El CFAA ha hecho suya la iniciativa de implementar estrategias y tecnologías de Industria 4.0 en sus instalaciones y procesos y puede acompañar a sus socios en su transformación digital
Digitalización al servicio de la fabricación. Un nuevo reto para el Centro de Fabricación Avanzada Aeronáutica CFAA
L. Sastoque, P. Bedialauneta, S. Sendino, N. Toledo-Gandarias, investigadores en el Centro de Fabricación Avanzada Aeronáutica
15/03/2019Pasando por los desarrollos en control numérico de los años 50 (Alan Parsons, MIT), a los circuitos integrados de los 60 (CNCs) y la llegada de Internet en los 80, fueron todas tecnologías ampliamente usadas en el ámbito de la fabricación, dando como resultado tecnologías avanzadas como la fabricación integrada (CIM), el diseño asistido (CAD) y la fabricación por ordenador (CAM), a los sistemas de ejecución de fabricación (MES) y sistemas de planificación de recursos empresariales (ERP).
Recientemente, el auge de nuevas tecnologías como Internet de las cosas (IoT), la computación en la nube o en los dispositivos (Cloud y Edge Computing, respectivamente), el análisis de Big data y la inteligencia artificial continúan revolucionando y evolucionando el paradigma de la fabricación. Tampoco ha sido fácil. Las crisis económicas de los últimos años junto con la necesidad de brindar una respuesta rápida a nuevas oportunidades de negocio han cambiado radicalmente el panorama del sector industrial. Las empresas en busca de mano de obra más económica, mejores condiciones contractuales, nuevos mercados y productos y mejores beneficios, están ahora comprometidas en recuperar la competitividad de antaño.
Los gobiernos alemán, estadounidense, vasco y chino han promovido iniciativas con miras a acelerar la adopción de tecnologías emergentes en la industria que apuntalen a una mejora de la calidad, el rendimiento y el control de los procesos [2]. Lo que se espera además es que la fabricación se realice de manera más inteligente y adaptativas usando sistemas flexibles y colaborativos que resuelvan problemas y mejoren la toma de decisiones. La iniciativa Basque Industry 4.0 es un claro ejemplo de éxito en generar acciones y opinión favorable a la necesidad del cambio social y económico.
Las pequeñas y medianas empresas han representado la columna vertebral de la economía en la Unión Europea y son pieza clave para la competitividad. Es por esto que sobre ellas recae una urgencia mayor de realizar acercamientos para conocer y aplicar tecnologías de la Industria 4.0 en sus procesos [3]. No se puede olvidar las similitudes dentro de este tipo de empresas a la hora de contemplar una estrategia de transformación digital: una cultura organizacional en ocasiones no lo suficientemente flexible como para experimentar y adoptar tecnologías de vanguardia [4], una baja disponibilidad de recursos financieros y una imposibilidad de actualizar y adoptar tecnologías por la falta de los recursos técnicos necesarios.
Esta falta de recursos dificulta así mismo el avance en innovación y desarrollo, lo que no traduce en que sus productos sean altamente especializados y lleven a diferenciarlos de sus competidores, gracias al arduo trabajo que realizan. “Las pymes saben que hay que hacer algo, pero no saben cómo ni por dónde empezar”, lo resume Maier & Student [5]. Esta afirmación es apoyada por las conclusiones de varios estudios que muestran que un gran porcentaje de empresas pequeñas y medianas no conocen siquiera los conceptos básicos relacionados con las tecnologías de la Industria 4.0 y sus modelos comerciales y operativos [6], lo que los lleva a ignorar, entre otras, tendencias asociadas como la digitalización y la automatización.
Sin embargo y a pesar de haber tomado la decisión de sumirse en un proceso de transformación digital, recorrer este camino, como ya lo habíamos mencionado, no es tarea fácil. La fabricación moderna es inherentemente compleja [7], por lo que establecer estrategias de colaboración con redes interdisciplinarias en investigación resulta crucial para el éxito de la organización. Las empresas pequeñas y medianas carecen en gran medida de este tipo de alianzas con universidades y otras instituciones de investigación que les den acceso a conocimiento compartido y especializado, lo que les limita a aprender tan solo de su propia experiencia.
Las tecnologías que soportan la transformación digital buscan integrar máquinas inteligentes, personas, objetos físicos y líneas de producción y proceso, esenciales para formar una nueva clase de cadena de valor en la organización. Un aspecto que se suma a la complejidad de la tarea es que la implementación de estas tecnologías ha de ser interdisciplinar y en estrecha relación entre las áreas claves de la empresa, ya que, en un contexto industrial, cada tecnología implementada de manera individual presenta un impacto menor del que lo haría el implementarlas de manera conjunta.
El Centro de Fabricación Avanzada Aeronáutica ha hecho suya la iniciativa de implementar estrategias y tecnologías de Industria 4.0 en sus instalaciones y procesos y de esta manera poder caminar de la mano con sus socios en la compleja tarea de transformarse digitalmente. Para una organización, este proceso incluye, primero, la implementación de distintas, y en algunos casos complejas, herramientas tecnológicas. Luego es necesario crear una red de transmisión de información en tiempo real para conectar estas herramientas y gestionar los datos que se generan, y una vez generados, se requiere de un equipo especializado en la gestión de dichos datos. Sencillo, ¿no?
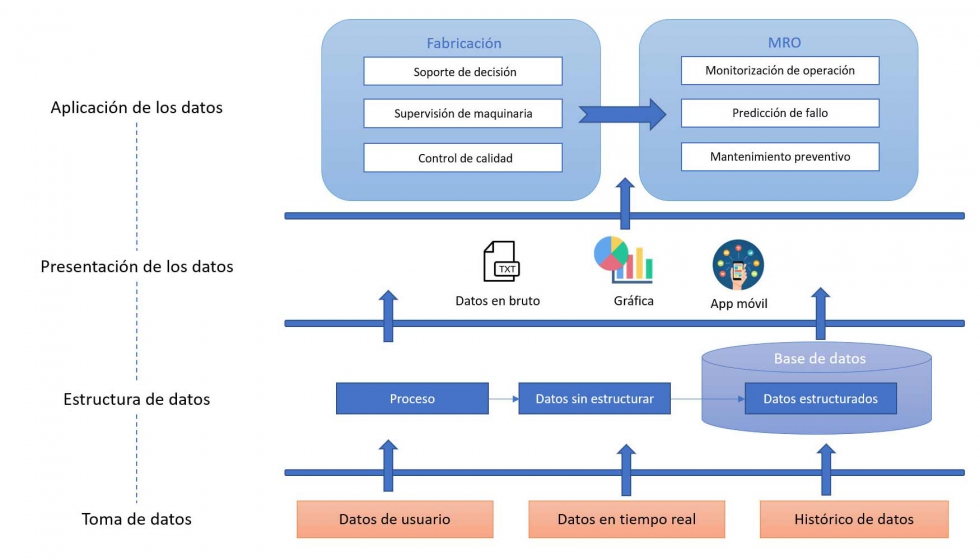
Con estos tres pasos y una adecuada gestión y análisis de los datos aupada en el uso de herramientas de tecnología artificial, se facilitaría la producción y se proporcionaría un servicio de alta eficiencia, calidad, rentabilidad y respeto con el medio ambiente a los usuarios, mejorando la competitividad en el mercado [8], lo que resultaría en una fabricación inteligente.
El objetivo de la fabricación inteligente es lograr un sistema de fabricación basado en dispositivos ciber físicos [9], diseñados para realizar una gestión de la producción, la planeación, los inventarios y las tareas de manera inteligente. Además, la fabricación inteligente debe poder producir no solo afectaciones positivas en los indicadores económicos de la empresa, sino también deberá convertirse en un motor de crecimiento continuo a través del desarrollo sostenible. Nace con el objetivo de analizar los elementos tecnológicos y los factores humanos e integrarlos al proceso logístico de la empresa.
Para alcanzar lo propuesto, se hace necesario implementar dispositivos IoT industriales que logren la convergencia de la fabricación del espacio físico y la fabricación digital con cualidades como la automatización, la interconexión inteligente, la monitorización en tiempo real y el control colaborativo. Estos dispositivos pueden adquirir los parámetros importantes de un proceso de fabricación cualquiera a un menor costo, de manera más conveniente y con un mayor valor que no se logran adquirir en una línea de producción industrial tradicional.
Las empresas de servicios y manufactura que recorren ya la segunda fase de transformación digital de sus procesos se han visto enfrentadas a una cantidad exorbitante de datos. Se calcula que estos dos sectores producen unos 1.600 exabites (1,7 x 1.012 gigabites) al año. Estos conjuntos de datos son tan inmensos y complejos que es difícil manejarlos usando herramientas de administración de bases de datos o aplicaciones de procesamiento tradicionales. El análisis del Big data llega entonces con el propósito de convertir los datos tomados durante el ciclo de vida del producto en inteligencia aplicada a la fabricación, para crear un impacto positivo en los aspectos relacionados [10].
Hay que tener en cuenta que los datos y recursos físicos son típicamente heterogéneos, lo que hace necesaria una estrategia de integración para asegurar la consistencia de los datos gestionados. Esto obliga a contar con un lenguaje de entendimiento para la presentación y representación de los datos junto con un protocolo que permita comunicar a los dispositivos IIoT con la fábrica digital.
La inteligencia artificial soporta a la fabricación inteligente de varias maneras. En las máquinas, los datos generados por los sensores pueden ser analizados a través del uso de herramientas analíticas avanzadas para monitorizar y predecir el funcionamiento de las mismas; el mantenimiento predictivo ayuda a evitar paradas de máquina innecesarias debido a fallos inesperados durante el proceso de producción. Adicionalmente permiten medir y así mejorar los procesos; las máquinas equipadas con inteligencia artificial pueden identificar automáticamente no conformidades en los productos en etapas tempranas de producción, incrementando la calidad del proceso y reduciendo los costos del mismo. Además, ayudan a afrontar de manera distinta los demás problemas relacionados; la adopción de métodos de fusión de datos y aplicación de técnicas de machine learning pueden suplir necesidades y requerimientos industriales específicos [11].
A un nivel conceptual, la fabricación dirigida por datos se compone de tres fases representando un ciclo de aprendizaje. El objetivo es realizar una mejora continua a través de los datos, extrayendo conocimiento y tendencias de los mismos. El punto de partida ha de ser un proceso ya existente y sus datos relacionados, para posteriormente integrarlos, analizarlos y optimizarlos, y finalmente ejecutar nuevamente el proceso adaptado.
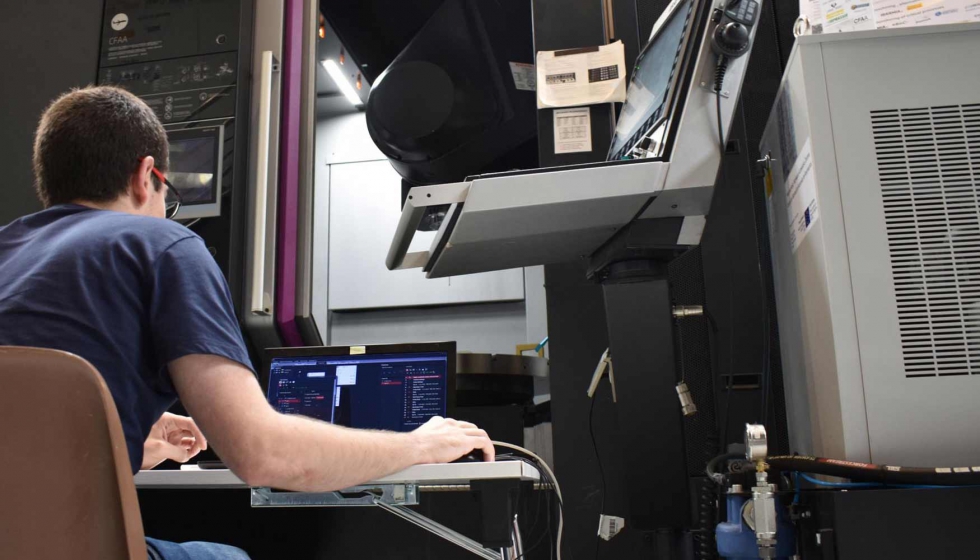
En un informe publicado por IDC se informa que, durante los próximos años, los fabricantes planean usar el análisis del Big data como elemento diferenciador competitivo para obtener ingresos rentables a largo plazo [12], optimizar las operaciones y elaborar decisiones estratégicas en tiempo real [13]. Rolls Royce, por ejemplo, ha conseguido llevar el análisis del Big data a un nivel superior con la unidad de monitorización del estado del motor, que utiliza los datos recopilados por los sensores de distintos componentes, sistemas y líneas de fabricación para mejorar la calidad del producto [14].
Este y varios ejemplos más dan prueba de que el análisis sistemático de los datos de fabricación o los generados durante el ciclo de vida del producto lleva a tomar decisiones que mejoran la efectividad de los procesos. Es por esto que los datos se han convertido en clave para alcanzar un alto nivel de competitividad en los procesos de fabricación.
Otra tecnología a tener en cuenta es la de los gemelos digitales, concepto introducido primero por Grieves en una de sus presentaciones en el año 2003 [15], la cual se ha desplazado en los últimos años hacia la fabricación y productos inteligentes. El gemelo digital puede ayudar a garantizar la continuidad de la información a lo largo de todo el ciclo de vida del producto, la puesta en marcha virtual de los sistemas de fabricación y como soporte de las decisiones y las predicciones de comportamiento del sistema en la fase de desarrollo del producto, así como en las subsiguientes de su ciclo de vida [16]. Gartner los clasificó como una de las diez mejores tendencias tecnológicas para el 2017 y el 2018 [17]. Asimismo un grupo de expertos de Lockheed Martin predijeron que el gemelo digital podría ser la tecnología más importante en la industria de la defensa y aeroespacial en los próximos años.

Digitalización en el Centro de Fabricación Avanzada Aeronáutica
Nuestra estrategia digital busca aprovechar la condición de planta piloto para obtener el mayor provecho posible de los datos que se generan en los procesos llevados a cabo en el Centro y orientarlos hacia una gestión inteligente de nuestros proyectos, un seguimiento del comportamiento de los equipos e implementar un sistema de mantenimiento inteligente en las máquinas.
Para realizarlo, el Centro cuenta actualmente con distintos equipos de metrología avanzada, brochadoras, tornos verticales y horizontales, de rebabado, rayos X, soldadura, electroerosión, fabricación aditiva, entre otros, que fue necesario identificar para poder monitorizar en tiempo real.
Dado que en la mayoría de nuestras máquinas disponemos de distintos dispositivos de edge computing (Sistema Vixion, Savvy, Artis, Mindsphere, Sk Inspect, Soc-e, Scanfield, entre otros), evitar interferencias con las operaciones normales de la máquina y las personas que las operan no fue tarea sencilla. Estos dispositivos (en medio de grandes diferencias entre cada uno) tienen comportamientos similares para la adquisición y gestión de los datos.
Sin embargo, y tal como lo mencionábamos antes, es imperativo organizar los distintos datos heterogéneos generados de las máquinas para lograr enfocarlos hacia una monitorización eficiente y eficaz.
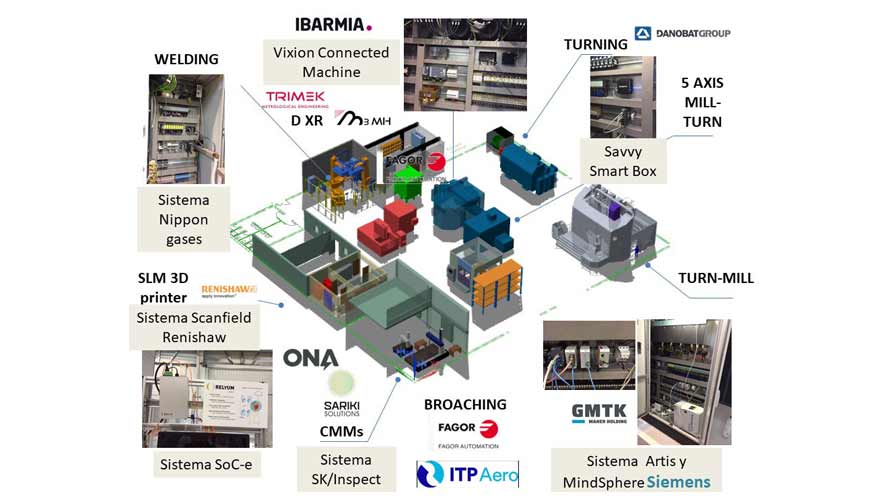
Asimismo, se ha realizado un despliegue de una red experimental SN4I (Smart Networks for Industry). Esta red es una infraestructura de cómputo y comunicaciones con capacidades NFV (Virtualización de funciones de red) y SDN (Redes definidas por software), que interconectan a la Universidad del País Vasco con el CFAA.
NFV proporciona un mecanismo flexible para el despliegue de servicios virtuales, mientras que SDN permite la programación de los elementos de red para interconectar los servicios virtuales a través de enlaces o redes virtuales. Ambas tecnologías garantizan un total aislamiento tanto a nivel de datos como de rendimiento, lo que asegura que servicios virtuales ejecutándose sobre el mismo hardware físico o enlaces virtuales desplegados sobre la misma red física nunca interfieran entre sí. [18]
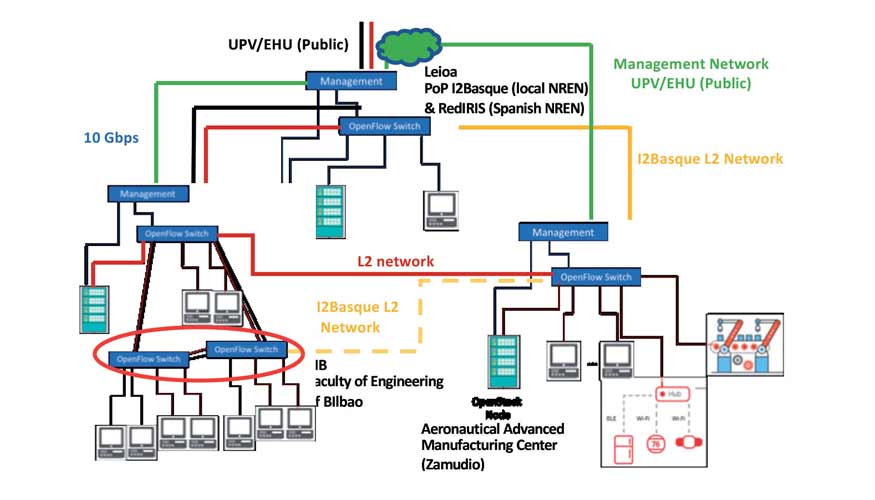
Finalmente, se creó una plataforma de monitorización de máquina en tiempo real habilitada para el uso de los dispositivos previamente descritos. En esta plataforma se implementa una base de datos relacional mediante MySQL que proporciona maneras fáciles de consultar, el grabar y gestionar de los datos.
La plataforma se ha basado en un servidor hospedado por la red SN4I. La comunicación entre el sistema de adquisición de datos y la máquina virtual que contiene la base de datos se hace también a través de la red previamente mencionada.
Una vez allí, los datos homogeneizados y organizados según distintos criterios de clasificación, y se hacen accesibles por los modelos de procesamiento de datos donde se realizarán sus análisis y se mostrarán por diversos canales a los usuarios.
Uno de esos canales es una aplicación móvil desde la cual se puede observar en tiempo real el comportamiento de las máquinas, el proyecto que se está realizando y el operario de la misma. Asimismo, se observan datos de comportamiento de proceso y rendimiento de máquina.
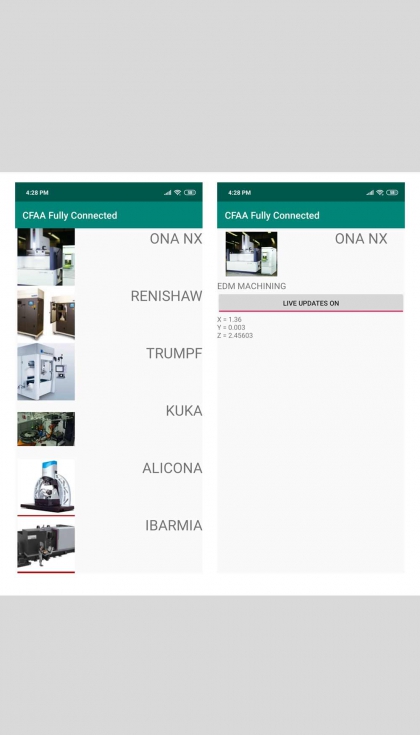
Después de la implementación de esta plataforma, con la asistencia de los dispositivos de edge computing y la red SN4I, se puede alcanzar la monitorización en tiempo real de todas las máquinas del Centro.
Se planea asimismo, una plataforma que permita analizar y clasificar los datos generados de las tareas ejecutadas en los proyectos, para poder evaluar y predecir su rendimiento en el ahora y en el final, para poder gestionar de manera inteligente los recursos con los que se cuenta.
Por otra parte, el desarrollo de modelos de simulación de procesos de soldadura por electro beam es otro de los proyectos a los que se están dirigiendo importantes esfuerzos y recursos. Se espera con estos modelos poder gestionar de una mejor manera los recursos que se invierten en pruebas de soldadura y mejorar los tiempos de ejecución de estas tareas.
Para concluir, no podemos olvidar que el éxito de una estrategia de transformación digital recae en la visión y en los objetivos planteados desde los entes más altos de la organización. Estos deben aceptar desde un inicio que una falla en la estrategia no tiene que significar un fracaso, sino que debe ser visto como un prerrequisito para el éxito. Ya con un camino andado, las empresas se tornan más flexibles y se sienten más cómodas tomando riesgos que aquellas que no lo han recorrido.
Para poder aprovechar las tecnologías emergentes se debe conocer muy bien su negocio y sus procesos. También hay que apoyarse en las personas con mayor experiencia dentro de la organización, pues son ellas, y no la tecnología artificial instalada en las máquinas, quienes marcan la verdadera diferencia. Además, es recomendable apoyarse en universidades, centros de investigación y mixtos.
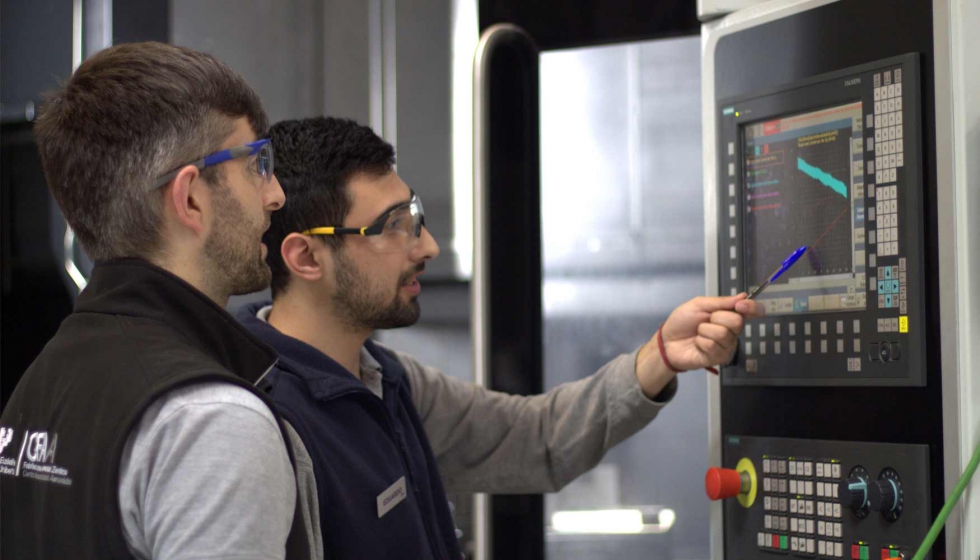
Autores
Leonardo Sastoque Pinilla. Investigador del Centro de Fabricación Avanzada Aeronáutica. Doctorando en Ingeniería de proyectos, Máster en dirección de proyectos europeos e ingeniero aeronáutico. Está especializado en la gestión y desarrollo de proyectos de transformación digital e implementación de tecnologías 4.0. Cuenta con experiencia en ingeniería de procesos y proyectos, e implementación de sistemas de gestión.
Pablo Bedialauneta Rodríguez. Investigador en el Centro de Fabricación Avanzada Aeronáutica. Estudiante de último año del doble grado en física e ingeniería electrónica de la UPV-EHU. Está centrado en el desarrollo de proyectos de simulación de procesos, implementación de la infraestructura de red local y optimización del proceso de soldadura láser. También está implicado en el proyecto de cohetería BiSKY Team como jefe técnico de aerodinámica y recuperación.
Sara Sendino Mouliet. Investigadora en el Centro de Fabricación Avanzada Aeronáutica (CFAA). Doctoranda en Ingeniería de materiales y procesos sostenibles, Máster en ingeniería de materiales avanzados e ingeniera ambiental. Está especializada en tecnologías de lecho de polvo y caracterización del mismo para procesos de fabricación aditiva y metrología avanzada, cuenta con experiencia en el manejo de big data y visualización de datos para procesos de control empresariales.
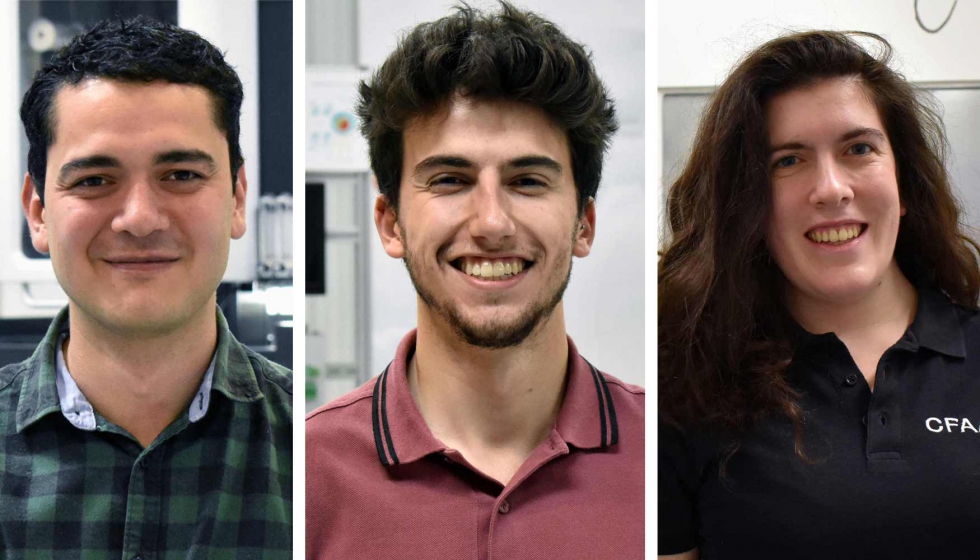
Bibliografía
[1] G. C. Kane, D. Palmer, A. N. Phillips, D. Kiron and N. Buckley, “Strategy, Not Technology, Drives Digital Transformation” MIT Sloan Management Review and Deloitte University Press, July 2015.
[2] S. Jeschke, C. Brecher, T. Meisen, D. Özdemir, T. Eschert, Industrial internet of things and cyber manufacturing systems, in: Industrial Internet of Things, Springer, 2017, pp. 3–19.
[3] R.A. Rojas, E. Rauch, R. Vidoni, D.T. Matt, Enabling Connectivity of Cyberphysical Production Systems: A Conceptual Framework, Procedia Manuf. 11 (2017) 822–829, https://doi.org/10.1016/j.promfg.2017.07.184.
[4] Van de Vrande V, De Jong JP, Vanhaverbeke W, De Rochemont M. Open innovation in SMEs: trends, motives and management challenges. Technovation 2009;29(6-7):423–37.
[5] Maier A, Student D. Industrie 4.0 - der große Selbstbetrug [In German] Retrieved April 2018 from 2015http://www.manager-magazin.de/magazin/artikel/digitalerevolution-industrie-4-0-ueberfordert-deutschen-mittelstand-a-1015724.html.
[6] Eisert R. Mittelständler verpassen die Zukunftstrends [In German] Retrieved April 2018 http://www.wiwo.de/unternehmen/mittelstand/industrie-4-0-mittelstaendler-verpassen-die-zukunftstrends/10004718.html.
[7] Esmaeilian B, Behdad S, Wang B. The evolution and future of manufacturing: A review. J Manuf Syst 2016; 39:79–100.
[8] Li, Bo-hu & Hou, Bao-cun & Yu, Wen-tao & Lu, Xiao-bing & Yang, Chun-wei. (2017). Applications of artificial intelligence in intelligent manufacturing: a review. Frontiers of Information Technology & Electronic Engineering. 18. 86-96. 10.1631/FITEE.1601885.
[9] L. Monostori, B. Kádár, T. Bauernhansl, S. Kondoh, S. Kumara, G. Reinhart, et al., Cyber-physical systems in manufacturing, CIRP Ann. Manuf. Tech. 65 (2) (2016) 621–641.
[10] O’Donovan P, Leahy K, Bruton K, O’Sullivan DTJ. An industrial big data pipeline for data-driven analytics maintenance applications in large-scale smart manufacturing facilities. J Big Data 2015;2(25):1–26, http://dx.doi.org/10.1186/s40537-015-0034-z.
[11] R.S. Michalski, J.G. Carbonell, T.M. Mitchell, Machine Learning: An Artificial Intelligence Approach, Springer Science & Business Media, 2013.
[12] Spotfire (2013). Big data in manufacturing: Rise of the machine: TIBCO Spotfire’s Trends and Outliers Blog.
[13] Khatri, H. (2013). Trends in manufacturing operations: Leveraging big data across the value chain: PROFIT ORACLE Technology Powered. Business
[14] BigData-Startups (2013). Rolls Royce shifts in higher gear with big data: BigData-Startup. The Online Big Data Knowledge Platform.
[15] Grieves M. Digital twin: Manufacturing excellence through virtual factory replication. White paper, 2014; Available: http://www.apriso.com.
[16] Edward M. Kraft, The Air Force Digital Thread/Digital Twin - Life Cycle Integration and Use of Computational and Experimental Knowledge, in: 54t AIAA Aerospace Sciences Meeting, AIAA SciTech Forum, (AIAA 2016–0897).
[17] Panetta K. Gartner’s top 10 strategic technology trends for 2017. Gartner, 2016; Available: https://www.gartner.com/smarterwithgartner/gartnerstop-10-technology-trends-2017/
[18] Jacob-Taquet, E., Astorga, J., Uncilla-Galan, J., Huarte, M., Garcia-Conejo, D., López-De La Calle Marcaide, L. (2018). TOWARDS A 5G COMPLIANT AND FLEXIBLE CONNECTED MANUFACTURING FACILITY. DYNA, 93(6). 656-662. DOI: http://dx.doi.org/10.6036/8831