Nuevos tejidos compuestos a partir de hilos híbridos de matriz termoplástica IMAMCI/2018/1 – 2018
Grupo Fibras Técnicas y Nanotecnología de Aitex
05/03/2019En la actualidad, los materiales de matriz termoestable predominan en el mercado. Sin embargo, la tendencia es la sustitución de las matrices termoestables por matrices termoplásticas. Esta predominancia de los materiales termoestables se debía a la superioridad de prestaciones en comparación con los termoplásticos. Sin embargo, en los últimos años se ha avanzado en el desarrollo de materiales termoplásticos obteniendo prestaciones similares a los termoestables. Esto supone un avance importante en los materiales compuestos, debido a que el procesado de los materiales termoplásticos es más rápido y simple que el de los termoestables debido a que no necesitan ser curados, se pueden reprocesar, se pueden unir por fundido y se pueden reutilizar. Sin embargo, también presentan alguna problemática ya que los materiales termoplásticos son sólidos a temperatura ambiente y tienen alta viscosidad en estado fundido, lo que dificulta la impregnación de las fibras de refuerzo.
El procesado de materiales compuestos de matriz termoplástica se lleva a cabo por métodos similares a los empleados para los materiales compuestos de matriz termoestable. En este proyecto se propone mejorar el procesado de este tipo de materiales compuestos de matriz termoplástica, además de mejorar también su comportamiento mecánico gracias a la incorporación de polímeros técnicos como el PEEK y/o PEI, que son polímeros de alto punto de fusión y de altas propiedades mecánicas, eliminando perdidas de resistencia o rigidez que se dan con el uso de otro tipo de polímeros con temperaturas de fusión inferiores.
Objetivos
El proyecto Refortex se ha centrado en el desarrollo de nuevos materiales compuestos de altas prestaciones por medio de cinco fases de trabajo, donde el desarrollo de hilos híbridos cobró una gran importancia. Este proyecto cuenta con el apoyo de la Conselleria d’Economia Sostenible, Sectors Productius, Comerç i Treball de la Generalitat Valenciana, a través del Ivace.
La primera fase se basó en la hilatura de filamentos continuos termofusibles de PEEK (Polieteretercetona) y PEI (Polieterimida). La característica principal de estos polímeros es su alto punto de fusión, lo que aportará alto rendimiento al producto final. Se estudiaron las propiedades de cada material y se investigó sobre los métodos de procesado que permitirían mejorar la homogeneidad de los hilos híbridos.
La segunda fase se basó en la investigación de procesos para el desarrollo de hilos híbridos homogéneos compuestos por filamentos de PEEK + Fibra de Carbono y PEI + Fibra de Carbono.
En la tercera fase se destinaron los hilos híbridos a su tejeduría, donde se estudiaron diferentes metodologías para obtener los mejores resultados en las siguientes fases.
Tras un estudio exhaustivo de los procesos y resultados obtenidos se validaron, en la cuarta fase, los prototipos mediante termo-conformado, obteniendo unas placas que permitieron generar resultados tras su estudio mecánico.
Tras la investigación y desarrollo de las fases iniciales enfocadas a obtener los mejores resultados y tras el estudio de los diferentes composites obtenidos se llevó a cabo un prototipo final que permitió examinar la metodología de procesado y corroborar las altas prestaciones de los materiales compuestos desarrollados durante el proyecto.
Desarrollo
Como inicio del proyecto se procedió a actualizar el conocimiento de la técnica enfocada al mismo, además de los requisitos necesarios para su ejecución.
Tras la adquisición de los conocimientos previos, se procedió a la compra de las materias primas necesarias para el desarrollo de las pruebas previstas en el proyecto.
Con los materiales adquiridos se procedió a desarrollar hilos híbridos a través del entrelazado de fibra de carbono con fibras de PEI (Polieterimida), PEEK (Polieteretercetona) y PP (Polipropileno).
Polieteretercetona (PEEK) es un polímero cuyo punto de fusión ronda los 345 oC otorgando al composite final gran estabilidad térmica y mecánica. El grado empleado en el proyecto presenta alta fluidez, por lo que lo hace idóneo para la extrusión de filamentos. Estas propiedades abren un gran abanico de aplicaciones para los materiales compuestos desarrollados en el marco del proyecto. El PEEK es utilizado en muchos ámbitos de ingeniería, entre los que destacan el aeroespacial y la automoción.
Polieterimida (PEI) es otro polímero cuyas propiedades térmicas también superan la media, otorgando excelentes resultados en cuanto a esfuerzos térmicos y mecánicos se refiere. Su alta fluidez lo hace idóneo para la extrusión multifilamento y facilita la impregnación de la fibra de carbono.
Para ello se optimizó el proceso de obtención de fibras de bajo dpf (denier por filamento) con el fin de mejorar la homogeneidad entre fibras de refuerzo y fibras de matriz. Una vez optimizado el proceso de hilatura se procedió a la optimización del desarrollo de hilos híbridos, tratando de reducir al mínimo los esfuerzos mecánicos sometidos a las fibras.
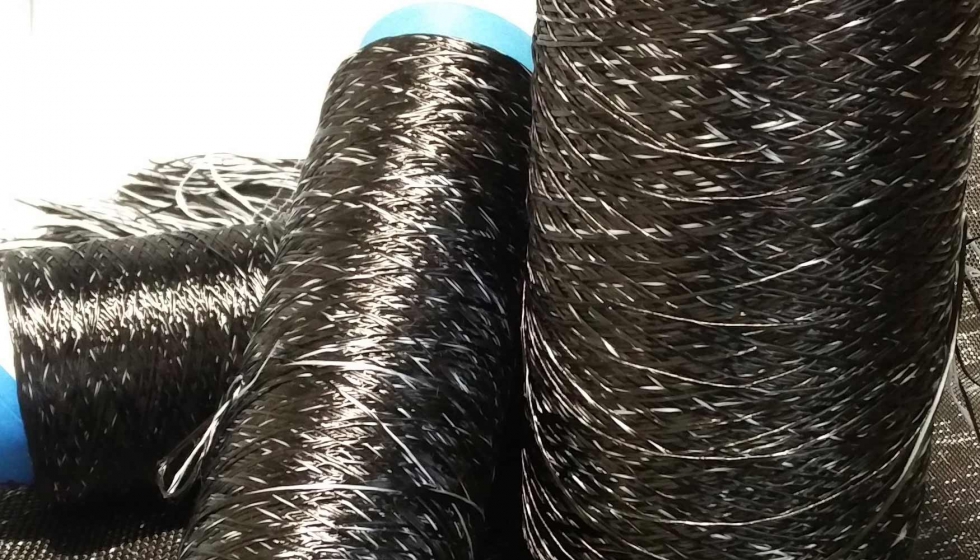
En la fabricación de los diferentes hilos híbridos se realizaron variaciones de porcentajes de materia de refuerzo y materia de matriz. Tras la optimización del proceso se procedió a la tejeduría de los mismos. Para la fabricación de los tejidos se aplicaron ligamentos abiertos favoreciendo la adaptabilidad del tejido a formas geométricas curvas.
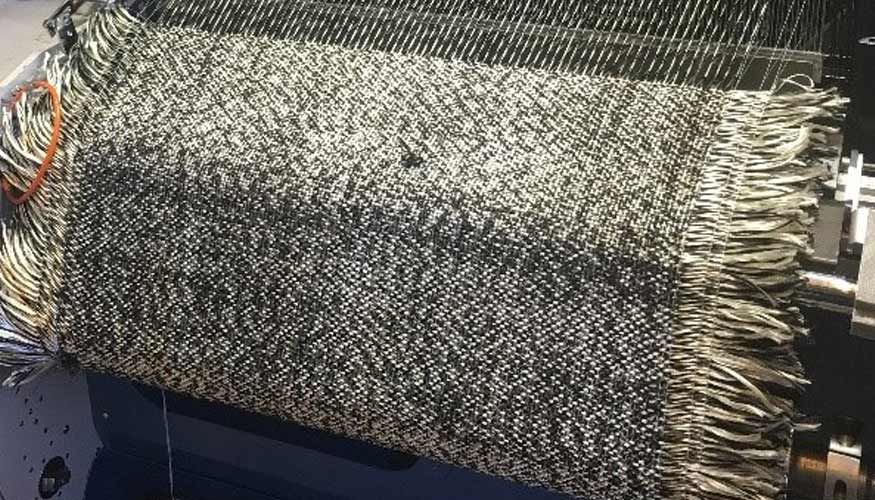
Una vez obtenidos los tejidos a partir de los hilos híbridos, se procedió al desarrollo de las pruebas de termo-conformado de los mismos, con el fin de optimizar el proceso y encontrar el equilibrio optimo entre matriz y fibra de refuerzo.
Las placas de composite preliminares obtenidas se caracterizaron por medio de ensayos mecánicos de tracción, flexión, impacto y módulo de Poisson. Estos ensayos aportan datos cuantitativos que permiten comparar las muestras entre sí, dando la posibilidad de seleccionar la composición de materias que mejores propiedades presentan.
Para concluir el proyecto se procedió al desarrollo del prototipo final, para lo que se desarrolló un molde calefactado capaz de alcanzar temperaturas superiores a 400oC. Este molde consta de un plato macho y uno hembra con forma de sillín de bicicleta. La selección de un sillín como prototipo final se debe a su gran variedad de formas geométricas, combinando en un mismo producto formas curvas y ángulos cerrados, pudiendo examinar la capacidad de adaptación de los tejidos desarrollados.
Resultados obtenidos
Los resultados obtenidos tras la ejecución del proyecto se han centrado fundamentalmente en el desarrollo de filamentos de bajo denier, tanto con polímeros de alto punto de fusión como polímeros de bajo punto de fusión, obtención de hilos híbridos con alta homogeneidad, tejidos de hilos híbridos con diferentes estructuras y materiales, nuevos materiales compuestos con matriz termoplástica. Estos pueden resumirse en los siguientes puntos.
- Análisis de las distintas tecnologías en materiales compuestos, los costes de los materiales potencialmente útiles y sus características con el fin de desarrollar unas pautas de procesado con respecto a sus temperaturas clave y características mecánicas.
- Creación de nuevos hilos híbridos de PEEK + Fibra de Carbono y de PEI + Fibra de Carbono, otorgando a los composites altas prestaciones de resistencia térmica, abriendo así un amplio abanico de potenciales aplicaciones. También se han creado hilos híbridos de PP + Fibra de Carbono.
- Tejeduría de hilos híbridos, tanto los desarrollados por AITEX como los que se han podido localizar en el mercado, consiguiendo así una comparativa y mejora de lo ya comercializado.
- Obtención de distintos prototipos de composites con matriz termoplástica, tanto en forma de placas como en modelos 3D logrando generar una caracterización de propiedades mecánicas y de procesado del material.
- Realización de acciones de difusión y transferencia de resultados.
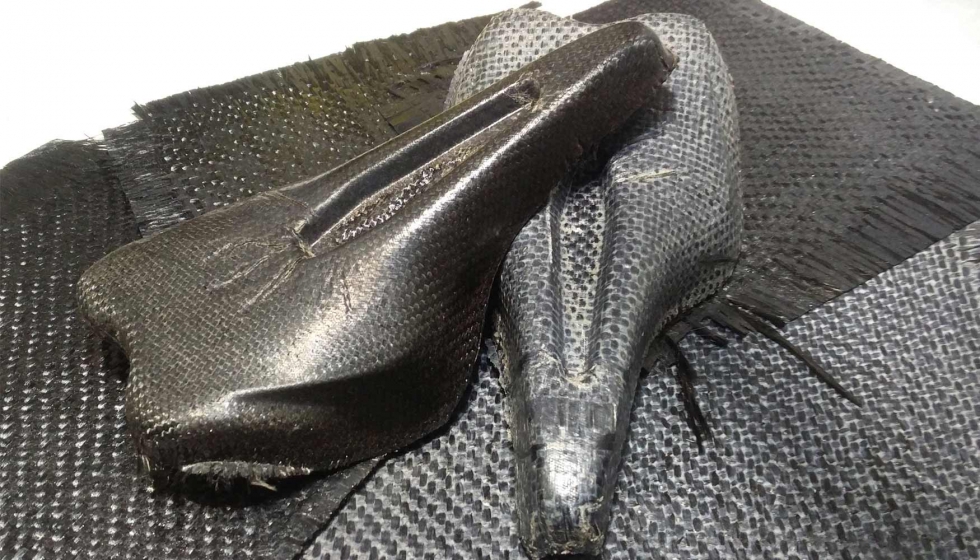