Los ascensores Revolution ofrecen un montaje sencillo, rápido y seguro
Algunas de las principales ventajas diferenciales que caracterizan a los ascensores ‘Revolution’, lanzados al mercado hace tres años por GLE, empresa perteneciente al Grupo Imem Ascensores, es su facilidad de montaje, así como su capacidad de adaptación y aprovechamiento de huecos difíciles. Disponibles en un rango en ascensores para obra nueva hasta los 1.000 Kg y en ascensores para reformas y sustituciones con un diseño innovador que maximiza el área disponible de hueco, en este último caso se utiliza únicamente 350 mm de ancho de hueco para la parte mecánica, lo que permite instalar ascensores de 8 personas donde normalmente entran solo de 6 personas. Hablamos con Luis Castillo, responsable de montaje de la delegación de Imem Ascensores en Cantabria con una experiencia de más de 30 años en el montaje de toda clase de ascensores, quien también participa de manera activa con el Departamento de I+D, colaborando en los diseños de principio a fin y llevando a los huecos reales los ascensores diseñados por Ingeniería. Esta práctica le permite tener una percepción real de las ventajas y desventajas que tienen los equipos diseñados y aportar una serie de mejoras que no se pueden realizar en la fase de diseño CAD, además de asegurar a la empresa que, antes de comercializar sus equipos, estos han sido testados por su primer usuario: el montador.
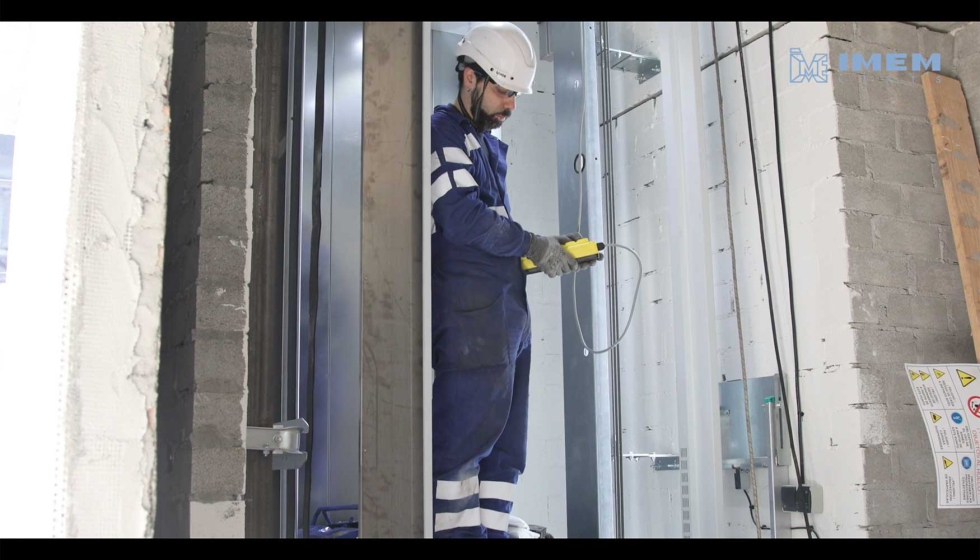
¿Qué es lo primero que sorprende a los montadores cuando reciben los equipos en la obra?
Bajo mi punto de vista, una de las cosas que más llama la atención al recibir el equipo en la obra es el embalaje y la distribución. Cada bulto viene marcado para colocarse en su posición específica y no esparcir un montón de cajas semiabiertas por la obra. Al final, en la obra todo cuenta y esto nos permite un ahorro de tiempo desde el minuto cero. Los componentes vienen premontados en subconjuntos, muy fáciles para manejar en obra y listos para llevarlos a su posición final; además, las bolsas de tornillos que se necesitan para unirlos entre sí y generar de esa forma el conjunto final vienen junto a cada uno de ellos, por lo que no se pierde tiempo buscándolas en otros bultos específicos solamente de tornillería.
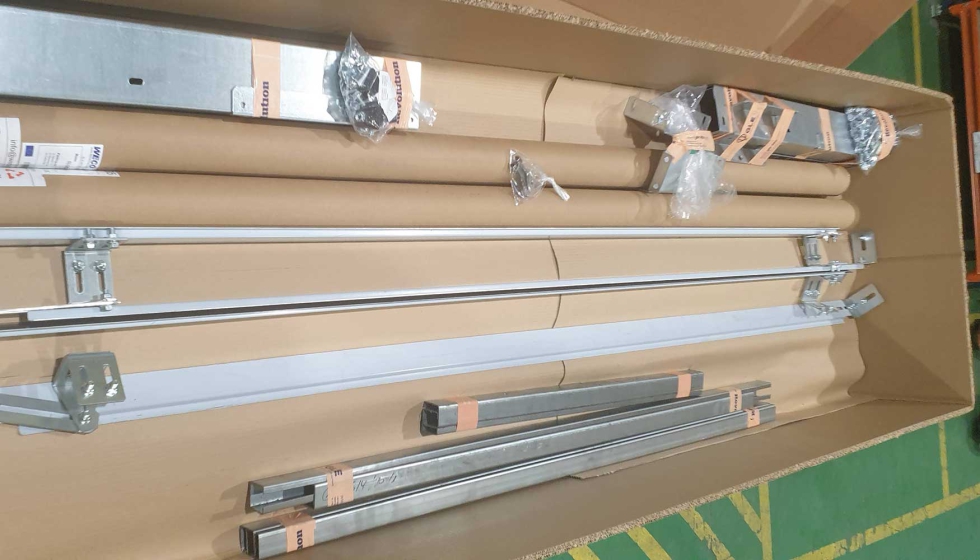
¿Qué tal el montaje con solo una persona?
Mi principal preocupación siempre es la seguridad de los operarios. En este caso, se nota el diseño del propio ascensor: piezas ligeras con un método de montaje muy estudiado. El método de montaje no es el convencional, pero, una vez aprendido, es una maravilla y los ahorros en tiempo y personal son tangibles. Además, la seguridad es máxima en todo momento y no tenemos ninguna incidencia en este sentido.
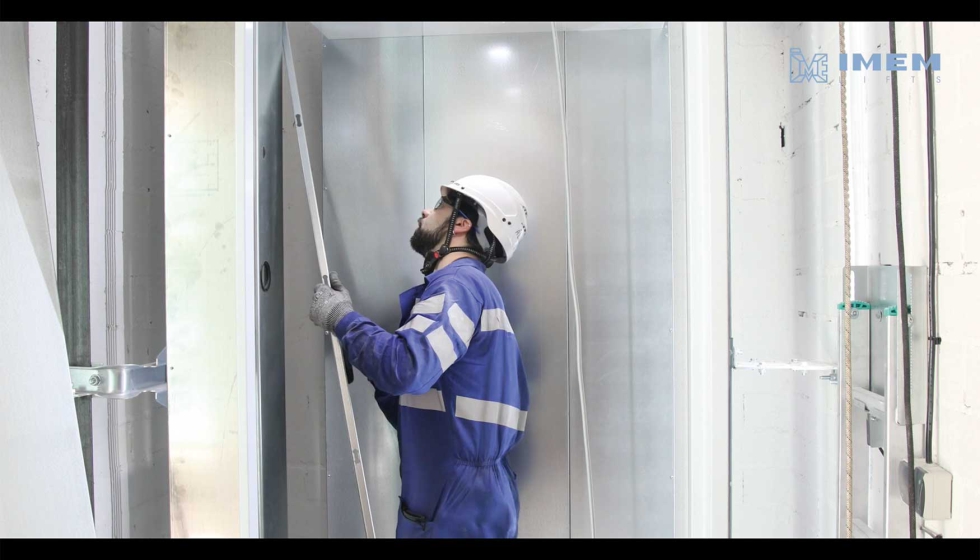
¿Se cumplen los tiempos establecidos?
Lo normal es que las primeras unidades lleven más tiempo; es como montar un mueble de Ikea: el primero te lleva mucho tiempo, pero el segundo, prácticamente la mitad. Nosotros, para equipos estándar de 5 paradas, estamos en un tiempo de montaje por debajo de las 90 horas en muchos casos. Eso sí, con la obra en buenas condiciones, el material repartido según las indicaciones del manual y con montadores buenos, se entiende. En cualquier caso, los ahorros en tiempo están ahí.
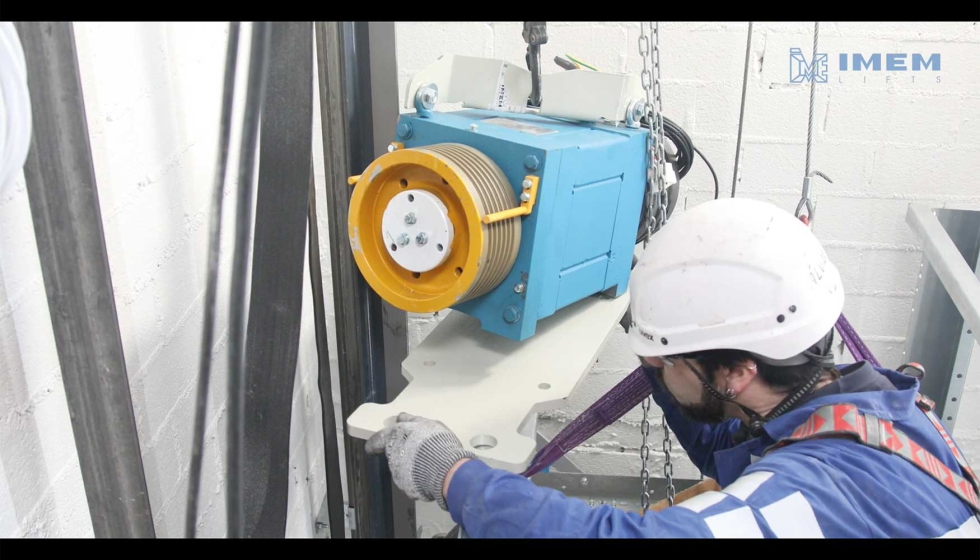
Además, hay que tener en cuenta la cantidad de componentes que no hay que montar, sobre todo en la parte eléctrica, ya que no existen muchos elementos en el hueco como finales, prefinales, imanes… Nada que decir del limitador, que siempre es un tema complicado de montar bien, sobre todo en recorridos largos o en obras con limitación de espacio. En estos equipos, el ‘limax’ actúa de limitador, desapareciendo este, y tampoco lleva la tradicional barra de acuñamiento entre los paracaídas –además, estos ya vienen montados en los largueros y lo único que hay que hacer es conectarlos eléctricamente–.
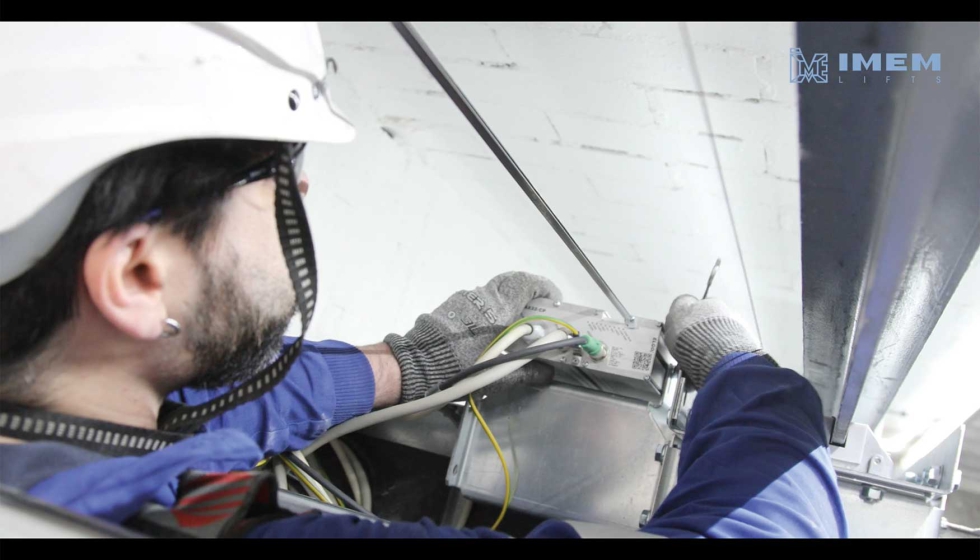
¿Y las cuñas nuevas?
Eso es maravilloso. Ahorrarte la regulación de la timonería y ajustar las cuñas en un minuto es un alivio. Además, las pruebas de paracaídas, que antes podían llevarte medio día, ahora se hacen en un rato y con mucha más seguridad.
¿Desde el punto de vista de la seguridad en el montaje, qué podrías destacar?
Como ya he comentado, si se siguen los procedimientos, el montaje es muy seguro. Nosotros no utilizamos andamios, así que, una vez tirados los plomos desde la parte superior, hacemos lo concerniente al foso y montamos los primeros tramos de guías y la cabina –sin decoración– para utilizar el techo de la misma como plataforma de montaje e ir subiendo por el hueco en ella, tirada con un tractel y donde ya tenemos instalado el sistema paracaídas, con lo que la seguridad es doble. Todo el montaje se compone de partes modulares perfectamente ensamblables que hacen que el montaje sea rápido y seguro. Además, gran cantidad de las pruebas de funcionamiento se realizan desde fuera del hueco: no puede ser más seguro.
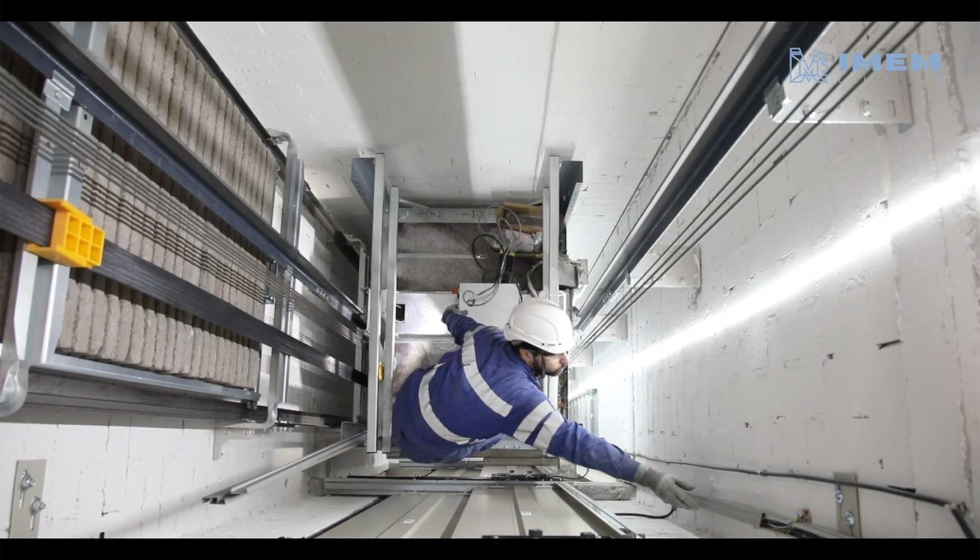
El montaje de la máquina, sobre todo en huecos pequeños, parece complicado, ¿no?
Como se puede extraer de todo lo comentado anteriormente, el procedimiento de montaje está muy trabajado y eso se nota. El posicionamiento de la máquina se realiza con unos útiles específicos que hacen que se pueda realizar de modo fácil y rápido.