Italtech deja claras sus intenciones
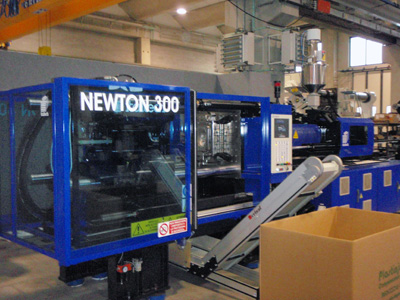
Más de 900 visitantes de más de 400 diferentes firmas, principalmente de Italia, España, Francia, Grecia, Gran Bretaña y Alemania, así como de EE UU, Argentina, Brasil y Sudáfrica, entre otros pudieron contemplar durante tres días las modernas instalaciones de la italiana Italtech y su capacidad de producción en esta nueva planta.
Inaugurada hace apenas dos años, la planta es la primera señal del renacimiento de la marca tras su compra por parte de la familia Pegoraro al grupo Fiat y, con sus 8.000 m2 de modernas instalaciones, da fe de la apuesta de futuro de este fabricante europeo. La nueva Italtech asume el desafío del crecimiento, invirtiendo además en el desarrollo de nuevos modelos y técnicas para adaptarse a las necesidades reales del transformador. La consecuencia de todo ello es su actual proceso de expansión y el aumento en la fabricación de máquinas.
Las jornadas de puertas abiertas sirvieron para realizar una nueva puesta en escena de la serie Newton, inyectoras ultrarrápidas de medio tonelaje (hasta 1.000 toneladas de cierre), presentadas el pasado mes de marzo en la feria Plast de Milán. Estas máquinas ya se fabrican en una versión mejorada respecto a la primera. Se ha conseguido aumentar la rapidez con el empleo de nuevos materiales y sistemas de descarga hidráulica en el sistema de cierre tipo '2 platos', a la vez que se garantizan unas altas prestaciones con un consumo energético muy bajo, “el menor del mercado en máquinas para similares aplicaciones” según el fabricante. Asimismo, el nuevo control por microprocesador Italtech alfa 7, común a toda la gama de máquinas y basado en el sistema operativo Windows, permite disponer de una interfaz gráfica de comunicación y programación sencilla y a la vez tan versátil como el utilizador final o la producción a realizar, precisen. Es totalmente modificable, incorpora de serie la tele asistencia; para resolución de problemas, actualización de software, control de la producción, calidad e incluso aviso de averías, anomalías o desviaciones vía sms a móviles, e-mail o envío de mensajes mediante voz generada por el ordenador.
Debido, parcialmente, a esta alta tecnología aplicada a las inyectoras, se presentó también el sistema Saptech de gestión informática de una planta completa de inyección. Es un sistema adaptable a las nuevas inyectoras Italtech de forma inmediata y a cualquier otro tipo y marca de inyectora, incluso de gran antigüedad, con una sencilla aplicación de hardware y software. Un protocolo de comunicación permite, desde un ordenador central, realizar un control exhaustivo de toda la producción, estado y funcionamiento de las máquinas, mantenimiento; lotes de producto acabado, almacenaje, etc. Genera estadísticas como el histórico de paradas de máquina, sea por avería, fallo o intervención humana, con registros permanentes de todos los parámetros, fecha y hora, motivo y detalles, así como registro del operario que motiva el paro, supervisa o modifica parámetros en la máquina, producción o mantenimiento.
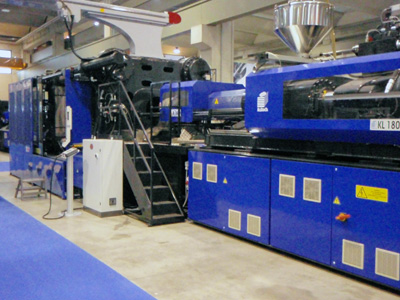
Italtech cuenta con 3 líneas totalmente renovadas de inyectoras: Impetus, Newton y KL, todas ellas fabricadas en Europa en su totalidad y fruto de las inversiones en investigación y desarrollo aplicado. El fabricante italiano ofrece soluciones técnicas vanguardistas y una infraestructura de servicio técnico acorde con las expectativas y planes de crecimiento de un fabricante de inyectoras europeo que han hecho de la crisis un revulsivo.
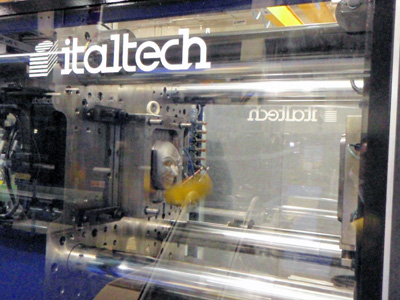
Digna de mención es también la renovada serie KL de inyectoras de gran tonelaje (hasta 6.000 toneladas de cierre) con la muestra de varias unidades de 1.000, 1.300 y 1.800 toneladas (modelos producidos en serie), dotadas de la avanzada tecnología híbrida de Italtech. Combinan variadores de frecuencia sobre los motores de las bombas y sobre el motor eléctrico empleado para la inyección, lo que resulta en unos consumos energéticos muy bajos. Por ejemplo, una máquina KL 1.800 produciendo un componente técnico del automóvil de crítica exigencia en cuanto a calidad, en PP, con un peso de 5.270 g y un tiempo de ciclo de 76", consumía tan sólo 102,6 kW/h para 249,63 kg/h plastificados. O lo que es lo mismo, 0,411 W por cada gramo de material.
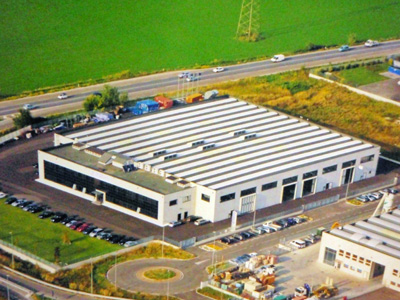