La electroerosión gana terreno en la fabricación de piezas de geometría compleja
El pasado 23 de abril tuvo lugar, en Bilbao, el congreso de ISEM XIX [6]. Pese a que ha sido tradicionalmente conocido y consolidado como la más importante conferencia de electroerosión y mecanizado electroquímico celebrada a nivel mundial, en estas últimas ediciones comienzan a cobrar relevancia otras aplicaciones a las que este congreso está dando cabida. Tanto es así que en esta última edición, en la que se han presentado cerca de 150 trabajos, se han dividido en las siguientes sesiones paralelas (las cuales pueden verse de forma sencilla en el esquema de la figura 1): corte por abrasivo o chorro de agua (Abrasive and Water Jet Machining, AJM), fabricación aditiva (Additive Manufacturing, AM), mecanizado electroquímico (Electro Chemical Machining, ECM), electroerosión (Electrical Discharge Machining, EDM), electrodeposición (Electrodeposition, EDP), corte láser y LBM (Laser and Electron Beam Machining, LBM & EB), procesos híbridos (Hybrid Processes, HP), mecanizado por plasma y ARC (Plasma & ARC Machining Processes, PAM) y, finalmente, mecanizado ultrasónico (Ultrasonic Machining, UM).
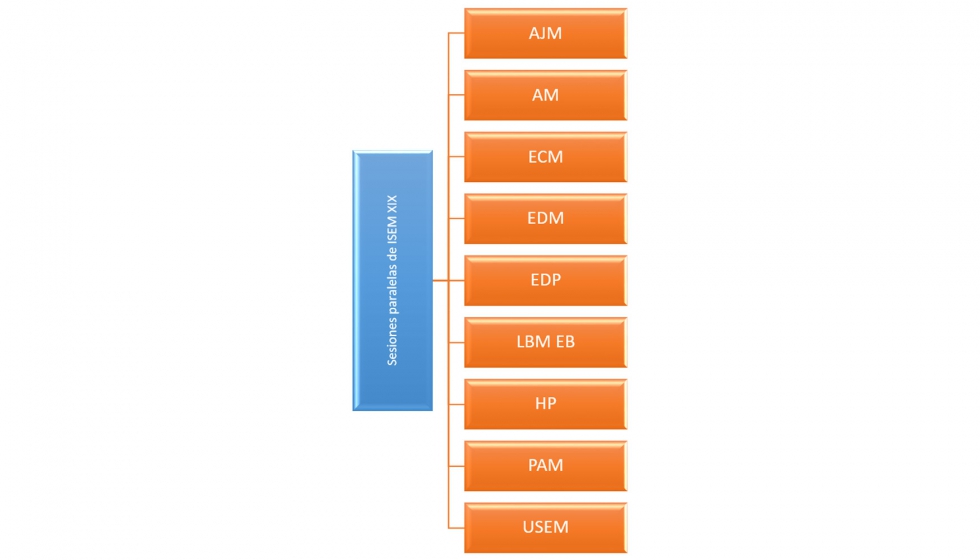
La primera conferencia de ISEM, denominada por aquel entonces como International Symposium for Electro-Machining (ISEM), tuvo lugar en Praga en 1960. Pese a que hasta 1974 se celebró únicamente cada seis años, desde esa fecha en adelante se ha celebrado trienalmente en diferentes países del mundo, repartidos en tres continentes: América, Asia y Europa. La edición XVII, la cual aconteció en Leuven, Bélgica, fue la primera patrocinada por la academia internacional de la ingeniería de producción (International Academy for Production Engineering, CIRP) y, por esta razón, cambió su nombre por el actual: CIRP Conference on Electro Physical and Electro Chemical Machining.
Sin embargo, esta décimo novena edición (2018) ha sido especial. Y el motivo es el siguiente: es la primera ocasión en la que esta conferencia se efectúa desde que se ha convertido en un evento bienal. La razón es muy simple. La producción científica sobre estos temas ha crecido tanto durante los últimos años (como se ha comentado más arriba, son cerca de 150 artículos recibidos para ser evaluados en este último congreso) que ha resultado preciso reducir el tiempo para poder presentar estos trabajos. A pesar de todo, esto supone un reto tanto para el comité organizador del mismo como para los investigadores que presentan sus artículos en un espacio de tiempo menor.
Por otra parte, cabe destacar la inclusión paulatina de otros procesos de mecanizado conocidos como no-convencionales; por ejemplo, el corte por chorro de agua o abrasivo, las tecnologías láser o, de forma más reciente, la fabricación aditiva que tan en boga está últimamente. La incorporación de estas otras tecnologías ha supuesto un cambio en la visión general del congreso en el que, aunque cerca del 70% de los artículos siguen estando relacionados con los procesos de EDM o ECM (aproximadamente el 50 y el 20%, respectivamente), los procesos híbridos han copado ya el 7% del total y la fabricación aditiva casi el 6%.
Esta ocasión es la segunda en la que se celebra en Bilbao (ya sucedió así en el año 2001) y el congreso ha sido organizado conjuntamente por la Universidad del País Vasco (UPV/EHU) [7] y el centro de investigación IK4-Tekniker [8]. El lugar elegido para presentar los trabajos seleccionados ha sido el Paraninfo de la Universidad del País Vasco (UPV/EHU) de la figura 2.
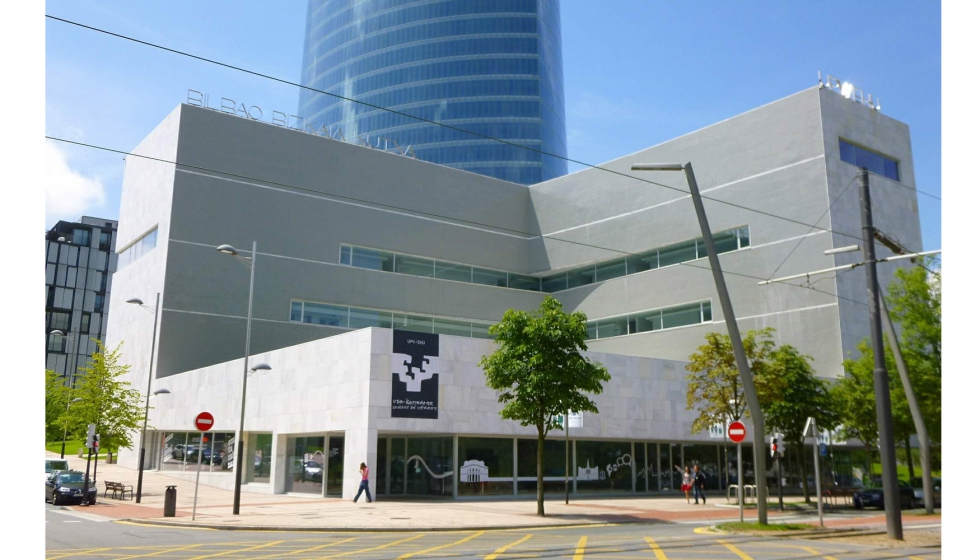
Un espacio para las jóvenes promesas
Otra de las novedades que se ha instaurado este año desde ISEM es la idea del Meeting of Young Researchers. Durante la primera hora de los días centrales del congreso, todos los participantes que fueran autores principales de los artículos enviados y estuvieran matriculados en un programa de doctorado, han tenido la oportunidad de presentar sus trabajos en formato póster con el objetivo de tomar parte en una especie de reunión de expertos. Algunos miembros del comité científico se han acercado por allí para evaluar tanto los artículos y las presentaciones orales de las sesiones como los posters y la explicación que los investigadores noveles puedan dar a los más veteranos y entendidos en la materia. Esta nueva iniciativa propicia la interacción entre dos generaciones de científicos e ingenieros que, de otro modo, no sería probable que pudieran intercambiar sus experiencias, y fomenta la interrelación entre instituciones de diferentes países.
Cabe destacar, además, que los autores con las mejores puntuaciones han recibido como premio una beca de 500 € (se han repartido 10), concedidas por la empresa Ona Electroerosión, las cuales se han repartido durante la cena de gala.
Homenaje al referente de EDM Dr. Xabier Maidagan
En este mismo evento se homenajeó al Dr. Xabier Maidagan Larrunbide por su trayectoria ligada a este sector, quien ha desempeñado la labor de Chairman durante este congreso [9]. Nacido en Bilbao, en 1950, es Doctor Ingeniero Industrial por la Escuela de Ingeniería de Bilbao. Desde el año 1975 su trayectoria profesional ha estado vinculada a la electroerosión mediante su actividad en la empresa fabricante de máquinas Ona Electroerosión [10]. Dos años más tarde, fue responsable del departamento encargado de desarrollar máquinas de electroerosión por hilo y, desde 1990, se erigió como director de I+D en la misma compañía hasta 2004. Posteriormente, su labor se centró en dirigir diferentes entidades como CIC marGUNE o Innobasque [11-12]. Por otra parte, es autor de numerosos proyectos, publicaciones técnicas y patentes en el sector de la máquina herramienta.
Saltaron chispas en ISEM XIX
El ISEM se ha considerado desde hace años como un punto de encuentro de los investigadores más prestigiosos del sector de la electroerosión, por lo que las publicaciones que aquí se presentan son el fiel reflejo de las últimas tendencias en las que se ha sumergido este proceso. Como ya es bien conocido, dentro de esta tecnología existen dos vertientes diferentes: la electroerosión por hilo y la electroerosión por penetración. A continuación, se van a citar las ideas más relevantes de diversos trabajos expuestos, algunos de los cuales, a su vez, han sido galardonados por los premios citados anteriormente dentro del marco de impulsión de los jóvenes investigadores.
- Elecroerosión por penetración
Dentro de este subgrupo, una de las aplicaciones en las que se está centrando la comunidad científica es la fabricación de los denominados blisks, que ha contado con un espacio relevante dentro de las sesiones paralelas llevadas a cabo.
Así, uno de los trabajos publicados y defendidos en este evento trata sobre uno de los retos a los que se enfrenta la electroerosión por penetración: el mecanizado multi-eje [13]. Esta respuesta a las necesidades de los usuarios de este binomio de máquinas y piezas se ha convertido en una solución factible en la fabricación de piezas de geometría complejas de la industria aeroespacial y energética.
Las piezas fabricadas por SEDM (electroerosión por penetración) se ven afectadas principalmente por dos factores: el desgaste del electrodo y el gap. Los fabricantes de este tipo de máquina-herramienta proporcionan información limitada sobre estas características, independientes de la geometría del electrodo y su trayectoria.
Por otro lado, hoy en día, las estrategias utilizadas hasta la fecha de prueba y error que requieren mucho tiempo y coste han dejado de ser una opción en la era de cero despilfarros.
Sin embargo, para poder evitar el uso de estas estrategias se debe de generar una mayor comprensión del desgaste del electrodo y los patrones de distribución del gap, que están relacionados con la geometría del electrodo y su recorrido. Como consecuencia, se podría mejorar el diseño del electrodo y la eficiencia del proceso.
Por lo tanto, los autores proponen el uso de unos indicadores del desgaste y el gap fáciles de llevar a la práctica industrial, siendo esta útil para aquellos casos en los que el valor promedio del desgaste no es suficiente. Estos indicadores han sido probados mediante la fabricación de un blisk por SEDM.
Otro de los documentos expuestos en Bilbao se centra en una nueva estrategia de pulido del electrodo en EDM para las ranuras que suelen realizarse en algunas piezas de la industria aeronáutica [14]. Se ha analizado la viabilidad de recuperación de la cara frontal del electrodo.
Para ello, se estudia la influencia de diferentes materiales y parámetros, empleando un grafito fino como electrodo y un acero de tungsteno y cobre como elementos de trabajo, y registrando variables como el tiempo de secado, el desgaste y la precisión geométrica.
- Electroerosión por hilo
En cuanto a la otra variedad del proceso, el de electroerosión por hilo o WEDM (Wire Electro Discharge Machining), existen numerosas aplicaciones que han sido presentadas durante los días del congreso. Algunas de las más representativas se resumen en los siguientes párrafos, proponiendo además, otras líneas de investigación emergentes que parecen ser el futuro de variedad de procesos de fabricación, tanto convencionales como no convencionales.
Uno de los problemas clásicos y tradicionales del WEDM es la deformación (conocida también como wire-lag) y la vibración del hilo [15]. Muchos componentes de alto valor añadido, principalmente de sectores como el aeroespacial, el médico o el de automoción, se benefician de las estrechas y ajustadas tolerancias que pueden lograrse mediante el uso de la electroerosión por hilo. Sin embargo, existen algunas condiciones particulares bajo las cuales la precisión requerida no se cumple: el corte de geometrías complejas en las que existen radios de acuerdo de pequeño diámetro. Por ejemplo, dentro del sector aeronáutico, se puede observar este tipo de geometrías en los firtrees, piezas como la de la figura 3.
![Figura 3. Ejemplo de la geometría tipo firtree [16] Figura 3. Ejemplo de la geometría tipo firtree [16]](https://img.interempresas.net/fotos/1843437.jpeg)
Por ello, y puesto que aún no se conoce con exactitud el comportamiento vibratorio del hilo, se propone una medición alternativa pero directa de la influencia de la deformación del hilo en la geometría de la pieza. Los métodos clásicos presentados en la literatura son ópticos o se basan en la medición del wire-lag mediante el corte y posterior contacto en la pieza, lo que no es un método completamente exacto. Sin embargo, con esta técnica, el efecto de la deformación del hilo puede medirse directamente tanto para medir trayectorias rectas o incluso circulares de radio pequeño.
Así, mediante un conjunto de pruebas experimentales bajo diferentes condiciones de corte que incluyen el efecto de la variación de la presión del fluido dieléctrico, el radio erosionado y espesor pieza, se analiza el valor de esta deformación en dos direcciones diferentes.
Otro de los temas que se aborda en este mismo artículo es el análisis de los patrones de las descargas, puesto que son varios los investigadores que creen que de las mismas se pueden obtener datos relevantes del proceso de corte [19]. De hecho, el análisis de la gran cantidad de datos que pueden recogerse de los procesos de mecanizado, para posteriormente proceder a su mejora, es una realidad que se contempla en función del tiempo en el que los fabricantes de máquinas-herramienta logren generar una base de datos robusta de los mismos.
Dentro del proceso de electroerosión por hilo se distinguen diferentes formas de llevarlo a cabo, en función de si el hilo es reutilizado o no. Esta variante en la que el hilo vuelve a descargar sobre la pieza se creó en China y, para ello, la velocidad de alimentación del mismo debe ser mayor a la habitual, de ahí su nombre (High Speed WEDM o HS-WEDM). Otro subgrupo es el de velocidad media (Medium Speed WEDM o MS-WEDM), aunque también pertenece a la categoría de HS-WEDM.
En cualquier caso, como en todos los aspectos, encontrar diferentes soluciones tiene tanto ventajas como desventajas. En el caso del HS-WEDM o MS-WEDM, en detrimento de la calidad del corte y la calidad superficial de la pieza, se reduce el coste de mecanizado.
Así, en otro de los artículos se presenta un esquema de diseño para el uso de hilo ultralargo (la longitud del cable es de 10 km) reutilizable [17], que pueda mejorar la precisión de erosión del MS-WEDM y el acabado de la pieza obtenida. Mediante el desarrollo de dos sistemas de rodillos extensibles de velocidad de alimentación variable, consiguen unir un sistema HS-WEDM con otro LS-WEDM o convencional.
Además de estudiar el sistema de alimentación del hilo, se analiza la calidad de la pieza obtenida. Con el método propuesto, la pieza se corta primero, con un hilo de alta velocidad reutilizable y, posteriormente, se realiza un repaso con el hilo de movimiento unidireccional a baja velocidad. De esta forma se eliminan los defectos causados por el primer hilo.
Por último, otro de los artículos relativos al proceso de WEDM con hilo reutilizable es el estudio de corte de piezas de gran espesor y espesor variable mediante esta variante [18]. Cuando los parámetros de corte están ajustados al espesor de pieza, el corte se realiza de forma óptima; sin embargo, cuando este espesor sufre alteraciones, la máquina se enfrenta a los desafíos característicos del WEDM convencional. Esto es, una falta de rendimiento o, incluso, la rotura del hilo. Por tanto, una línea de investigación que lleva años siendo estudiada es, precisamente, la estimación de espesor de pieza en tiempo real.
En este trabajo, se propone un método de estimación en tiempo real del espesor de piezas basado en un método de Inteligencia Artificial denominado Support Vector Machine (SVM). Utilizando como entradas al sistema SVM la frecuencia de descarga, el tiempo de pulso, la velocidad de avance programada y la velocidad de avance real, se pretende generar como salida el espesor estimado. Este algoritmo se integra en el sistema de control numérico, adquiriendo las señales de corriente y tensión generadas por las descargas y, mediante una unidad de control adaptativo, se ajustan los parámetros de erosión de acuerdo con la estimación del espesor de pieza.
Por un lado, los datos para el entrenamiento del SVM se han adquirido mediante la fabricación de piezas con saltos escalonados. Por otro, la verificación se ha llevado a cabo mediante otros cortes de piezas de altura variable en rampa. Aun obteniendo unos buenos resultados, es innegable que las redes neuronales artificiales deben estudiarse de forma más exhaustiva para su aplicación en este sector.
De hecho, este tipo de aplicaciones en las que se utilizan diversos mecanismos de Inteligencia Artificial y redes neuronales artificiales (Artificial Neural Networks, ANNs) están cada vez más de moda, puesto que, al haber demostrado su gran capacidad de resolución de problemas altamente no lineales en otros ámbitos, la naturaleza estocástica de este proceso es el ingrediente principal para la introducción de estas técnicas en este ámbito. Sin embargo, como las soluciones son todavía algo complejas y es necesario explicar de forma exhaustiva la estructura de red elegida, aún queda un largo camino por recorrer para que se usen de forma común y masiva y, por ello, estén presentes en los congresos. Algunos investigadores apuntan hacia este tipo de soluciones [19].
Midiendo la complejidad
Hoy en día existen pocos sectores donde los componentes sean tan complejos como en el sector aeronáutico. La eficiencia y el rendimiento del motor imponen diseños donde las formas regladas se sustituyen a menudo por geometrías libres más propias de los Relojes Blandos de Dalí. Así, no es difícil de imaginar que el proceso de fabricación y control geométrico y dimensional de estos componentes se convierta en un reto.
Ejemplos de este tipo de componentes son los IBRs, Blisk o NGVs donde, además, en algunos casos ya se está solicitando el control del 100% de la geometría (digitalización completa del componente). Esta tendencia necesita nuevas tecnologías de medición, más rápidas y precisas.
Actualmente existen en el mercado 3 tecnologías capaces de hacer frente a este reto: medición en Máquina de Medir por Coordenadas (MMC) en 5 ejes simultáneos con cabezal Revo? (Renishaw), medición en CMM en 3+2 ejes con escáner láser y sistema de medición con luz estructurada. Todos ellos son capaces de obtener grandes cantidades de puntos con suficiente precisión (en condiciones óptimas), si bien el tiempo de medición varía entre unos y otros. Para entender estos sistemas se van a describir a continuación las características generales de cada uno de ellos.
1. Sistema de medición en CMM con cabezal Revo:
Es un sistema integrado en una CMM con una unidad de control capaz de realizar movimientos en 5 ejes de forma simultánea. La configuración estructural típica de este sistema es de 3 ejes lineales en la máquina y 2 ejes rotativos en el cabezal. La precisión de este sistema es la más elevada de cuantos se exponen en este escrito como alternativas y ronda las 2µm (a falta de combinarla con la de la CMM). La capacidad de adquisición de puntos del sistema es elevada (miles de puntos por segundo a velocidades máximas de 500mm/s), si bien depende fuertemente de la unidad de control, de la capacidad del ordenador asociado a la máquina y de la velocidad máxima de medición que permita una medición con suficiente precisión. Dicho de otra forma, la capacidad es excelente, pero no siempre se puede aprovechar al máximo debido a que las inercias del sistema a grandes velocidades penalizan la precisión obtenida en la medida.
En el caso de los componentes en estudio, se recomienda que la velocidad máxima de avance del palpador sobre la pieza no supere los 30mm/s (recomendación de Mitutoyo).
2. Sistema de medición en CMM con escáner láser:
En este caso nos encontramos ante un sistema de medición sin contacto dependiente de las propiedades ópticas de la superficie del objeto de medición. Presenta capacidad para adquisición de nubes de puntos densas, lo que reporta, en pocos segundos, millones de puntos medidos que se deben procesar posteriormente. La precisión de estos sistemas está mejorando año a año y, actualmente, existen modelos que garantizan una precisión de 2µm bajo condiciones óptimas de medición (a falta de combinarla con la de la CMM). La limitación más importante para que sea empleado de forma extensiva es la accesibilidad a la zona a medir. En este tipo de componentes complejos, con una CMM con 3+2 ejes, pueden aparecer zonas de sombra para el láser imposibles de medir lo que implica la necesidad del empleo de sistemas híbridos (contacto+óptico) para completar la medición del componente.
3. Sistema de medición basado en luz estructurada:
Este último sistema permite en muy poco tiempo la adquisición de la geometría de una pieza de tamaño medio obteniendo une nube de puntos densa. La precisión es algo inferior a la del escáner láser (alrededor de las 10µm) pero es un sistema mucho más veloz. Su principio de medida se basa en la triangulación láser, pero empleando fotogrametría en vez de un sensor láser, de modo que se emplean dos cámaras situadas en ángulos diferentes (estereoscopia) y conocidos (calibrados), que miden un patrón de luz proyectado sobre la pieza de trabajo. De esta forma obtiene las coordenadas XYZ de los puntos del patrón mediante triangulación entre las cámaras y el foco de luz. En función del patrón de luz empleado (fijo, dinámico, colores, etc.) la precisión del sistema puede variar.
La limitación fundamental de la luz estructurada es la misma que presenta el resto de sistemas ópticos, es decir, la imposibilidad de adquirir puntos de la superficie en zonas denominadas “de sombra” donde la luz no llega. En este caso, sin embargo, se compensa parcialmente esta limitación colocando el componente a medir en un robot de modo que la accesibilidad de la luz se ve mejorada con la libertad de movimientos.

Referencias
[1] F. Klocke, D. Welling, A. Klink, R. Perez. Quality Assessment through In-process Monitoring of Wire-EDM for Fir Tree Slot Production. Procedia CIRP, 24 (2014) 97-102.
[2] F. Klocke, D. Welling, A. Klink, D. Veselovac, T. Nöthe, R. Perez. Evaluation of Advanced Wire-EDM Capabilities for the Manufacture of Fir Tree Slots in Inconel 718. Procedia CIRP, 14 (2014) 430-435.
[3] F. Klocke, D. Welling, J. Dieckmann, D. Veselovac, R. Perez. Developments in Wire-EDM for the Manufacturing of Fir Tree Slots in Turbine Discs Made of Inconel 718. Key Engineering Materials, 504-506 (2012) 1177-1182.
[4] F. Klocke, R. Schmitta, M. Zeis, L. Heidemanns J. Kerkhoff, D. Heinen, A.Klink. Technological and Economical Assessment of Alternative Process Chains for Blisk Manufacture. Procedia CIRP, 35 (2015) 67-72.
[5] F. Klocke, M. Zeis, A. Klink, D. Veselovac. Technological and Economical Comparison of Roughing Strategies via Milling, EDM and ECM for Titanium- and Nickel-based Blisks Procedia CIRP, 2 (2012) 98-101.
[7] https://www.ehu.eus/es/web/ingeniaritza-bilbo/hasiera
[11] https://www.bicgipuzkoa.eus/cic-margune/
[12] https://www.innobasque.eus/
[13] O. Flaño, I. Ayesta, B. Izquierdo, J. A. Sánchez, J.M. Ramos. Experimental study on the influence of electrode geometry and electrode path on wear pattern in EDM. Procedia CIRP 68 (2018) 405-410.
[14] H. Bravo, I. Ayesta, J. A. Sanchez, I. Zamakona, B. Izquierdo, O. Flaño, J.del Campo. Study of Interpolation Strategies to Dress Electrodes by Means of EDM. Procedia CIRP, 68 (2018) 393-398.
[15] A. Conde, J. A. Sanchez, S. Plaza, M. Ostolaza, I.de la Puerta, Z. Li. Experimental Measurement of Wire-lag Effect and Its Relation with Signal Classification on Wire EDM. Procedia CIRP, 68 (2018) 132-137.
[16] http://www.geograph.org.uk/photo/3565152
[17] C. He, J. Zhao, J. Liu. Ultra-long Wire Reciprocated-WEDM with Dual Tensile Reels Winded?Procedia CIRP 68 (2018) 115-119.
[18] G. Huang, W. Xia, L. Qin, W. Zhao. Online Workpiece Height Estimation for Reciprocated Traveling Wire EDM Based on Support Vector Machine. Procedia CIRP, 68 (2018) 126-131.
[19] A. Caggiano, R. Perez, T. Segreto, R.Teti, P. Xirouchakis. Advanced Sensor Signal Feature Extraction and Pattern Recognition for Wire EDM Process Monitoring. Procedia CIRP, 42 (2016) 34-39.