Entrevista a Fernando Lasagni, director de la División de Materiales y Procesos del Centro Avanzado de Tecnologías Aeroespaciales
La Sociedad Alemana de Materiales (Deutsche Gesellschaft für Materialkunde) entregó el pasado mes de septiembre a Fernando Lasagni, director de la División de Materiales y Procesos del Centro Avanzado de Tecnologías Aeroespaciales (Catec), el premio internacional Georg-Sachs-Preis que cada año concede con el fin de reconocer el trabajo y proyección científica de aquellos investigadores que están estrechamente relacionados con la práctica de la ciencia y la ingeniería de los materiales. El premio reconoce el trabajo de Lasagni y su equipo en la aplicación de la fabricación aditiva e impresión 3D a nuevos usos en el campo aeronáutico y espacial, como son la producción de componentes para lanzadores espaciales, satélites, misiones científicas de la Agencia Espacial Europea y aeronaves civiles y militares. Un trabajo que nos detalla él mismo a continuación.
Con su experiencia en la fabricación aditiva para el sector aeronáutico, ¿cuáles son los principales avances realizados en los últimos años? Es decir, de prototipos a piezas funcionales.
Desde el Centro Avanzado de Tecnologías Aeroespaciales (Catec) venimos trabajando con la tecnología desde hace casi una década y hemos sido testigos y actores del avance sostenido de la fabricación aditiva. Por un lado, a nivel de sistemas de fabricación hay una oferta mucho más amplia, y por otro, la fiabilidad, repetitividad y productividad de los equipos ha mejorado mucho. A nivel de componentes y específicamente para el sector aeroespacial, solo en Catec hemos trabajado en el desarrollo de un centenar de elementos, muchos de los cuales han sido validados en entorno relevante bajo condiciones de operación y otros que están siendo embarcados para vuelo, como es el caso de diversos desarrollos que hemos realizado para satélites de telecomunicaciones y científicos para la Agencia Espacial Europea (ESA).
¿Qué tecnología, de las disponibles, es la más adecuada para este sector?
Dependerá de la aplicación y del grado de certificación de la tecnología. Para la fabricación de utillaje se están consiguiendo resultados muy interesantes en tecnología de fabricación de plástico por FDM. Aquí la ventaja principal no es solo la reducción de costes sino la mejora en los tiempos de entrega. Después, en piezas no críticas el plástico también ha conseguido posicionarse en varios part numbers de aviones comerciales, mientras que, en cuanto a la fabricación metálica, los esfuerzos de los grandes fabricantes de aeronaves, satélites, lanzadores, etc., ha sido en la tecnología de fusión de lecho de polvo, por su madurez tecnológica y también por las prestaciones de los componentes que se consiguen. Actualmente, existe normativa para la certificación de equipos y cualificación/certificación de componentes, por lo cual las empresas ya conocen las reglas de juego para poder ofrecer servicio de fabricación.
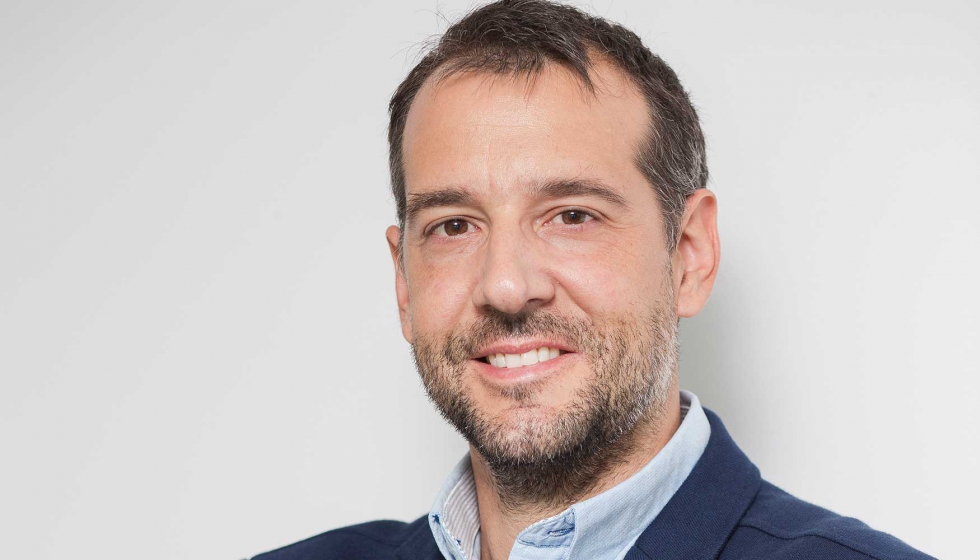
Y en cuanto a materiales, ¿cuál es la disponibilidad actual y qué carencias se detectan?
Primero hay que diferenciar entre materiales certificados y emergentes. Para el sector ya están certificados varios termoplásticos y en cuanto a metales, sin lugar a duda, es el titanio, particularmente el Titanio 6 Aluminio 4 Vanadio, el material en el que se posee la mayor madurez tecnológica. Le siguen los aluminios AlSi10Mg y el Scalmalloy, aleaciones que ya están siendo embarcadas, por ejemplo, en el satélite Proba3 donde desarrollamos un proyecto en colaboración con Tryo Aerospace para la fabricación de una antena, o el caso de brackets estructurales para el lanzador Vega fruto de una colaboración con Airbus Defence & Space y la ingeniería CiTD. Por otra parte, a nivel de motores, el Inconel es uno de los materiales más desarrollados y que está siendo certificado por varios fabricantes de motores. A nivel de investigación se está trabajando en el desarrollo de diversas aleaciones, principalmente para definir sistemas de aleación ideales para la fabricación aditiva, y no realizar solo una extrapolación de otros métodos de fabricación como la fundición, forja, extrusión, etc. Aquí se destacan el desarrollo de nuevas aleaciones de aluminio, de titanio y de alta temperatura principalmente. Finalmente, y como no puede ser de otra manera en este sector, hay una gran necesidad en el desarrollo de materiales compuestos. Aquí no solo hablamos de desarrollar un material sino también sistemas/conceptos de fabricación que permitan distribuir una fibra continua de material en 3D.
¿Cuáles son los requisitos en cuanto a certificaciones para la fabricación aditiva aplicada a la aeronáutica? A menudo se dice que las normativas van por detrás de la tecnología. ¿Es así?
La normativa siempre va por detrás de la tecnología. Para conseguir normativa se debe tener primero la experiencia suficiente en la materia que permita definirla. Quienes hayan trabajado en este país en la implantación de los materiales compuestos lo saben muy bien. Certificar componentes críticos ha costado muchos años porque era necesario un gran conocimiento de los materiales y de los procesos de fabricación.
Luego, la certificación de la fabricación aditiva en la aeronáutica consiste en certificar todos los procesos de la cadena de valor, no solo el sistema de fabricación. Aquí nos enfrentamos a varios retos: por ejemplo, en fabricación metálica no hacemos una recepción de un material por lote como puede ser para el caso del mecanizado. Recibimos una materia prima en polvo, la cual reciclamos y reutilizamos, por lo cual nuestra materia prima se va modificando durante el proceso. Solo este punto ha dado varios dolores de cabeza a la hora de determinar los métodos de control y almacenamiento del polvo metálico. Posteriormente debemos controlar todos los posprocesos, como los tratamientos térmicos, tratamientos superficiales, etc. Y, para terminar, definir la tecnología de inspección, donde hoy en día la tomografía computarizada tiene un rol principal. Esta última era casi una desconocida para el sector aeronáutico. Aquí realmente es donde centros como Catec, con un conocimiento global de todos los procesos, han sido claves para volar la tecnología. En 2016 junto con Airbus DS, Space Systems, en Madrid, fuimos capaces de validar frente a la Agencia Espacial Europea (ESA) los protocolos de fabricación y verificación de todos los procesos involucrados en la fabricación de estructura crítica de vuelo, como son los soportes de los paneles solares del satélite de telecomunicaciones Quantum. Y fue un reto porque no había una normativa establecida y tuvimos que trabajar desde 2014 en establecer los métodos de control.
En los próximos años la fabricación de aeronaves crecerá empujada en parte por la necesidad de renovar flotas y la exigencia de reducir el consumo de combustible. ¿Qué papel puede jugar aquí la fabricación aditiva?
En el espacio la fabricación aditiva definitivamente tendrá un rol muy importante. El impacto en la reducción de peso por optimización es muy grande tanto para reducir el peso de una misión/satélite, reducir costes de lanzamiento y los tiempos de entrega. Desde el punto de vista aeronáutico, las aplicaciones más importantes que se vislumbran son en componentes de titanio. Es aquí donde se obtiene en muchos casos una ventaja competitiva en coste, y tras una optimización también en peso. La implementación de la tecnología también dependerá del aumento de productividad de los sistemas de fabricación. Varios fabricantes están trabajando en ello, como es el caso de Renishaw, con una nueva gama de sistemas muy industriales. Luego, la tecnología puede tener un impacto en la personalización o en aviones de series más cortas, como los militares.
¿Un avión impreso íntegramente en 3D sería factible? ¿Es necesario o sería básicamente un reto para los ingenieros?
Le respondo con otra pregunta: ¿un avión fabricado por laminado de chapa o extrusión de aluminio es viable? La fabricación aditiva será uno de los procesos que se utilice para fabricar componentes de avión, pero cada proceso tendrá su lugar cuando sea viable económica y tecnológicamente. Los retos de los ingenieros ahora mismo se concentran en desarrollar equipos que permitan fabricar componentes de grandes dimensiones. Equipos que luego, además, habrá que certificar y desarrollar una normativa ad-hoc.
Personalmente, ¿cuándo se planteó integrar la fabricación aditiva en la aeronáutica, y por qué?
Precisamente hace 10 años, cuando me incorporé a Catec, estuve en contacto con las empresas aeronáuticas analizando sus necesidades y también realizando un estudio exhaustivo de las tecnologías emergentes. Hubo dos tecnologías de las cuales no tuve ninguna duda que debían integrase a nuestra cartera: en primer lugar, la tomografía computarizada, por sus posibilidades prácticamente ilimitadas en la inspección de componentes complejos, análisis de fallo en servicio o en producción, y para validar otras tecnologías de inspección; y en segundo lugar, la fabricación aditiva en metal. De mi actividad anterior en Austria conocía ambas tecnologías, pero en el caso de la fabricación aditiva se trataba de piezas fabricadas por SLA en plástico. Cuando vi que se podía fabricar una pieza metálica a partir de polvo, sinceramente fue espectacular. Solo pensar en las geometrías que se podían desarrollar y compararlo con otros procesos de fabricación convencionales fue revelador. Esta segunda decisión también hizo que refuerce la primera, porque fabricar piezas imposibles requiere en el sector aeronáutico de tecnologías de inspección muy versátiles, como la tomografía.
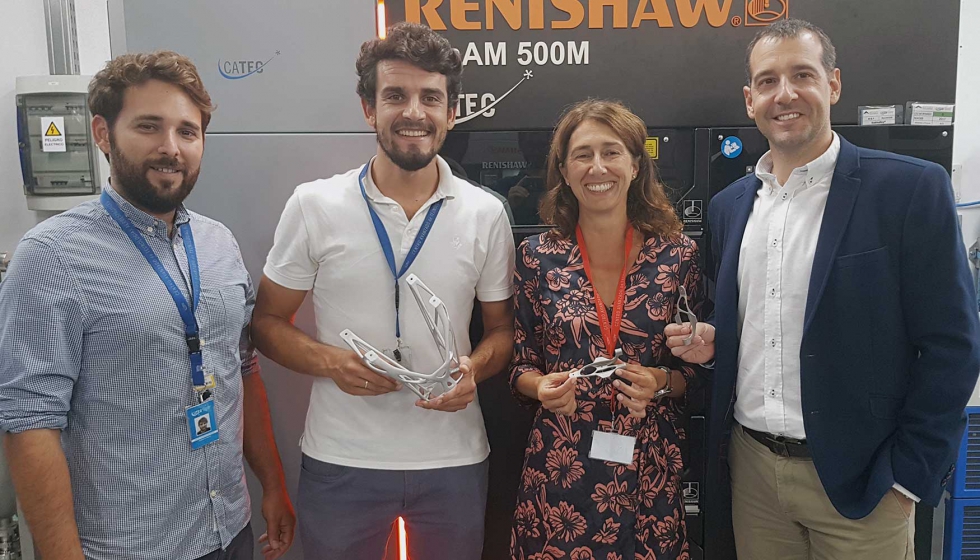
Esta trayectoria le ha supuesto el reconocimiento de la Sociedad Alemana de Materiales con el premio Georg-Sachs-Preis. ¿Qué supone este premio para Catec y para usted particularmente?
Los premios muchas veces son individuales, pero son al final el reconocimiento del trabajo de un equipo. El Georg Sachs Preis es el reconocimiento a todo el equipo de Catec que ha puesto su granito de arena en el desarrollo de la tecnología. Hablamos de una trayectoria que abarca aplicaciones para aeronaves como los aviones Airbus A400M, C295, p A320neo, los lanzadores Vega y Ariane 5, los satélites Cheops, Quantum, ProbaA3, entre otros, el helicóptero Racer o el regional aircraft del programa Clean Sky 2. Y por delante de todo, el agradecimiento a las empresas, porque nuestra misión es brindarnos a ellas y ayudarlas a introducir las tecnologías del futuro. Todo esto hubiese sido imposible sin la confianza de empresas como Airbus Defence & Space, CiTD, Airgrup, Tryo Aerospace, Airbus Helicopters, Alestis, Inespasa, Aernnova, CT Ingenieros, Renishaw, la Agencia Espacial Europea, y muchos otros. Más importante aún, esta experiencia acumulada nos permitirá volar a cientos de millones de kilómetros de la tierra en una misión espacial que anunciaremos en breve.
El Dr. Fernando Lasagni es en la actualidad uno de los pioneros en la introducción de la fabricación aditiva (conocida popularmente como impresión 3D) en el sector aeroespacial en Europa, un campo en el que se imponen exigencias extremas a los componentes y piezas de lanzadores o satélites. Desde 2014, forma parte de la delegación española en los encuentros de armonización tecnológica de la fabricación aditiva liderados por la Agencia Espacial Europea y, desde 2016, coordina el grupo de fabricación aditiva de la Plataforma Aeroespacial Española (PAE). Por sus innovaciones y avances en este campo, ha recibido junto a su equipo numerosos premios y distinciones de carácter industrial. Entre ellos, el prestigioso premio científico internacional Georg-Sachs-Preis, que cada año concede la Sociedad Alemana de Materiales (Deutsche Gesellschaft für Materialkunde), entregado recientemente, en reconocimiento por su trabajo en el campo de la aplicación de la tecnología de fabricación aditiva a nuevos usos en el campo aeronáutico y aeroespacial, como son la producción de piezas para los lanzadores espaciales Ariane 5 y Vega, y para diferentes aviones y aeronaves de Airbus como el A400M, el C295 o el A320neo y helicópteros de última generación como el nuevo RACER, también del grupo Airbus.
Nacido en Cinco Saltos, provincia de Río Negro (Argentina), Fernando Lasagni estudió Ingeniería Química en la Universidad Nacional del Comahe (Neuquén). En 2002 se trasladó a Viena (Austria) donde realizó su tesis doctoral en el área de materiales compuestos de matriz metálica (MMC) y aleaciones ligeras para uso en motores de automóviles, cuyos resultados fueron reconocidos con el Premio Fritz Grasenick de la Sociedad Austríaca de Microscopía Electrónica como el mejor artículo del año 2007. Estos trabajos siguen siendo la base para una comprensión más profunda, así como la base del desarrollo de procesos y materiales en el campo de la fabricación aditiva.
Desde el año 2008 Fernando Lasagni es jefe de la División de Materiales y Procesos del Centro de Tecnologías Aeroespaciales Avanzadas (Fada-Catec) en Sevilla, puesto para el que fue reclutado tras un breve paso por la empresa española lberEspacio.