Robot flexible para la automatización de taladrado y remachado de grandes componentes aeronáuticos
El presente trabajo presenta la conceptualización, desarrollo y validación, mediante prototipo industrial, de una solución innovadora de automatización flexible. Esta consiste en un sistema macro-micro: un robot industrial porta como ‘end-effector’ una maquina CNC de 4 ejes, que ejecuta operaciones de taladrado, avellanado, aplicación de sellante e instalación de remaches ciegos.
El robot industrial como portador del ‘end-effector’ permite posicionar el mismo sobre el fuselaje en distintas áreas de trabajo, con una precisión de posicionamiento limitada a las prestaciones del robot. El sistema de visión integrado en el ‘end-effector’ para detección de pretaladrados de referencia, permite alcanzar la precisión de posicionamiento relativo a la pieza requerido por el proceso. A su vez, gracias a la precisión de los ejes del end-effector, es posible hacer una única referenciación para toda la ventana de trabajo, obteniendo un ahorro de tiempos muy significativo. Las ventosas contribuyen, igualmente, a alcanzar la calidad requerida en el taladrado aeronáutico, ya que permiten absorber el esfuerzo del proceso y amortiguar las vibraciones generadas, que de otra forma serían transmitidas íntegramente al robot.
El innovador sistema de automatización, validado en un prototipo preindustrial, mejora de forma importante la producción de esta operación de ensamblaje, recortando tiempos y disminuyendo de forma significativa el coste del proceso.
1. El ensamblaje de grandes componentes aeronáuticos: una actividad todavía muy manual
Las operaciones de ensamblaje de grandes componentes aeronáuticos son hoy en día todavía muy manuales. La necesidad que tienen los constructores de reducir costes e incrementar la productividad les obliga a buscar formas de automatizar dichos procesos productivos.
La automatización de la unión de grandes componentes aeronáuticos, y en particular el del ensamblaje de secciones de fuselaje de un avión, es una tarea extremadamente compleja en las que hay que conjugar las grandes dimensiones de los componentes con estrechas tolerancias de fabricación. La problemática se ve agravada con la tendencia a incorporar materiales ligeros, como los materiales compuestos, en la construcción de dichos componentes ya que las tolerancias de fabricación de los mismos, al menos actualmente, no son tan precisas como lo pueden ser para otros materiales como el aluminio o el titanio. Para lograr automatizar las operaciones de ensamblaje de estos componentes, los principales constructores están trabajando intensamente tanto en el propio diseño de estas uniones, a fin de que sean más fácilmente automatizables, así como en los medios necesarios para llevar a cabo la automatización de la unión. En este contexto, Tecnalia lleva varios años trabajando junto a los principales constructores aeronáuticos en el desarrollo de soluciones innovadoras que permitan automatizar la unión de componentes aeronáuticos. En el presente documento se describe el trabajo realizado en la automatización del ensamblaje de secciones de fuselaje, en particular, la sección 13 del A3X0 (próxima generación de aeronaves con estructura mayoritaria de fibra de carbono, fuente de estudio del proyecto europeo aeronáutico FP7 Maaximus). Se trata de una sección de fuselaje de unos 4 m de diámetro, cuyas pieles están fabricadas en fibra de carbono de 6 mm de espesor, reforzadas con largueros de aluminio. El espesor de las pieles en la zona de la unión es de 3 mm, debido a que en esta zona las pieles se superponen con una banda exterior denominada ‘buttstrap’, que también tiene 3 mm de espesor (a fin de mantener el espesor total de 6mm del fuselaje) y está rigidizada en su parte posterior mediante la correspondiente costilla y ‘stringers’ de aluminio. El buttstrap tiene la particularidad de estar 100% pre-taladrada (a un diámetro de 3,3 mm), al contrario de los barriles, que no llevan ningún pre-taladro. Los pretaladros del ‘buttstrap’ están distribuidos en filas de 4 taladros (quedando dos taladros sobre cada barril) y una separación entre filas de 21,6 mm.
La unión de dicha sección de fuselaje se realiza mediante remaches ciegos, con lo que es necesario realizar operaciones de taladrado/avellanado, aplicación de sellante e instalación de remaches. A continuación se detallan los principales requerimientos establecidos por normativa para dichas operaciones:
- Diámetro del taladro: 4,8 [mm]
- Profundidad (max. grip FC): 6,4 [mm]
- Tolerancia en diámetro taladrado: +/-0,05 [mm]
- Tolerancia en perpendicularidad: +/-0,5 [º]
- Tolerancia entre agujeros: +/-0,2 [mm]
- Max. desviación del remache respecto a la superficie (enrasado): -0,1/+0,2 [mm]
2. Automatización flexible basada en robótica
Bajo las premisas establecidas en el punto anterior, Tecnalia ha conceptualizado, desarrollado y validado mediante prototipo, una solución innovadora de automatización flexible. Esta consiste en un robot industrial que porta como garra o ‘end-effector’ una maquina CNC de 4 ejes, que se fija al fuselaje mediante ventosas y ejecuta, en áreas discretas del fuselaje, operaciones de taladrado, avellanado, aplicación de sellante e instalación de remaches ciegos.
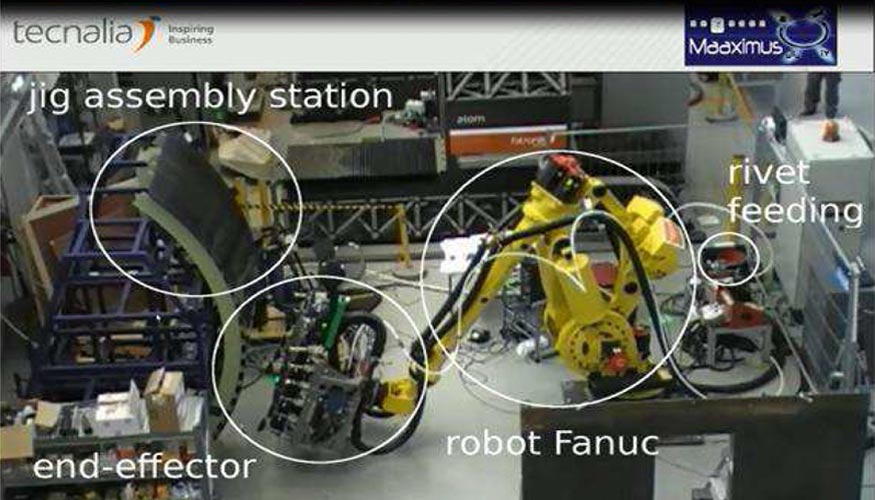
La solución desarrollada consta de los siguientes elementos principales:
- Robot Industrial: su función es mover y sujetar el ‘end effector’ sobre el fuselaje durante el procesado del mismo.
- End-effector: máquina CNC de 4 ejes controlados (dos translaciones y dos giros). Está dotado de un sistema de ventosas montadas sobre unos actuadores lineales (neumáticos) para poder anclarse al fuselaje.
- Cabezal multifunción: integra todas las herramientas necesarias para realizar la unión del fuselaje (taladrado/avellanado, sellante, remachado), además de un sistema de visión para la identificación de elementos en la superficie del fuselaje que se utilizan para la referenciación de la máquina CNC.
- Sistemas auxiliares: alimentación automática de remaches, aspiración de polvo de taladrado.
2.1 Operativa general del sistema
- La zona que debe procesar el sistema automatizado se divide en un determinado número de áreas o ventanas de trabajo. Dependiendo del tamaño de fuselaje serán necesarias más o menos ventanas.
- El robot industrial posiciona el ‘end-effector’ en la primera zona de trabajo y se bloquea en esa posición. Todavía no existiría contacto entre ‘end-effector’ y fuselaje.
- El ‘end-effector’ despliega las ventosas y hace contacto con el fuselaje. Las ventosas no están dedicadas a compensar el peso del end-effector, sino a minimizar el impacto en el robot del esfuerzo normal durante taladrado.
- El sistema de visión busca sobre el fuselaje cuatro pre-taladros (en principio los cuatro que conforman las esquinas de la ventana de trabajo), y los utiliza para referenciarse y corregir el CAM programado (rototraslación).
- Una vez referenciada, el cabezal se posiciona sobre el primer agujero de la ventana de trabajo e inicia la secuencia de operaciones correspondiente:
a. Taladrado/avellanado
b. Aplicación de sellante
c. Instalación de remache
d. Movimiento al siguiente agujero
- Esta secuencia se repite tantas veces como agujeros haya que procesar en la ventana de trabajo actual.
- Una vez se completan todos los orificios, se suelta el “end-effector” del fuselaje (se retraen las ventosas) y el robot industrial mueve el end-effector a la siguiente ventana de trabajo.
- El procedimiento se repite tantas veces como ventanas de trabajo se hayan definido en el área que se quiere procesar.
2.2 Componentes principales del sistema
• 2.2.1 Robot industrial
Tal y como se ha explicado anteriormente, la función del robot industrial es posicionar y soportar el ‘end-effector’ en las distintas posiciones de trabajo que se definan. En el caso del prototipo desarrollado por Tecnalia se ha trabajado sobre una sección de fuselaje de 90º (un cuarto del barril completo), y se han necesitado 5 posiciones distintas para cubrir dicho volumen de trabajo.
El robot empleado en el prototipo desarrollado es un Fanuc M900iA-400L, con una capacidad de carga de 400 kg y un alcance de 3.165 mm. Los principales requerimientos establecidos para la selección del robot industrial son que pueda gestionar el peso del ‘end effector’ (aprox. 300 kg) y que sea capaz de cubrir los 90º de fuselaje con el mismo. No es necesario que el robot tenga una elevada precisión de posicionamiento, ya que está prestación viene dada por el ‘end-effector’ una vez se ‘ancla’ sobre el fuselaje.
• 2.2.2 End-effector: máquina CNC
El ‘end-effector’ es el elemento que permite realizar las operaciones de unión con las tolerancias que exigen los estándares del fabricante. Está constituido por una estructura mecanosoldada de tubo de acero (marco) sobre la que se ha montado una máquina CNC con cuatro ejes controlados, dos lineales (X e Y) y dos giros (B y C). Sobre dicha máquina va montado un cabezal multifunción con las herramientas necesarias para llevar cabo la unión de los tramos de fuselaje.
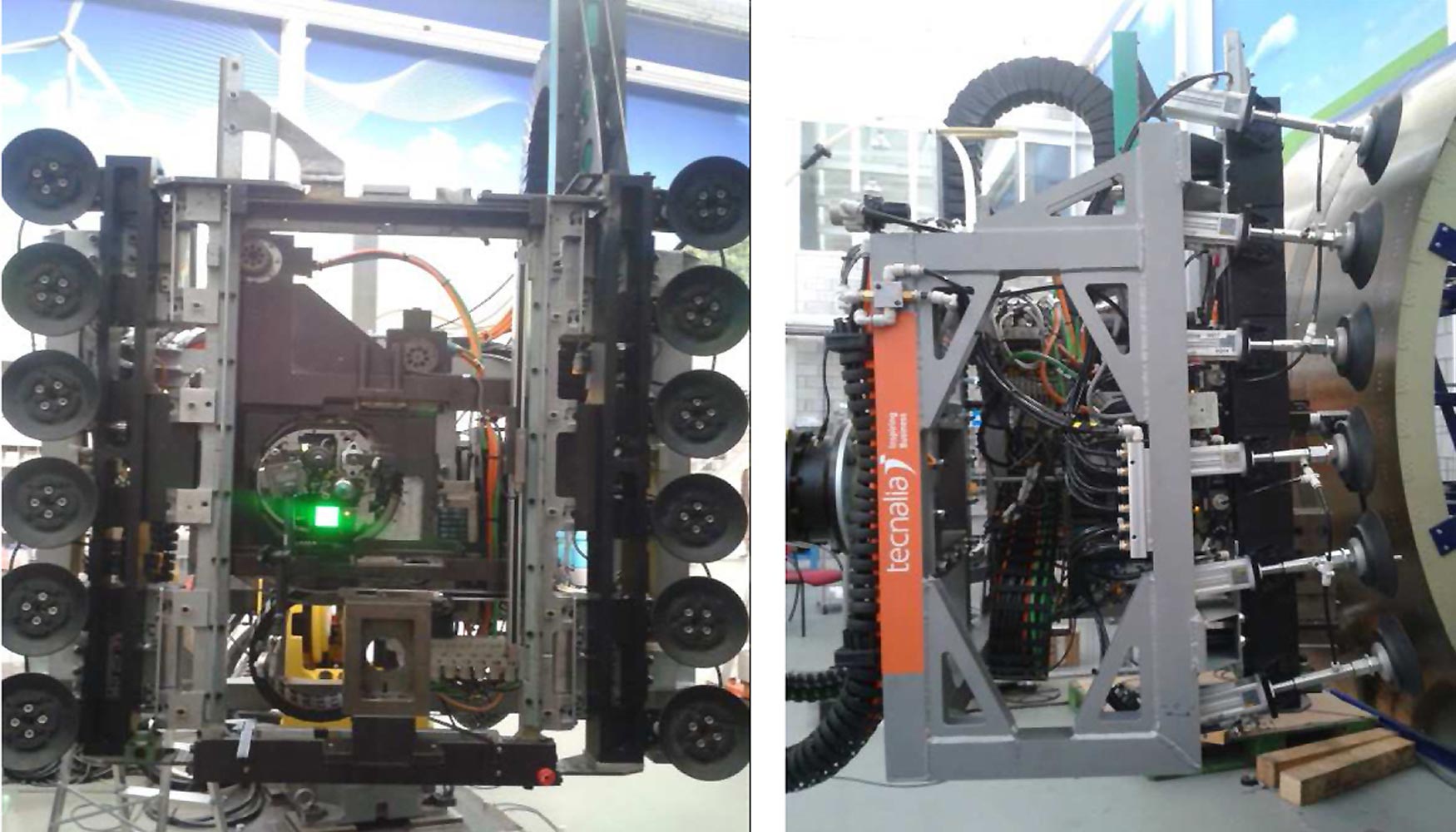
Las dimensiones máximas de la ventana de trabajo que puede ser procesada por la máquina es de 160 x 600 mm. En el demostrador que se ha utilizado para validar el prototipo se ha dividido el panel en 5 ventanas de trabajo, pudiendo procesarse en cada una de ellas entre 14 y 16 filas de agujeros. El marco de la máquina lleva incorporados doce actuadores lineales (seis a cada lado) sobre cuyos vástagos van colocadas las ventosas que se utilizan para anclar la máquina al fuselaje. Estos actuadores están orientados según la curvatura del fuselaje sobre el que se va a trabajar. Cada ventosa ejerce una fuerza máxima de 15kg sobre la superficie del fuselaje. La deformación provocada por la presión de los actuadores al apoyarse sobre el fuselaje es prácticamente cero. Las ventosas permiten absorber esfuerzo de taladrado y amortiguar vibraciones generadas durante la operativa.
• 2.2.3 End-effector: cabezal
El ‘end-effector’ se completa con el cabezal multifunción que consta de diversas herramientas para llevar a cabo la unión de los tramos de fuselaje. En la construcción del cabezal se ha priorizado el uso de equipos industriales estándares de bajo coste: herramientas semiautomáticas ‘off the shelf’ de taladrado, aplicación de sellante y remachado, empleadas actualmente en la producción aeronáutica. Cada una de las herramientas integradas en el cabezal va montada sobre su propio actuador lineal de manera que puedan operar de forma independientemente sobre el fuselaje. En un principio todas las herramientas están retraídas en el interior del cabezal, y solo avanza la que sea necesaria para cada secuencia del proceso de montaje.
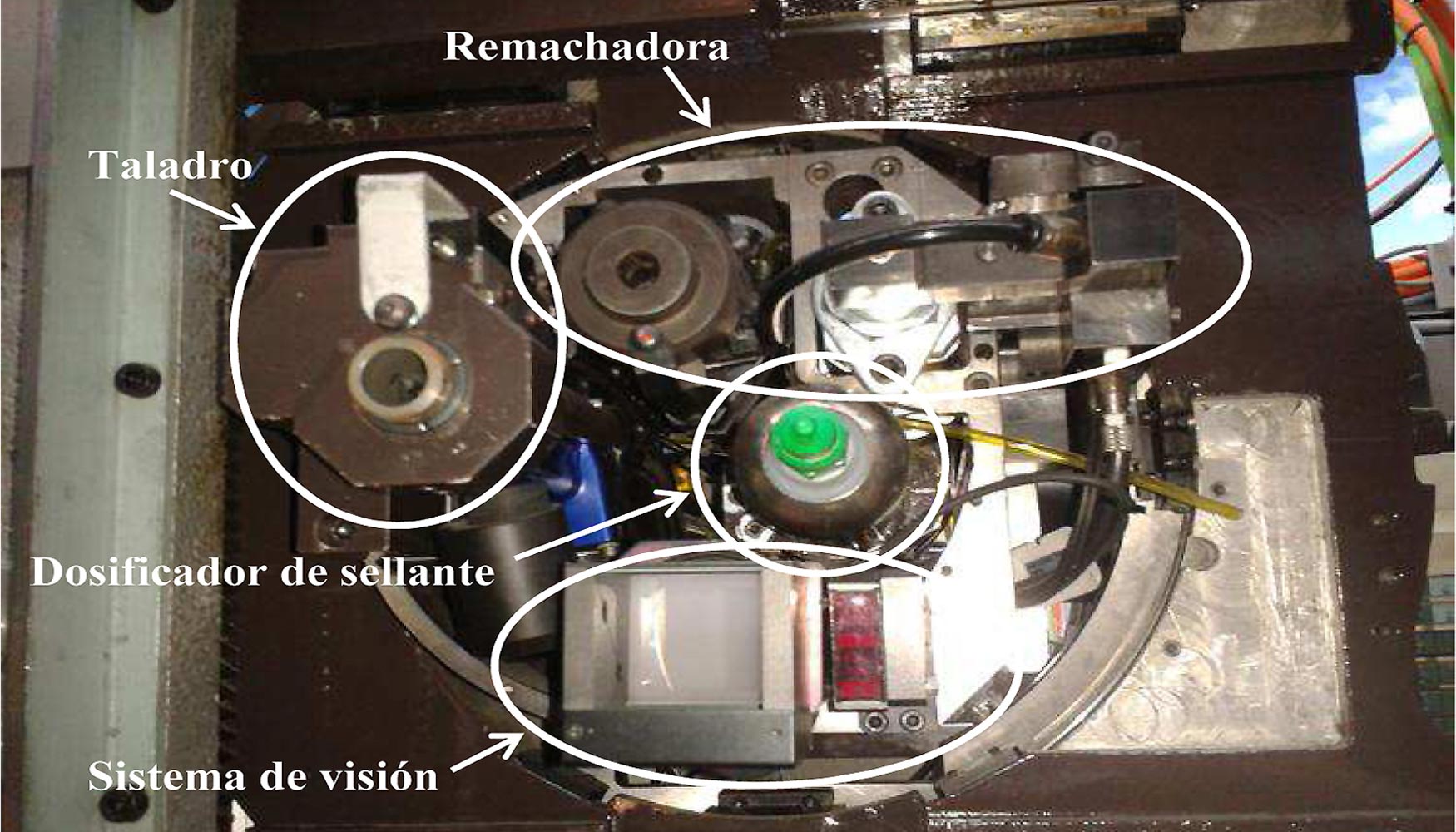
- Sistema de visión: El sistema de visión permite reconocer los pre-taladros existentes en el ‘buttstrap’ y determinar las coordenadas XYZ de su centro. Una vez la máquina CNC se fija sobre el fuselaje, se procede a reconocer cuatro pre-taladros (cuatro esquinas de la ventana de trabajo) y se obtiene la rototraslación del CAM programado. Los 4 grados de libertad del ‘end-effector’ de alta precisión permiten hacer una única calibración para todo el volumen de la ventana de trabajo, en vez de para cada remache, con la consiguiente reducción del tiempo de procesado (mayor productividad) del sistema.
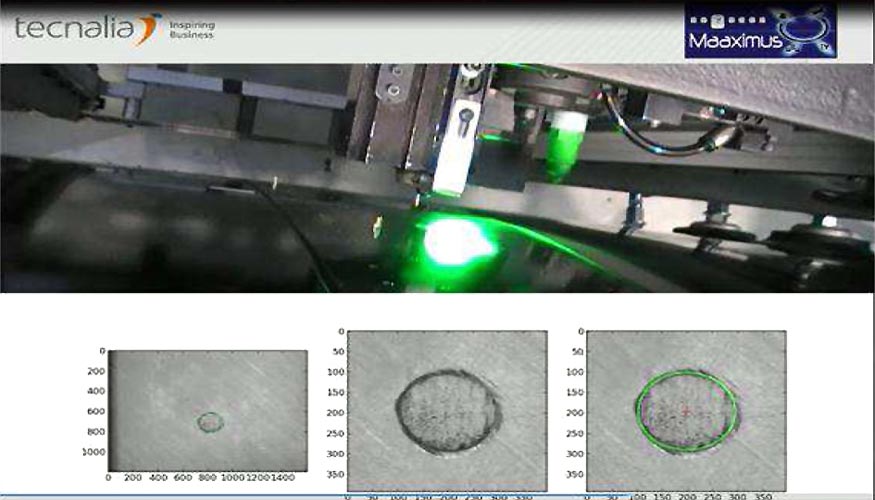
- Taladro: Se ha integrado un ADU (Automatic Drilling Unit). Se trata de una herramienta semiautomática que ya es utilizada para la realización del proceso de forma manual, pero con algunas modificaciones que permitan su utilización en un contexto automático. Para realizar el taladrado, el ADU se apoya sobre el fuselaje y ejerce una presión de 60 kg sobre el mismo para poder garantizar un proceso OWA (One Way Assembly). La herramienta incorpora un sistema de aspiración que evacua el polvo que se generan durante el proceso de taladrado. Se han desarrollado brocas específicas para la aplicación. La forma de la broca empleada en el taladrado permite realizar el taladrado y avellanado en una única operación.
- Dosificador de sellante: Una vez realizado el taladro es necesario aplicar una pequeña cantidad de sellante en el avellanado del agujero. El sistema de sellante integrado está compuesto por un dosificador automático, un porta-cartuchos y una boquilla.
- Remachadora (+ transfer de alimentación): El ‘end-effector’ es capaz de instalar remaches ciegos del tipo Composilok (tipos 2 y 3). Para la instalación de los remaches se ha integrado una herramienta de remachado comercial. El remache es cargado en la herramienta mediante un brazo transfer. La alimentación automática de los remaches se realiza mediante alimentador por soplado, tipo tolva vibratoria que se ha ubicado en la parte trasera del robot y conectado con la unidad transfer mediante un tubo flexible.
2.3 Validación sobre demostrador: prestaciones alcanzadas
El funcionamiento del sistema desarrollado se ha validado sobre un demostrador físico. En concreto se ha fabricado un utillaje sobre el que se ha montado el equivalente a un cuarto de fuselaje, a escala 1:1 (aproximadamente 4 m de diámetro), y fabricado en fibra de carbono con los espesores reales descritos en el apartado 1 (6 mm, 3+3 en la zona de la unión). Para la colocación del buttstrap sobre el fuselaje se han instalado una serie de remaches temporales de forma manual, siguiendo las directrices de Airbus para la instalación de este tipo de elementos (tanto en posición como en cantidad).
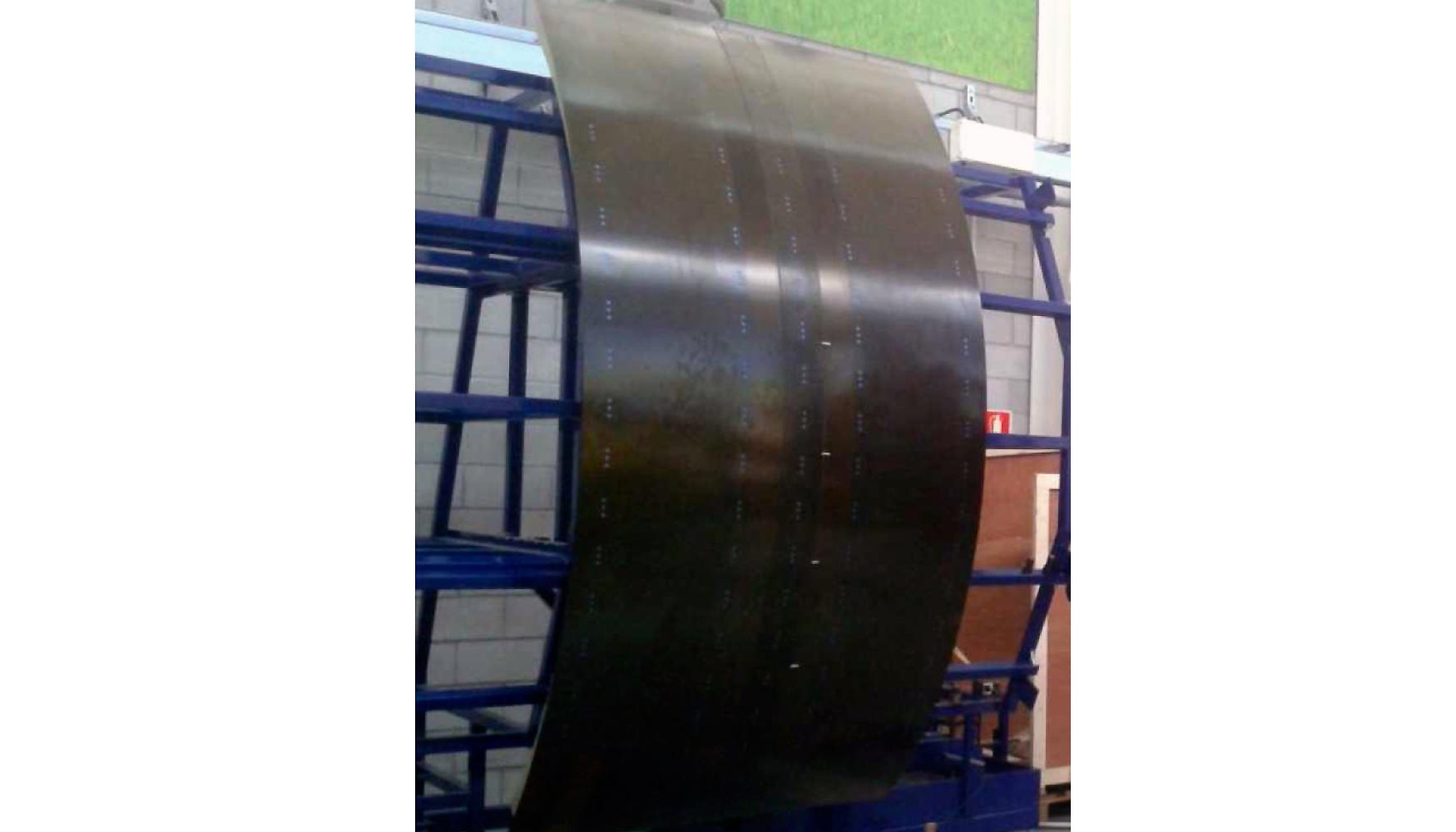
Las prestaciones alcanzadas por el sistema responden a las exigencias de calidad del ensamblaje aeronáutico. Se indican a continuación los valores de precisión alcanzados en los ensayos de validación del sistema:
- Error de posicionamiento entre taladros consecutivos (hole-to-hole): < +/-0,1 [mm]
- Error de posicionamiento entre taladros extremos de una misma fila: < +/-0,1 [mm]
- Error de profundidad del avellanado: < +/-0,1 [mm]
- Error diametral del taladrado: < +/-0,05[mm]
- Error de perpendicularidad del remache: < +/-0,5 [º]
- Error de enrasado de la cabeza del remache respecto a superficie < ±0,1 [mm]
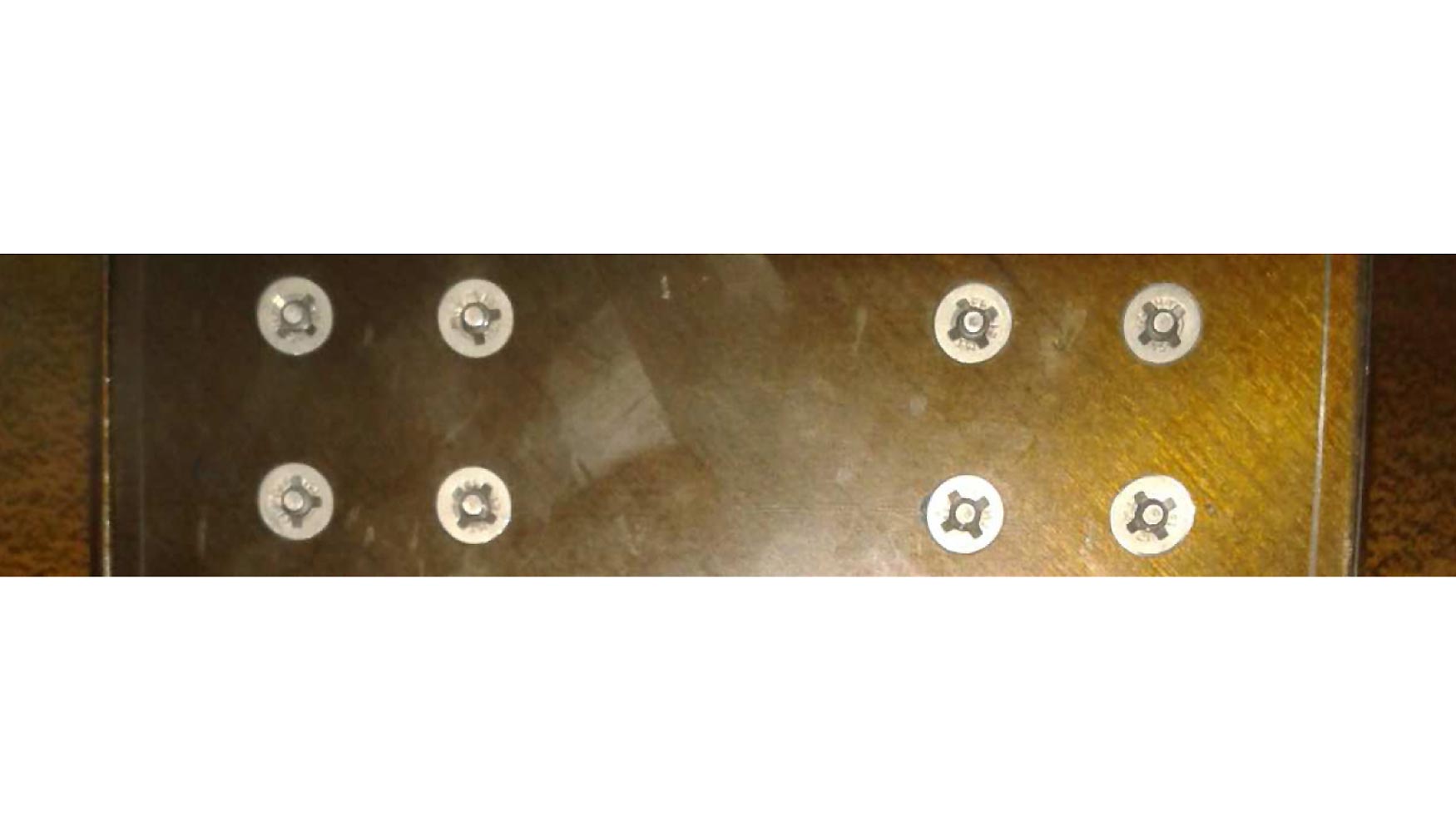
La productividad alcanzada por el sistema supera también el objetivo establecido al comienzo del proyecto. Los valores obtenidos son los siguientes:
- Productividad sistema con respecto al objetivo establecido: + 32 [%]
- ‘Lead Time’ de proceso por remache instalado: 27 [s]
El tiempo de ciclo de 27s por remache incluye la totalidad de las operaciones a realizar. Es decir: traslación del end-effector entre ventanas de trabajo realizado por el robot; anclaje y desanclaje del end-effector en el fuselaje mediante ventosas; referenciación a través del sistema de visión; rototraslación; desplazamiento del cabezal entre agujeros; taladrado y avellanado; aplicación de sellante; alimentación del remache; instalación del remache. Es de esperar que este tiempo de ciclo obtenido en fase de demostrador se reduzca en el sistema optimizado en fase de industrialización.
3. Solución para el despliegue en la línea de ensamblado final
Para poder cumplir con los requerimientos de productividad impuestos por Airbus, la solución planteada exigiría combinar varios robots en la línea final de montaje (FAL), de forma que pudieran trabajar en paralelo sobre una misma sección de fuselaje. A partir de los resultados obtenidos en el demostrador se realizaron diversas simulaciones para tratar de visualizar posibles soluciones que permitan abordar la unión del fuselaje completo. Se analizaron dos posibles alternativas: una primera que utiliza cuatro robots trabajando a la vez, y una segunda en la que únicamente se utilizan dos. En las siguientes imágenes se ilustran ambos conceptos.
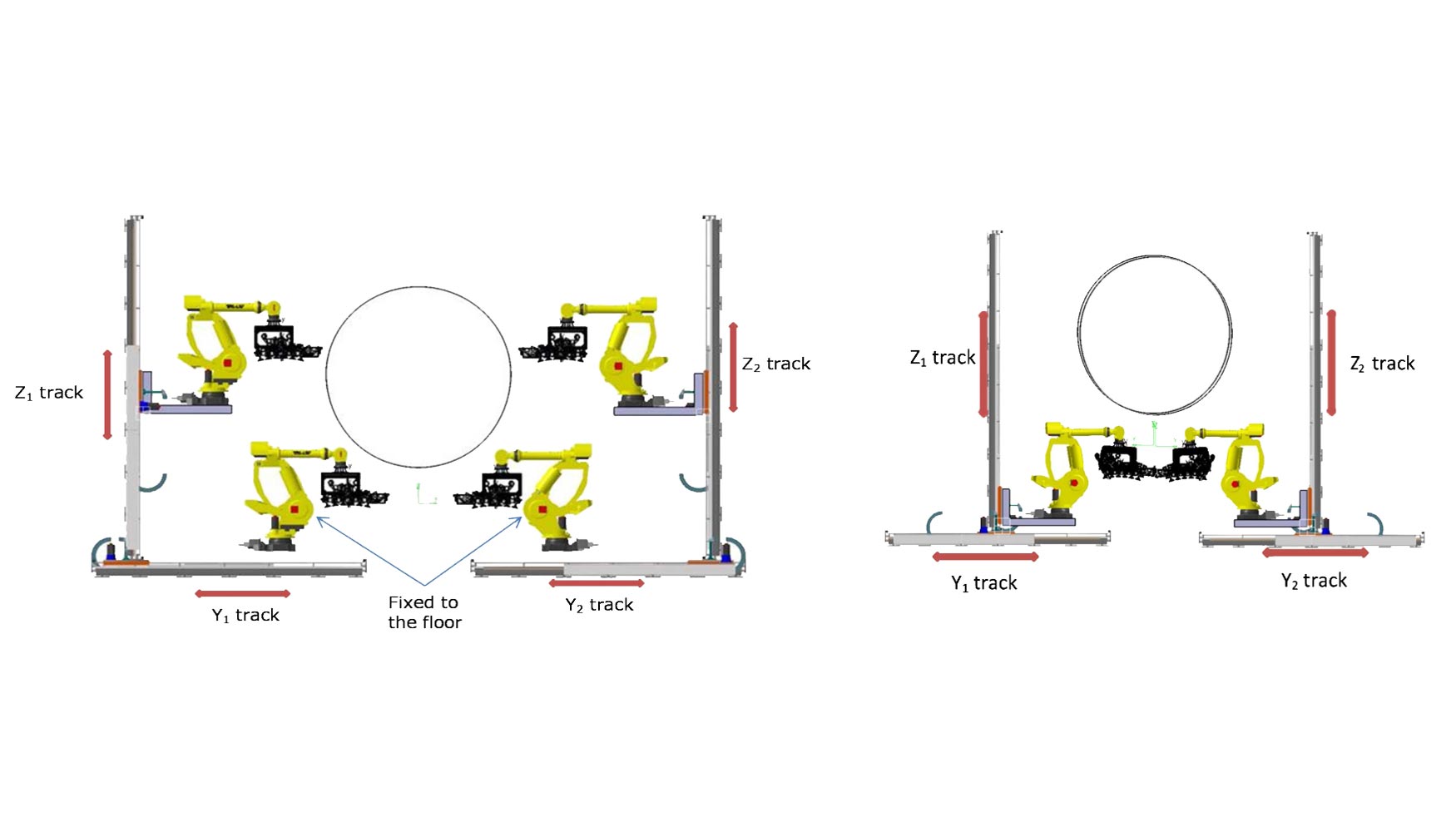
La solución con cuatro robots resultaría bastante compleja de implementar. Los dos robots de la parte inferior irían fijados al suelo. Los dos robots encargados de unir la mitad superior del fuselaje requerirían ir montados sobre dos ‘tracks’ cada uno (uno vertical y otro horizontal). Por otro lado hay que recordar que el espacio disponible en FAL para la instalación del sistema automático es bastante reducido (1,5 m de ancho), con lo que se prevé que existirían muchos problemas de interferencias entre robots al implementar esta opción. Una solución más sencilla sería utilizar únicamente dos robots para realizar la unión. Cada robot realizaría la unión de medio fuselaje (uno la mitad izquierda y otro la derecha). También sería necesario montar cada robot sobre dos ‘tracks’, pero la implementación sería más sencilla que en el caso de cuatro robots. Teniendo en cuenta la reducción de tiempos de procesado obtenidos, la configuración de dos robots resulta la opción más competitiva.
4. Conclusiones
El sector aeronáutico se encuentra ante la necesidad, cada vez más acuciante, de automatizar sus procesos productivos con el fin de aumentar la productividad, garantizar la calidad de sus productos y reducir costes para poder ser competitivos. Para responder a dicha demanda Tecnalia ha diseñado, fabricado y puesto en marcha un sistema robotizado capaz de realizar la unión automática de secciones de fuselaje, que incluye operaciones de taladrado, aplicación de sellante y remachado. Dicho sistema se ha validado mediante un demostrador sobre una réplica a escala 1:1 de un cuarto de fuselaje de la sección 13 de un Airbus 3X0. Los resultados obtenidos han sido muy satisfactorios por la calidad alcanzada, que responde a los parámetros exigidos por la normativa aeronáutica, así como por los tiempos de procesado, que han mejorado los objetivos establecidos al comienzo del proyecto en un 32%.
Se trata de un sistema innovador, que permite automatizar de manera competitiva la compleja operación de ensamblaje de grandes componentes estructurales, como son las secciones de fuselaje. El innovador sistema de automatización, mejora de forma importante la producción de esta operación de ensamblaje, recortando tiempos y disminuyendo de forma significativa el coste del proceso. Se trata, a su vez, de una solución flexible, de arquitectura ligera y coste de instalación contenido, resultando una alternativa competitiva a soluciones basadas en grandes máquinas de arquitectura convencional.
Agradecimientos
Este proyecto ha sido parcialmente financiado por la comisión europea dentro del marco del proyecto FP7 Maaximus. FP7/2007-2013 under grant agreement n°213371 (Maaximus, www.maaximus.eu).