Entrevista a Asunción Martínez, responsable de materiales y tecnologías de Aiju
El proyecto Life11 ENV/ES/513 Mastalmond liderado por Aiju, y que ha implicado durante tres años a la empresa juguetera Injusa, la suministradora de masterbastches IQAP Masterbatch Group y el inyectador Pérez Cerdá Plastics, ha llegado a su fin. Asunción Martínez, responsable de materiales y tecnologías del Instituto Tecnológico del Producto Infantil y de Ocio, nos cuenta en esta entrevista qué fases ha atravesado el proyecto y qué retos han debido superar. El resultado, un éxito: conseguir concentrados de color biodegradables desarrollados a partir de materiales como la cáscara de almendra, con el fin de obtener productos más respetuosos con el medio ambiente. Algo que abre nuevas posibilidades para el sector de la inyección de plásticos. El nuevo masterbatch ya está a la venta y un nuevo procedimiento se encuentra disponible en la industria de la inyección de plásticos.
El proyecto Mastalmold finalizó el pasado mes de septiembre de 2015 con un evento internacional de puertas abiertas en el que se estableció la relación entre materiales innovadores, diseño y personalización, tecnologías de fabricación avanzada y nuevos modelos de negocio.
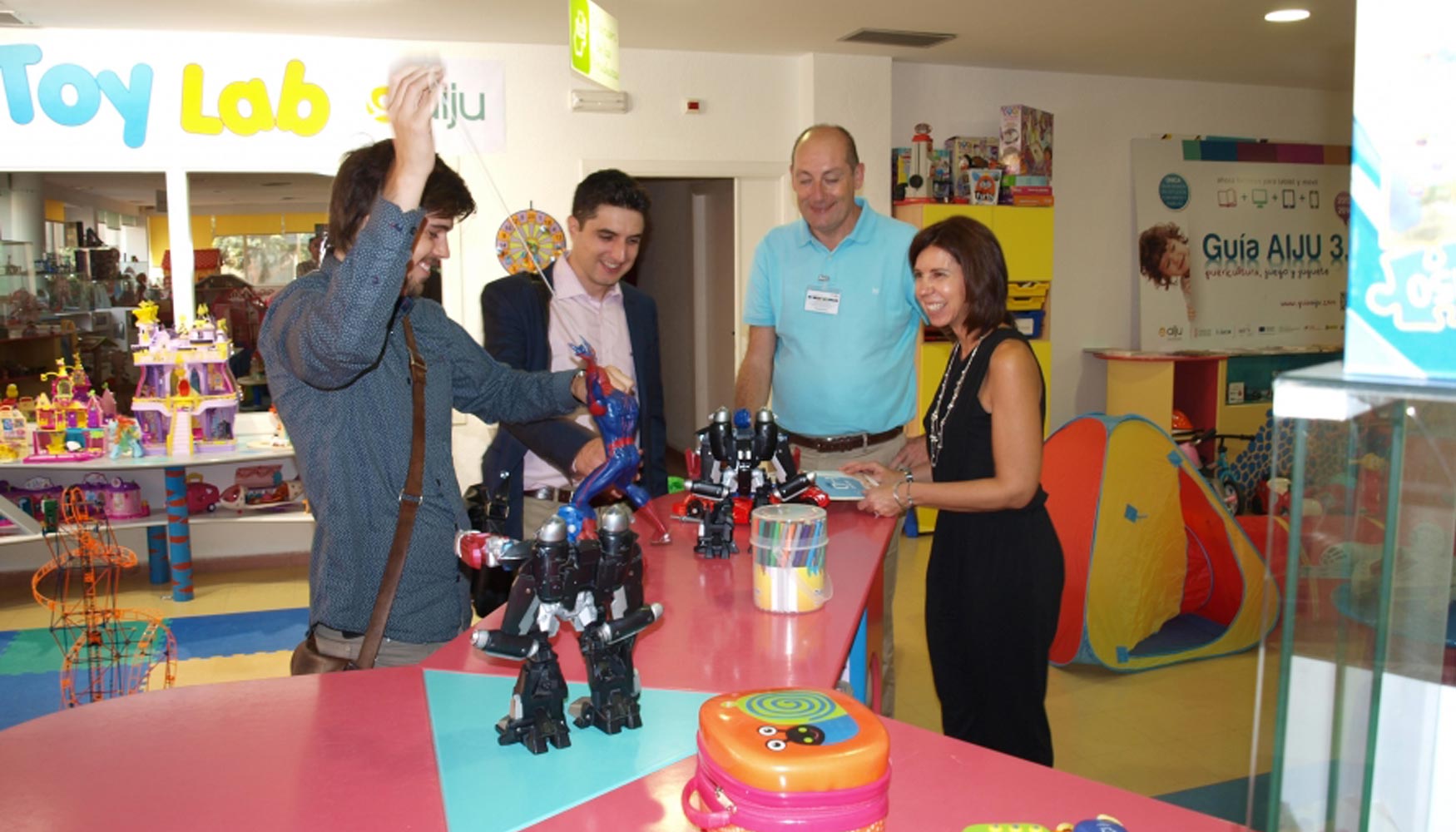
Evento Internacional. Momento de la visita al Laboratorio de Juegos.
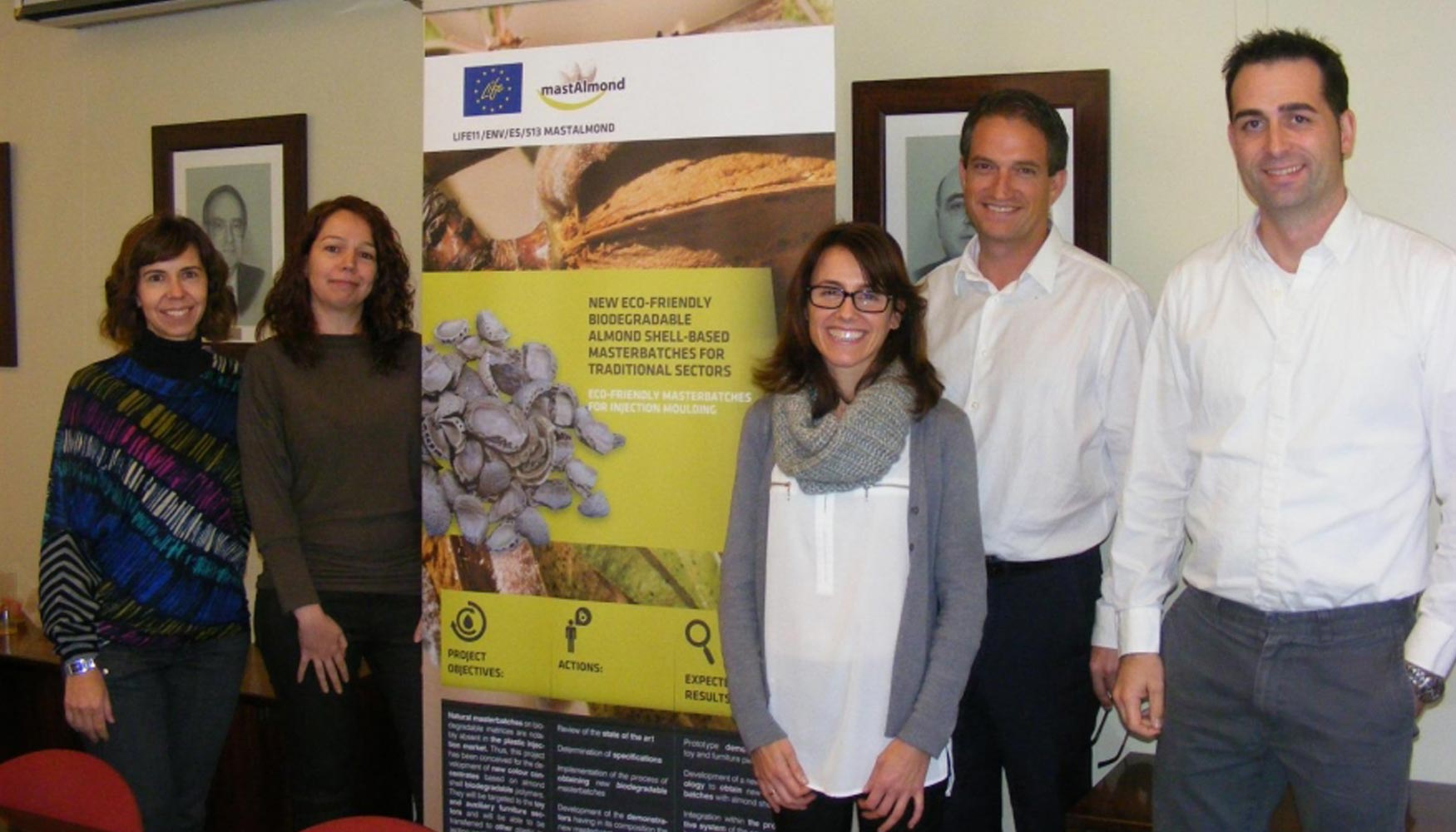
Socios del proyecto Mastalmond de las empresas Injusa, IQAP, Pérez Cerdá Plastics y Aiju (Asunción Martínez).
La jornada sobre el uso y consecuencias de nano y bio materiales en las industrias creativas. ¿Es la primera vez que se celebra?
Esta jornada es la primera vez que se celebra como tal porque proviene de la conclusión de un proyecto europeo, Life, que ha estado basado en la creación de nuevos masterbatches de matriz biodegradable con un porcentaje de cáscara de almendra en el interior. Éstos deben incorporarse al plástico biodegradable después durante el proceso de inyección. Además de tener la cáscara de almendra, se han introducido diversos pigmentos y colorantes. Mastalmond está financiado por la Comisión Europea a través del instrumento financiero LIFE 11 ENV/ES/513.
¿El color era una dificultad?
Sí, era todo un reto para la empresa de masterbatch porque introducir la cáscara de almendra y colores compatibles con la coloración natural de ésta ha sido definitivo para el aspecto final. La cáscara de almendra es de color marrón, y tiende a tapar otras tonalidades.
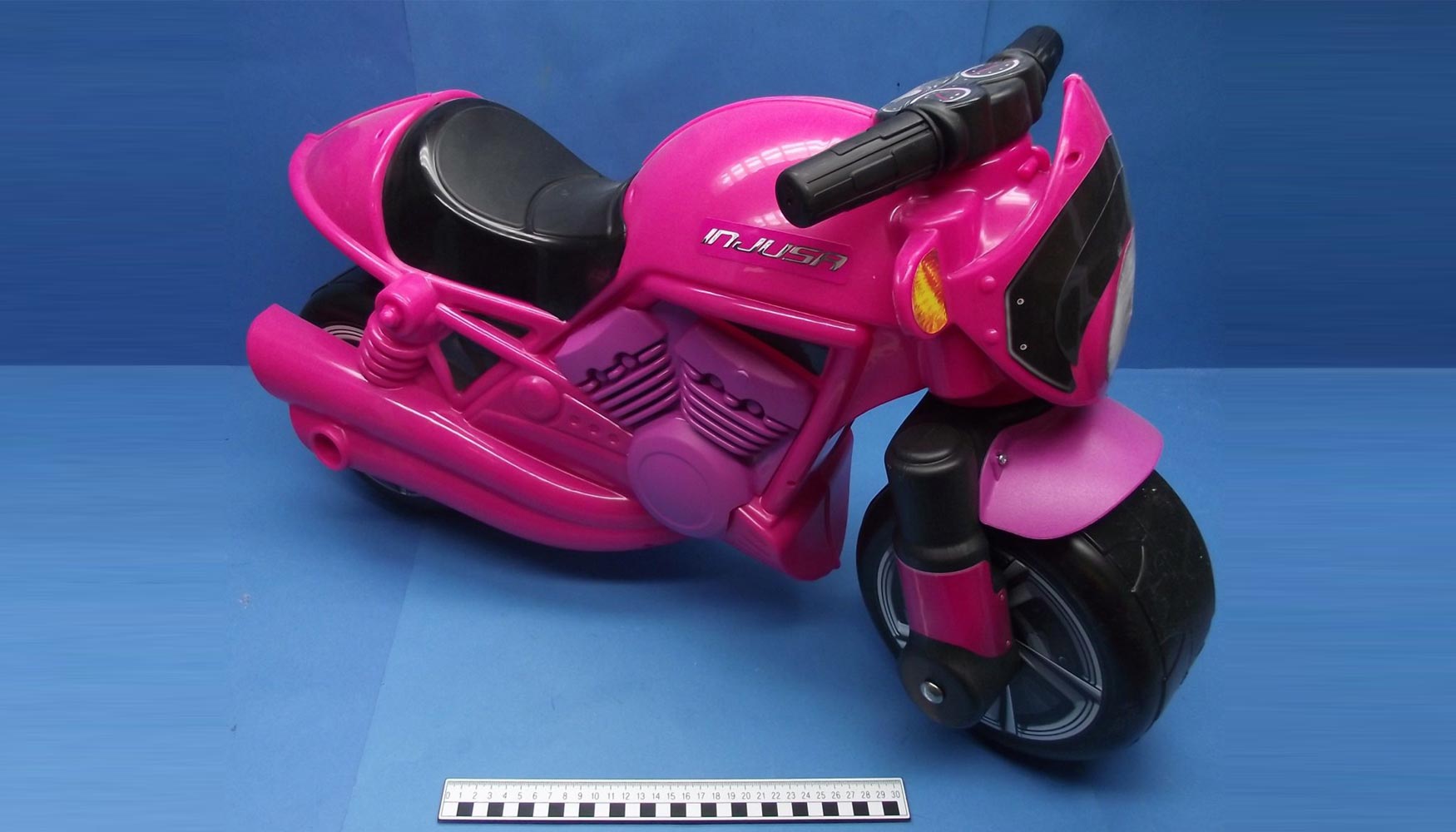
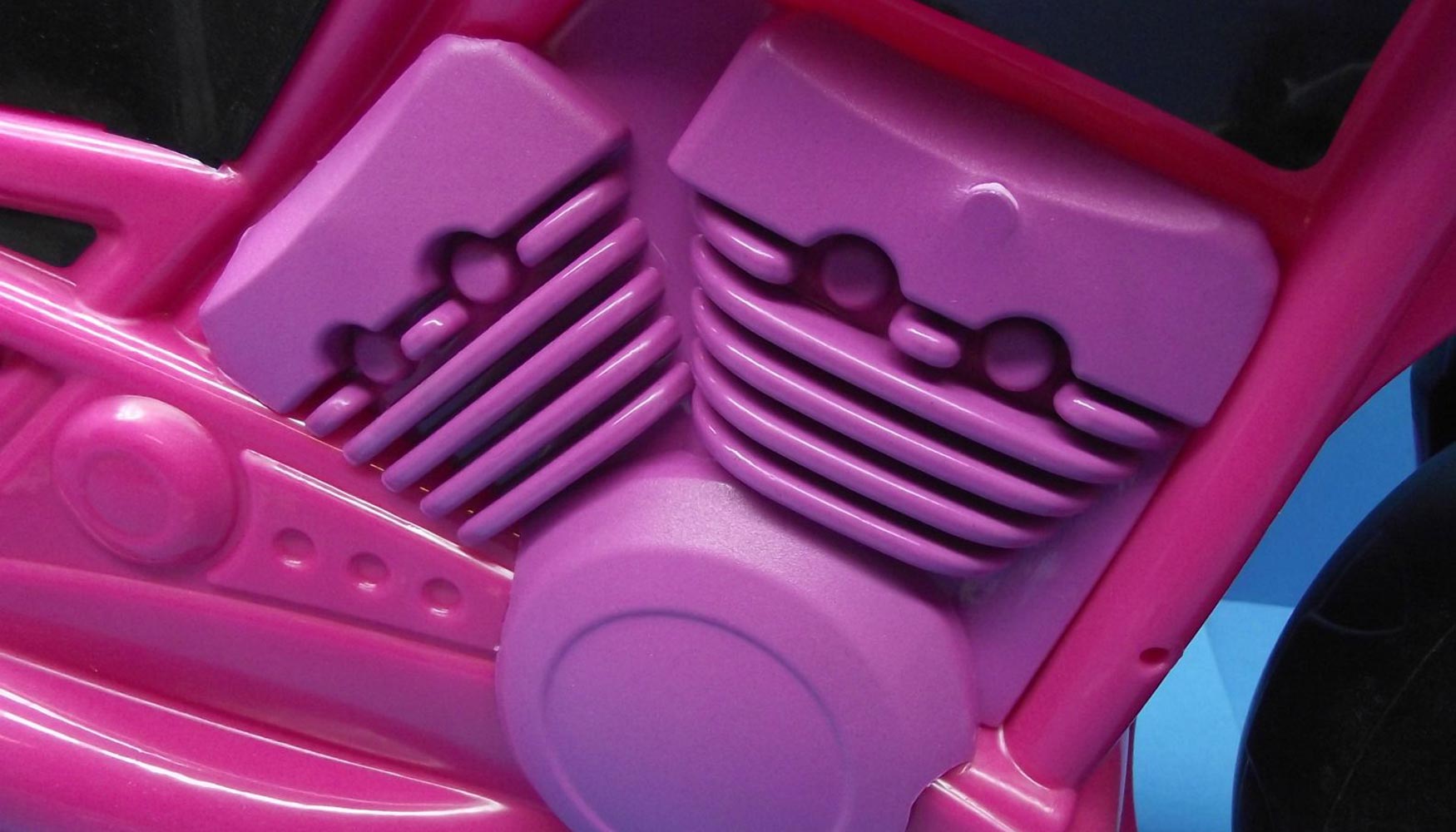
Detalle de una pieza inyectada con los nuevos masterbatches y detalle de una pieza inyectada con los masterbatches Mastalmond.
¿Qué es exactamente un masterbatch natural?
Un masterbatch consiste en una matriz plástica en la que se integra una alta proporción (entre el 50 y el 80%) de pigmentos, colorantes, agentes dispersantes y otros aditivos. Los masterbatches, en forma de granza o granulada, se añade al polímero (también en forma de granza) durante el proceso de transformación (moldeo por inyección, extrusión…) en una proporción aproximada del 2-3% de su peso total. Ello presume unas 360.000 toneladas de consumo anual de masterbatches en el ámbito Europeo.
Los masterbatches naturales sobre matrices biodegradables son los grandes ausentes en el mercado de la inyección de plásticos. Por eso, este proyecto desarrolla nuevos colorantes plásticos basados en polímeros biodegradables con cáscara de almendra orientados a las industrias del juguete y el mueble auxiliar y trasladables a otras industrias del mundo de la inyección de plásticos.
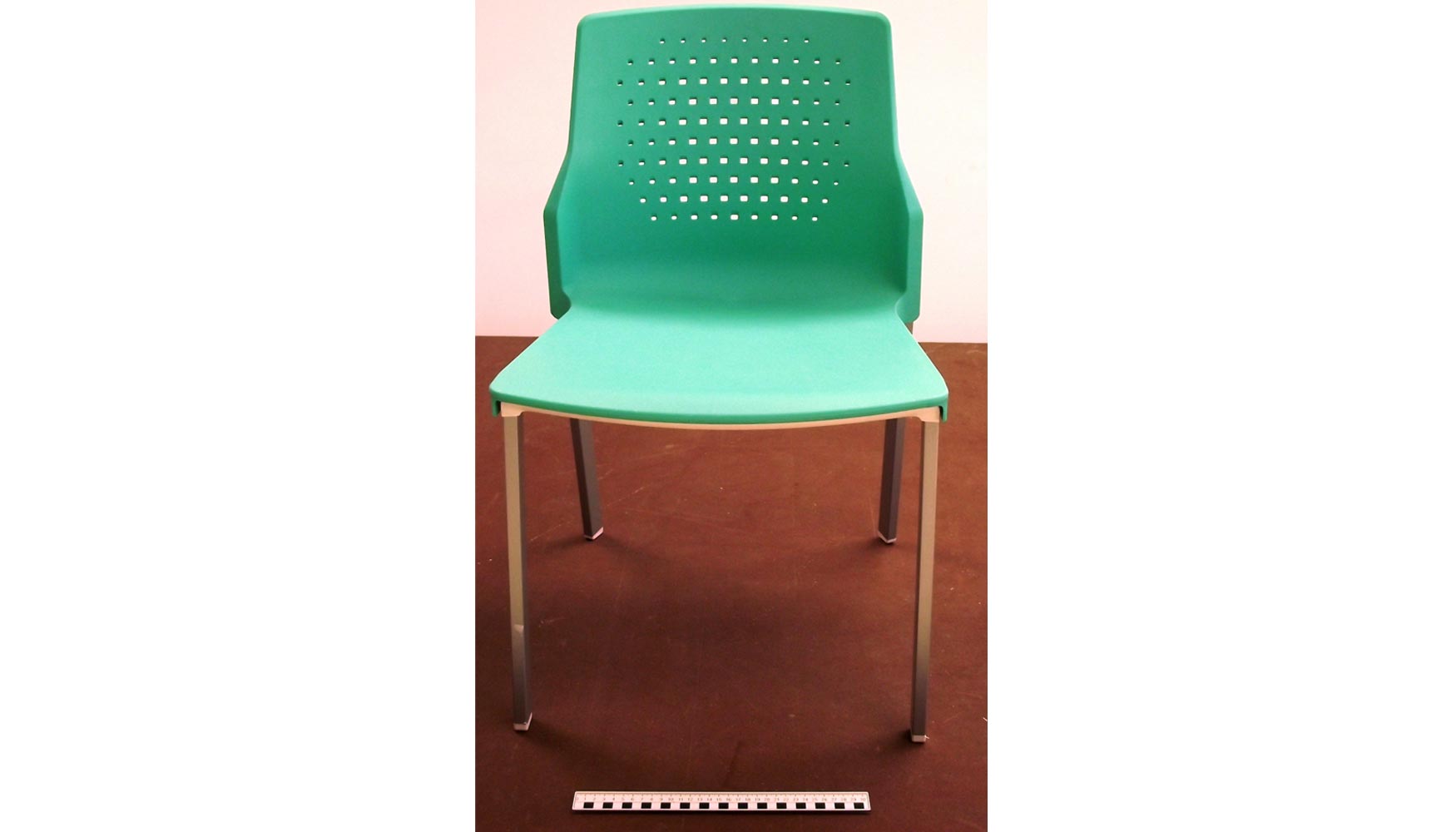
Silla realizada con los masterbatches Mastalmond.
Y no existían…
No existían masterbatches en el mercado basados en plásticos biodegradables ni con componentes naturales y además la implementación de polímeros biodegradables en el mercado resulta muy pobre fuera del ámbito de los envases y embalajes. La introducción de estos polímeros en industrias tradicionales como la del juguete o la del mueble auxiliar constituyen un factor de competitividad en el mercado actual respecto a otros mercados emergentes, contribuyendo además a generar y potenciar un consumo sostenible sin necesidad de realizar inversión adicional para su procesado.
Si se pueden implementar en un proceso de inyección convencional, tienen un gran potencial...
Sin duda. El 30% de los productos plásticos en el mercado se procesan mediante el moldeo por inyección. El método más extendido, simple y económico de colorear y/o modificar las propiedades de los plásticos (80% – 90%), es el uso de colorantes plásticos o masterbatches, que deben ser compatibles con el tipo de plástico matriz. Ello supone unos 12 millones de toneladas de productos plásticos.
¿A quién se dirigía el proyecto?
Al mercado de la inyección. Lo hemos llevado a cabo con unos demostradores para comprobar que es factible su empleo, inicialmente, en dos sectores: en el juguete, donde la empresa Injusa ha trabajado inyectándolos con diferentes geometrías y tamaños, y viendo en cada caso, las dificultades que se presentaban. También hemos trabajado con una empresa de inyección, Pérez Crdá Plastics, especializada en mobiliario entre otras cosas, que ha realizado pruebas de inyección con piezas de diferentes tamaños.
¿Han difundido las conclusiones?
El programa Life desea que se difundan los resultados y que se cree networking con otro tipo de iniciativas medioambientales. Así, nosotros hemos intentado que llegue a todo tipo de sectores planteando esta jornada como un punto de partida para nuevos retos en distintos tipos de industrias susceptibles de usar estos nuevos materiales y otros, como pueden ser biomateriales, nanomateriales, procesos de fabricación convencionales y no tradicionales, como las tecnologías de fabricación aditiva… En definitiva, soluciones que permitan nuevas posibilidades como que el usuario se involucre o logren poner en contacto todas las etapas de los procesos de producción.
Hemos llevado a cabo una difusión muy amplia por toda Europa, a través de congresos, notas de prensa, artículos y organización de jornadas en las que invitamos a otros implicados en proyectos Life orientados a mejoras medioambientales.
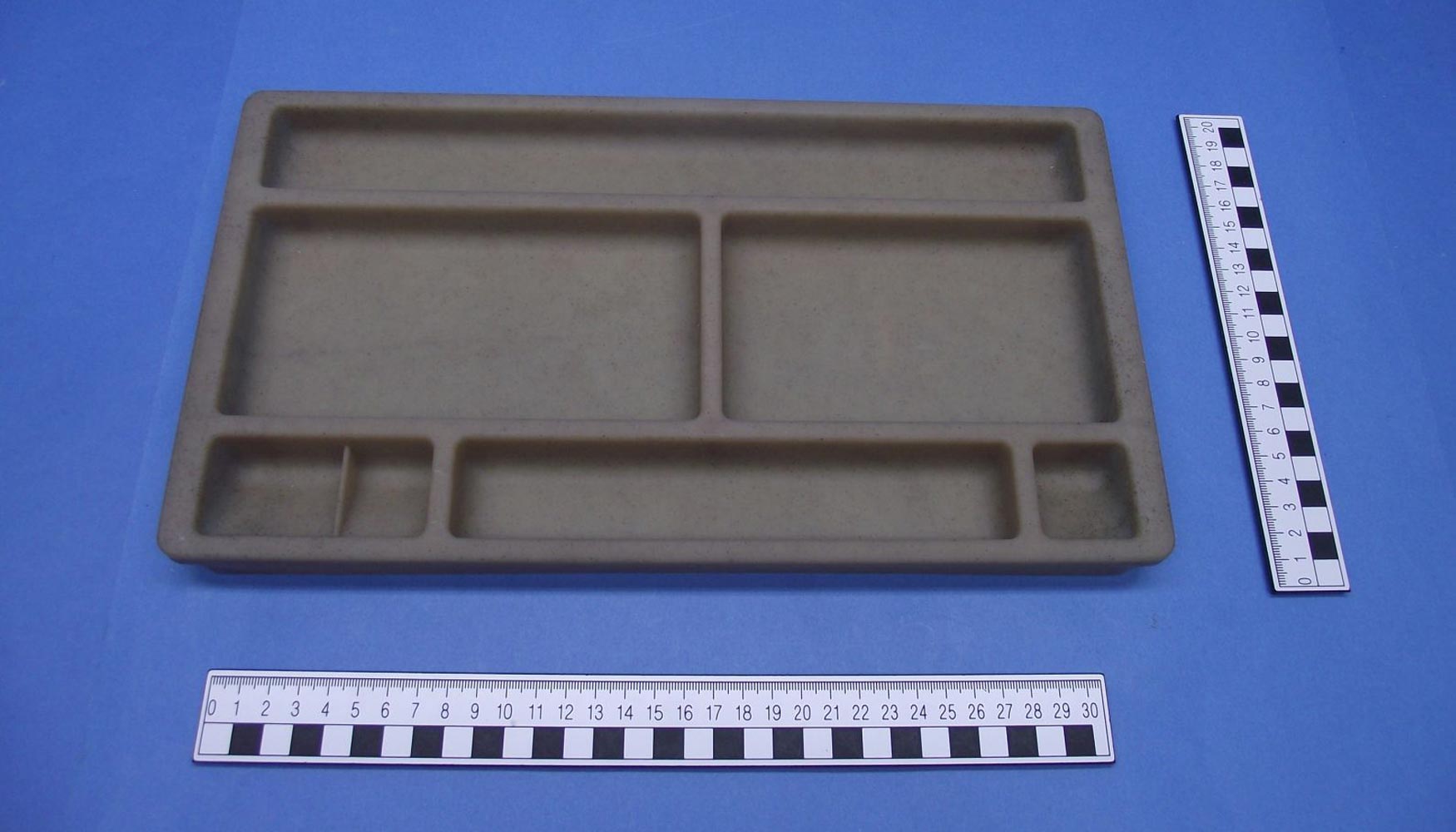
Bandeja portalápices marrón.
¿En qué sectores o ámbitos de aplicación tienen más futuro?
Los masterbatches se han desarrollado para emplearse en los procesos de moldeo por inyección, por tanto en cualquier tipo de sector. Nosotros lo hemos probado en estos dos, pero pueden aplicarse en cualquier ámbito industrial en el que se inyecten piezas, como pueden ser la automoción, el menaje, el calzado o los electrodomésticos, entre otros.
Además del respeto por el medioambiente, ¿qué otras ventajas ofrece por ejemplo un masterbatch biodegradable al inyectador?
Depende de la coloración que se añada, le otorga a la pieza un aspecto diferente, más natural. Si no se le añade color, parece madera. Esto permite desarrollar productos con aspecto de madera pero con la ventaja de poder transformarlos mediante un proceso de inyección convencional, es decir, sin tener que modificar los sistemas de producción existentes. Con cualquier inyectora normal se pueden emplear.
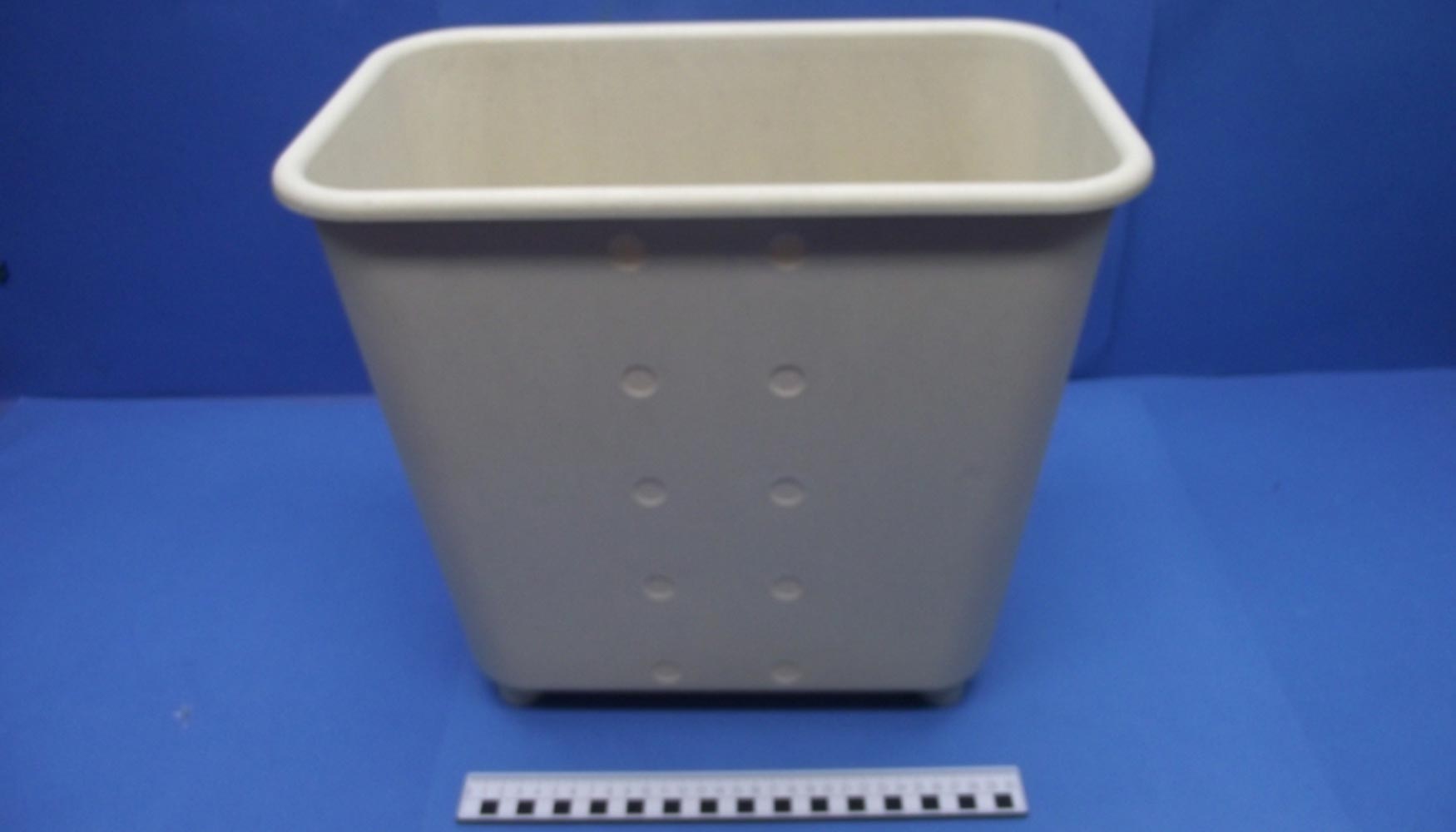
Papelera fabricada con los nuevos masterbatches de color beige.
¿Qué etapas ha tenido el proyecto?
En los tres años que ha durado el proyecto, ha tenido diferentes fases. Primero, se realizó una búsqueda de inforamción relacionada con incorporación de residuos naturales en los plásticos. Hicimos un estudio más profundo sobre la cáscara de almendra y las diferentes variedades del fruto seco, porque según el tipo, la cáscara tiene unas propiedades distintas, de dureza o de tonalidad. Estudiamos cómo se modificaba el plástico dependiendo de la variedad y qué ocurría si incorporábamos mezclas.
¿Cáscaras de almendras mezcladas?
Sí, porque normalmente los suministradores de cáscara las mezclan, no se separan por variedades. Entonces, llevamos a cabo un estudio para ver si influía y lo cierto es que las propiedades no cambiaban excesivamente, por lo que se decidió trabajar siempre con mezcla, más fácil de conseguir y más económica.
¿Qué más fases superaron?
Realizamos estudios para ver si tratábamos la cáscara para hacerla más compatible con el polímero, analizamos los diferentes porcentajes de cáscara dentro del plástico para ver cómo éste cambiaba su aspecto, sus propiedades mecánicas y se modificó el tamaño de partícula, porque en función de si el tamaño es más fino o másgrueso, tanto el aspecto como las propiedades mecánicas cambian.
Tras numerosas etapas iniciales más centradas en el laboratorio, comenzamos las pruebas de inyección de todas las formulaciones, que eran muchísimas, obteniendo finalmente 33 formulaciones de masterebatch adecuadas.
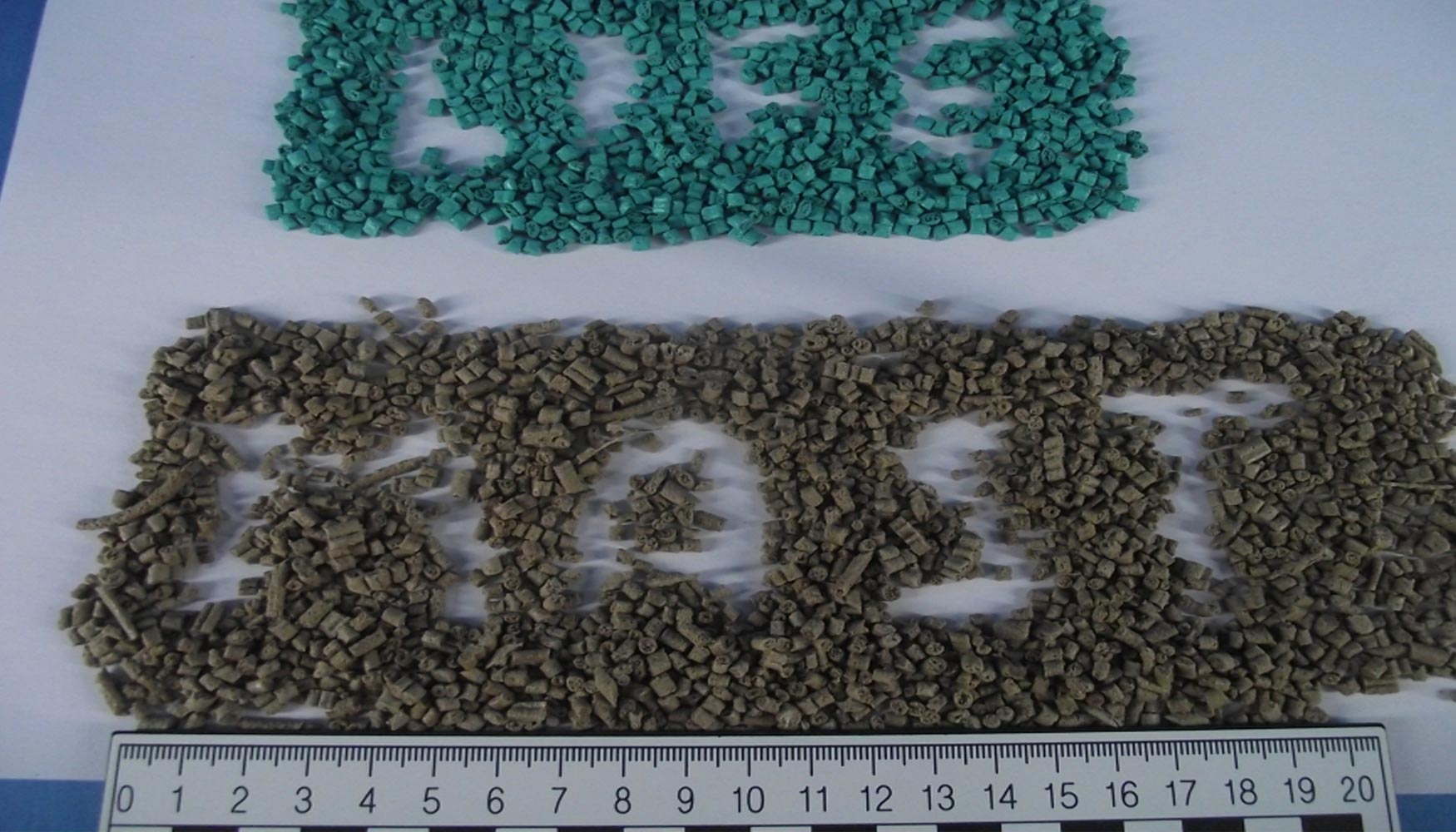
Masterbatches obtenidos en el proyecto.
Con las tres empresas implicadas…
Sí, además ellos también indicaron sus requerimientos, por ejemplo, los jugueteros sugerían que se pudiese inyectar de una forma específica, que los colores fuesen vivos porque son para niños, que cumpliesen las normativas de seguridad del juguete, que las propiedades mecánicas, en el caso del mobiliario auxiliar, llegaran a unos valores determinados, por ejemplo a la hora de fabricar una silla, o que el tamaño de partícula de la cáscara triturada fuese inferior a los de las boquillas de extrusión o inyección.
Con todos esos requerimientos y con las formulaciones conseguidas, se seleccionaron algunas, se optimizaron y en el ámbito más industrial, la empresa de masterbatches trabajó en el color a nivel de laboratorio. Finalmente se realizaron pruebas con demostradores reales. Primero, pruebas de inyección de piezas pequeñas, después de mayor tamaño: juguetes, sillas, accesorios de escritorio, bandejas de portalápices, papeleras, etc.
¿El proceso es exactamente igual que una inyección convencional?
Tuvo que llevarse a cabo una optimización de todo el proceso de inyección de esas piezas porque los plásticos biodegradables no se inyectan igual que un polipropileno convencional por ejemplo, algo que limitó ciertos tamaños y geometrías. Se probaron varios tipos de plástico y se llevaron a cabo multitud de pruebas hasta optimizar las condiciones de inyección.
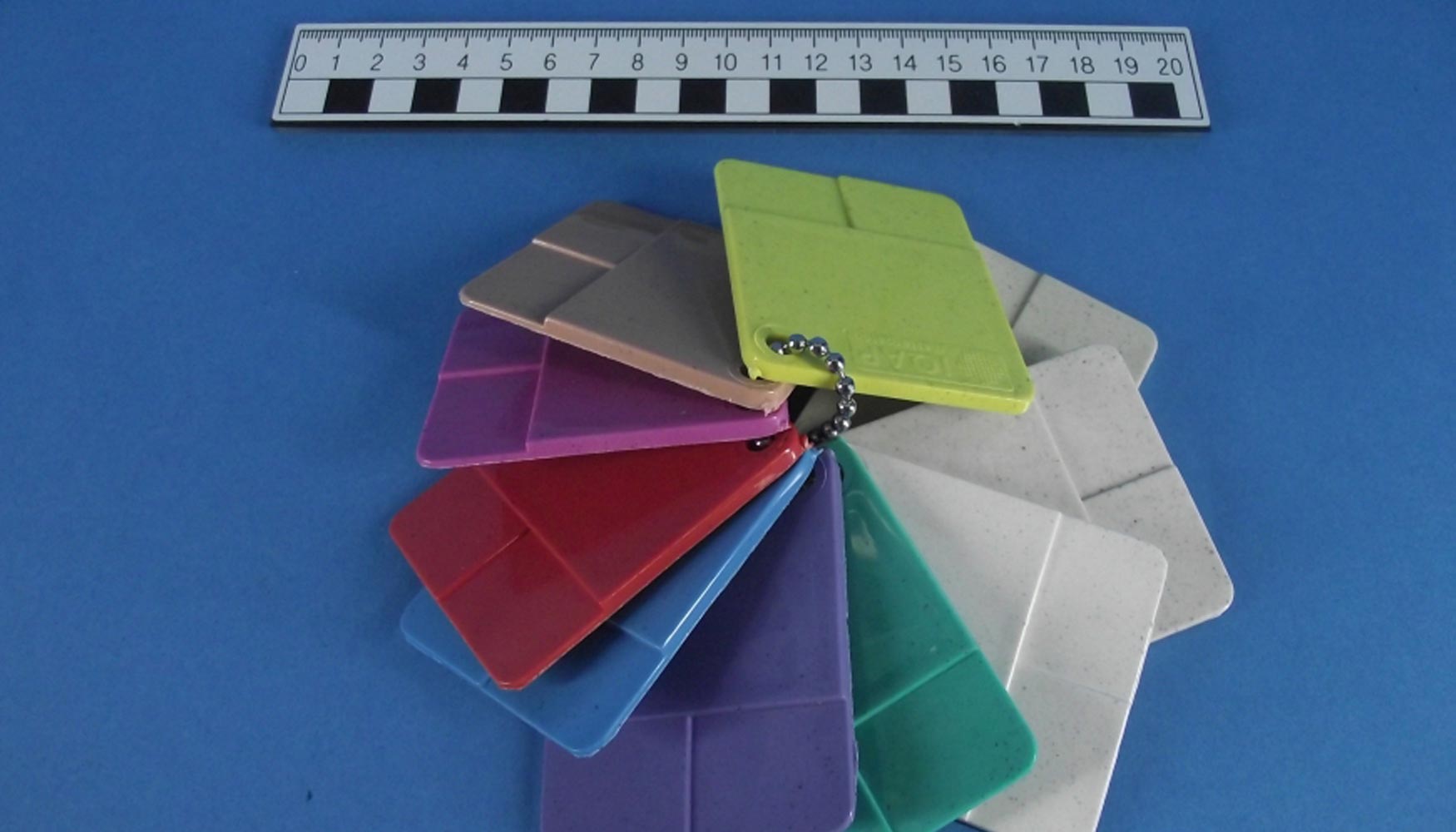
¿El resultado?
Los diferentes masterbatches biodegradables con cáscara de almendra ya están listos para la venta y accesibles a las empresas que lo requieran.
Decía que han difundido el proyecto dentro y fuera de España, ¿Qué tipo de acogida ha tenido el proyecto Europa?
Muy bueno, hemos tenido muchas muestras de interés. Nos han invitado a dar charlas, congresos, escribir artículos y mucha gente se ha interesado por los resultados y las piezas. Esta semana nos han solicitado llevar algunas para poder mostrarlas en una feria europea en Berlín.
España es un gran productor de almendra, por eso, el proyecto resultaría interesante para dar salida al volumen de residuos. ¿Han mostrado interés estas empresas del sector de la alimentación?
Sí, varios productores de almendra o cáscara nos han contactado para ofrecer sus productos, para ver si encajan dentro del sistema de producción que siguen las empresas.
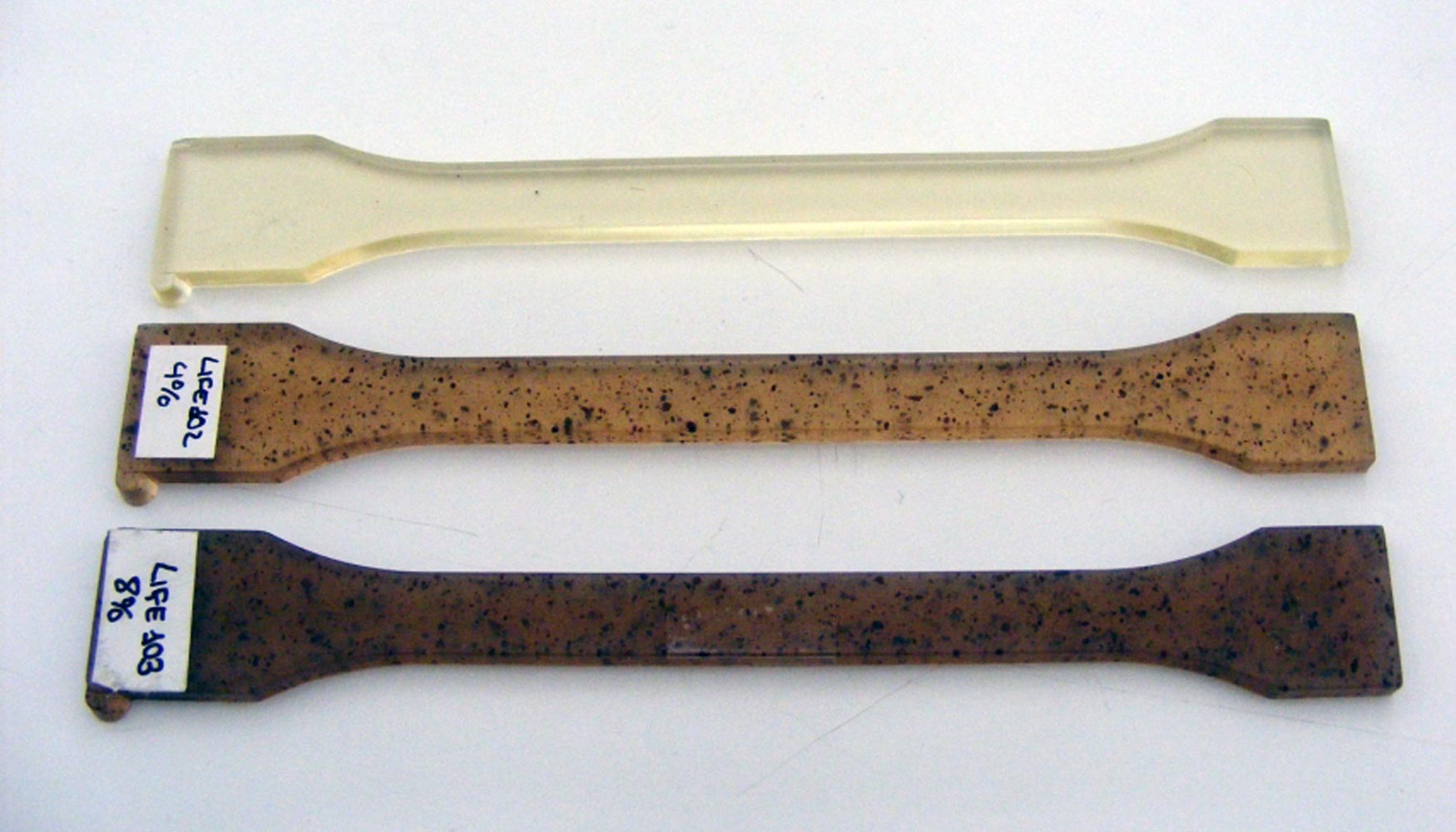
¿En qué otros proyectos relacionados con el sector del plástico está implicado Aiju?
Recientemente estuvimos en Bruselas en la reunión de inicio de un proyecto para personalizar productos de juguete y de mobiliario mediante tecnologías convencionales y de fabricación aditiva o impresión 3D. Se trabajará en toda la parte de modificaciones de diseño y conexión y se creará una plataforma donde el usuario pueda decidir la personalización de un producto y que éste se pueda fabricar o bien con tecnologías convencionales o bien con tecnología aditiva. Y además, lo pueda tener en casa, cumpliendo con la normativa de seguridad, algo que hasta ahora no se contempla.
¿La seguridad?
Claro. Si alguien se fabrica en su casa una pieza de plástico con una impresora 3D, por ejemplo, un juguete, no se sabe si es seguro o no. Lo que queremos además en esta plataforma es integrar cuestiones medioambientales. Es decir, si modifico el diseño y cambio el espesor, ¿será menos o más sostenible?, ¿influirá a la horade cumplir la normativa de seguridad?, etc.. El sistema hará una predicción o ensayo virtual en el caso de que sea posible y si no, lo valoraríamos desde Aiju. Se trata de un proyecto de gran envergadura, de cuatro años de duración.