Aseguramiento de la fiabilidad de las MMC
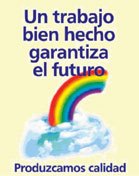
La medición es la acción de determinar la longitud, extensión, volumen o capacidad de algo. Ya hace años que la industria ha estado siempre muy interesada en saber como se produce. Prueba de ello es que la mayoría de empresas están realizado un gran esfuerzo para invertir en la adquisición de instrumentos y aparatos de medida y control.
Con las implantaciones de las nuevas tendencias de la calidad total, la industria está obligada a mejorar sus sistemas de producción y para ello es preciso el aseguramiento de las mediciones y de los elementos con que son realizadas.
Para controlar la calidad en la producción es necesario medir parámetros, y lo que es más importante, hay que cuantificar la calidad de la medida.
Por tanto resulta que metrología, calibración y verificación van de la mano en el aseguramiento de la medida, puesto que todas las mediciones están en dependencia directa del equipo o máquina de control.
Según la norma UNE EN ISO 14253-1 (1998). Especificación geométrica de productos GPS. Inspección mediante medición de piezas y equipos de medida. Parte 1:
“Cuando se verifica cualquier especificación geométrica de cualquier pieza, se debería tener en cuenta la incertidumbre de medición”.
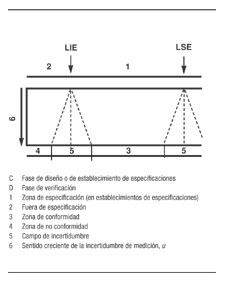
Incertidumbre de Medición:
La incertidumbre de medida permite la mejora de la calidad en la ejecución de una medición ya que refiere a un entorno del valor proporcionado por la medida donde es probable que se encuentre el valor real.
Existen muchos y varios factores que pueden contribuir a la incertidumbre de medida.
Algunas de las causas mas frecuentes de incertidumbres en la medida pueden ser las siguientes:
- Condiciones de la medición (temperatura, humedad, vibraciones, etc.).
- El equipo de medida (incertidumbre de la calibración, coeficientes de dilatación, resolución, etc.).
- La realización.
- El procedimiento de la medida.
- Las características GPS.
- La persona que realiza la medición.
- Etc.
Uno de los factores que contribuyen a la incertidumbre de medida mencionada anteriormente es el propio equipo de medida, en nuestro caso la MMC (máquina de medición por coordenadas).
Conocer a fondo como se comportan las MMC’S ha sido siempre uno de los principales retos de Dea, por ello dispone de un potente y avanzado centro de investigación y desarrollo en su sede central en Torino (Italia).
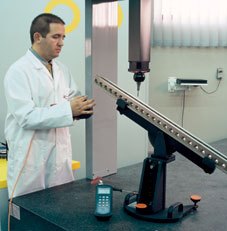
Aseguramiento de la fiabilidad de las MMC
Para asegurar un correcto funcionamiento de la CMM y una buena fiabilidad de las mediciones realizadas, se deberían seguir unas determinadas pautas de control de la CMM.
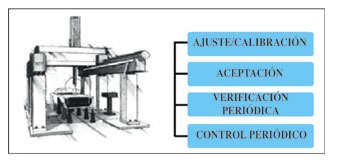
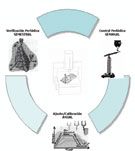
Aunque la avanzada tecnología de fabricación permite tolerar y hacer piezas de forma muy precisa, aún existen imperfecciones. Por pequeñas que éstas sean, que existan tolerancias significa que existen errores.
Las máquinas de medición por coordenadas no son diferentes a otros productos en este aspecto. Aunque están hechas con tolerancias muy ajustadas, hay errores en su estructura (errores de rotación, rectitud, ortogonalidad, cedimientos, y escala) que afectan a su eficacia. Cuanto más ajustadas sean las tolerancias, más precisas tendrán que ser las MMC.
La mayoría de las imprecisiones de las MMC se pueden corregir automáticamente en el ordenador de la propia MMC. Una vez medidos todos los errores geométricos de la MMC se pueden minimizar o incluso eliminar con potentes algoritmos de software. Ese proceso se conoce como compensación del error volumétrico. Con la eliminación matemática de errores se reduce el coste de fabricación.
En este aspecto habría que considerar que estas imprecisiones o errores geométricos de las MMC deberían ser periódicamente controlados y compensados, para asegurar la fiabilidad de las mediciones realizadas.
Bajo nuestra experiencia, de años de trabajo y como fabricantes de MMC’S Dea recomienda, para un buen funcionamiento y una buena fiabilidad de las MMC’S que se realicen anualmente dichos ajustes (calibración y corrección).
Así mismo habría que considerar la importancia de que las correcciones, que se realizan a cualquier MMC (ajustes geométricos totales o parciales) sean siempre realizadas por el fabricante, ya que es este, el que mejor conoce el sistema (tanto la MMC, como el software de compensación).
Aceptación - Verificación periódica:
Entre las normas internacionales que regulan la Metrología por coordenadas se encuentra la Norma ISO 10360.
Esta norma en su parte 2 se ocupa de los ensayos de aceptación que verifican las especificaciones del fabricante de las MMC utilizadas para la medición de dimensiones. También especifica los ensayos de verificación periódica que permiten al usuario comprobar las prestaciones de las MMC para medición de dimensiones.
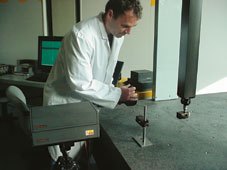
UNE-EN ISO 10360-2:
- Verificar el error de indicación en mediciones de dimensión.
- Verificar el error de palpado.
Siendo el mas importante la verificación del error de indicación en las mediciones de dimensión.
La ventaja de este ensayo con respecto a otros es que el resultado de la medición tiene una trazabilidad directa a la unidad de longitud, el metro.
Dimensión:
El principio del método de evaluación de la dimensión establece si una MMC es capaz de medir dentro del error máximo permisible de indicación de una MMC utilizada para mediciones de dimensión, MPEE. La evaluación debe realizarse comparando los valores calibrados con los valores indicados por cinco patrones de dimensiones diferentes, cada uno de ellos con una longitud distinta.
Los cinco patrones de dimensión deben situarse en siete posiciones y/u orientaciones diferentes dentro del volumen de la medición de la MMC, y medirse tres veces, es decir se realizan un total de 105 mediciones.
Error de Palpado:
El principio del método de evaluación del error de palpado es establecer si una MMC es capaz de medir dentro del error de palpado máximo permisible especificado, MPEp,, determinando el rango de las distancias entre los puntos medidos (25) y el centro de la esfera gaussiana asociada.
En casos de aceptación estarán indicados por el fabricante:
MPEE = error máximo permisible de indicación.
MPEp = error máximo permisible de palpado.
El usuario será quien indique en casos de verificación periódica.
En caso de verificación periódica se puede utilizar el ensayo de verificación anteriormente citado UNE-EN ISO 10360-2 (2001) u otros diferentes, que sean probadamente validos.
La Norma UNE-EN ISO 10360-2 (2001) junto con la Norma CMMA (1989), son las normas utilizadas por el Laboratorio de Dea Brown & Sharpe, S.A. (España y Portugal) para la realización de calibraciones “In Situ” de Maquinas de Medición por Coordenadas. Este Laboratorio está acreditado por Enac bajo norma UNE-EN ISO/IEC 17025, desde el mes de febrero del 2001.
Aparte de realizar la compensación o los ajustes de los errores geométricos y/o la calibración o aceptación de la MMC, en un sistema de calidad interna de una empresa, deberían contemplarse los ensayos de verificación periódica y un control periódico de forma regular, tal y como se recomienda en muchas normas internacionales.
Control periódico:
Entre ensayos de verificación periódicos es recomendable realizar controles periódicos de la MMC.
Se trata de demostrar que la MMC es conforme a los requisitos especificados con relación a los errores máximos permitidos tanto de indicación como de palpado.
El intervalo entre los ensayos debería determinarse en base a las condiciones ambientales y a las prestaciones de medición requeridas.
Para ello es posible medir dimensiones características de otros tipos de patrones materiales, y no solo considerar materiales de dimensión.
En función de los tipos de medición para los cuales se utiliza la MMC, se pueden utilizar múltiples artefactos: pieza de ensayos, placa de bolas, placa de agujeros, anillos patrón, etc.
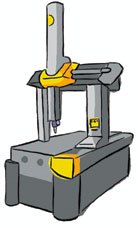
Después de ajustar la máquina (corrección de parámetros geométricos) y de su aceptación y/o verificación, el cliente puede disponer de un elemento: “pieza patrón” que podría ser una pieza “normal” y “corriente” en la cual se realizan mediciones de varios tipos y se guardan los resultados. De este modo mas adelante y con un plazo corto (diario, semanal etc.), realizar las mismas mediciones y comparar los resultados de medición. Esto nos permitirá cuantificar las desviaciones obtenidas resultantes de la medición con las que se realizaron cuando la máquina fue por ultima vez ajustada, aceptada y/o verificada .
Dea y la Universidad Politécnica de Madrid desarrollan un nuevo sistema: Dayly Check.
El Laboratorio de Dea Brown & Sharpe S.A. recomienda utilizar un interesante y novedoso sistema con el cual se podrá fácilmente realizar controles periódicos de la MMC.
Este sistema está siendo desarrollado de forma conjunta por Dea y por el Laboratorio de Metrología y Metrotecnia de la Universidad Politécnica de Madrid.
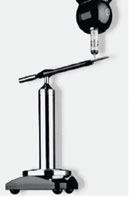
- Un dispositivo Renishaw.
- Programa de ejecución-medición automático.
- Software gráfico de evaluación.
El Dayly Check permite realizar comprobaciones puntuales rápidas y eficaces del rendimiento de una CMM, tal y como se recomienda en muchas normas internacionales. Proporciona una evaluación rápida y automática de las capacidades de la maquina.
El brazo contrapesado tiene un asiento que se sitúa sobre una bola de precisión de rubí en un pilar ajustable. El asiento permite que el brazo pivote con gran precisión, 360º horizontalmente y ± 45º verticalmente. En el extremo del brazo hay un segundo punto de medición formado por dos varillas y la bola de metal duro del brazo, y un palpador especialmente calibrado que se acopla a una sonda Renishaw. El brazo es capaz de describir una esfera truncada de radio R alrededor del pivote.
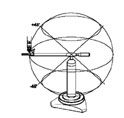
También puede determinarse la repetibilidad realizando múltiples pruebas y comparando los valores de radio medidos en las mismas posiciones.
Después de recoger los datos, se determina el rendimiento de medición volumétrica calculando la diferencia entre las desviaciones máximas.
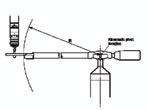