Recubrimientos mediante proyección térmica: comparativa frente a otras tecnologías
Las tecnologías de modificación superficial son una alternativa perfecta para mejorar y reparar las propiedades superficiales de las piezas sin alterar sus funciones estructurales. En general, esta metodología puede resultar una solución económica y rápida, si bien es cierto, que en algunos casos la reparación puede ser inviable.
Aunque existen muchos tipos de tecnologías de modificación superficial, las más usuales son, por un lado, las másicas, con tratamientos térmicos convencionales, TT criogénicos, conformación en frío y conformación en caliente; y por el otro, las superficiales con tratamientos térmicos convencionales (nitruración y cementación), temples por inducción y láser, pinturas y recubrimientos orgánicos, soldadura, PVD y CVD, implantación iónica, procesos electrolíticos, procesos químicos o la proyección térmica.
Tecnologías en competencia con la proyección térmica
Si entramos a comparar las diferentes tecnologías disponibles actualmente en el mercado en competencia con la proyección térmica, veremos que existe un amplio abanico de posibilidades que serán más o menos útiles según cada caso.
En la que se aplica por temple, por ejemplo, aunque es económica y útil para grandes producciones, también puede causar deformaciones y la mejora de las propiedades está limitada a las puramente mecánicas (límite elástico, resiliencia, etc). Además, hay que tener en cuenta que si se aplica esta técnica los materiales susceptibles a templar son:
- Los aceros al carbono con contenidos medios-altos de carbono
- Los aceros inoxidables martensíticos
- Algunas fundiciones blancas
- Algunas aleaciones de aluminio y titanio
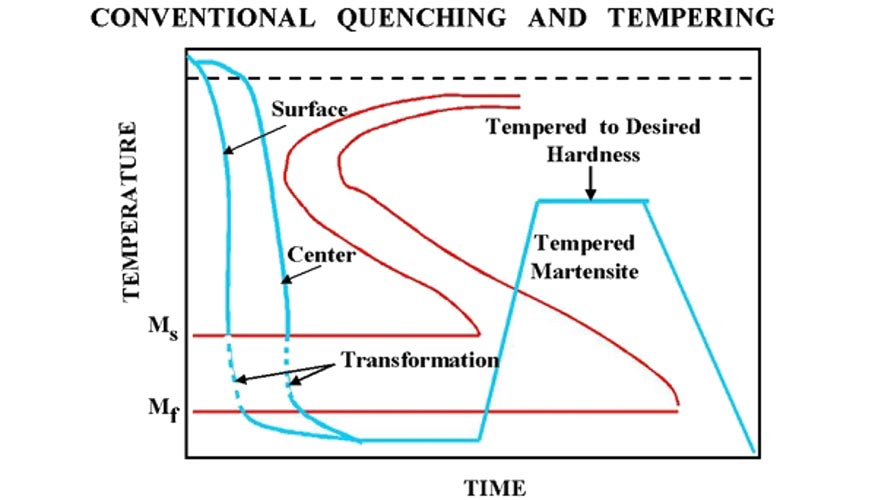
Si por el contrario analizamos la tecnología por nitruración-cementación veremos que también es una técnica económica, sobretodo, para medianas y grandes producciones; que modifica las propiedades de dureza y/o lubricación pero que puede, a su vez, causar posibles deformaciones en función de la composición y geometría del material. En este caso, los materiales susceptibles a nitrurar-cementar son:
- Aceros al carbono con contenidos medios-altos de carbono, níquel, cromo y aleaciones de Titanio
- Aceros inoxidables
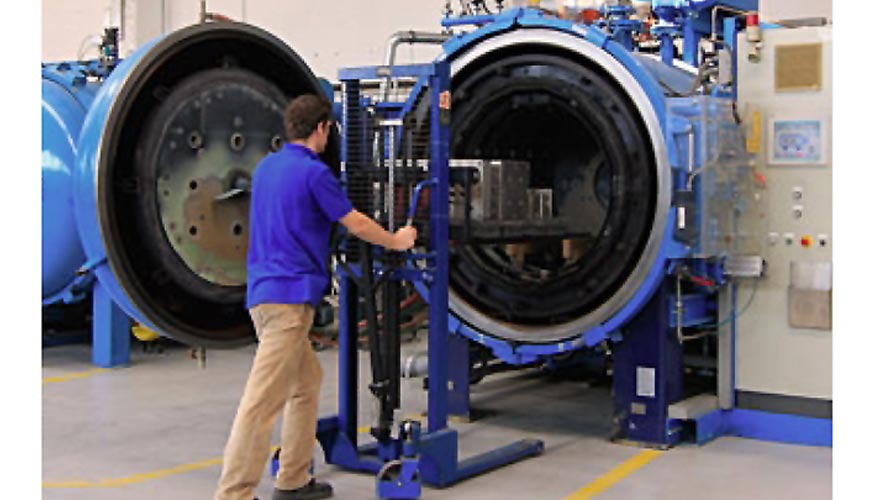
En la tecnología de modificación superficial por soldadura se pueden aplicar distintas técnicas: TIC, MIG, Arco Sumergido, PTA, etc. En este caso el precio dependerá de la técnica que se emplee y es ideal para pequeñas y medias producciones o para grandes si está automatizado. Cuenta con un amplio abanico de propiedades en función del aporte aunque puede producir deformaciones severas del material (debidas al aporte térmico) además de grietas o poros. Los materiales susceptibles a recargar por soldadura son:
- Aceros
- Aceros inoxidables
- Algunas fundiciones
- Aleaciones de aluminio, titanio, cobre, etc.
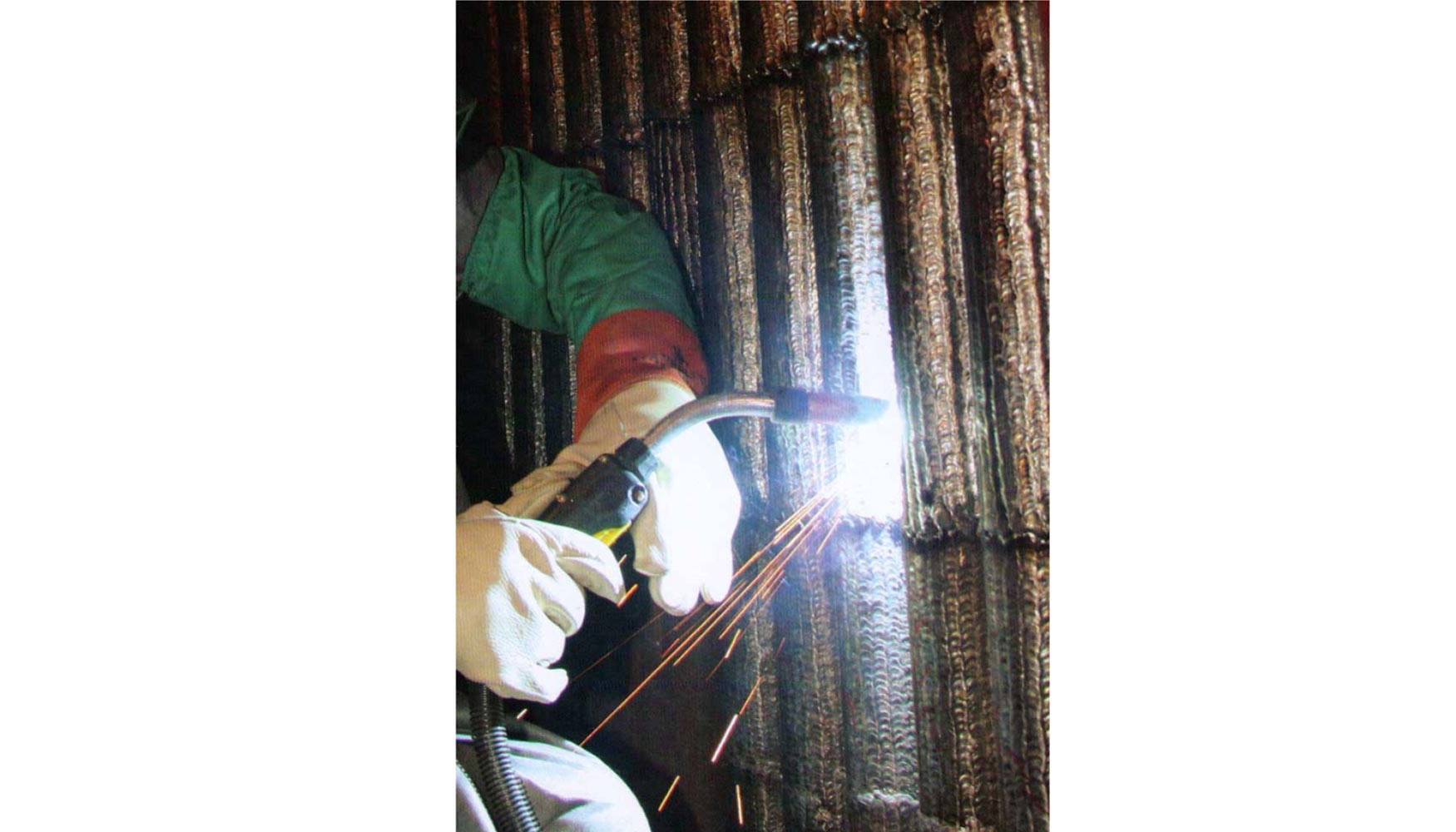
En cuanto al cromo duro (hard chromium), es económico, pero el coste también dependerá mucho del proceso que se lleve a cabo. No comporta deformaciones porque se trata de un proceso por inmersión a baja temperatura y que por lo general es homogéneo. A espesores elevados puede ocasionar porosidad y grietas, y se produce una sobreacumulación de material debido a la mayor densidad de corriente que se da en las aristas. Este proceso, además, es lento y genera compuestos cancerígenos contaminantes. En esta técnica los materiales susceptibles a cromar son:
- Aceros
- Aceros inoxidables
- Algunas fundiciones
- Aleaciones de aluminio (difícil), cobre, etc.
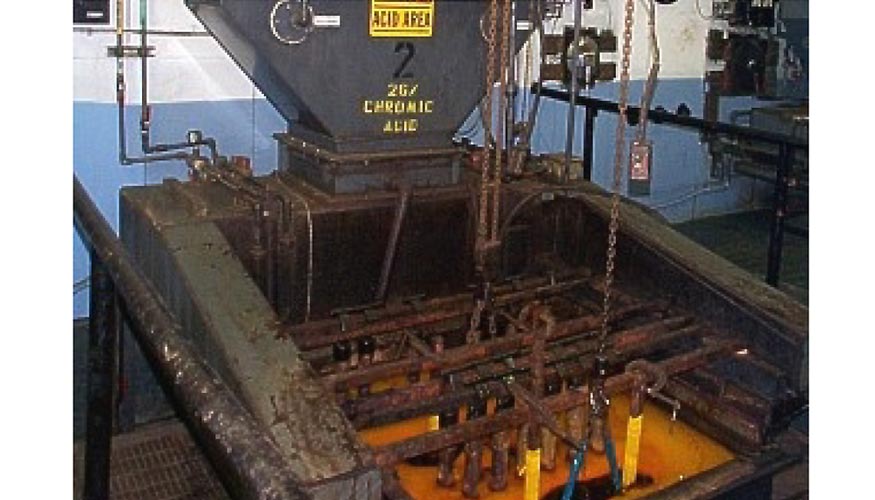
En el caso del PVD-CVD, el coste es bastante bajo para grandes series, aunque aumenta para medias producciones, y confiere grandes propiedades contra el desgaste, debido a la elevada dureza superficial. Existe el riesgo de deformaciones (entre 400-900 °C) y se trata de un proceso lento que depende de un proveedor especializado además de tener una clara la limitación del tamaño ya que se hace en cámara de vacío. Los materiales susceptibles a recubrir son:
- Aceros
- Aceros inoxidables
- Aleaciones de aluminio
- Aleaciones de titanio, cobre, etc.
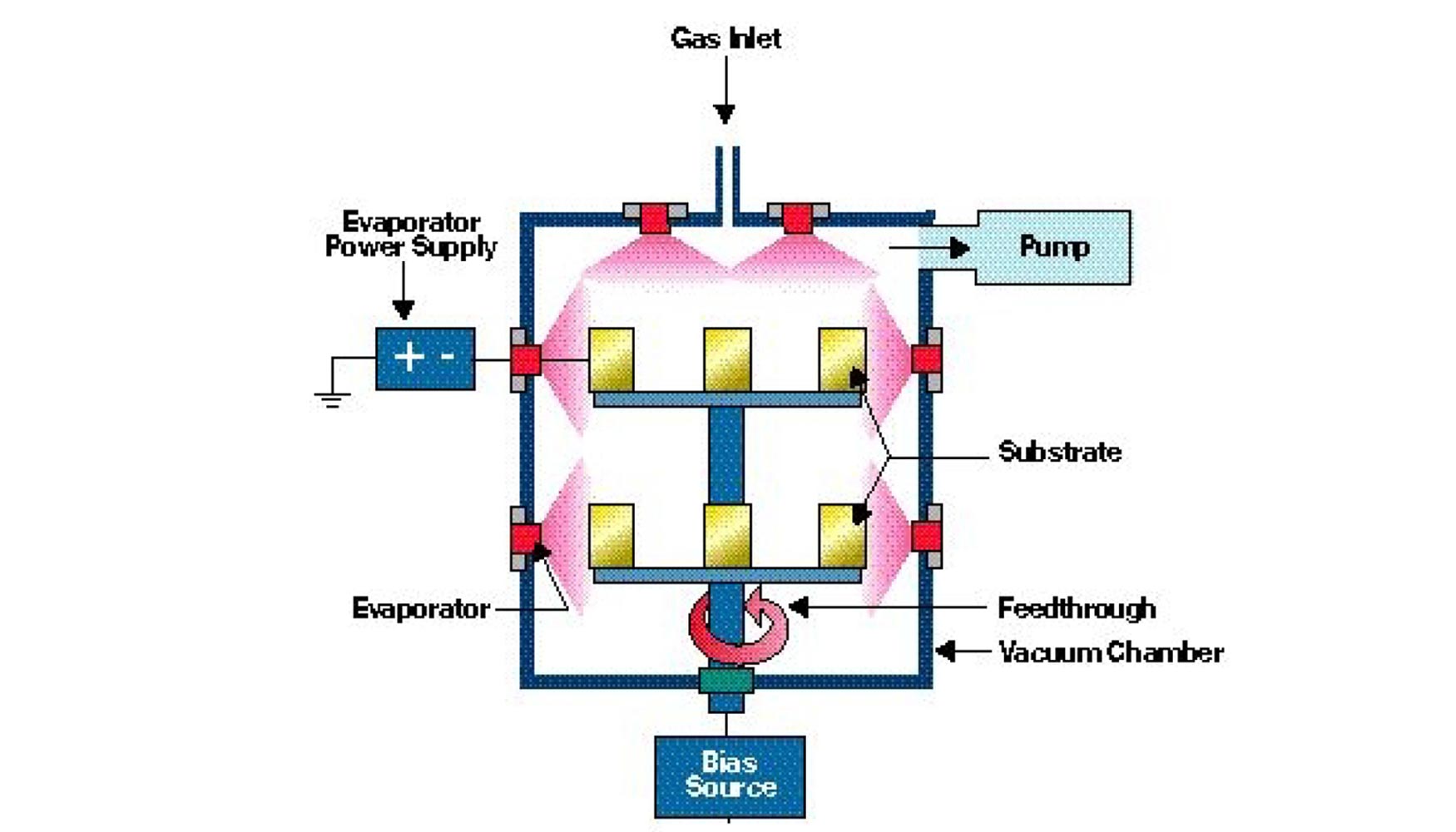
La tecnología Laser Cladding está pensada para pequeñas y medias producciones además de ser automatizable, y aunque es un proceso rápido, necesita de un proveedor especializado. En este caso, existe la posibilidad mínima de deformación pero en menor medida que con la soldadura por arco. El recubrimiento está bien adherido y puede alcanzar espesores considerables. Además existen una gran variedad de materiales de aporte y cuenta con una alta tasa de deposición y las diluciones son casi inexistentes. Mediante esta técnica, los materiales susceptibles a recubrir son:
- Aceros
- Aceros inoxidables
- Aleaciones de aluminio, titanio, cobre, etc.
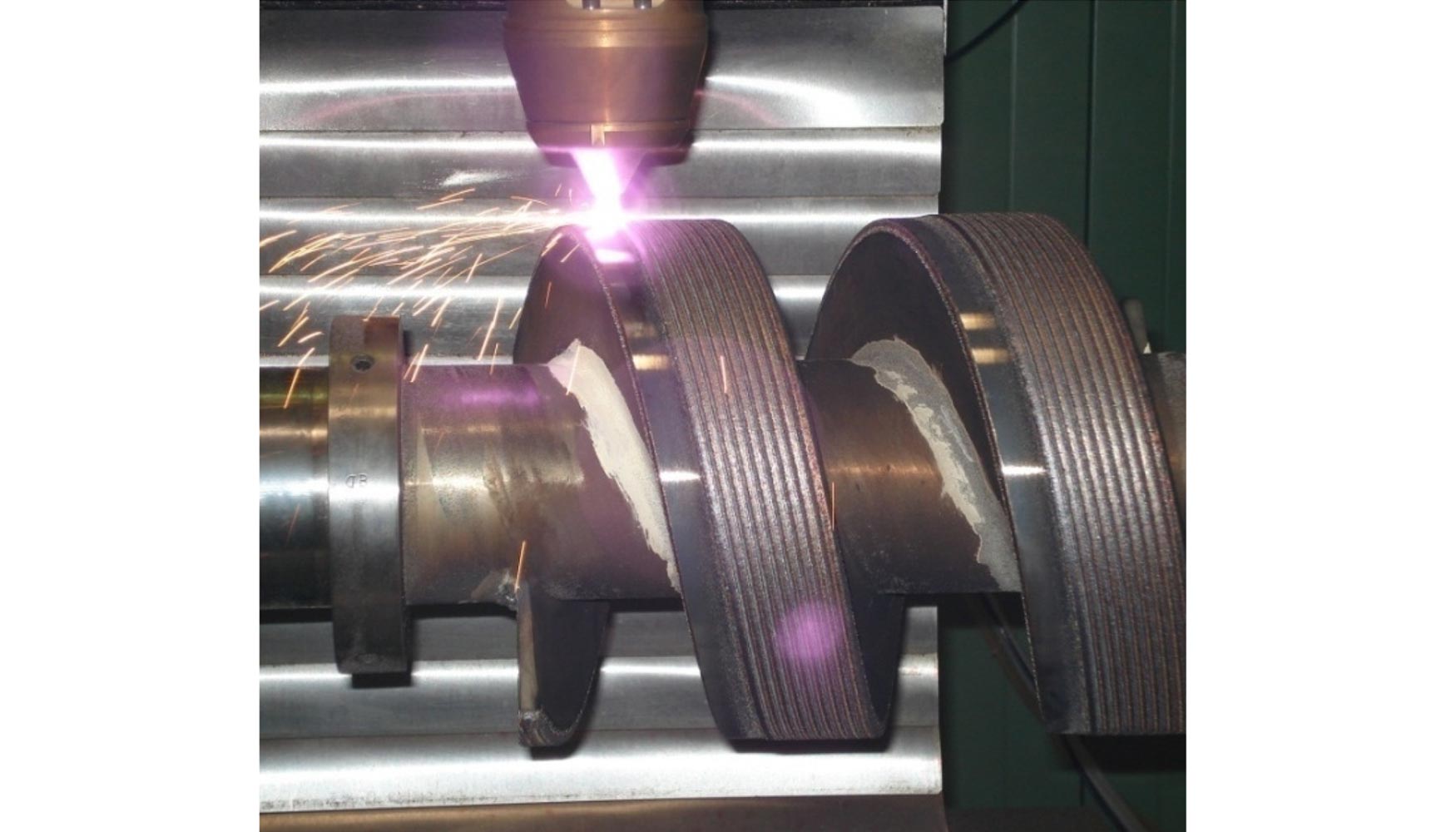
Finalmente, la tecnología por Spray Fuse tiene como principales ventajas el precio y que es un proceso rápido y sencillo, pero se tiende a usar en pequeñas producciones y provoca deformaciones importantes ya que se alcanza la temperatura de fusión del material de aportación (más de 700 °C). Permite espesores considerables y hay disponible un amplio abanico de materiales de aporte, aunque pueden aparecer defectos por alta aportación de calor. En este caso, los materiales susceptibles a recubrir son:
- Aceros
- Aceros inoxidables
- Algunas fundiciones
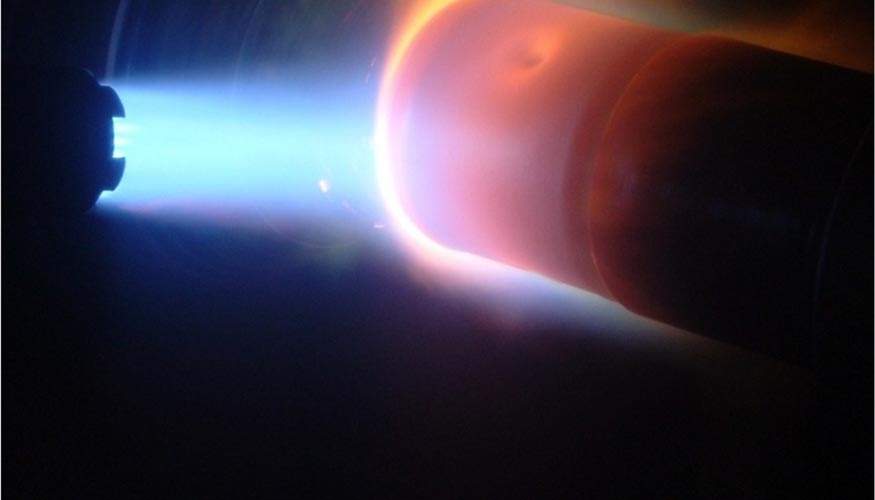
En la gráfica siguiente, se muestran los rangos de espesor y durezas más usuales de cada técnica en comparación con los de la proyección térmica:
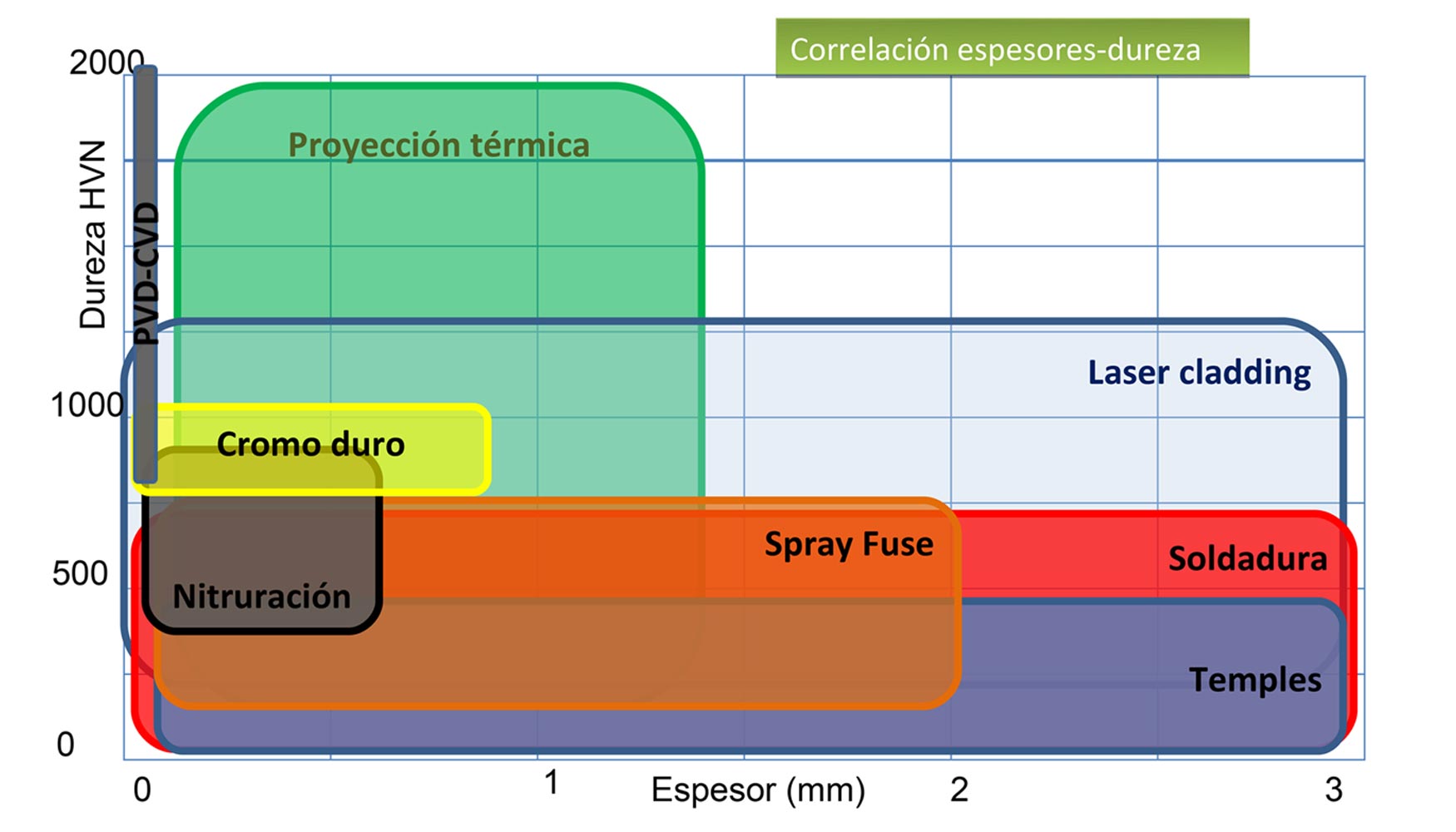
¿Qué entendemos por proyección térmica?
La proyección térmica es una tecnología de superficie que permite obtener recubrimientos delgados (0,03-1mm) a partir de un material de aporte en forma de polvo o hilo gracias a la acción combinada de tratamiento térmico + aceleración que le confieren gases a presión, creando un haz de partículas que incide sobre la superficie a recubrir.
Proceso de generación del recubrimiento:
1) Generación de energía cinética/térmica.
2) Interacción de la energía con el material.
3) Interacción de las partículas del spray con el substrato.
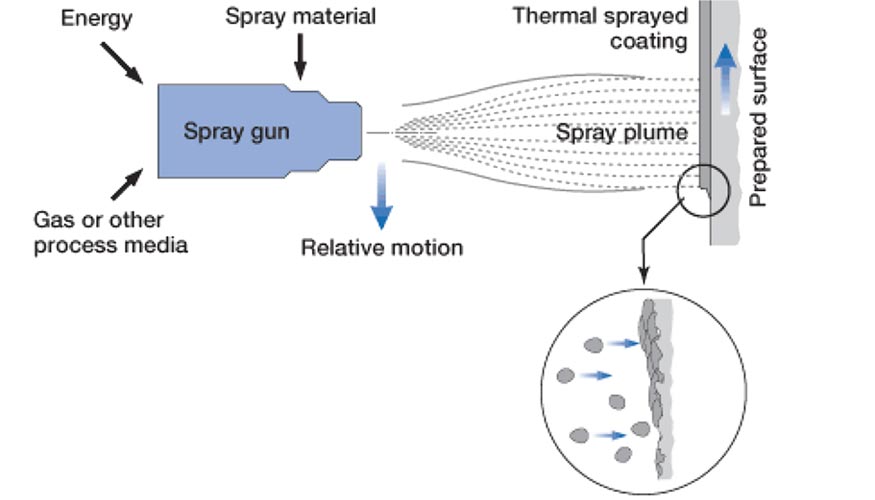
¿Técnicas de proyección térmica?
Dentro de la proyección térmica hay distintas técnicas en las cuales se utilizan fuentes de energía térmica y cinética que dan origen a diferentes recubrimientos:
Proyección térmica por llama con hilo (WFS):
- Bajo coste, alta eficiencia
- Portátil (recubrimientos in-situ)
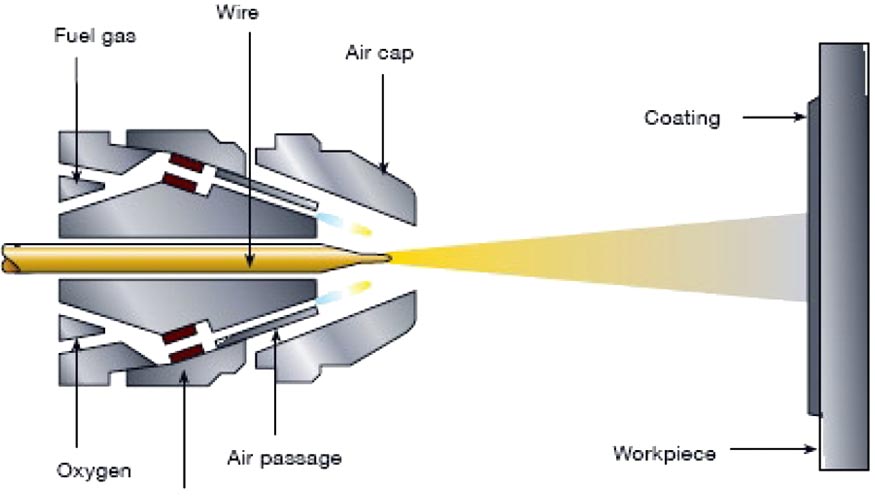
Proyección térmica al arco (AS):
- Bajo coste, alta eficiencia
- Facilidad de uso (recubrimientos in-situ)
- Portátil
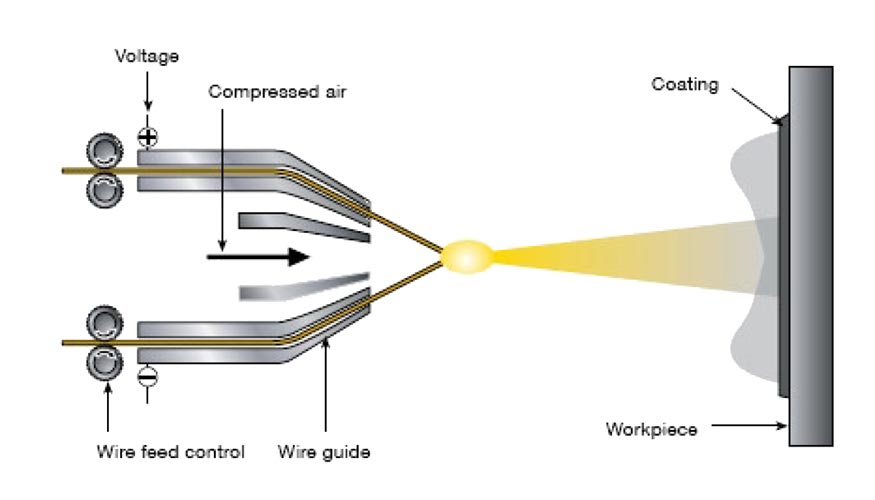
Proyección térmica de alta velocidad (HVOF):
- Mejor adherencia y propiedades mecánicas
- Recubrimientos de carburos con la máxima dureza y resistencia al desgaste

Proyección térmica por plasma (APS):
- Versátil (se pueden aportar la mayoría de los materiales)
- Buena Calidad
- La única técnica que permite aportar cerámicas
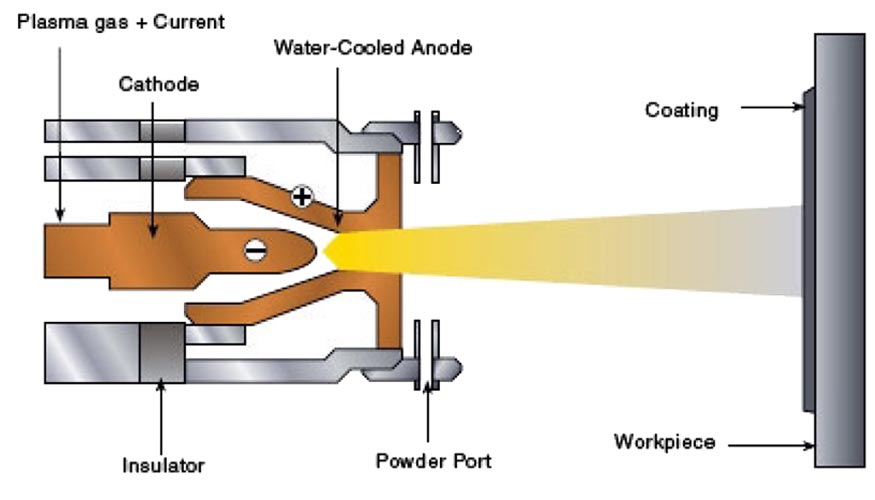
Cold spray:
- Alto coste, alta eficiencia
- Recubrimientos libres de oxidación
- Básicamente limitado al aporte de aleaciones metálicas
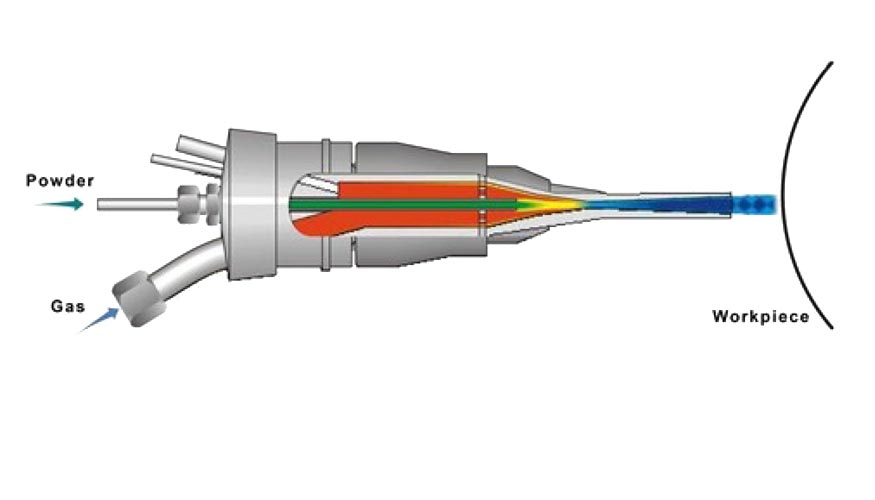
¿Cómo se forma el recubrimiento?
El proceso de fusión del material del aporte será distinto según la técnica que se aplique. En el caso de proyección mediante polvo, el material se fundirá totalmente, parcialmente o no se fundirá en función de su naturaleza:
- Materiales cerámicos: suelen fundir en su totalidad.
- Metales: suelen fundir en su totalidad pero depende la técnica utilizada. Hay técnicas que sólo los reblandecen.
- Cermets: suelen reblandecer o fundir la matriz metálica.
Por el contrario, en el caso de proyección mediante hilo, el material se fundirá totalmente.
En cuanto a la aceleración de las partículas fundidas o reblandecidas, esa aceleración la producen corrientes de gases a presión que se encuentran presentes en el momento de la transferencia de calor. La presión se puede obtener con los periféricos (presión de servicio) o bien mediante toberas (nozzles) de geometrías que favorezcan expansiones bruscas de estos gases en la pistola. Además, la naturaleza de los gases de cada proceso, influye en el poder de arrastre del gas como medio propulsor y la entrada de aire turbulento de la atmósfera, produce una caída de la velocidad, más o menos intensa en función del tamaño de la partícula.
Por todas estas razones, es importante desarrollar unos parámetros de proyección que produzcan una velocidad y temperatura adecuada en el momento del impacto con el substrato.
Si nos centramos en el impacto, hay que destacar que en función del estado de la partícula, si es líquida, sólida o reblandecida, tendremos una morfología u otra de la partícula depositada (splat).
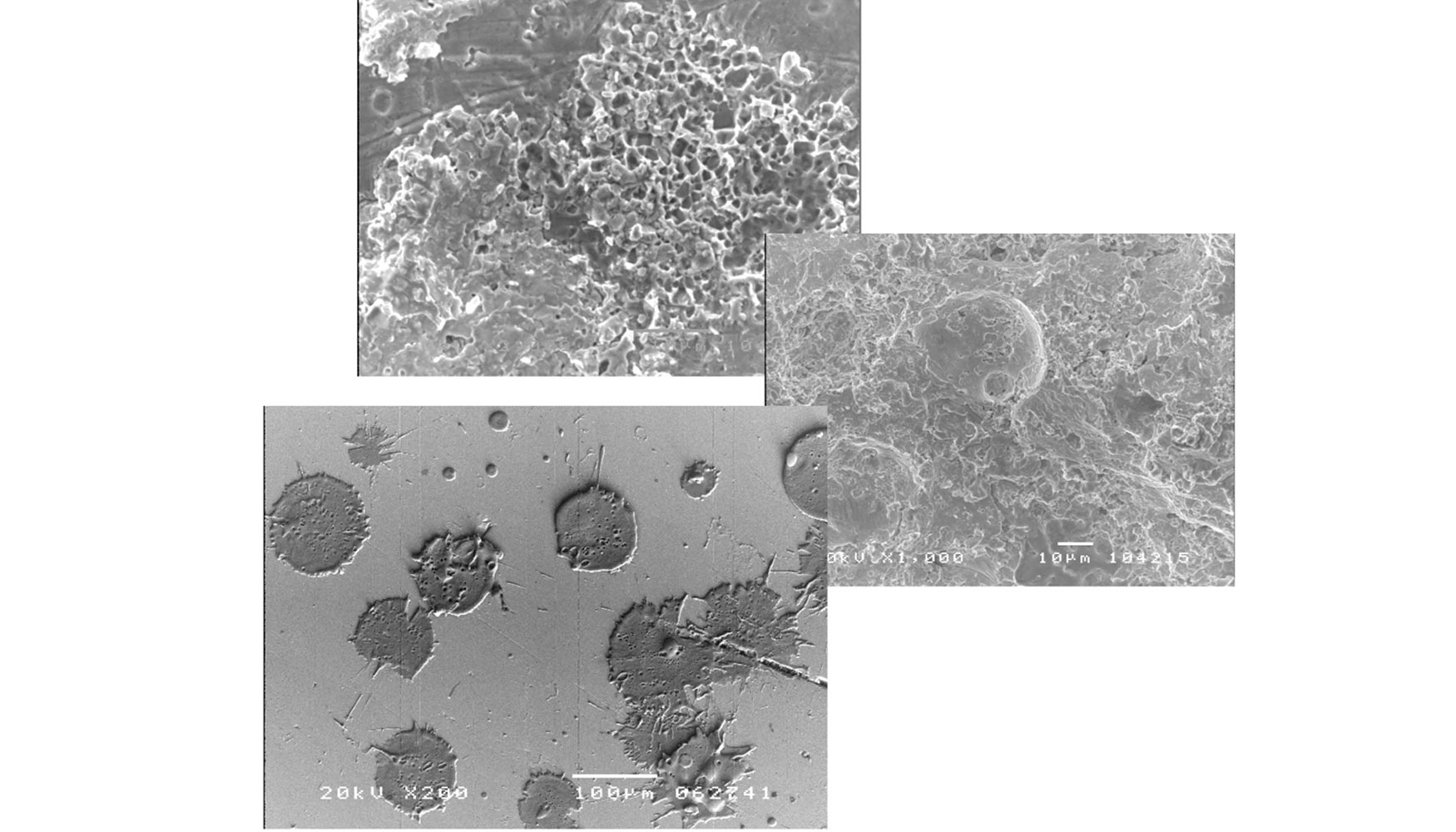
El mecanismo de adherencia al substrato empleado es por anclaje mecánico. Gracias al proceso de solidificación, se produce una contracción de las partículas que junto a la rugosidad del substrato produce un anclaje mecánico suficiente. Los rangos de adherencia son 30-80 MPA en función de la tecnología, el material y los parámetros de proyección. A velocidad de impacto, se favorece la unión perfecta entre la partícula y el substrato y la adherencia aumenta.
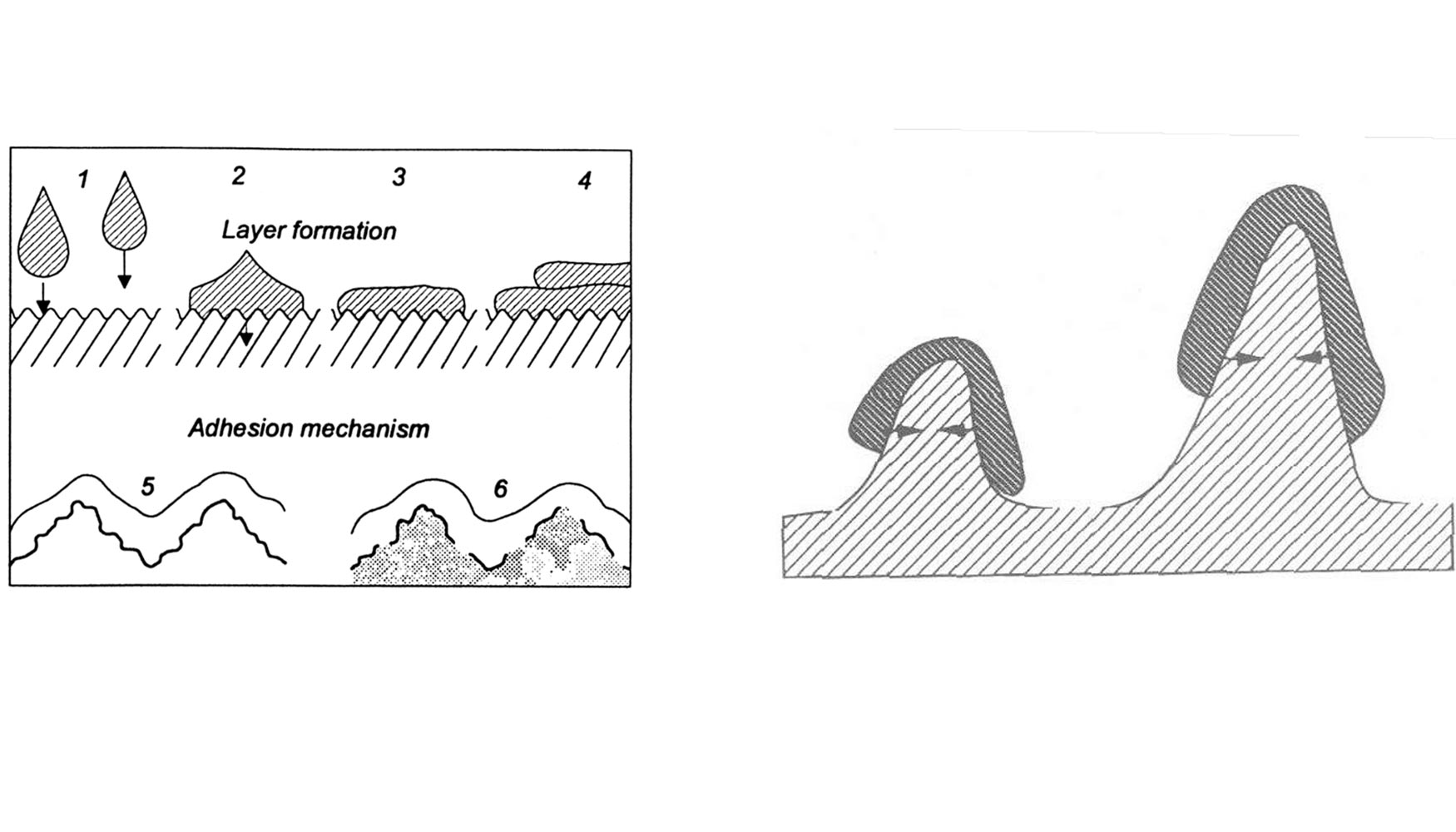
Los recubrimientos de proyección térmica se suelen mecanizar o rectificar tras su aportación. Para ello, lo más normal es usar herramientas con gran poder de corte o muelas de abrasivo especiales. Si la aplicación lo requiere (superficies rugosas para favorecer la tracción y el agarre) o el acabado superficial no es importante (aplicaciones de abrasión por sólidos), se puede dejar sin mecanizar, siendo el abanico de rugosidades disponibles en función de la técnica y del material de aportación de 3 a 7 micras de Ra.
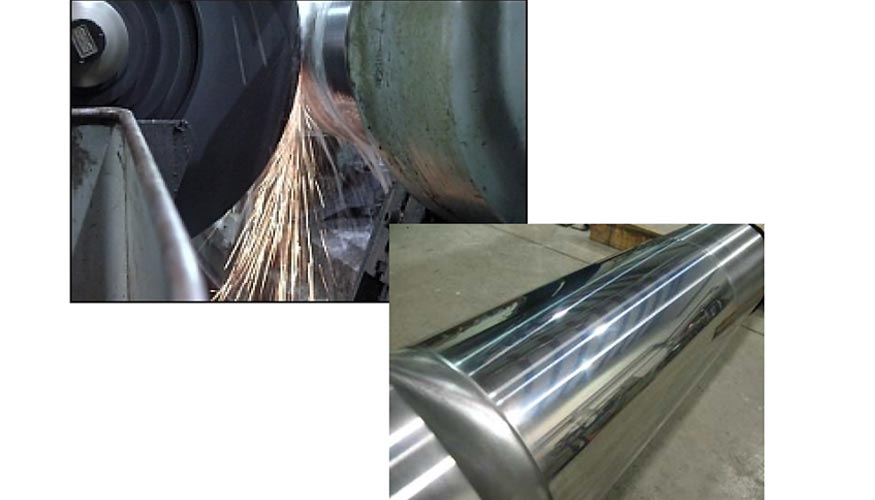
Criterios de elección de la técnica más adecuada
Pero teniendo en cuenta la gran variedad de técnicas existentes, ¿cómo decidirnos por una o por otra? Pues simplemente, valorando sus pros y sus contras de manera que veamos qué se ajusta más a nuestras necesidades según cada caso.
Los criterios principales de elección serán:
- La especificación de cada cliente: será él quien marcará qué necesita a nivel de dureza, de espesor, de resistencia al desgaste, de resistencia química y de otros factores del tipo rugosidad, color, dielectricidad, etc.
- La ubicación: hay técnicas que nos permitirán hacer aportaciones in-situ y otras que no. Si la pieza no es desmontable, las opciones de material de aportación se reducen a las posibles en equipos portátiles.
- Las dimensiones: hay tratamientos en horno, en cabina, portátiles, etc.
- El precio: valorar si merece la pena compensar el aumento de propiedades con el precio final.
Por todo ello, y como especialistas y referentes en el sector de la proyección térmica en España, podemos decir que la tecnología por proyección térmica ofrece un abanico de soluciones fantásticas para la gran mayoría de problemas superficiales gracias a su gran versatilidad y que al realizarse sin aportación térmica a la pieza no genera deformaciones.