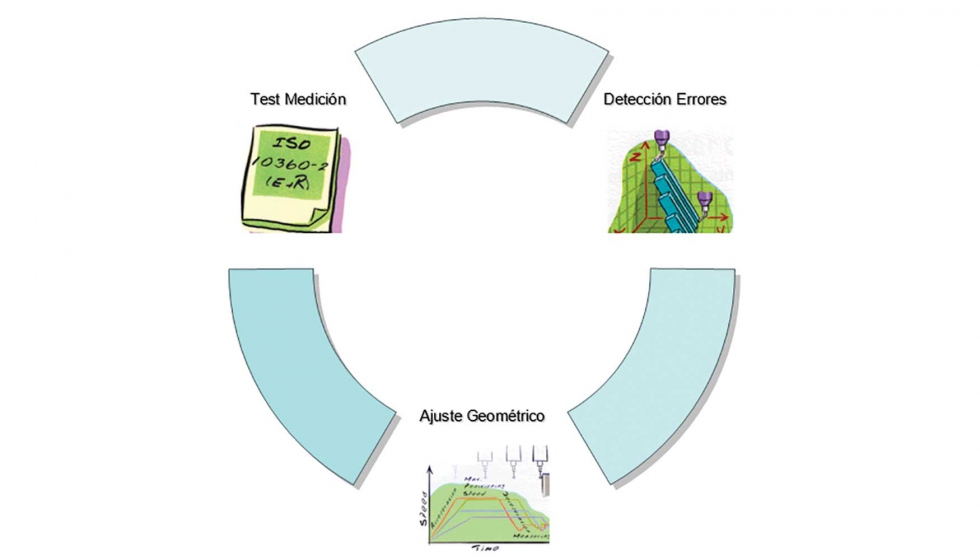
Patrón de cómo los sistemas de medición pueden entregar una alta fiabilidad
- Ajuste/Calibración:
Aunque la avanzada tecnología de fabricación permite hacer piezas de forma muy precisa, pero aún así existen imperfecciones. Por pequeñas que estas sean, que existan tolerancias significa que existen errores.
Los sistemas de medición por coordenadas no son diferentes a otros productos en este aspecto. Aunque están hechos con tolerancias muy ajustadas, hay errores en su estructura (errores de rotación, rectitud, ortogonalidad, cedimientos y escala) que afectan a su eficacia. Cuanto más ajustadas sean las tolerancias, más precisos tendrán que ser los sistemas de medición por coordenadas.
La mayoría de las imprecisiones de los sistemas de medición por coordenadas se pueden corregir automáticamente en el ordenador del propio sistema. Una vez medidos todos los errores geométricos, se pueden minimizar o incluso eliminar con potentes algoritmos de software. Ese proceso se conoce como compensación del error volumétrico. Con la eliminación matemática de errores se reduce el coste de fabricación.
En este aspecto habría que considerar que estas imprecisiones o errores geométricos de los sistemas de medición por coordenadas deberían ser periódicamente controlados y compensados, para asegurar la fiabilidad de las mediciones realizadas.
Bajo nuestra experiencia, de años de trabajo y como fabricantes de sistemas de medición por coordenadas se recomienda, para un buen funcionamiento y una buena fiabilidad de los sistemas que se realicen anualmente dichos ajustes (calibración y corrección).
Así mismo habría que considerar la importancia de que las correcciones, que se realizan a cualquier sistema de medición por coordenadas (ajustes geométricos totales o parciales) sean siempre realizadas por el fabricante, ya que es éste quien mejor conoce el sistema (tanto el hardware como el software de compensación).
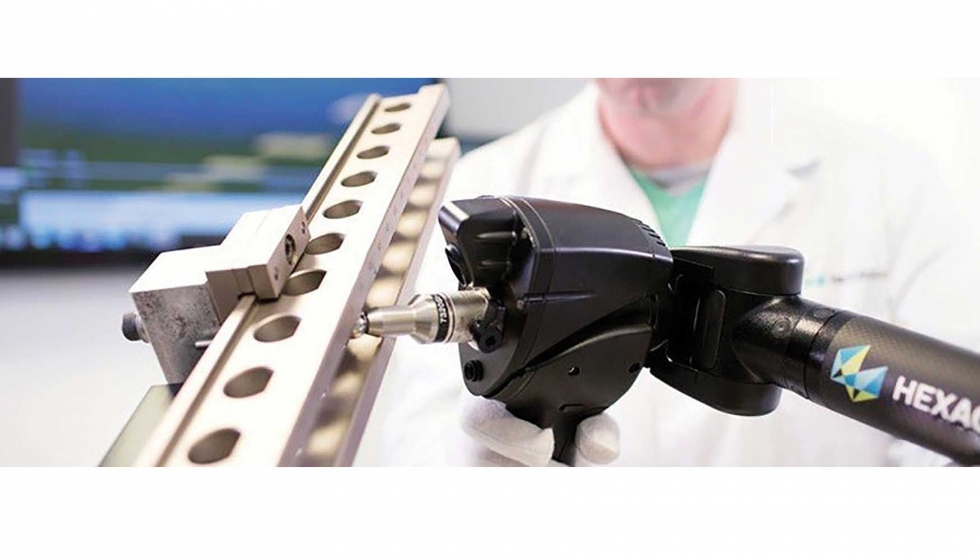
Hexagon Metrology S.A. recomienda una perfecta calibración y corrección de los ajustes para aumentar la fiabilidad de los sistemas de medición.
- Aceptación - Verificación periódica:
Entre las normas internacionales que regulan la metrología por coordenadas se encuentra la Norma ISO 10360.
Esta norma, en sus diferentes partes (parte 2, 10, 12...) se ocupa de los ensayos de aceptación que verifican las especificaciones del fabricante de los sistemas de medición por coordenadas, utilizados para la medición de dimensiones. También especifica los ensayos de verificación periódica que permiten al usuario comprobar las prestaciones de dichos sistemas, para medición de dimensiones.
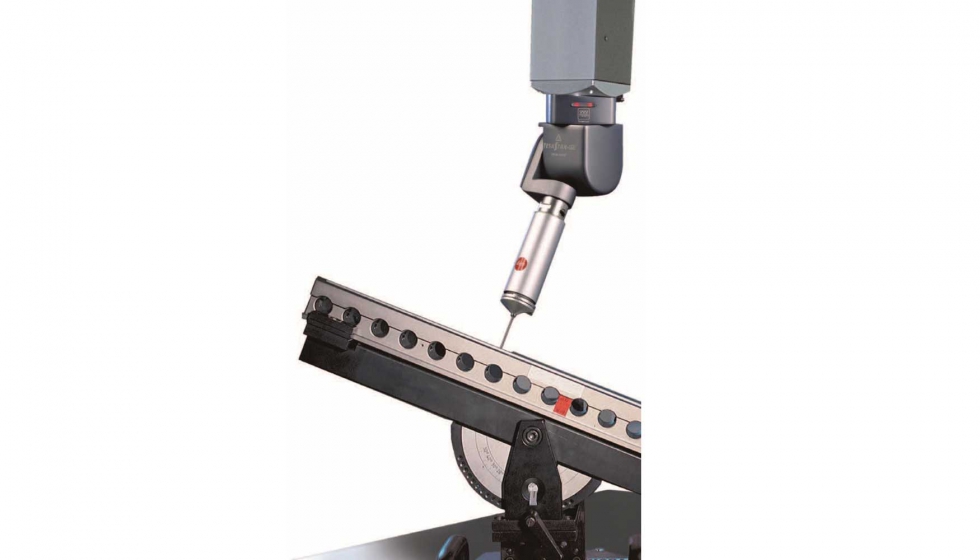
Aparte de realizar la compensación o los ajustes de los errores geométricos y/o la calibración o aceptación de los sistemas de medición por coordenadas, en un sistema de calidad interna de una empresa, deberían contemplarse los ensayos de verificación periódica y control periódico de forma regular, tal y como se recomienda en muchas normas internacionales.
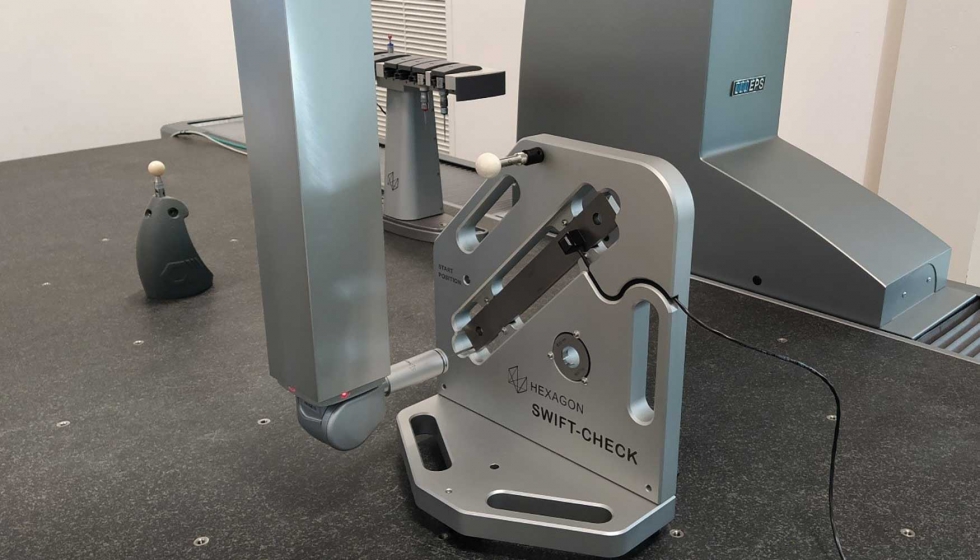
El laboratorio de Hexagon Metrology S.A. realiza el servicio de calibración ‘in situ’ para máquinas de medición por coordenadas y en su laboratorio permanente para brazos de medición portátil, basándose en procedimientos específicos que toman referentes normas internacionales (C.M.M.A.:1989, ISO 10360-2:2002, ISO 10360-2:2010 e ISO 10360-12:2016).
Este tipo de calibraciones se encuentran incluidos en el anexo técnico asociado a la acreditación N.º 116/LC10.083.
- Control periódico:
Entre ensayos de verificación periódicos es recomendable realizar controles periódicos de los sistemas de medición por coordenadas.
Se trata de demostrar que de los sistemas de medición por coordenadas son conformes a los requisitos especificados con relación a los errores máximos permitidos indicados.
El intervalo entre los ensayos debería determinarse en base a las condiciones ambientales y a las prestaciones de medición requeridas.
Para ello es posible medir dimensiones características de otros tipos de patrones materiales y no sólo considerar materiales de dimensión.
En función de los tipos de medición para los cuales se utiliza los sistemas de medición por coordenadas, se pueden utilizar múltiples artefactos: pieza de ensayos, placa de bolas, placa de agujeros y anillos patrón, entre otros.
- Un ejemplo de ello sería:
Después de ajustar un sistema de medición por coordenadas (corrección de parámetros geométricos) y de su aceptación y/o verificación, el cliente puede disponer de un elemento: ‘pieza patrón’ que podría ser una pieza ‘normal’ y ‘corriente’ en la cual se realizan mediciones de varios tipos y se guardan los resultados.
De este modo, más adelante y con un plazo corto (diario, semanal...) realizar las mismas mediciones y comparar los resultados de medición. Esto nos permitirá cuantificar las desviaciones obtenidas resultantes de la medición con las que se realizaron cuando el sistema fue por última vez ajustado, aceptado y/o verificado.