Ventajas del sistema de filtración rotativo
Economía en filtración de masas fundidas de plásticos
En la práctica, la segunda pregunta siempre se la pasa por alto cuando se elige y considera la especificación de un equipo nuevo. Este es el caso particularmente cuando se considera una línea llave en mano y cuando el proveedor de la línea llave en mano selecciona el sistema de filtración. Esto significa que frecuentemente se selecciona el sistema más barato que se consiga, que apenas cumpla con las especificaciones mínimas necesarias. La causa es simple: el proveedor de una línea llave en mano no tiene que operar la línea y por lo tanto los costos operativos de la línea no son su prioridad. El proveedor de la línea llave en mano recibirá su pago cuando la línea esté funcionando dentro de los rangos especificados y con la calidad de producto especificada.
Por esta razón, cuando planee invertir en una línea nueva, vale la pena para el futuro operador de la línea considerar tempranamente la selección de un sistema de filtración óptimo para evitar caros ajustes en una etapa posterior.
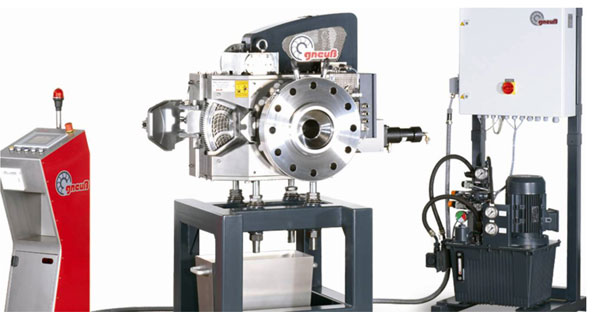
La economía de filtrado rotativo de masas fundidas de plástico
Que el sistema de filtración es –por una gran cantidad de razones diferentes– un factor importante en la eficiencia de costo del proceso de producción, es a menudo desestimado.
En comparación con los sistemas de cambio de mallas, el sistema de filtración rotativo representa una inversión un tanto más alta. Sin embargo, a mediano plazo representa la alternativa más barata. Esto es debido a que –entre otras cosas– los costos operativos resultantes del sistema de filtración rotativo quedan bien debajo de los sistemas de intercambio de mallas convencionales. En suma, se abren más oportunidades que no podrían ser tenidas en cuenta sin la tecnología de filtración rotativa. El gráfico número 1 nos muestra este punto claramente.
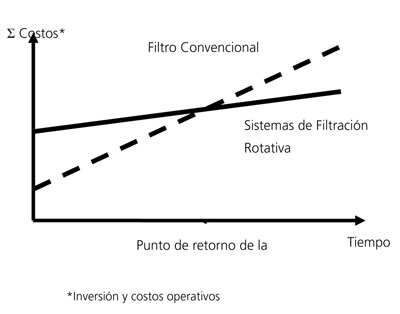
La influencia de cambio de mallas en el proceso de producción
La mayoría de los cambiadores de mallas causan problemas considerables en el proceso de producción. Esto se aplica no solo a los sistemas discontinuos (por ejemplo, cambiadores de malla de pistón simple, de plato deslizable y filtros simple tipo vela) sino también a los sistemas semicontinuos (cambiador de mallas de pistón doble o múltiple, filtros doble tipo vela).
Las causas de estos problemas son diversas y dependen del tipo de cambiador de mallas o del sistema de filtración en cuestión. En el caso de un pistón doble o múltiple o de cambiadores de mallas de plato deslizable, el área de filtración activa queda reducida durante los cambios de mallas, o en el caso de un filtro simple tipo vela la línea debe ser parada completamente, aún en el caso de un filtro doble tipo vela, el proceso fluctúa en forma enfervorizada mientras el polímero es desviado del filtro de bloqueo al de 'espera'.
Además, en los platos deslizables o en los cambiadores de mallas a pistón, el polímero se degrada con el resultado que esas partículas quemadas son introducidas a la masa fundida cuando se mueve el pistón o el plato deslizable, y por lo tanto, se introduce contaminación al producto durante el cambio de mallas.
Con el pistón y los cambiadores de mallas de plato deslizable y también con los filtros tipo vela, el aumento de la presión diferencial a lo largo del tiempo puede llevar a ablandar contaminantes que serán empujados a través del medio filtrante. Con los cambiadores de plato deslizable y pistón, es particularmente un tema sensible durante el cambio de malla, pues todo el polímero debe fluir por un área mucho menor que ya tiene una retorta sucia.
Estos problemas en los procesos con cambiadores de mallas convencionales a menudo llevan a interrupciones en la producción o a la producción de scrap o de productos 'fuera de grado' durante y por un tiempo después, de haber cambiado las mallas.
La consecuencia de esto es, que costos significativos son causados por: a) tener que moler el material o b) a través de la pérdida de ganancias teniendo que vender el material 'fuera de grado' a un precio más bajo o teniendo que reciclarlo.
Con el proceso constante del sistema de filtración rotativo, tales problemas son evitados completamente y consecuentemente ofrecen un potencial considerable para ahorros.
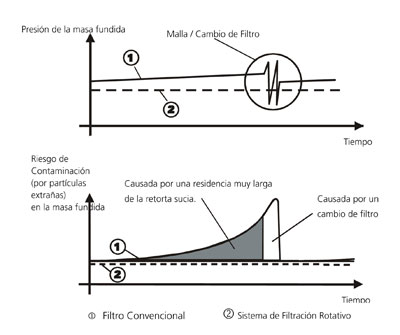
Ejemplo de un caso:
Un fabricante de polímeros asiático de pellets de ABS/SAN internacionalmente activo operaba en el pasado con cambiadores de mallas semicontinuos1. Con estos cambiadores de mallas era necesario desviar la producción a 'fuera de grado' durante y por aproximadamente 15 a 20 minutos cada vez que se cambiaba la malla. Este material era liquidado a un precio muy bajo. El rango de salida de la línea es de hasta 11.000 kg/h. Por lo tanto, al máximo rango de salida, 2.750 kg de material 'fuera de grado' por cambio de malla, lo cual debía ser liquidado al valor de costo (sin ganancia). Con el cambiador de malla de doble pistón, eran necesarios hasta 3 cambios de mallas por día, así que el total de 'fuera de grado' era de hasta 8.250 kg diarios.
Estos cambiadores de mallas han sido reemplazados por el sistema de filtración rotativa Gneuss (RSFgenius). El problema 'fuera de grado' fue completamente resuelto y la calidad del producto fue mejorado al mismo tiempo, debido a que las pequeñas variaciones de color causadas por los diferentes valores promedio estadísticos, resultantes de las variaciones de presión del cambiador de mallas de doble pistón, fueron completamente evitadas.
Filtración más fina y/o uso (incrementado) de material reciclado
Los usuarios de cambiadores de malla convencionales saben que cada cambio de malla lleva a problemas en el producto final. Por esta causa, generalmente intentarán incrementar el cambio de una malla a la otra lo más alejado posible o de demorar el cambio de malla hasta la próxima parada de producción planificada –por ejemplo el cambio de un cabezal. Esta extensión de tiempo entre los cambios de mallas puede ser lograda a través de dos factores:
- Una filtración más gruesa
- Materia prima más limpia.
Ambos factores tendrán un efecto negativo en la eficiencia de costo del proceso de producción. Una filtración más gruesa llevará a la reducción en la calidad del producto terminado y materia prima más limpia será materia prima más cara.
La consecuencia de la operación de proceso constante del sistema de filtración rotativo es que productos de alta calidad pueden ser fabricados usando materia prima más barata (por ejemplo material remolido/reciclado).
Debido a que los cambios de filtros no tienen efecto sobre el proceso, el programa de producción de la línea de extrusión no necesita ser planificada en función de estos cambios.
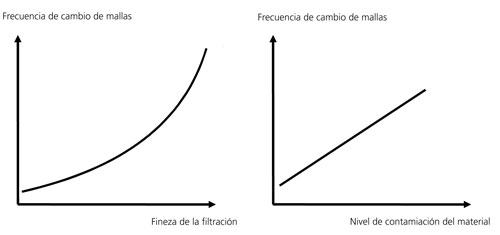
Ejemplo de un caso:
Un fabricante europeo de láminas de PET para termoformado de alta calidad con un espesor de poca tolerancia operado con un cambiador de malla discontinuo. Debido a los serios problemas durante los cambios de mallas no era posible usar escamas de botellas de PET.
La conversión de la línea con un RSFgenius hizo posible que use hasta el 100% de escamas de botellas de PET. El proceso continúa sin problema alguno aún durante el cambio de los elementos filtrantes. La salida de la línea es de 1.000 kg/h. El precio de las escamas de botella de PET es alrededor de 50 a 70% el precio del material virgen así que la inversión fue recuperada en un período extremadamente corto.
Pérdida por retrolavado en los sistemas de filtración autolimpiantes
Los cambiadores de mallas con retrolavado se usan frecuentemente con materiales altamente contaminados. Con estas unidades, una cierta cantidad de material se usa para limpiar los elementos filtrantes. Este material se pierde. La cantidad de polímero usado para retrolavado varía muchísimo dependiendo en el diseño del cambiador de mallas autolimpiante. El material perdido con el retrolavado es un factor de costos particularmente importante para la eficiencia de costo del proceso, especialmente cuando son procesados materiales más caros como el PET o el PA (Nylon).
El sistema de autolimpieza patentado del RSFgenius ofrece una eficiencia de retrolavado más alta que los cambiadores de mallas de retrolavado convencionales, los cuales simplemente desvían algo del polímero a través del lado reverso de los elementos filtrantes.
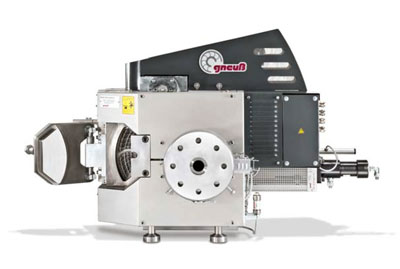
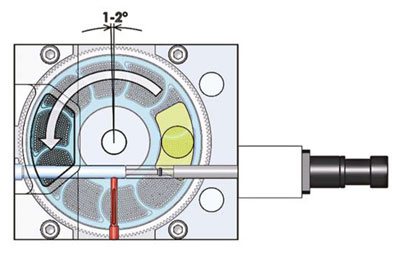
El RSFgenius purga los elementos filtrantes de manera integrada. Un pistón de retrolavado (patentado) justo antes del elemento filtrante es reintroducido en el flujo principal de masa fundida. Se extrae polímero fundido filtrado en el block de salida a través de un pistón. Este pistón luego acelera el polímero y provee un impulso de alta presión, un 'disparo' de polímero el cual es inyectado a través del lado reverso del elemento filtrante y subsecuentemente, hacia el exterior. La cantidad de material que es usado para este ciclo de limpieza es libremente ajustable y en la práctica normalmente va entre el 0,01 y 0,5% (con material altamente contaminado) del rango de salida de producción.
La velocidad de inyección, del 'disparo' y por lo tanto, la presión de limpieza es ajustable y controlada automáticamente durante el proceso. El proceso automático de autolimpieza tiene lugar sin ninguna interferencia en el proceso de producción.
Ejemplo de un caso:
Un fabricante internacionalmente activo de flejes para empaque de PET a partir de escamas de botella, originalmente operaba con cambiadores de mallas con autolavado semicontinuo en varias de sus plantas antes de equipar esas líneas con el RSFgenius.
En los cambiadores de mallas semicontinuos con autolavado, la variación de los procesos causados por el autolavado hacía que los cambios de mallas durante la producción fueran imposibles.
Consecuentemente, solo una limitada proporción de la materia prima podía ser sustituida con escamas de botellas de PET.
Gracias al RSFgenius con su permanente y completo proceso, de operación constante, esta restricción no existe más y consecuentemente hasta 100% de escamas de botellas pueden ser usadas con su correspondiente efecto positivo en los costos del material.
Costos de los elementos filtrantes (mallas)
Con el fin de que los elementos filtrantes o paquetes de mallas no se transformen en un factor de costo, la selección de un cambiador de mallas autolimpiante que permite el uso repetido de los elementos filtrantes podría ser la solución más económica. Frecuentemente, los costos de inversión son más altos pero –gracias a los bajos costos de los elementos filtrantes– el retorno de la inversión es corto.
Con el fin de obtener el mejor uso posible de los elementos filtrantes, son importantes la eficiencia del sistema autolimpiante y la configuración óptima de los elementos filtrantes. El sistema autolimpiante de RSFgenius, como se ha descrito arriba, es también ventajoso con respecto a la capacidad de reutilización de los elementos filtrantes y provee un alto nivel de eficiencia.
![F ine z a de las m a lla s [μm] F ine z a de las m a lla s [μm]](https://img.interempresas.net/fotos/351864.jpeg)
Influencia de las variaciones de procesamiento en las tolerancias de fabricación
Frecuentemente los problemas de procesamiento causados durante el cambio de mallas tienen un efecto negativo en las tolerancias dimensionales del producto terminado.
Las condiciones de funcionamiento con proceso constante provistas por el RSFgenius usualmente ofrece la oportunidad de (en comparación a los cambiadores de mallas convencionales), ser capaz de funcionar con tolerancias muy justas. El gráfico abajo muestra el efecto que puede tener en el proceso de producción
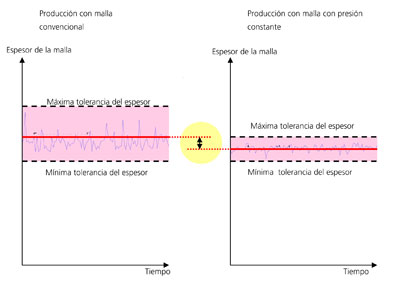
En el caso mostrado aquí, el cliente tiene un mínimo especificado y un máximo aceptable de espesor de malla. Debido a que con el RSFgenius la producción puede ser mantenida en un proceso constante, se puede lograr un espesor promedio más fino, lo que lleva a un significante ahorro en materia prima.
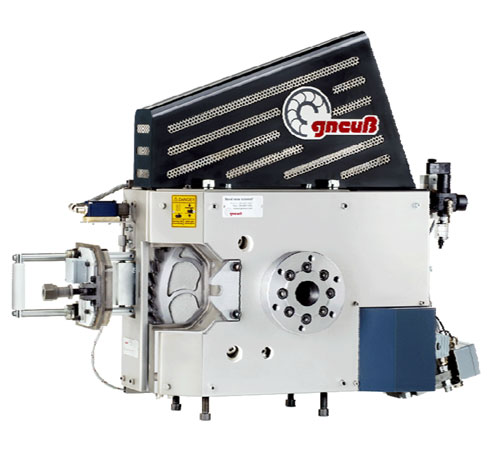
Ejemplo de un caso:
Un fabricante de film barrera (PE) tiene varias líneas equipadas con el sistema de filtración rotativo SFXmagnus. El proceso de operación constante provisto por este sistema hizo posible reducir el espesor del film promedio en un 4%.
Con una salida promedio de 1.000 kg/h, fue posible ahorrar 300 toneladas de materia prima por año.
Resumen
Los sistemas de filtración pueden influenciar decisivamente la economía de un proceso de producción. Cuando se considera la compra de una nueva línea de extrusión, es importante considerar cuidadosamente cuál sistema de filtración es el mejor para el proceso de producción en cuestión. El sistema ofrecido por el proveedor de una línea llave en mano por un lado, cumplirá con los requerimientos técnicos mínimos pero por el otro, frecuentemente no es la solución más económica.