El sinterizado láser populariza los moldes a la carta
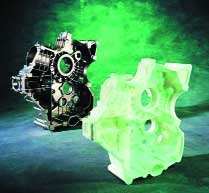
El proceso DirectCast
De acuerdo con este método patentado, el modelo se diseña primero en CAD, luego se produce automáticamente en una máquina de sinterizado láser, que aglutina los granos de arena recubiertos de resina capa por capa de acuerdo con el modelo digital del que dispone la máquina. Los machos pueden terminarse en horas y emplearse para producir piezas de fundición de acero, aluminio o magnesio, por poner algunos ejemplos. Normalmente, la mayor parte de las piezas de fundición requieren moldes mecanizados, lo que retrasa la producción como mínimo varias semanas.
Esta tecnología la ha introducido EOS en un sistema de sinterizado láser llamado Eosint S 700, que utilizan compañías de automoción como BMW, DaimlerChrysler, Ford, ITT Flygt, Nissan, Porsche y Volkswagen. Eosint S 700 es un sistema de prototipado rápido —que emplea dos láseres— que trabaja directamente a partir de datos tridimensionales en CAD. Su volumen de trabajo es de 720x380x380mm, suficiente para fabricar componentes de motores de cuatro y seis cilindros de una sola pieza, como culatas, ó una gran cantidad de machos más pequeños simultáneamente. Las aplicaciones típicas son desarrollo de motores y grupos motopropulsores, bombas y sistemas hidráulicos.
Aplicaciones para plásticos
Por otra parte, Eosint P 700 asegura la calidad superficial de las piezas sinterizadas mediante un cuidadoso control de la temperatura. Según un miembro del departamento de Prototipado Rápido de la firma DaimlerChrysler, este sistema, junto con el nuevo material PrimerCast 100, es la máquina más productiva del mundo de prototipado rápido.
Nuevo material
Este nuevo material ha sido probado por varias empresas, como Alphaform o DaimlerCrhysler, a la que ya habíamos hecho referencia. La empresa nuremburguesa FIT (Fruth Innovative Technologien), por ejemplo, cliente de hace muchos años de EOS, empleó este nuevo material en una Eosint P para producir modelos para una parrilla directamente a través del sinterizado láser, fabricada empleando el método de la cera perdida. El bastidor de plástico de la parrilla se produjo mediante colada por vacío. Empleando este método directo, FIT redujo sus costes un 29 por ciento.
Producción de series
En industrias como la fabricación de artículos deportivos, por ejemplo, con frecuencia se necesita disponer de pequeñas series que no son rentables si se emplean métodos más convencionales de producción de moldes. Estos sectores son terreno abonado para el sinterizado láser, que además ofrece una libertad desconocida hasta ahora en el diseño de estos moldes. Un ejemplo claro es la integración de los canales de refrigeración.
Este método fue el objeto de un proyecto conjunto entre la firma italiana EsTec con Democenter, que consiguieron series de 20 millones de pelotas de golf con moldes sinterizados por láser. Las piezas se fabricaron mediante extrusión- soplado de polipropileno, seguido de una inyección de elastómero. El elevado número de pelotas producidas puede parecer asombroso, pero los canales de refrigeración siguiendo la forma de la pieza y los sistemas de ventilación desaireación en los insertos del molde —impensables en sistemas convencionales— mejoraron de forma crítica las propiedades del molde. Esto mejoró los índices de la producción y la esfericidad de las pelotas.
Otro ejemplo extraído de los productos "de temporada" —sujetos a modas y a tendencias varias— fue el llavero en forma de scooter para motocicleta, producido en series pequeñas de centenares de piezas. Era un llavero bicolor que se inyectaba mediante un proceso bicomponente. El molde se hizo usando Direct Metal 20 como material en una Eosint 250 Xtended y la calidad fue tan alta que no se requirió postmecanizado ni pulido.
Otro ejemplo, la compañía TransCat quería un molde para la inyección de un ventilador tan pronto como fuera posible, así que empleó DirectMetal 20 y la Eosint M 250 Xtended y construyó su molde en 16 horas. después de un breve micro-chorreado y pulido, el molde se empleó para inyectar series de piezas de paredes delgadas (PA6 + 30% FV) para trabajar a 30.000 rpm
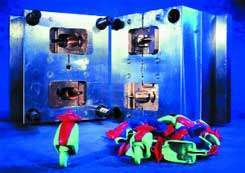