Industria 4.0: predicción de fallos por Kfew Systems
Jordi Batet Torras, Kfew Systems
30/09/2019La implantación de la Industria 4.0 está basada en un alto grado de integración de la gestión de la maquinaria y de los procesos. La posibilidad de monitorizar, adquirir y evaluar de forma automática gran cantidad de datos que afectan a la maquinaria e instalaciones, se convierte en la herramienta más preciada para el aumento de la calidad y de la productividad. No obstante, los datos solos no facturan, sino los recursos de producción. Las máquinas de la Industria 4.0 deberán dotarse de medios que minimicen sus paros. Más aún, aquellos paros incontrolados que más daño hacen a la planificación y cumplimiento de compromisos.
Siempre romperá el eslabón más débil
Esta afirmación es tan certera que ha permitido diseñar sistemas que tengan predeterminados sus puntos de rotura: Fusibles eléctricos, mecánicos o hidráulicos. En una situación de sobrecarga, “rompen” por donde se ha previsto. Dejan al sistema inoperativo, pero con daños confinados y con relativamente fácil reparación.
Detección de los fallos
El gráfico que sigue muestra la evolución más generalizada en que se visualizan los fallos antes del colapso de la máquina. Dependiendo de la naturaleza de la avería y del porcentaje de carga, la escala temporal puede variar, no obstante, los síntomas son prácticamente invariables.
La curva en verde muestra los costes a soportar en función de la anticipación en la detección de los fallos. Como siempre, los costes reales pueden ser mucho más exagerados al factor x5, ya que fallos en instalaciones críticas y/o en temporadas críticas pueden tener un impacto notablemente superior.
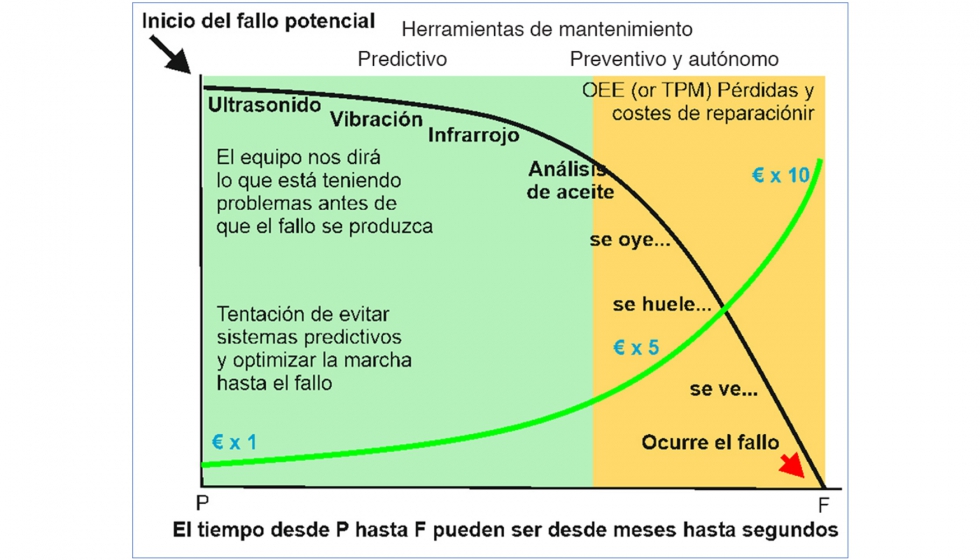
Evolución costes reparaciones.
¿Por dónde se averían las máquinas?
Los accionamientos y transmisiones, como partes móviles y portadoras de la potencia absorbida por la máquina, son los principales orígenes de las averías. Dentro de los fallos de la cinemática, los motores, por sus velocidades más elevadas, suelen acumular el mayor número de incidencias.
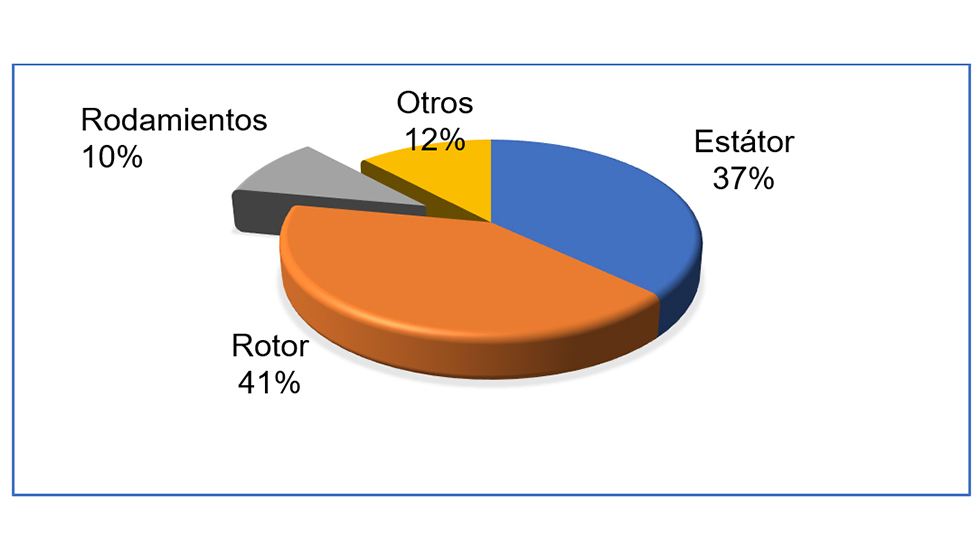
Porcentajes generales fallos motor.
Los datos estadísticos atribuyen el 41% de fallos al rotor del motor, mientras que sólo un 10% a los rodamientos. El gráfico que sigue muestra la tipología y porcentaje de estos fallos:
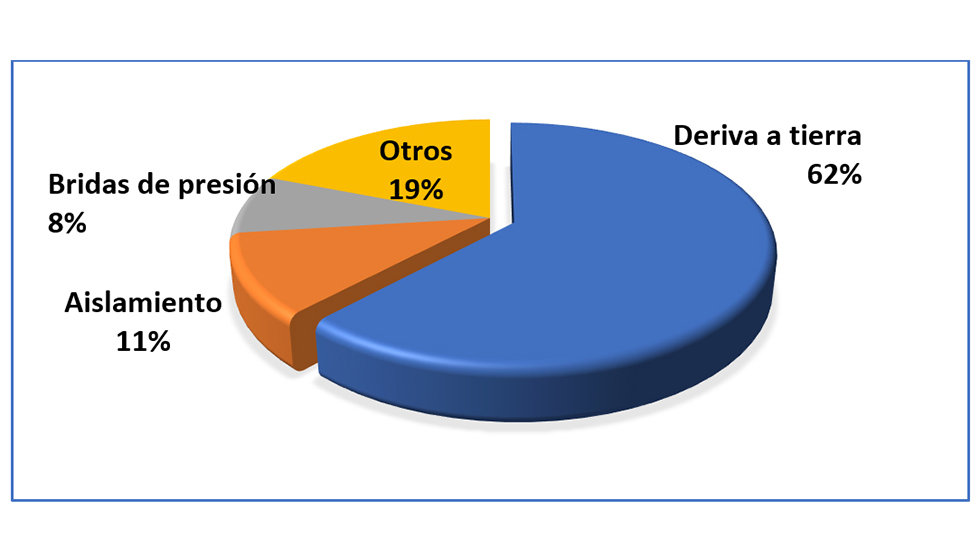
Tipología y porcentaje de fallos.
El siguiente mayor porcentaje de fallos de los motores de inducción está en el rotor y dentro del mismo, las grietas en las barras y la integridad del eje son los mayores generadores de problemas.
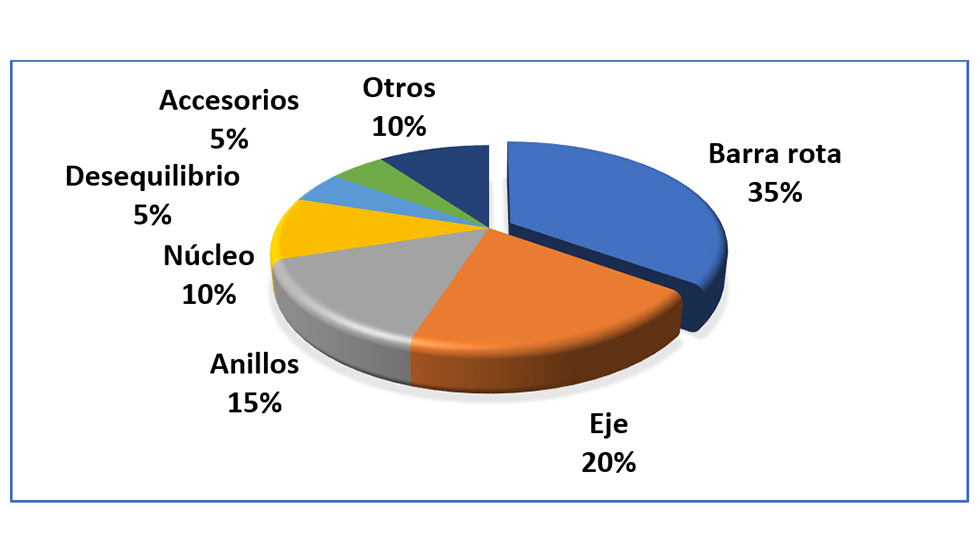
Porcentaje de fallos de rotor e interior del mismo.
Además del motor, el resto de los elementos de mando, regulación, control y transmisión mecánica son igualmente susceptibles de fallos, las mismas consecuencias que el propio motor. En el gráfico se muestran las causas que pueden producir los fallos.
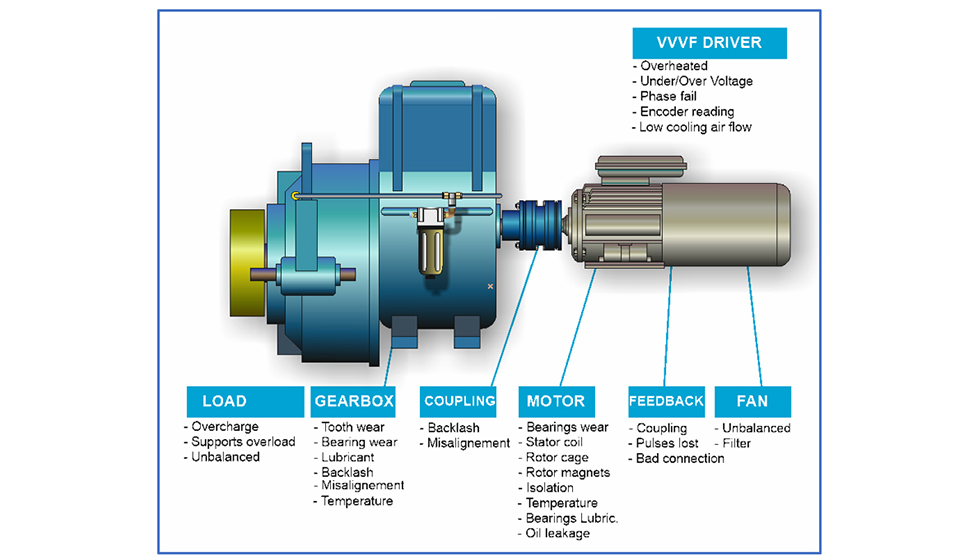
Elementos donde se producen los fallos.
Medios predictivos y cobertura de riesgos
En el mercado se presentan diversas categorías de familias de instrumentos de predicción de fallos, claramente diferenciados en prestaciones, facilidad de instalación y costes.
El primer criterio de decisión debería basarse siempre en las prestaciones del aparato y su capacidad de evaluar la gravedad de los fallos detectados. Al igual que un seguro, los costes del material instalado deberán estar de acuerdo con la cobertura deseada. No es lo mismo la bomba de agua del surtidor que la refrigeración de una central nuclear.
En este sentido cabe referirse a los gráficos mostrados anteriormente. Si las posibilidades de fallo eléctricas de un motor son mucho mayores que las de los rodamientos, las coberturas por vibración, aún siendo las más simples, no son las que mayor cobertura de riesgo aportan. Por otro lado, cambiar los rodamientos es mucho más rápido y económico que rebobinar el motor.
Teniendo en cuenta la diversidad en la progresión temporal de los fallos (Tiempo entre la primera manifestación medible y el colapso), los aparatos no conectables a red de datos (Wifi), no son considerados como elemento fiable, ya que no pueden asegurar una monitorización continua.
Las hojas de datos publicadas de cada producto deben formar parte del primer filtro de selección. Es muy importante observar el detalle de la información transferida, ya que no tiene nada que ver el fijar un umbral de amplitud de vibración para generar la alarma que la evaluación espectral en banda ancha de la vibración para determinar el origen de la misma.
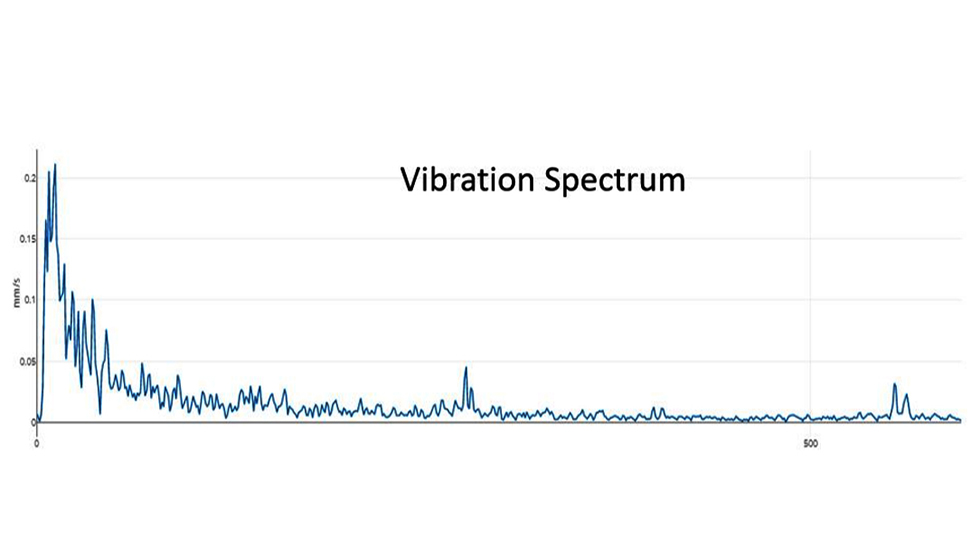
Espectro de vibraciones del motor.
También es resaltable que los datos obtenidos sean presentados en formatos claros, fácilmente comprensibles y que complementen las medías realizadas con diagnóstico y predicción lo más precisa posible del tiempo operativo remanente. El mejor resultado se obtiene facilitando datos elaborados, fácilmente interpretables, complementados en toda la información detallada que ha permitido su elaboración, además de la comparación histórica.
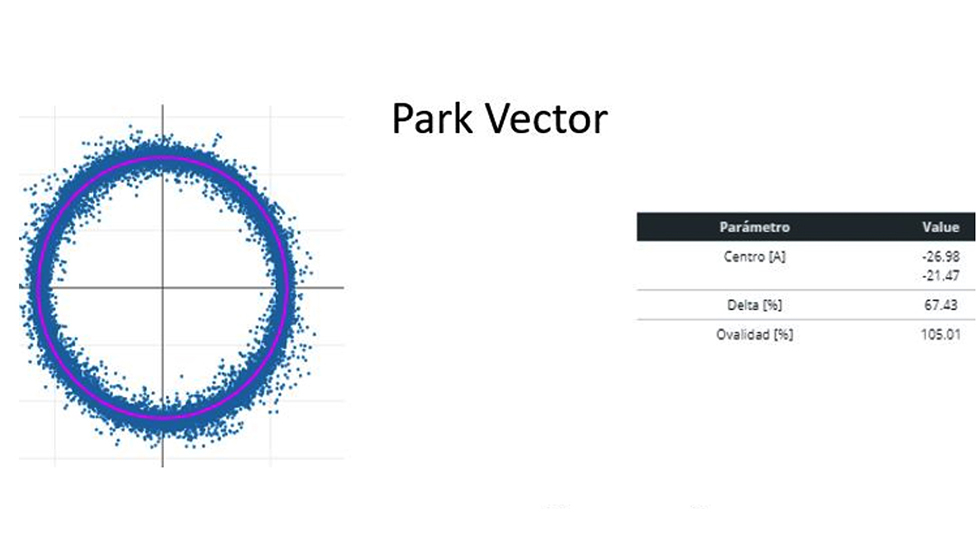
Diagrama del vector de Park.
Contra el criterio de valorar la facilidad de instalación de aparatos autónomos, alimentados con baterías, debería siempre considerarse que en una planta industrial suele ser mucho más rentable usar sistemas no dependientes del mantenimiento (recambio de baterías) para evitar falta de supervisión justo cuando se está generando un fallo.
En el extremo más alto de gama están los sistemas modulares, con capacidad para varios sensores y con la supervisión y procesado de todos los valores eléctricos, incluidos aislamiento, diagrama de Park, temperatura de bobinados, diagrama de fasores, etc. Sistemas que puedan supervisar toda la cadena cinemática, incluidos los codificadores de realimentación del motor o las dimensiones de las partículas del aceite.
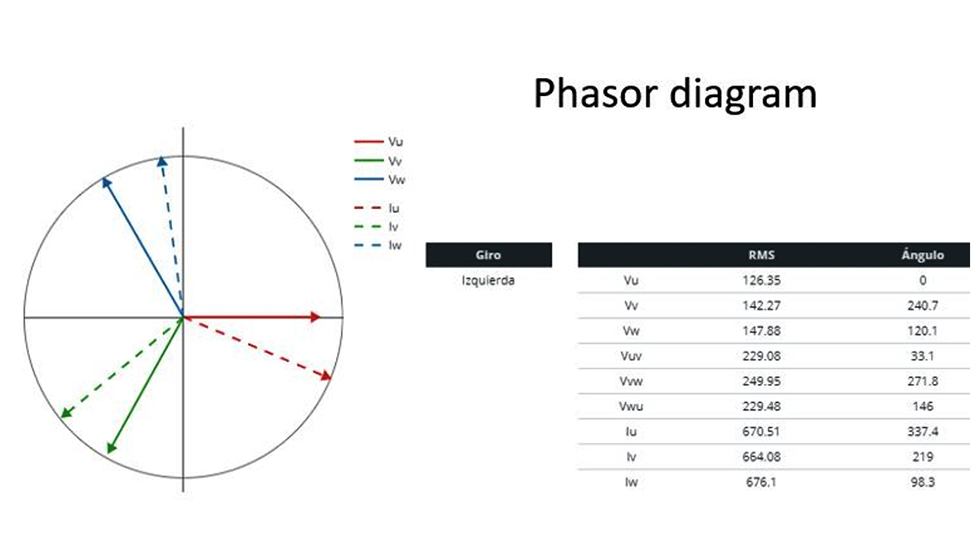
Diagrama de fasores completo.
Otro criterio de decisión complementario está en la especialización del aparato al propósito específico de monitorización en tiempo real en ambientes industriales o incluso en clasificados. Un factor de forma modular en Rack de 19” puede cubrir perfectamente las especificaciones, pero los costes para su implementación en un ambiente industrial pueden ser exagerados.
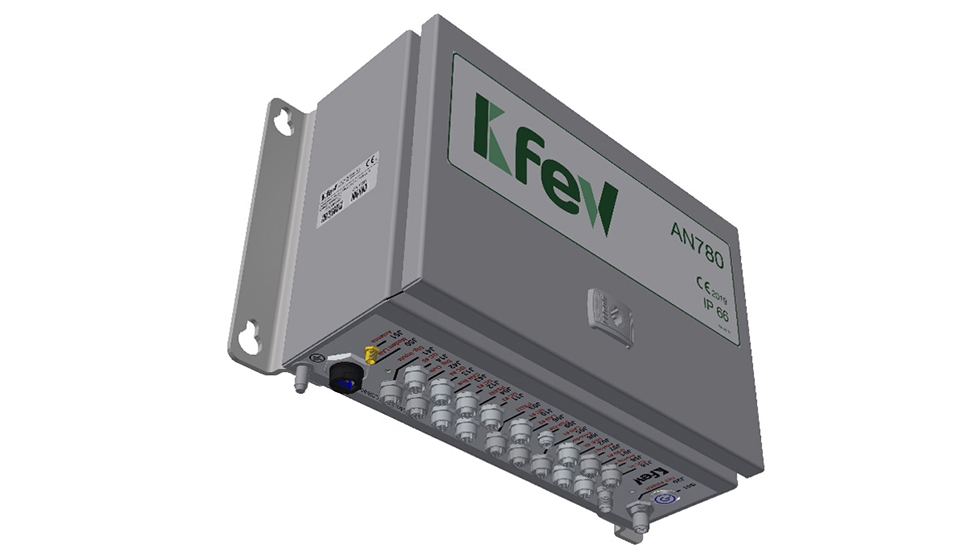
Otra ventaja destacable de sistemas de supervisión especializados es su capacidad de “filtrar” los datos adquiridos. Los filtros permiten eliminar adquisición de datos en aquellas situaciones temporales conocidas donde éstos no son representativos y con ello poder ajustar mejor los umbrales de alarma, eliminando las falsas alarmas y generando con ello más confianza en el sistema.
Nunca se podrá asegurar una instalación al 100% libre de fallos, ya que existen accidentes externos o defectos originales en componentes de la cadena cinemática. En los accidentes fortuitos es prácticamente imposible generar alertas anticipadas. No obstante, utilizando sistemas especializados en la cobertura específica de los fallos eléctricos y físicos de motores, la cinemática y las transmisiones mecánicas, más del 95% de averías pueden ser detectados y evaluados en su fase inicial. Con las ventajas de la información en la nube, el diagnóstico asistido y la predicción forman un importante eslabón de la Industria 4.0.
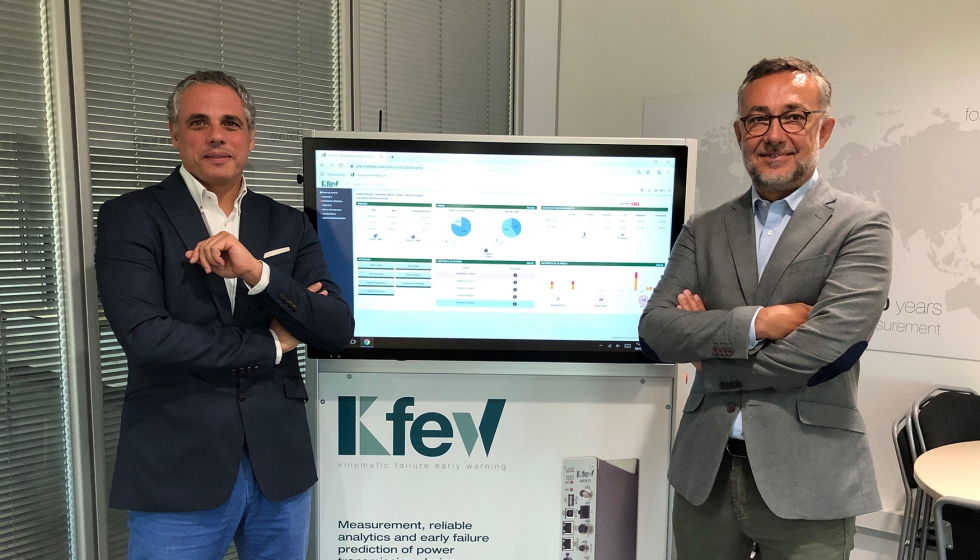
De izquierda a derecha, Albert Ginestà y Jordi Batet Santcliment, director general y consejero delegado de Kfew Systems, respectivamente.
Sobre el autor
Con más de 30 años de experiencia en ingeniería de diseño de sistemas automáticos y mantenimiento de instalaciones industriales, Jordi Batet Torras es miembro de IEEE y del equipo de diseño de Kfew Systems.