Reducir el gasto en herramientas no garantiza la reducción de costes de producción
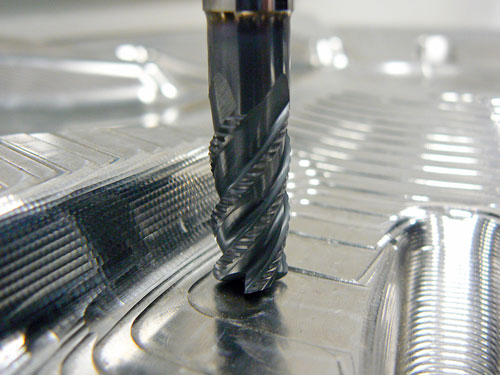
Desarrollos como la nueva geometría Duplex o JETCut, entre otras, son una muestra de nuestro compromiso con este tipo de industria y que seguiremos apostando por este sector. Sobre las ventajas de aplicar estas geometrías profundizaremos a continuación.
Desbaste
Partiendo de la base que el mecanizado es la mayor parte del costo total del molde o matriz, alrededor de un 65%, deberíamos pensar en qué forma podríamos reducir este coste. La primera opción es el gasto en herramienta. Sin duda ésta es la manera más fácil pero no la más acertada ya que diferentes estudios demuestran que este coste es de aproximadamente entre un 5 y un 7%.
Realmente, debemos trabajar en la optimización del tiempo de mecanizado. En éste apartado será donde consigamos los mayores beneficios y ahorro de costes. Para esto debemos analizar desde las estrategias de mecanizado, las herramientas y su sujeción y demás factores que intervienen en el proceso de mecanizado, que iremos desarrollando en este artículo.
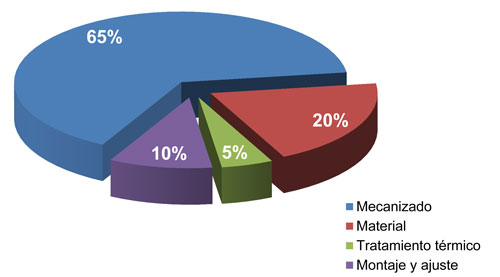
Los métodos de fabricación han evolucionado enormemente en los últimos años. Tanto las máquinas como los software CAD-CAM o las herramientas han dado un gran salto cualitativo brindando interesantes oportunidades para mejorar en el apartado del mecanizado.
En los últimos años hemos visto cómo se ha hablado, cada vez más, de mecanizados HSC (alta velocidad) o Alto rendimiento HPC (High Performance Cutting) o mecanizados trocoidales. De este último quiero hacer hincapié ya que la gran mayoría de compañías de software CAM han desarrollado estrategias para la aplicación de este tipo de mecanizado.
Esta estrategia de desbaste nos aporta un gran volumen de viruta arrancado (Q cm³/min) por el cual podemos reducir el tiempo de mecanizado hasta un 50% con respecto a trabajar con un plato de gran avance. Con este mecanizado podemos utilizar hasta 2 veces el diámetro (2XD) en incremento axial (ap) y entre un 40 o 50% de la herramienta en incremento radial (ae). Esto es posible porque estas estrategias respetan siempre las profundidades de corte programadas, entonces las trayectorias serían como un mecanizado lateral y en el momento que la herramienta debería mecanizar a diámetro completo el software genera una trayectoria trocoidal respetando la geometría de la pieza. Esto permite tener una evacuación de viruta mejor controlada y de esta manera hacer que el proceso de desbaste sea mucho más seguro.
En Franken ya empezamos a trabajar sobre este tema hace unos años, dando como resultado nuestra geometría Duplex, que nos permite trabajar de dos maneras diferentes y hasta 66HRc. La primera como comentamos anteriormente y la segunda mecanizando alto rendimiento (HPC). Entendemos por HPC como un mecanizado con poco incremento axial (ap) y un alto avance por diente (fz) con velocidades de corte estándar. Muchas veces se confunde este tipo de mecanizado con alta velocidad (HSC).
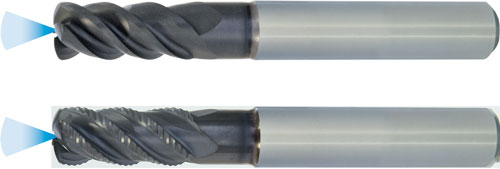
Volviendo al tema del trocoidal, deberíamos decir que no siempre esta opción es aplicable a todo tipo de desbastes, ya que nos limitará la longitud de la herramienta. Sobre todo este tipo de mecanizado, donde mejor se adapta es en la fabricación de postizos o de cajeras.
Como comentamos al principio, en el proceso de mecanizado intervienen varios factores y uno muy importante es el de la sujeción de la herramienta. En un desbaste las fuerzas de corte suelen ser bastante altas y tienden a expulsar la herramienta hacia abajo sobre todo en diámetros a partir de 12 mm donde es imprescindible una buena sujeción. Emuge-Franken ofrece tanto Safe-Lock, un novedoso sistema de sujeción por inducción térmica más una ranura helicoidal que asegura que no haya movimientos axiales de la herramienta, como PWRGrip, un sistema de sujeción por pinzas que nos brinda fuerzas de apriete superiores a 1.100 Nm una concentricidad de 0,003 µ.
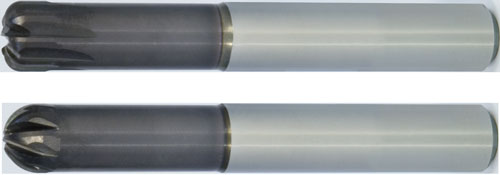
Acabados
Hasta el momento hemos hablamos de desbaste pero en el acabado también podríamos reducir costes aplicando herramientas JETCut. Estas tienen la particularidad, tanto en herramientas tóricas como en esféricas, de la cantidad de filos de corte. Por ejemplo una herramienta de diámetro 12 milímetros tiene 8 filos.
Con la evolución de las máquinas, la llegada de los 5 ejes, muchos métodos de mecanizado han cambiado y otros no tanto. Las operaciones de acabado son el claro ejemplo de ello. Es muy frecuente encontrarse todavía con empresas, que teniendo máquinas de 5 ejes continuos o de 3+2, continúen planteando el mecanizado como si dispusieran de una máquina de 3 ejes.
Volviendo al acabado con herramientas esféricas JETCut a la hora de hacer una operación de copiado por ejemplo, sería muy beneficioso tanto para la vida de la herramienta, como para el tiempo de mecanizado o la calidad superficial inclinar el cabezal de la máquina. A partir de 15º haríamos efectivos los 8 filos de la herramienta obteniendo como resultado una reducción del tiempo significativo o unos valores de Ra (rugosidad) menores en comparación con una herramienta de dos filos de corte.
Por otro lado las empresas que no dispongan de este tipo de maquinaria (5 ejes) podrían beneficiarse empleando herramientas tóricas aplicando el mismo concepto pero en trayectorias en Z-constante. Por ejemplo en acabado de paredes verticales o inclinadas.
En conclusión, hemos visto maneras diferentes de ahorrar tiempos de mecanizado, ya sea en operaciones de desbaste y también de acabado, inclusive con diferentes tipos de configuraciones de máquina. El ser más competitivo no pasa por reducir el gasto de herramienta, si no por producir mejor y más rápido.