El ajuste manual y la programación CNC, una tortura innecesaria para los operarios
14 de julio de 2009
“Alp debe ser un centro de conocimiento técnico y la clave para conseguirlo es la comunicación y las relaciones entre mis empleados” – comenta Şenay İdil, director general, que ha logrado una perfecta cultura entre su personal sobre cómo controlar los procesos productivos. Al hablar con los ingenieros queda claro que comparten el mismo entusiasmo por lograr los mejores resultados – “Analizamos el tiempo de ciclo de todo el proceso productivo y fuimos capaces de reducir los tiempos de ajuste en algunos casos hasta el 50%” dice Cenk Akin, responsable de departamento de ingeniería.“El software Productivity+ y las sondas de inspección de pieza de Renishaw han hecho que esto sea posible”. Los beneficios no solo incluyen el ahorro en tiempo y costes; podemos confiar completamente en el proceso productivo, puesto que hemos eliminado la posibilidad del error humano. La repetibilidad del proceso ha mejorado – hemos alcanzado un mayor nivel de calidad usando sondas con una repetibilidad menor a una micra”.
La ingeniería del proceso productivo
Cuando se inicia la fabricación de una nueva pieza un ingeniero de procesos es asignado a dicha pieza y es responsable de todos los procesos del ciclo de producción. El cliente envía el fichero CAD al ingeniero y se decide un proceso de mecanizado, incluyendo la selección de las herramientas de mecanizado, usando un sistema CAM de Unigraphics. El programa CNC que el CAM genera se carga en el software Productivity+ de Renishaw, donde el ingeniero añade los ciclos de inspección. Este programa final se envía a la máquina correspondiente mediante un sistema DNC y se mecaniza una pieza de prueba antes de que comience su fabricación en serie.
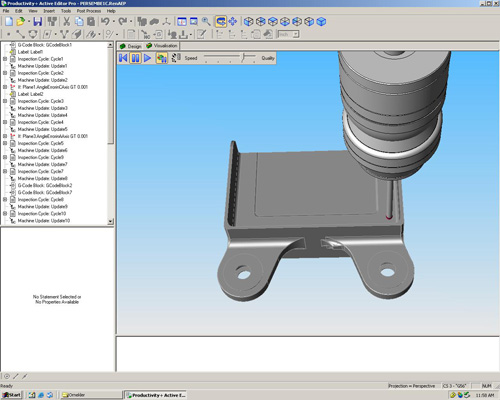
Productivity+ reduce tiempos y costes
El software Productivity+ fue adquirido en julio del 2007 con el objetivo de reducir el tiempo de desarrollo del proceso – el entorno de trabajo de Alp está altamente automatizado por lo que no se consideraba aceptable programar manualmente las rutinas de inspección. Productivity+ está basado en un entorno gráfico que permite una programación “amigable” y de fácil manejo. Los ingenieros de Alp simplemente usan del modelo de CAD las características a controlar, o definen los parámetros desde las ventanas de diálogo para definir el programa de inspección. Cuando se ha completado, se selecciona el postprocesador deseado y el programa CNC se genera automáticamente, preparado para ser enviado directamente a la máquina.
Para una mayor seguridad, las rutinas de inspección se pueden simular gráficamente en el software, corrigiendo errores antes de que el programa llegue a la máquina. Cenk Akin, Responsable de Departamento de Ingeniería, explica los factores clave de beneficio para Alp, “Productivity+ facilita el chequeo de las rutinas de inspección antes de enviarlas a la máquina. Si se está usando la máquina para chequear procesos en vez de para producir piezas estamos perdiendo dinero”.
Sondas para ajuste de pieza y comprobación en ciclo
Pese a que Productivity+ ha sido adquirido no hace mucho, Alp lleva usando las sondas de inspección de pieza de Renishaw desde hace años – “de hecho, todas las máquinas nuevas se piden desde fábrica con dichas sondas”. Los ingenieros pueden recordar las dificultades que se encontraban antes de empezar a usar las sondas de Renishaw en Alp- “El operario necesitaba alinear manualmente la pieza sobre la mesa, o necesitábamos un utillaje especial de gran coste para cada una de las referencias que mecanizábamos. Era necesario cambiar este método de ajuste manual y pasar a un método más automatizado y fiable - era una tortura para los operarios.
Ahora los operarios usan sistemas sencillos de amarre y programamos la máquina para que use la sonda y calcule el cero pieza exacta. La sonda se utiliza también como control de proceso, por ejemplo, cada pieza es comprobada antes del mecanizado de acabado y una vez finalizado éste se inspeccionan los puntos críticos de la pieza en la propia máquina. El tiempo de ciclo, al eliminar el ajuste manual y el tiempo de inspección en una máquina tridimensional, se ha reducido hasta en un 50%.
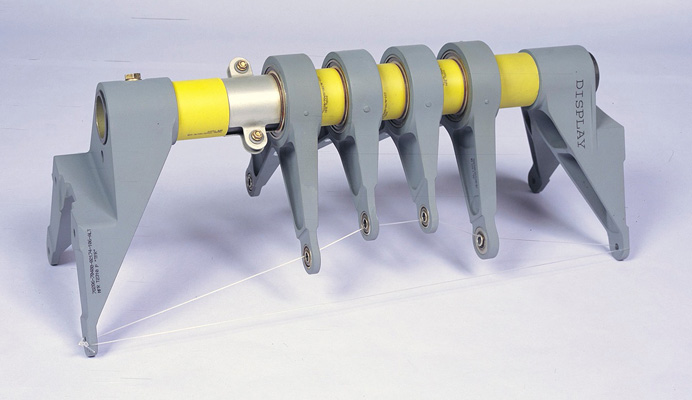
Otra característica importante para nosotros es que usando las rutinas de inspección de la sonda podemos actualizar automáticamente el cero pieza de la máquina. Solíamos confiar en el buen hacer del operario, quien podía confundirse fácilmente – hemos evitado muchos rechazos gracias a esto. La precisión también ha mejorado – la sonda es calibrada regularmente y normalmente alcanzamos repetibilidades de menos de una micra en las mediciones”.
El objetivo de reducir en Alp los tiempos de ajuste es particularmente importante, puesto que las piezas mecanizadas tienen muchas variaciones y se necesita una gran flexibilidad. Algunas series de piezas pueden estar mecanizándose durante un año, pero algunas máquinas cambian las series 2 ó 3 veces por día con sólo unas pocas piezas por cada serie. Es por eso particularmente llamativo que Alp esté cerca de conseguir tiempos de ajuste cercanos a cero, usando sistemas de cambio de palé para permitir a los operarios cargar las piezas mientras la pieza previa está siendo mecanizada, y mediante las sondas de inspección de pieza para calcular el cero pieza en segundos.
Filosofía e historia de Alp Aviation
Senay Idil, director general de Alp, explica cómo funciona la compañía. “Nosotros no realizamos mecanizado en general, ni fabricamos piezas sencillas del sector aeroespacial. Seleccionamos cuidadosamente a nuestros clientes con la idea de establecer relaciones duraderas. Esto es debido a que creemos en realizar un trabajo que sabemos continuará en el tiempo, con lo que podemos establecer un plan estratégico de crecimiento en el momento de la firma del contrato.
Nuestra idea de establecer relaciones a largo plazo se refiere tanto a clientes como a suministradores. Las tecnologías de las que estamos hablando, sistemas de inspección de pieza de Renishaw y el software Productivity+, son críticas para, con una inversión relativamente baja, hacer funcionar las máquinas de la forma más eficiente posible. En el año 2006 invertimos 12,5 millones de dólares en máquinas y otros sistemas después de un periodo de cuidadosa reflexión, pero tenía claro que quería que cada máquina tuviera una sonda de inspección de pieza.
La calidad es un elemento clave en la fabricación de piezas para el sector aeroespacial, con un control dimensional 'in-process' definido por el ingeniero de producción, pero con una comprobación independiente del 100% de las características relevantes de la pieza final”.
Cabe recordar que Alp comenzó su andadura en Eskisehir, Turquía, en el año 1998 como una empresa independiente en la misma época en que Sikorski estaba buscando suministradores. Alp empezó fabricando piezas para ellos desde entonces y, en junio de 1999, Sikorski - "impresionada con el servicio ofrecido por Alp"- compró el 50% de la empresa. Todas las decisiones se toman en conjunto con Sikorski y sus empleados están trabajando permanentemente en Alp.
La mayoría de los componentes fabricados para Sikorski tienen como destino EE UU, aunque algunas piezas son enviadas a la República Checa o a Ankara en Turquía, donde los componentes son añadidos a los helicópteros en el montaje final.
Otro de los clientes de Alp es Pratt and Whitney, para quien se fabrican elementos de la parte trasera del fuselaje del caza F135 Joint Strike Fighter. También se fabrican trenes de aterrizaje para Goodrich. El trabajo para esta empresa es un claro ejemplo de cómo ha sido introducido y comprobado un nuevo componente de un modo completamente automático. Actualmente Alp está buscando más clientes en el sector civil, en concreto se está trabajando junto con la empresa turca TAI para intentar conseguir fabricar componentes para el Boeing 787 y el Airbus 380.
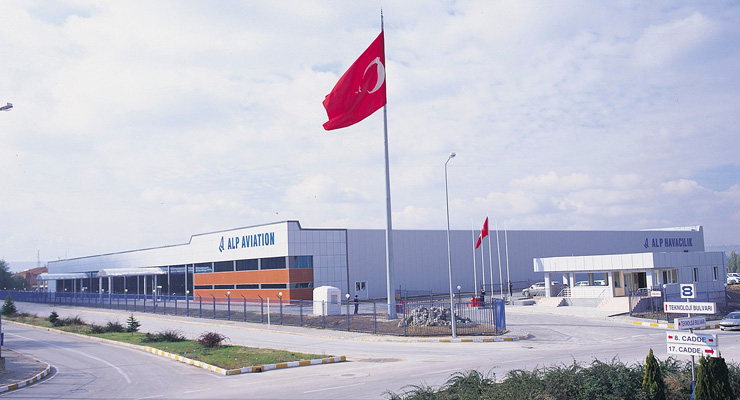