Breves anotaciones sobre desengrasado, decapado y pasivado de acero inoxidable
Sdinox es una compañía de reciente creación formada a partir de un experto equipo especializado en el tratamiento superficial del acero inoxidable (limpieza, desengrasado, decapado, pasivado y electropulido) que actúa desde 1993. Su actividad abarca todos los formatos que pueden relacionarse con esta tecnología, desde la comercialización de una gama propia de productos, hasta el tratamiento de las piezas en nuestras propias instalaciones (por inmersión o proyección) o in situ en las de nuestros clientes, pasando por el asesoramiento completo y la formación necesaria para creación de equipos profesionales especializados. Naturalmente, contamos con todos los medios de control (electrónicos y físico-químicos) necesarios para comprobar que el resultado final es el requerido. Igualmente trabajamos con procedimientos que aseguran el correcto tratamiento de los residuos y el escrupuloso respeto al medio ambiente.
A lo largo de nuestra larga trayectoria como expertos hemos encontrado que el principal problema de la corrosión del inoxidable es el desconocimiento de las personas que lo manejan. Por ello, la contribución de Sdinox a que nuestros sistemas productivos evolucionen, comienza ahora, con la formación/información que publicamos en este artículo con la pretensión que sea útil y práctica sobre qué es el acero inoxidable, qué lo hace inoxidable, por qué se oxida y cómo reducir al mínimo esta corrosión, así como los procesos existentes contra la corrosión del acero inoxidable.
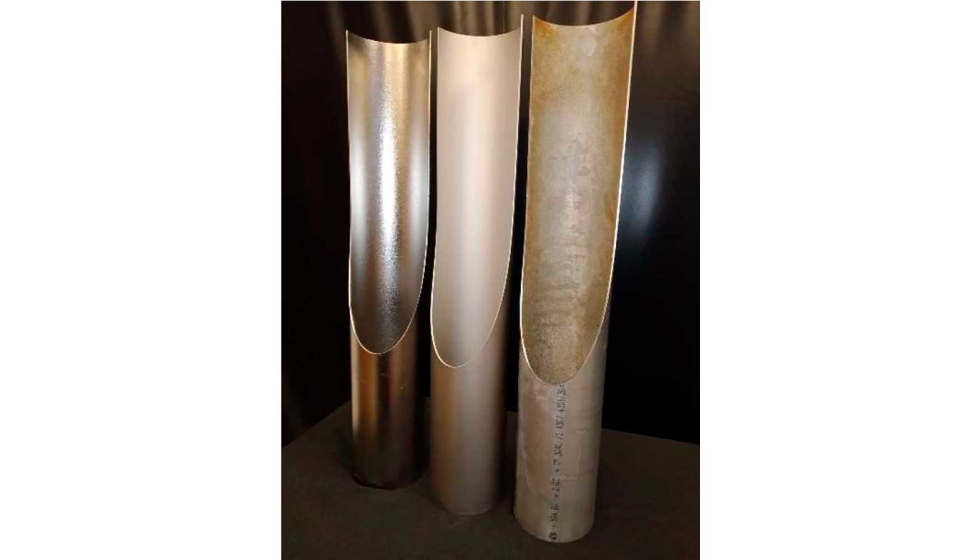
Qué es el acero inoxidable
Es una aleación férrica que contiene un mínimo del 10,5% de cromo y que, en condiciones óptimas, resiste la corrosión mejor que un acero al carbono ordinario. En todo caso, dicha corrosión, cuando se produce en el acero inoxidable, lo hace de forma localizada, mientras que, en el anterior, se puede generalizar muy fácilmente. Hay cuatro tipos de acero inoxidable, y las denominaciones respectivas definen su estructura mayoritaria:
- Ferrítico: contiene un 12-17% Cr.
- Martensítico: contiene un 11-17% Cr y un carbono superior al del ferrítico.
- Austenítico: contiene un 18-30% Cr y un mínimo del 7% Ni.
- Dúplex, Superdúplex: tienen una estructura mixta austeno-ferrítica.
Existen, como cabe suponer, una gama de distintas aleaciones en cada tipo (excepto en la última clase), que adecúan su comportamiento a diferentes sustancias corrosivas y solicitaciones mecánicas.
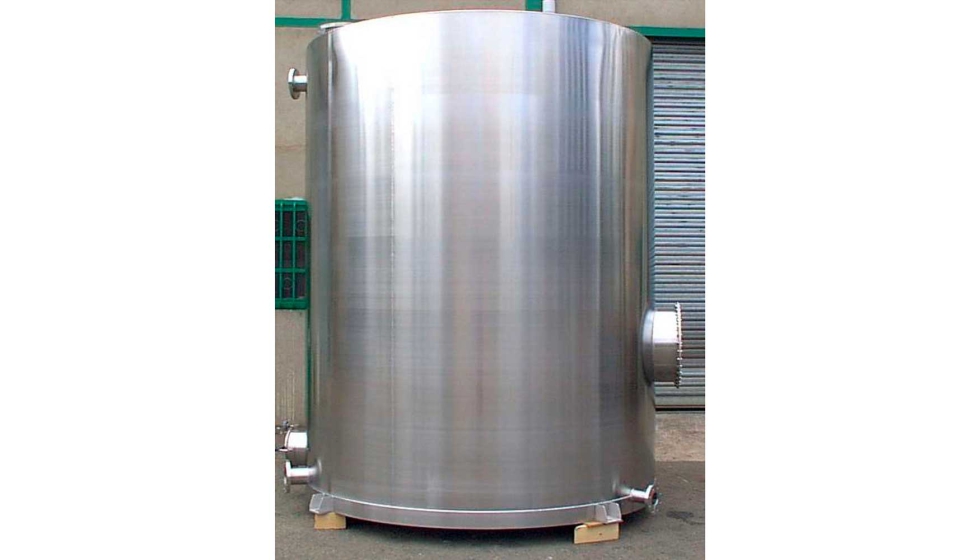
Qué hace inoxidable al acero inoxidable
No todos los aceros inoxidables resisten a cualquier agente corrosivo, naturalmente. Y tampoco todas las aleaciones de acero inoxidable se comportan igual ante una misma sustancia; por ello existen distintas aleaciones y presencia de elementos diferenciadores entre ellas. Pero, en cualquier caso, y de forma general, evitando los detalles, la respuesta al título de este capítulo es muy sencilla: una capa de óxido de cromo que se crea en la superficie del material, bien de forma espontánea entre el cromo del metal y el oxígeno del aire, bien mediante la pasivación forzada con productos químicos. Esa es la coraza que protege el acero inoxidable de los ataques a que pueda estar sometido: una capa pasiva que, además, si es dañada, vuelve a regenerarse en cuanto toma contacto con el oxígeno del aire. Es muy importante prevenir (crucial, porque aquí se encuentra un origen importante de problemas posteriores) sobre que en el momento de formación de dicha capa (durante las 48 horas del pasivado al aire, o durante los 15 minutos de pasivado químico) no haya obstáculos (y son muchos los posibles) o interrupción en el contacto del metal con el agente pasivante: suciedad, restos de adhesivo, grasa, otros metales, óxido previo…
Por qué se oxida el acero inoxidable
La explicación obvia es porque no es resistente al agente corrosivo que lo ataca. Puede ser, en efecto, que el acero, en esa aleación concreta, no tolere la sustancia con la que entra en contacto, por eso existen distintas composiciones: 304, 308, 316… Este es un problema que se resuelve con diseño y con la elección del material adecuado. Pero, ¿por qué se corroen piezas de materiales que están diseñados para resistir sustancias específicas cuando se encuentran con estas, o lo hacen antes de tiempo? Y la respuesta es: porque la capa pasiva que protege el inoxidable está dañada o es discontinua en el momento del contacto con el producto agresor. Estos son algunos ejemplos de las incidencias que pueden dañar la citada capa de óxido de cromo: la destruyen, siquiera parcialmente, e impiden su regeneración:
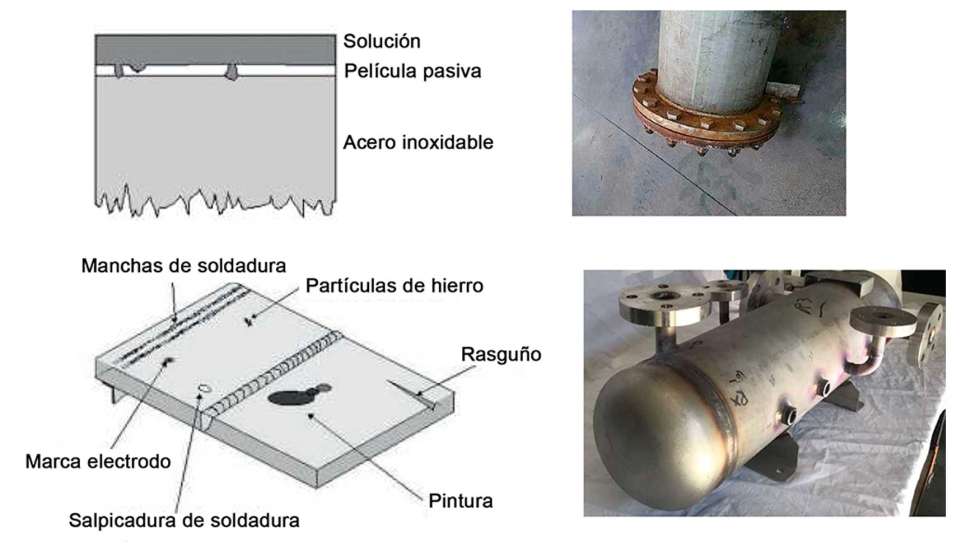
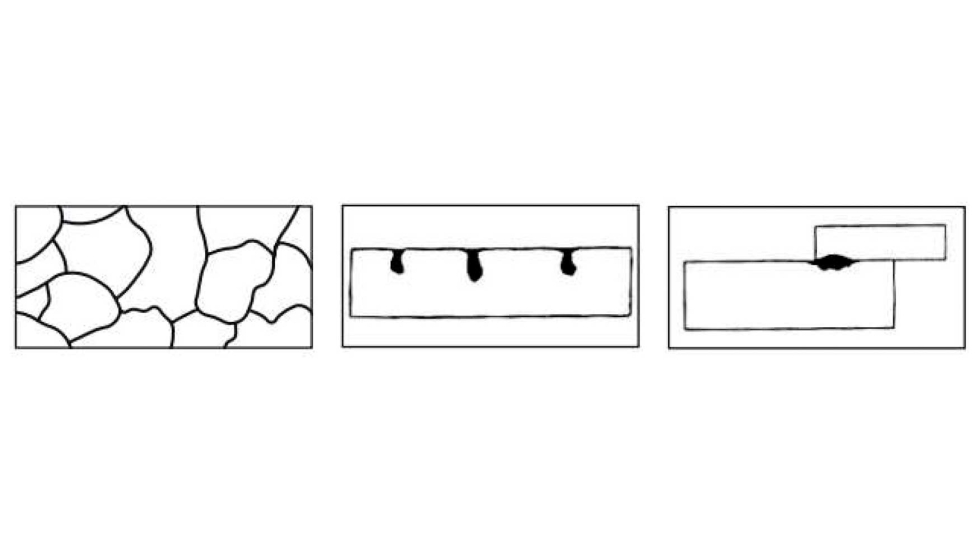
Corrosión intergranular. Corrosión por picadura. Corrosión en resquicios.
Cómo reducir al mínimo la corrosión en el acero inoxidable
Las piezas suelen ser suministradas por el fabricante en unas buenas condiciones de limpieza y pasivado, sin embargo, la manipulación posterior, desde el transporte hasta su procesamiento (corte, doblado, taladrado, marcado, soldeo…) deterioran su estado inicial. Todo el equipo construido (puede ser una chapa o todo un conjunto) deberá ser meticulosamente limpiado a fondo para eliminar toda contaminación producida por óxidos, polvo de hierro, partículas procedentes de herramientas, fundente de soldadura, suciedades y sustancias orgánicas. Esto se puede realizar fácilmente mediante un decapado. La limpieza química suele ofrecer mejores resultados contra la corrosión debido a que los métodos mecánicos (esmerilado, pulido y chorreado) tienden a producir una superficie más rugosa, con microporos que pueden facilitar la contaminación. Por ello, incluso después de una limpieza mecánica, es muy conveniente un pasivado, o un decapado+pasivado, para obtener la máxima resistencia a la corrosión.
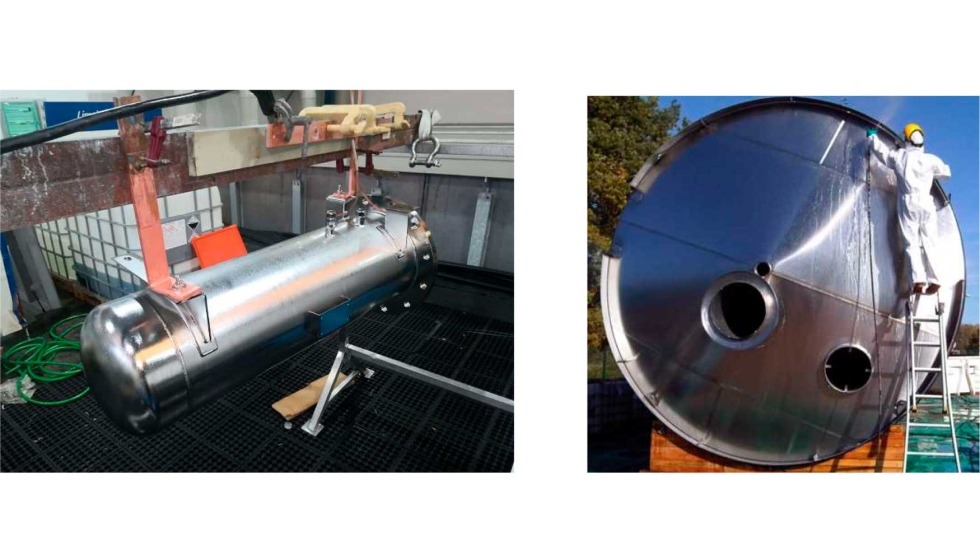