Effect of the thermal sensors contribution in the mechanical properties of the alloy of the aluminium
Dr. Alberto Echeverría: technological director Lortek-IK4.
Msc. Egoitz Aldanondo: Engineer of investigation Lortek-IK428/12/2012
The aim of the present work was to study the effect of the thermal sensors contribution in the mechanical properties of the welding FSW in an alloy of aluminium AW6082 of 5 mm of thickness. It realised the characterisation microestructural of the unions soldered, realised profiles of microdureza and evaluated the mechanical properties through essays of traction and fatigue. They obtained free unions of defects with good mechanical properties for the two configurations analysed.
Introduction
The process of welding by friction by means of agitation or beaten (FSW, Friction Stir Welding) was invented in 1991 and patented by the centre The Welding Institute (United Kingdom) [1]. It treats of a process of union in solid state and without contribution of material [2, 3], whose excellent results of quality and big rank of application in diverse materials, even in some considered up to now insoldables, turn it into a very attractor trucks technology for numerous and important industrial states. This process has been able to delete defects in alloys of aluminium hardly soldables by fusion (2xxx and 7xxx) [4-6] such as agrietamiento or microporosidad and also has applied successfully in other alloys of aluminium endurecibles by precipitation (6xxx), in other materials as they can be steels to the carbon, alloys of copper, titanium, magnesium, etc. [7-14] and lately is using to join material of different nature or material disimilares [15, 16].
The conventional processes of welding by fusion, such as MIG/MAG, TIG, soldeo laser or by do of electrons present diverse types of characteristic problems of the process: big quantity of heat generated by the arch; need of employment of fundentes; incompatibility (in occasions) of the mechanical properties of the metal of contribution and the basic metal. These problems drive to the apparition of different types of defects such as, high distortions of the elements soldered, inclusion of slags in the union soldered, excessive salpicaduras during the process and excessive porosidad.
The technician centred initially in alloys of aluminium but already has extended to other materials like the steels to the carbon for distinct applications in the sectors of automotive sector, railway industry and nautics construction, the alloys of titanium (aeronautical sector component manufacturing sector component manufacturing sector), the alloys of magnesium (sector of automotive sector), other materials (copper, lead, nickel, etc.). In the International Symposium of FSW and in the annual meeting of the Commission III of the International Institute of Welding (IIW), have identified the areas of work in which it has to deepen so that this technology can disseminate and apply of extensive way in the sectors of the aerospace industries, aeronautical sector component manufacturing sector component manufacturing, automotive sector or of defence. The thematic keys that require an effort of investigation so that it favour of this technology are: Fatigue properties, True lightweight construction, Coatings of the FSW tools, Surface contamination of the workpieces, Modelling, Tolerances, FSW specific design, Cost factors and models, Normalisation (Quality standards), Development of NDT techniques, Microstructural Development and Life in service (mechanics and corrosion).
Taking into account these guidelines opted for realising the project of investigation ‘Optimisation of processes of union by means of Friction stir welding for elements of high exigencia subjected to fatigue in the transport (composolda V2)' with file Number IMDEEA/2011/168 (subsidised by the Institute of the Small and medium enterprise, Impiva), dependent to his time of the Conselleria of Company, Universitat i Science of the Valencian Community), in collaboration with the Centre of Investigation in Technologies of Union (Lortek-IK4), with which pretended study the welding FSW in the alloy of aluminium AW6082-T6 and analyse the mechanisms that control the mechanical properties (hardness, traction, fatigue), the corrosion, the characteristic microestructurales of the unions by FSW and his correlation with the parameters of soldeo.
Regarding the mechanical properties of alloys of aluminium soldered by FSW, Von the Strombeck et al. [17] and Mishra et al. [18], they realised studies of FSW in an alloy 7075 to determine the properties to traction in distinct zones of the union using miniprobetas of traction. It obtained an almost constant resistance in the zone nugget, the effort of fluencia reached an equivalent value to 80% of the basic material, the resistance last this near of 100% and the ductility improves significantly. An effort last, relatively high, and a high ductility in this zone attribute to the microstructure of fine grain generated. On the other hand, near of the region of transition of nugget/ZACM, the resistance remains the same to the one of the zone of the nugget, but the ductility begins to direct to the one of the basic metal. The decrease in ductility compared with the one of the centre of the nugget can put in correlation to the fact that the ZACM retains the structure deformed.
Elangovan Et al. [19], it realised an approximation by means of a mathematical model to predict the values of resistance to traction in function of the variables of the process FSW (profile, speeds of advance and rotation, axial strength applied by part of the tool) in boards to tope in alloys of aluminium AA6061. The maximum resistance attained with a suitable combination of the variables, given a speed of rotation of 1.200 rpm and a speed of advance of 1,25 mm/s, realising proofs with different geometries of pin, where the geometry of pin cylindrical threaded was the one who better presented a mechanical behaviour.
James et al [20], realised studies to predict the properties of fatigue of unions type FSW in alloys 5083-H321. It evaluated the influence of the speed of advance, the population of defects and the curve S-N of fatigue. The work suggests that the main variables that affect to the life to fatigue are the residual tensions, the relation microstructure/hardness and the presence of small defects.
In another very interesting work related with the behaviour to fatigue and fracture, Lockyer [21] analysed resulted of essays of fatigue S-N in samples with and without defects. The main conclusion is that the unions by FSW have static resistance and inferior hardness that the one of the basic material but resistance to fracture or tear upper. Unlike the conventional weldings, the essays of fatigue indicate properties of similar fatigue to the of the basic material if there is absence of defects.
Ghidini And Dalle Donne [22] studied the effect of the residual tensions in the speed of growth of cracks by fatigue in unions FSW. They explained like simplistic analyses of essays obtained to low relations of tension, R, indicate properties of better fatigue that the basic material if the effect of the residual tensions does not take into account. They have developed a technician simplified of measure of residual tensions, ‘cut compliance', that shows that the speed of growth of cracks in FSW are inside the band of dispersion of the basic material if it uses the strength impulsora effective, in which they include the residual tensions.
Experimental development
In the first place looked for an alloy of aluminium envejecible (by the mechanical characteristics), of easy conformed plastic (extrusion, laminado) and of good behaviour in front of the corrosion and fatigue. With these characteristic find us with the family of alloys AA 6XXX of which stand out the 6063, 6061 and 6082 all they in state of thermal sensors treatment T6. The selected for this project was the AW6082-T6 of 5 mm of thickness with the chemical composition that shows in the table 1.

The centre of investigation in technologies of union, Lortek-IK4, realised two types of weldings FSW with the following parameters of soldeo:
• 10-1500
- Speed of rotation: 1.500 rpm
- Speed of advance: 10 ipm = 254 mm/min
- Relation of soldeo: 0,17 mm/revolution (high thermal sensors contribution)
- axial Strength: 1.350 lbf = 6 kN
- Angle of inclination: 1,5º
• 20-900
- Speed of rotation: 900 rpm
- Speed of advance: 20 ipm = 508 mm/min
- Relation of soldeo: 0,56 mm/revolution (low thermal sensors contribution)
- axial Strength: 2.700 lbf = 12 kN
- Angle of inclination: 1,5º
The tool used observes in the figure 1 and has the following geometrical characteristics:
- Diameter shoulder: 15 mm
- Diameter of the pin: 4 mm
- Length of the pin: 4,8 mm
- Type of pin: threaded
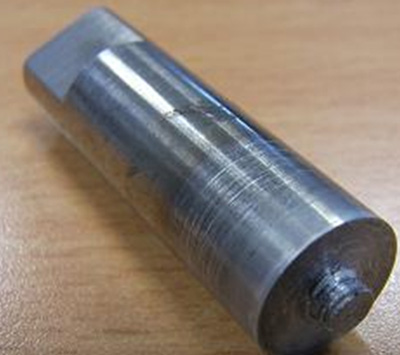
Realised an analysis microestructural of the distinct samples soldered, previously prepared according to the methods described in the norm ASTM And3 – 95: cutting of the probeta, filling of the sample, desbaste manual, manual polishing and attack with reactive agent. To obtain the microstructure used the reactive of attack to colour Weck's (100 ml H2Or, 4 g KMnO4, 1 g NaOH) to temperature acclimatise and with a time of immersion of roughly 20 seconds. For the characterisation of the unions soldered employed the technician of microscopía optical (OM). For the mechanical characterisation realised essays of traction in accordance with the norm ASTM And8M-04, essays of fatigue according to the norm ASTM And466-02 (for the design of the probeta of essay) and ASTM And739-91 (for the analysis of the data) with a relation of load R=0,1, a function loads-sinusoidal time (constant amplitude) and a frequency of swing of 7 Hz. The real area of interest of the weldings was the infinite life (>106 cycles) but the alloys of aluminium, generally, do not show a limit of asymptotic fatigue [23]. Finally they realised swept of microdureza as it JOINS-IN ISO 9015-2:2011.
Results and discussion
1. Characterisation microestructural
In the figure 2 present the macrografías, in state of polishing, of the weldings realised where do not reveal any type of fissures or pores from the lines of union that indicate some fault of penetration by part of the pin, by what treats of healthy weldings. Neither it observes the presence of typical defects of the welding FSW known eat: tunnel defect, pin hole, kissing bond, worm hole or piping defect [24].
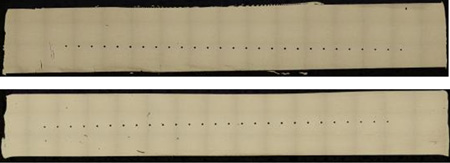
In the figures 3 and 4 present the micrografías in state of attack, obtained through microscopía optical, for the sample 10-1500 (high thermal sensors contribution) and 20-900 (low thermal sensors contribution), respectively. The parameters microestructurales to that refers this study, correspond to the different zones found in the welding by friction-agitation: basic metal (MB), zone affected térmicamente (ZAC), zone affected termomecánicamente (ZACM), zone nugget (ZN).
In the MB the grains are lengthened because of his process of manufacture (laminación) and in the ZN are equiaxiales and fine. This refinement is resulted of the recristalización dynamic, that is to say, an action combined of high speed of deformation and high temperature. Said structure recristalizada characterises by a very low level of residual tensions, excellent ductility and upper mechanical properties to the ones of the ZAC [25].
To obtain the size of grain of the ZN applied the empirical relation obtained by S. Rajakumar, et. To the [24], where relate the resistance to traction with the size of grain of the ZN from experimental results in an alloy AA6061-T6 soldered by FSW:
ợb = 252.4 – 1.339G (1)
Where:
ợb: Resistance to traction [MPa]
G: size of grain of the ZN [<#comment>µm]
It obtained a size of grain of the ZN of 24.94 <#comment>µm for the configuration with high thermal sensors contribution and of 17.47 <#comment>µm for the configuration of low thermal sensors contribution, what involves that to measure that increases the size of the grain, the resistance to the traction diminishes.
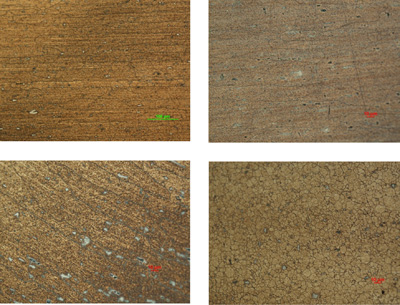
The zone TMAZ has the grains deformed, lengthened and curvados because of the deformation to which were subjected (figures 3b and 4b) and in occasions some recristalización local. The microstructure of the ZAC is similar to the one of the MB, the grains are a bit bigger like result of the exhibition to the heat of the welding (figures 3b and 4b).
They observe precipitated that vary in size and morphology along the different zones FSW. In plates soldered by FSW of AA6082-T6, reported that the phase <#comment>β” finds disperses homogéneamente in the basic material, but dissolves in the ZN, the ZATM and in the main part of the ZAC [26, 27]. During the cooling of the welding, the precipitation of particles, that are less effective in the hardening, like the phase <#comment>β', carries out quickly in the region ZAC of minimum hardness. In the ZN, with high temperatures hammer, all the precipitated <#comment>β” dissolve, but the precipitation <#comment>β' does not take place because of the speed of cooling. In the regions where produces the dissolution, a natural aging can cause some precipitations of the zones GP [28].
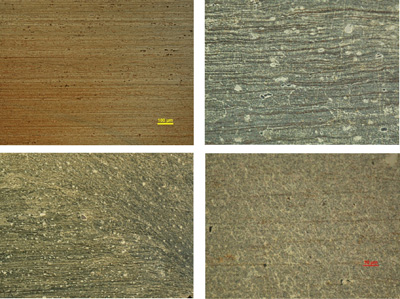
Appears 4. Images of microscopía optical of the sample 20-900 attacked: to) MB 100X, b) ZAC 500X, c) ZACM 100X, d) ZN 1000X.
i. Essays of microdureza
In the profiles of microdureza obtained for the two configurations the hardness diminishes from the basic metal to the centre of the welding, arrives to a minimum value in the ZAC, afterwards increases in the ZN remaining finally with a value underneath of the basic material. In the figure 5 observes that the hardness increases with the decrease of the thermal sensors contribution, possibly because it dissolves less quantity of precipitated (also generates a size of grain smaller). In alloys toughened by aging, the level of hardness tends to diminish in the ZAC, what indicates that the thermal sensors cycle during the process of welding has a significant influence, already was by on-aging or when diminishing the density of dislocaciones, probably by both factors in alloys entirely aged. Whereas the endurecimiento by work is the dominant effect near of the ZN. Also it is possible that can reach a sufficiently high temperature local areas that allow the partial dissolution of precipitated, especially in the ZATM.
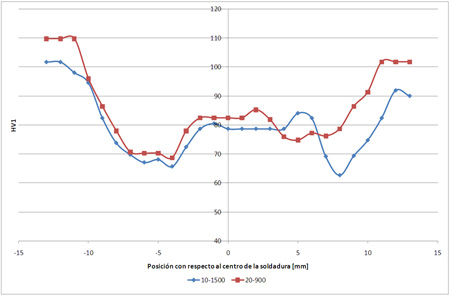
ii. Essay of traction
In the table 2 present the results obtained of the probetas subjected to the essay of traction. The parameters of process with strong influence in the mechanical properties are the speed of rotation of the tool and the speed of advance of the tool, which define the specific heat supplied to the welding (thermal sensors contribution). In the two cases the samples presented the failure in the ZAC by the side of advance, similar to the reported in [25].
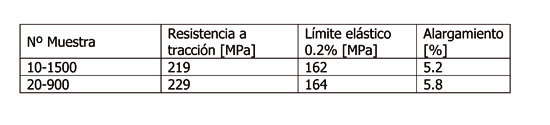
Can observe that diminishing the speed of rotation (1500 to 900 RPM) and increased the speed of trip (of 254 to 508 mm/min) the mechanical resistance of the union increases. This can attribute to the decrease of the thermal sensors contribution and the ablandamiento limited relative of the material in the ZAC [26].
iii. Essays of fatigue
The figure 6 sample the graphic of fatigue obtained for the two conditions of FSW, where observes that the configuration with parameters of processed FSW of high thermal sensors contribution has a greater resistance to fatigue, besides show a classical behaviour that reveals a tendency of the increase of resistance to the fatigue to measure that diminishes the amplitude of the tension cíclica.
The results of the essays show that the behaviour to fatigue of the unions FSW diminishes with a speed of greater and lower advance speed of rotation, that is to say, a low thermal sensors contribution. Cavaliere And Panella [30] also communicated that the resistance to fatigue of the most common alloys diminishes to measure that the relation speed of advance/speed of rotation is greater. On the other hand, Ericsson and Sandström [31] reported that with a speed of low advance obtained the best results to fatigue in an alloy of aluminium 6082 soldered by FSW due to the fact that the quantity of heat supplied to the region of the welding was greater and therefore the flow of metal and the creation of the welding could have been more effective. This could explain the behaviour to fatigue relatively high of the welding FSW with a high thermal sensors contribution (speed advance low and speed of high rotation).
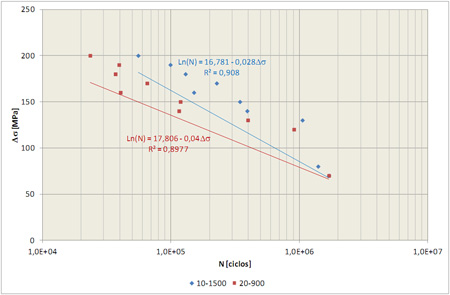
iv. Analysis fractográfico of the essays of fatigue
The figure 7 sample the fractures obtained in the essay of fatigue for the condition with high thermal sensors contribution. The images have ordered of minor to greater tension applied. In the two first can observe how the initiation of crack gives in a small zone of the edge and this goes extending by all the surface, doing it in elder measured what lower is the load, until it produces the break. In the two last images by the contrary observes how initiate cracks around big part of the section growing these very shortly before that produce the break. It observes the presence of a growth of stable crack and an unstable growth final. What elder was the load applied more violent is this unstable growth.
The fractures of fatigue of the unions FSW produced between the TMAZ and the ZN by the side of shrinking. For weldings FSW, the fracture during the load of fatigue propagates in the root of the weldings because of the low entrance of heat or an orientation of the unsuitable tool and defects of the type ‘kissing bond' in the root of the side of shrinking [32].
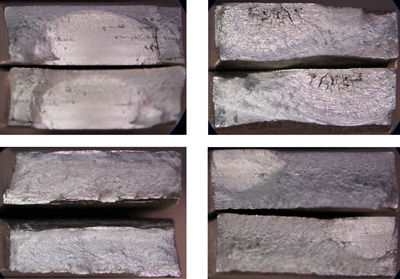
Appears 7. Macrografías Of the breaks of the essay of fatigue for the sample 10-1500: to) ∆ợ =180 MPa, b) ∆ợ=170 MPa, c) ∆ợ =160 MPa, d) ∆ợ =150 Mpa.
For the same speed of advance to a greater speed of rotation, the characteristic of ductile fracture is more evident [32].
Conclusions
The mechanical properties of the alloy of aluminium AW6082-T6 soldered by FSW change with the parameters of process. The resistance to traction is directly proportional to the relation of soldeo, that is to say, with a low thermal sensors contribution have a better resistance to traction, however, for the resistance to fatigue the high thermal sensors contribution presents better behaviour.
This improvement in the life of fatigue of the FSW with high thermal sensors contribution can be associated with the greater quantity of heat supplied to the welding by unit of length.
Gratitudes
The results presented in this article do part of the development of the project IMDEEA/2011/168 (subsidised by the Institute of the Small and medium enterprise, IMPIVA), dependent to his time of the Conselleria D'Company, Universitat I Science of the Valencian Community), in collaboration with the Centre of Investigation in Technologies of Union (LORTEK-ik4).
References
[1] W.M. Thomas, And.D. Nicholas, J.D. Needham, M.G. Murch, P. Templesmith and C.J. Daws: Friction stir butt welding, International Patent Appl. N° 9125978.8, December 1991, Or.S. Patent N° 5,460,317.
[2] R.S. Mishra, Z.And. Ma. Friction Stir Welding and Processing. Materials Science and Engineering R: Reports, 50 (1-2), 2005, p. 1-78.
[3] R.S. Mishra, M.W. Mahoney. Introduction in Friction Stir Welding and Processing. (R.S. Mishra, M.W. Mahoney, Ed). ASM International, 2007, p. 1-5.
[4] K.V. Jata. Friction Stir Welding of High Strength Aluminum alloys, Materials Science Forum, 331(II), 2000, p 1701-1712.
[5] To.P. Reynolds, W.D. Lockwood, T.Or. Seidel. Processing-Property Correlation in Friction Stir Welds. Materials Science Forum, 331(II), 2000, p 1719-1724.
[6] And. Aldanondo, To.To.M gives Silva, P.Alvarez, To. Lizarralde, To. Echeverria. Dissimilar Friction Stir Welding of AA2024-T3 and AA7075-T6 Aluminium Alloys. Proceedings of Friction Stir Welding and Processing V – TMS2009 Annual Meeting, 15-19 February 2009, San Francisco, EE UU.
[7] M. Cabibbo, H.J. McQueen, And. Evangelista, S. Spigarelli, M. I gave Paola, To. Falchero. Microstructure and Mechanical Property Studies of AA6056 Friction Stir Welded Plates. Materials Science and Engineering To, 460-461, 2007, p. 86-94.
[8] To. Denquin, D. Alleaux, M.H. Campagnac, G. Lapasset, Microstructural and mechanical evolutions within friction stir welds of precipitation hardened aluminium alloys, Materials Science Forum, 426-432, 2003, p 2921-2926.
[9] Woong-Seong Chang, Yun-Mo Yeon, Joint properties and thermal sensors behaviors of friction stir welded age hardenable 6061 To the alloy, Materials Science Forum, 426-432, 2003, p 2953-2958.
[10] C.D. Sorensen, T.W. Nelson. “Friction Stir Welding of Ferrous and Nickel Alloys”. In: Friction Stir Welding and Processing. (R.S. Mishra, M.W. Mahoney, Ed). ASM International, 2007, p. 111-121.
[11] T.J. Lienert. “Microstructure and Mechanical Properties of Friction Stir Welded Titanium Alloys”. In: Friction Stir Welding and Processing. (R.S. Mishra, M.W. Mahoney, Ed). ASM International, 2007, p. 123-154.
[12] T.R. McNelley, K. Oh-Ishi, To.P. Zhilyaev. “Microstructure and Properties of Copper Alloys after Friction Stir Welding/Processing”. In: Friction Stir Welding and Processing. (R.S. Mishra, M.W. Mahoney, Ed). ASM International, 2007, p. 155-173.
[13] R. Zettler, J.F. Two Saints, To. White, To.A.m. it gives Silva. 7th International Conference on Trends in Welding Research, 16-20 May 2005, Pine Mountain, USA
[14] R. Zettler, To.A.m. it gives Silva, S. Rodrigues, To. White, J.F. Two Saints. “Dissimilar To the to Mg Alloy Friction Stir Welds”. Advanced Engineering Materials 8, 2006, p. 415-421.
[15] V. Firouzdor, S. Kou. To the-to-Mg Friction Stir Welding: Effect of Positions of To the and Mg with Respect to the Welding Tool. Supplement to the Welding Journal, 2009, 123-224.
[16] YAN Yong, ZHANG Gives-tong, QIU Cheng, ZHANG Wen. Dissimilar friction stir welding between 5052 aluminum alloy and AZ31 magnesium alloy. Trans. Nonferrous Met. Soc. China, Vol. 20, 2010, 619-623
[17] To. von Strombeck, J.F. Two Saints, F. Torster, P. Laureano, M. Koc. Proceedings of the first international symposium on friction stir welding, thousand Oaks. 1999.
[18] R. S. Mishra, S. R. Sharma, N.To. Mara, M.W. Mahoney. Proceedings of the international conference on jointing of advanced and specialty materials III. ASM international, 2000, p. 157.
[19] K. Elangovan, V. Balasubramanian, S. Babu. Predicting tensile strength of friction stir welded AA6061 aluminium alloy joints by to mathematical model. Materials and Design 30 (2008). p. 188-193.
[20] M.N. James, P.J. Webster, D.J. Hughes, D.G. Hattingh, G. Bradley, G. Mills. “Residual Stress Field in Friction Stir Welded Marine Grade Aluminium Alloy”. Internal Report. February 2002.
[21] S. Lockyer. Fracture and Fatigue Performance of Friction Stir Welds. Dissemination Report EUREKA project EUROSTIR.
[22] T. Ghidini, C. Dalle Donne. Fatigue crack propagation assessment based on Residual stresses obtained through cut-compliance technique. Fatigue and Fracture of Engineering Materials and Structure 30(3), 2006, p. 214-222.
[23] ZHOU Car-zhi, YANG Xin-qi, LUAN Guo-hong. Comparative study on fatigue properties of friction stir and MIG-Presses welded joints in 5083 To the-Mg alloy. Trans Nonferrous Met. Soc. China, Vol. 15, Number 4, 2005, 789-794.
[24] S. Rajakumar, C. Muralidharan, V. Balasubramanian. Establishing empirical relationships to predict grain size and tensile strength of friction stir welded AA6061-T6 aluminium alloy joints. Trans Nonferrous Met. Soc. China, Vol. 20, 2010, 1863-1872.
[25] J. Adamowski, M. Szkodo. Friction Stir Welds (FSW) of aluminium alloy AW6082-T6. Journal of Achievements in Materials and Manufacturing Engineering, Vol. 20, 2007, 403-406.
[26] J. Adamowski, C. Gambaro, And. Lertora, M. Put you, M. Szkodo. Analysis of FSW welds made of aluminium alloy AW6082-T6. Journal of Achievements in Materials and Manufacturing Engineering, Vol. 28, 2007, 453-460.
[26] Peel, M.J., Steuwer, To., Withers, P.J. Dissimilar Friction Stir Welds in AA5083-AA6082. Part II: Process Parameter Effects on Microstructure. Met. and Mat. Trans. To, Vol 37, 2006, 2195-2206.
[27] K. Mroczka, To. Pietras. FSW characterization of 6082 aluminium alloys sheets. You file of Materials Science and Engineering, Vol. 40, 2009, 104-109.
[28] D. Carron, P. Bastid, And. Yin, R.G. Faulkner. Modelling of precipitation during friction stir welding of an To the-Mg-If alloy. Technische Mechanik, Vol. 30, 2010, 29- 44.
[29] Svennson, L.And., Karlsson, L., Larsson, H., Karlsson B., Fazzini, M., Karlsson, J. Microstructure and mechanical properties of friction stir welded aluminium alloys with special reference to AA 5083 and AA 6082. Sci. Tech. Weld. Join, Vol. 5, 2000, 285-296.
[30] Cavaliere P., Panella F. Effect of Tool Position on the Fatigue Properties of Dissimilar 2024-7075 Sheets Joined by Friction Stir Welding. Journal of Materials Processing Technology, Vol. 206, 2008, 249 – 255.
[31] Ericsson M., Sandström R. Influence of Welding Speed on the Fatigue of Friction Stir Welds, and Comparison with MIG and TIG. International Journal of Fatigue, Vol. 25, 2003, 1379 – 1387.
[32] Hakan To., Ali B., M. Tahir And., Kurtuluş And. Influence of Welding Parameters on the Fatigue Behaviours of Friction Stir Welds of 3003-Or Aluminum Alloys. Materials Science (Medžiagotyra), Vol. 16, No. 4, 2010, 311-319.