Exactamente en el punto
El proveedor de automóviles SMP Alemania produce en Neustadt an der Donau, entre muchos otros tableros de instrumentos, también el tablero para el Audi Q5. Su construcción está compuesta de tres diferentes capas de materiales: un soporte de plástico reforzado con fibra larga de vidrio, una capa de espuma de poliuretano (PUR), así como la piel de moldeado de PVC (slush skin), que se adapta a la forma del soporte. El soporte se fabrica de polipropileno (PP) por moldeo por inyección, un plástico no polar que requiere obligatoriamente un pretratamiento, a fin de preparar su superficie para el proceso de adhesión.
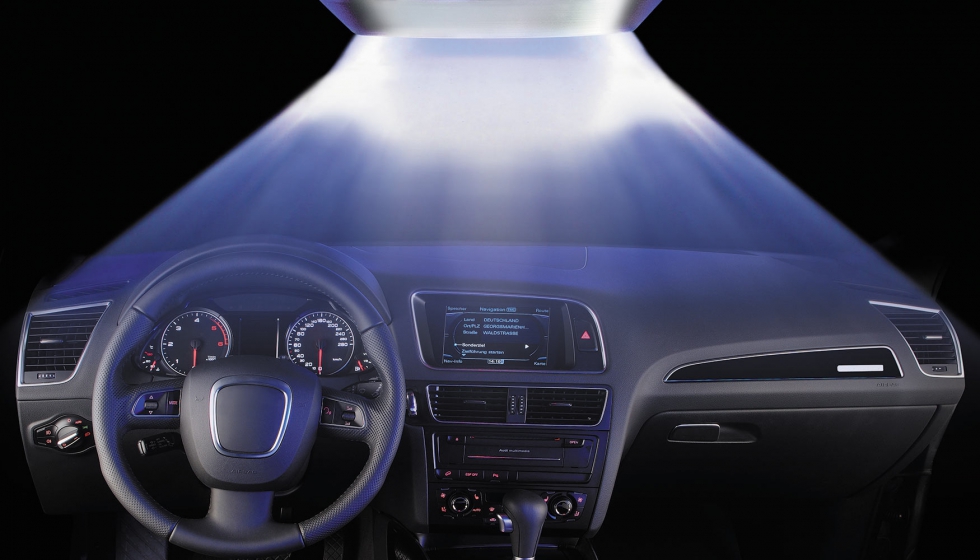
Imagen 1. Plasma en vez de llama: Para la seguridad del plástico térmicamente sensible y reforzado con fibra larga y para ahorrar el enmascaramiento antes del espumado, el tablero de instrumentos del Audi Q5 se somete a un pretratamiento con plasma atmosférico. Foto Plasmatreat.
Rentable y seguro
Para la producción del tablero de instrumentos, el fabricante se decidió en contra del tratamiento con llama aplicado hasta ahora y en favor de un pretratamiento con plasma atmosférico. Después de la fase de prueba y comparación de los costes de adquisición de una nueva máquina para tratamiento con llama, las ventajas para el fabricante eran obvias. De gran importancia fue la aplicación selectiva y precisa que proporciona este plasma y, por lo tanto, la renuncia al uso de enmascaramiento. Añadido a esto, el ‘plasma frío’ no daña la superficie de polipropileno reforzado con fibra larga de vidrio, el sistema ofrece una particularmente alta seguridad de proceso y reproducibilidad, y todo esto acompañado con un significativo ahorro de costes operativos (imagen 1).
Efecto triple
La tecnología Plasma Openair, inventada por el líder de mercado Plasmatreat hace más de 20 años y que actualmente se utiliza a nivel mundial, se basa en el desarrollo de sistemas de plasma que operan bajo presión atmosférica, quiere decir sin cámaras de vacío, y son fácil de integrar en las líneas existente de producción. El pretratamiento es ecológico, las toberas funcionan sólo con aire comprimido y alto voltaje. El método, que se utiliza en particular para plásticos no polares, tales como el PP usado aquí, une tres procesos en un sólo paso instantáneo: se proporciona la limpieza exhaustiva de la superficie, al mismo tiempo su descarga estática y simultáneamente su activación (imagen 2). Este efecto triple sobrepasa por mucho los métodos convencionales de pretratamiento. El resultado es la humectabilidad homogénea de la superficie y la adhesión permanente del pegado o del recubrimiento también en condiciones de máxima utilización.
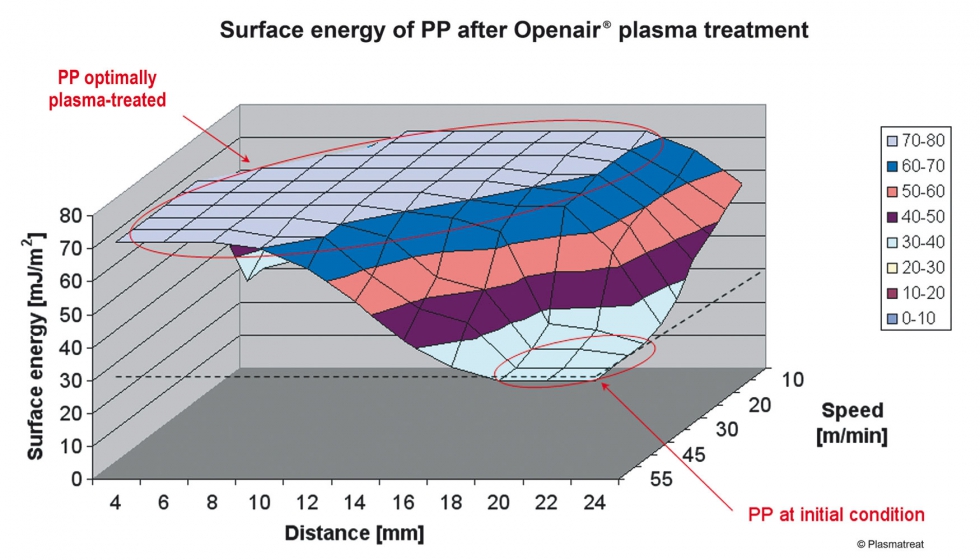
Imagen 2. La figura muestra una superficie de plástico no polar, tratada con Plasma Openair en función de la distancia y la velocidad. Después del tratamiento, la superficie se ha vuelto polar y la energía superficial ha aumentado a más de 72mJ/m² en una gran ventana de proceso. Figura Plasmatreat.
Pretratamiento al contorno exacto
La instalación de plasma que se emplea por SMP Alemania dispone de tres toberas rotativas, controladas por un robot y funciona a una velocidad de flujo de aproximadamente 250 m/s. Esto hace posible la activación eficaz incluso para componentes de geometría compleja, como por ejemplo con pequeñas cavidades y cortes traseros. El área de acción del plasma está junto a la tobera, por lo que las variaciones por la distancia, condicionadas por diversas tolerancias a los componentes o las herramientas, son apenas perceptibles en la zona del pretratamiento. Un efecto particularmente positivo es el escaneo del contorno exacto de la superficie de plástico (imagen 3). Mientras la tobera de plasma puede cambiar la dirección y moverse sobre el componente de tratar no sólo en líneas rectas, un mayor cambio de dirección durante el tratamiento con llama debe hacerse fuera del componente, puesto que la energía térmica de la llama puede causar quemaduras en la superficie en el momento de regreso.
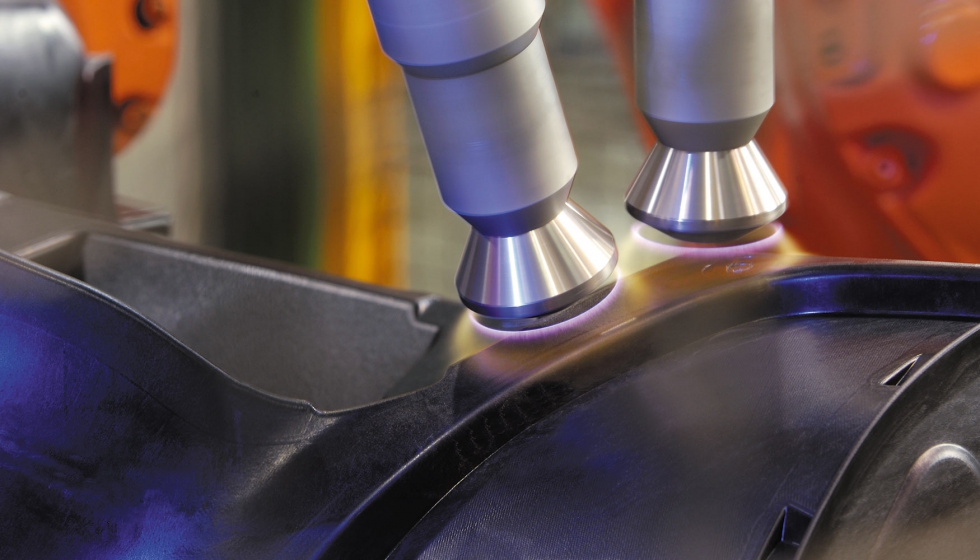
Imagen 3. Las toberas rotativas, controladas por un robot, funcionan exactamente al contorno. El plasma proporciona la limpieza exhaustiva y el alto grado de activación de la superficie de plástico, también en componentes de geometrías compleja. Foto Plasmatreat.
Riesgo del tratamiento con llama
Si los parámetros ‘distancia al componente’ o ‘duración de la llama’ se desvían de los valores establecidos, aunque sea mínimamente, la llama con una temperatura de más de mil grados puede ser un peligro para el polipropileno térmicamente sensible. Especialmente, si como en este caso, se trata de un plástico reforzado con fibra larga de vidrio. Si el polipropileno se derrita por el calor de la llama, las fibras quedarían sueltas en la superficie y la adhesión con la espuma de poliuretano no sería posible. La llama también podría causar acumulación de energía térmica en las cavidades y se llegaría al mismo resultado porque el calor no puede escapar. Pero todos estos riesgos se pueden evitar con el método Plasma Openair. El calentamiento del plástico durante el tratamiento no sobrepasa los 30 °C.
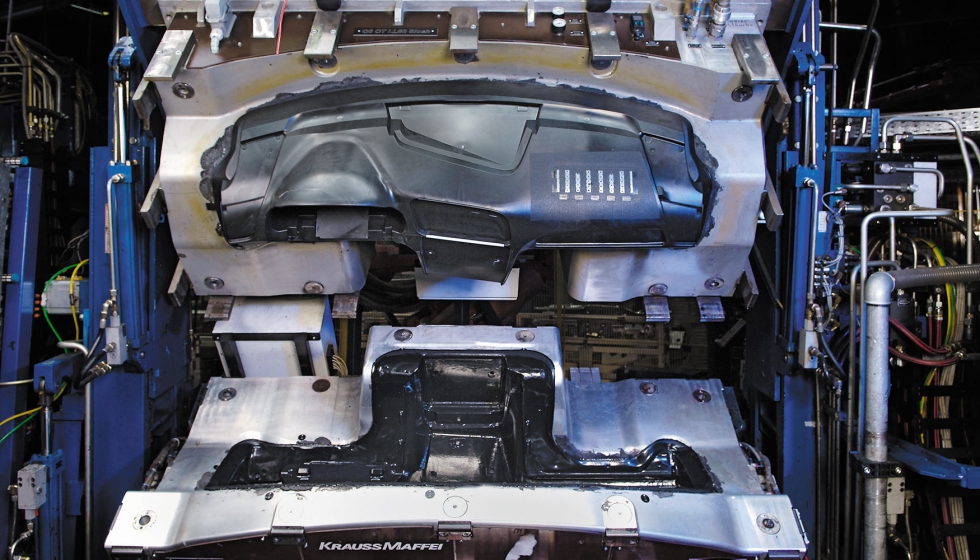
Imagen 4. Abierta, la máquina para aplicación del espumado se parece a una tostadora gigante de sándwiches. La espuma de PUR se aplica sobre la piel de moldeado negro insertada por debajo. Después de cerrar la máquina, la espuma se distribuye completamente entre el soporte de PP (por arriba) y la piel y queda pegada entre ambos. Foto Plasmatreat.
Sin enmascaramiento
La espuma que asegura el tacto suave del tablero entre el soporte de PP y la piel de moldeado se inyecta en la máquina de espuma (imagen 4) y debe pegarse a ciertas áreas, pero a otras no. El método convencional de tratamiento con llama exige que todas las áreas, en las que la espuma no debe pegarse posteriormente, se cubran con máscaras termoestables. La tecnología Plasma Openair permite eliminar por completo el paso de enmascaramiento, ya que el chorro de plasma opera de manera selectiva. Al contrario del tratamiento con llama, el chorro de plasma se ajusta con una precisión milimétrica a la geometría de la pieza tratada. A continuación, la piel de moldeado perforada, junto con la espuma de PUR, se puede quitar fácilmente de las áreas no tratadas. Las áreas previstas para los orificios del soporte e instalación de los instrumentos, se perforan en un paso adicional (imágenes 5 y 6).
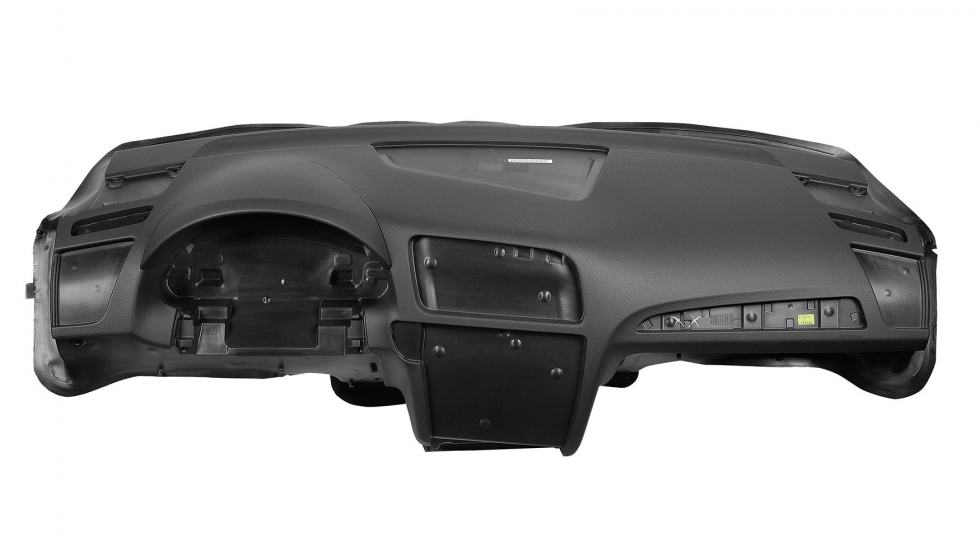
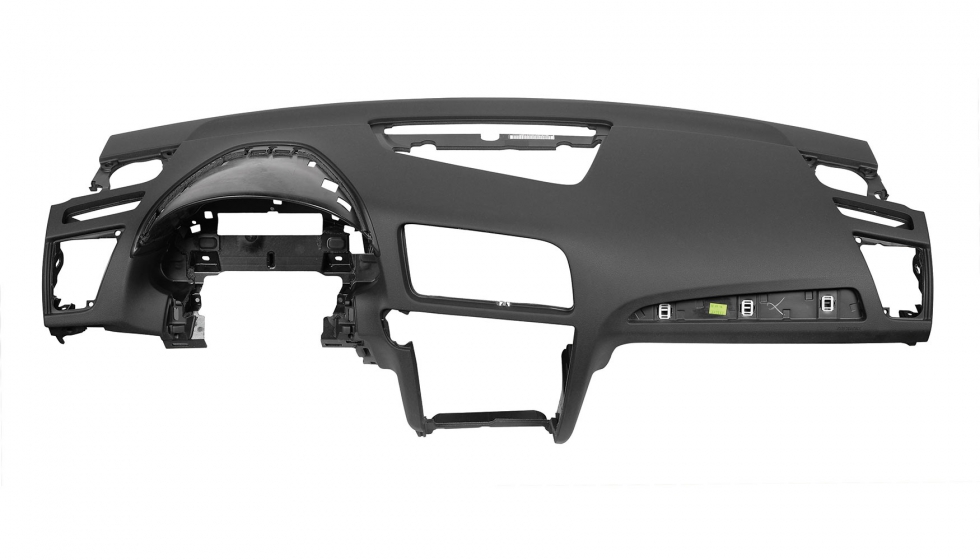
Imágenes 5 y 6. Arriba: El soporte de instrumentos después del tratamiento con plasma, la piel de moldeado y la espuma pegada, así como el debilitamiento de la parte trasera de la piel en el área de la bolsa de aire. Abajo: Los orificios para los instrumentos se perforan a continuación. La piel moldeada con la espuma de respaldo se puede eliminar fácilmente a mano de las áreas no tratadas con plasma. Fotos Plasmatreat.
Conclusión
Según Oliver Berger, responsable para la Producción de Tableros de Instrumentos en SMP Alemania, el proceso estable de pretratamiento de Plasmatreat se ha comprobado desde hace años. Las ventajas principales son, ante todo, la confiabilidad y la gran eficiencia del método en la producción. Además, el método se destaca por su fácil integración en procesos automatizados, así como por la mayor rentabilidad en comparación con los métodos convencionales de pretratamiento, y asimismo se ofrece una excelente compatibilidad con el medio ambiente.
Plasmatreat GmbH, Ibérica, www.plasmatreat.es
SMP Deutschland GmbH, www.smp-automotive.com