Composites: propiedades útiles pero difíciles de mecanizar
La construcción aeronáutica sería imposible sin los compuestos y también en la industria del automóvil tienen un papel cada vez más importante. No obstante, su procesamiento y mecanizado resultan difíciles. Para la máquina de mecanizado y las herramientas son extremadamente exigentes sobre todo los plásticos reforzados con fibra de carbono en los que la fibra está insertada en una matriz, así como los compuestos de materiales con una estructura por capas. Los fabricantes exponen las posibles soluciones en la próxima AMB, la exposición internacional para el mecanizado de metal que se celebra del 16 al 20 de septiembre de 2014 en Stuttgart.
El ambiente del sector de compuestos es sumamente positivo. A mediados de año se juntaron las cuatro organizaciones técnicas, es decir, la Asociación Industrial para Plásticos Reforzados (AVK), Carbon Composites, Plásticos Reforzados con Carbono (CFK) - Valley Stade y el Foro Composite Technology en la VDMA para formar la Asociación Profesional Composite Germany y una de sus primeras acciones conjuntas fue la realización de una encuesta sobre la situación económica. La mayor parte de las empresas asociadas la califican como “sumamente positiva o muy positiva", según constata Walter Begemann, director del proyecto del Foro de la VDMA. Lo que resulta especialmente satisfactorio para los fabricantes de máquinas-herramienta y herramientas de precisión es que dos terceras partes planifican un compromiso aún mayor. Los impulsos de crecimiento más importantes proceden de las industrias alemana y asiática del automóvil y de la aeronáutica. Es por ello que Michael Effing, presidente de la asociación, califica los compuestos como “una tecnología clave para el emplazamiento industrial en Alemania”.
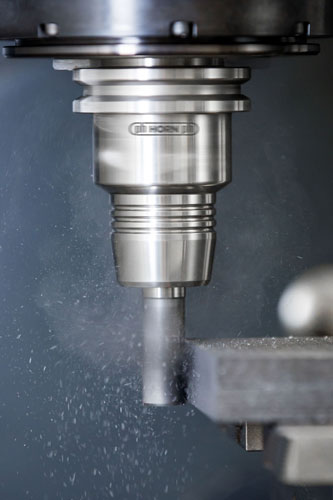
Lo mismo opina el catedrático Frank Barthelmä, director general de la Sociedad para Tecnología de Producción y Desarrollo (GFE) e.V., Schmalkalden. No obstante, advierte acerca de algunos de los retos centrales: el peligro de las deslaminaciones, vidas útiles insuficientes de las herramientas y la aspiración de las partículas de polvo generadas. “A la hora de diseñar soluciones para problemas de este tipo, resulta imprescindible contemplar toda la cadena de proceso para el mecanizado de los compuestos, comenzando con el concepto de máquina, los parámetros del proceso, la calidad de los componentes y, por supuesto, también las herramientas”. La GFE ha conseguido adecuar perfectamente las herramientas en un proceso iterativo a la tarea de mecanizado. En concreto: “Gracias a unas tecnologías de mecanizado adecuadas como el pulido por cepillado, el micro-acabado mediante rectificado de arrastre o el micro-granallado, ha sido posible fabricar de forma reproducible unos radios de filos de corte perfectamente definidos de unos pocos micrómetros, todo ello a lo largo de todo el filo de corte de la herramienta”. Estos aspectos son especialmente importantes en caso de herramientas combinadas o escalonadas para poder evitar las deslaminaciones, según comenta Barthelmä. Otro paso es el recubrimiento. En este sentido, las capas de oxinitruro con oxígeno insertado han resultado especialmente aptas, mejorando las vidas útiles en más del doble en comparación con las herramientas convencionales de metal duro macizo. Los expertos de mecanizado de Schmalkalden esperan unos resultados aún mejores de capas similares a diamantes (DLC: carbono tipo diamante) que pueden convertirse en una alternativa económica para los diamantes policristalinos (PKD) o las herramientas de diamante CVD (CVD: deposición en fase de vapor) cuyo coste es muy elevado.
También los fabricantes de máquinas-herramienta deben realizar su aportación. Barthelmä expone que “altas velocidades con novedosos husillos encapsulados son una de las condiciones para el mecanizado de compuestos. A todo ello se añaden la máxima dinámica de la máquina y la posibilidad del fresado de varios ejes, tal y como ocurre en el mecanizado lateral o simultáneo de cinco ejes”. Además, muestra gran esperanza en el mecanizado con métodos de producción híbridos, como el fresado asistido por ultrasonido.
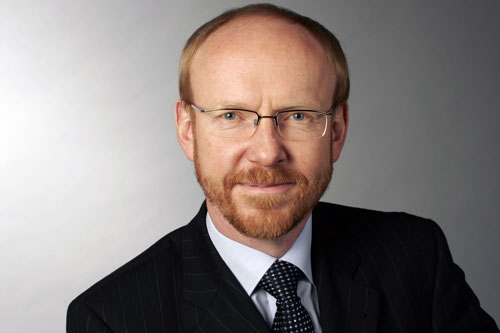
Reducción de costes a pesar de unas soluciones personalizadas
Peter Büttler, responsable de actividades de construcción ligera de Komet Group, asume que las exigencias son heterogéneas: “Por un lado, las fibras se diferencian por su material, longitud, espesor y sentido de fibra. Por el otro lado, el mercado ofrece actualmente más de 100 resinas diferentes para la matriz: duroplásticos y termoplásticos que deben ser mecanizados en frío, y elastómeros que requieren una alta velocidad de corte, debiéndose mantener bajo el calor de fricción en la ranura de viruta a altas velocidades”. Correspondientemente, es muy importante mantener una estrecha colaboración entre el usuario y el fabricante de herramientas. “Nosotros comprobamos desde la fase previa todos los factores relevantes, como el material a mecanizar, pero también la tecnología de mecanizado”. El trabajo es diferente dependiendo si se realiza en un centro de mecanizado, con un robot o con máquinas de mecanizado manual. A todo ello debe añadirse la sujeción de la pieza de trabajo y los correspondientes riesgos de vibraciones. Otros factores: la refrigeración, los números de revoluciones, la tarea de mecanizado propiamente dicha y la aspiración.
Lo ideal sería una herramienta universal para un mayor número de aplicaciones, “pero para ello actualmente no existe ninguna solución económica, ya que los compuestos de materiales extremadamente inhomogéneos establecen unas exigencias muy variadas”, explica también el catedrático Diethard Thomas, director de la LMT Group Academy. Por lo general es necesario adecuar la herramienta de forma personalizada a los materiales compuestos. Sin embargo, en caso de compuestos de materiales en base a materiales diferentes ensamblados por capas, una solución para garantizar la rentabilidad podría ser “orientar los valores de corte al socio de materiales más difícil, por ejemplo, en caso de compuestos de CFK/aluminio o CFK/titanio”. Thomas percibe una necesidad de perfeccionamiento permanente ya que los materiales se están modificando y optimizando constantemente, sobre todo por su elevado coste (suponen aproximadamente el 50 por ciento del coste): “En consecuencia también surgen constantemente nuevas exigencias con respecto al diseño de las herramientas para seguir optimizando el proceso de mecanizado, es decir, las versiones de herramientas y las recomendaciones de valores de corte están sometidas a cambios constantes”.
Aribert Schroth, especialista de producto para materiales de corte ultraduros del fabricante de herramientas Paul Horn, desaconseja comparar siempre los compuestos únicamente con plásticos reforzados con fibra de carbono. “Es posible mecanizar los grupos contiguos con las mismas herramientas pero con diferentes parámetros de mecanizado”. Este punto de partida es similar al que persigue el fabricante de herramientas Mapal. Según Peter Müller-Hummel, jefe de la unidad de negocio Aeroespacial y Compuestos: “Como las exigencias suelen ser idénticas, seleccionamos siempre el caso más crítico lo que nos permite cubrir un gran número de las aplicaciones menos críticas”. No obstante, la intención de Mapal es ayudar al cliente a ahorrar costes también por otras vías, tal y como lo explica Müller-Hummel: “Actualmente, la realización del mecanizado en una sola operación de trabajo, en lugar de entre tres y cinco pasos del proceso, tiene el máximo potencial”. Además, los recubrimientos especiales para herramientas proporcionan unas vidas útiles más largas reduciendo, por ejemplo, el coste por taladro.
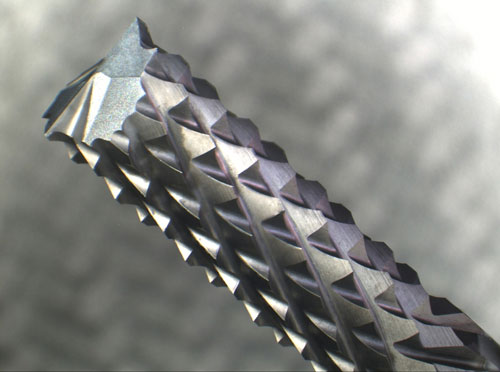
Por lo general, en lo que al desgaste de las herramientas se refiere, aún existe mucho potencial para incrementar claramente la rentabilidad, tal y como refleja Schroth de Paul-Horn: “En lo que a la investigación y comprensión de los procesos que provocan el desgaste del filo se refiere, aún queda mucho camino por recorrer”. Él centra la atención sobre otro aspecto, junto con la exigencia a los fabricantes de materiales: “La prevención resultaría más eficaz desde la fase de desarrollo del material. Asimismo, unas especificaciones más estrechas y claras en la producción repercutirían de forma positiva sobre la rentabilidad”. En este sentido, la tendencia actual hacia un menor porcentaje de resina y una orientación estrictamente unidireccional de las fibras resulta ventajosa, haciendo que el material sea más previsible y calculable. Este experto en construcción ligera opina que la correspondiente mayor deslaminación puede ser controlada: “Lo que importa es que el filo de la herramienta esté afilado y siga estándolo, para lo cual nos viene bien prácticamente cualquier ayuda”. Los sensores pueden servir para ello. Schroth: “Además de la detección del desgaste que aporta máxima utilidad, el comportamiento de oscilación del componente resulta fundamental para el funcionamiento y la vida útil de la herramienta utilizada”.
Una detección exacta del desgaste es también indispensable para el desarrollo en el wbk, Instituto para la Tecnología de Producción, en Karlsruhe. El empleado científico Stefan Klotz ha analizado con más detalle los daños de material producidos por el desgaste de la herramienta durante el taladrado. Ha descubierto que junto con el desgaste de la herramienta “cambian las relaciones de engrane del filo de herramienta, dando lugar a cambios en los sentidos de fuerza del proceso y un incremento de los daños en la pieza de trabajo”. Klotz propone por tanto una “adaptación dinámica de los parámetros de proceso al actual estado de desgaste de la herramienta“con el fin de”reducir directamente los daños producidos en las capas de cobertura”.
La máquina-herramienta clásica suele resultar demasiado cara
Mientras que los fabricantes de herramientas siguen investigando y desarrollando para el atractivo mercado del futuro del mecanizado de compuestos, los fabricantes de máquinas-herramienta clásicas para el mecanizado parece que tienen un problema general con los compuestos: normalmente sus máquinas son demasiado pequeñas y demasiado caras. Ivica Kolaric, responsable del Departamento para Materiales Funcionales en el Instituto Fraunhofer para Tecnología de Producción y Automatización IPA explica lo siguiente: “Para el mecanizado de los compuestos se utilizan frecuentemente máquinas que tienen su origen en el sector del mecanizado de madera y plástico”. No es de extrañar si se analizan los precios específicos por superficie. Si en caso de una máquina-herramienta clásica, el precio por metro cuadrado de superficie de mecanizado puede alcanzar los 600.000 euros, las máquinas de mecanizado de madera comienzan con unos precios en torno a los 10.000 euros por metro cuadrado, por supuesto, con una precisión claramente inferior. La situación podría cambiar modificando las exigencias de la industria del automóvil. Mientras que en la industria aeronáutica y en las instalaciones eólicas se emplean piezas muy grandes, muy frágiles y de menor precisión, la industria del automóvil requiere piezas mucho más pequeñas que deben producirse rápidamente en grandes cantidades y con una elevada precisión. La conclusión de Kolaric: “La oferta de los fabricantes de máquinas debe ser más económica y los fabricantes de máquinas de mecanizado de madera deben mejorar la precisión”.
Esta particularidad también se ha detectado en Mag Ias, tal y como lo explica Matthias Meyer, vicepresidente de Composites: “La gama de piezas principales incluye componentes alargados de paredes finas y, por tanto, tanto el área de trabajo de la máquina como la mesa de la máquina deben dimensionarse correspondientemente. A pesar de la falta de mecanizado de forma libre, las geometrías de piezas hacen necesario en la mayoría de los casos un mecanizado en cuatro o cinco ejes para generar unos bordes de corte ortogonales con respecto a la superficie del componente”. Además, las exigencias con respecto al husillo de herramienta son diferentes a las del mecanizado de metales. Como competidor tecnológico, Meyer ha identificado sobre todo el corte por chorro de agua; aunque este método todavía pelea con desventajas como daños en los componentes y grandes volúmenes de basuras especiales. “Es por ello que en Mag se ha decidido ampliar consecuentemente el mecanizado por fresado de los compuestos y recurrir a los conocimientos de la automatización y de la producción en serie”.
Otro fabricante de máquinas-herramienta clásico que asume el reto es DMG Mori. “Además de un concepto de máquina a largo plazo y máxima dinámica, la máquina debe estar especialmente preparada para el mecanizado de polvos abrasivos”, explica Patrick Diederich, director general de la empresa Sauer GmbH en Pfronten, una filial de DMG Mori. La gama incluye un concepto híbrido en forma de máquinas ultrasónicas, ideales precisamente para el mecanizado de materiales difíciles. En este proceso, un sistema inductivo de actuadores solapa la rotación de la herramienta con una cinemática de movimiento oscilante en sentido longitudinal. “De este modo conseguimos una clara reducción de las fuerzas de proceso que están actuando en torno a un 40%, obtenemos bordes limpios y evitamos roturas de fibras, así como la deslaminación a la vez que aumentan los avances”.
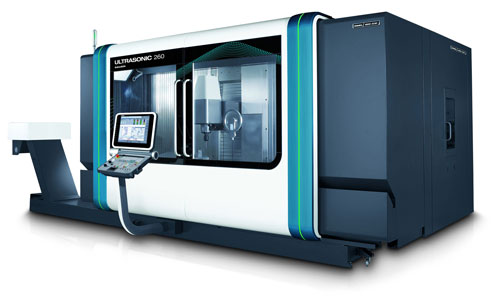
Un gran problema para el mecanizado lo suponen los polvos abrasivos y de conductividad eléctrica. “La integración de un concepto de aspiración integral que funcione perfectamente es uno de los factores más importantes. Además de una aspiración de alto rendimiento con vigilancia integrada de polvo fino, así como una recuperación de calor en el caso óptimo, la máquina debe disponer de un área de trabajo cerrada con una aspiración integrada del recinto”. Para evitar directamente que los polvos puedan producir peligros, se han ubicado los accionamientos y las guías fuera del recinto de máquina. Además, se han aislado los ejes X y Z. Un consejo muy serio de Diederich: “Por lo general deben protegerse todos los componentes eléctricos. Además, el husillo de mecanizado debe estar libre de aceite para evitar contaminaciones en el componente”.
Los polvos que se van generando y sus repercusiones sobre la seguridad y la salud son el reto principal para el empleado de IPA Ivica Kolaric, además de la reducción de costes y la prolongación de la vida útil de las herramientas. En su opinión, tanto las personas como las máquinas estarán expuestas a riesgos mientras no se analicen detenidamente los efectos concretos que tienen estos polvos y se defina la mejor manera de tratarlos: “Los polvos no solo pueden suponer un peligro para la salud, sino que pueden volar a través de las naves de producción a otras máquinas y provocar anomalías en ellas”. En el IPA un grupo de trabajo en el que también participa la mutua profesional está abordando estas cuestiones. El señor Meyer, empleado de MAG, también confirma el problema de tener que proteger a las personas y las máquinas: “La integración de la aspiración y la impermeabilización simultánea de los componentes de las máquinas supone en este sentido un aspecto clave del trabajo. No obstante, no solo se generan polvos, sino también piezas residuales muy grandes que no puede evacuarse del área de trabajo de forma segura, garantizando la seguridad del proceso recurriendo a los mecanismos convencionales como transportadores sinfín”. Otro punto central es la fabricación de medios de construcción para una manipulación y sujeción seguras de estructuras de paredes finas.
Por lo general, el mecanizado de compuestos establece altas exigencias para el desarrollo de tecnología, tal y como lo explica Patrick Diederich: “Una combinación de los materiales más variados que da lugar a un comportamiento de material extremadamente anisótropo, requiere optimizar todos los datos del proceso, las herramientas, así como la selección de los lubricantes refrigerantes”. Además del mecanizado propiamente dicho, deben tenerse en cuenta también los pasos siguientes del proceso, como los métodos de pegado, la pintura o el procesamiento posterior. Prácticamente todas las operaciones de rebordeado requieren un fresado de varios ejes. “En este sentido, precisamente en el mecanizado lateral y también en el simultáneo de cinco ejes, especialmente la dinámica de los diferentes ejes debe sincronizarse perfectamente entre sí, ya que solo así es posible garantizar un rápido posicionamiento o reposicionamiento durante las exigentes tareas de mecanizado”, destaca Diederich.
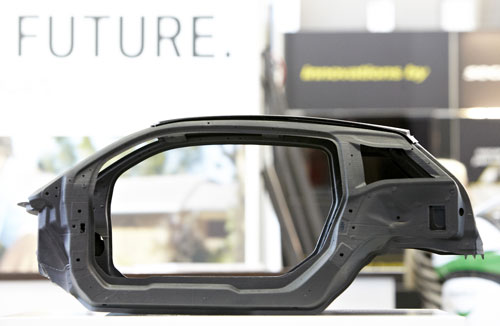
Pero incluso las máquinas-herramienta pueden beneficiarse de los compuestos. En este sentido, en DMG Mori se están analizando los sectores en los que estos materiales pueden aportar ventajas. Florian Feucht, director del Departamento de Desarrollo de Composite Sauer en Stipshausen: “En una primera fase nos centramos en las masas en movimiento y el aumento de la eficiencia energética con el objetivo de conseguir una dinámica máxima con la correspondiente sostenibilidad”. En cambio, la posibilidad de compensar los desplazamientos inducidos térmicamente mediante el empleo de fibra de carbono resulta menos interesante. “Este aspecto ya lo tenemos bastante controlado con los materiales actuales”. También en el caso de Mag son muy importantes los compuestos para la construcción de máquinas-herramienta, sobre todo cuando se trata de la dinámica, tal y como lo explica Matthias Meyer: “Son muchos los sectores en los que nuestras máquinas tienen que acelerar las masas en poco tiempo”.
Para la AMB 2014 que se organizará entre el 16 y el 20 de septiembre se esperan más de 90.000 visitantes profesionales y aproximadamente 1.300 expositores que mostrarán sobre una superficie de 105.000 metros cuadrados brutos sus innovaciones y perfeccionamientos de desarrollo en el sector de la tecnología de arranque de viruta y en la industria de herramientas de precisión, así como herramientas de sujeción, CAD, CAM, CAE, software, rectificadoras, sistemas de manipulación de piezas y herramientas, y técnica de medición. La AMB 2014 se ve apoyada por las asociaciones patrocinadoras VDMA Asociación especializada en herramientas de precisión, VDMA Asociación especializada en software, así como la VDW Asociación de fábricas alemanas de máquinas-herramienta.