Fabricación aditiva SLM para fabricación integral de componentes de SS316L e IN718
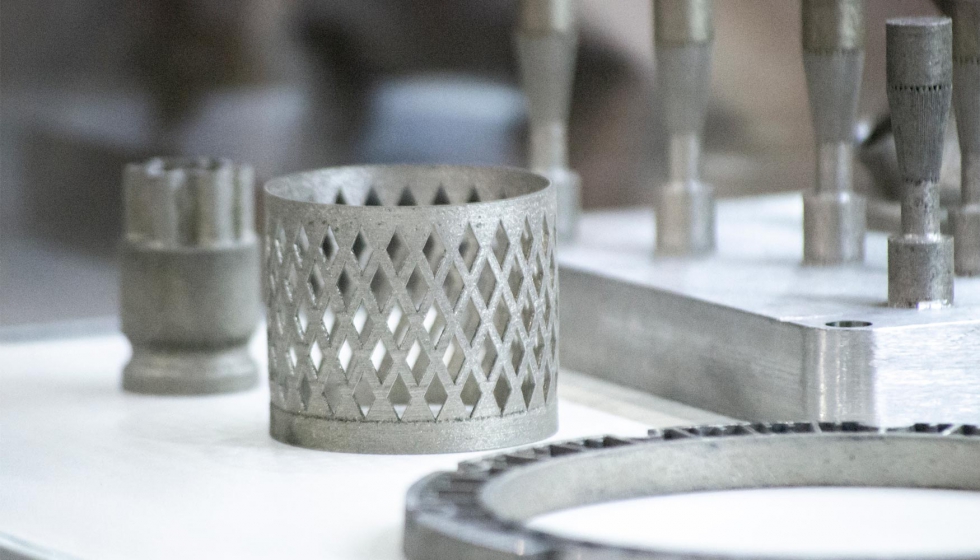
En este trabajo se muestran dos ejemplos prácticos de desarrollo de producto mediante tecnología Selective Laser Melting (SLM): un kit de piezas en SS316L para el sector de la ciencia y un componente aeronáutico en IN718 para el sector aeroespacial. Se mostrarán algunos de los resultados más relevantes del proceso como el rediseño, la caracterización del polvo metálico, la optimización de algunos de los parámetros más relevantes para el aseguramiento de la calidad y los postprocesos.
1. Introducción
En este trabajo se muestra las diferentes etapas de la cadena de valor en las que trabaja Egile, que corresponde no solo a la propia fabricación en aditiva, sino que también abarca labores de co-ingeniería y los posprocesos. Para mostrar todas estas etapas se contará con dos productos que se están desarrollando en Egile:
- Un kit de piezas en SS316L para el sector de la ciencia y
- Un componente en IN718 para el sector aeronáutico
Para el desarrollo de estos productos, Egile dispone de un área de fabricación aditiva metálica de tecnología SLM (Selective Laser Melting) con una máquina AM400 de Renishaw, un laboratorio de materiales (preparación de muestras, microscopía óptica y medición de la rugosidad), y un departamento de metrología.
Además, Ceit dispone de los medios necesarios para una caracterización más profunda de los materiales, como microscopía electrónica de barrido, difracción láser, psicometría, composición química por ICP, etc. así como un atomizador de gas para la fabricación de polvo metálico para la tecnología SLM.
2. Co-ingeniería
Egile ha colaborado con un cliente del sector de la ciencia para la fabricación en SLM de varios componentes que forman parte de un kit. Cada kit está formado por entre 25 y 30 piezas de acero inoxidable 316L de geometría compleja, todas ellas similares, pero con diferentes tamaños. En este caso, las tecnologías tradicionales como el mecanizado no eran viables, debido al alto coste de los ‘no recurrentes’. La fabricación de utillajes de mecanizado para tantas referencias y una serie relativamente corta hacen que el mecanizado no sea viable. En este caso, la fabricación aditiva aparece como la tecnología más adecuada: variedad de geometrías a fabricar para una serie relativamente corta.
En cuanto a las exigencias del cliente, las desviaciones con respecto a la geometría original deben ser mínimas, ya que el kit va encapsulado en una estructura rígida. Finalmente, para facilitar el montaje, se realizan unas ranuras en las piezas para dotarlas de cierta flexibilidad. Estas ranuras se fabrican con EDM (Electro Discharge Machining) tras el alivio de tensiones y la eliminación de los soportes.
Primeramente, se ha realizado una simulación de las distorsiones debidas a la propia fabricación en SLM, se observa que hay zonas con unas desviaciones de hasta 0.7 mm, que imposibilitaría el montaje final de las piezas, por lo que es necesario plantear una solución. En la figura 1 puede observarse el resultado de la simulación de distorsiones de una de las piezas a fabricar. Para verificar las distorsiones simuladas en pieza real, se ha impreso una pieza y no se han observado diferencias significativas.
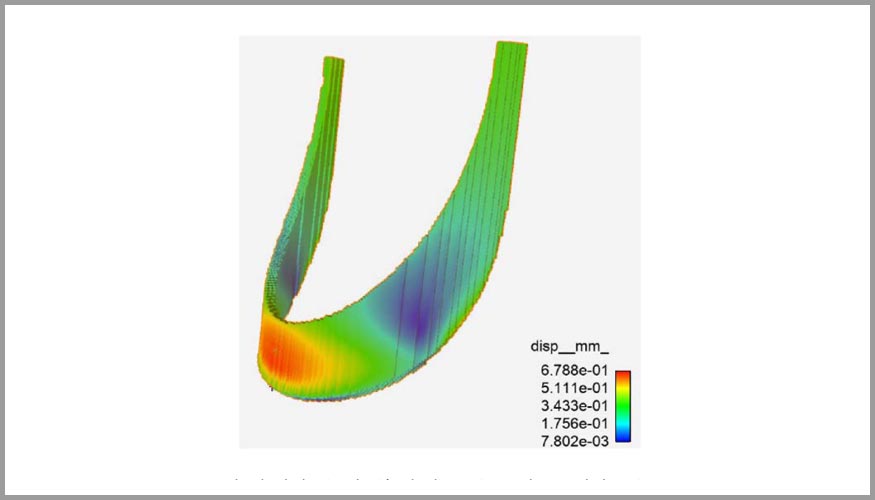
Las distorsiones observadas se concentran en la zona más másica de la pieza y con mayor sección a fundir. Estas distorsiones tienen lugar debido a las tensiones residuales que se generan durante el proceso de impresión. Inicialmente, se plantea disminuir las distorsiones en la pieza optimizando la estrategia de rigidizar los soportes. Las zonas más propensas a la distorsión o con mayor dificultad para disipar el calor del láser, se soportan con soportes más gruesos. Estos soportes son más rígidos y facilitan la disipación de calor en la zona soportada a la vez que son capaces de contener las posibles distorsiones. Aunque se observa una disminución en la distorsión final de la pieza, únicamente con la optimización de los soportes no se ha logrado fabricar la pieza dentro de las tolerancias que exige el cliente.
Durante el análisis de los posprocesos, se propone al cliente integrar la fabricación de las ranuras en la propia impresión de las piezas. Estas ranuras son necesarias para dotar a la pieza de cierta flexibilidad necesaria en el montaje. Incluyendo las ranuras en la impresión se logra que la pieza sea menos másica y las secciones más constantes, ya que las secciones a fundir ahora se encuentran divididas por estas ranuras, tal y como se muestra en la figura 2. Tras la impresión de varias pruebas, se observa que, efectivamente, se ha logrado reducir las distorsiones hasta cumplir las exigencias del cliente. Se decide entonces combinar ambas estrategias, soportes rígidos y ranuras integradas para obtener piezas prácticamente sin distorsiones.
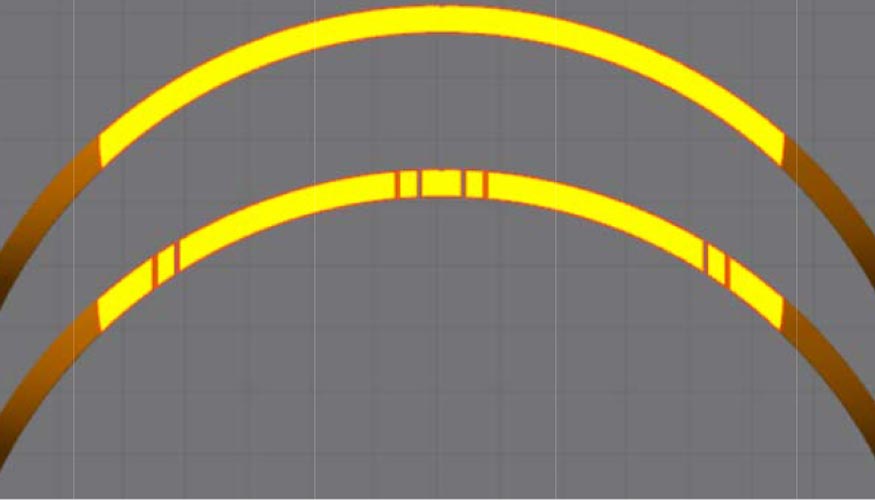
En la figura 3 se puede observar uno de los primeros kits impresos. La propuesta de integrar el proceso de impresión y de ranurado en uno solo, no solo es beneficioso desde el punto de vista de eliminación de las distorsiones, sino que esta mejora también incidirá en una reducción del lead time y del coste final de las piezas.
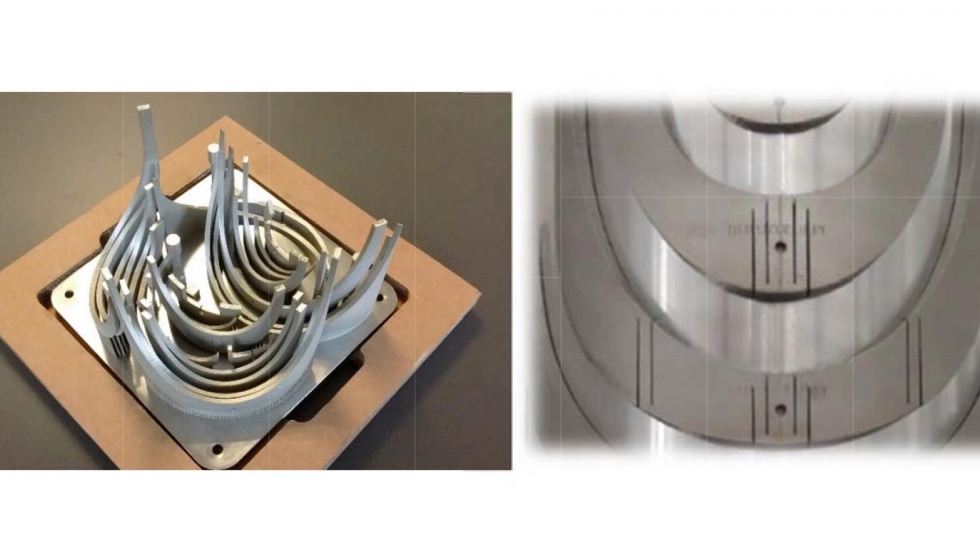
Existen también componentes similares al kit que en la actualidad se fabrican mediante mecanizado ya que, al ser muy másicos, incluso con ranuras integradas, se generarían unas distorsiones muy importantes. En este sentido se ha elaborado un estudio de aligeramiento junto con el centro tecnológico Lortek de estas piezas con un doble objetivo (en esta aplicación en concreto, la reducción de peso no es prioritaria):
- Minimizar las distorsiones en los conjuntos más másicos y
- Mejorar la productividad (menor volumen supone menor tiempo de fabricación)
Se han seguido dos estrategias diferentes y ambas suponen una reducción importante tanto en las distorsiones como en el tiempo de fabricación.
Una de las estrategias ha sido aplicar estructuras internas aligeradas de tipo lattice. Las estructuras lattice son de tipo repetitivo donde se concentra el material en las direcciones óptimas para que la pieza aguante las cargas a las que se encuentra solicitada. Este tipo de estructuras también se emplean en aplicaciones que requieren: aislante térmico, intercambiadores de calor, absorción de energía y biocompatibilidad. En este caso, se han optimizado los parámetros de la estructura lattice (diámetros, longitud máxima y redondeos) para cumplir con los requerimientos mecánicos. De esta manera se obtiene una reducción del tiempo medio de fabricación de un 14% con respecto a la estructura maciza por pieza.
La otra estrategia consiste en una optimización topológica de la pieza, que se basa en el análisis mecánico del componente para aligerar la estructura manteniendo las funcionalidades mecánicas de la misma. Mediante esta estrategia de optimización topológica, se ha logrado una reducción de un 17% en el tiempo de fabricación.
La figura 4 muestra la pieza con estructura lattice y la optimizada topológicamente y en la tabla 1 se recogen las reducciones de tiempo con cada estrategia.
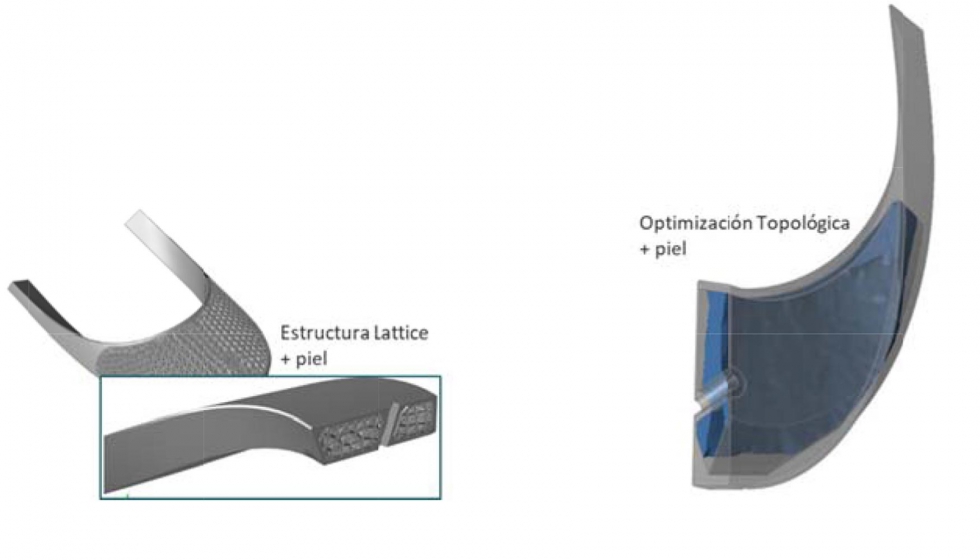
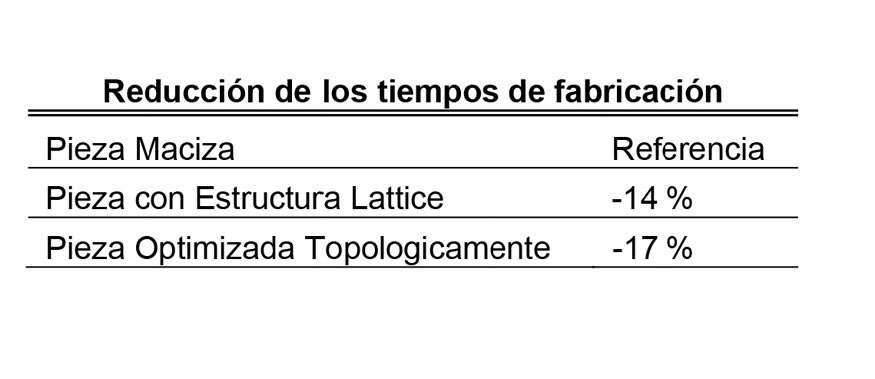
3. Fabricación SLM
A continuación, se describe el proceso fabricación en SLM y los posprocesos de un componente aeronáutico de IN718. Para su fabricación se ha utilizado una máquina Renishaw AM400, ubicada en las instalaciones de Egile.
3.1. Caracterización del polvo metálico
En cuanto a la materia prima, en este caso polvo metálico de la aleación base níquel IN718, es necesario controlar ciertas especificaciones antes de utilizarlo en máquina. La distribución de tamaño de partícula adecuada para la fabricación aditiva tipo SLM es 15-53 micras.
Primeramente, se realiza un control del polvo que se va a utilizar. Se revisan, entre otras características, la composición química y distribución del tamaño de partícula del polvo. Al no disponer de medios suficientes para realizar algunos de los controles, se solicita el certificado de conformidad al proveedor y se controlan las características más relevantes de Ceit, como el contenido de elementos intersticiales (O y N) y fluidez del polvo. Cabe destacar que estos controles se realizan tanto en la recepción de polvo nuevo como en el control de polvo usado, con una frecuencia previamente determinada.
En el caso del polvo IN718 analizado, las características de lote a lote de un mismo material de polvo metálico pueden ser diferentes, aun estando conforme según la norma ASTM F3055. En este sentido existe cierta inquietud sobre la influencia de la variabilidad del polvo metálico en la calidad de las piezas fabricadas por SLM.
A continuación, en la figura 5, se muestra el análisis de tres muestras de polvo de IN718 pertenecientes a lotes y proveedores diferentes. La morfología de las partículas de polvo es esférica con algunas partículas irregulares y con pocos satélites. La distribución del tamaño de partícula muestra una distribución gaussiana unimodal, tal y como se recomienda para SLM. Sin embargo, el polvo A no fluye en el Hall Flow (test de fluidez), probablemente debido a un mayor ancho de la distribución del tamaño de partícula.
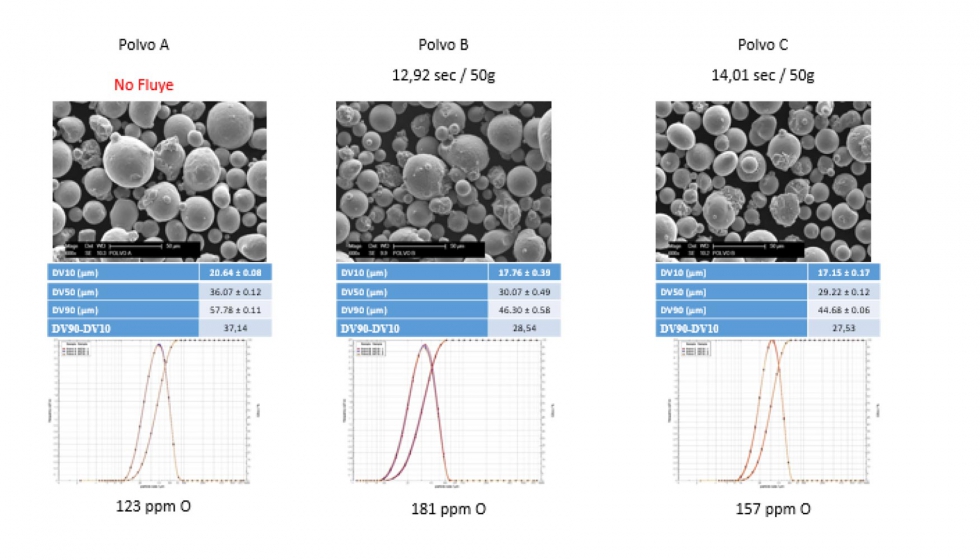
3.2. Mapas de proceso SLM
El desarrollo de parámetros de fabricación SLM de cada material es imprescindible para garantizar la calidad y minimizar los defectos (1). En este sentido, los criterios para optimizar los parámetros han sido: reducir la porosidad, las tensiones residuales y la rugosidad superficial; mantener las propiedades mecánicas y mejorar la productividad.
En el mapa de proceso desarrollado por Egile, que se muestra en la figura 6, se ha delimitado la zona óptima de trabajo, denominada 'Conduction mode zone', en el que se encuentran las combinaciones de potencia y velocidad de láser óptimas para conseguir una densidad por encima del 99,9% en probeta. Para ello se ha caracterizado la defectología asociada que delimita el área óptima de trabajo:
- Con altos valores de potencia y velocidades bajas tenemos una alta concentración de energía que da lugar a el sobrecalentamiento del melt pool (baño fundido) y consecuente evaporación de material. Este tipo de defecto suele mostrarse como poros esféricos (2)(3).
- Bajos valores de potencia y altas velocidades están asociados con una insuficiente densidad de energía del láser que, al no ser capaz de fundir completamente el polvo, genera porosidades irregulares, asociadas a partículas de polvo no fundidas o semi fundidas.
- Altos valores de potencia y altas velocidades están relacionadas con el efecto balling (4)(5). Esto se debe a las altas perturbaciones en el cordón fundido, que interrumpen la continuidad del cordón provocando un enfriamiento en forma de equilibrio esférica.
Dentro de la zona de conducción optaremos por los parámetros asociados a una mayor productividad, delimitados en verde y denominados 'Optimum energy contour'.
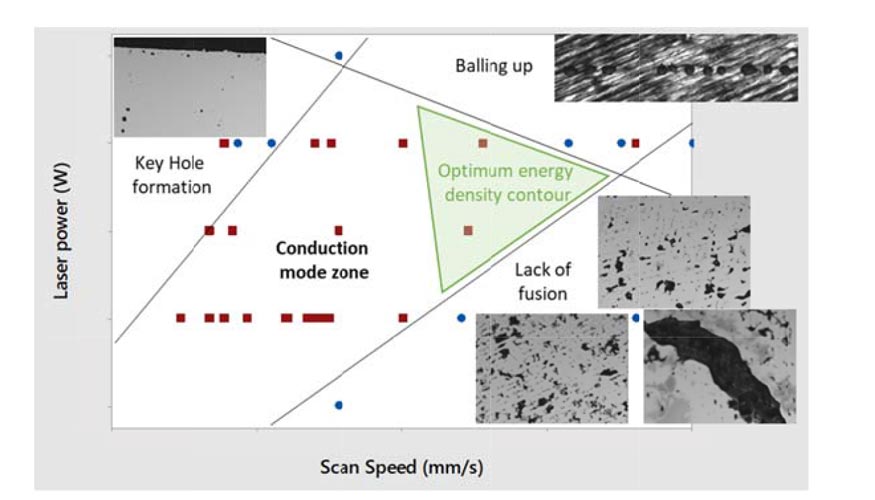
3.3. Microestructura SLM
La figura 7 muestra las microestructuras atacadas obtenidas en el plano paralelo (XY) y perpendicular a la dirección de fabricación (YZ). Así mismo, se aprecian las zonas fundidas por el láser, los melt pool, en la dirección paralela a la fabricación Z, mientras que en la dirección perpendicular se puede distinguir la estrategia de escaneado utilizada. Ambas características microestructurales están relacionadas con los parámetros utilizados en la fabricación (potencia, velocidad de escaneado, espesor de chapa...).
Como se puede ver en las fotos obtenidas en el microscopio óptico, tras el tratamiento térmico realizado en las piezas fabricadas con SLM no se observa la microestructura resultante de un enfriamiento rápido característico del proceso de SLM observada anteriormente en las muestras as-SLM, tanto en la dirección paralela como perpendicular a Z. De acuerdo con esto, se pueden apreciar más claramente las juntas de grano en lugar de los melt pool o la estrategia de escaneado.
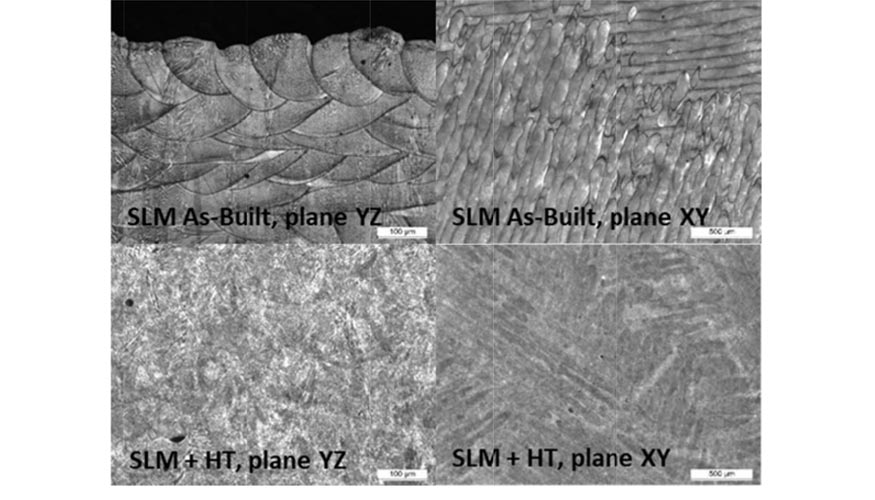
En las piezas as-SLM se han identificado óxidos de Al-Ti esféricos que pueden estar relacionados con ligeras cantidades de oxígeno presenten en la atmosfera durante la fabricación. No obstante, la presencia de estos óxidos es aislada (se puede confirmar con bajos contenidos de oxígeno medidos con LECO). Se han detectado también de manera marginal óxidos relacionados con la evaporación de aluminio (bajo punto de fusión) y posterior precipitación como óxido. Es habitual encontrar este tipo de óxidos localizados entre dos capas de polvo fundido (6)(7).
3.4. Propiedades mecánicas
Generalmente las propiedades de IN718 fabricado por SLM pueden variar en función de las condiciones de fabricación y de los tratamientos posprocesado que se apliquen (8)(9). Pero se ha observado que es posible alcanzar valores similares al os conseguidos mediante procesos de fabricación convencionales, como la forja o el fundido (10). Las piezas y probetas de Inconel 718 fabricado en Egile se han tratado térmicamente y se han caracterizado en el Ceit mostrando unos valores coherentes con los de literatura, mostrando una resistencia ligeramente superior en el plano XY pero una elongación superior en el plano ZY paralelo a la dirección de fabricación (UTS 1.1000-1.200 MPa, límite elástico 850-900 MPa, elongación 25-30%).
3.5. Defectos geométricos
En la fabricación del componente aeronáutico se han identificado varios defectos geométricos. Uno de ellos ha sido el plano de distorsión que ha aparecido en una zona de transición en la que el área de la sección a fundir es mayor que la suma de los dos anteriores, tal y como se puede observar en el croquis de la figura 8. En la capa en la que la sección interior y exterior se unen, la sección a fundir pasa a ser mayor que la suma de las capas precedentes. El aumento de la sección provoca reducción de la velocidad de enfriamiento, que se traduce en tensiones de expansión y contracción desiguales a las de las capas inferiores. Estas tensiones alcanzan su máximo varias capas por debajo del evento dando lugar a un deslizamiento entre capas. Para minimizar este defecto de deslizamiento entre capas se ha realizado un cambio de diseño de la pieza, promoviendo que la unión de las dos secciones independientes sea más progresiva. De esta manera, se evitan zonas de voladizo que generan el sobrecalentamiento responsable de las distorsiones.
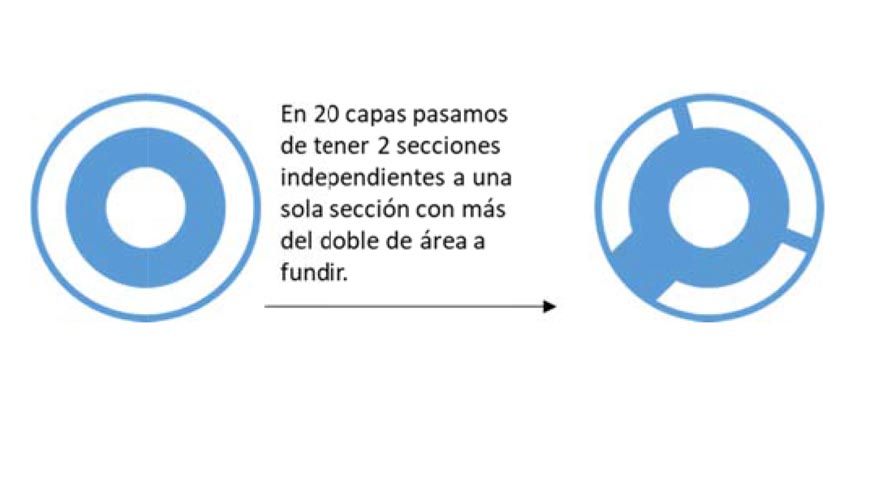
4. Posprocesos
Para asegurar la calidad y repetibilidad de las piezas aeronáuticas fabricadas por SLM es preciso llevar a cabo una serie de controles de manera rigurosa. Al tratarse de una tecnología relativamente novedosa en el ámbito industrial, la disponibilidad de procedimiento de inspección de piezas fabricadas por SLM es limitada. En este sentido. Egile ha desarrollado una guía interna basada en la propia experiencia. Por supuesto, las especificaciones y requerimientos del cliente siempre prevalecen sobre los criterios internos, si estos últimos fuesen menos exigentes. A continuación, se muestran los requerimientos más significativos para validar una pieza aeronáutica.
Una vez fabricada la pieza se realiza un control dimensional en el que se identifican las áreas con distorsiones superiores a las tolerancias del plano; en el control visual se asegura la ausencia de golpes, inhomogeneidades de color en la piza y porosidades abiertas. Es importante la eliminación de partículas de polvo que se desprendan de la superficie de la pieza.
En cuanto a la defectología interna, se utilizan métodos como la radiografía y tomografía computerizada para buscar burbujas de gas o faltas de fusión. Sin embargo, la morfología del grano (microestructura) y los defectos propios de la tecnología aditiva SLM, muchas veces dificultan su detección. En vista de estos acontecimientos y del alto coste de estos ensayos no destructivos (END), en la actualidad se están desarrollando sistemas de monitorización de la melt pool durante el propio proceso de fabricación. Si se consiguen asociar las señales recogidas en la monitorización con los diferentes tipos de defectología, esto podría suponer una nueva técnica de END para la fabricación aditiva a medio plazo.
Tras los tratamientos térmicos se realizarán controles habituales, como metalografía, dureza o ensayos de tracción. Para la validación de los primeros artículos, adicionalmente, se efectuarán ensayos mecánicos de creep y fatiga.
5. Conclusiones
En este trabajo, se han tratado algunos de los puntos clave en el desarrollo de la tecnología de fabricación aditiva SLM para la fabricación integral de componentes de diferentes sectores. Por un lado, Egile ha colaborado con un cliente para la fabricación en SLM de un kit de varios componentes para el sector de la ciencia. El reto consiste principalmente en la reducción de las distorsiones que tienen lugar durante la fabricación SLM, pues su magnitud no es compatible con la funcionalidad de estas. Para reducir estas distorsiones, se han desarrollado diferentes estrategias, como integración de postprocesos, optimización de los soportes, introducción de estructura lattice y optimización topológica de las piezas.
Por otro lado, se ha descrito el desarrollo de un componente de IN718 del sector aeronáutico, donde los requerimientos de calidad son mucho más exigentes. El desarrollo para obtener una capacitación tecnológica que permita fabricar las piezas de una manera repetitiva y con un proceso robusto, comprende diferentes etapas: desde la caracterización del polvo metálico, desarrollo de mapas de proceso SLM y propiedades mecánicas; a los postprocesos, incluyendo el control de los defectos, los tratamientos térmicos y el control dimensional de las piezas.
6. Bibliografía
1. Luke Nelson Carter. Selective laser melting of nickel superalloys for high temperature applications. University of Birmingham; 2013.
2. H. Gong, H. Gu, K. Zeng, J.J.S. Dilip, D. Pal BS. MeltPool Characterizationfor SelectiveLaser Meltingof Ti-6Al-4V Pre-alloyedPowder. In: 28th AnnualInternational Solid FreeformFabrication Symposium -An Additive ManufacturingConferenc, 2016. 2016.
3. Courtois M, Carin M, Masson P Le, Gaied S, Balabane M. A new approach to compute multi-reflections of laser beam in a keyhole for heat transfer and fluid flow modelling in laser welding. J Phys D Appl Phys. 2013 Dec 18;46(50):505305. Available from: http://stacks.iop.org/0022-3727/46/i=50/a=505305?key=crossref.cb1eaadf4d6b9f6e5fe57f49a825b655
4. Li R, Liu J, Shi Y, Wang L, Jiang W. Balling behavior of stainless steel and nickel powder during selective laser melting process. Int J Adv Manuf Technol. 2012 Apr 18;59(9–12):1025–35. Available from: http://link.springer.com/10.1007/s00170-011-3566-1
5. Jia Q, Gu D. Selective laser melting additive manufacturing of Inconel 718 superalloy parts: Densification, microstructure and properties. J Alloys Compd. 2014 Feb; 585:713–21. Available from: https://linkinghub.elsevier.com/retrieve/pii/S0925838813023451
6. Sercombe TB, Li X. Selective laser melting of aluminium and aluminium metal matrix composites: review. Mater Technol. 2016 Mar 24;1–9. Available from: http://www.tandfonline.com/doi/full/10.1179/1753555715Y.0000000078
7. Hebert RJ. Viewpoint: metallurgical aspects of powder bed metal additive manufacturing. J Mater Sci. 2016 Feb 18;51(3):1165–75. Available from: http://link.springer.com/10.1007/s10853-015-9479-x
8. Amato KN, Gaytan SM, Murr LE, Martinez E, Shindo PW, Hernandez J, et al. Microstructures and mechanical behavior of Inconel 718 fabricated by selective laser melting. Acta Mater. 2012 Mar;60(5):2229–39. Available from: https://linkinghub.elsevier.com/retrieve/pii/S1359645411008949
9. Wang Z, Guan K, Gao M, Li X, Chen X, Zeng X. The microstructure and mechanical properties of deposited-IN718 by selective laser melting. J Alloys Compd. 2012 Feb; 513:518–23. Available from: https://linkinghub.elsevier.com/retrieve/pii/S0925838811020767
10. Appa Rao G, Srinivas M, Sarma DS. Effect of thermomechanical working on the microstructure and mechanical properties of hot isostatically pressed superalloy Inconel 718. Mater Sci Eng A. 2004 Oct; 383(2):201–12. Available from: https://linkinghub.elsevier.com/retrieve/pii/S0921509304007439