Prediction of the temperate layer in the 'grind-hardening' of cylindrical pieces by means of a model FEM 3D
Or.Alonso, N.Ortega, I.Pombo, J.To.Sanchez, S.Square, B.Izquierdo, of the department of
The rectified cylindrical is a process of mechanised of high precision widely employed in pieces of revolution (around 75% of the pieces rectified use this application). Many of the pieces rectified are toughened superficialmente by means of processes that are difficult to integrate in the lines of production. The 'grind-hardening' is a new process that pretends to carry out the hardening and finishing of the piece by means of an only process of mechanised. With the aim to study the excessive generation of heat and his repercussion on the pieces rectified, in previous works developed a thermal sensors model of finite elements 3D for rectified cylindrical in traverse. In this work will evaluate the validity of the model to predict the temperate layer in experimental proofs of grind-hardening in pieces of steel AISI 1045. Besides, it has evaluated the possibility to use the method of noise Barkhausen like essay no destructive for prediction of the temperate layer in the piece.
1. Introduction
The rectified cylindrical in traverse is a process industrialmente used for the finishing of surfaces of revolution. In previous stages of the process of manufacture, a lot of mechanical components have been toughened superficialmente by means of thermal sensors treatments like the temper by induction. However, this type of processes are very difficult to integrate in the lines of production and, besides, present a high cost. In front of this, in the last decades, have developed innovative processes like the ‘grind-hardening' that pretend to carry out the hardening and the finishing of the piece by means of an only process of mechanised [1, 2, 3]. This process takes advantage of the heat generated in the interaction of the grains of abrasive with the piece to elevate the temperature above the one of austenización in a period of time very short. Had to, on the one hand, to the demanding requirements of finishing, superficial integrity and dimensional tolerances and, on the other hand, to the high number of variables that influence in the process, the selection of the parameters of mechanised for the tuned of this process requires of a high number of experimental essays. Thus, they have developed mathematical models for 'grind-hardening' in rectified flat [4, 5, 6] and for 'grind-hardening' in rectified cylindrical [7,8] that pretend to reduce this strong experimental component.
An important appearance to take into account is the tensional state of the piece after the process of finishing. The plastic deformation no homogénea (because of the high variations of temperature and mechanical efforts in the surface) and the changes of volume generated by changes in the micro-structure of the material, can cause unwanted residual tensions that affect to the life to fatigue of the piece.
However, the detection of this type of tensional states requires of destructive technicians or semi-destructive as 'hole-drilling', the elimination of layers or the diffraction of X-rays. In the last decades has done an important effort for developing technicians no destructive as, for example, the based in the noise of Barkhasuen, that allow to predict the state tensiona of the piece, as well as the changes in the metallurgical structure that have been able to suffer the material during the mechanised.
The signal of noise Barkhausense attributes to the irreversible movement of the domuinios magnetic during a process of magnetisation cíclica. This movement is strongly influenciado by the microstructure of the material and by the tensional state of the piece [10]. Until the moment, this method only allows compares two states of lapieza of qualitative signature. However, recent works have tried prededir of quantitative form the distribution of residual tensions [11, 12, 13] or the evolution of the hardness of the material under the surface [14, 15].
The aim of this work is to develop a model FM 3D for rectified cylindrical in traverse that allow prefecir the depth of layer tempered in the process of grind-hardening. Likewise, it will evaluate the possibility to use the method of noise Barkhausen like essay no destructive for prediction of the depth of the temperate layer generated in the piece.
2. Description of the model FM
The simulation by means of finite elements of the process of grind-hardening has like aim the preducción of the thickness of the temperate layer. The thermal sensors models of rectified substitute the action of grind it on the piece by a source of heat that moves on this with an equal movement to the relative between grind it and the piece. For this, results imprescibndible define properly the zone of contact on which applies the source, the distribuciónd the heat on this ace like the quantity of the total heat generated that evacúa through the piece.
2.1. Estimate of the zone of contact
As it observes in the figure 1, the zone of contact has considered like a cylindrical surface. In the experimental essays, that will comment later, observed that the wear of grind it was irregular. When existing a type of different contact (see figure 4) in each zone of grind it, would be necessary to define several source s of heat. This would complicate excessively the model and, thus, has opted consider an only source of heat on a width of grind effective (bseff).
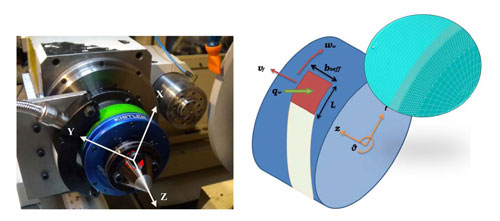
Regarding the length of the zone of contact (lc) has considered that this can approximate from the proportionate expressesion by Rowe et. To the. [15]:
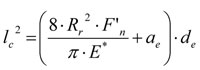
Where:
• F'N: specific strength of rectified that it can obtain from the following expressesion:
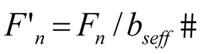
Where Fn is the normal strength in the zone of contact between grind it and the piece and bseff the width grind effective engaged in the cut. The value of the normal strength has been measured by means of a rotary presses dynamometer Kistler 9123C planted in the cabezal piece. This dynamometer is able to measure three strengths (Fx, Fy, and Fz) in the steerings of the axles of a system of mobile coordinates (see figure 1).
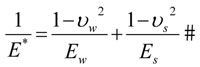
- And*: it represents the elastic properties of grind it and the piece.
Taking into account the following approximate values of the elastic properties of the steel and of grind it:
or Module of elasticity of the steel: 210 GPa.
or Module of elasticity of grind it: 50 GPa.
or Coefficient of Poisson of the steel: 0,29.
or Coefficient of Poisson of grind it: 0,22.
Obtains a value of said coefficient of 42,75 GPa.
- Rr: Factor of rugosidad. According to Rowe [15] a value of Rr=5 provides values of length of suitable contact when it grind it finds blunted (see section 3.1).
- Toand: depth of past radial real.
- dAnd: equivalent diameter. His value can obtain from the diameter of grind it (ds) and of the piece (dw) from the following expressesion:
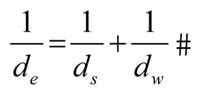
2.2. Quantity of heat evacuated to the piece and distribution of heat
The power consumed during the process of rectified in transforms , practically in his whole, in heat in the zone of contact between grind it and the piece. His value can approximate from the following expressesion:

Where Fc is the strength of cut, vc is the peripheral speed of grind it, bseff is the width of grind it effective engaged in the cut and lc is the length of real contact. This power calorífica is evacuated through the piece, grind it, the shaving and the fluid refrigerante. The fraction of heat evacuated to the piece can obtain through the parameter Rw (fraction of the total power that derives to the piece).
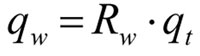
3. Validation of the model by means of experimental essays
3.1. Essays posed
The essays were realizar in a rectificadora cylindrical of outsides Danobat FG-600-S using one grind of white alumina Tyrolit CS33To802HH4VK1 of diameter 400 mm and width 18,5 mm. Regarding the material used in the probetas of the essays, chose a half steel in carbon (AISI 1045), and these were cubic capacities and later rectified until an external diameter of 50 mm. On the other hand, during the essays took measured of the power consumed by the cabezal grind and of the strengths generated during the process.
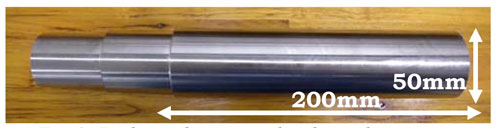
Carried out three essays in which it realizar a past in dry with the parameters indicated in the table 1. Before each one of the essays, grind it was diamantada with a loseta of diamond multipunta, using for this a speed of grind of 35 m/s, a speed of advance of 200 mm/min and a depth of past radial of 10 μm. During the essays, did not use any type of refrigerante, since it has pretended favour the increase of the temperature of the material above the one of change of phase. However, the warming of grind it could accelerate his wear. Danobat Proposes (by means of a system patented with reference IS2315064B1) refrigerate grind it in a point moved away of the zone of contact avoiding like this the cooling of the piece.

In the figures 4 and 5 observes the appearance of the piece and the state of grind it after the past of rectified in dry for the essays 1 and 2 respectively.
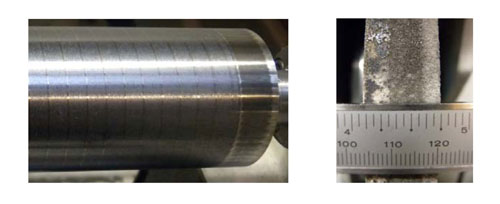
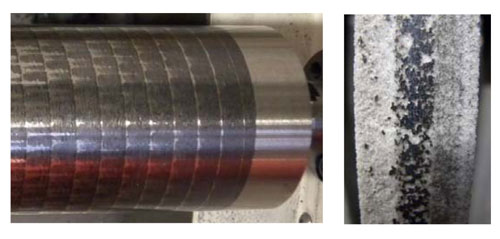
The appearance of grind them after each one of the essays indicates that the wear produced along the width of grind it has not been uniform. In the figure 4, observes that roughly a third of grind it finds blunted. In this zone, the friction between grind it and the piece will be stronger and will generate high quantities of heat (during the essay observed that in this zone concentrated the shaving incandescente). To continuation, presents another grey zone (characteristic of the process of rectified) and finally a white zone that hardly has mechanised material.
In the essay 2, however, the zone blunted finds in the centre of grind it. In this case, during the essay, observed roughly in the central zone of the piece the shaving incandescente displaced to the centre of grind it. This effect can be due to that an excessive increase of the normal strength in the first segment (causing by an embotamiento excessive of grind it) have caused the break of the bridges of aglomerante, generating, therefore, a severe wear of grind it. For this reason, it has I decide to consider the hypothesis that, in each instant of the essay, the width of grind engaged in the cut (bseff) is 2/3 of the total width of this. This hypothesis tries to simplify the fact to employ three independent sources in the model when supposing an only source with an active width of 2/3 of the width of grind it and that it was representative of what sucede in all she.
3.2. Validation of the model FEM
The validation of the model of finite elements has realizar comparing the temperate layer in each probeta with the depth of the model to which reaches the temperature of change of phase. With the aim to obtain information to near of the existence of said temperate layer by means of a no destructive essay, has have measured values of noise Barkhausen using a team Rollscan 300 of Stresstech Group. In the figure 6 observe the values of BN before and after the three essays in 10 points of the piece spaced 20 mm. As it has commented previously, although they exist works in which it tries relate the absolute values of level of noise Barkhausen with the microstructure and the tensional state of the material, at present, these measures contribute only qualitative information. Therefore, it is necessary to take measures of BN of the piece without temperate layer before rectifying like value of reference to compare.
As it observes in the figure 6, the level of noise Barkhausen is not uniform along the probeta. This effect is due to that the irregular wear of grind it has caused that the friction generated in the intercara grind-piece (and therefore the quantity of heat generated in the process and the depth of temperate layer) vary along the length of the piece rectified.
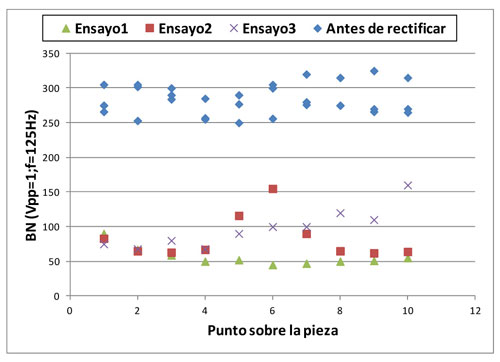
To continuation has studied the depth of temperate layer in the probetas in the left, centre and right of these. In the figure 7 show three micrografías where observes the depth of temperate layer in each one of the three ensayios in the right extreme of the piece. The depths obtained are of 140 µm for the essay 1, 80 µm for the essay 2 and 36 µm for the essay 3 respectively.
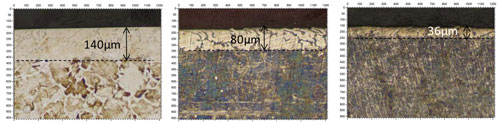
Splitting of the hypothesis that the width of grind engaged in the cut corresponds with 2/3 of the total width of grind it, have carried out several simulations for each one of the three essays. The model represents an excellent correlation with the reality for values of the parameter Rw of 0,65 (essay 1), 0,675 (essay 2) and 0,8 (essay 3). These values of the fraction of power evacuated to the piece agree with the obtained by authors for rectified with grind of alumina [16, 17, 18, 19].
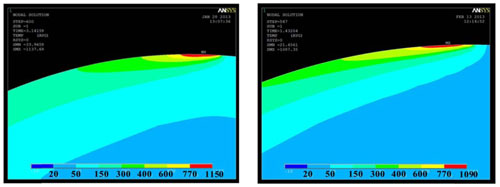
On the other hand, in the figure 8 show the values of noise Barkhausen corresponding to each one of the depths of temperate layer. It observes that the relation is roughly linear, therefore, this method can be used to obtain an estimate of the depth of temperate layer in the material. However, it has to take into account that the tensional state of the piece also affects also to the level of noise Barkhausen registered, by what would be convenient to carry out a study of the distribution of the residual tensions in the piece.
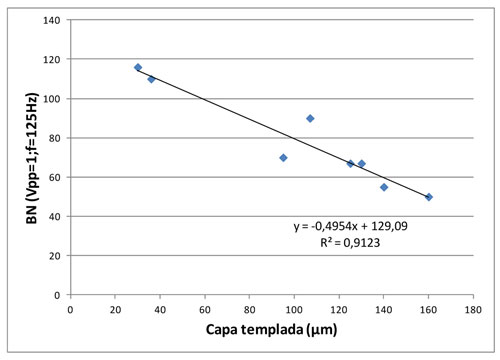
An important parameter to take into account in the taking of measures of BN is the depth associated to this (in the practice the depth of the measure is used to to vary between 0,01 and 2 mm). The spectrum of power of the signal of noise Barkhausen issued to a determinate depth sees cushioned by the material that finds on this. The main factors that determine the intensity of the amortiguamiento are the electrical conductivity and the magnetic permeability of the material. The depth associated to the signal for a determinate bandwidth can estimate from the expressesion 7.
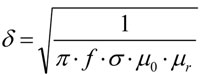
Where ƒ is the frequency of the signal of noise BN, σ the electrical conductivity of the material, μr the relative magnetic permeability of the material and μ0 the magnetic permeability of the empty.
The values of BN proportionate by the team and showed in the figures 6 and 8 correspond to the effective value of the signal (half quadratic value or RMS) for the bandwidth of 70-200 kHz. Taking into account that the conductivity of the martensita for the steel AISI 1045 is roughly 0,41•107Ω-1m-1 and the relative permeability 75 [20], the maximum depth associated to the signal analysed corresponds to 110 μm. This depth is adapted to compare temperate layers with inferior or next depth to this value. Therefore, has to adapt this value to the depth of layer estimated, since in contrary case is not possible his prediction by means of noise BN.
4. Conclusions
In this work has presented a model that allows to predict the depth of layer tempered in the process of grind-hardnening. The analysis of the state of grind it after the rectified suggests that the mechanisms of start are distinct in each zone of this. In front of the difficulty to enter several sources of heat in each zone of grind it in the model, has considered a width of grind engaged in the effective cut (bseff) on which has had an only source of heat. For the essays realizar, the consideration of a width of grind effective of 2/3 of the width of grind total together with the adjust of the fraction of heat evacuated to the piece allows to predict properly the depth of temperate layer.
On the other hand, has observed that exists a correlation between the half quadratic value (RMS) of the signal of noise Barkhausen and the depth of temperate layer in the piece.
Therefore, could use this method like a no destructive essay for approximate prediction of the temperate layer in the piece.
5. Gratitudes
Appreciates the contribution of the Ministry of Science and Innovation (MICINN) by the subvention of the Project of Investigation ‘Integration of numerical models and experimental technicians for the increase of the value added in the rectified of components of precision' of code DPI-2010-21652-C02-00.
Bibliography
[1] Brinksmeier And, Brockhoff T. Randschicht-Wärmebehandlung durch Schleifen. HTM J. Heat Treatm. Mat., Vol. 49, No. 5, 1994, pag. 327-330.
[2] And. Brinksmeier and T. Brockhoff, ‘Utilization of Grinding Heat ace to New Heat Treatment Process', CIRP Annals - Manufacturing Technology, vol. 45, no. 1, pag. 283-286, 1996.
[3] And. Brinksmeier and T. Brockhoff, ‘Advanced grinding processes for surface strengthening of structural parts', Machining Science and Technology, vol. 1, no. 2, pag. 299- 309, 1997.
[4] M. F. Zäh, And. Brinksmeier, C. Heinzel, J.-W. Huntemann, and T. Föckerer, ‘Experimental and numerical identification of process parameters of grind-hardening and resulting part distortions', Production Engineering, vol. 3, no. 3, pag. 271-279, 2009.
[5] T. Nguyen and L. C. Zhang, ‘Grinding–hardening using dry air and liquid nitrogen: Prediction and verification of temperature fields and hardened layer thickness', International Journal of Machine Tools and Manufacture, vol. 50, no. 10, pag. 901-910, 2010.
[6] T. Foeckerer, M. F. Zaeh, and Or. B. Zhang, ‘To three-dimensional analytical model to predict the thermo-metallurgical effects within the surface layer during grinding and grindhardening', International Journal of Heat and Mass Transfer, vol. 56, pag. 223-237, 2013.
[7] V. S. K. Venkatachalapathy and B. Rajmohan, ‘Experimental Studies on the Grind-Hardening Effect in Cylindrical Grinding', Materials and Manufacturing Processes, vol. 18, no. 2, pag. 245-259, 2003. 9
[8] T. Nguyen and L. C. Zhang, ‘Realisation of grinding-hardening in workpieces of curved surfaces—Part 1: Plunge cylindrical grinding', International Journal of Machine Tools and Manufacture, pag. 1-11, 2010.
[9] G. Totten, M. Howes And T. Inoue. Handbook of Residual Stress and Deformation of Steel. 1ª ed. ASM International, 2002.
[10] D. Jiles, ‘Review of magnetic methods for nondestructive evaluation', NDT & And International, vol. 21, no. 5, pag. 311-319, 1988.
[11] Or. Kypris, I. C. Nlebedim, and D. C. Jiles, ‘Mapping Stress ace to Function of Depth at the Surface of Steel Structures Using to Frequency Dependent Magnetic Barkhausen Noise Technique', IEEE Transactions on Magnetics, vol. 48, no. 11, pag. 4428-4431, 2012.
[12] N. S. Prabhu, J. Joseyphus, T. S. N. Sankaranarayanan, B. R. Kumar, to. Mitre, and to. K. Panda, ‘Residual Stress Analysis in Surface Mechanical Attrition Treated (SMAT) Ironinging and Steel Component Materials by Magnetic Barkhausen Emission Technique', IEEE Transactions on Magnetics, vol. 48, no. 12, pag. 4713-4717, 2012.
[13] L. Mierczak, D. C. Jiles, and G. Fantoni, ‘To New Method for Evaluation of Mechanical Stress Using the Reciprocal Amplitude of Magnetic Barkhausen Noise', IEEE Transactions on Magnetics, vol. 47, no. 2, pag. 459-465, 2011.
[14] P. Zerovnik, J. Grum, and G. Zerovnik, ‘Determination of Hardness and Residual- Stress Variations in Hardened Surface Layers With Magnetic Barkhausen Noise', IEEE Transactions on Magnetics, vol. 46, no. 3, pag. 899-904, 2010.
[15] W.B. Rowe, M.N. Morgan, H. S. Qi, H. W. Zheng. ‘The effect of deformation on the contact area in grinding'. Annals of the CIRP, 42, pag. 409–412,1993.
[16] AM. Or. Mohamed, To. Warketin, R. Bauer. ‘Use of surface roughness measurements to improve the estimation of the heat partition in grinding'. Journal of Materials Processing Technology, 211, pag. 566-572, 2011.
[17] Z. B. Hou, R Komanduri. ‘On the mechanics of the grinding process, PartII-thermal sensors sensors analysis of fine grinding'. Int. Journal of Machine Tools & Manufacture, vol. 44, pag. 247- 270, 2004.
[18] W. Brian Rowe. ‘thermal sensors sensors analysis of high efficiency deep grinding'. Int. Journal of Machine Tools and Manufacture, vol. 4, 1/1-19, 2001.
[19] S. Malkin and C. Guo, ‘thermal sensors sensors Analysis of Grinding', Annals of the CIRP, vol. 56, no. 2, pag. 760-782, 2007.
[20] S. Kahrobaee and M. Kashefi, ‘Hardness profile plotting using multi-frequency multioutput electromagnetic sensor', NDT & And International, vol. 44, no. 4, pag. 335-338, Jul.